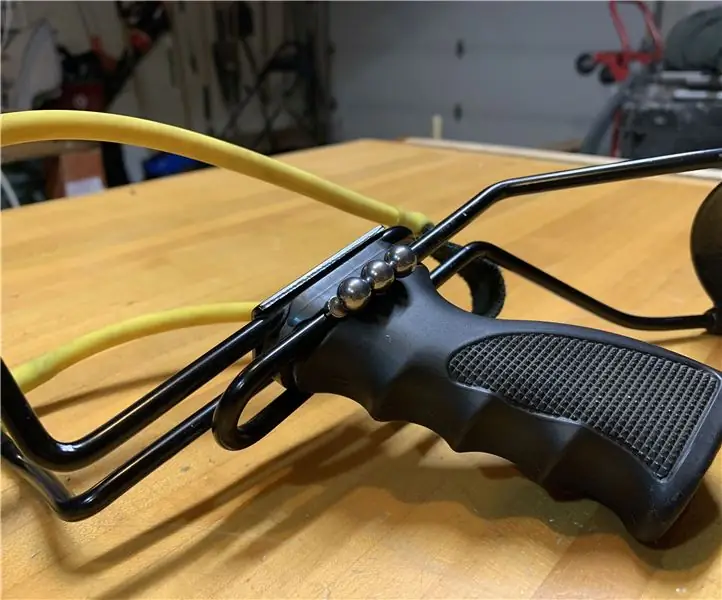
Table des matières:
2025 Auteur: John Day | [email protected]. Dernière modifié: 2025-01-23 14:45
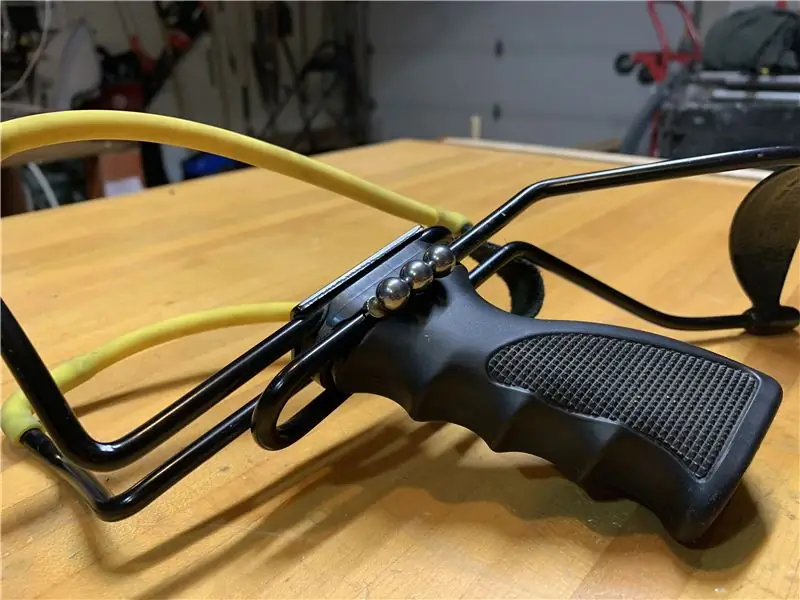
Bonjour et bienvenue dans un autre Instructable ! Dans la précédente, je vous ai montré comment j'ai créé des bobines dans KiCad à l'aide d'un script python. Ensuite, j'ai créé et testé quelques variantes de bobines pour voir laquelle fonctionne le mieux. Mon objectif est de remplacer les énormes électro-aimants de l'affichage mécanique à 7 segments par les bobines PCB.
Dans ce Instructable, je vais couvrir les bases d'un pont en H et vous montrer comment je vais l'utiliser pour contrôler les segments. Enfin, je vais vous présenter quelques-uns des ponts en H en petits emballages disponibles sur le marché.
Commençons
Étape 1: le plan
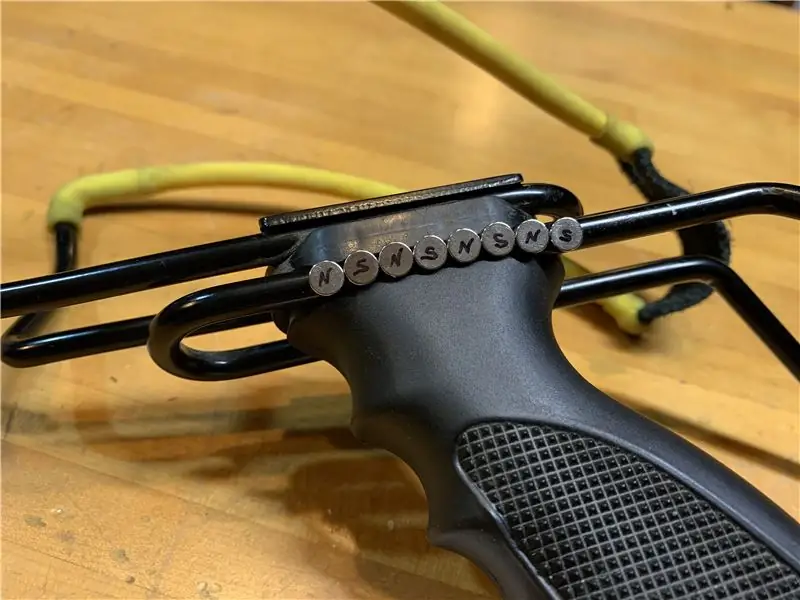
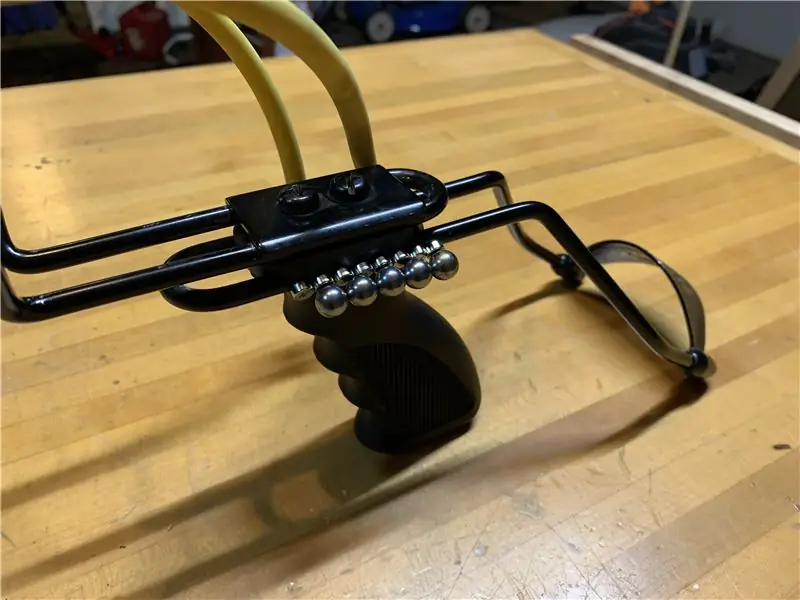
Dans la construction d'origine, j'avais pris des dispositions de telle sorte que lorsque la bobine est alimentée, elle s'oppose ou pousse l'aimant avec le segment. Mais lorsque la bobine est désexcitée, l'aimant est attiré par le noyau de l'électro-aimant et ainsi le segment revient à sa position d'origine. De toute évidence, cela ne fonctionnera pas car il n'y a pas de noyau dans la bobine PCB. J'avais en fait une bobine avec un trou au milieu pour le noyau mais cela n'a pas fonctionné.
