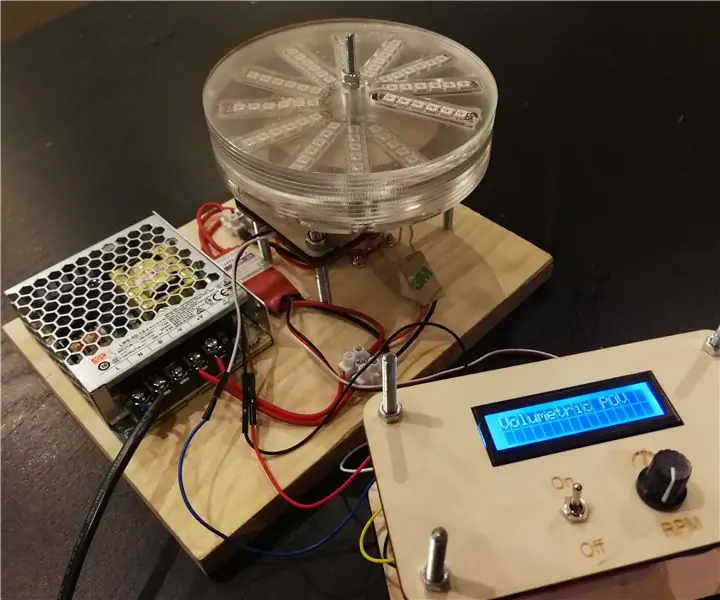
Table des matières:
- Étape 1: Matériel et outils utilisés
- Étape 2: Unité de contrôleur de moteur pour réguler la vitesse de rotation
- Étape 3: Construire la plate-forme pour la puissance de transmission sans fil
- Étape 4: Rotation du boîtier
- Étape 5: Cylindre rotatif avec les bandes LED
- Étape 6: Leçons apprises
- Étape 7: Améliorations potentielles
- Étape 8: Criez
2025 Auteur: John Day | [email protected]. Dernière modifié: 2025-01-23 14:46
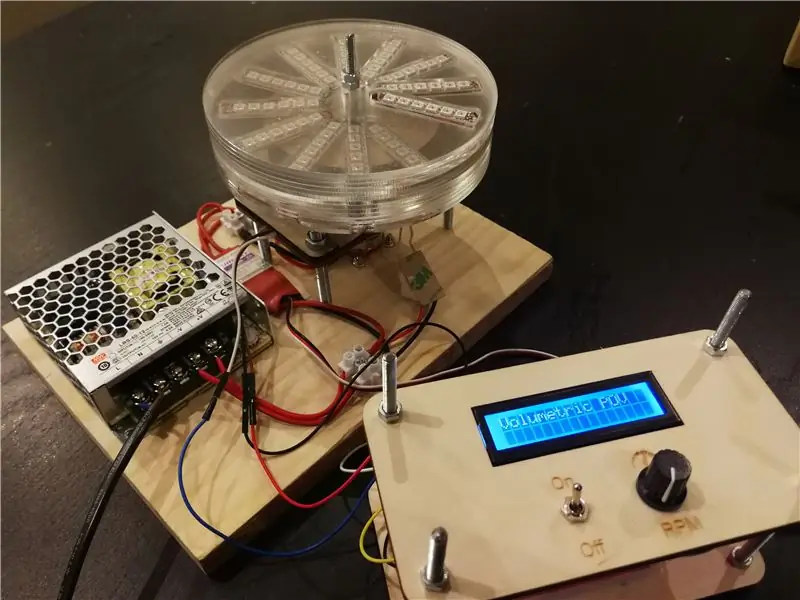
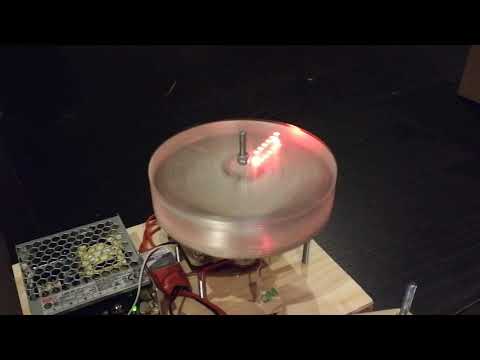

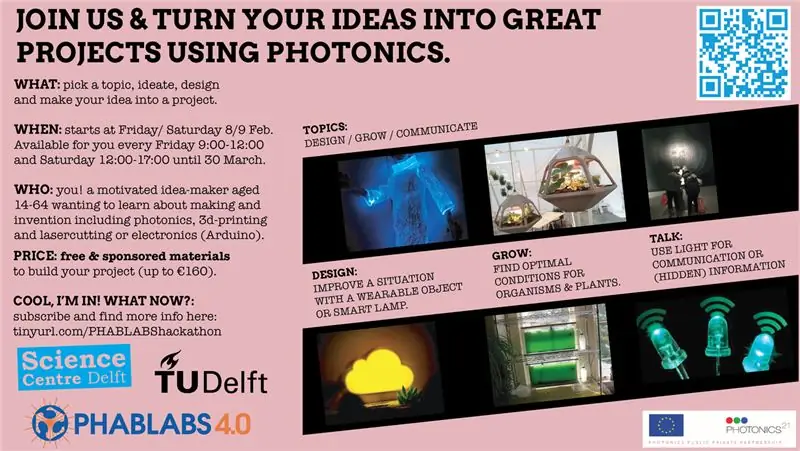
Il y a quelques semaines, j'ai reçu une invitation de dernière minute pour participer à un PhabLabs Hackathon au Science Center Delft aux Pays-Bas. Pour un amateur enthousiaste comme moi, qui ne peut normalement consacrer qu'un temps limité à bricoler, j'ai vu cela comme une excellente occasion de prévoir du temps dédié pour transformer l'une de mes nombreuses idées, dans le cadre du Hackathon: la photonique, en un projet réel. Et avec les excellentes installations du Makerspace du Science Center Delft, il était tout simplement impossible de refuser cette invitation.
L'une des idées que j'avais déjà depuis un certain temps concernant la photonique était que je voulais faire quelque chose avec Persistence of Vision (POV). Il existe déjà des tonnes d'exemples disponibles en ligne sur la façon de construire un affichage POV de base à l'aide de certains composants de base: microcontrôleur, ancien ventilateur/disque dur/moteur et une chaîne de LED connectées perpendiculairement à l'axe de l'appareil rotatif. Avec une configuration relativement simple, vous pouvez déjà créer une image impressionnante en 2 dimensions, par exemple:
Une autre variante des affichages POV connecte une chaîne de leds parallèles à l'axe du dispositif rotatif. Cela se traduira par un affichage POV cylindrique en 3 dimensions, par exemple:
Au lieu de connecter la chaîne de leds parallèlement à l'axe du dispositif rotatif, vous pouvez également arc la chaîne de leds. Cela se traduira par un affichage POV sphérique (globe), par exemple: https://www.instructables.com/id/POV-Globe-24bit-… Le niveau suivant consiste à construire plusieurs couches de chaînes LED pour créer un affichage 3D volumétrique. Voici quelques exemples de tels affichages POV 3D volumétriques que j'ai utilisés comme source d'inspiration pour ce projet spécifique:
- https://www.instructables.com/id/PropHelix-3D-POV-…
- https://github.com/mbjd/3DPOV
- https://hackaday.io/project/159306-volumetric-pov-…
- https://hackaday.com/2014/04/21/volumen-the-most-a…
Comme les créateurs des exemples ci-dessus ont fourni des informations très utiles, il était tout à fait logique de remixer des parties de leurs projets. Mais comme un hackathon est censé être un défi, j'ai également décidé de créer un autre type d'affichage POV 3D volumétrique. Certains d'entre eux utilisaient des rotors et beaucoup de colle chaude pour empêcher les composants de voler. D'autres ont créé des PCB personnalisés pour leur projet. Après avoir examiné certains des autres projets de POV 3D, j'ai vu de la place pour une « innovation » ou pour me présenter quelques défis:
- N'ayant aucune expérience préalable dans la création de circuits imprimés personnalisés et en raison de la contrainte de temps du Hackathon, j'ai choisi de suivre une approche de prototype plus basique. Mais au lieu de créer de véritables rotors, j'étais curieux de savoir à quoi ressemblerait un tel affichage POV 3D volumétrique lors de l'utilisation d'un cylindre construit à partir de couches de plastique acrylique.
