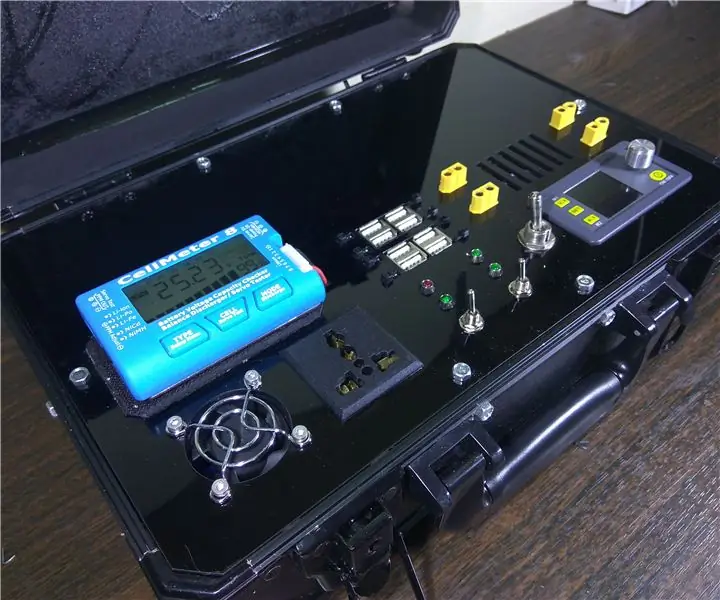
Table des matières:
- Étape 1: Les matériaux et outils
- Étape 2: le schéma
- Étape 3: Le tableau de bord
- Étape 4: le boîtier (peinture et supports de montage)
- Étape 5: La batterie, partie 1 (test des cellules et création de groupes)
- Étape 6: La batterie, partie 2 (rejoindre les groupes)
- Étape 7: La batterie, partie 3 (soudage et finition)
- Étape 8: La batterie, partie 4 (installation)
- Étape 9: l'onduleur, partie 1 (démontage et installation du dissipateur thermique)
- Étape 10: L'onduleur (installation et montage)
- Étape 11: Le module USB (installation et câblage)
- Étape 12: Le module DPH3205 Partie 1 (Installation et câblage d'entrée)
- Étape 13: Le module DPH3205, partie 2 (montage de l'écran et câblage de sortie)
- Étape 14: Les E/S auxiliaires (montage et câblage)
- Étape 15: CQ (inspection rapide)
- Étape 16: Finition et test
- Étape 17: Mises à jour
2025 Auteur: John Day | [email protected]. Dernière modifié: 2025-01-23 14:46
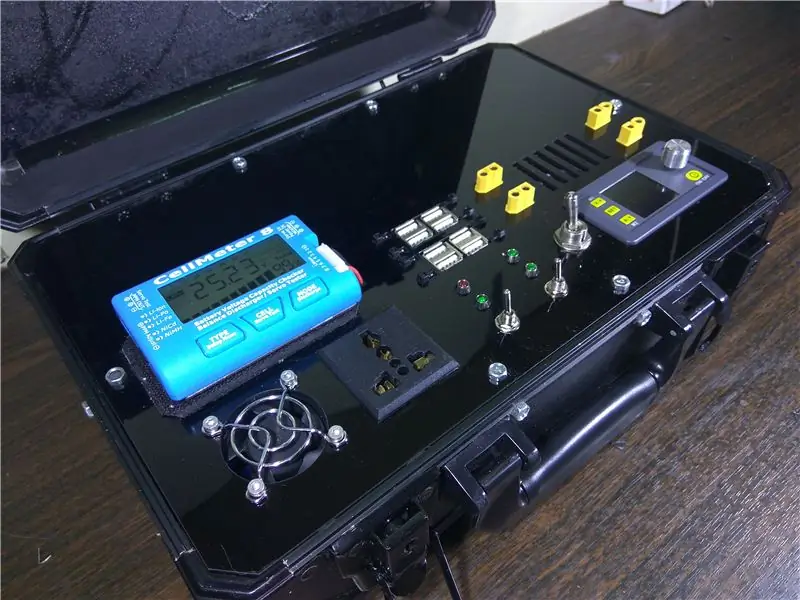
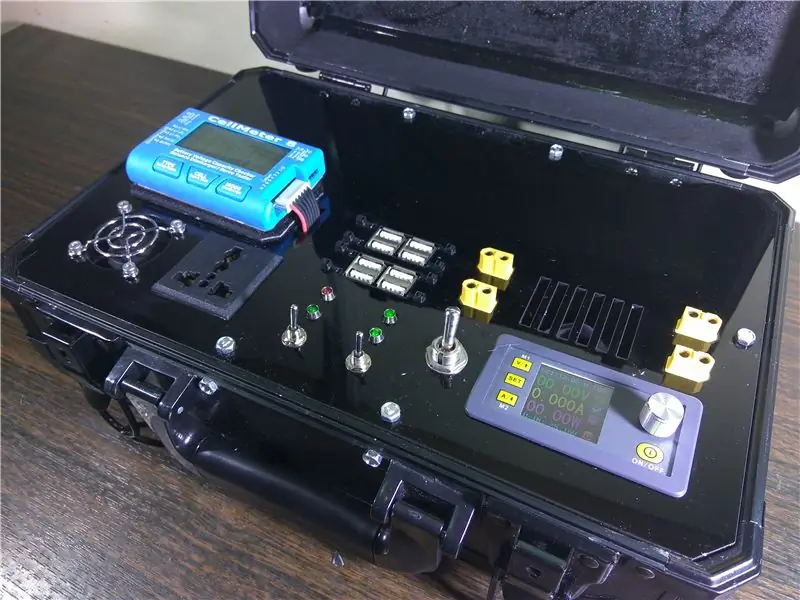
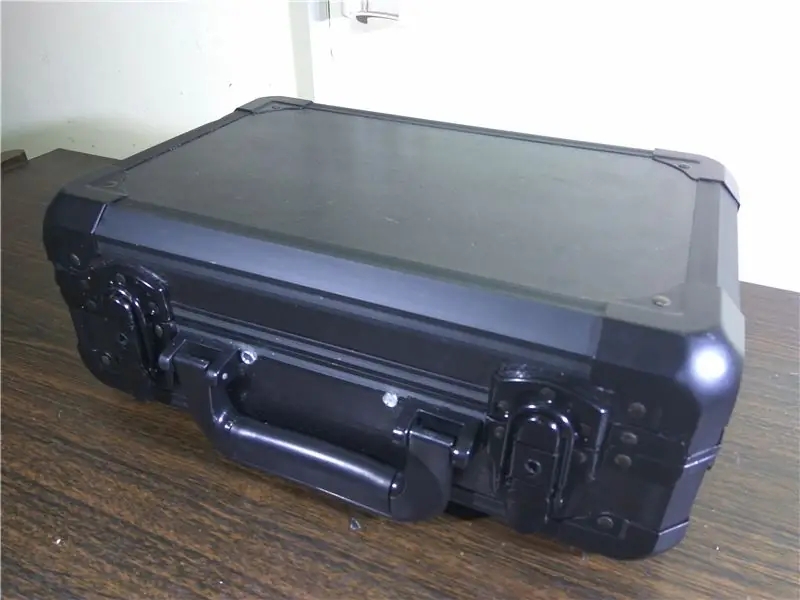
Pour mon premier Instructable, je vais vous montrer comment j'ai fait cette alimentation portable. Il existe de nombreux termes pour ce type d'appareil comme banque d'alimentation, centrale électrique, générateur solaire et bien d'autres, mais je préfère le nom "Listrik L585 Portable Power Supply".
Le Listrik L585 a une batterie au lithium intégrée de 585Wh (6S 22.2V 26, 364mAh, testée) qui peut vraiment durer. Il est également assez léger pour la capacité donnée. Si vous souhaitez le comparer avec une banque d'alimentation client typique, vous pouvez le faire facilement en divisant la valeur mAh par 1 000, puis en la multipliant par 3,7. Par exemple, la PowerHouse (l'une des plus grandes banques d'alimentation grand public bien connues) a une capacité de 120 000 mAh. Maintenant, faisons le calcul. 120 000 / 1 000 * 3,7 = 444 Wh. 444Wh contre 585Wh. Facile n'est-ce pas ?