Sans le noyau, le segment restera dans sa nouvelle position même si la bobine est hors tension. Pour ramener le segment à sa position d'origine, le courant traversant la bobine doit être inversé, ce qui à son tour renverserait les pôles et attirerait cette fois l'aimant.
Étape 2: les bases du pont en H
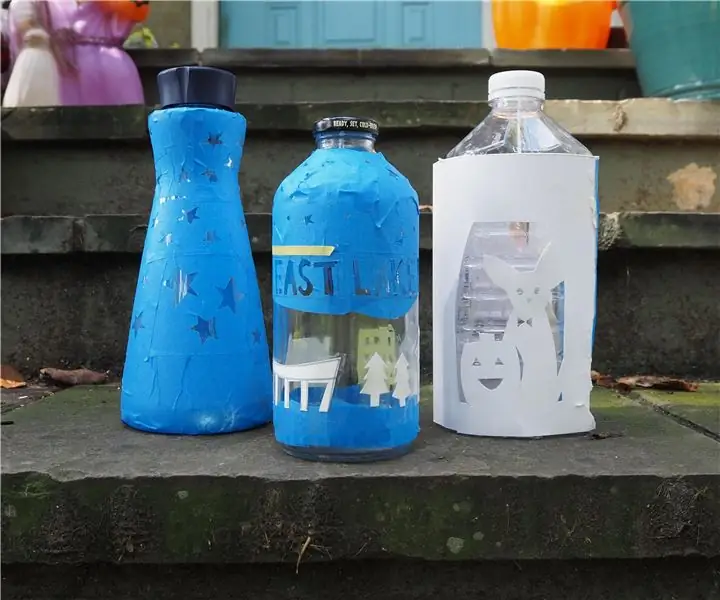
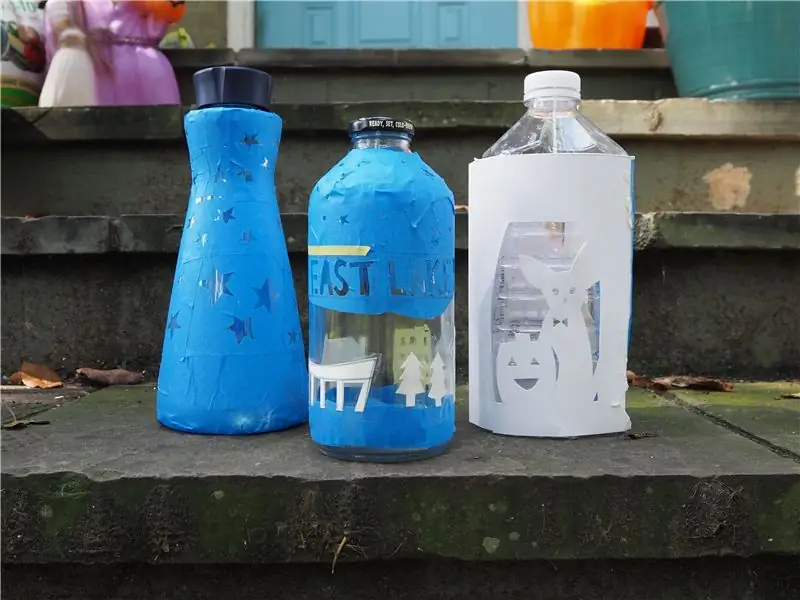
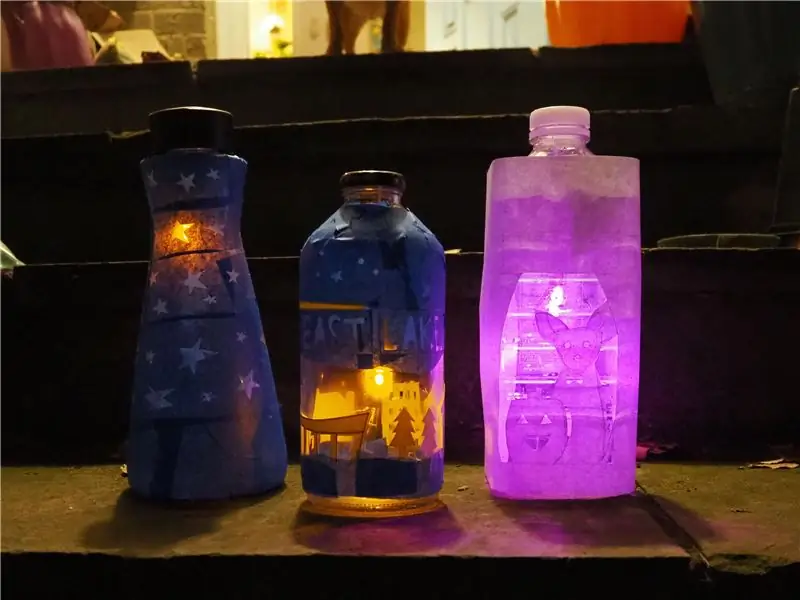
L'inversion de courant requise est réalisée à l'aide d'un circuit composé de 4 interrupteurs disposés en forme de majuscule H et d'où le nom H-Bridge. Ceci est le plus souvent utilisé pour inverser le sens de rotation d'un moteur à courant continu.
