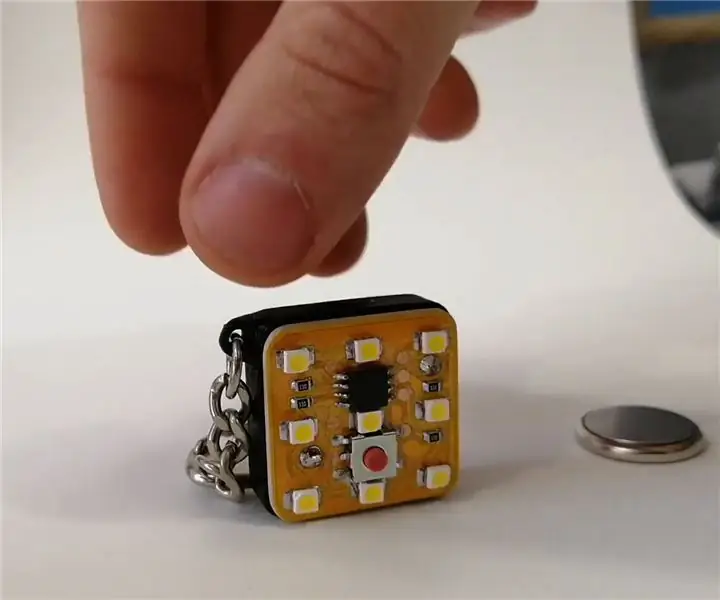
Table des matières:
- Étape 1: Matériaux, fournitures et outils
- Étape 2: préparez tous les autocollants
- Étape 3: graver le revêtement de cuivre
- Étape 4: Coupez et poncez les dés
- Étape 5: Application des autocollants Kapton Soldermask
- Étape 6: Assembler les dés: Application de la pâte à souder
- Étape 7: Soudage par remplissage et par refusion
- Étape 8: Imprimez en 3D les étuis porte-clés
- Étape 9: Créer un gabarit de programmation
- Étape 10: Programmation des dés
2025 Auteur: John Day | [email protected]. Dernière modifié: 2025-01-23 14:45
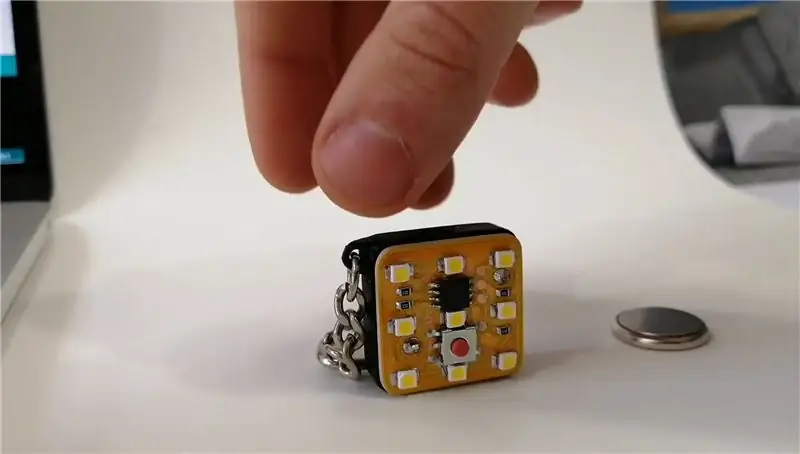
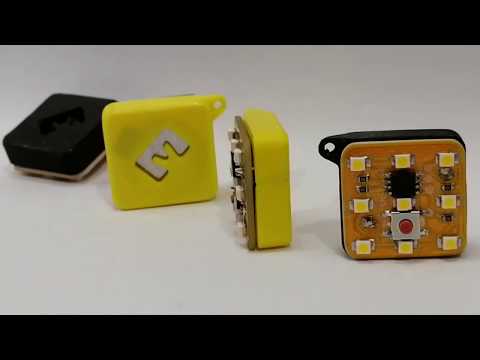
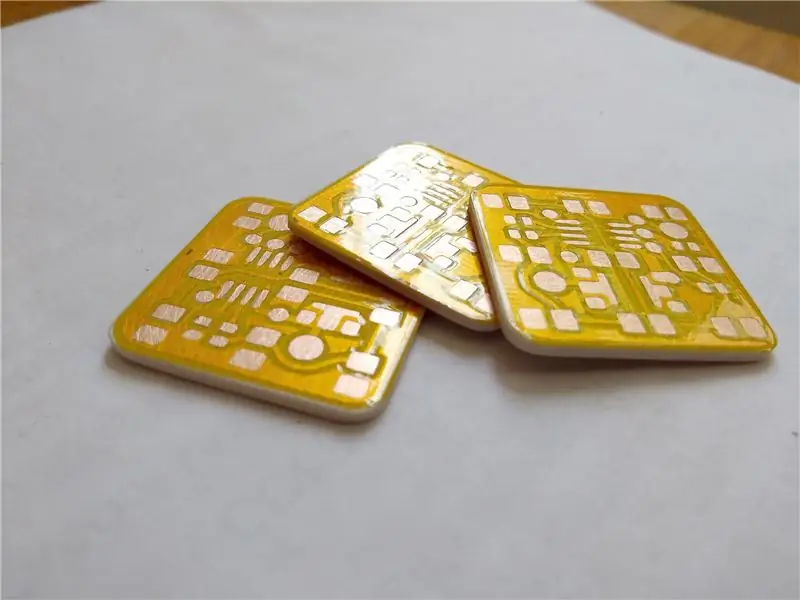
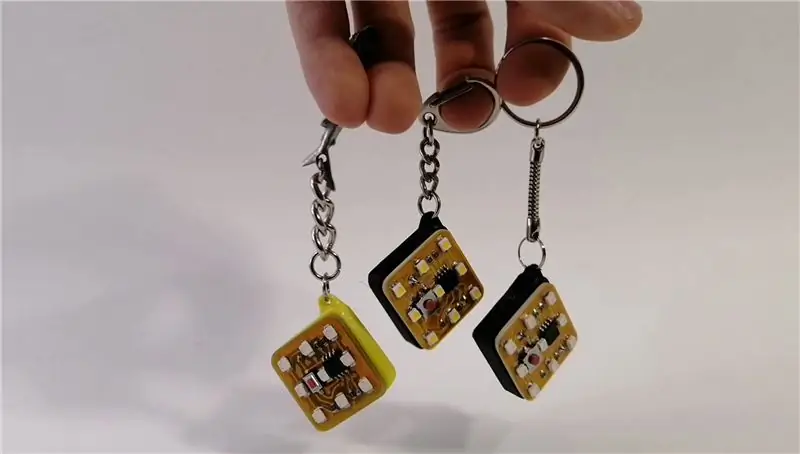
Cette instructable consiste en un guide étape par étape documentant une méthode de fabrication de circuits imprimés de qualité professionnelle à la maison grâce à l'utilisation d'un coupe-vinyle, de manière fiable, simple et efficace. Cette méthode permet de produire à domicile des PCB homogènes et de haute qualité avec peu de matériaux courants et dans un laps de temps très court. Avec tous les fichiers prêts, l'ensemble du processus peut être accompli en quelques heures.
Sujet du guide, tinyDice:
Pour les besoins de ce guide, le processus sera illustré avec la production d'un lot de 3 tinyDice, une puce électronique basée sur le microcontrôleur atTiny85 avec le logiciel charlieplexing, qui permet le contrôle de 9 LED avec seulement 4 broches et 4 résistances. Il s'agit d'une version améliorée de mon tinyDice original (2014), et tous les fichiers sources requis pour ce Instructable sont disponibles en téléchargement sous forme de package compressé à l'étape des fournitures.
Origine de la méthode:
En tant que passionné d'électronique, j'ai eu ma juste part d'expérience dans la fabrication de circuits imprimés dans le passé, mais la plupart des méthodes domestiques sont soit excessivement peu fiables, comme la méthode de transfert de toner, soit excessivement complexes et laborieuses, comme la méthode du routeur CNC ou l'UV méthode photoresist (que j'ai couverte dans le passé sur le tinyDice d'origine). De plus, la qualité finale des produits a tendance à être plutôt médiocre, surtout si vous essayez de mettre en œuvre des masques de soudure UV.
De ces expériences insatisfaisantes, j'ai décidé d'explorer des méthodes alternatives pour créer des PCB à la maison. Comme j'ai récemment commencé à expérimenter avec un découpeur de vinyle de bureau, il m'est venu à l'esprit qu'un tampon en vinyle pouvait constituer un masque excellent et fiable pour la gravure de circuits imprimés. Lors des premières recherches en ligne, je n'ai trouvé aucune référence de personnes utilisant des tampons en vinyle pour fabriquer des PCB, ce qui m'a surpris car cela semble très plausible. Cela m'a motivé à expérimenter le processus et à découvrir s'il pouvait fonctionner de manière fiable et efficace pour transférer les traces de PCB de l'ordinateur au cuivre.
Développement des processus:
Faire des traces de cuivre propres et cohérentes dans un circuit imprimé domestique est en soi un exploit, mais pour que les circuits imprimés fonctionnent correctement et durent longtemps, ils nécessitent une sorte de masque de soudure, qui empêche les ponts de soudure indésirables et protège les traces de cuivre de la corrosion. Traditionnellement, le masque de soudure utilisé se présente sous la forme d'une résine durcissable aux UV, ce qui en pratique est assez difficile à travailler.
À l'origine, j'avais l'intention d'utiliser indirectement des malades en vinyle comme masque pour durcir le masque de soudure UV. Cependant, à plusieurs reprises, je n'ai pas pu faire durcir le masque de soudure UV de manière fiable uniquement aux endroits prévus, et je n'ai jamais été capable de faire une couche suffisamment fine et uniforme, ce qui a finalement abouti à un tas de cartes en ruine. J'ai donc abandonné cette idée et il m'est venu à l'esprit que peut-être une sorte de tampon pourrait également être utilisé directement comme masque de soudure, bien que ce ne soit certainement pas du vinyle, car il ne résisterait pas à la chaleur de la soudure par refusion.
Dans cet esprit, je me suis tourné vers le ruban Kapton, qui est auto-adhésif, mince et promet de résister à des températures suffisamment élevées pour le soudage. Le ruban Kapton est vendu en rouleaux, mais il m'est venu à l'esprit que s'il était appliqué sur le support de vinyle conventionnel, il pourrait être coupé directement sur le coupe-vinyle et utilisé directement comme tampon. Dès le premier essai, il était évident que le ruban Kapton se comportait de manière assez prometteuse sur le coupe-vinyle, bien que toutes les coupes qui passaient sur de minuscules bulles aient été irrégulières ou incomplètes. support en vinyle sans laisser l'air se coincer en dessous. Cela s'est d'abord avéré assez délicat, car Kapton est excessivement fin et collant, mais en essayant de le poser à l'aide d'une carte en plastique standard, j'ai réalisé que cela pouvait être fait parfaitement et facilement de cette manière.