Tout est emballé dans cette jolie mallette en aluminium. De cette façon, le Listrik L585 peut être transporté facilement et le couvercle supérieur protégera les instruments sensibles à l'intérieur lorsqu'ils ne seront pas utilisés. J'ai eu cette idée après avoir vu quelqu'un construire un générateur solaire à l'aide d'une boîte à outils, mais la boîte à outils n'a pas l'air si géniale, n'est-ce pas ? Alors je l'ai poussé d'un cran avec une mallette en aluminium et ça a l'air beaucoup mieux.
Le Listrik L585 a plusieurs sorties qui peuvent couvrir presque tous les appareils électroniques grand public.
Le premier est la sortie CA qui est compatible avec près de 90% des appareils secteur de moins de 300 W, pas tous en raison d'une sortie non sinusoïdale, mais vous pouvez résoudre ce problème en utilisant un onduleur à onde sinusoïdale pure, ce qui est beaucoup plus cher que le standard modifié onduleur à onde sinusoïdale que j'ai utilisé ici. Ils sont aussi généralement plus gros.
La deuxième sortie est la sortie USB. Il y a 8 ports USB, ce qui est un peu excessif. Une paire d'entre eux peut fournir un courant maximum de 3A en continu. Le redressement synchrone le rend très efficace.
Le troisième est l'E/S auxiliaire. Il peut être utilisé pour charger ou décharger la batterie interne à un taux maximum de 15A (300W+) en continu et 25A (500W+) en instantané. Il n'a aucune régulation, essentiellement une simple tension de batterie, mais il dispose de plusieurs protections, notamment les courts-circuits, les surintensités, les surcharges et les décharges excessives.
Le dernier et mon préféré est la sortie CC réglable, qui peut produire 0-32V, 0-5A sur toutes les plages de tension. Il peut alimenter une très grande variété d'appareils CC comme un ordinateur portable typique avec une sortie 19V, un routeur Internet à 12V et bien plus encore. Cette sortie CC réglable élimine le besoin d'utiliser une alimentation CA vers CC, ce qui, en passant, aggravera l'efficacité car l'ensemble du système convertit le CC en CA puis à nouveau en CC. Il peut également être utilisé comme alimentation de banc avec fonction tension constante et courant constant, ce qui est très utile pour les personnes comme moi qui travaillent souvent avec l'électronique.
Étape 1: Les matériaux et outils
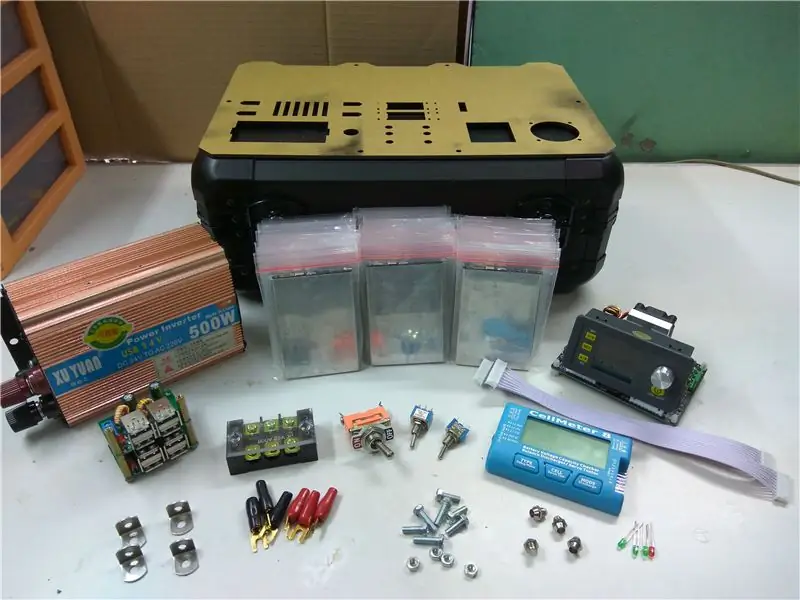
Matériaux principaux:
* 1X mallette en aluminium DJI Spark
* Cellules au lithium prismatique 60X 80*57*4.7mm (vous pouvez les remplacer par des 18650 plus courantes, mais j'ai trouvé que cette cellule avait le facteur de forme et la dimension parfaits)
* Onduleur 1X 300W 24V DC vers AC
* 1X DPH3205 alimentation programmable
* Convertisseurs buck USB 2X 4 ports
* 1X vérificateur de batterie Cellmeter 8
* 1X 6S 15A BMS
* Connecteur d'équilibre 1X 6S
* Boulons 12X M4 10mm
* 12X écrous M4
* 6X supports en acier inoxydable
* Interrupteur à bascule unipolaire 1X 6A
* Interrupteur à bascule bipolaire 1X 6A
* Interrupteur à bascule unipolaire 1X 15A
* Support LED en acier inoxydable 4X 3mm
* 4X connecteurs femelles XT60
* 4X entretoises en laiton M3 20mm
* 4 vis à métaux M3 30mm
* 2 vis à métaux M3 8mm
* 6X écrous M3
* Borne 1X 25A 3 broches
* 4 cosses de câble de 4,5 mm
* Tableau de bord personnalisé de 3 mm
-
Consommables:
* Thermorétractables
* Soudure
* Flux
* Fil de cuivre solide de 2,5 mm
* Ruban adhésif double face robuste (obtenez-en un de la plus haute qualité)
* Ruban adhésif double face fin
* Ruban Kapton
* Epoxy
* Peinture noire
* Fil 26 AWG pour indicateurs LED
* Fil toronné en argent 20 AWG pour le câblage à faible courant
* Fil toronné en argent 16 AWG pour le câblage à courant élevé (un AWG inférieur est préférable. Le mien est évalué à un câblage de châssis continu de 17 A, juste assez)
-
Outils:
* Fer à souder
* Pince
* Tournevis
* Ciseaux
* Couteau de loisir
* Pince à épiler
* Percer
Étape 2: le schéma
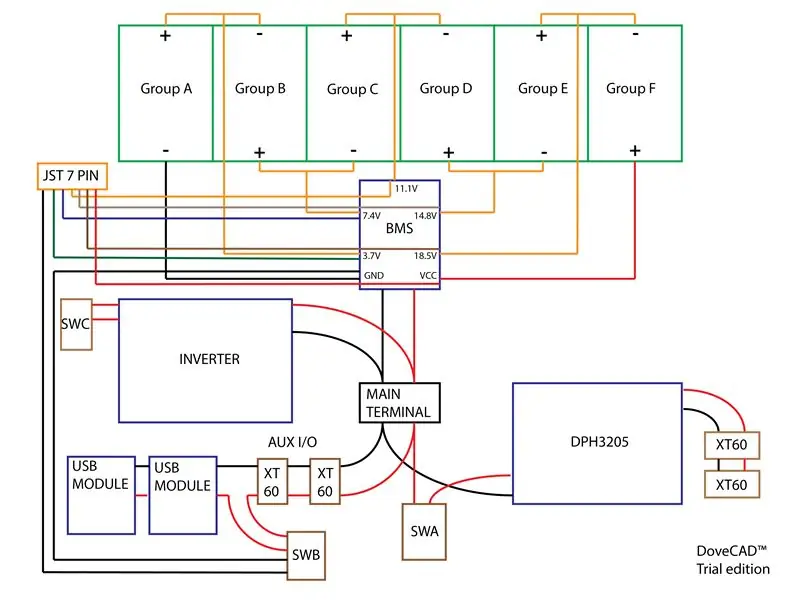
Le schéma doit être explicite. Désolé pour le mauvais dessin, mais cela devrait être plus que suffisant.
