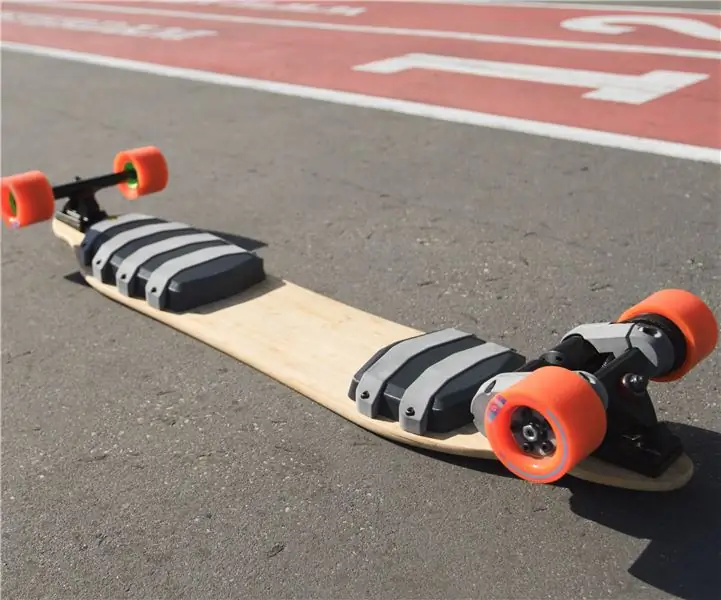
Table des matières:
2025 Auteur: John Day | [email protected]. Dernière modifié: 2025-01-23 14:46
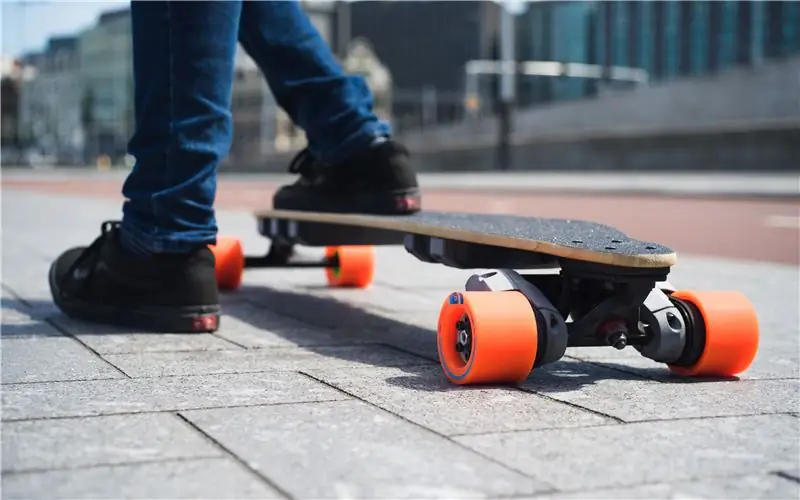
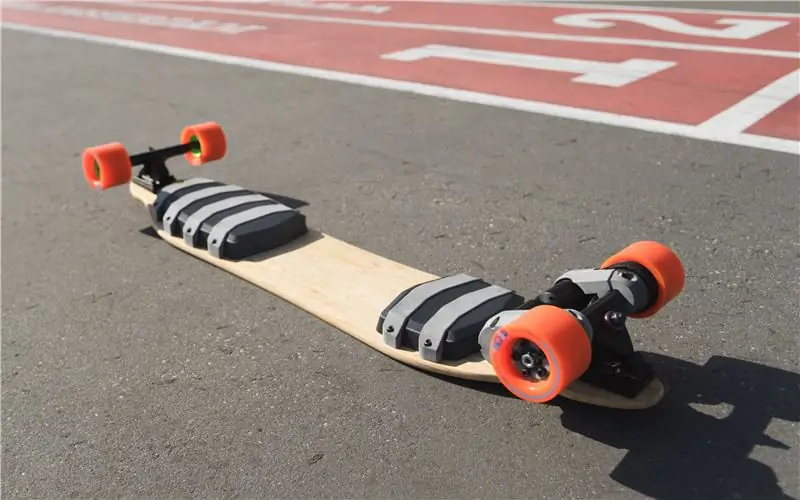
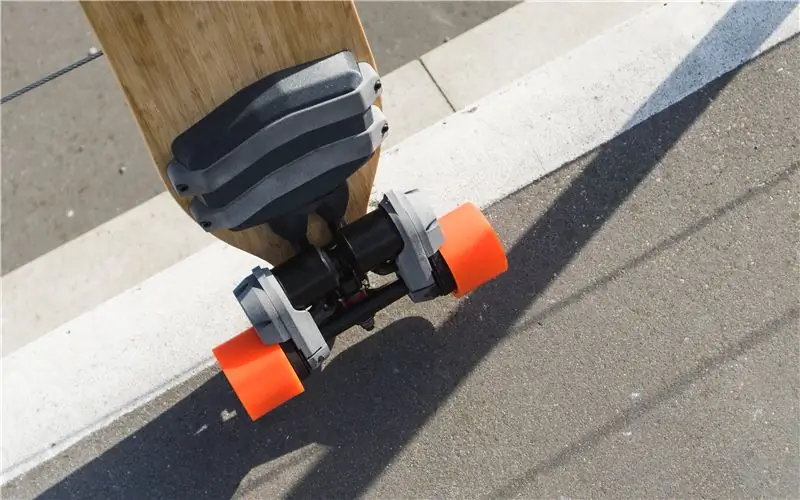
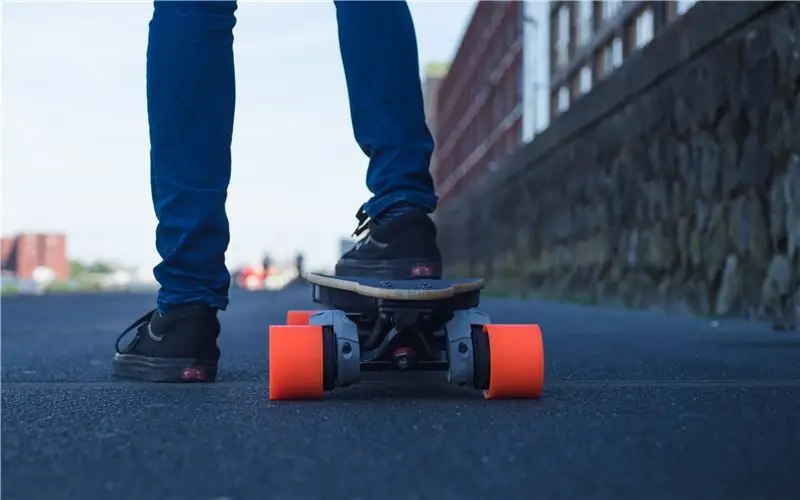
Ce Instructable est un aperçu du processus de construction du Fusion E-Board que j'ai conçu et construit tout en travaillant chez 3D Hubs. Le projet a été mandaté pour promouvoir la nouvelle technologie HP Multi-Jet Fusion offerte par 3D Hubs, et pour montrer plusieurs technologies d'impression 3D et comment elles peuvent être combinées efficacement.