- Aucune utilisation ou bien utilisation minimale de colle chaude pour rendre l'appareil moins dangereux
Étape 1: Matériel et outils utilisés
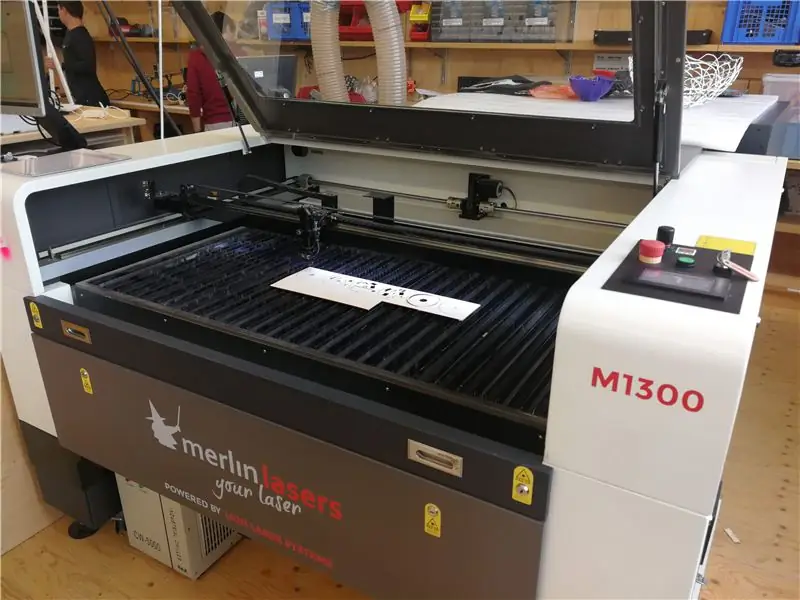
Pour le contrôleur de moteur
- Arduino Pro Micro 5V/16Mhz
- Petite planche à pain
- 3144 Capteur de commutateur à effet Hall
- Aimant avec diamètre: 1 cm, hauteur: 3 mm
- Interrupteur à bascule - MTS-102
- Potentiomètre 10K
- Fils de connexion Dupont
- 16 écrous M5
- Module d'affichage LCD avec rétroéclairage bleu (HD44780 16×2 caractères)
- Résistance 10K - Résistance de tirage pour le capteur à effet Hall
- Résistance 220Ohm - Pour contrôler le contraste de l'écran LCD
- Diamètre de la tige filetée: 5 mm
- Contreplaqué, Épaisseur: 3 mm
Pour la base de la plate-forme
- Morceau de bois de rebut (250 x 180 x 18 mm)
- Mean Well - 12V 4.2A - Alimentation à découpage LRS-50-12
- Câble d'alimentation 220V
- Convertisseur sans fil DC-DC - 5V 2A (émetteur)
- Moteur sans balais Turnigy D2836/8 1100KV
- Turnigy Plush Contrôleur de vitesse 30 ampères avec BEC
- Borniers Connecteurs
- 12 écrous M6 pour fixer la plate-forme à l'aide des tiges filetées d'un diamètre de 6 mm.
- 3 x boulons M2 (longueur 18 mm) pour fixer l'adaptateur boulonné au moteur sans balai
- 4 x écrous et boulons M3 pour fixer le moteur sans balai au morceau de bois de rebut
- Diamètre de la tige filetée: 6 mm (4 x longueur 70 mm)
- Diamètre de la tige filetée: 4 mm (1 x longueur 80 mm)
- Contreplaqué, Épaisseur: 3 mm
Pour le boîtier rotatif
- Convertisseur sans fil DC-DC - 5V 2A (Récepteur)
- Adaptateur boulonné imprimé en 3D (filament PLA, blanc)
- Ados 3.6
- Convertisseur/décaleur de niveau logique quadruple IC 74AHCT125 (3V à 5V)
- Résistance 10K - Résistance de tirage pour le capteur à effet Hall
- Condensateur 1000uF 16V
- Diamètre de la tige filetée 4 mm
- Aimant avec diamètre: 1 cm, hauteur: 3 mm
- Contreplaqué, Épaisseur: 3 mm
- Contreplaqué, Épaisseur: 2 mm
- Feuille acrylique, épaisseur: 2 mm
- Diamètre de la tige en acier: 2 mm
- Écrous et boulons
- Ruban led 0,5 mètre APA102C 144 leds / mètre
Les outils utilisés
- Coupeur laser Merlin M1300 - Contreplaqué et feuille acrylique découpés au laser
- Ultimaker 2+ pour l'impression 3D de l'adaptateur Bolt On
- Station de soudure et soudure
- Perceuse de table
- Tournevis
- Pinces
- Marteau
- Étrier
- Scie à métaux
- Clés
- Gaine thermorétractable
Logiciel utilisé
- Fusion 360
- Ultimaker Cura
- Arduino IDE et Teensyduino (contenant Teensy Loader)
Étape 2: Unité de contrôleur de moteur pour réguler la vitesse de rotation
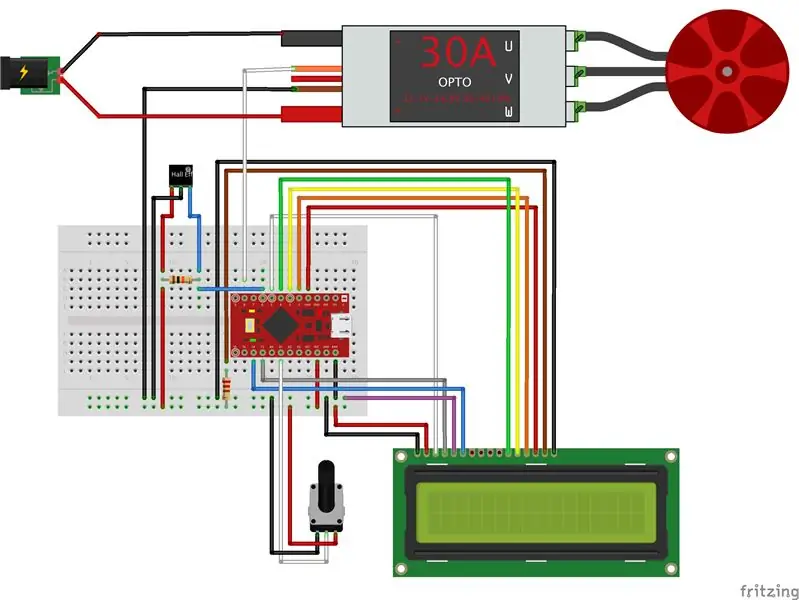
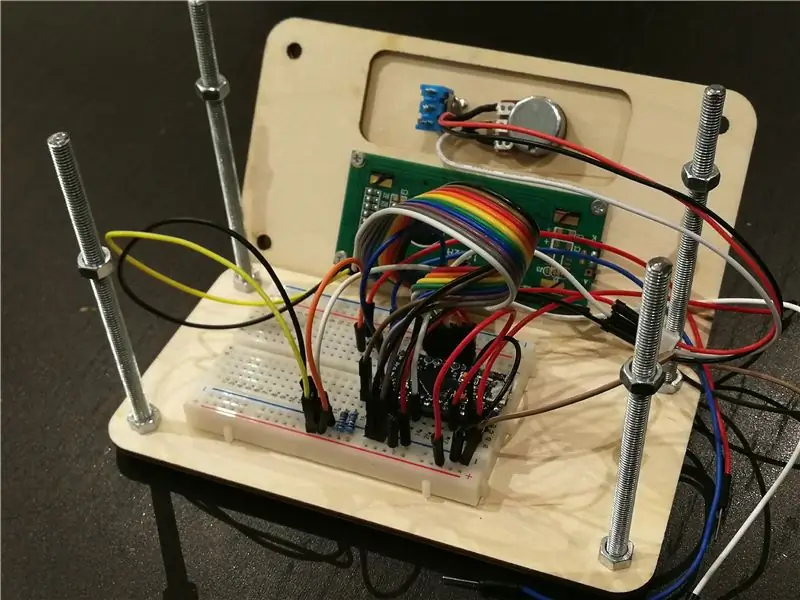