Étape 3: Le tableau de bord
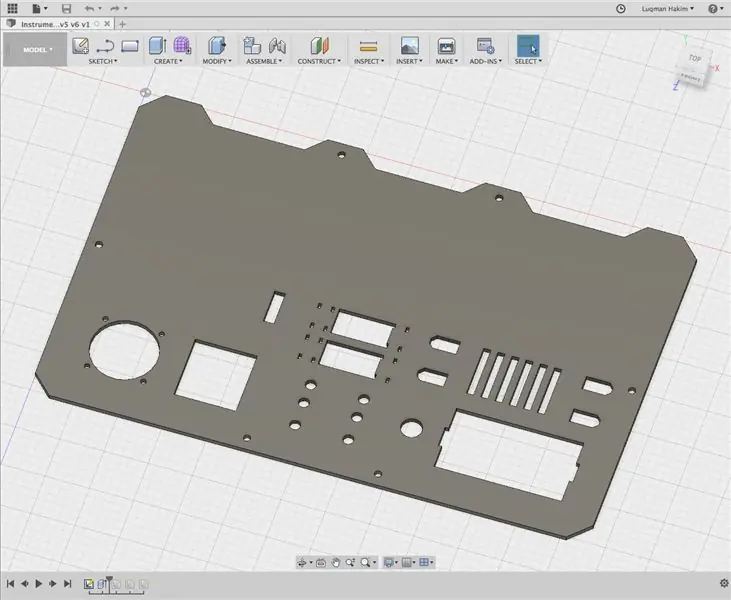
J'ai d'abord conçu le tableau de bord. Vous pouvez télécharger gratuitement le fichier PDF. Le matériau peut être du bois, une feuille d'aluminium, de l'acrylique ou tout autre objet ayant des propriétés similaires. J'ai utilisé de l'acrylique dans ce "cas". L'épaisseur doit être de 3 mm. Vous pouvez le couper par CNC ou simplement l'imprimer sur du papier à l'échelle 1: 1 et le couper manuellement.
Étape 4: le boîtier (peinture et supports de montage)
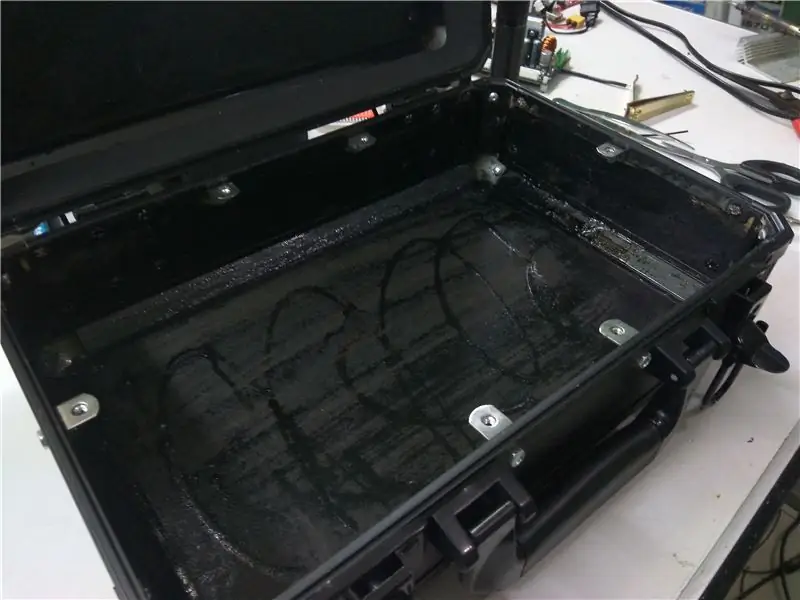
Pour l'étui, j'ai utilisé une mallette en aluminium pour DJI Spark, elle a juste la bonne dimension. Il est venu avec un truc en mousse pour tenir l'avion, alors je l'ai sorti et j'ai peint la partie intérieure en noir. J'ai percé 6 trous de 4 mm en fonction de la distance des trous sur mon tableau de bord personnalisé et j'y ai installé les supports. Ensuite, j'ai collé des écrous M4 sur chaque support afin de pouvoir visser les boulons de l'extérieur sans tenir les écrous.
Étape 5: La batterie, partie 1 (test des cellules et création de groupes)
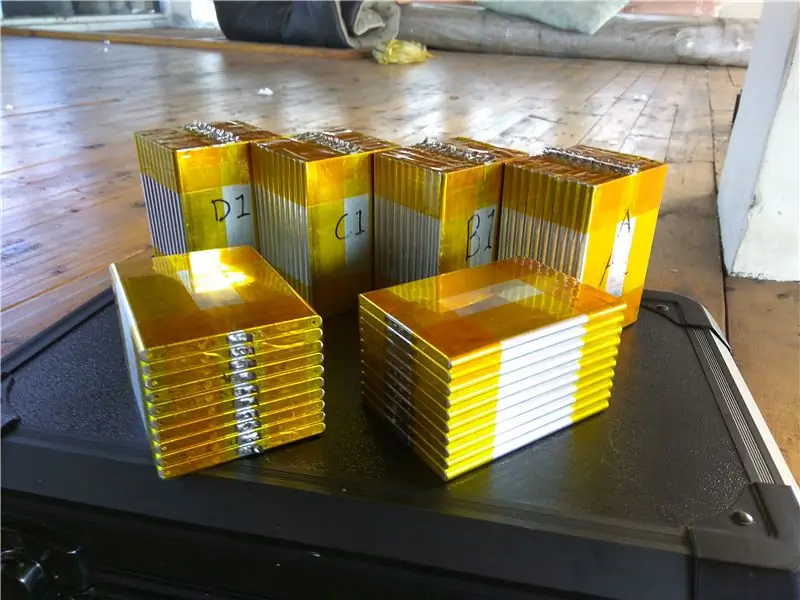
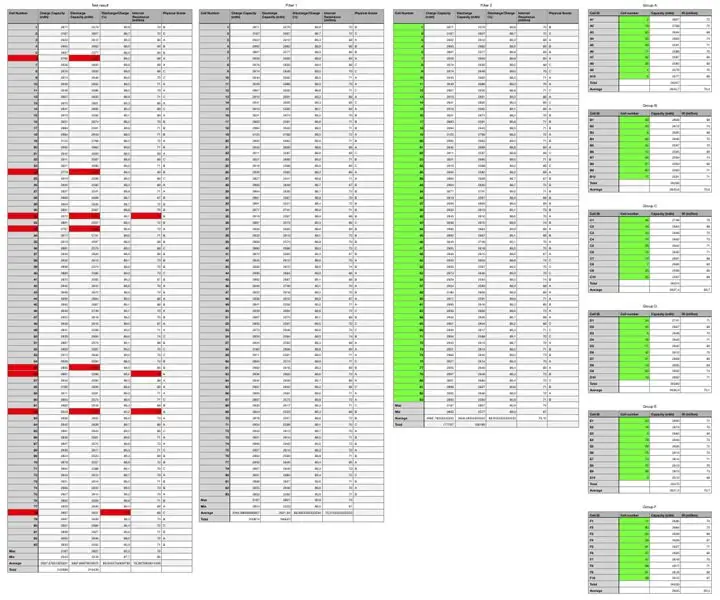
Pour la batterie, j'ai utilisé des cellules au lithium prismatiques LG rejetées que j'ai obtenues pour moins de 1 $ chacune. La raison pour laquelle ils sont si bon marché est simplement parce qu'ils ont un fusible grillé et qu'ils sont étiquetés comme défectueux. J'ai enlevé les fusibles et ils sont comme neufs. C'est peut-être un peu dangereux, mais pour moins d'un dollar chacun, je ne peux pas vraiment me plaindre. Après tout, j'utiliserai un système de gestion de batterie pour les protections. Si vous allez utiliser des piles usagées ou inconnues, j'ai un bon Instructables sur la façon de tester et de trier les piles au lithium usagées ici: (COMING SOON).
J'ai vu beaucoup de gens utiliser une batterie au plomb pour ce genre d'appareil. Bien sûr, ils sont faciles à utiliser et bon marché, mais l'utilisation d'une batterie au plomb pour une application portable est un grand non-non pour moi. Un équivalent plomb-acide pèsera environ 15 kilogrammes ! C'est 500% plus lourd que la batterie que j'ai fabriquée (3 kilogrammes). Dois-je vous rappeler qu'il sera aussi plus gros en volume ?
J'en ai acheté 100 et les ai testés un par un. J'ai la feuille de calcul du résultat du test. Je l'ai filtré, trié et j'ai obtenu les 60 meilleures cellules. Je les divise également par la capacité afin que chaque groupe ait une capacité similaire. De cette façon, la batterie sera équilibrée.
J'ai vu beaucoup de gens construire leur batterie sans autre test sur chaque cellule, ce qui, je pense, est obligatoire si vous voulez créer une batterie à partir de cellules inconnues.