Un arrangement typique de pont en H est montré dans la 1ère image. La charge/le moteur (ou la bobine PCB dans notre cas) est placé entre les deux jambes comme indiqué.
Si les interrupteurs S1 et S4 sont fermés, le courant circule comme on le voit sur la 3ème image, et lorsque les interrupteurs S2 et S3 sont fermés, le courant circule dans le sens opposé comme on le voit sur la 4ème image.
Il faut veiller à ce que les commutateurs S1 et S3 ou S2 et S4 ne soient jamais fermés comme indiqué. Cela court-circuiterait l'alimentation électrique et pourrait endommager les commutateurs.
J'ai construit ce circuit exact sur une maquette en utilisant 4 boutons-poussoirs comme interrupteurs et un moteur comme charge. L'inversion du sens de rotation confirme que le sens du courant s'est également inversé. Super!
Mais je ne veux pas rester assis là et appuyer manuellement sur les boutons. Je veux qu'un microcontrôleur fasse le travail à ma place. Pour construire pratiquement ce circuit, nous pouvons utiliser des MOSFET comme commutateurs.
Étape 3: Petits ponts en H
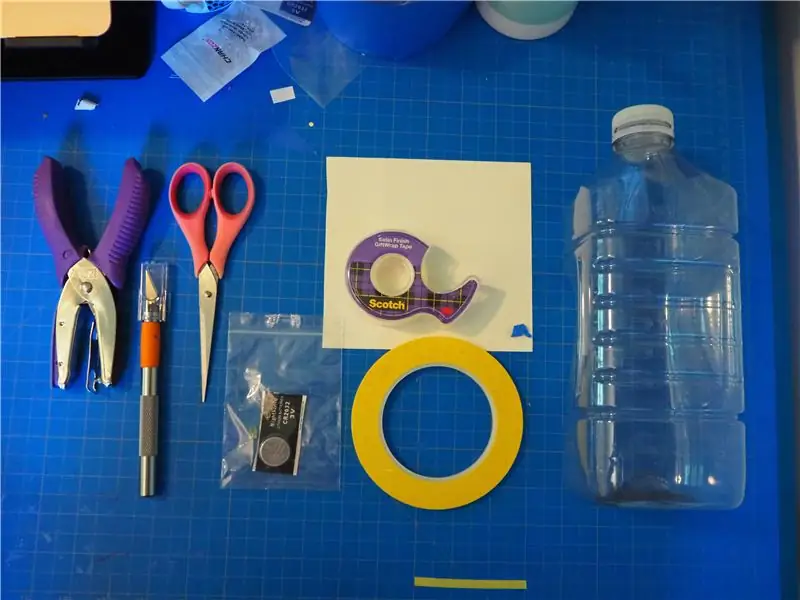
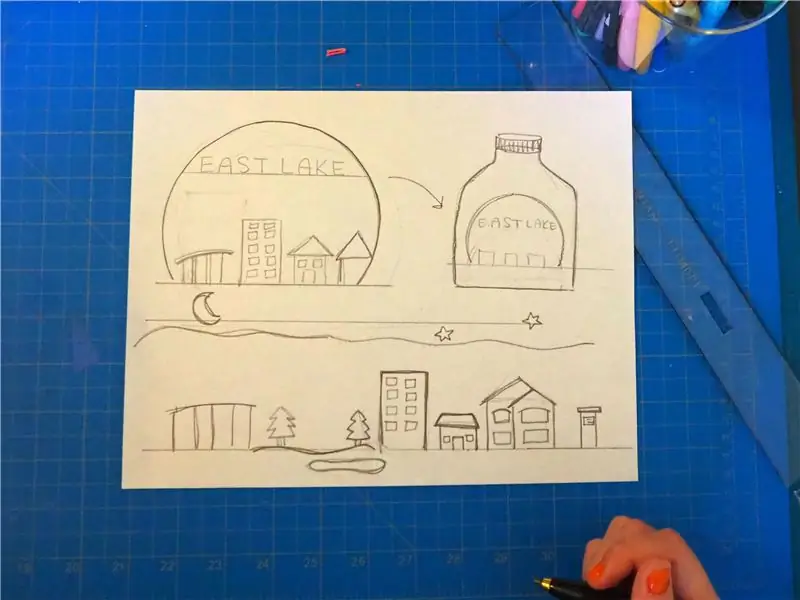
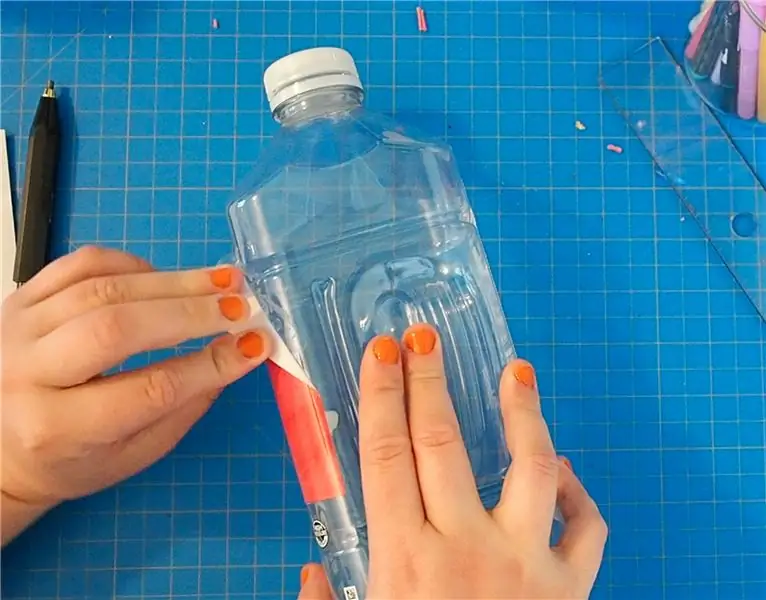
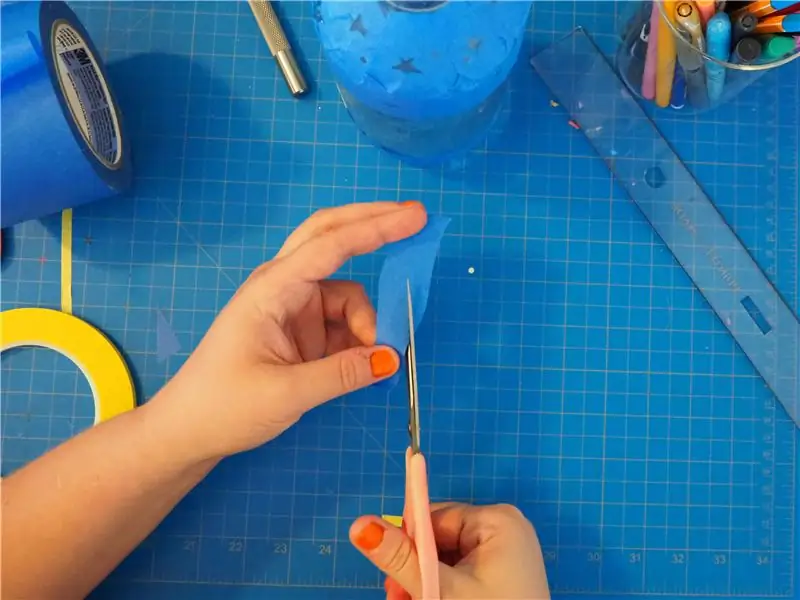
Chaque segment nécessitera 4 MOSFET. Comme vous pouvez probablement l'imaginer, le circuit de commande deviendra assez énorme pour 7 segments ainsi que d'autres composants complémentaires pour piloter la grille de chaque MOSFET, ce qui va finalement à l'encontre de mon objectif de réduire la taille de l'affichage.