J'ai conçu et construit un longboard motorisé électrique, qui peut être utilisé pour des trajets courts à modérés ou combiné avec les transports en commun pour offrir une autonomie beaucoup plus large. Il a une vitesse de pointe élevée, est très maniable et se transporte facilement lorsqu'il n'est pas utilisé.
Étape 1: Processus de conception
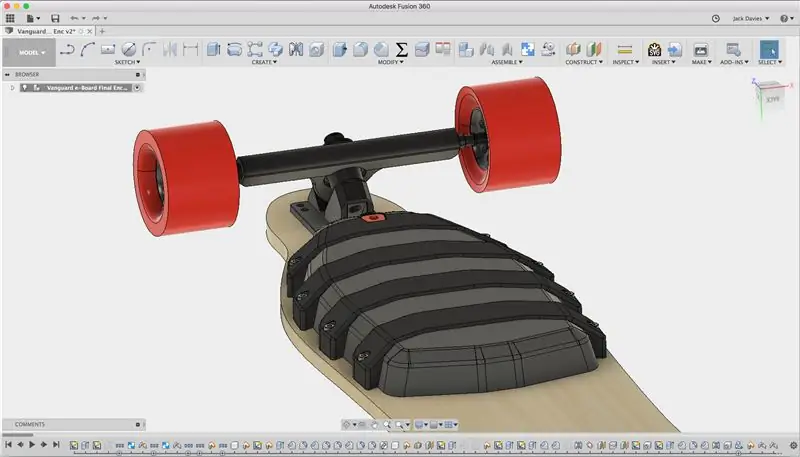
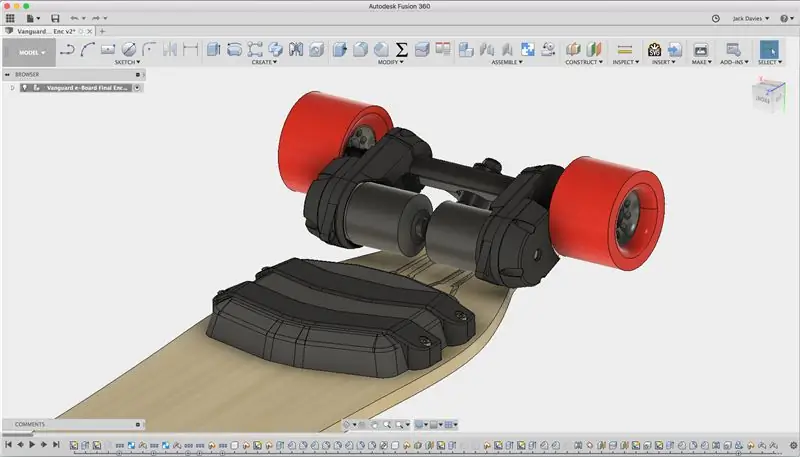
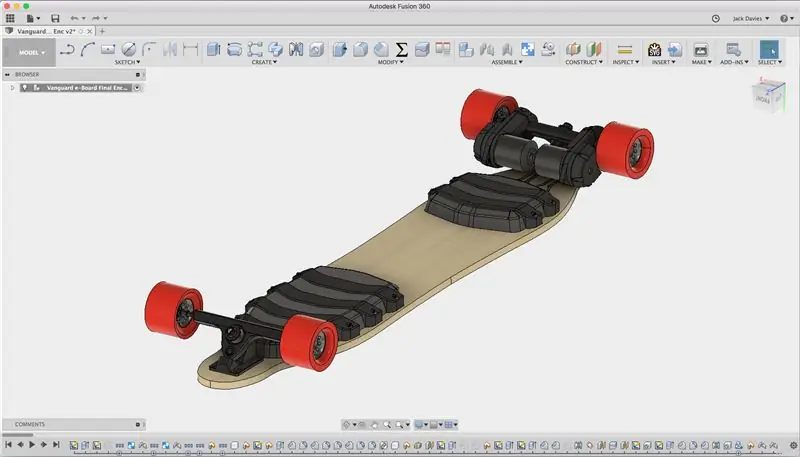
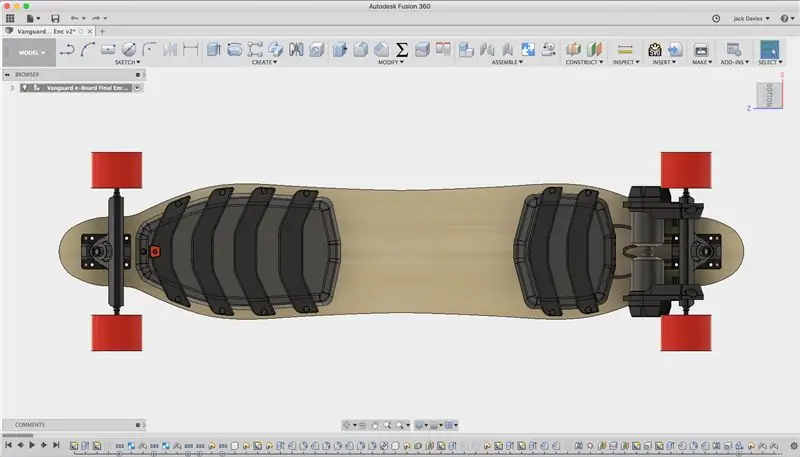
J'ai commencé le projet en identifiant les principaux composants standards du longboard; camions, pont et roues. Il s'agissait de pièces standard, je les ai donc utilisées comme point de départ de la conception. La première étape consistait à concevoir la transmission, cela comprend les supports de moteur, la configuration des engrenages et certaines modifications des camions. La taille et la position des supports de moteur dicteraient la taille et l'emplacement des boîtiers, il était donc important que cela soit terminé en premier. J'ai calculé les exigences de vitesse de pointe et de couple souhaitées, ce qui m'a ensuite permis de sélectionner les moteurs et la batterie de la carte. Le rapport d'engrenage a également été calculé et les tailles de poulie ont été sélectionnées, ainsi que la longueur de la courroie d'entraînement. Cela m'a permis de déterminer la taille correcte des supports de moteur qui ont assuré une courroie bien tendue.
