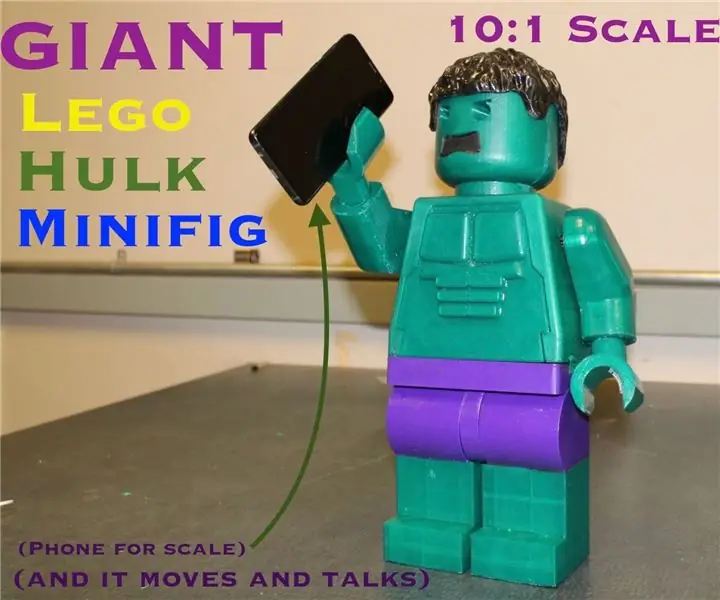
Table des matières:
- Étape 1: Nomenclature
- Étape 2: Diviser pour régner
- Étape 3: [Facultatif] Conception et impression 3D: Conception
- Étape 4: Conception et impression 3D: Impression 3D
- Étape 5: [Facultatif] Lissage des impressions 3D
- Étape 6: Assemblage [partiel]: Assemblage de la tête
- Étape 7: Électronique: Souder le PCB et la majeure partie de l'électronique
- Étape 8: Électronique: Adaptateur de connecteur de batterie
- Étape 9: Code: Compiler et télécharger le code
- Étape 10: Assemblage: ajustement des composants électroniques
- Étape 11: Assemblage: Montage des servomoteurs
- Étape 12: Assemblage: enclenchez les pattes
- Étape 13: Assemblage: Torse
- Étape 14: Votez pour moi
2025 Auteur: John Day | [email protected]. Dernière modifié: 2025-06-01 06:09
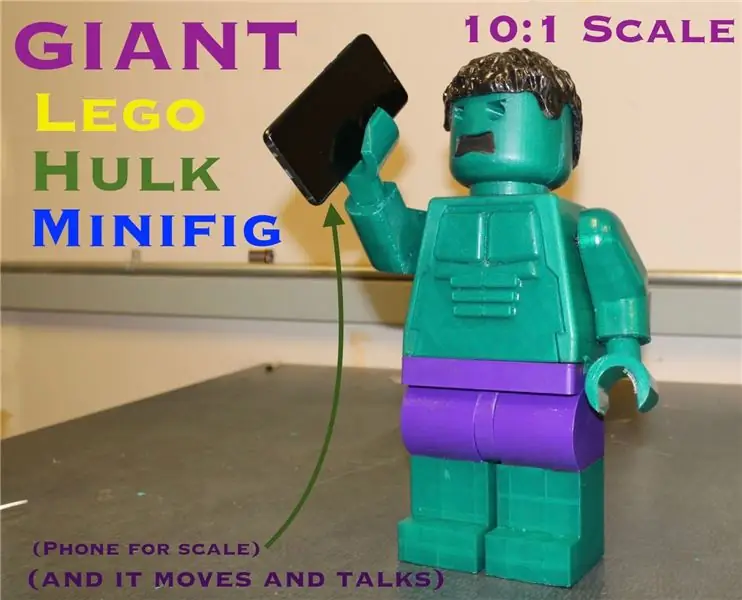


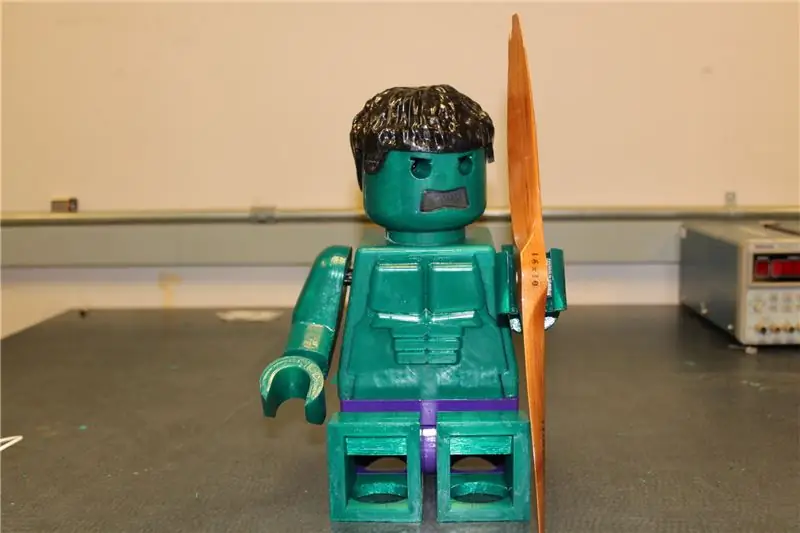
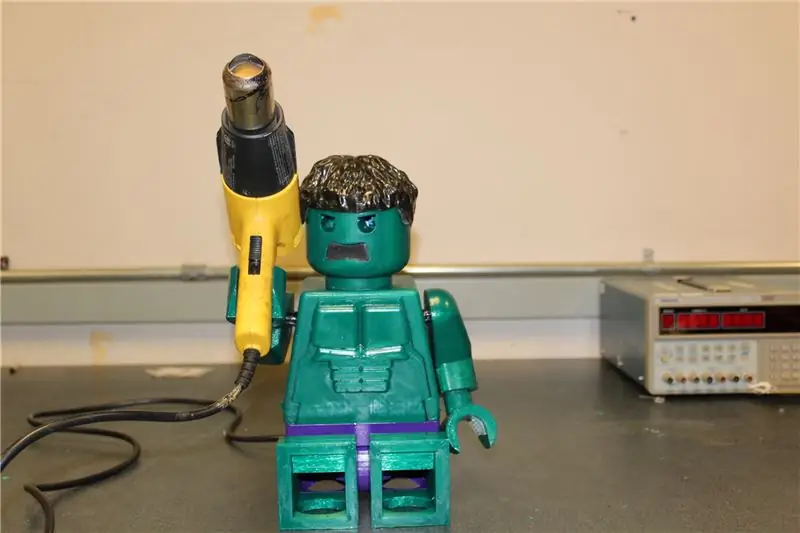
Projets Fusion 360 »
J'ai toujours joué avec des legos quand j'étais enfant, mais je n'avais aucun des legos "fantaisies", juste des briques lego classiques. Je suis également un grand fan de Marvel Cinematic Universe (MCU) et mon personnage préféré est Hulk. Alors pourquoi ne pas combiner les deux et créer des figurines hulk géantes, car plus c'est gros c'est toujours mieux, non ? J'ai donc décidé de faire un modèle à l'échelle 10:1 des figurines lego originales.
Une minifig géante Lego Hulk (je suppose qu'elle s'appellerait mégafig) ne suffit pas, j'ai décidé de m'amuser davantage et de lui donner vie. J'ai également ajouté quelques nouvelles fonctionnalités supplémentaires qui lui permettent à la fois de bouger et de parler en ajoutant 3 servomoteurs, un module de lecteur MP3 et un haut-parleur avec un amplificateur intégré.
Comme il possède un module de lecteur MP3 et un haut-parleur, vous pouvez réellement charger tous vos morceaux préférés sur une carte SD et l'utiliser également comme haut-parleur !