Le test a montré que la capacité de décharge moyenne de chaque cellule est de 2636 mAh à un courant de décharge de 1,5 A. Avec un courant plus faible, la capacité sera plus élevée en raison de la perte de puissance moindre. J'ai réussi à obtenir 2700mAh+ avec un courant de décharge de 0,8A. J'obtiendrai une capacité supplémentaire de 20% si je charge la cellule à 4,35 V/cellule (la cellule autorise une tension de charge de 4,35 V) mais le BMS ne le permet pas. De plus, charger la cellule à 4,2 V prolongera sa durée de vie.
Retour à la notice. Tout d'abord, j'ai joint 10 cellules ensemble à l'aide d'un fin ruban adhésif double face. Ensuite, je l'ai renforcé avec du ruban kapton. N'oubliez pas d'être très prudent lorsque vous utilisez une batterie au lithium. Ces piles au lithium prismatiques ont des parties positive et négative extrêmement proches, il est donc facile d'en court-circuiter une.
Étape 6: La batterie, partie 2 (rejoindre les groupes)
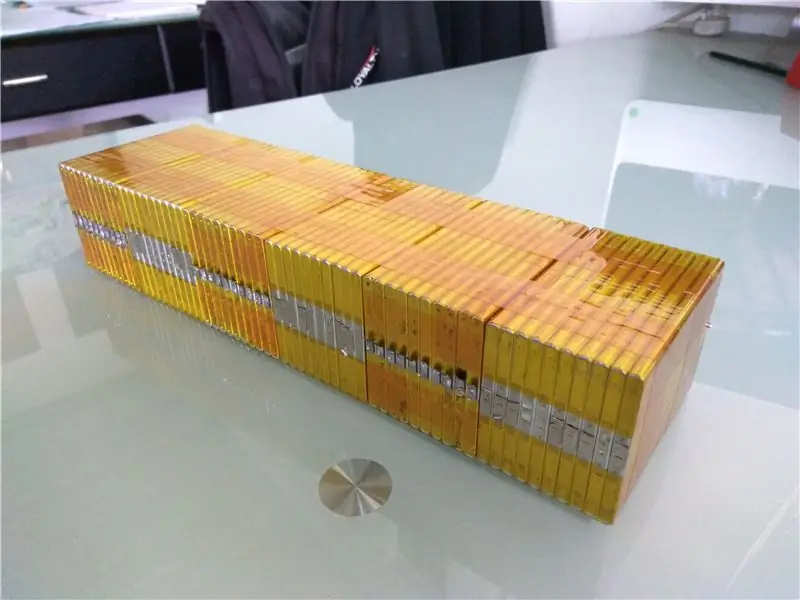
Une fois que j'ai fini de créer les groupes, l'étape suivante consiste à les réunir. Pour les assembler, j'ai utilisé du ruban adhésif double face fin et je l'ai renforcé à nouveau avec du ruban kapton. Très important, assurez-vous que les groupes sont isolés les uns des autres ! Sinon, vous obtiendrez un court-circuit très désagréable lorsque vous les souderez ensemble en série. Le corps de la cellule prismatique est référencé à la cathode de la batterie et inversement pour les 18650 cellules. Veuillez garder cela à l'esprit.
Étape 7: La batterie, partie 3 (soudage et finition)
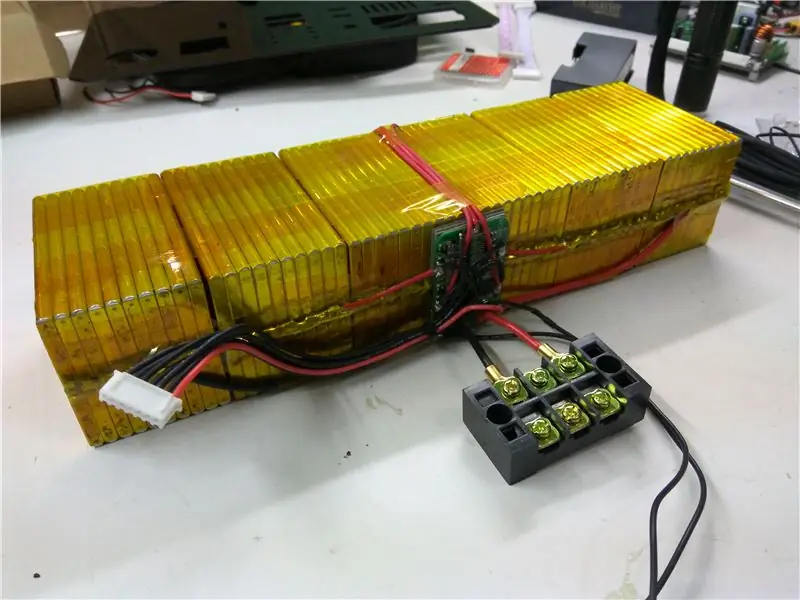
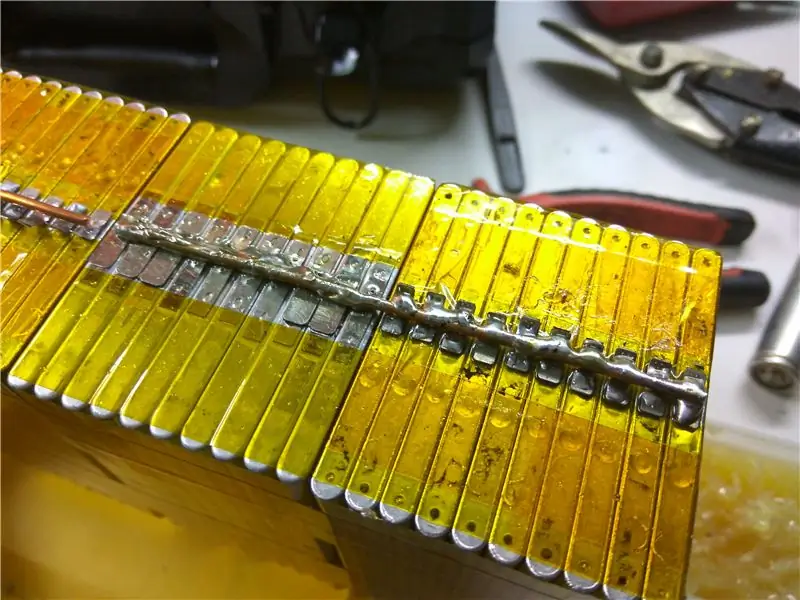
C'est la partie la plus difficile et la plus dangereuse, souder les cellules ensemble. Vous aurez besoin d'un fer à souder d'au moins 100 W pour un soudage facile. Le mien était de 60W et c'était un PITA total à souder. N'oubliez pas le flux, une sacrée tonne de flux. Cela aide vraiment.
** Soyez extrêmement prudent à cette étape ! La batterie au lithium haute capacité n'est pas quelque chose avec laquelle vous voulez être maladroit. **
Tout d'abord, j'ai coupé mon fil de cuivre massif de 2,5 mm à la longueur souhaitée, puis j'ai décollé l'isolant. Ensuite, j'ai soudé le fil de cuivre à la languette de la cellule. Faites-le assez lentement pour permettre à la soudure de s'écouler, mais assez rapidement pour éviter l'accumulation de chaleur. Cela demande vraiment du savoir-faire. Je recommanderais de pratiquer sur autre chose avant de l'essayer avec la vraie chose. Donnez une pause à la batterie après plusieurs minutes de soudure pour qu'elle refroidisse, car la chaleur n'est bonne pour aucun type de batterie, en particulier pour la batterie au lithium.
Pour la finition, j'ai collé le BMS avec 3 couches de rubans mousse double face et câbler le tout selon le schéma. J'ai soudé des cosses de câble sur la sortie de la batterie et immédiatement installé ces cosses sur la borne d'alimentation principale pour empêcher les cosses de se toucher et de provoquer un court-circuit.
N'oubliez pas de souder un fil du côté négatif du connecteur de la balance et un fil du côté négatif du BMS. Nous devons ouvrir ce circuit pour désactiver le Cellmeter 8 (indicateur de batterie) afin qu'il ne s'allume pas pour toujours. L'autre extrémité va à un pôle d'un interrupteur plus tard.