L'étape suivante consistait à concevoir les boîtiers de la batterie et du contrôleur de vitesse (ESC). Le pont sélectionné est principalement composé de bambou, il est donc assez flexible, se pliant sensiblement au milieu. Cela a l'avantage d'être confortable à conduire, car il absorbe les bosses de la route et ne les transfère pas au cycliste. Cependant, cela signifie également qu'un boîtier divisé est nécessaire pour loger la batterie et l'électronique, car un boîtier pleine longueur ne pourrait pas fléchir avec la carte et entrerait en contact avec le sol pendant le fonctionnement. Les variateurs électroniques de vitesse (ESC) ont été placés au plus près des moteurs en raison de contraintes électriques. Étant donné que les moteurs sont attachés via les camions, la position change pendant les virages, de sorte que l'enceinte a dû être conçue pour permettre le dégagement des moteurs.
Le système de batterie était placé à l'autre extrémité du pont et abritait l'électronique liée à l'alimentation. Cela comprenait la batterie, composée de 20 cellules Lithium ion 18650, le système de gestion de la batterie, l'interrupteur marche/arrêt et la prise de charge.
J'ai utilisé Autodesk Fusion360 pour l'ensemble du processus de conception, ce logiciel m'a permis de modéliser rapidement des composants à l'intérieur de l'assemblage principal, ce qui a considérablement accéléré le temps de développement. J'ai également utilisé les fonctionnalités de simulation de Fusion360 pour m'assurer que les pièces seraient suffisamment solides, en particulier les supports de moteur. Cela m'a permis de réduire réellement la taille des supports car je pouvais vérifier les exigences de résistance et de déflexion et retirer le matériau tout en maintenant un facteur de sécurité approprié. Une fois le processus de conception terminé, il était très facile d'exporter les pièces individuelles pour l'impression 3D.
Étape 2: Transmission
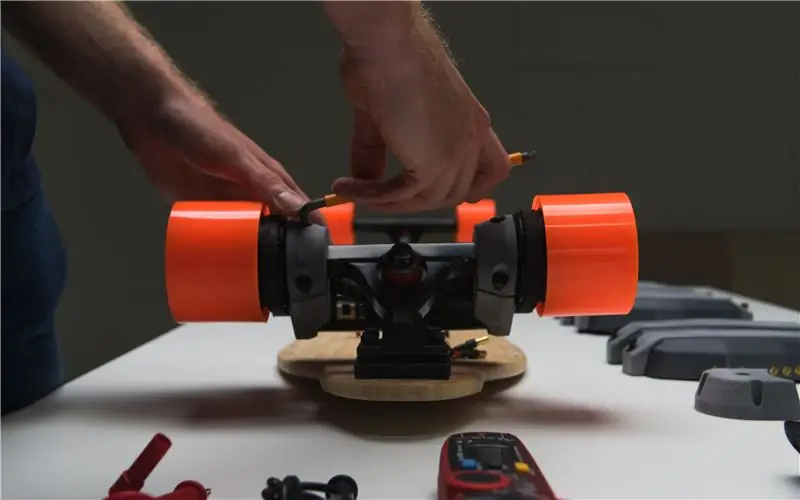
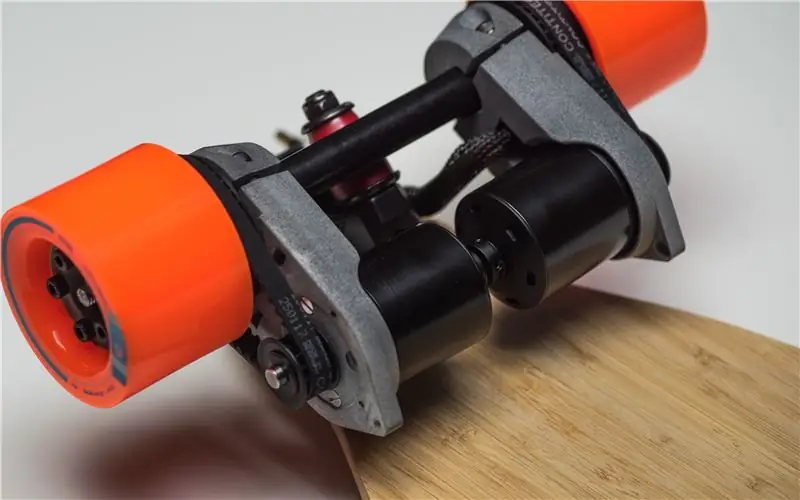
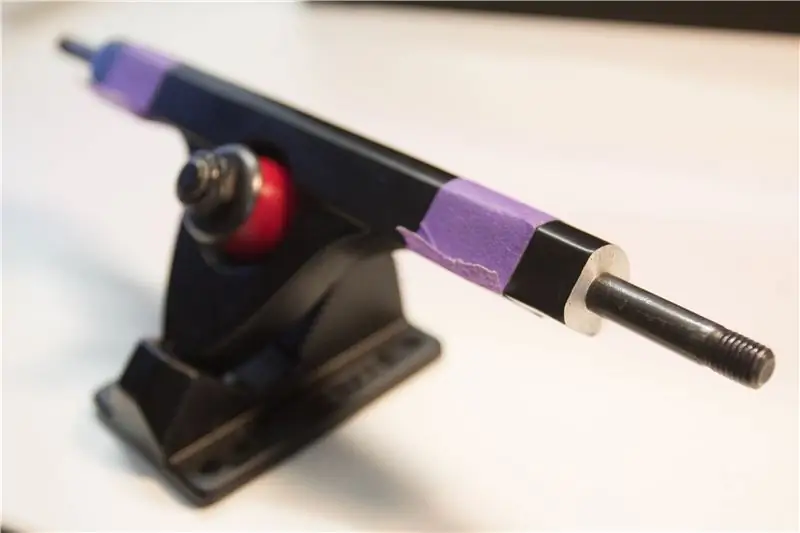
J'ai d'abord terminé la construction de la transmission, afin d'assurer un dégagement approprié pour le boîtier électronique. J'ai choisi les camions Caliber à utiliser car ils ont un profil carré qui était parfait pour fixer les supports de moteur sur. Cependant, l'essieu était légèrement trop court pour permettre aux deux moteurs d'être utilisés sur le même camion, j'ai donc dû le rallonger pour permettre aux roues de s'adapter.