Grâce à ces essais itératifs, j'ai également observé certaines des limites pratiques du processus, qui sont principalement dues au fait que le masque de cuivre était à l'origine un tampon. Ces limitations ont évolué vers un ensemble de directives de conception pour rendre ce processus fiable.
Étape 1: Matériaux, fournitures et outils
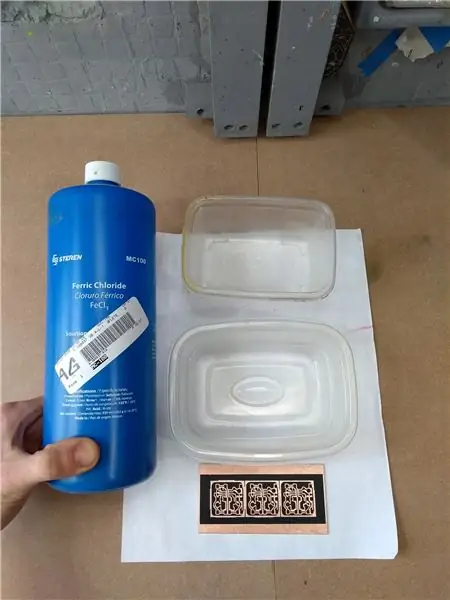
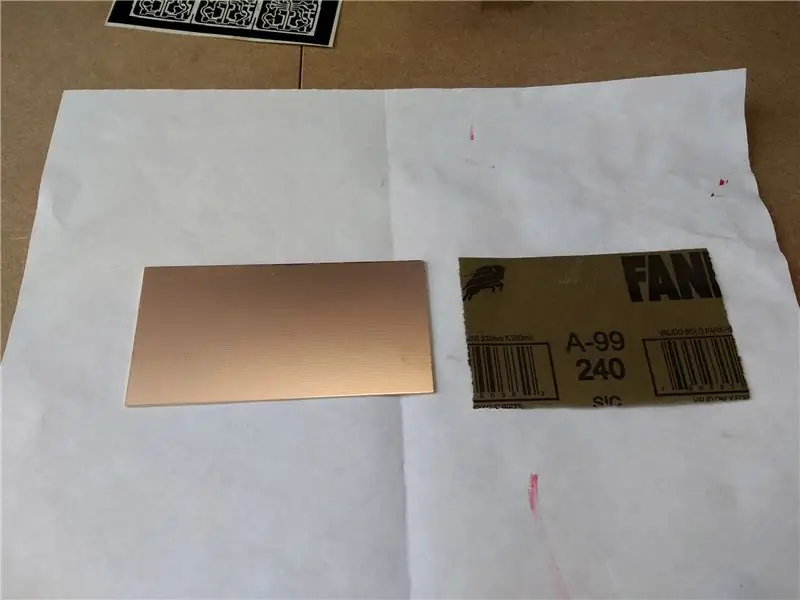
Matériaux:
- PCB vierge de 5 x 10 cm
- Vinyle autocollant 10 x 15 cm
- Ruban Kapton de 50 mm de large
- Film de transfert vinyle 10 x 15 cm
Fournitures:
- Agent de gravure au chlorure ferrique
- Alcool isopropylique
- Pâte à braser
- Filament PETG (pour l'étui porte-clés)
Outils:
- coupeur de vinyle de bureau (j'utilise le Silhouette Cameo 3, mais n'importe quelle machine de base fonctionnera)
- Station de reprise à air chaud (pas indispensable mais utile)
- fer à souder
- carte plastique (ancienne pièce d'identité ou autre)
- USBtinyISP ou Arduino comme ISP
- cutter acrylique manuel (peut être fait maison à partir d'une section de vieille lame de scie à métaux)
- Papier de verre grain 220 et 400
- Imprimante 3D (en option, uniquement pour la fabrication de l'étui porte-clés)
Logiciel:
- Silhouette Studio (ou équivalent pour les autres marques de découpeuses de vinyle)
- EAGLE CAD (non requis si vous n'avez pas l'intention de modifier la conception)
- Photoshop ou tout autre éditeur d'images (non requis si vous n'avez pas l'intention de modifier le design)
- Arduino IDE + atTinyCore
- AVRDUDESS
- Slic3r ou tout autre logiciel d'impression 3D.
-
Pack de ressources tinyDice (disponible en téléchargement à cette étape sous forme de fichier RAR)
Composants:
pour chaque tinyDice85:
- 9x 3528 LED SMD (n'importe quelle couleur, tout de même recommandé)
- 1x attiny85 (SOIC)
- 4 résistances 33 ohm 0805 (la valeur exacte n'est pas critique, utilisez une valeur similaire mais tout de même !)
- 1x bouton poussoir CMS
- 1x pince à piles CR20XX
- 1x pile CR2032
Pour le gabarit de programmation:
- 6x épingles pogo
- 1x connecteur mâle 2x3 (pour FAI)
- 1x connecteur mâle 2x1 (pour source VCC externe)
- 1x régulateur AMS1117 3.3v LDO (SOT-23)
Étape 2: préparez tous les autocollants
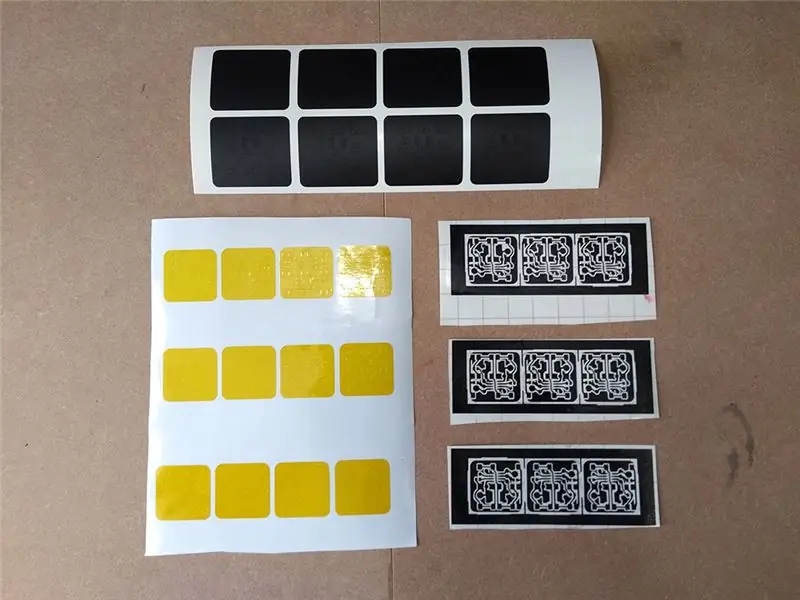
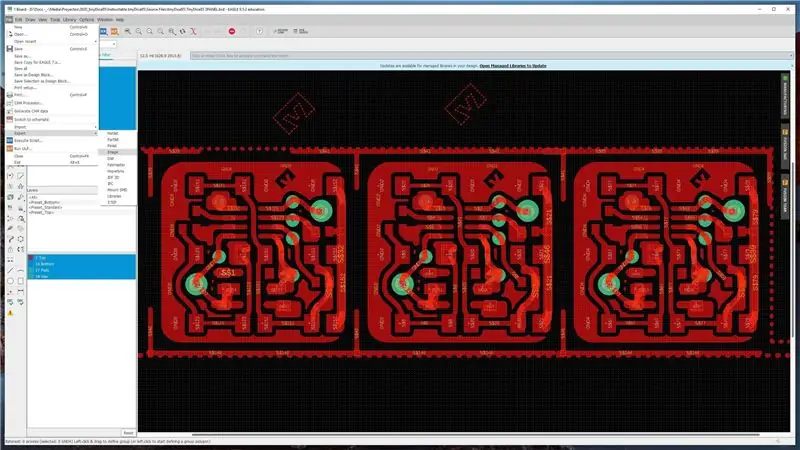
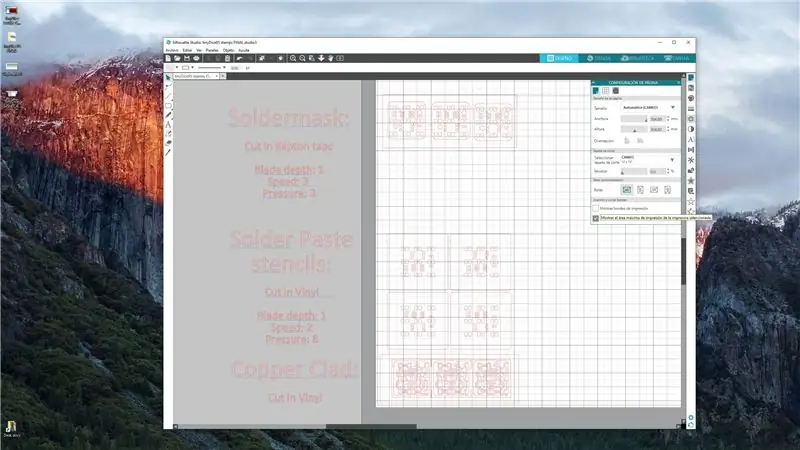
Pour ce processus de fabrication de PCB à la maison, les autocollants interviennent à trois étapes; En tant que masque pour graver la gaine de cuivre, en tant que masque de soudure pour protéger les traces et contraindre la soudure, et en tant que pochoir pour appliquer de la pâte à souder sur les pastilles. Afin d'optimiser au maximum le processus, tous les autocollants peuvent être préparés en une seule assise.
Préparation des fichiers à découper:
Si vous n'avez pas l'intention de modifier le design, vous pouvez directement utiliser les images préparées ou le fichier Silhouette Studio avec tous les autocollants. Si vous utilisez un autre motif, procédez comme suit pour préparer le fichier à découper:
Comme la plupart des logiciels de découpe de vinyle gratuits fonctionnent avec des images, nous devons exporter le design d'EAGLE en tant qu'image haute résolution. Pour cela, masquez d'abord tout le calque sauf TOP et VIAS, puis exportez le panneau sous forme d'image en MONOCHROME et au moins 1500 dpi. Ensuite, répétez le processus mais uniquement avec le calque Tstop, afin d'obtenir uniquement les pads.
Une fois les images exportées, il est conseillé de faire un peu de nettoyage dans photoshop pour augmenter la fiabilité du processus. Pour l'image plaquée de cuivre, cela consiste à effacer toutes les petites zones de cuivre isolées ou à les connecter à des zones plus grandes, à effacer le centre de tous les trous traversants et à augmenter le jeu autour des thermiques. Pour l'image des pastilles, il faut les enfiler sur une forme noire qui déborde un peu l'ensemble plaqué de cuivre.
Ensuite, importez les images dans le logiciel de découpe de vinyle, tracez-les et redimensionnez-les à une taille de 100 x 100 mm. L'un des avantages de la panélisation des PCB est que vous disposez d'une référence cohérente pour les mettre à l'échelle correctement, quelle que soit la résolution.