L'électronique et le matériel de ce projet sont également faciles à trouver et relativement peu coûteux. De cette façon, ce projet est facilement reproductible par les masses (et la communauté Instructables). Mon estimation du coût du projet est d'environ 50-80 $ - cela dépendra de l'endroit où vous vous procurez les articles. Si vous êtes prêt à attendre eBay ou Aliexpress, ce sera moins cher, sinon DFRobot a expédié le mien via DHL et je l'ai eu en 2 jours. Le même argument peut être dit pour la qualité du filament que vous avez utilisé. Étant donné que vous pouvez en acheter un minuscule pour 5 $ sur Amazon, je dirais que le prix augmente de manière assez linéaire, ou moins étant donné qu'il a beaucoup plus de fonctionnalités que n'importe quelle figurine Lego achetée en magasin.
Étape 1: Nomenclature
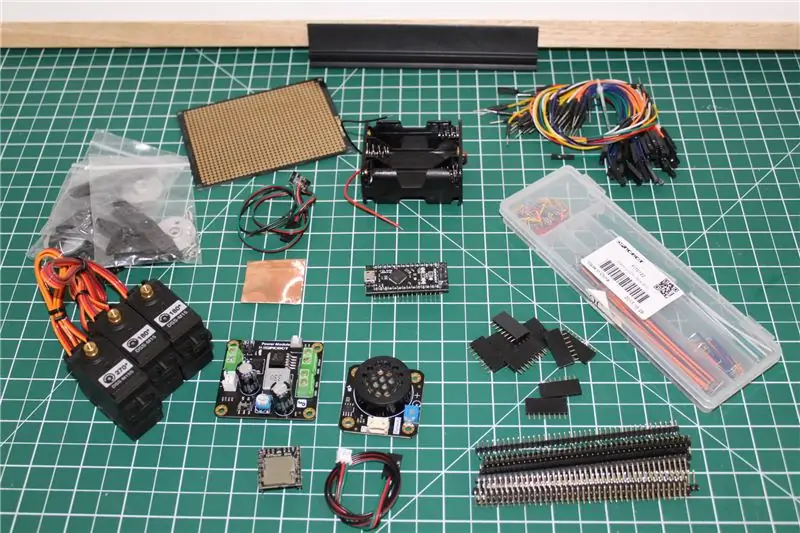
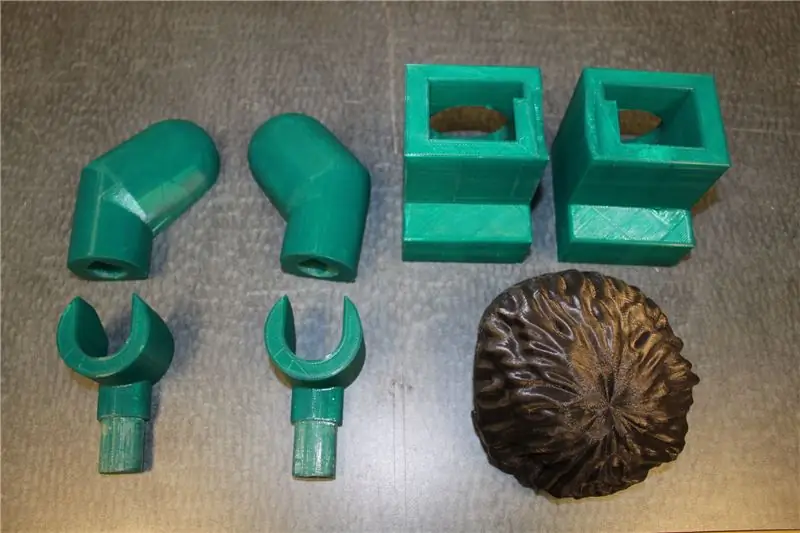
Matériel
Boulons et écrous M3 assortis
1kg de PLA vert (j'ai eu une tonne de filament pour une bonne affaire sur Kijiji, mais vous pouvez vous procurer le vôtre sur Amazon ou filaments.ca si vous êtes en Amérique du Nord)
200g de Purple PLA (j'ai utilisé la marque CCtree d'Amazon et cela a dépassé mes attentes pour le prix)
200 g de PLA noir (j'ai utilisé ma marque de confiance préférée, bien que légèrement chère, Innofil)
Résine époxy et durcisseur (c'est pour lisser et faire briller l'impression, vous pouvez aussi utiliser XTC3D mais je les ai trouvés très chers)
CA Glue and Accelerant ou Superglue (la première est préférable car vous pouvez accélérer le temps de durcissement à quelques secondes seulement)
Brosse en mousse (j'ai eu la mienne dans un magasin d'art local, Curry's, qui m'a offert un rabais étudiant !)