J'y suis parvenu en coupant une partie du corps de suspension de camion en aluminium, exposant davantage l'essieu en acier. J'ai ensuite coupé la majeure partie de l'axe, laissant environ 10 mm que je pouvais ensuite enfiler avec une matrice M8.
Un coupleur pourrait alors être vissé et un autre axe fileté ajouté à cela, prolongeant efficacement l'axe. J'ai utilisé du composé de retenue Loctite 648 pour fixer de façon permanente le coupleur et le nouvel axe pour m'assurer qu'il ne se dévisse pas pendant l'utilisation. Cela a permis aux deux moteurs de s'adapter sur le camion et a fourni beaucoup d'espace pour les roues.
La transmission a été principalement imprimée à l'aide de la technologie HP Multi-Jet Fusion, pour assurer la rigidité et la résistance lors des accélérations et des freinages élevés, où les forces les plus importantes seraient transférées.
Une poulie spéciale a été conçue pour se verrouiller dans les roues arrière, qui a ensuite été reliée à la poulie du moteur avec une courroie HTD 5M. Un couvercle imprimé en 3D a été ajouté pour protéger l'ensemble poulie.
Étape 3: Enclos de nervures
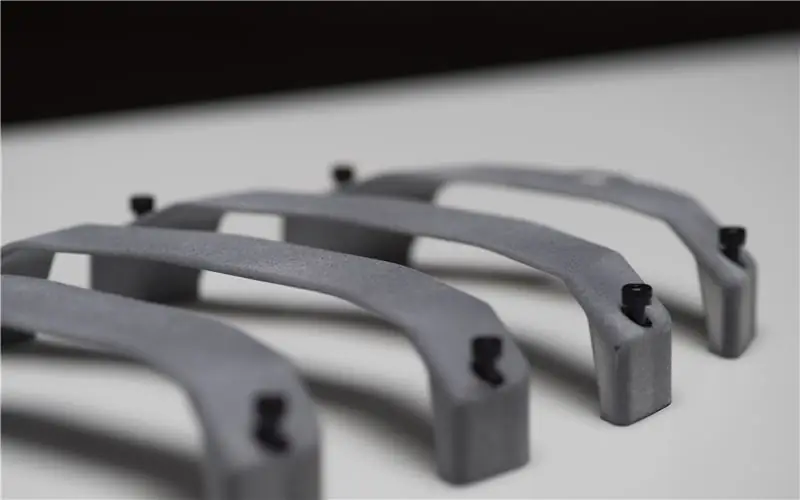
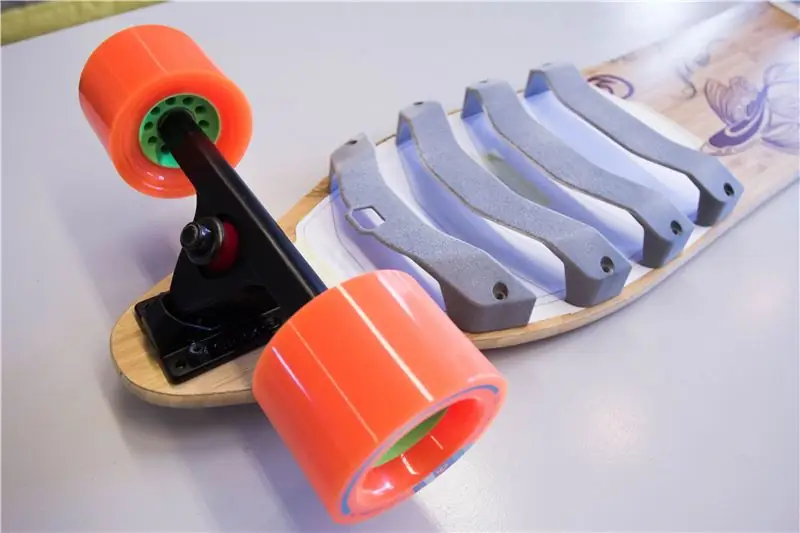
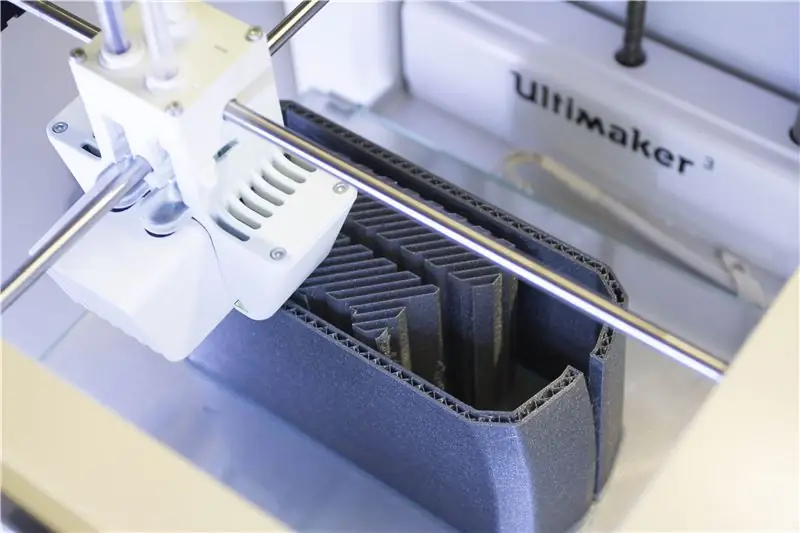
L'une des principales décisions de conception que j'ai prises a été de séparer les boîtiers, ce qui a donné un aspect épuré et permettant au pont flexible de fonctionner sans aucune rigidité supplémentaire des boîtiers. Je voulais transmettre les aspects fonctionnels de la technologie HP Multi Jet Fusion, j'ai donc décidé d'imprimer en FDM le corps principal des boîtiers, ce qui a réduit les coûts, puis j'ai utilisé les pièces HP pour les soutenir et les fixer au pont. Cela a fourni une esthétique intéressante tout en étant également très fonctionnel.