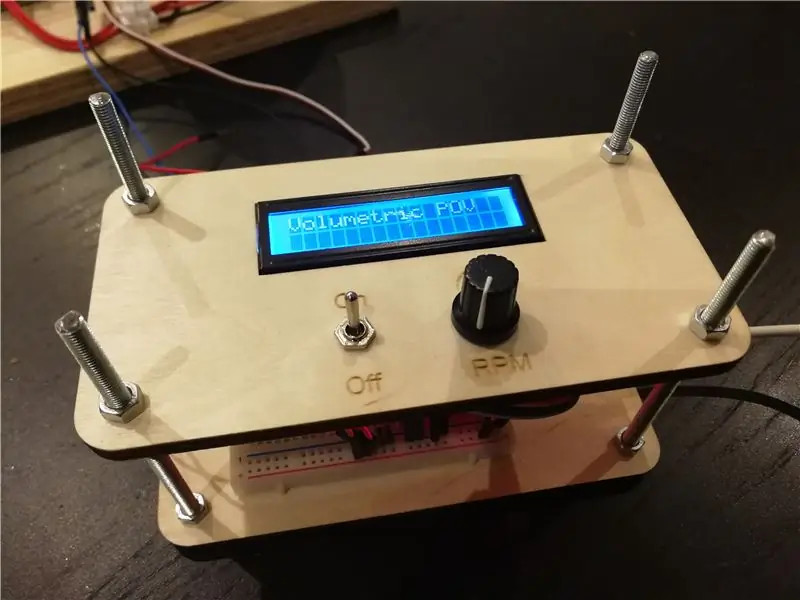
L'unité de contrôleur de moteur envoie un signal au contrôleur de vitesse électronique Turnigy (ESC) qui contrôlera le nombre de rotations fournies par le moteur sans balai.
De plus, je voulais également pouvoir afficher les rotations réelles par minute du cylindre POV. C'est pourquoi j'ai décidé d'inclure un capteur à effet Hall et un écran LCD 16x2 à l'unité de contrôleur de moteur.
Dans le fichier zip ci-joint (MotorControl_Board.zip), vous trouverez trois fichiers dxf qui vous permettront de découper au laser une plaque de base et deux plaques supérieures pour l'unité de commande de moteur. Veuillez utiliser du contreplaqué d'une épaisseur de 3 mm. Les deux plaques supérieures peuvent être placées l'une sur l'autre, ce qui vous permettra de visser l'écran LCD 16x2.
Les deux trous de la plaque supérieure sont destinés à un interrupteur à bascule marche/arrêt et un potentiomètre pour contrôler la vitesse du moteur sans balai (je n'ai pas encore câblé l'interrupteur à bascule marche/arrêt moi-même). Pour construire l'unité de contrôleur de moteur, vous devez scier la tige filetée d'un diamètre de 5 mm en 4 morceaux de la hauteur souhaitée. À l'aide des 8 écrous M5, vous pouvez d'abord fixer la base. Ensuite, j'ai attaché la petite planche à pain à la plaque de base à l'aide de l'autocollant adhésif double face fourni avec la planche à pain. Le schéma ci-joint montre comment câbler les composants afin qu'ils puissent fonctionner avec le code source (MotorControl.ino) attaché à cette étape. J'ai utilisé une résistance pull-up de 10K pour le capteur à effet Hall. Une résistance de 220 Ohm a fonctionné assez bien pour rendre le texte visible sur l'écran LCD.
Assurez-vous d'isoler les broches du capteur à effet Hall à l'aide de tubes thermorétractables, comme indiqué sur les images. Le bon fonctionnement du capteur à effet Hall reposera sur un aimant qui sera placé dans le boîtier rotatif à l'étape 3.
Une fois le câblage terminé, vous pouvez fixer les 2 plaques supérieures avec l'écran LCD, l'interrupteur et le potentiomètre en utilisant à nouveau 8 écrous M5 comme indiqué sur les photos.
En fonction du modèle de votre moteur utilisé, vous devrez peut-être ajuster la ligne de code suivante dans le fichier MotorControl.ino:
accélérateur = map(averagePotValue, 0, 1020, 710, 900);
Cette ligne de code (ligne 176) mappe la position du potentiomètre 10K au signal pour l'ESC. L'ESC accepte une valeur entre 700 et 2000. Et comme le moteur que j'ai utilisé pour ce projet a commencé à tourner autour de 823, j'ai limité les RPM du moteur en limitant la valeur maximale à 900.