Je pourrais utiliser les composants SMD mais ce serait quand même gros et compliqué. Cela aurait été beaucoup plus facile s'il y avait eu un circuit intégré dédié. Dites bonjour à PAM8016, un circuit intégré avec tous les composants mentionnés précédemment dans un petit boîtier de 1,5 x 1,5 mm !
En examinant son schéma fonctionnel dans la fiche technique, nous pouvons voir le pont en H, les pilotes de grille ainsi que la protection contre les courts-circuits et l'arrêt thermique. La direction du courant à travers la bobine peut être contrôlée en ne fournissant que deux entrées à la puce. Doux!
Mais il y a un problème. Souder une puce aussi minuscule sera un cauchemar pour une personne dont la seule expérience avec la soudure par refusion est quelques LED et résistances. Cela aussi à l'aide d'un fer à repasser ! Mais j'ai décidé de tenter le coup quand même.
Comme alternative, j'ai trouvé le DRV8837, qui fait la même chose mais est un peu plus gros. Alors que je continuais à chercher des alternatives plus faciles à souder sur LCSC, je suis tombé sur FM116B qui est encore la même chose mais avec moins de puissance de sortie et dans un boîtier SOT23 qui peut même être soudé à la main. Malheureusement, j'ai découvert plus tard que je ne pouvais pas le commander en raison de problèmes d'expédition.
Étape 4: Faire des tableaux de répartition
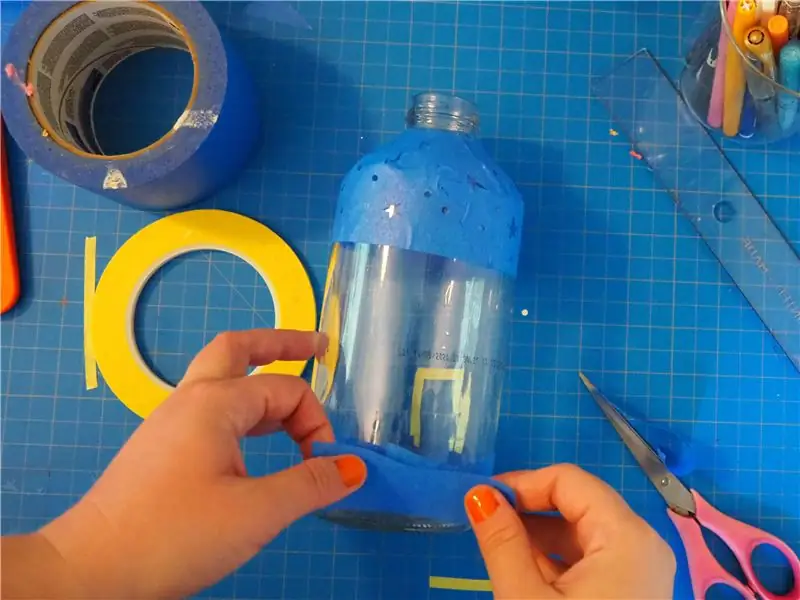
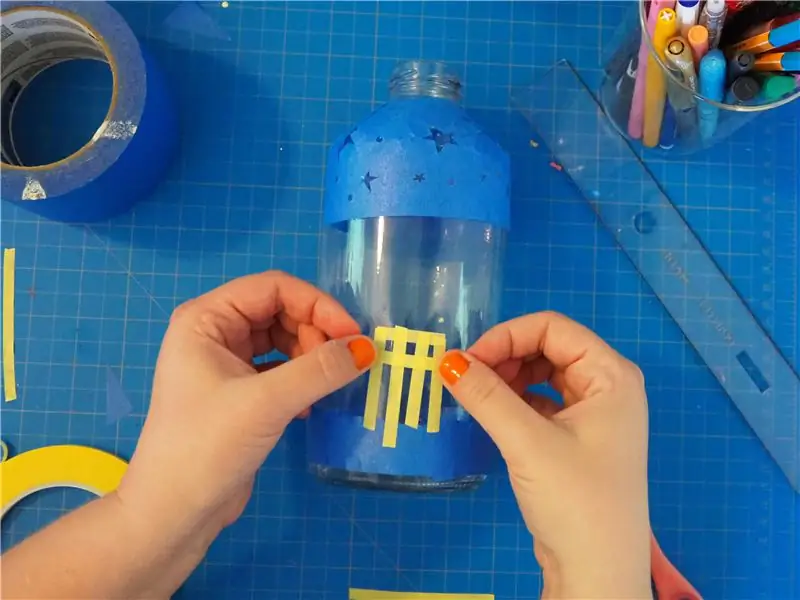
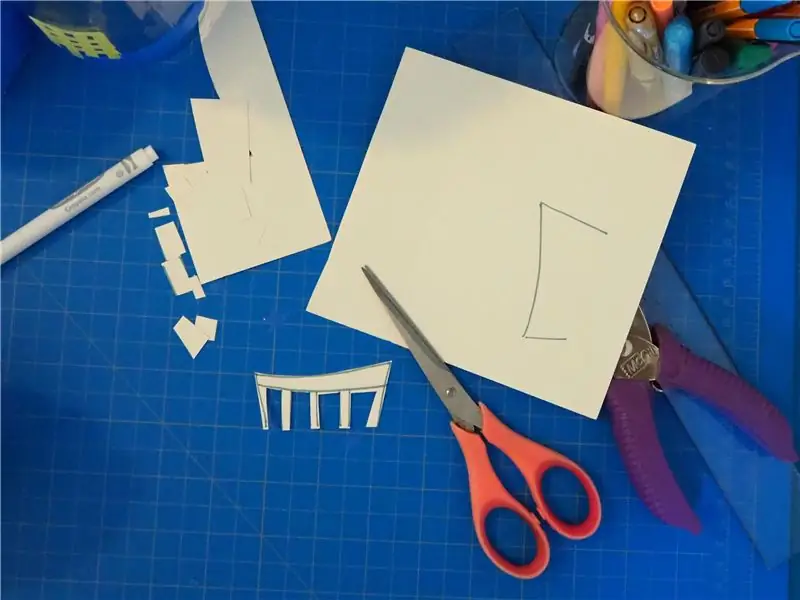