Préparation du ruban Kapton pour la découpe:
Le ruban Kapton est un excellent matériau, cependant pour l'utiliser comme autocollant, nous devons d'abord le placer sur un support plat. Pour cela, nous utiliserons le support du ruban de transfert en vinyle, alors décollez le pâté et mettez-le temporairement de côté, en prenant soin de le garder propre. Ensuite, déroulez un segment de ruban adhésif et appliquez-le soigneusement sur le support en papier ciré en utilisant une carte en plastique comme raclette pour vous assurer qu'aucune bulle ne reste piégée en dessous. Je recommande de préparer plus que ce que vous prévoyez d'utiliser, car certains autocollants peuvent ne pas sortir parfaitement.
Découpe des autocollants:
Une fois que vous avez tracé et mis à l'échelle tous les autocollants dans le logiciel de découpe de vinyle, placez le matériau vinyle autocollant sur un coin du tapis de découpe et placez le ruban Kapton sur un autre coin.
Ensuite, sur le logiciel, placez uniquement les motifs de pochoir en cuivre et en pâte à souder sur la zone correspondant au vinyle et définissez les paramètres de découpe sur: Vitesse 3, Profondeur de lame 1, Pression 8. Envoyez le travail pour la découpe et laissez la machine faire c'est chose.
Enfin, écartez les dessins précédemment utilisés et placez uniquement le dessin du masque de soudure sur la zone correspondant au ruban Kapton. Réglez les paramètres de coupe sur: Vitesse 1, Profondeur de lame 1, Pression 3. Continuez à envoyer le travail à la machine et une fois terminé, retirez soigneusement le vinyle autocollant et les matériaux Kapton du tapis de coupe. Attention à ne pas faire de plis pointus en les décollant.
Désherber les autocollants:
Afin de transférer les autocollants en vinyle sur le circuit imprimé, nous devons utiliser un film de transfert en vinyle pour garantir que toutes les régions sont transférées en place. Pour ne pouvoir transférer que les segments de tampon prévus, il faut supprimer toutes les zones indésirables avant d'appliquer le film de transfert. Pour cela, utilisez un cutter et soulevez soigneusement un coin de la zone non désirée. Poussez le cutter en dessous et appuyez sur le vinyle sur la lame pour le faire adhérer. Ensuite, retirez le cutter et l'excédent devrait commencer à se décoller. Selon la conception, toutes les zones indésirables peuvent sortir en une seule pièce. Une fois désherbé, placez le film de transfert UNIQUEMENT sur les autocollants recouverts de cuivre et jetez tout l'excédent. À ce stade, les autocollants en vinyle sont prêts à l'emploi. Les autocollants Kapton tape sont d'une seule pièce, ils peuvent donc être transférés directement sans le film de transfert.
Étape 3: graver le revêtement de cuivre
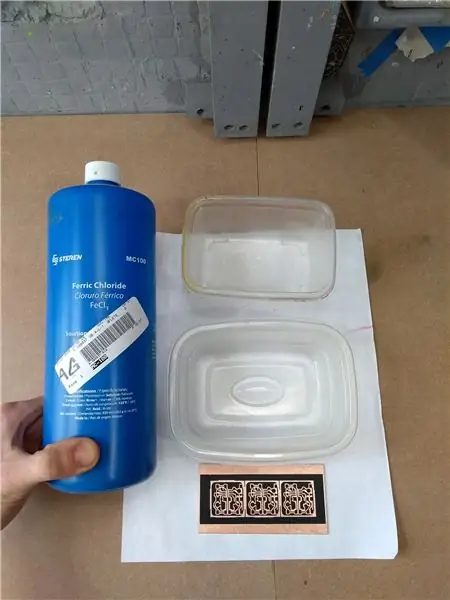
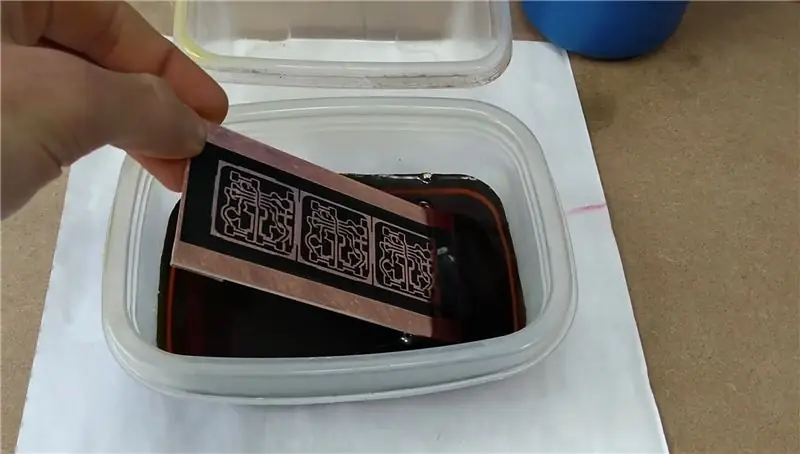
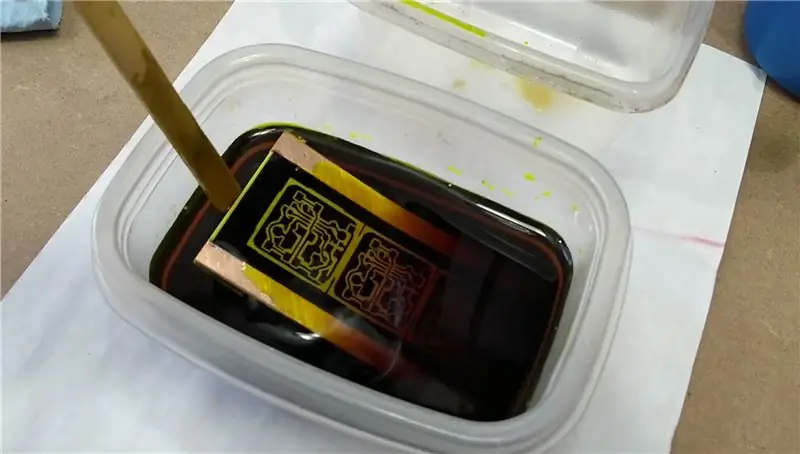
C'est l'étape la plus importante du processus, car la qualité des traces de cuivre déterminera le taux de réussite des produits finaux. Si cela est fait avec soin, il peut être à 100%.
Transfert de l'autocollant CLAD sur le cuivre:
Afin d'assurer des résultats propres et fiables, vous devez d'abord dégraisser le PCB vierge avec de l'alcool isopropylique. Si le flan est ancien, il est recommandé de poncer soigneusement la surface avec du papier de verre grain 320-400 en faisant de petits cercles tout au long de la planche.
Une fois parfaitement propre, il est temps de transférer l'autocollant sur le cuivre. Pour cela, décollez d'abord un coin du film transfert puis placez l'autocollant à l'envers sur une table propre. Ensuite, retirez lentement le papier du transfert en faisant un pli net et en tirant le long de la table. De cette façon, même les petits tampons doivent coller sur le transfert et ne pas rester sur le papier. Ne vous inquiétez pas si un ou deux pads restent derrière, vous pouvez les placer manuellement plus tard.
Ensuite, tenez le transfert de vinyle avec l'autocollant du bout de vos doigts (collez-les légèrement jusqu'au bord) et alignez lentement l'autocollant sur la planche avant de le poser. Une fois aligné, posez-le sur le cuivre et appuyez légèrement avec les doigts FORMER LE CENTRE, afin d'éviter les bulles piégées. Ensuite, utilisez une carte en plastique pour racler toute la surface afin d'assurer que le vinyle adhère fortement au cuivre. Procédez au décollement du film de transfert de vinyle du revêtement en cuivre de la même manière que vous avez décollé le support en papier et placez manuellement tous les tampons laissés derrière. Si l'autocollant ne couvre pas tout le blanc, vous pouvez couvrir toutes les zones restantes avec du ruban adhésif transparent pour éviter de graver l'excès de cuivre et de surutiliser vos fournitures.
Gravure de la gaine de cuivre:
Pour le processus de gravure, vous aurez besoin de 2 récipients rectangulaires de style Tupperware, d'un petit bâton en bois et de l'agent de gravure au chlorure ferrique.
La planche préparée avec le tampon CLAD est presque prête pour la gravure, mais il est très important de la nettoyer à nouveau avec de l'alcool isopropylique pour éliminer tout résidu du film de transfert et assurer une gravure uniforme et complète, sans qu'il ne reste de cuivre indésirable.
Pour préparer le chlorure ferrique pour la gravure, versez-le dans l'un des récipients jusqu'à environ la moitié et ajoutez environ 30 % d'eau en plus. À ce stade, la solution est prête pour la gravure, mais vous pouvez éventuellement la réchauffer au four à micro-ondes. pendant 15 secondes AVANT de placer dans le PCB afin d'accélérer le processus de gravure.
Enfin, placez la planche dans le chlorure ferrique et laissez-la couler. Le processus peut prendre un certain temps, mais il est important de revenir toutes les 10 à 15 minutes pour remuer la solution et vérifier la progression. Pour cela, utilisez simplement une petite chute de bois pour atteindre la planche et inclinez-la plusieurs fois dans et hors de la solution. Cela déplacera la solution pour s'assurer qu'elle réagit uniformément et vous permettra de voir quelle quantité de cuivre a été retirée. Continuez ainsi jusqu'à ce que vous ne voyiez plus de cuivre exposé, mais ne le laissez pas plus longtemps car l'agent de gravure peut commencer à percer sous l'autocollant et endommager les traces. En attendant, laissez le stick sur l'autre récipient pour éviter de tacher quoi que ce soit avec la solution de mordançage, car il est très sensible aux taches et dégage également une très forte odeur ferreuse.
Une fois cela fait, retirez la planche du décapant et rincez-la abondamment avec de l'eau et du savon abondants. Après cela, prenez un entonnoir ou fabriquez-en un à l'aide d'une feuille de plastique et fixez-le sur une bouteille en PP vide pour récupérer et stocker le décapant. Ne jetez JAMAIS le chlorure ferrique épuisé par le drain, réutilisez-le autant que possible et jetez-le en le laissant sécher, puis en l'éliminant comme un solide.
La gravure est l'étape la plus longue du processus. Si cela est fait avec du chlorure ferrique frais, cela peut être accompli en moins d'une heure, cependant, avec des fournitures réutilisées, cela peut prendre jusqu'à 4 heures, alors soyez patient et vérifiez périodiquement.