Étape 8: La batterie, partie 4 (installation)
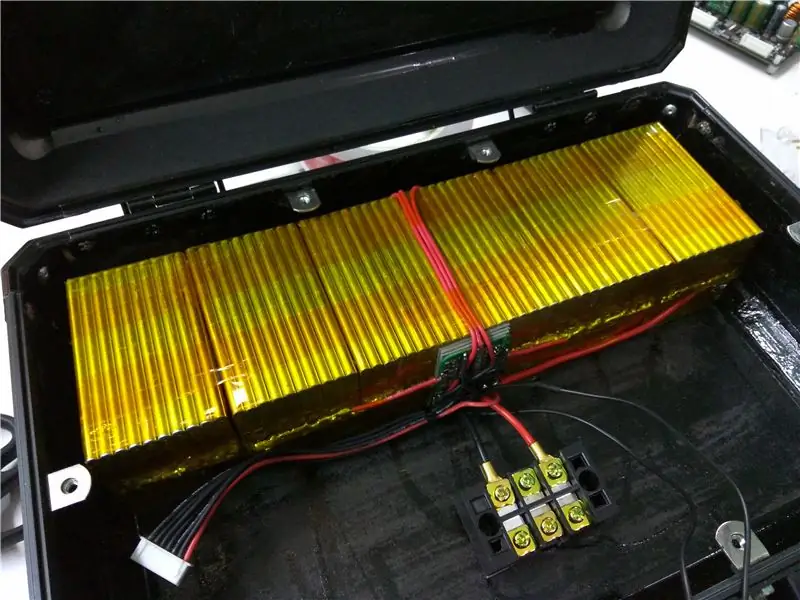
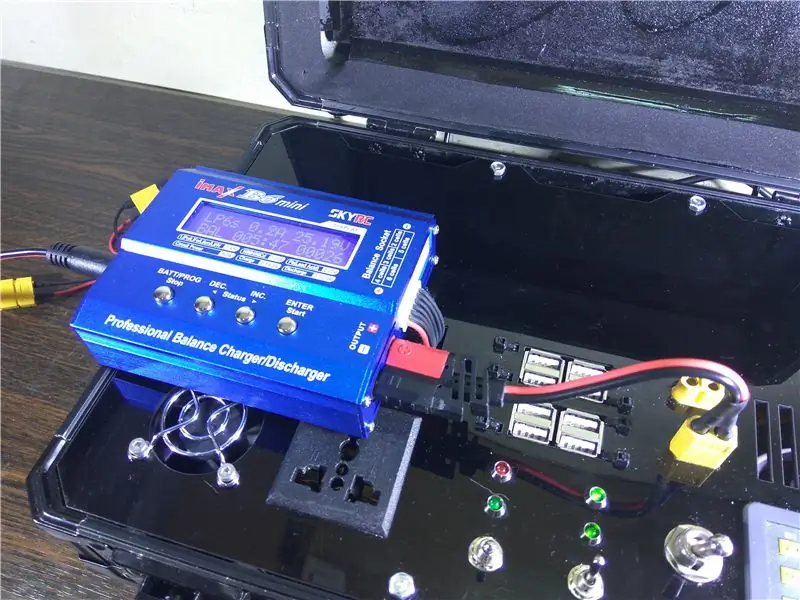
Pour l'installation, j'ai utilisé du ruban adhésif double face. Je recommande d'utiliser du ruban adhésif double face résistant de haute qualité pour ce boîtier car la batterie est assez lourde. J'ai utilisé du ruban adhésif double face 3M VHB. Jusqu'à présent, la bande tient très bien la batterie. Aucun problème.
La batterie s'adapte très bien là-bas, l'une des raisons pour lesquelles j'ai choisi cette pile au lithium prismatique plutôt que la pile au lithium cylindrique. L'entrefer autour de la batterie est très important pour la dissipation de la chaleur.
Concernant la dissipation de chaleur, je ne m'en soucie pas trop. Pour la recharge, j'utiliserai mon IMAX B6 Mini qui ne peut délivrer que 60W. Ce n'est rien comparé à la batterie de 585Wh. La charge a pris plus de 10 heures, si lente qu'aucune chaleur n'est générée. La charge lente est également bonne pour tout type de batterie. Pour la décharge, le courant maximum que je peux tirer de la batterie est bien inférieur au taux de décharge de 1C (26A) à seulement 15A en continu, 25A en instantané. Ma batterie a une résistance interne d'environ 33 mOhm. L'équation de puissance dissipée est I^2*R. 15 * 15 * 0,033 = 7,4 W de puissance perdue sous forme de chaleur à un courant de décharge de 15 A. Pour quelque chose d'aussi gros, ce n'est pas grave. Des tests en conditions réelles montrent qu'à charge élevée, la température de la batterie s'élève à environ 45-48 degrés Celsius. Pas vraiment une température confortable pour la batterie au lithium, mais toujours dans la plage de température de fonctionnement (60º maximum)
Étape 9: l'onduleur, partie 1 (démontage et installation du dissipateur thermique)
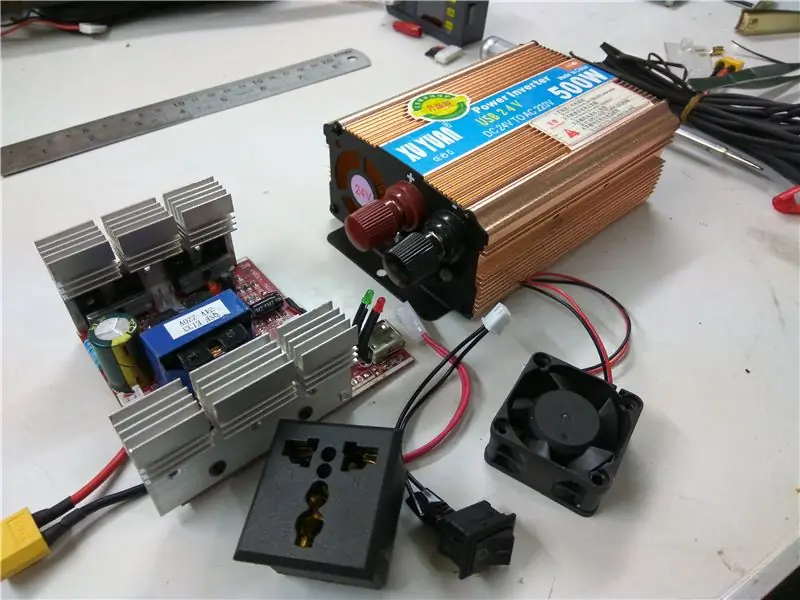
Pour l'onduleur, je l'ai retiré du boîtier pour qu'il rentre dans la mallette en aluminium et j'ai installé une paire de dissipateurs thermiques que j'ai obtenus d'une alimentation d'ordinateur cassée. J'ai également pris le ventilateur de refroidissement, la prise secteur et l'interrupteur pour une utilisation ultérieure.
L'onduleur fonctionne jusqu'à 19V avant que la protection contre les sous-tensions ne se déclenche. C'est assez bon.
Une chose inhabituelle est que l'étiquetage indique clairement 500W tandis que la sérigraphie sur le PCB indique qu'il s'agit de 300W. En outre, cet onduleur dispose d'une véritable protection contre l'inversion de polarité, contrairement à la plupart des onduleurs qui utilisent une diode muette + un engin à fusible pour la protection contre l'inversion de polarité. Sympa, mais pas très utile dans ce cas.