Avant d'implémenter les circuits intégrés dans le PCB final, je voulais d'abord tester si je suis capable de contrôler les segments comme je le souhaite. Comme vous pouvez le voir, les circuits intégrés ne sont pas compatibles avec la planche à pain et mes compétences en soudure ne sont pas aussi bonnes pour y souder des fils de cuivre directement. C'est pourquoi j'ai décidé de faire un tableau de bord car ils ne sont pas facilement disponibles sur le marché. Une carte de dérivation « déploie » les broches du circuit intégré sur une carte de circuit imprimé qui possède ses propres broches parfaitement espacées pour une planche à pain sans soudure, vous donnant un accès facile pour utiliser le circuit intégré.
Un coup d'œil à la fiche technique aide à décider quelles broches doivent être cassées. Par exemple, dans le cas du DRV8837:
- Le circuit intégré a deux broches pour l'alimentation, une pour la charge/le moteur (VM) et une autre pour la logique (VCC). Puisque j'utiliserai 5V pour les deux, je connecterai les deux broches ensemble.
- Vient ensuite la broche nSleep. Il s'agit d'une broche basse active, c'est-à-dire que la connexion à GND mettra le circuit intégré en mode veille. Je veux que le circuit intégré soit actif tout le temps et je le connecterai donc en permanence au 5V.
- Les entrées ont des résistances pull-down internes. Il n'est donc pas nécessaire de fournir ceux qui figurent au tableau.
- La fiche technique indique également de mettre un condensateur de dérivation de 0,1 uF sur les broches VM et VCC.
En gardant les points ci-dessus à l'esprit, j'ai conçu une carte de dérivation pour les circuits intégrés dans KiCad et envoyé les fichiers Gerber à JLCPCB pour la fabrication de PCB et de stencil. Cliquez ici pour télécharger les fichiers Gerber.