Les boîtiers imprimés FDM ont été divisés en deux pour faciliter l'impression, car le matériau de support pouvait être éliminé de la surface extérieure. La ligne de séparation a été soigneusement positionnée pour s'assurer qu'elle était cachée par la partie HP lorsqu'elle était fixée à la planche. Des trous pour les connexions du moteur ont été ajoutés et des connecteurs de balle plaqués or ont été collés en place pour
Des inserts filetés ont été intégrés dans le pont en bambou pour fixer les boîtiers à la planche et ont été poncés au ras de la surface de la planche pour s'assurer qu'il n'y avait pas d'espace entre le pont et le boîtier.
Étape 4: Électronique
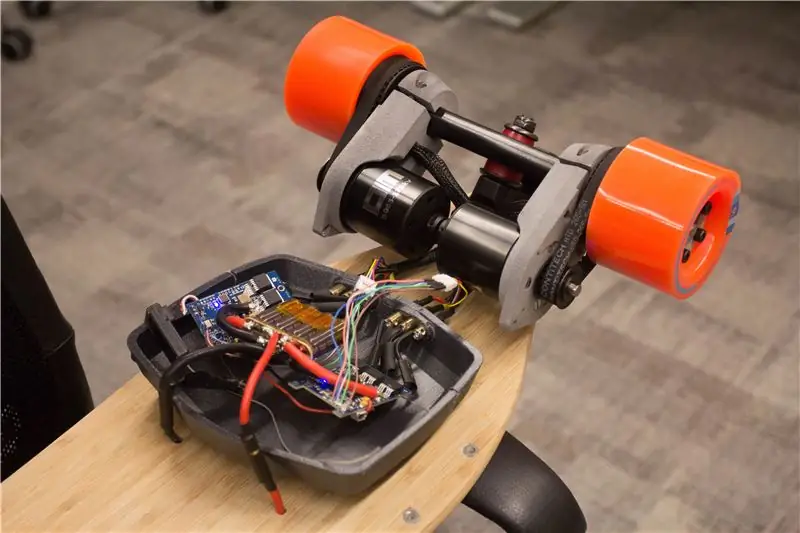
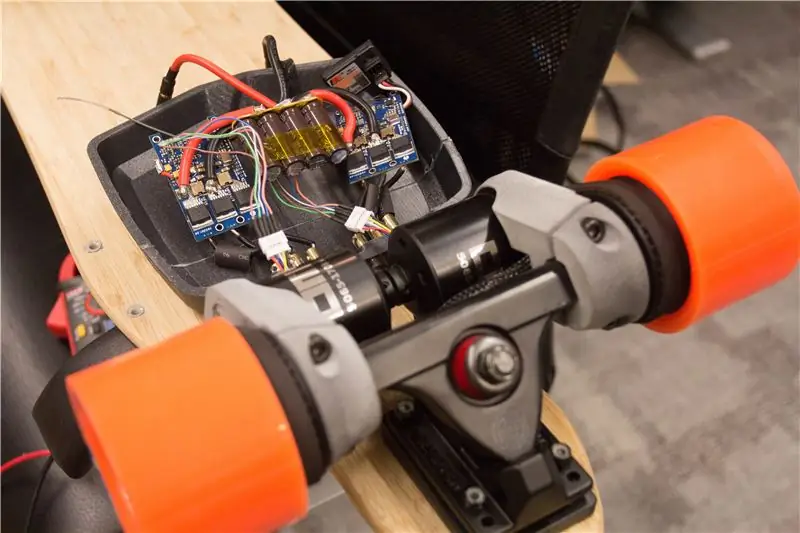
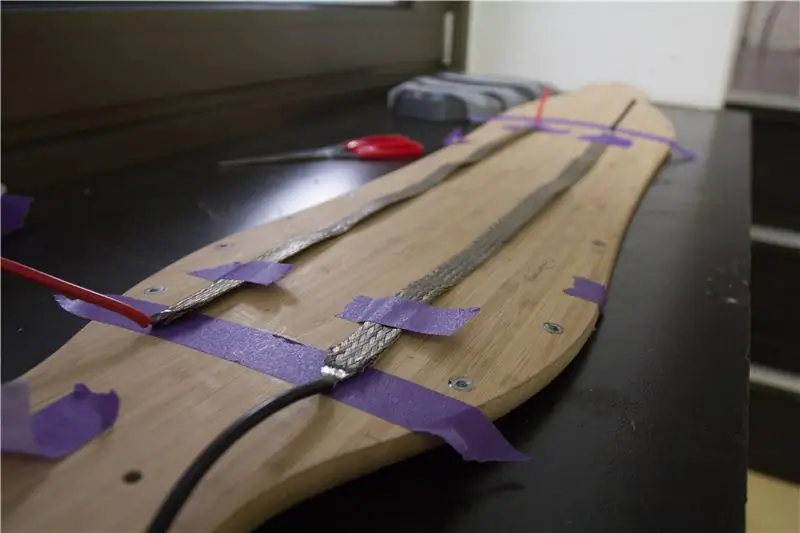
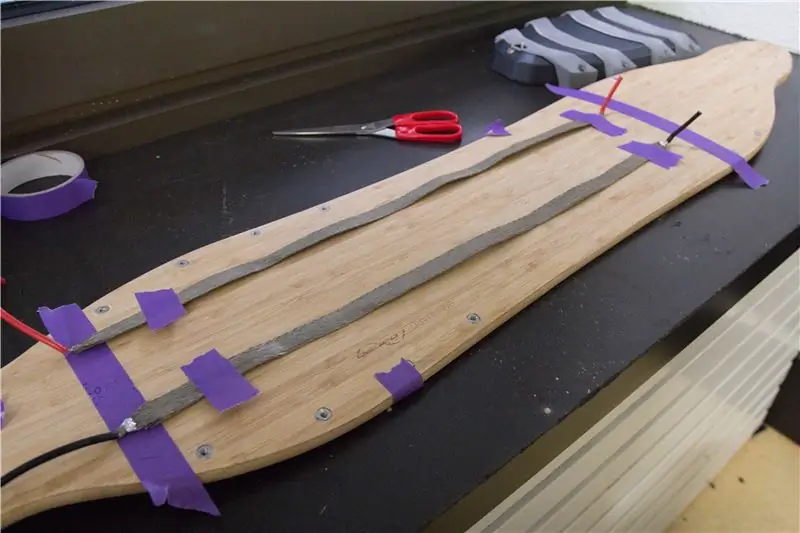
L'électronique a été soigneusement choisie pour garantir que la carte soit puissante mais aussi intuitive à utiliser. Cette carte pourrait être potentiellement dangereuse si des dysfonctionnements se produisaient, la fiabilité est donc un facteur très important.
La batterie est composée de 20 cellules individuelles au lithium-ion 18650 qui sont soudées par points ensemble pour former un pack 42v. 2 cellules sont soudées en parallèle et 10 en série; les cellules que j'ai utilisées étaient des Sony VTC6. J'ai utilisé une soudeuse par points pour souder les languettes de nickel pour former le pack, car la soudure crée trop de chaleur qui peut endommager la cellule.