Étape 3: Construire la plate-forme pour la puissance de transmission sans fil
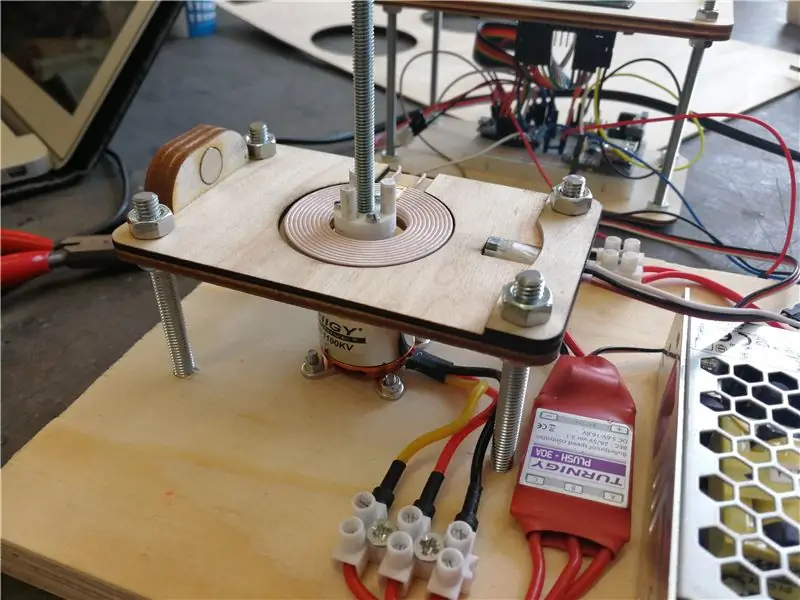
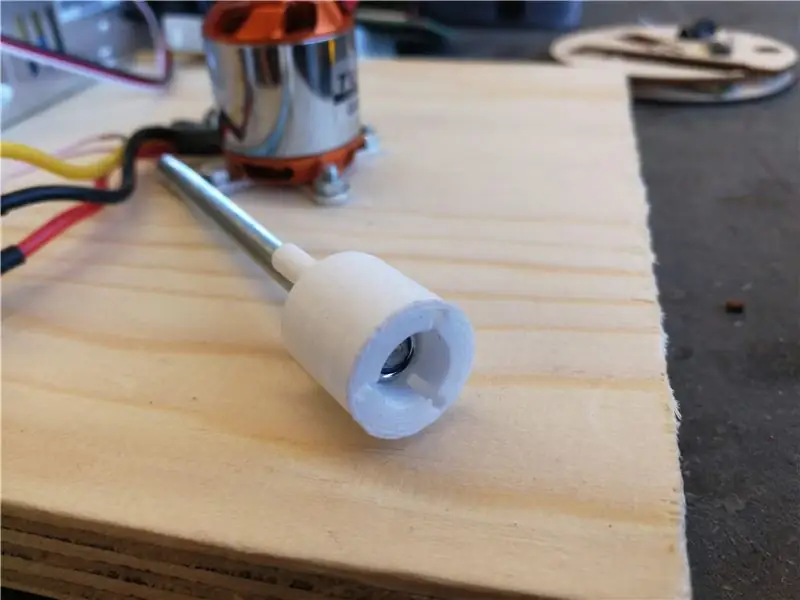
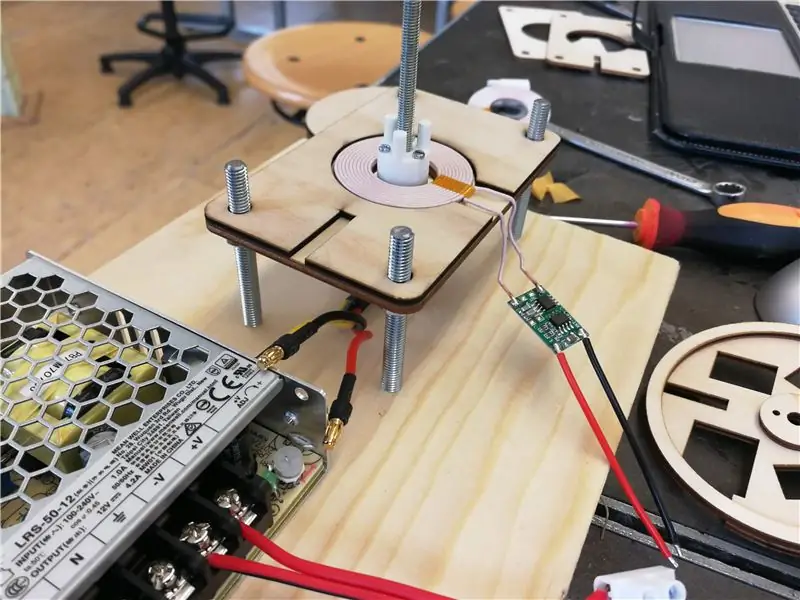
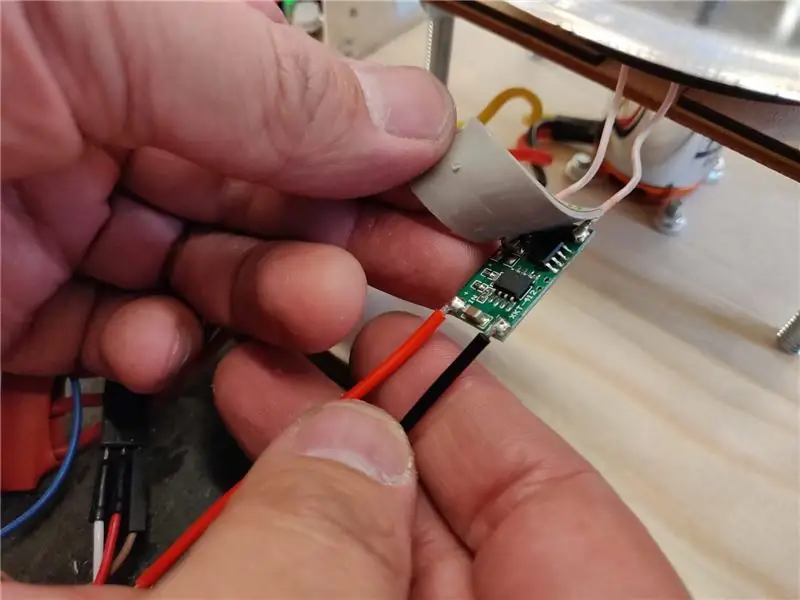
De nos jours, il existe essentiellement deux façons d'alimenter des appareils qui doivent tourner: des bagues collectrices ou la transmission de puissance sans fil via des bobines d'induction. Comme les bagues collectrices de haute qualité qui peuvent supporter des RPM élevés ont tendance à être très chères et plus sujettes à l'usure, j'ai opté pour l'option sans fil utilisant un convertisseur DC-DC sans fil 5V. Selon les spécifications, il devrait être possible de transférer jusqu'à 2 ampères à l'aide d'un tel convertisseur.
Le convertisseur DC-DC sans fil se compose de deux composants, un émetteur et un récepteur. Veuillez noter que le PCB connecté à la bobine d'induction émettrice est plus petit que celui de réception.
La plate-forme elle-même est construite à l'aide d'un morceau de bois de récupération (250 x 180 x 18 mm).
Sur la plate-forme, j'ai vissé l'alimentation Mean Well 12V. La sortie 12V est connectée à l'ESC (voir les schémas à l'étape 1) et au PCB de la partie émettrice du convertisseur DC-DC sans fil.
Dans le fichier Platform_Files.zip ci-joint, vous trouverez les fichiers dxf pour découper au laser la plate-forme dans du contreplaqué d'une épaisseur de 3 mm:
- Platform_001.dxf et Platform_002.dxf: Vous devez les placer l'un sur l'autre. Cela créera une zone en retrait pour la bobine d'induction de transmission.
- Magnet_Holder.dxf: Découpez ce motif trois fois au laser. Une des trois fois, incluez le cercle. Dans les deux autres découpes laser: retirez le cercle de la découpe. Après la découpe, collez les trois pièces ensemble pour créer un support pour un aimant (diamètre 10 mm, épaisseur: 3 mm). J'ai utilisé de la superglue pour coller l'aimant dans le support d'aimant. Assurez-vous de coller le bon côté de l'aimant sur le support car le capteur à effet Hall ne fonctionnera qu'avec un côté de l'aimant.