Étape 5: Contrôle d'un segment
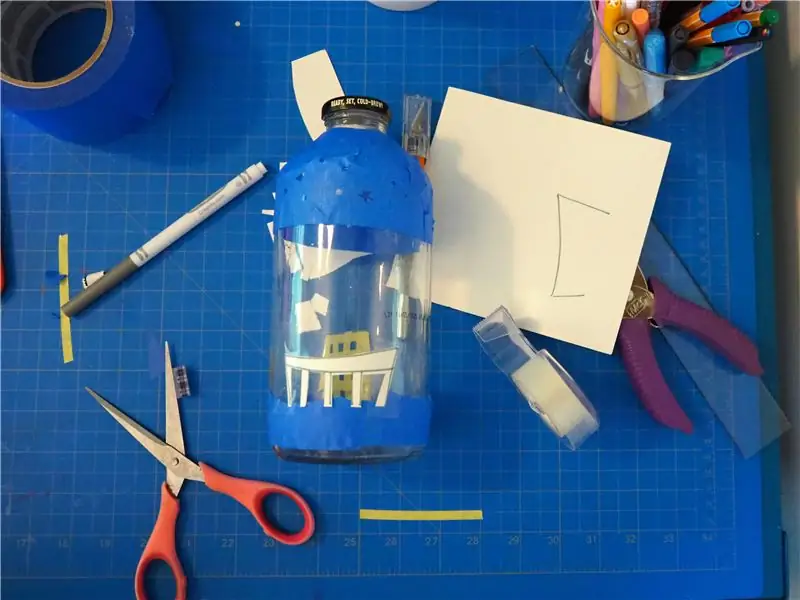
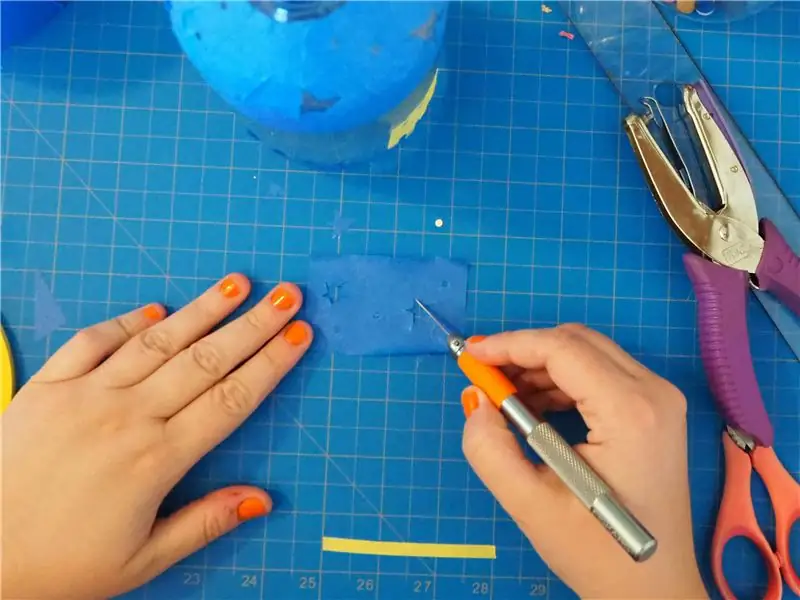
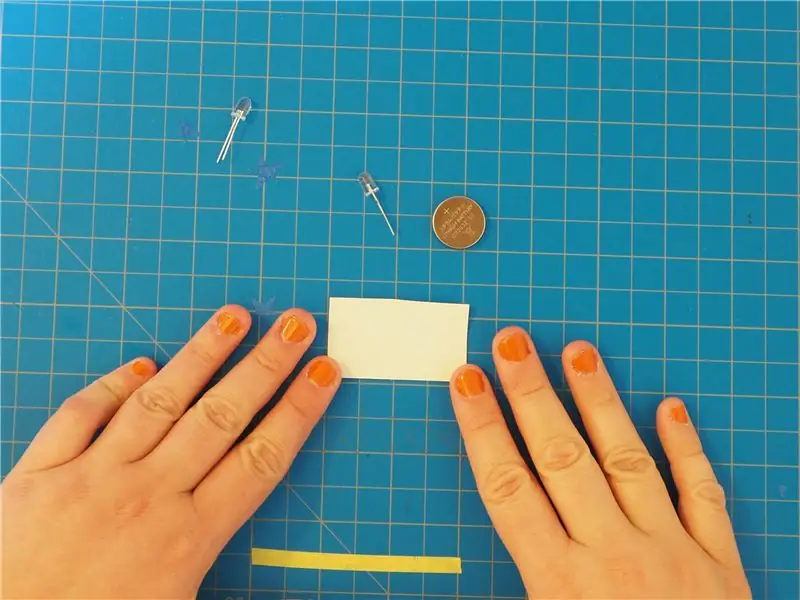
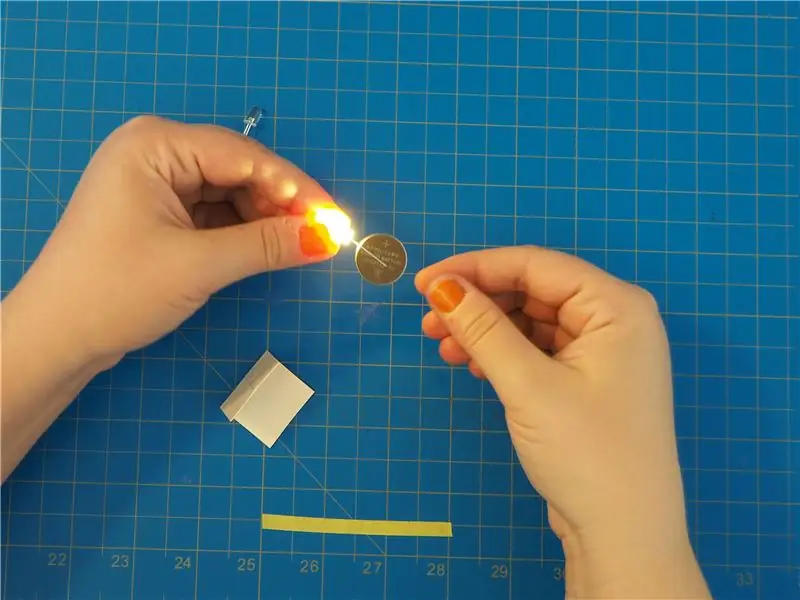
Une fois que j'ai reçu mes PCB et mon pochoir de JLCPCB, j'ai assemblé la carte. C'était la première fois que j'utilisais un pochoir et que je soudais de minuscules circuits intégrés. Doigts croisés! J'ai utilisé un fer à repasser comme plaque chauffante pour refondre la pâte à souder.
Mais peu importe combien j'ai essayé, il y avait toujours un pont de soudure sous PAM8016. Heureusement, le DRV8837 a été un succès du premier coup !
Ensuite, je teste si je suis capable de contrôler le segment. Selon la fiche technique du DRV8837, je dois fournir HIGH ou LOW aux broches IN1 et IN2. Lorsque IN1 = 1 & IN2 = 0, le courant circule dans un sens et lorsque IN1 = 0 & IN2 = 1, le courant circule dans le sens opposé. Ça marche!