Étape 4: Coupez et poncez les dés
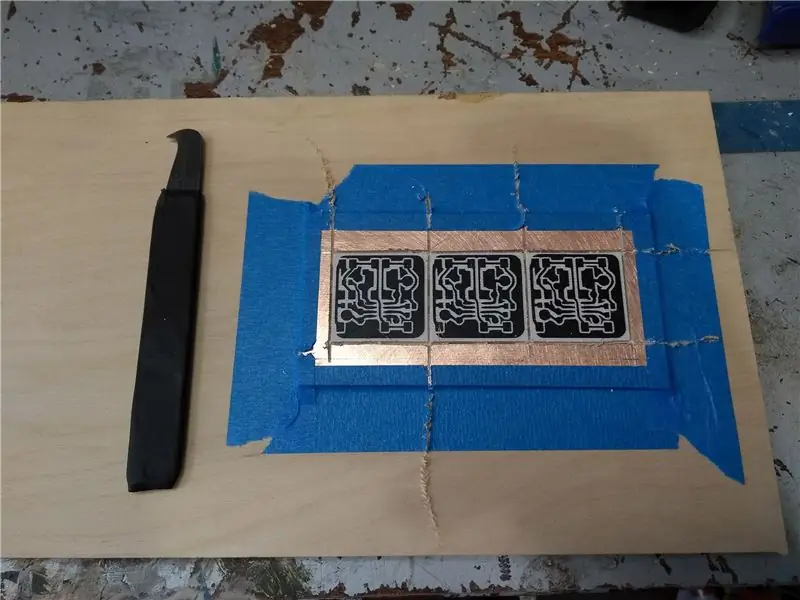
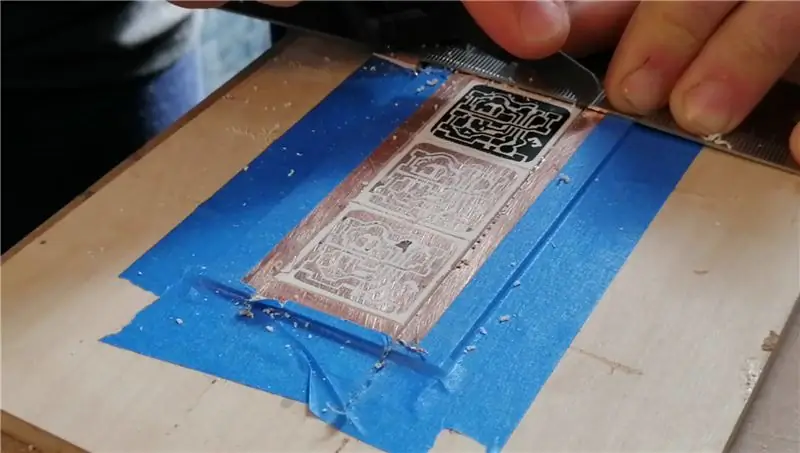
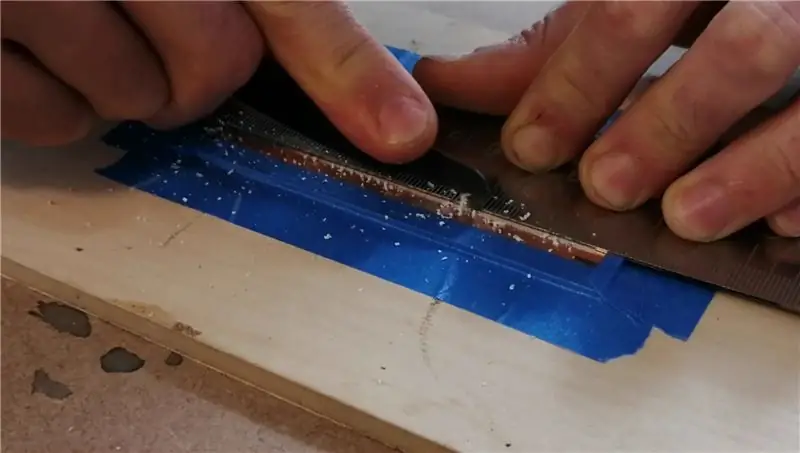
Un avantage du panneautage des circuits imprimés est que vous pouvez utiliser le panneau comme guide pour la découpe, et qu'il est plus facile de manipuler une carte plus grande. Afin de séparer les planches et de leur donner une finition correcte, il faut d'abord les découper et les poncer les bords et les coins.
La découpe du PCB ne peut pas être effectuée avec un cutter, des ciseaux ou des scies ordinaires, car ces processus échoueraient presque certainement ou endommageraient les cartes. Pour la coupe, nous utiliserons un simple outil à griffes qui racle progressivement les couches à chaque passage, en creusant une rainure tout au long. Ces lames sont vendues dans le commerce sous forme de couteaux acryliques, mais peuvent également être fabriquées à partir de lames de scie à métaux cassées. il est conseillé de réaffûter la lame tout au long du processus, car les panneaux en fibre de verre usent rapidement le tranchant. Il n'est pas nécessaire de couper tout le long, seulement la plupart du temps, et ensuite, il suffit de casser chaque morceau.
Après la coupe, les bords sont assez rugueux et inégaux, nous devons donc les poncer soigneusement d'abord avec du papier de verre grain 240 et ensuite avec un grain 400 pour plus de douceur. Assurez-vous également d'arrondir les coins en suivant la forme du revêtement en cuivre.
Enfin, utilisez un cutter pour décoller soigneusement les autocollants des planches. Cela peut être fait avant de couper, mais les autocollants aident à protéger le cuivre tout au long du processus de coupe.
Étape 5: Application des autocollants Kapton Soldermask
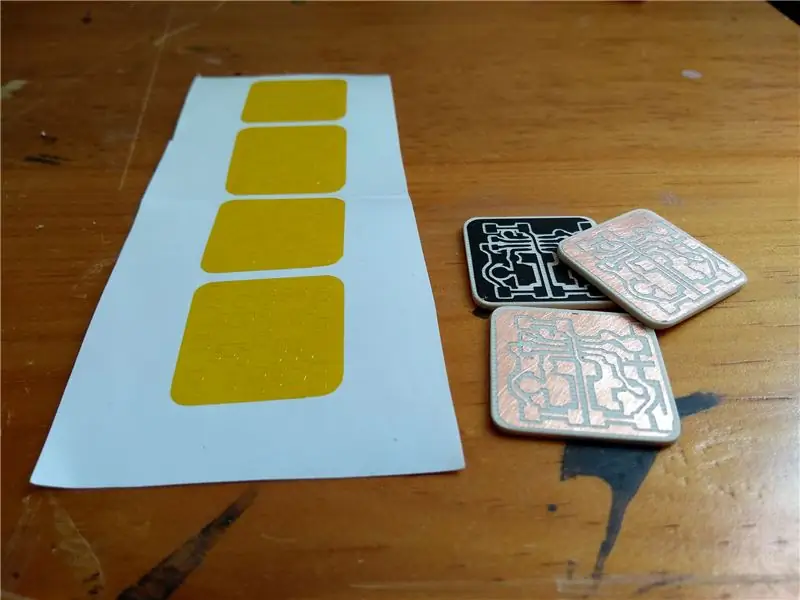
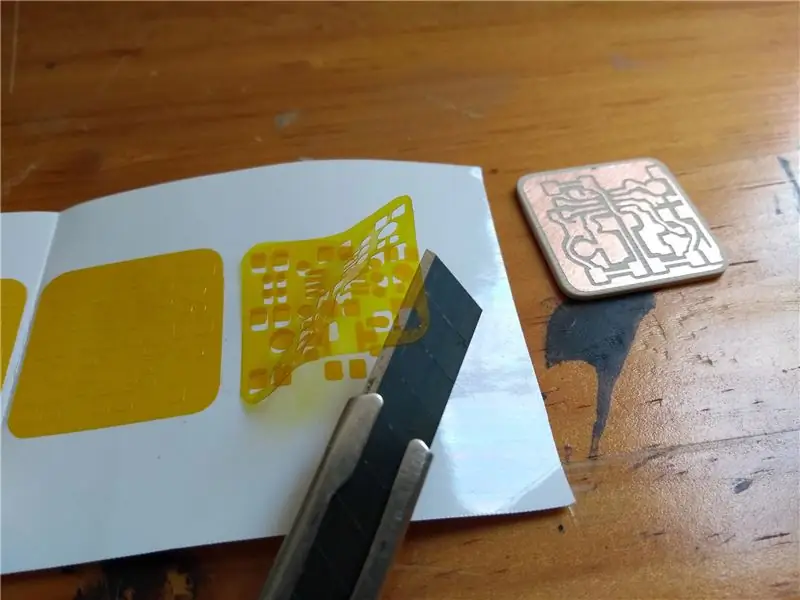
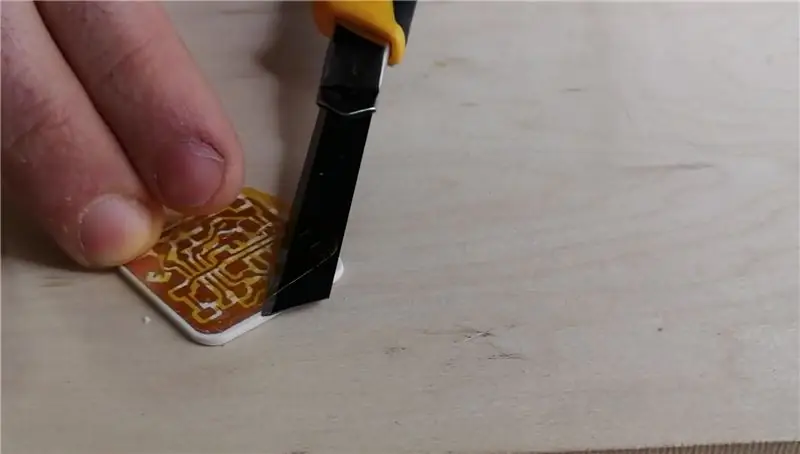
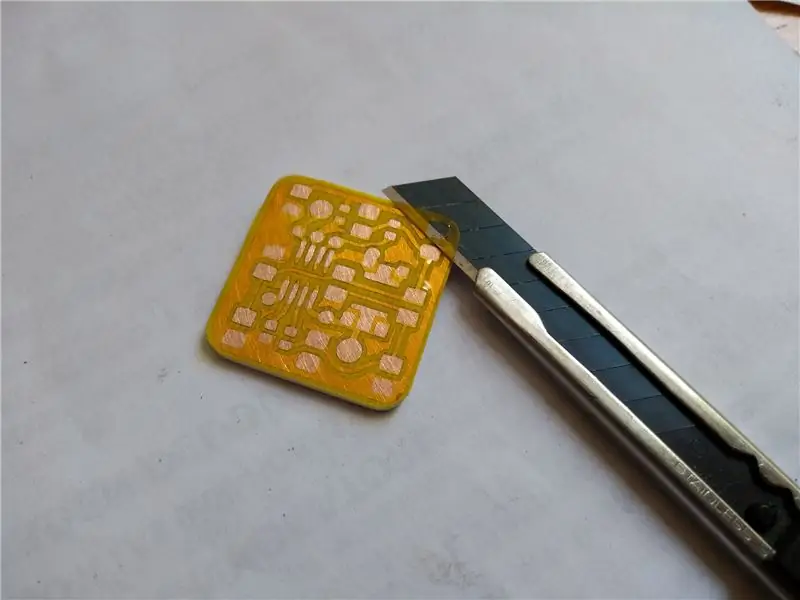
Maintenant, avec les cartes coupées, nous sommes presque prêts à assembler le circuit, cependant, afin de garantir que les traces de cuivre sont protégées à long terme et que la soudure ne reste que là où elle le devrait, nous avons besoin d'un masque de soudure, qui est fabriqué de manière conventionnelle à l'aide de résines UV.. Le processus traditionnel est assez toxique, désordonné et peu fiable, une alternative plus pratique est donc nécessaire pour la fabrication à domicile.