- Platform_Sensor_Cover.dxf: cette pièce vous aidera à maintenir le capteur à effet Hall attaché à l'unité de commande du moteur en place, comme indiqué sur la première image.
- Platform_Drill_Template.dxf: J'ai utilisé cette pièce comme gabarit pour percer les trous dans le morceau de bois de rebut. Les quatre plus grands trous de 6 mm sont destinés aux tiges filetées de support d'un diamètre de 6 mm pour soutenir la plate-forme. Les 4 trous plus petits servent à fixer le moteur sans balais au morceau de bois de rebut. Le plus grand trou au milieu était nécessaire pour l'axe qui dépassait du moteur sans balai. Comme les boulons du moteur et les tiges filetées de la plate-forme doivent être fixés au bas de la plate-forme, il est nécessaire d'agrandir ces trous de quelques mm de profondeur pour permettre l'insertion des écrous.
Malheureusement, l'arbre du moteur sans balais est sorti du «mauvais» côté pour ce projet. Mais j'ai pu inverser l'arbre à l'aide de l'instruction suivante que j'ai trouvée sur Youtube:
Une fois le moteur et les tiges de support fixés, la plate-forme peut être construite à l'aide des pièces de plate-forme découpées au laser. La plate-forme elle-même peut être fixée à l'aide de 8 écrous M6. Le porte-aimant peut être collé à la plate-forme à la frontière comme indiqué sur la première image.
Le fichier joint "Bolt-On Adapter.stl" peut être imprimé à l'aide d'une imprimante 3D. Cet adaptateur est nécessaire pour fixer une tige filetée d'un diamètre de 4 mm au moteur Brushless à l'aide de 3 boulons M2 d'une longueur de 18 mm.
Étape 4: Rotation du boîtier
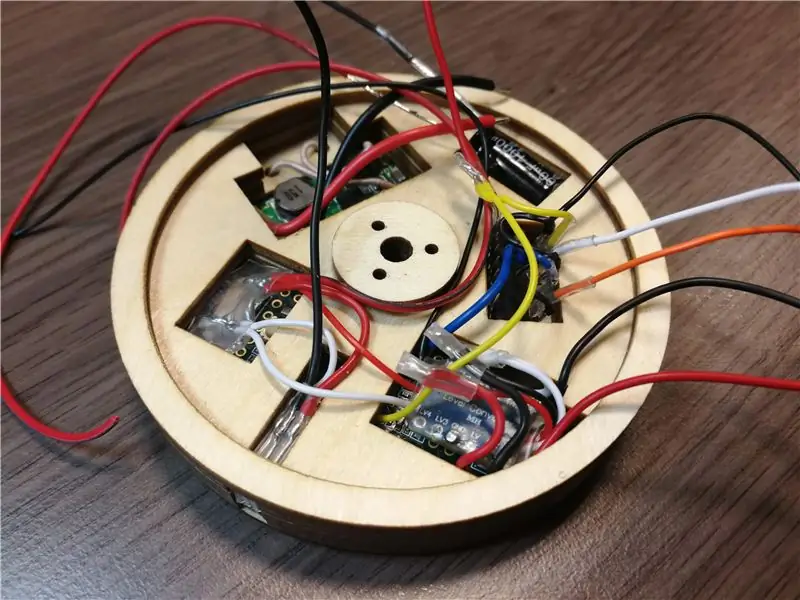
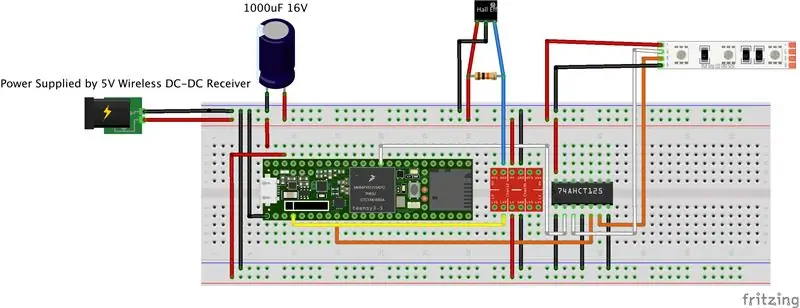
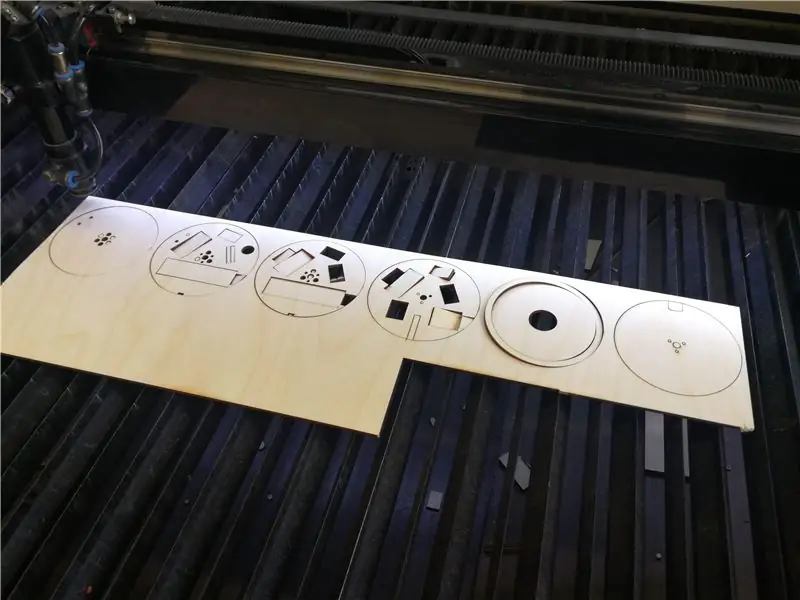
Le fichier Base_Case_Files.zip joint contient les fichiers dxf pour découper au laser les 6 couches pour construire le boîtier des composants contrôlant la bande led APA102C.
Les couches 1 à 3 de la conception du boîtier sont destinées à être collées ensemble. Mais assurez-vous qu'un aimant (diamètre 10 mm, hauteur: 3 mm) est inséré dans la découpe circulaire de la couche 2 avant de coller les trois couches ensemble. Assurez-vous également que l'aimant est collé avec le bon pôle vers le bas, car le capteur à effet Hall placé sur la plate-forme construite à l'étape 3 ne répondra qu'à un côté de l'aimant.
La conception du boîtier contient des compartiments pour les composants répertoriés dans les schémas de câblage ci-joints. L'IC 74AHCT125 est nécessaire pour convertir le signal 3,3V du Teensy au signal 5V requis pour la bande led APA102. Les couches 4 et 5 peuvent également être collées ensemble. La couche supérieure 6 peut être empilée sur les autres couches. Toutes les couches resteront dans la bonne position à l'aide de 3 tiges d'acier d'un diamètre de 2 mm. Il y a trois petits trous pour les tiges en acier de 2 mm entourant le plus grand trou pour la tige filetée rotative de 4 mm fixée au moteur sans balai. Une fois tous les composants soudés selon le schéma, le boîtier complet peut être placé sur l'adaptateur boulonné imprimé à l'étape 3. Veuillez vous assurer que tous les fils ouverts sont correctement isolés à l'aide de tubes thermorétractables. Veuillez noter que le bon fonctionnement du capteur à effet Hall de cette étape dépend de l'aimant placé dans le porte-aimant décrit à l'étape 3.