La configuration ci-dessus nécessite deux entrées d'un microcontrôleur et 14 entrées pour un affichage complet. Étant donné que les deux entrées sont toujours complémentaires l'une de l'autre, c'est-à-dire que si IN1 est HAUT alors IN2 est BAS et vice versa, au lieu de donner deux entrées séparées, nous pourrions directement envoyer un signal (1 ou 0) à une entrée tandis que l'autre entrée est donnée après être passé par une porte NON qui l'inverse. De cette façon, nous pouvons contrôler le segment/bobine en utilisant une seule entrée comme un affichage normal à 7 segments. Et cela a fonctionné comme prévu !
Étape 6: Quelle est la prochaine étape ?
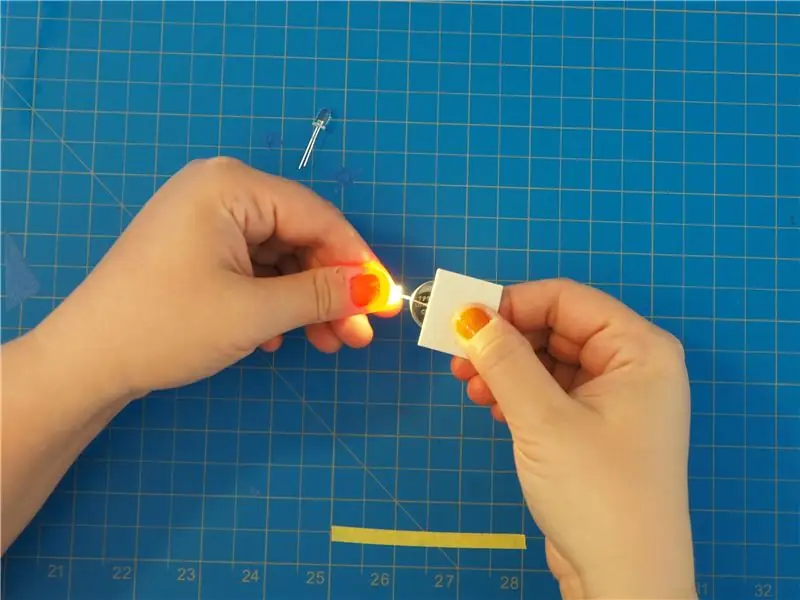
Alors c'est tout pour l'instant ! La prochaine et dernière étape consisterait à combiner les 7 bobines et les pilotes H-Bridge (DRV8837) sur un seul PCB. Alors restez à l'écoute pour cela! Faites-moi part de vos réflexions et suggestions dans les commentaires ci-dessous.
Merci d'être resté jusqu'au bout. J'espère que vous aimez tous ce projet et que vous avez appris quelque chose de nouveau aujourd'hui. Abonnez-vous à ma chaîne YouTube pour plus de projets de ce type.
Conseillé:
MOSTER FET - Pilotes de lit chauffant pour imprimante 3d MOSFET 500Amp 40 Volts : 7 étapes (avec photos)
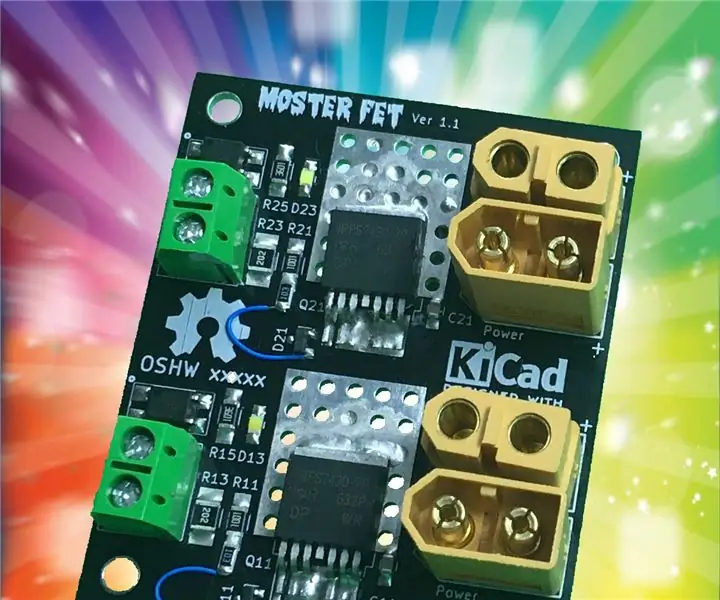
MOSTER FET - Double 500Amp 40 Volt MOSFET Imprimante 3d Pilotes de lit chauffant : Vous avez probablement cliqué sur cette vache sacrée pensante, 500 AMPS !!!!!. Pour être honnête, la carte MOSFET que j'ai conçue ne pourra pas faire 500 ampères en toute sécurité. Cela pourrait pendant un court instant, juste avant qu'il ne s'enflamme avec enthousiasme. Cela n'a pas été conçu pour être un clev
Comment contrôler le commutateur intelligent de base Sonoff basé sur ESP8266 avec un smartphone : 4 étapes (avec photos)
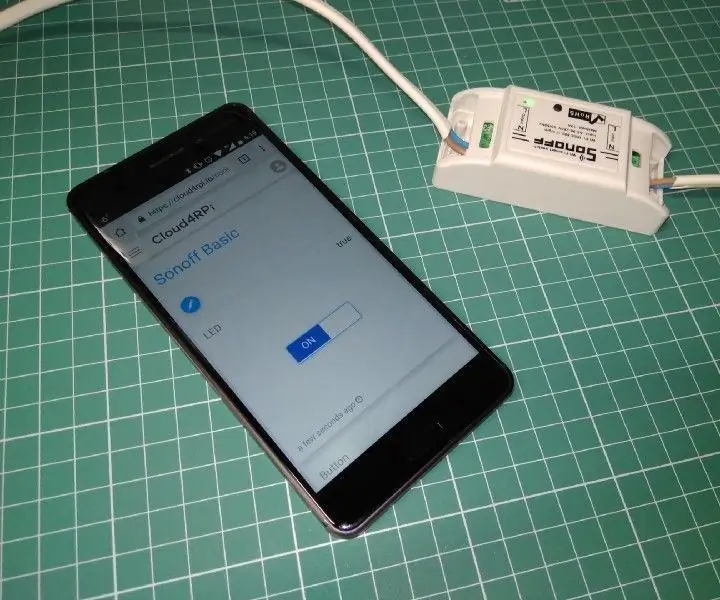