Dans ce cas, nous exploitons le ruban Kapton comme un masque de soudure en raison de sa résistance à haute température et de ses propriétés auto-adhésives. Pour transférer les autocollants sur les PCB, nous utiliserons à nouveau le cutter comme support. Avant de transférer les autocollants, nettoyez soigneusement les PCB avec de l'alcool à friction pour enlever toute graisse ou résidu du vinyle. Ensuite, retirez délicatement l'autocollant Kapton du papier support avec le cutter (voir image 2). Pour cela, soulevez d'abord un petit coin de l'autocollant avec le cutter et appuyez-le contre la lame pour le faire coller, puis retirez lentement le cutter du papier sans faire de pli sur le bord tranchant jusqu'à ce que tout l'autocollant se détache du papier et reste collé à la lame.
Enfin, il est important de s'assurer que l'autocollant est correctement aligné avec les tampons avant de le fixer en place, alors amenez-le doucement sur le PCB avec le cutter et brossez-le légèrement sur la carte plusieurs fois, cela le chargera d'électricité statique et fera il flotte en quelque sorte à la surface, ce qui vous permettra d'ajuster le placement avant de le presser en place. Si le tampon colle prématurément, décollez-le soigneusement du carton comme vous l'avez décollé du papier et répétez l'alignement. Une fois correctement aligné, appuyez fermement sur le PCB avec vos doigts et retirez soigneusement le cutter de l'autocollant pour terminer le réglage. Ensuite, nettoyez à nouveau les cartes avec de l'alcool et maintenant les PCB sont officiellement terminés. Ils peuvent être utilisés immédiatement ou stockés pour plus tard.
Étape 6: Assembler les dés: Application de la pâte à souder
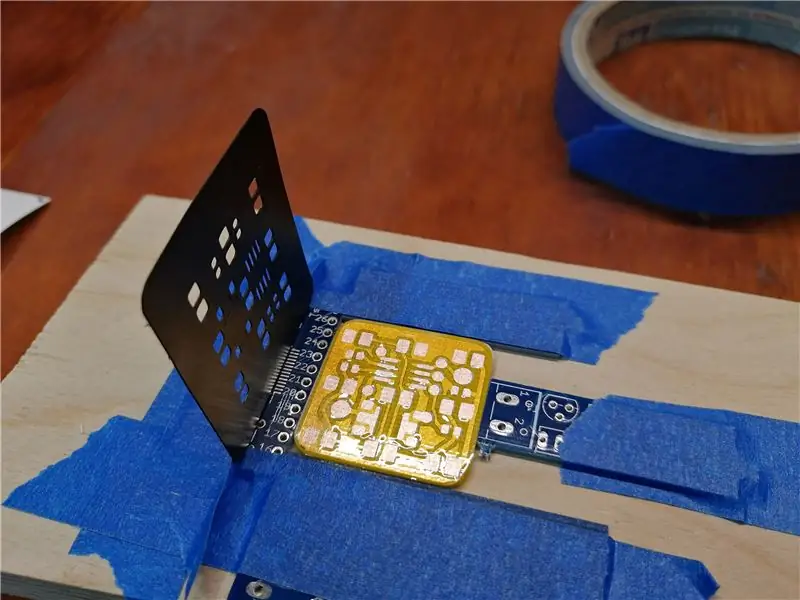
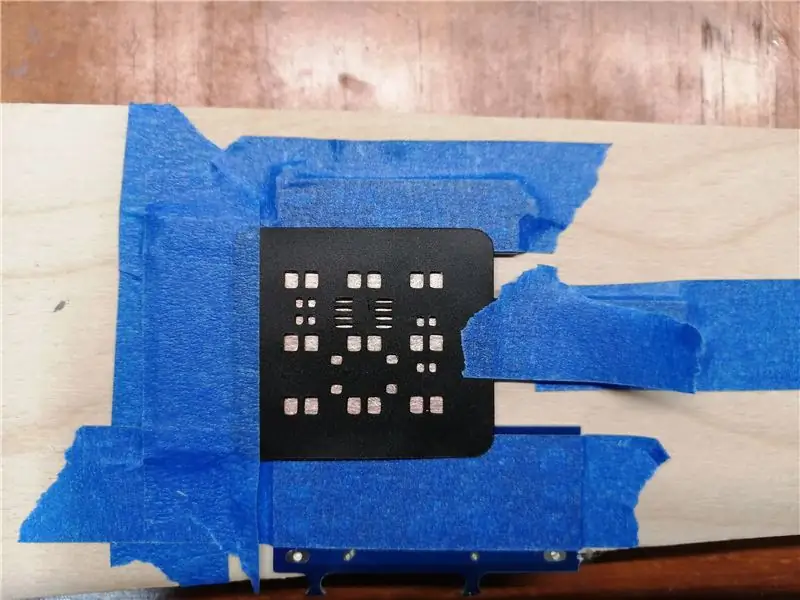
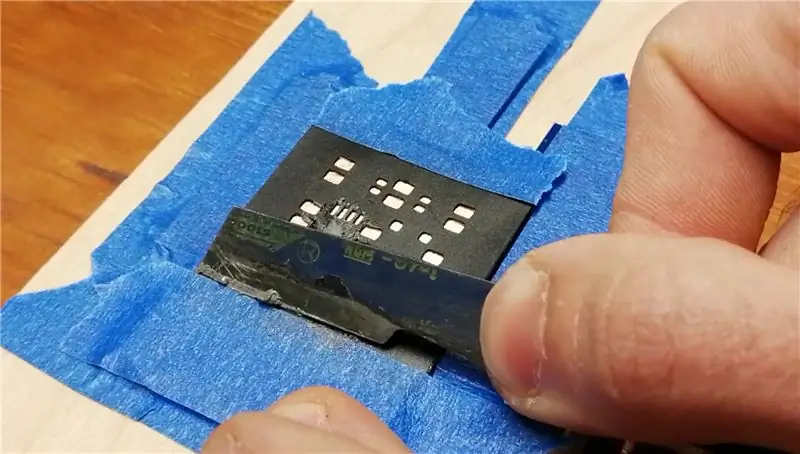
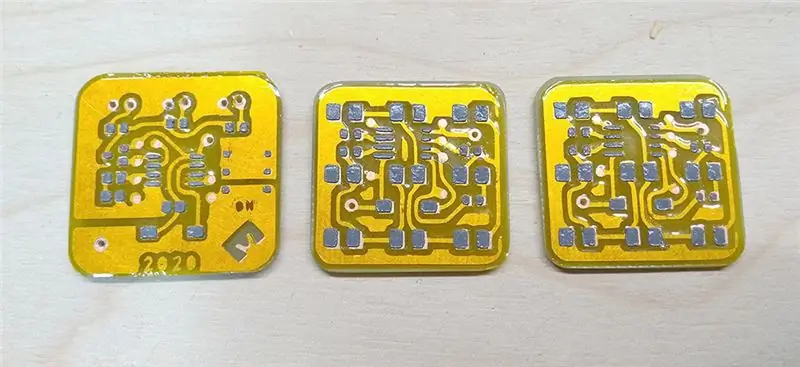
Un avantage des circuits CMS est qu'ils peuvent être soudés avec de la pâte de manière très fiable et rapide en utilisant un simple pochoir pour l'appliquer uniquement sur les pastilles, qui peuvent être réutilisées pour un nombre quelconque d'unités. Les pochoirs CMS conventionnels sont fabriqués en acier, ils sont donc assez coûteux et peu pratiques pour le prototypage, cependant, le pochoir peut également être composé d'autocollants en vinyle. Pour cela, nous utilisons à la fois l'original et une version miroir de l'autocollant pour créer un pochoir en plastique qui n'est pas auto-adhésif.
La pâte à souder contient beaucoup de flux, elle se réduit donc considérablement lors de la refusion. Ainsi, nous devons appliquer une couche suffisamment épaisse pour assurer que les joints se remplissent correctement de soudure. Afin de faire le pochoir de la bonne épaisseur, nous devons superposer 4 autocollants en vinyle ensemble. Faites-le soigneusement pour vous assurer que les trous sont parfaitement alignés tout au long.
Ensuite, construisez une petite bordure autour d'une planche à partir de déchets de circuits imprimés ou de tout autre matériau de la même épaisseur et fixez le pochoir en place par un seul côté pour servir de charnière, en assurant un bon alignement du pochoir sur les plaquettes (voir image 2).
Enfin, à l'aide de n'importe quel outil à bord droit, prenez de la pâte à souder et commencez à l'étaler sur le pochoir jusqu'à ce que tous les trous soient remplis, puis raclez le reste dans la bouteille avec le même outil. Ne touchez pas directement la pâte à souder, car elle contient du plomb, qu'il vaut mieux éviter. Ne vous inquiétez pas si vous le touchez, nettoyez-le simplement soigneusement.
Soulevez le pochoir et retirez la planche du gabarit. Répétez le processus pour toutes les planches que vous avez l'intention d'assembler. Les cartes sont maintenant prêtes à être remplies et soudées.