Le code de preuve de concept ci-joint 3D_POV_POC.ino allumera certaines leds en rouge. L'esquisse entraîne l'affichage d'un carré une fois que le cylindre commence à tourner. Mais avant que la rotation ne commence, les leds nécessaires pour simuler un carré sont allumées par défaut. Ceci est utile pour tester le bon fonctionnement des leds à l'étape suivante.
Étape 5: Cylindre rotatif avec les bandes LED
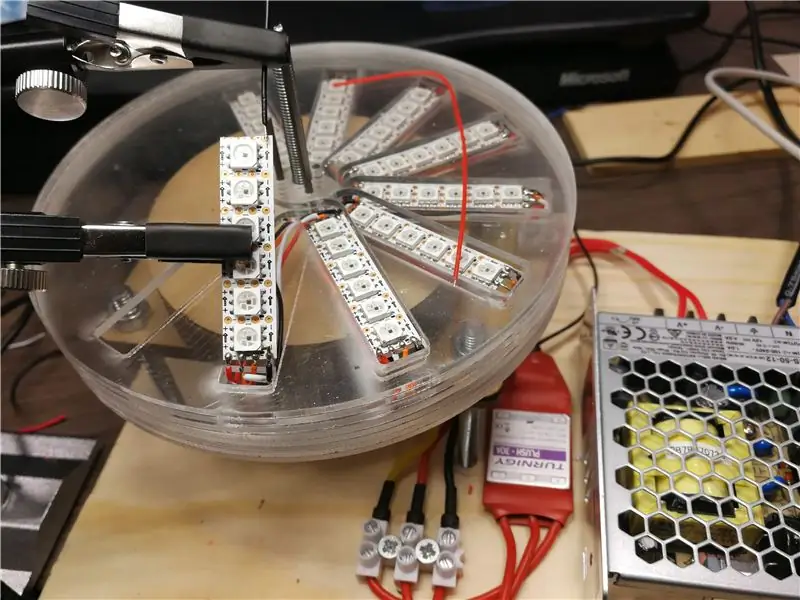
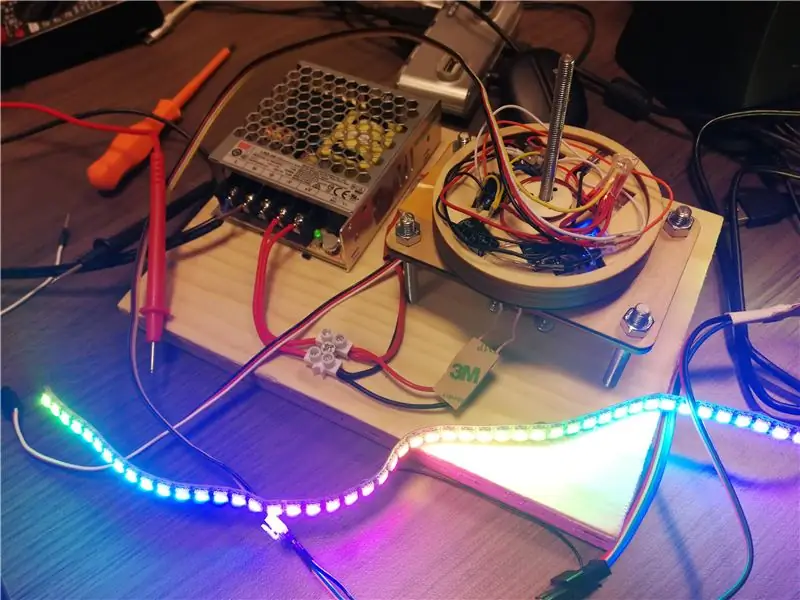
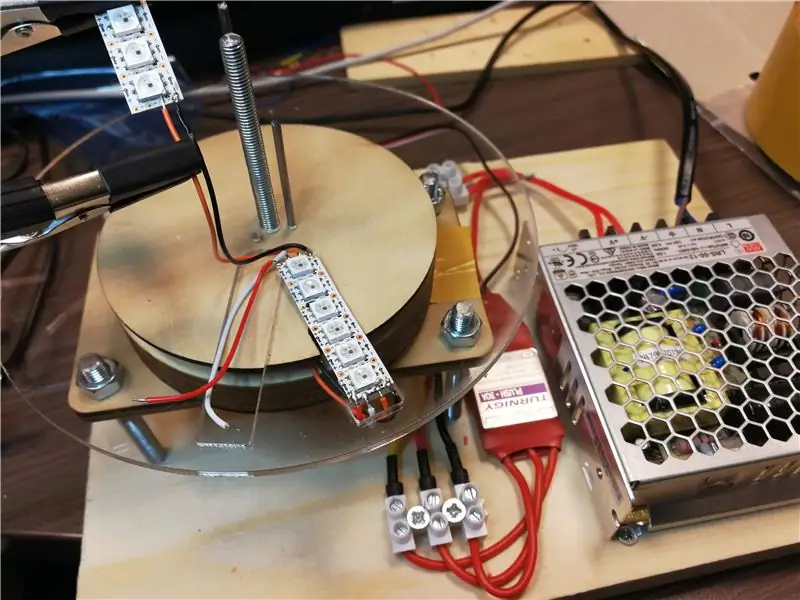
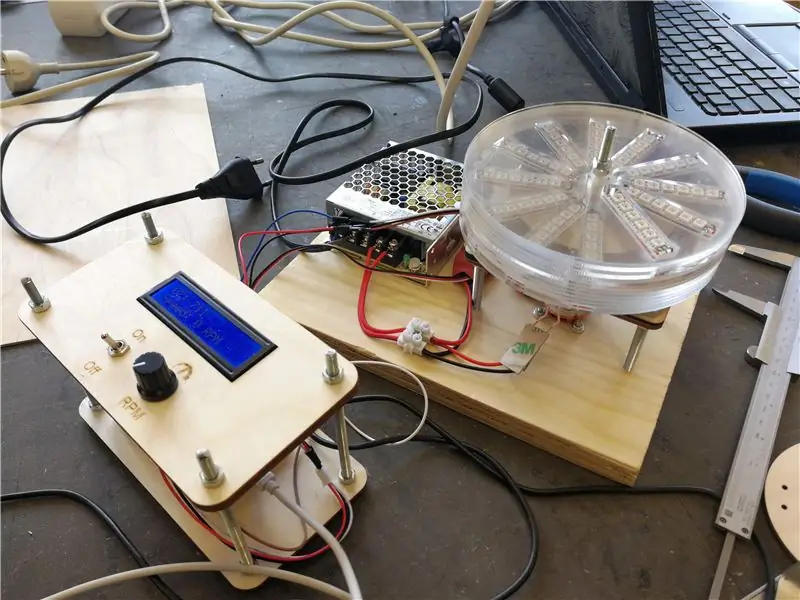
Le fichier Rotor_Cylinder_Files.zip joint contient les fichiers dxf pour couper une feuille acrylique de 2 mm d'épaisseur. Les 14 disques résultants sont nécessaires pour construire le cylindre transparent pour ce projet POV. Les disques doivent être empilés les uns sur les autres. La conception des disques cylindriques permet de souder 12 bandes LED ensemble en une longue bande LED. À partir du disque un, une petite bande LED contenant 6 LED doit être fixée sur un disque à l'aide des autocollants adhésifs sur la bande LED. Soudez d'abord les fils à la bande led avant de fixer les bandes led au disque à l'aide des autocollants adhésifs. Sinon, vous courez le risque que le pistolet à souder fasse fondre le disque acrylique.