Étape 10: L'onduleur (installation et montage)
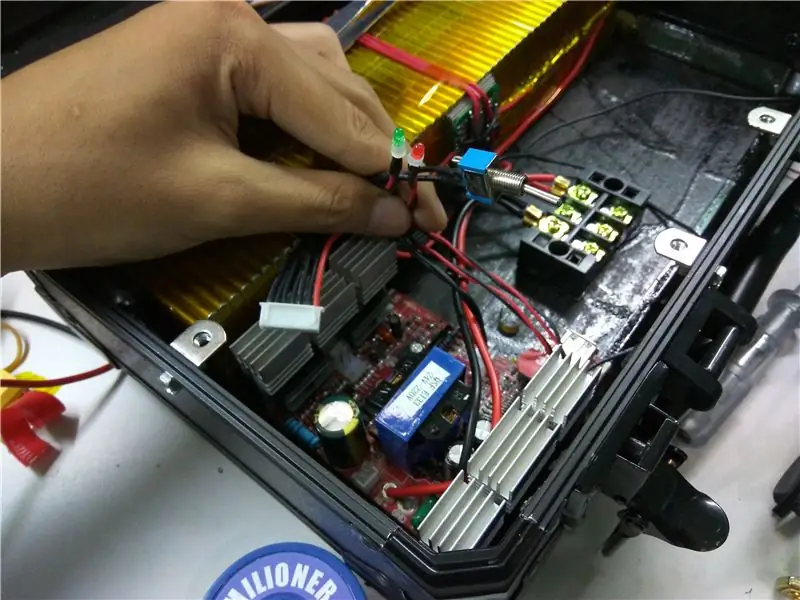
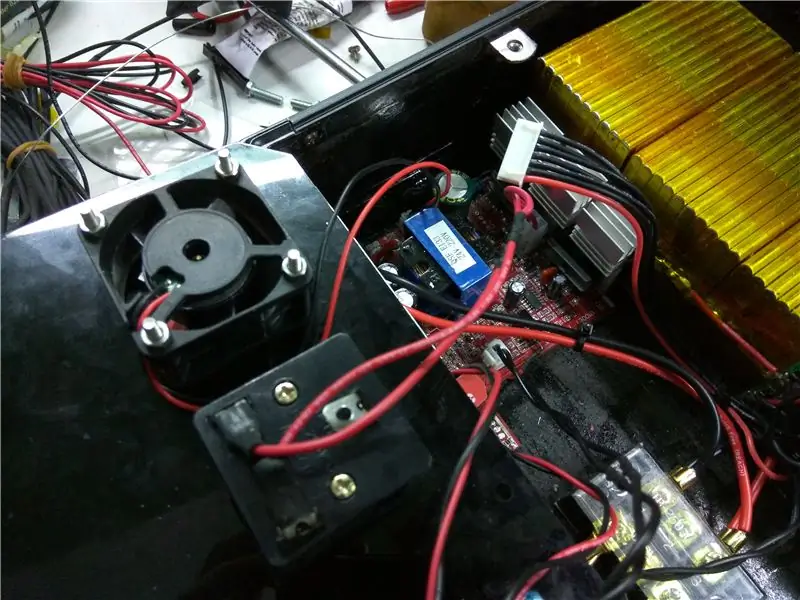
Tout d'abord, j'ai étendu la puissance d'entrée, les indicateurs LED, l'interrupteur et le fil de la prise secteur afin qu'ils soient suffisamment longs. Ensuite, j'ai installé l'onduleur dans le boîtier à l'aide de ruban adhésif double face. J'ai soudé des cosses de câble à l'autre extrémité des fils d'alimentation et les ai connectées à la borne principale. J'ai monté les indicateurs LED, le ventilateur et la prise secteur sur le tableau de bord.
J'ai trouvé que l'onduleur a un courant de repos nul (<1mA) lorsqu'il est connecté à une source d'alimentation mais désactivé, j'ai donc décidé de connecter le fil d'alimentation de l'onduleur directement sans aucun interrupteur. De cette façon, je n'ai pas besoin d'un interrupteur à courant élevé encombrant et de moins d'énergie gaspillée sur le fil et l'interrupteur.
Étape 11: Le module USB (installation et câblage)
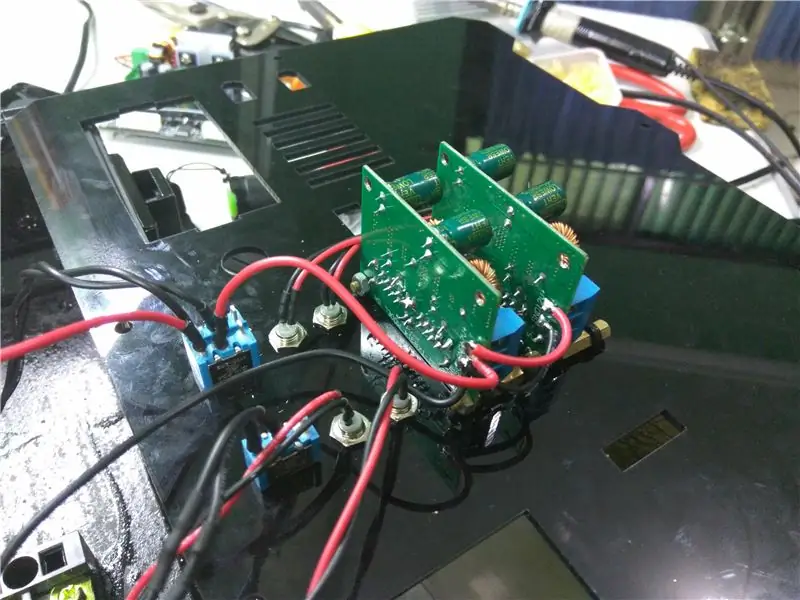
Tout d'abord, j'ai étendu les indicateurs LED sur les deux modules. Ensuite, j'ai empilé les modules avec les entretoises en laiton M3 20mm. J'ai soudé les fils d'alimentation selon le schéma et mis l'ensemble sur le tableau de bord et l'ai attaché avec des attaches. J'ai soudé les 2 fils de la batterie dont j'ai parlé plus tôt à l'autre pôle de l'interrupteur.
Étape 12: Le module DPH3205 Partie 1 (Installation et câblage d'entrée)
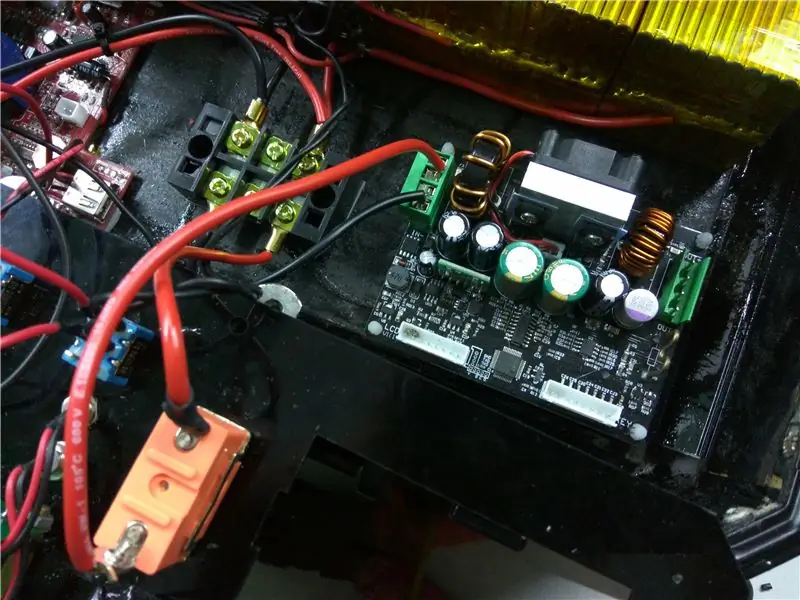
J'ai percé 2 trous de 3 mm à travers la plaque inférieure en diagonale, puis j'ai installé le module DPH3205 avec des vis M3 de 8 mm qui traversent ces trous. J'ai câblé l'entrée avec des fils épais 16 AWG. Le négatif va directement au module. Le positif va d'abord à un interrupteur puis au module. J'ai soudé des cosses de câble à l'autre extrémité qui seront connectées à la borne principale.