Étape 7: Soudage par remplissage et par refusion
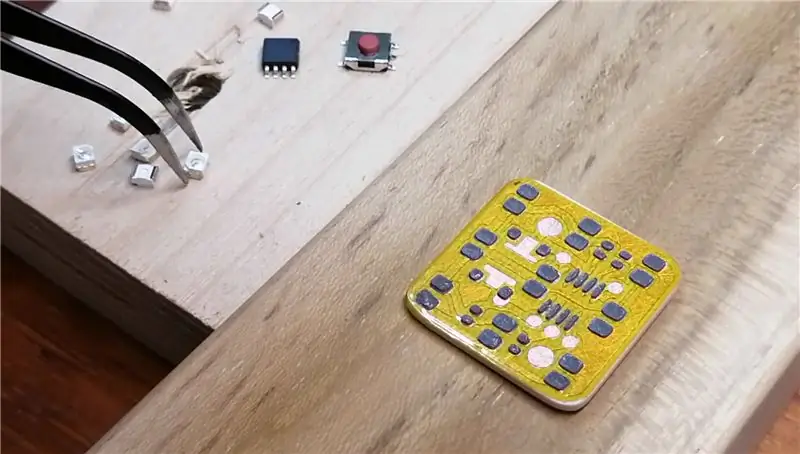
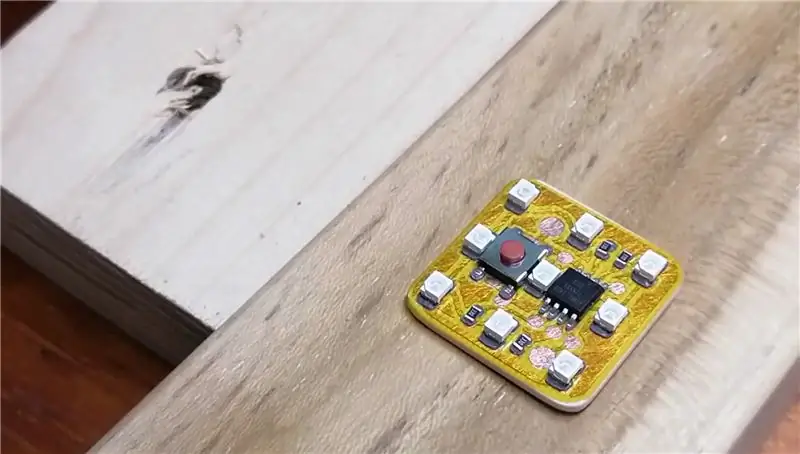
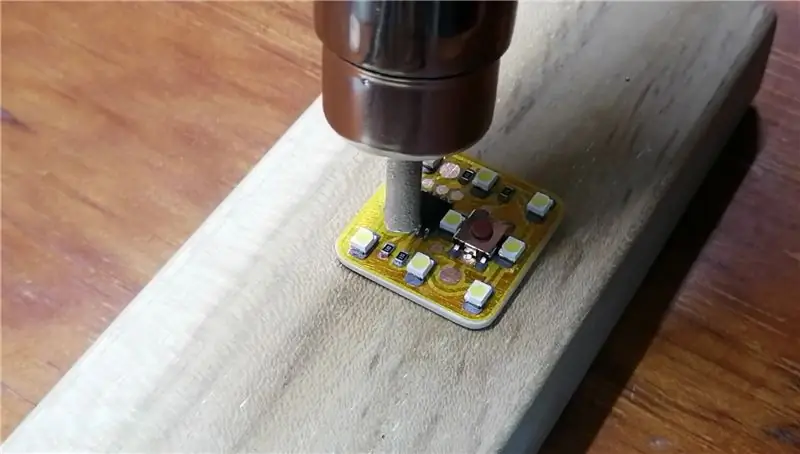
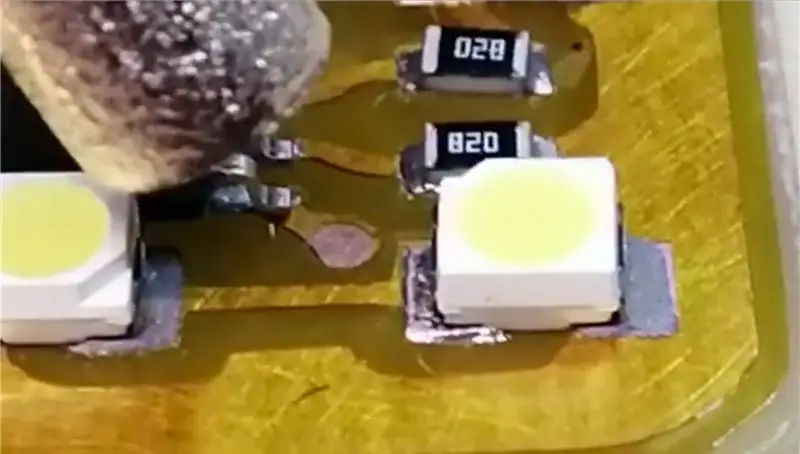
Avec la pâte à souder sur les cartes, il est temps de remplir tous les composants. Pour cela, utilisez des pincettes à pointe fine et placez soigneusement chaque composant sur ses coussinets, en veillant à l'orientation et à l'alignement corrects (voir image 2). Prenez votre temps pour le faire et corrigez les erreurs de placement. Une fois tous les composants placés, allumez l'outil de refusion d'air et commencez progressivement à préchauffer l'ensemble de la carte en la survolant en cercles (voir image 3). Ensuite, dirigez l'air chaud directement sur chaque coussin jusqu'à ce qu'ils refluent complètement (image 4). Lorsque vous avez terminé de refusionner, il est temps d'ajouter le clip de batterie. Pour cela, percez les centres des 2 plus gros coussinets ronds et placez le clip de la batterie sous la planche. Il est conseillé de coller également le clip de la batterie à la carte avec de l'époxy pour soulager toute contrainte des broches d'alimentation car le clip maintiendra la carte sur le boîtier. À ce stade, le PCB est entièrement assemblé et prêt pour la programmation.
Étape 8: Imprimez en 3D les étuis porte-clés
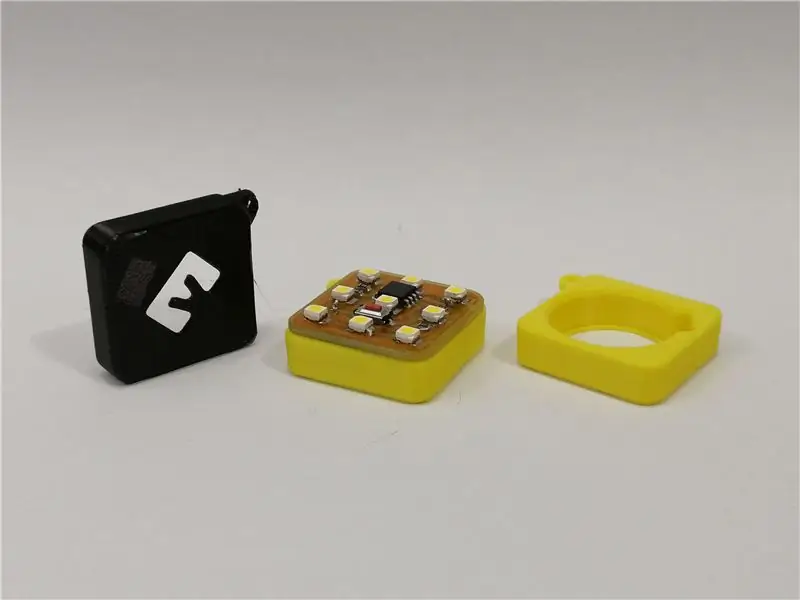

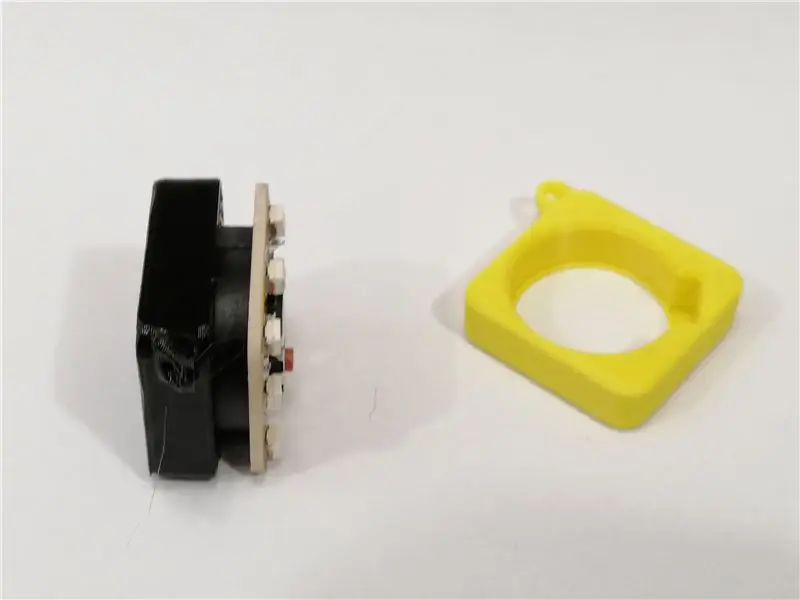
Les étuis imprimés en 3D sont facultatifs mais fortement recommandés, car ils ajoutent beaucoup de caractère à l'objet en le transformant en porte-clés, tout en protégeant le dé. Il est obligatoire de les imprimer en PETG afin d'assurer une durabilité élevée, car le PLA se brisera très probablement très rapidement. J'ai réalisé deux versions du boîtier, une avec un support creux pour retirer la batterie et une autre avec mon logo au dos, ce qui maintient la batterie en sécurité et cachée. Comme le circuit consomme très peu d'énergie, la batterie peut être piégée à l'intérieur du boîtier sans aucun probléme.
Pour assembler le boîtier, il suffit de presser le clip de la batterie sur l'impression 3D jusqu'à ce que la planche affleure le bord. En fonction de votre clip de batterie exact, vous devrez peut-être le poncer légèrement ou augmenter la hauteur du boîtier pour vous assurer qu'il s'adapte parfaitement, alors assurez-vous de vérifier avant de l'assembler. Si nécessaire, cependant, le boîtier peut être ouvert en tirant lentement la planche tout autour du bord.