L'alimentation du boîtier de la batterie a été transférée au boîtier du contrôleur de vitesse à l'aide d'un câble tressé plat qui passait juste sous le grip-tape sur la face supérieure du pont. Cela a permis de « cacher » les câbles et d'éliminer le besoin de faire passer des câbles sur la face inférieure, ce qui aurait eu l'air moche.
Comme il s'agit d'une carte à double moteur, deux contrôleurs de vitesse sont nécessaires pour contrôler indépendamment chaque moteur. J'ai utilisé le contrôleur de vitesse VESC pour cette construction, qui est un contrôleur spécialement conçu pour les skateboards électriques, ce qui le rend très fiable pour cet usage.
Les moteurs utilisés sont des moteurs 170kv 5065 pouvant produire 2200W chacun, ce qui représente beaucoup de puissance pour cette carte. Avec la configuration d'engrenage actuelle, la vitesse maximale de la planche est d'environ 35 MPH et accélère très rapidement.
La dernière étape consistait à créer une télécommande pour contrôler la carte. Un système sans fil a été préféré en raison de la facilité d'utilisation. Cependant, il était important d'assurer une fiabilité élevée de la transmission, car une baisse de la communication pouvait avoir de graves problèmes de sécurité, en particulier à haute vitesse. Après avoir testé quelques protocoles de transmission radio, j'ai décidé que la fréquence radio de 2,4 GHz serait la plus fiable pour ce projet. J'ai utilisé un émetteur de voiture RC standard, mais j'ai considérablement réduit la taille en transférant l'électronique dans un petit boîtier portable qui a été imprimé en 3D.
Étape 5: Tableau terminé et vidéo promotionnelle