Une fois le disque #13 empilé sur le cylindre transparent, la tige d'acier de 2 mm utilisée pour maintenir toutes les couches dans les bonnes positions peut maintenant également être coupée à la bonne longueur, alignée sur le haut du disque #13 du cylindre. Le disque #14 peut ensuite être utilisé pour maintenir les tiges d'acier de 2 mm en place à l'aide de deux écrous M4.
En raison du temps nécessaire à la construction de l'ensemble de l'appareil, je n'ai pas encore pu programmer des écrans 3D plus stables et visuellement intéressants dans les délais du hackathon. C'est aussi la raison pour laquelle le code fourni pour contrôler les leds est encore très basique pour prouver le concept, ne montrant qu'un carré rouge en 3 dimensions pour le moment.
Étape 6: Leçons apprises
Ados 3.6
- J'ai commandé un Teensy 3.5 pour ce projet, mais le fournisseur m'a envoyé un Teensy 3.6 par erreur. Comme j'avais hâte de terminer le projet dans les délais du hackathon, j'ai décidé d'aller de l'avant avec le Teensy 3.6. La raison pour laquelle je voulais utiliser le Teensy 3.5 était à cause des ports, ils tolèrent 5V. Ce n'est pas le cas avec le Teensy 3.6. C'est aussi la raison pour laquelle j'ai dû introduire un convertisseur logique bidirectionnel dans la configuration. Avec un Teensy 3.5, cela n'aurait pas été nécessaire.
- Problème de montée en puissance: lors de la mise sous tension de l'appareil, il y a une montée en puissance via le module de charge sans fil dc-dc pour alimenter le Teensy 3.6. Malheureusement, la montée en puissance est trop lente pour que le Teensy 3.6 démarre correctement. Comme solution de contournement, je dois actuellement alimenter le Teensy 3.6 via la connexion micro USB, puis brancher l'alimentation 12V alimentant l'émetteur sans fil dc-dc. Une fois que le récepteur dc-dc sans fil alimente également le Teensy, je peux débrancher le câble USB. Les gens ont partagé leur hack avec un MIC803 pour le problème de montée en puissance lente ici:
Module d'écran LCD
Comportement erratique sur alimentation externe. L'écran fonctionne correctement lorsqu'il est alimenté via USB. Mais lorsque j'alimente l'écran LCD via la maquette en utilisant le 5V fourni par le BEC ou une alimentation indépendante, le texte commence à être brouillé après quelques secondes après que le texte est censé changer. Je dois encore enquêter sur la cause de ce problème
Mécanique
Afin de tester mon contrôleur de moteur pour mesurer les RPM réels, j'ai laissé le moteur tourner avec le boulon sur l'adaptateur, le boulon et le boîtier de base attachés au moteur. Lors d'un des premiers essais, les vis reliant le support moteur au moteur se dévissent en raison des vibrations. Heureusement, j'ai remarqué ce problème à temps, ce qui a permis d'éviter une catastrophe potentielle. J'ai résolu ce problème en vissant un peu plus les vis sur le moteur et j'ai également utilisé quelques gouttes de Loctite pour fixer encore plus les vis
Logiciel
Lorsque vous exportez des esquisses Fusion 360 sous forme de fichiers dxf pour la découpeuse laser, les lignes de support sont exportées sous forme de lignes régulières
Étape 7: Améliorations potentielles
Qu'aurais-je fait différemment en fonction de l'expérience que j'ai acquise avec ce projet:
- Utiliser une bande led contenant au moins 7 leds au lieu de 6 leds par couche pour des visualisations textuelles plus agréables
- Achetez un moteur sans balais différent où l'arbre dépasse déjà du bon côté (inférieur) du moteur. (par exemple: https://hobbyking.com/de_de/ntm-prop-drive-28-36-1000kv-400w.html) Cela vous évitera de couper l'arbre ou de pousser l'arbre du bon côté comme je devait faire maintenant.
- Passer plus de temps à équilibrer l'appareil pour minimiser les vibrations, qu'elles soient mécaniques ou modélisées dans Fusion 360.
J'ai également réfléchi à certaines améliorations potentielles, que je pourrais examiner si le temps le permet:
- Utilisation réelle de la fonctionnalité de carte SD sur le Teensy pour créer des animations plus longues
- Augmentez la densité de l'imagerie en utilisant des LED plus petites (APA102(C) 2020). Lorsque j'ai commencé ce projet il y a quelques semaines, les bandes de led contenant ces petites leds (2x2 mm) n'étaient pas facilement disponibles sur le marché. Il est possible de les acheter en tant que composants SMD séparés, mais je n'envisagerais cette option que si vous êtes prêt à souder ces composants sur un PCB personnalisé.
- Transférez des images 3D sans fil vers l'appareil (Wifi ou Bluetooth). Cela devrait également permettre de programmer l'appareil pour visualiser le son/la musique.
- Convertir les animations Blender dans un format de fichier pouvant être utilisé avec l'appareil
- Placez toutes les bandes LED sur la plaque de base et concentrez la lumière sur les couches d'acrylique. Sur chaque couche différente, de petites zones peuvent être gravées pour refléter la lumière lorsqu'elle est omise des LED. La lumière doit être focalisée sur les zones gravées. Cela devrait être possible en créant un tunnel guidant la lumière ou en utilisant des lentilles sur les leds pour focaliser la lumière.
- Amélioration de la stabilité de l'affichage volumétrique 3D et de la régulation de la vitesse de rotation en séparant la base rotative du moteur brushless à l'aide d'engrenages et d'une courroie de distribution.
Étape 8: Criez
Je tiens à remercier tout particulièrement les personnes suivantes:
- Ma femme et mes filles fantastiques, pour leur soutien et leur compréhension.
- Teun Verkerk, pour m'avoir invité au Hackathon
- Nabi Kambiz, Nuriddin Kadouri et Aidan Wyber, pour votre soutien, votre assistance et vos conseils tout au long du Hackaton
- Luuk Meints, un artiste et un autre participant de ce Hackaton qui a eu la gentillesse de me donner un cours de vitesse d'introduction personnel d'une heure à Fusion 360 qui m'a permis de modéliser toutes les pièces dont j'avais besoin pour ce projet.