Étape 9: Créer un gabarit de programmation
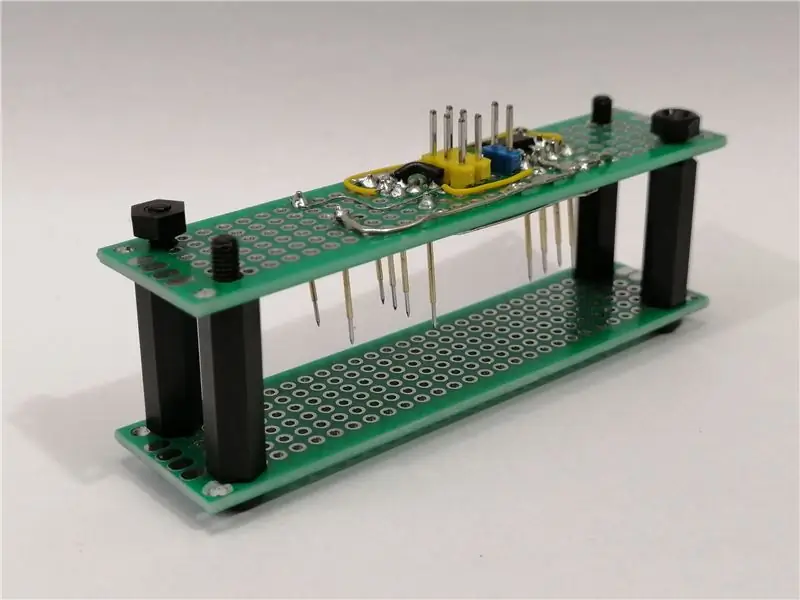
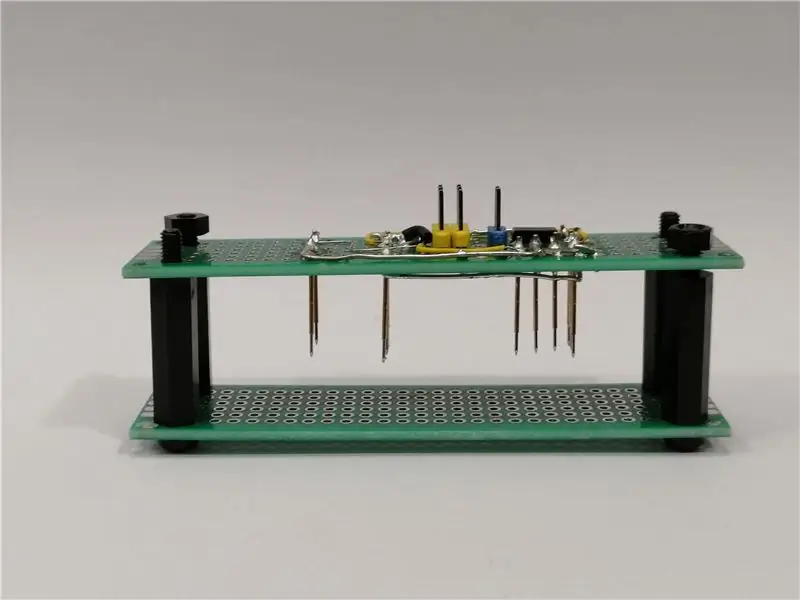
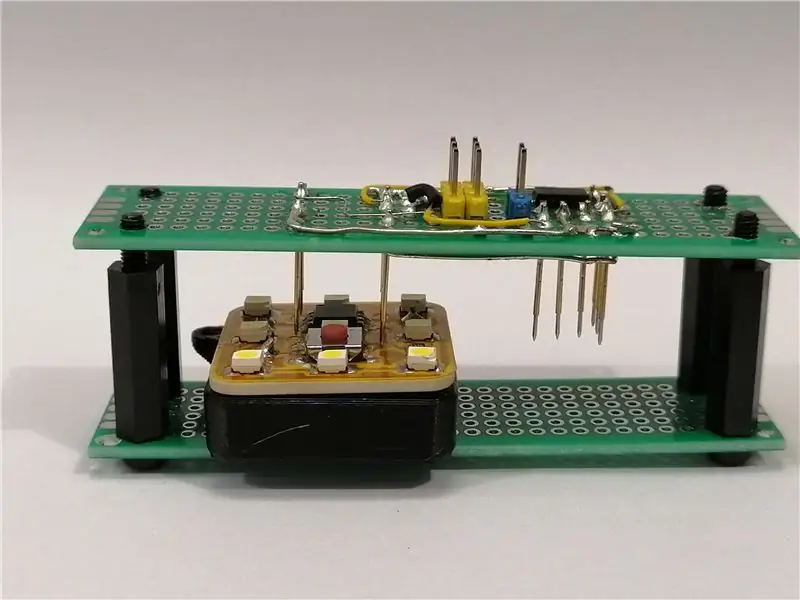
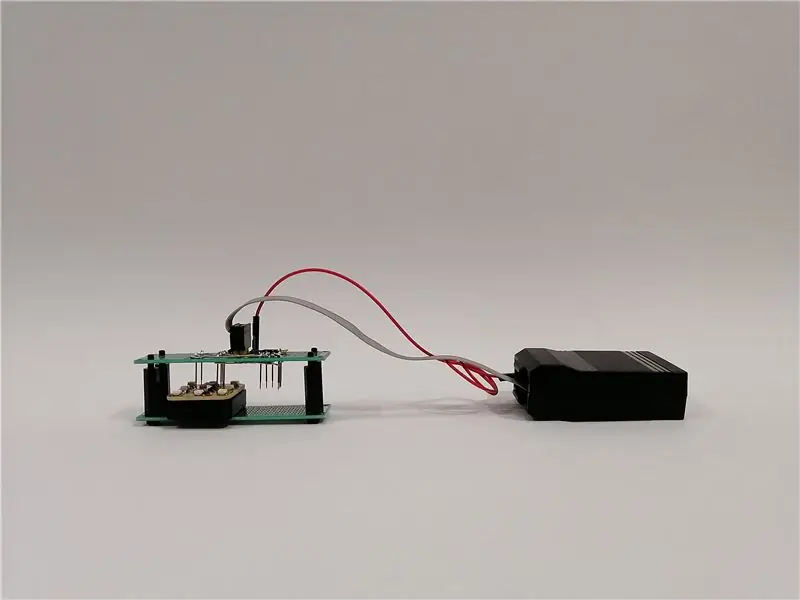
Maintenant, les tinyDice sont entièrement assemblés, mais nous devons les programmer pour qu'ils fonctionnent comme ils le devraient. Pour cela, nous utilisons un gabarit de broche pogo qui contacte tous les plots de programmation de la carte et se branche sur un programmeur ISP, qui peut être un USBtinyISP ou n'importe quel Arduino comme ISP. le tinyDice dispose de toutes les broches de programmation disponibles sur des pads avec un espacement standard de 100 mill (2,54 mm), afin de permettre l'assemblage du gabarit sur une planche perforée standard. Suivez le schéma de connexion pour lier chaque broche pogo à l'en-tête du FAI. À des fins de développement, j'ai fait un double gabarit qui sert également pour une autre carte sur laquelle je travaille et j'ai incorporé un régulateur LDO pour éviter de vider les batteries pendant le test, mais pour une programmation unique, nous pouvons utiliser la puissance directement de la batterie
Les tinyDice sont conçus pour fonctionner à 3 volts, donc les programmer à 5 volts présente le risque d'endommager les broches IO du microcontrôleur, les LED ou même le programmateur car trop de courant serait tiré à travers les résistances de limitation de courant de la LED. Ainsi, afin de programmer la puce sans endommager quoi que ce soit, nous devons utiliser sa tension native de la batterie. Si vous utilisez un USBtinyISP, retirez simplement son cavalier d'alimentation, qui alimentera le levier logique interne de la batterie du tinyDice, et si vous utilisez un Arduino, laissez simplement l'alimentation déconnectée pour alimenter uniquement les dés avec la batterie, et ajoutez une résistance série 5k à chaque ligne de données.
Étape 10: Programmation des dés
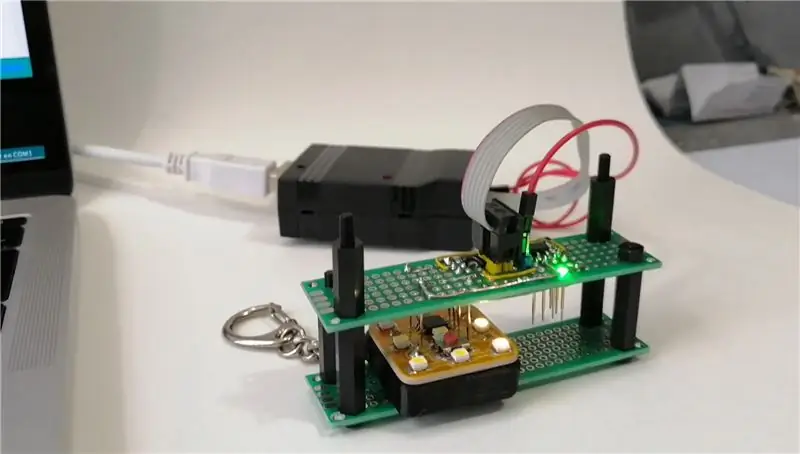
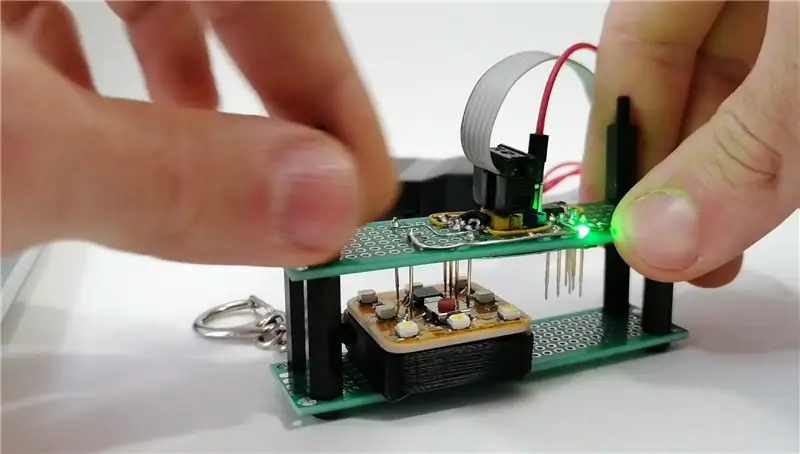
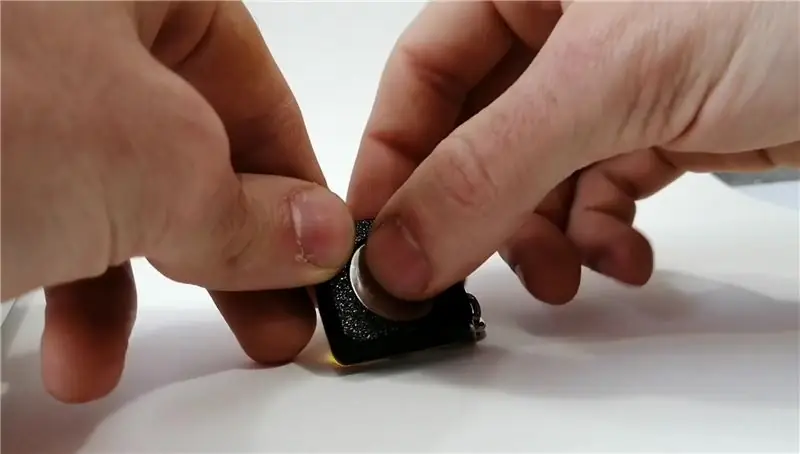
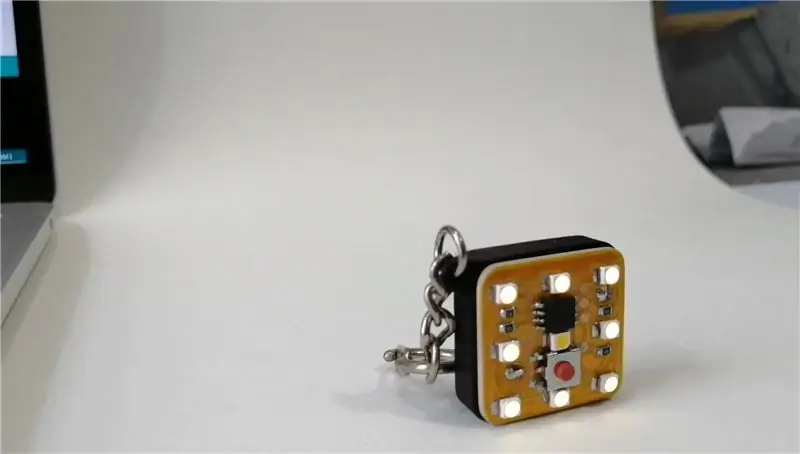
Pour le processus de programmation, assemblez soigneusement le gabarit sur les dés à l'aide d'entretoises et assurez-vous que toutes les broches pogo appuient correctement sur les pads correspondants. Soyez prudent et ne glissez pas le Die sous les broches car il est très facile de les casser. Ensuite, branchez l'USBtinyISP sur le gabarit et l'ordinateur.
Ouvrez l'IDE Arduino, chargez le sketch tinyDice et sélectionnez la puce atTiny85 avec l'USBtinyISP en tant que programmeur. Appuyez sur le bouton de téléchargement et vérifiez les dés, 2 LED devraient commencer à clignoter pendant un certain temps. Si tout se passe bien, le tinyDice est maintenant programmé, terminé et prêt à l'emploi. Répétez le processus de programmation pour toutes les unités que vous avez faites et stockez ensuite le gabarit entièrement assemblé afin de protéger les broches pogo.