Astuce de pro / Fait amusant: CA Glue n'est en fait que de la super colle, où CA signifie Cyanoacrylate (un peu comme lorsque vous achetez Tylenol vs Acetaminophen dans une pharmacie, cette dernière étant une marque générique avec le nom chimique réel). L'avantage d'utiliser CA Glue est que vous pouvez l'acheter avec un accélérateur qui réduit le temps de durcissement à quelques secondes, vous n'avez donc pas besoin de le serrer ou de le maintenir jusqu'à ce qu'il sèche.
Attention: Attention à ne pas mettre de mélange colle CA + accélérateur sur vos mains car cela brûlerait.
Électronique
Arduino Pro Nano
Module lecteur MP3
Module haut-parleur et amplificateur
Servos 180 et 270 degrés (j'ai choisi d'utiliser 2 180 degrés pour le bras et 1 270 degrés pour la tête)
Convertisseur abaisseur de tension (Vous pouvez également utiliser un 7805, mais ils ne peuvent pas fournir autant de courant que celui-ci, et cela fonctionne également pour un LiPo à 3 cellules !)
Résistance 1K Ohm (je suis sûr que vous en avez probablement qui traînent ou que vous pouvez acheter un pack qui durera toute une vie)
PCB protoboard
Fils de cavalier
Fils de planche à pain
Batterie Lithium Polymère (LiPo) 2 cellules ou support de batterie 6V AA (je préfère LiPo car il est rechargeable et peut donner 7,2V aux servomoteurs)
En-têtes de broche (H/F)
Connecteur XT60 (si vous choisissez d'utiliser une batterie lithium polymère avec un xt60)
JST Crimp Pins (Ou vous pouvez simplement souder ces extrémités femelles du fil de connexion - je possédais déjà une pince à sertir et j'avais des broches JST Crimp, donc je l'ai utilisé pour lui donner un aspect plus professionnel)
Thermorétractable (Beaucoup plus soigné et plus professionnel que le ruban électrique !)
Outils
Imprimante 3D
Fer à souder, Souder, Pompe à dessouder
Multimètre (pour le dépannage des circuits)
Pince à sertir (si vous choisissez d'utiliser une batterie lithium-polymère avec un connecteur XT60)
Couteau X-acto - J'ai eu le mien dans un magasin d'art local pour environ 2 $ avec un rabais étudiant
Papier de verre - grain 400, grain 600, grain 1000, grain 200
"Mais, je n'ai pas d'imprimante 3D"
Aucun problème! Vous pouvez envoyer les STL à des services d'impression 3D comme Shapeways et 3DHubs
Je sais que la liste semble intimidante et longue. J'ai essayé de le rendre aussi complet que possible, tout en fournissant des justifications et des détails sur la façon dont j'ai procédé à mes choix de conception. De cette façon, vous pouvez choisir et modifier le projet pour le transformer en votre propre projet. Mon objectif est de toujours permettre aux utilisateurs d'être créatifs et de créer leurs propres projets en utilisant le mien comme guide plutôt que de simplement découper des cargaisons, mais n'hésitez pas à le dupliquer également !
L'impression 3D est également de plus en plus courante, alors peut-être avez-vous un ami qui possède une imprimante 3D que vous pouvez utiliser. Les filaments sont de moins en moins chers et vous pouvez obtenir une bobine de 1kg pour moins de 20$CAD ou AUD (ou <15$ USD) !