Comment contrôler le commutateur intelligent de base Sonoff basé sur ESP8266 avec un smartphone : Sonoff est une gamme d'appareils pour Smart Home développée par ITEAD. L'un des appareils les plus flexibles et les moins chers de cette gamme est le Sonoff Basic. Il s'agit d'un commutateur compatible Wi-Fi basé sur une excellente puce, ESP8266. Cet article décrit comment configurer le Cl
Construire un casque avec les pilotes Beats Studio 2.0 : 7 étapes (avec photos)
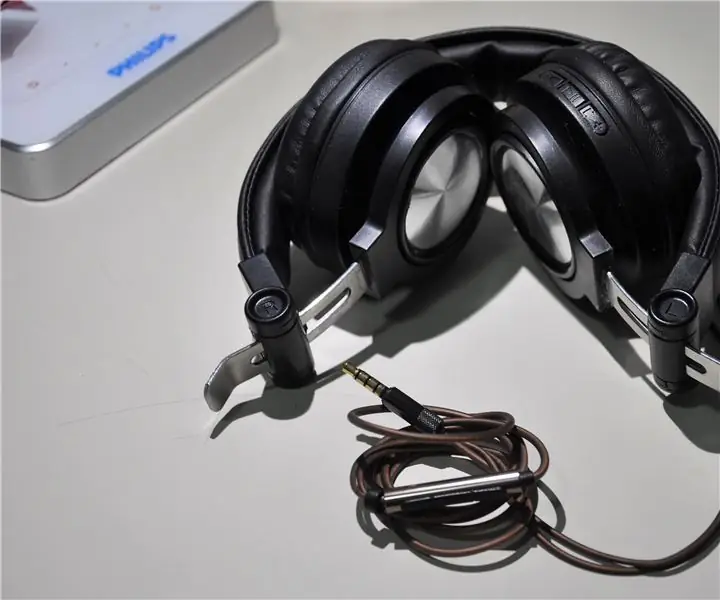
Construire un casque avec les pilotes Beats Studio 2.0 : Je construis ce casque à partir de 30 composants avec une paire de pilotes 40 mm de Beats Studio 2.0. Assembler un casque à partir de zéro est plus ou moins amusant. Comme dans mes autres projets de bricolage de casques, les lecteurs peuvent avoir des difficultés à évaluer la qualité sonore
TinyPi - le plus petit appareil de jeu basé sur Raspberry Pi au monde : 8 étapes (avec photos)
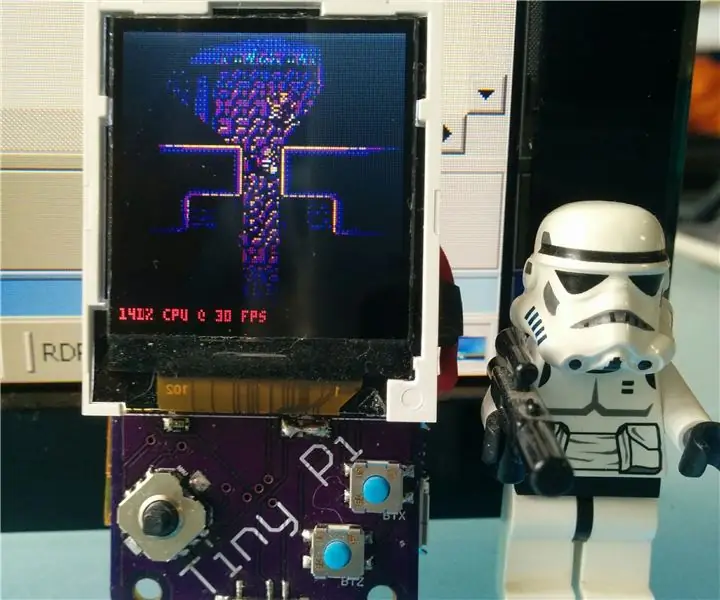
TinyPi - le plus petit appareil de jeu basé sur Raspberry Pi au monde : J'ai donc joué avec la fabrication de PCB personnalisés pour le Raspberry Pi pendant un certain temps maintenant, et ce qui a commencé comme une blague est devenu un défi pour voir jusqu'où je pouvais aller. Le TinyPi est né. , il est basé sur un Raspberry Pi Zero, et rentre presque dans le sa
Construisez un très petit robot : créez le plus petit robot à roues du monde avec une pince. : 9 étapes (avec photos)
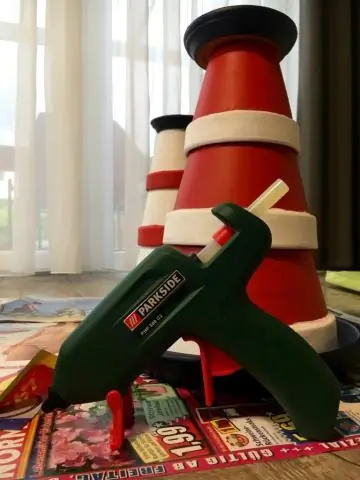
Construisez un très petit robot : créez le plus petit robot à roues du monde avec une pince. : Construisez un robot de 1/20 de pouce cube avec une pince qui peut ramasser et déplacer de petits objets. Il est contrôlé par un microcontrôleur Picaxe. À ce stade, je pense qu'il s'agit peut-être du plus petit robot à roues au monde doté d'une pince. Cela fera sans aucun doute ch