Le code:
Le programme du tinyDice est tel qu'il affiche d'abord une animation "pensée", puis génère un nombre aléatoire entre 0 et 9 qui s'affiche pendant quelques secondes. Toutes les transitions sont effectuées avec PWM pour chaque LED afin de permettre les fondus. Après avoir affiché le nombre et disparu, le processeur passe en mode veille, ce qui arrête essentiellement la consommation de la batterie. La batterie devrait donc théoriquement durer environ 6 000 "lancements" de dés.
L'ensemble du code est structuré autour d'une interruption timer 8 Khz qui gère le charlieplexing et le PWM 10 pas pour chaque LED, ainsi que l'avancement des animations. Des explications plus détaillées de chaque fonction sont commentées sur le croquis Arduino.
Conclusion:
Les résultats de cette méthode pour la fabrication de circuits imprimés à domicile ont largement dépassé mes attentes initiales, car j'ai trouvé qu'elle peut être extrêmement fiable et donner des résultats de très haute qualité pour un prototypage facile et rapide des circuits CMS et traversants. Pour cette raison, j'encourage les bricoleurs à essayer cette méthode pour leurs propres conceptions et à partager vos résultats et découvertes avec la communauté.
Cette nouvelle version du tinyDice est en soi un objet très agréable et amusant à avoir et à partager avec des amis, car les animations et l'étui porte-clés le rendent tout à fait unique et intéressant. J'espère que vous avez aimé cette instructable et s'il vous plaît partagez vos commentaires et expériences sur le sujet afin que la méthode continue d'évoluer. De plus, n'hésitez pas à expérimenter le code et à partager toutes les variantes intéressantes pour que d'autres puissent les essayer.
Ce guide est sur le concours de conception de circuits imprimés, alors votez pour lui si vous le jugez digne et partagez-le avec vos amis et les passionnés d'électronique.
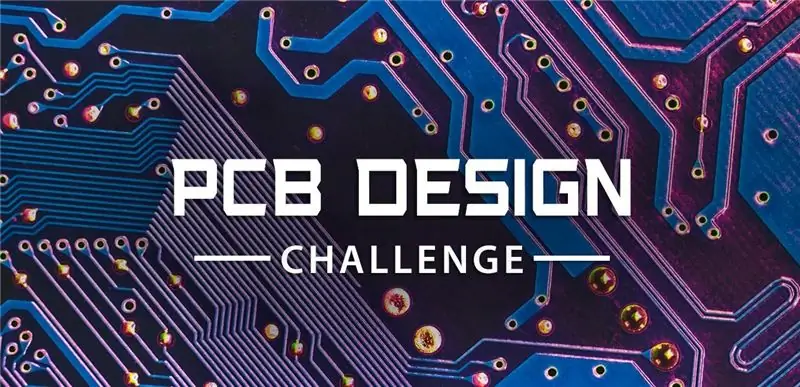
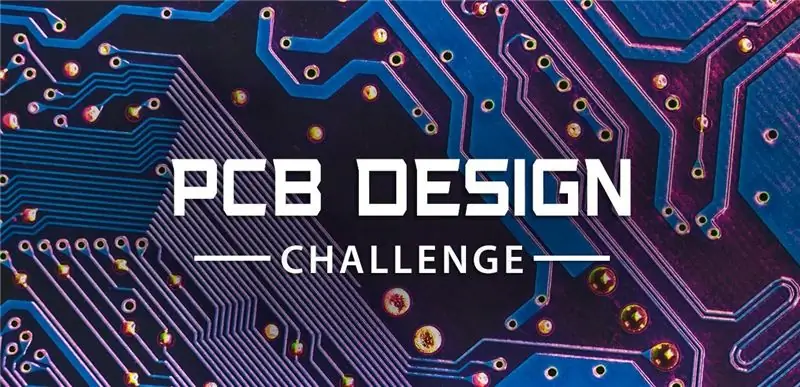
Deuxième prix du PCB Design Challenge
Conseillé:
Comment faire des PCB à la maison : 14 étapes (avec photos)
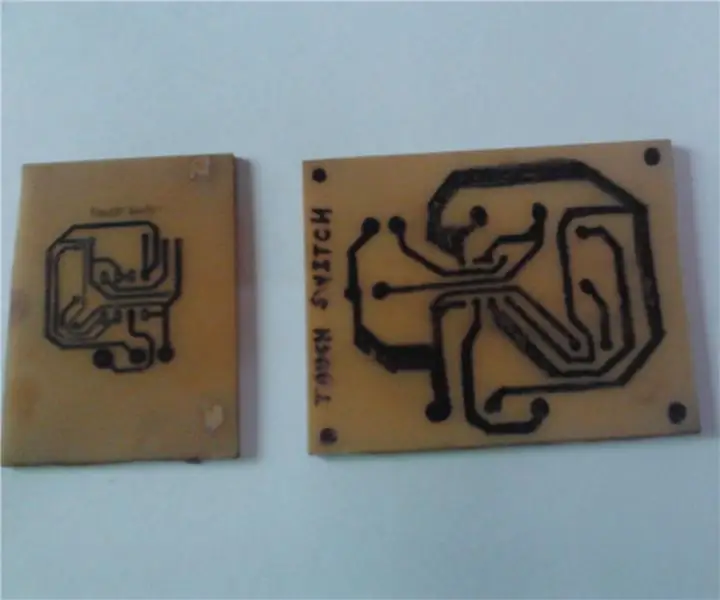
Comment faire des PCB à la maison : Lien du site Web : www.link.blogtheorem.com sans aucun matériel spécial.En tant qu'étudiant en génie électronique, j'essaie de réaliser des projets de bricolage qui nécessitent un circuit électronique simple
Les professionnels le savent ! : 24 étapes
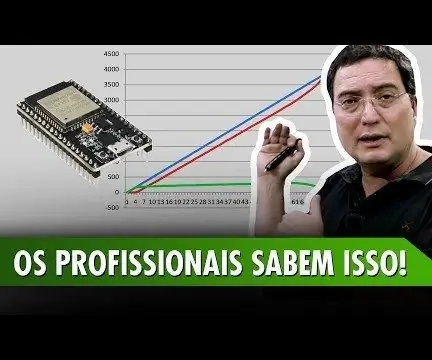
Les professionnels le savent ! : Aujourd'hui, nous allons parler de « l'étalonnage automatisé de l'ADC ESP32 ». Cela peut sembler un sujet très technique, mais je pense qu'il est très important que vous en sachiez un peu à ce sujet. C'est parce qu'il ne s'agit pas seulement de l'ESP32, ou même du calibre ADC
Souder : c'est ce que font les professionnels : 5 étapes
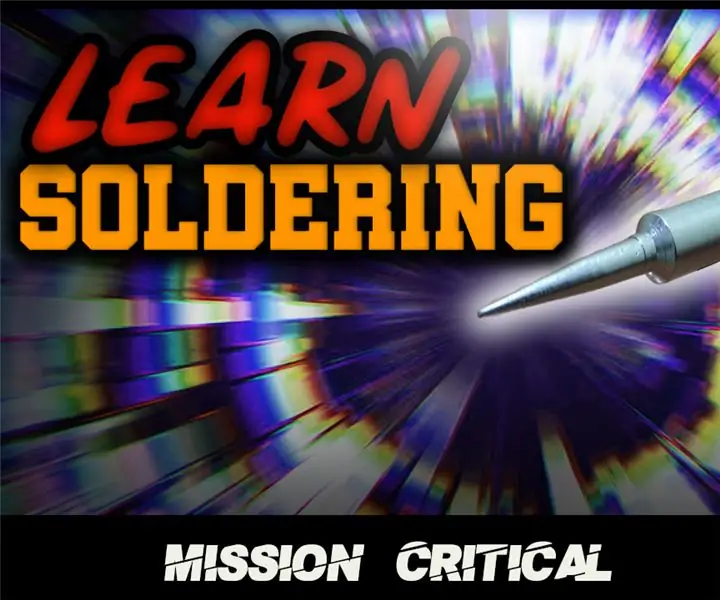
Soudure : c'est ce que font les professionnels : êtes-vous ingénieur ? Êtes-vous un électricien ou simplement un amateur qui aime réparer ses appareils électroniques ou en construire un ? dans votre vie, et voici une vidéo qui vous aidera à SOUDER le
Créez des circuits imprimés amateurs avec des outils de CAO professionnels en modifiant les « règles de conception » : 15 étapes (avec images)
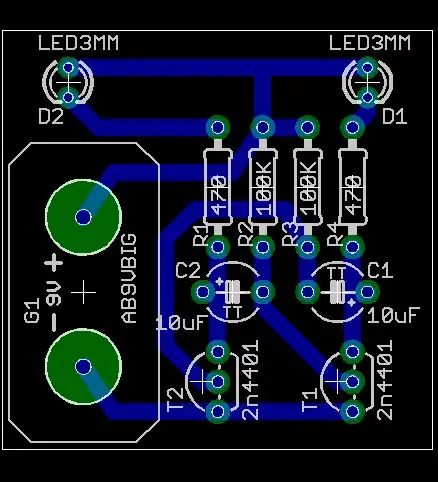
Créez des circuits imprimés pour amateurs avec des outils de CAO professionnels en modifiant les « règles de conception » : il est bon qu'il existe des outils de circuits imprimés professionnels disponibles pour les amateurs. Voici quelques conseils pour les utiliser pour concevoir des planches qui n'ont pas besoin d'un fabricant professionnel pour les FAIRE
PCB professionnels presque moins chers que de les fabriquer à la maison : 14 étapes
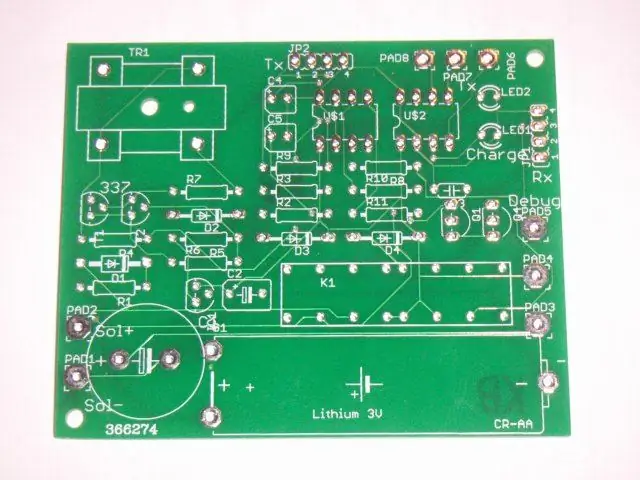
PCB professionnels presque moins chers que de les fabriquer à la maison : Bien qu'il y ait une grande satisfaction dans la construction de PCB à domicile, le coût du PCB vierge, de l'agent de gravure et des forets s'élève à plus de 4 $ par carte. Mais pour 6,25 $ la planche, le tout peut être fait professionnellement. Ce Instructable vous emmène à travers