Étape 13: Le module DPH3205, partie 2 (montage de l'écran et câblage de sortie)
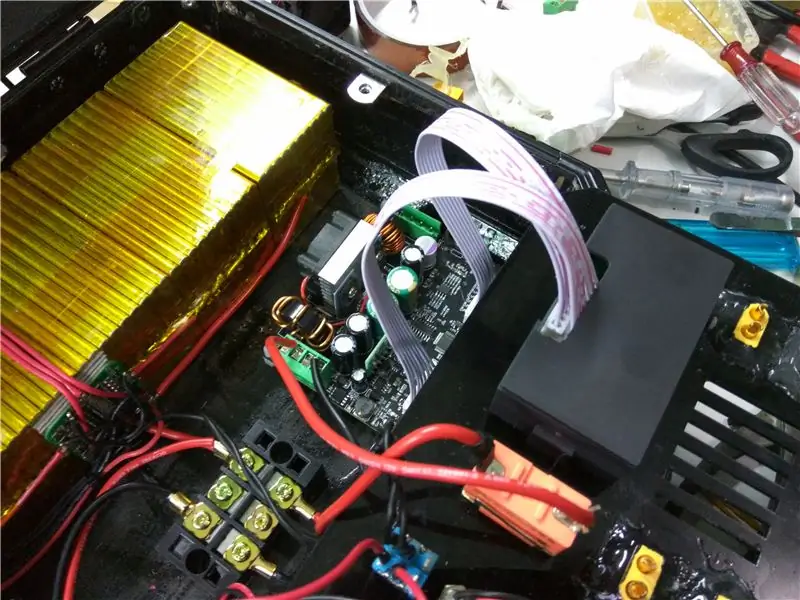
J'ai monté l'écran sur le panneau avant et connecté les fils. Ensuite, j'ai monté les connecteurs XT60 sur le tableau de bord à l'aide d'époxy en deux parties et j'ai câblé ces connecteurs en parallèle. Ensuite, le fil va à la sortie du module.
Étape 14: Les E/S auxiliaires (montage et câblage)
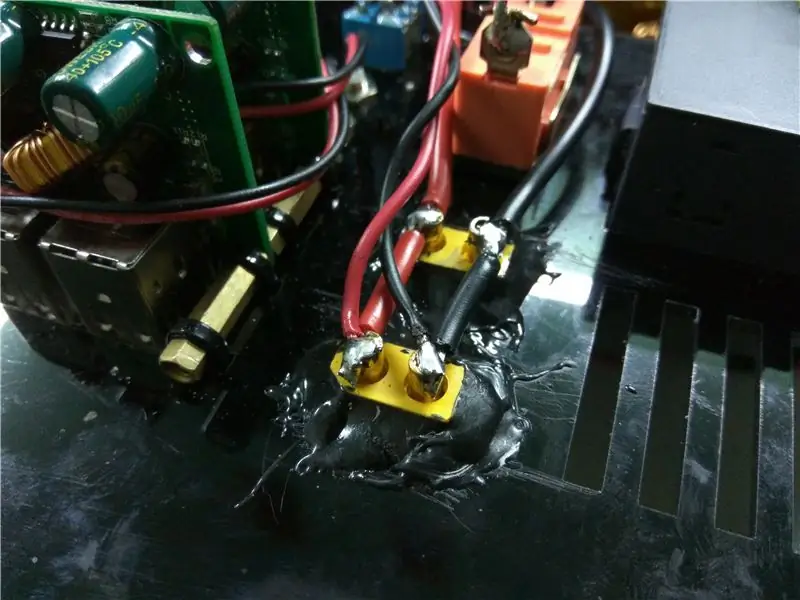
J'ai monté 2 connecteurs XT60 avec de l'époxy en 2 parties et j'ai soudé les connecteurs en parallèle avec des fils épais 16 AWG. J'ai soudé des cosses de câble à l'autre extrémité qui vont à la borne principale. Le fil du module USB va également ici.
Étape 15: CQ (inspection rapide)
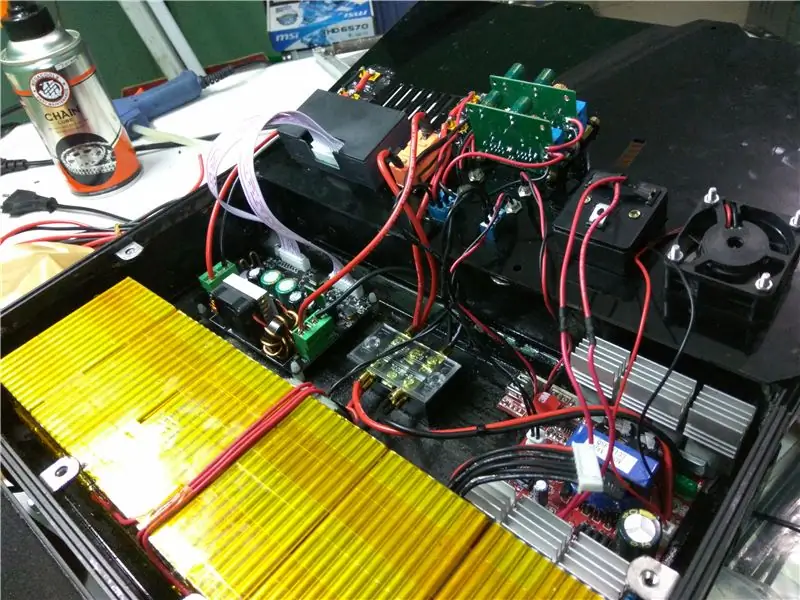
Assurez-vous qu'il n'y a rien de cliquetis à l'intérieur. Les éléments conducteurs indésirables peuvent provoquer un court-circuit.
Étape 16: Finition et test
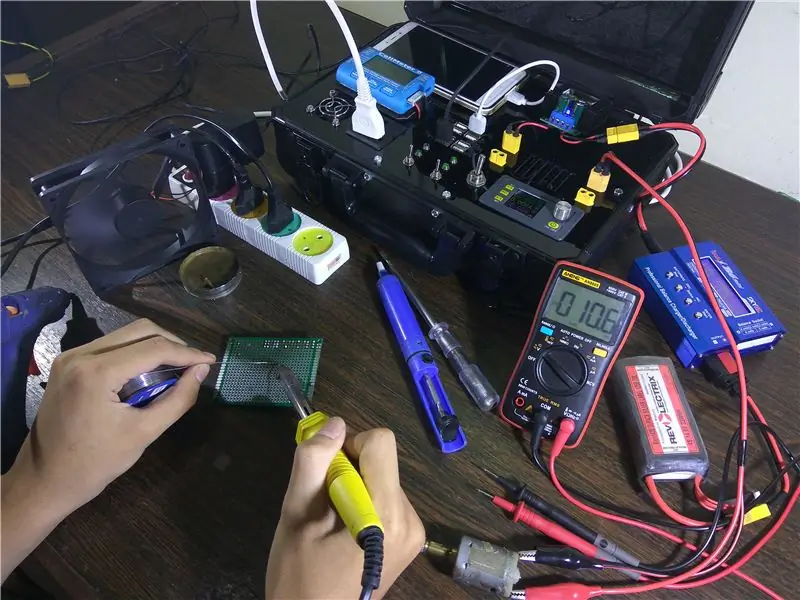
J'ai fermé le couvercle, vissé les boulons et le tour est joué ! J'ai testé toutes les fonctions et tout fonctionne comme je l'espérais. Certainement très utile pour moi. Cela m'a coûté un peu plus de 150 $ (matériel uniquement, échecs non compris), ce qui est très bon marché pour quelque chose comme ça. Le processus d'assemblage a pris environ 10 heures, mais la planification et la recherche ont pris environ 3 mois.
Même si j'ai fait pas mal de recherches avant de construire mon alimentation, mon alimentation a encore de nombreux défauts. Je ne suis pas vraiment satisfait du résultat. À l'avenir, je construirai le Listrik V2.0 avec beaucoup d'améliorations. Je ne veux pas gâcher tout le plan, mais en voici une partie:
- Passez aux cellules 18650 haute capacité
- Capacité légèrement supérieure
- Puissance de sortie beaucoup plus élevée
- De bien meilleures caractéristiques de sécurité
- Chargeur MPPT interne
- Meilleur choix des matériaux
- Automatisation Arduino
- Indicateur de paramètre dédié (capacité de la batterie, puissance consommée, température, etc.)
- Sortie DC contrôlée par l'application et bien d'autres que je ne vous dirai pas pour l'instant;-)
Étape 17: Mises à jour
Mise à jour n°1: j'ai ajouté un interrupteur de commande manuelle pour le ventilateur de refroidissement afin que je puisse l'allumer manuellement si je veux utiliser l'alimentation à pleine charge afin que les pièces à l'intérieur restent froides.
Mise à jour n°2: Le BMS a pris feu, j'ai donc refait tout le système de batterie avec un meilleur. Le nouveau dispose d'une configuration 7S8P au lieu de 6S10P. Un peu moins de capacité mais une meilleure dissipation de la chaleur. Chaque groupe est désormais espacé pour une meilleure sécurité et un meilleur refroidissement. Tension de charge de 4,1 V/cellule au lieu de 4,2 V/cellule pour une meilleure longévité.