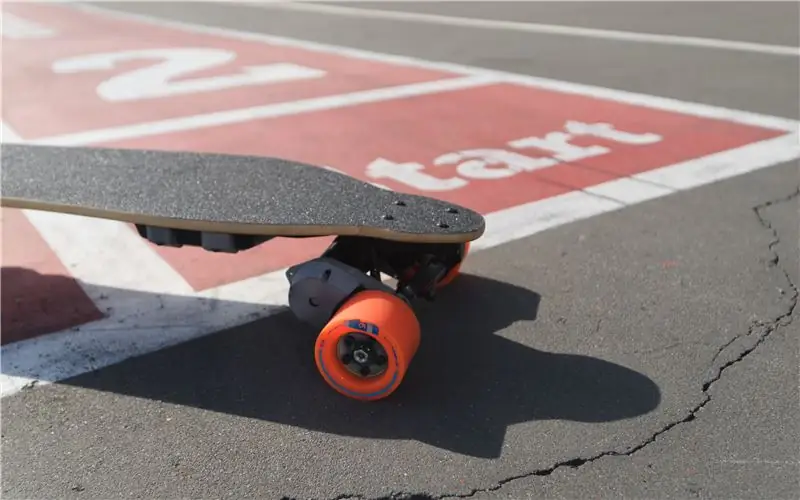
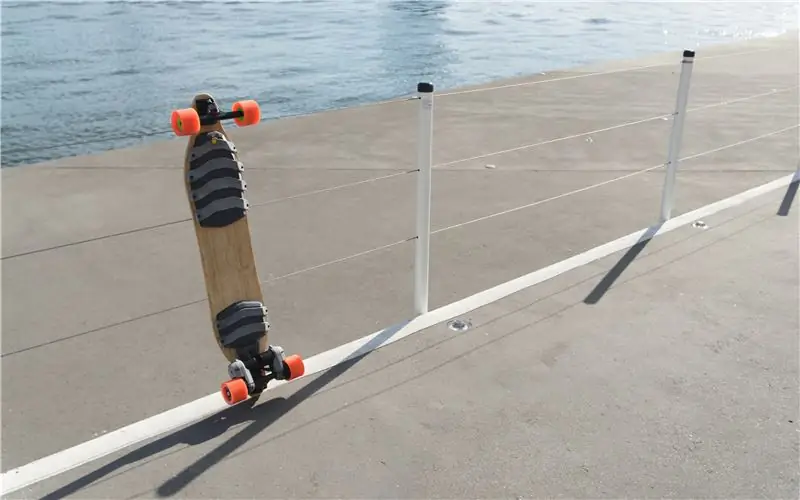
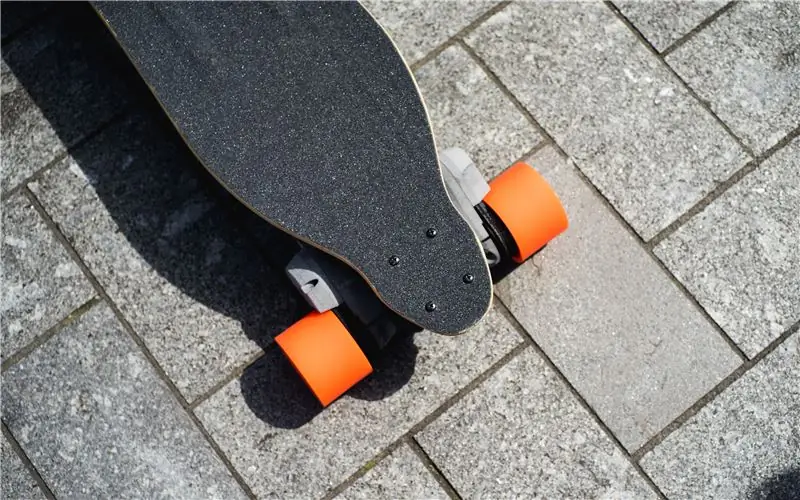
Le projet est maintenant terminé ! Nous avons créé une vidéo assez impressionnante de la planche en action, vous pouvez la regarder ci-dessous. Un grand merci à 3D Hubs pour m'avoir permis de réaliser ce projet - consultez-les ici pour tous vos besoins d'impression 3D ! 3dhubs.com
Conseillé:
Un amplificateur imprimé en 3D pour instrument de musique électrique. : 11 étapes (avec photos)
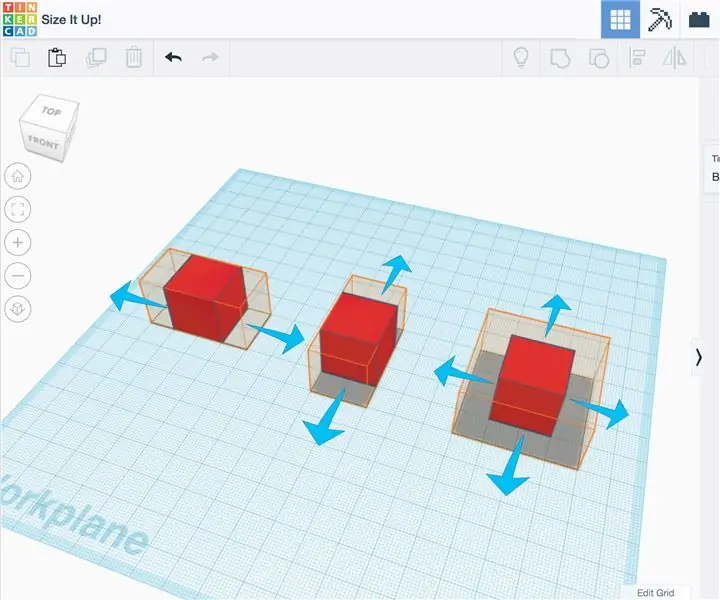
Un amplificateur imprimé en 3D pour instrument de musique électrique. : Définition du projet. J'espère créer un amplificateur imprimable à utiliser avec un violon électrique ou tout autre instrument électrique. amplificateur actif et le garder petit.Ele
Interrupteur à glissière électrique imprimé en 3D (en utilisant uniquement un trombone): 7 étapes (avec photos)
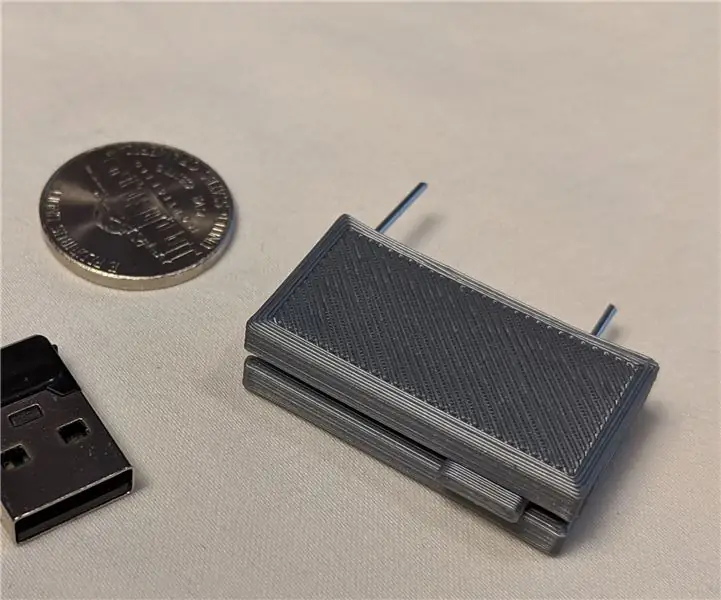
Interrupteur à glissière électrique imprimé en 3D (en utilisant uniquement un trombone): J'ai essayé de câbler ensemble mes propres petits projets électriques au fil des ans, principalement sous la forme de trombones, de papier d'aluminium et de carton bricolés avec de la colle chaude. J'ai récemment acheté une imprimante 3D (la Creality Ender 3) et je suis allé à la recherche de f
Circuit imprimé d'extension d'E/S polyvalent pour contrôler de nombreux tubes Nixie avec I2C : 9 étapes (avec photos)
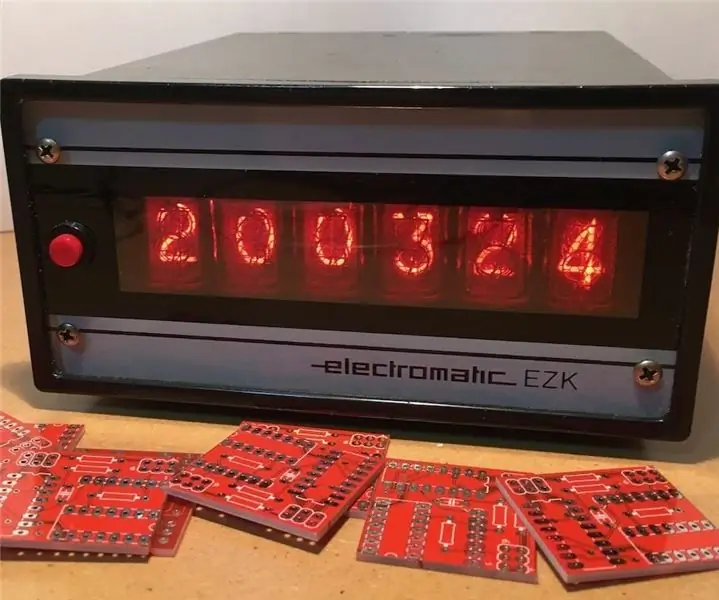