Conseillé:
Calcul de l'humidité, de la pression et de la température à l'aide du BME280 et de l'interfaçage photonique : 6 étapes
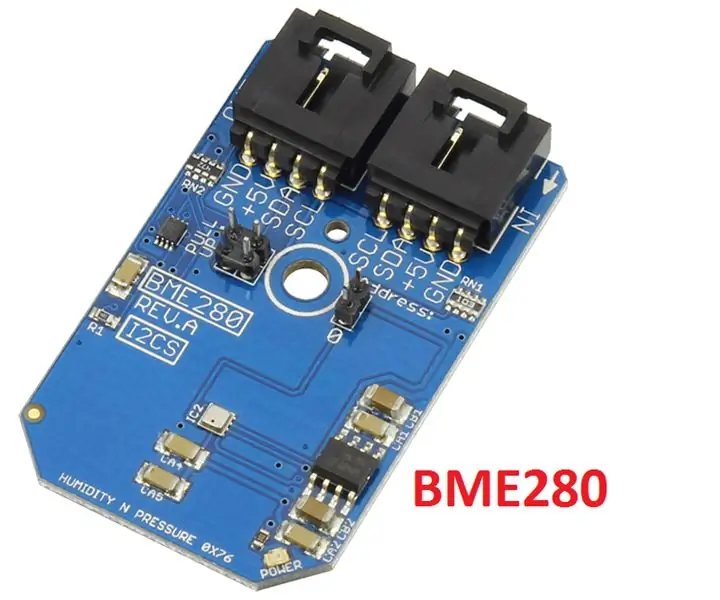
Calcul de l'humidité, de la pression et de la température à l'aide du BME280 et de l'interfaçage photonique.: Nous rencontrons divers projets qui nécessitent une surveillance de la température, de la pression et de l'humidité. Ainsi, nous réalisons que ces paramètres jouent en fait un rôle essentiel pour avoir une estimation de l'efficacité de fonctionnement d'un système à différentes conditions atmosphériques
Beatbox photonique portable : 7 étapes
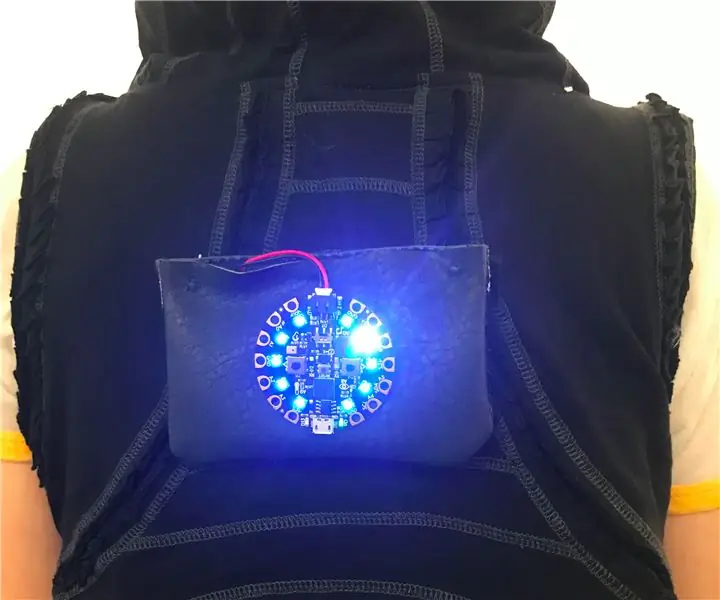
Wearable Photon Beatbox : Ce projet a été inspiré par le code d'une photon beat box que j'ai trouvé sur Adafruit : https://makecode.adafruit.com/examples/photon-beat… J'ai décidé de développer ce concept en prenant le code et en faire un gilet électronique portable qui changera
Plaques holographiques - Challenger photonique Hackathon PhabLabs : 6 étapes
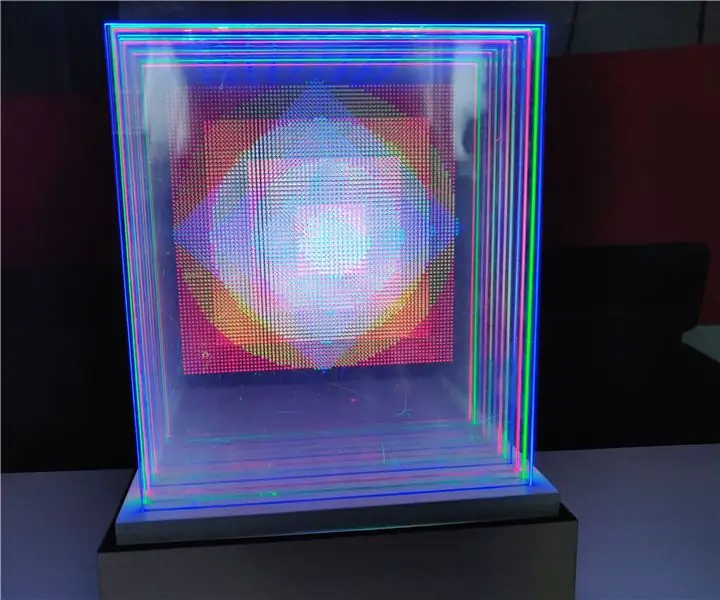
Plaques holographiques - Challenger photonique Hackathon PhabLabs : Au début de cette année, on m'a demandé de participer au PhabLabs Photonics Hackathon au Science Center Delft aux Pays-Bas. Ici, ils ont un grand espace de travail avec beaucoup de machines qui pourraient être utilisées pour créer quelque chose que je normal
Capteur d'air photonique - Surveiller les niveaux de PM : 3 étapes
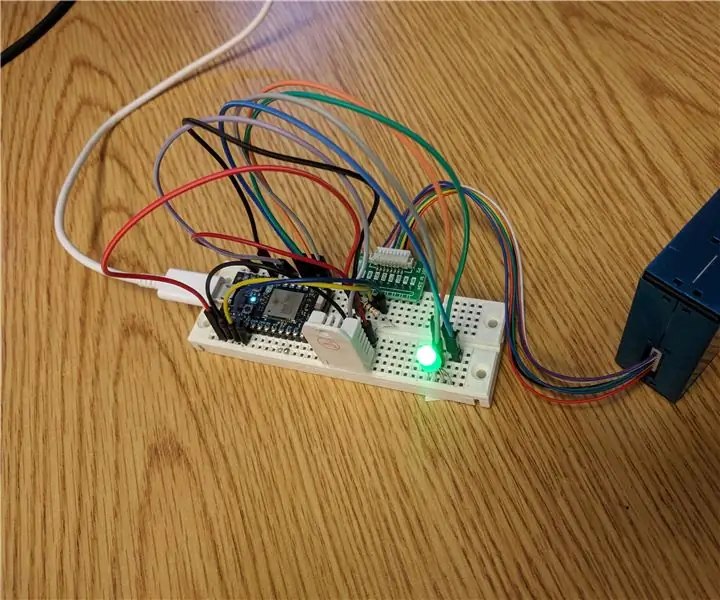
Capteur d'air à photons - Surveiller les niveaux de PM : j'ai mis à jour mon ancien capteur d'air à photons pour utiliser le nouveau capteur d'air Plantower PMS5003. Il se met à jour plus rapidement, est plus stable et fournit des lectures pour PM1, PM2.5, PM 10. J'ai également inclus un capteur de température et d'humidité avec le DHT22. Vous n'avez pas besoin de je
Faire un affichage volumétrique : 7 étapes
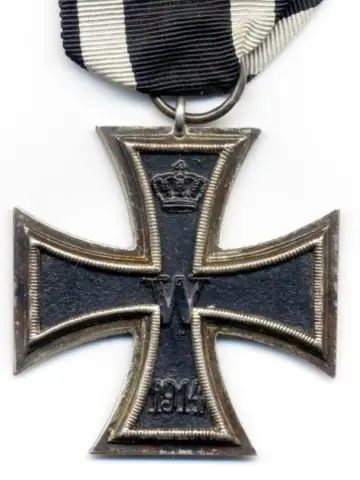
Faire un affichage volumétrique : un affichage volumétrique 3D GRATUIT à partir de restes qui traînent dans l'atelier. Il s'agit de mon premier instructable, alors veuillez être indulgent. L'affichage a une très faible résolution, 4 x 4 x temps. écran un peu. J'ai inclus