Étape 2: Diviser pour régner
Cette construction peut ne pas sembler complexe, mais elle englobe les blocs fondamentaux de la robotique - électromécanique, circuits et programmation embarquée. En tant que tel, une certaine planification préalable aiderait grandement à la construction.
J'ai séparé cette version en 5 segments:
- Phase de conception et d'impression 3D
- Post-traitement
- Électronique
- Code
- Assemblée
Diviser et conquérir! Pendant que vous attendez la fin de vos impressions, vous pouvez commencer avec l'électronique et le codage.
Étape 3: [Facultatif] Conception et impression 3D: Conception
![[Facultatif] Conception et impression 3D: conception [Facultatif] Conception et impression 3D: conception](https://i.howwhatproduce.com/images/011/image-30025-8-j.webp)
Étant donné que mes compétences en Fusion360 sont limitées, j'ai un ami pour m'aider à CAO ces fichiers. Vous n'êtes pas obligé de concevoir le vôtre si vous suivez exactement ce guide. Passez simplement à l'étape suivante et imprimez-les en 3D. Toutes les dimensions sont métriques !
Cependant, si vous choisissez un PCB ou un haut-parleur différent, vous devrez peut-être redimensionner les trous et couper les extrusions là où les composants sont censés être.
Cependant, si vous voulez d'autres minifigs lego qui ne sont pas le hulk, alors n'hésitez pas à CAD le vôtre. Quelqu'un, s'il vous plaît, faites une version géante de Batman en lego !
Conseils de pro: concevez avec l'impression 3D en tête
(1) Les cercles en forme de larme peuvent être imprimés sans support, alors incorporez des formes en larme pour les découpes circulaires au lieu de cercles
(2) Les angles de 45 degrés ou plus peuvent être imprimés sans supports, alors faites en sorte que vos surplombs aient des angles de 45 degrés pour les soutenir.
Étape 4: Conception et impression 3D: Impression 3D
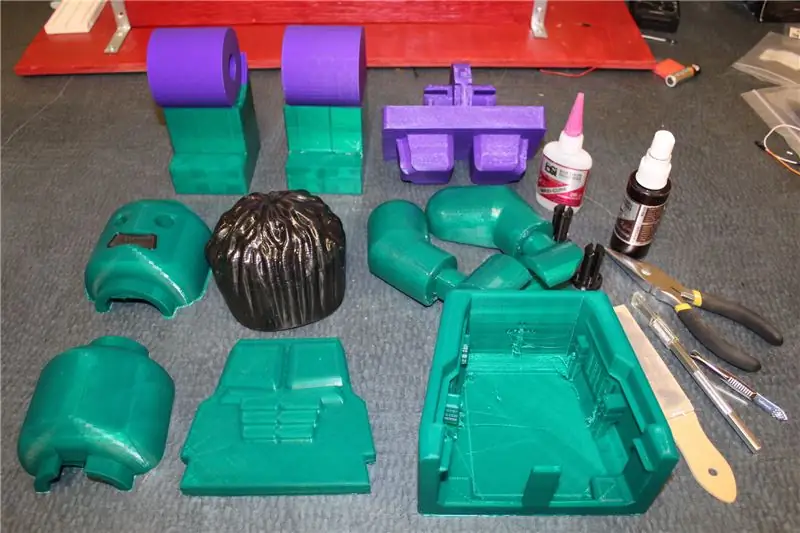
Cette étape est assez simple, prenez votre carte SD, enregistrez le gcode de votre trancheuse pour le fichier STL que vous souhaitez imprimer et imprimez-le ou commandez-le simplement auprès de Shapeways ou 3DHubs.
Le temps d'impression total pour toutes les impressions était d'environ 80 heures. Il a utilisé environ un peu plus de 1 kg de matériau au total en utilisant des filaments noirs, violets et verts - principalement verts parce que Hulk est vert, duh. Vous pouvez toujours l'imprimer en monochrome puis peindre au pistolet les pièces individuelles, ce qui est une autre méthode de lissage (voir étape suivante).