Circuit imprimé d'extension d'E/S polyvalent pour contrôler de nombreux tubes Nixie avec I2C : Actuellement, il y a beaucoup d'intérêt à donner vie aux tubes nixie vintage. De nombreux kits d'horloges à tubes nixie sont disponibles sur le marché. Il semblait y avoir même un commerce animé sur le vieux stock de tubes nixie russes. Aussi ici sur Instructables là
Curseur de caméra de suivi d'objet avec axe de rotation. Imprimé en 3D et construit sur le contrôleur de moteur à courant continu RoboClaw et Arduino : 5 étapes (avec photos)
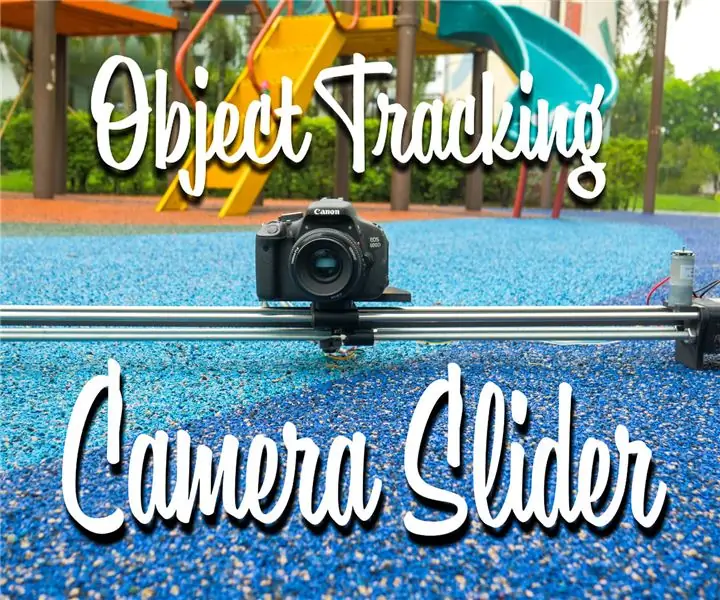
Curseur de caméra de suivi d'objet avec axe de rotation. Imprimé en 3D et construit sur le contrôleur de moteur à courant continu RoboClaw et Arduino : Ce projet est l'un de mes projets préférés depuis que j'ai pu combiner mon intérêt pour la réalisation de vidéos avec le bricolage. J'ai toujours regardé et voulu imiter ces plans cinématographiques dans les films où une caméra se déplace sur un écran tout en faisant un panoramique pour suivre le
OAREE - Imprimé en 3D - Robot évitant les obstacles pour l'enseignement de l'ingénierie (OAREE) avec Arduino : 5 étapes (avec photos)
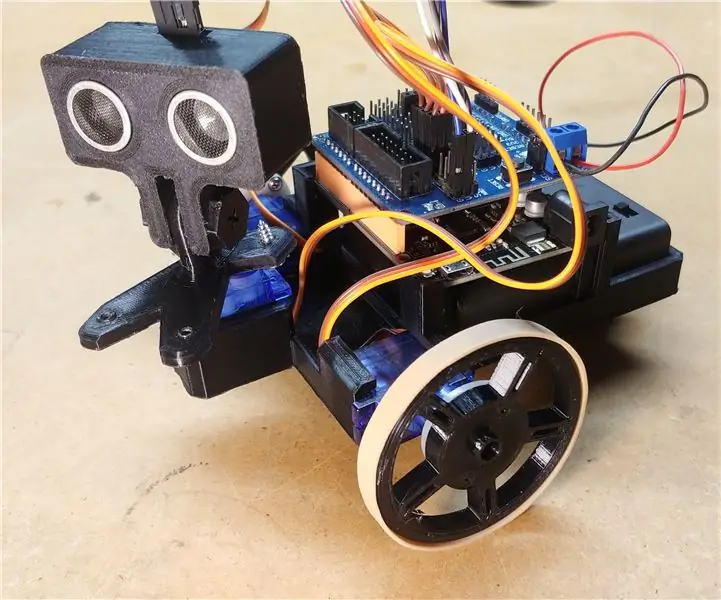
OAREE - imprimé en 3D - Robot évitant les obstacles pour l'enseignement de l'ingénierie (OAREE) avec Arduino : conception OAREE (robot évitant les obstacles pour l'enseignement de l'ingénierie) : l'objectif de cette instructable était de concevoir un robot OAR (robot évitant les obstacles) qui était simple/compact, Imprimable en 3D, facile à assembler, utilise des servos à rotation continue pour le mouvement