Conseillé:
Une alimentation Sleak Bench à partir d'un bloc d'alimentation PC : 8 étapes (avec photos)
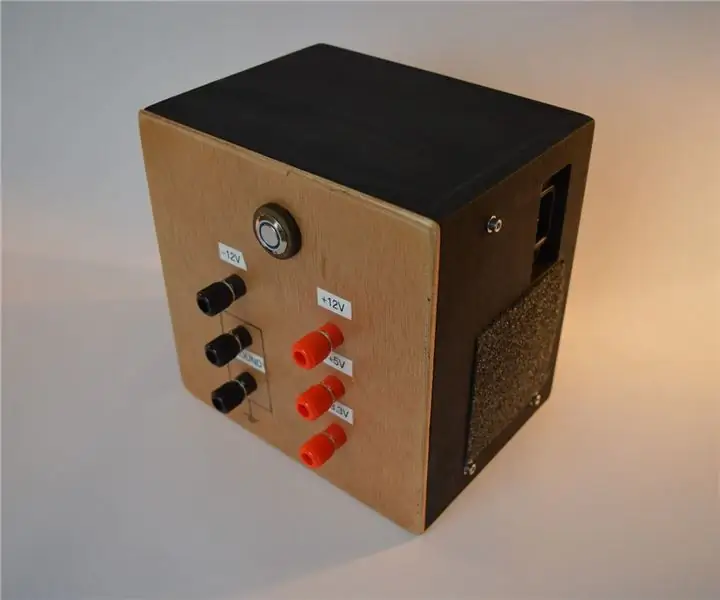
A Sleak Bench Power Supply From PC PSU: Update: La raison pour laquelle je n'ai pas eu à utiliser de résistance pour arrêter la mise hors tension automatique du PSU est que (je pense…) la led dans le commutateur que j'ai utilisé consomme suffisamment de courant pour empêcher le Arrêt du bloc d'alimentation. J'avais donc besoin d'une alimentation de table et j'ai décidé de faire un
Alimentation ATX secrète pour alimentation de banc : 7 étapes (avec photos)
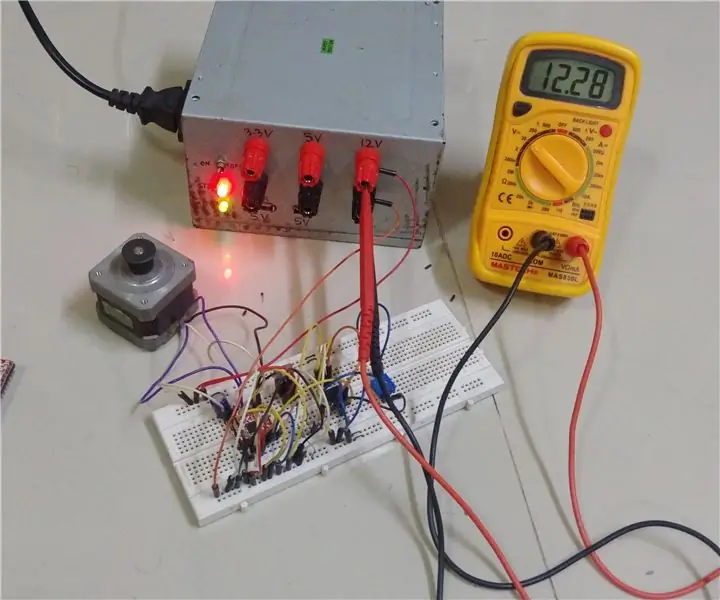
Alimentation ATX secrète pour alimentation de banc : Une alimentation de banc est nécessaire lorsque vous travaillez avec de l'électronique, mais une alimentation de laboratoire disponible dans le commerce peut être très coûteuse pour tout débutant qui souhaite explorer et apprendre l'électronique. Mais il existe une alternative bon marché et fiable. Par conve
De la barre d'alimentation à la banque d'alimentation : 7 étapes (avec photos)
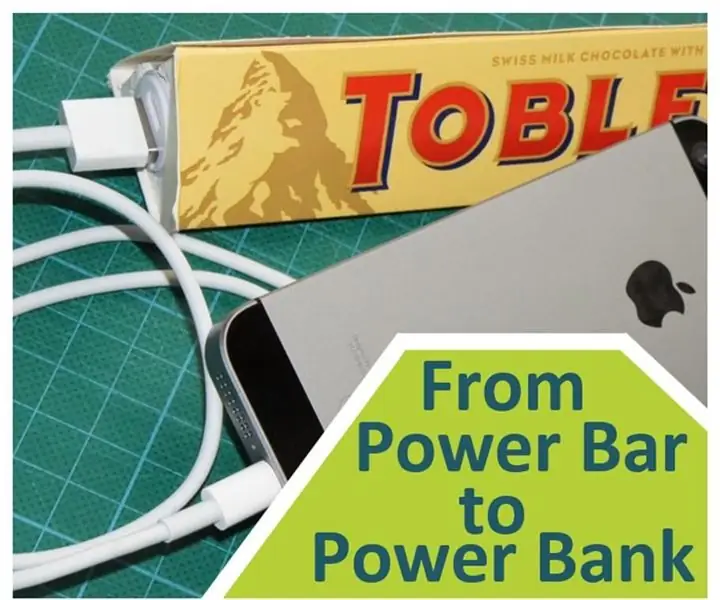
De la barre d'alimentation à la banque d'alimentation : ce Instructable vous montre comment transformer ma barre d'alimentation préférée (Toblerone) en une banque d'alimentation. Ma consommation de chocolat est énorme, j'ai donc toujours des paquets de barres de chocolat qui traînent, m'inspirant à faire quelque chose de créatif. Alors, j'ai fini par
Comment faire une alimentation de banc réglable à partir d'une ancienne alimentation de PC: 6 étapes (avec photos)
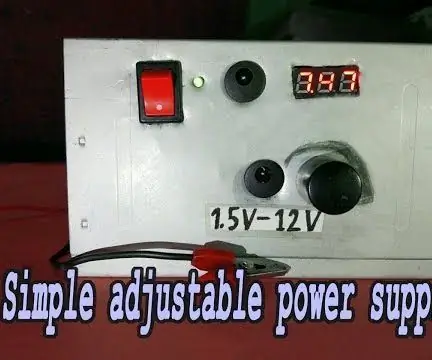
Comment faire une alimentation de banc réglable à partir d'une ancienne alimentation de PC : J'ai une vieille alimentation de PC qui traîne. J'ai donc décidé d'en faire une alimentation de banc réglable. Nous avons besoin d'une gamme différente de tensions pour alimenter ou vérifiez différents circuits ou projets électriques. Il est donc toujours bon d'avoir un réglage réglable
Éliminez l'alimentation en veille avec un interrupteur d'alimentation de bureau ! : 7 étapes (avec photos)
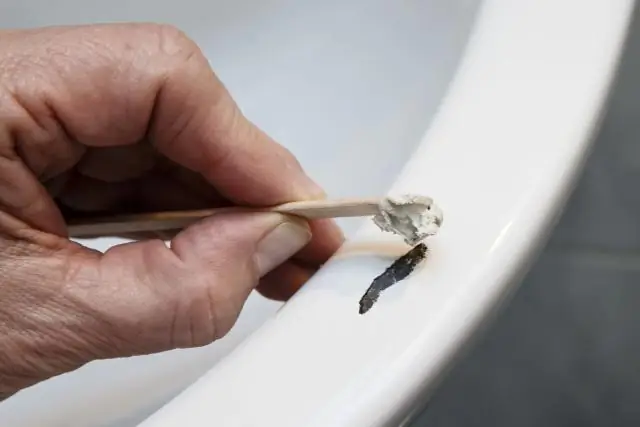
Éliminez l'alimentation en veille avec un interrupteur d'alimentation de bureau ! : Nous savons tous que cela se produit. Même lorsque vos appareils (TV, ordinateur, haut-parleurs, disques durs externes, moniteurs, etc.) sont éteints "OFF", ils sont toujours allumés, en mode veille, gaspillant de l'énergie. Certains téléviseurs à écran plasma utilisent en fait plus de puissance dans