Astuce de pro 1: lutter contre le filament translucide
Si vous avez un filament d'aspect transparent comme celui que j'ai obtenu pour mon vert, vous pouvez vous en sortir avec un aspect toujours opaque en (1) augmentant l'épaisseur de la coque ou (2) en utilisant un ensemble de remplissage dynamique pour remplir jusqu'à 50 % par incréments de 5 %.. Malheureusement, comme la résine est transparente, elle ne recouvre pas la transparence du filament.
Astuce de pro 2: gérer les déformations non plastiques
Pour les pièces qui doivent fléchir légèrement, imprimez-le avec un remplissage plus élevé que le paramètre par défaut, environ 50 %, afin qu'il ne soit pas trop cassant lorsque vous devez serrer les broches ensemble. Vous pouvez laisser l'épaisseur de paroi par défaut. Il m'a fallu environ 5 essais avant d'obtenir la bonne combinaison de remplissage et d'épaisseur de paroi. Utilisez également un filament de haute qualité. Le filament CCTree d'Amazon est excellent car il permet une déformation non plastique sur les broches.
Astuce de pro 3: réduire le temps d'impression
Il n'y a pas de déjeuner gratuit si vous voulez gagner du temps en impression 3d. Il y a presque toujours un compromis à faire. En voici quelques-uns que j'ai utilisés et qui n'ont pas beaucoup affecté la qualité d'impression:
(1) Utilisez une hauteur de couche plus élevée - environ 0,2 mm est acceptable pour la tête et l'avant du corps et 0,3 mm pour tout le reste.
(2) Réduisez la densité de remplissage à environ 5 à 10 % ou utilisez un remplissage dynamique comme indiqué dans l'astuce 1.
(3) Activez le mode de peignage pour réduire les temps de trajet.
(4) Utilisez des bords ou des radeaux - Il peut être contre-intuitif d'utiliser des bords et des radeaux, mais cela vous fera gagner du temps contre les échecs d'impression qui sont sortis du lit d'impression de la buse en frappant à plusieurs reprises des impressions légèrement décalées sur l'axe z.
(5) Utilisez moins de supports. Pour les impressions qui nécessitent un grand nombre de supports comme les cheveux, utilisez des supports de densité inférieure, environ 5 à 10 %, donneront toujours une impression réussie.
Étape 5: [Facultatif] Lissage des impressions 3D
![[Facultatif] Lissage des impressions 3D [Facultatif] Lissage des impressions 3D](https://i.howwhatproduce.com/images/011/image-30025-10-j.webp)
![[Facultatif] Lissage des impressions 3D [Facultatif] Lissage des impressions 3D](https://i.howwhatproduce.com/images/011/image-30025-11-j.webp)
![[Facultatif] Lissage des impressions 3D [Facultatif] Lissage des impressions 3D](https://i.howwhatproduce.com/images/011/image-30025-12-j.webp)
C'est un processus long et onéreux, mais très gratifiant. Vous n'êtes pas obligé de le faire, mais cela rend le résultat final tellement meilleur. En suivant le guide de BrittLiv, j'ai choisi de lisser mon impression avec un revêtement époxy, sauf que j'ai d'abord décidé de la poncer au grain 1000 (préférable 2000, mais je n'en avais pas).
Mélangez l'époxy avec un temps de travail de 30 minutes à 1 heure pour vous permettre de faire toutes les pièces avant qu'il ne durcisse. Ensuite, il faudra encore 24 à 48 heures pour durcir, selon l'épaisseur de la couche que vous avez utilisée.
Attention: Portez des gants lors de l'époxy. Vous pouvez devenir allergique à l'époxy, ce qui entraînera une dermatite de contact, vous n'en voulez donc pas sur vos mains. De plus, vous n'avez pas à poncer minutieusement vos empreintes digitales sur votre travail d'impression qui n'a pris que 12 heures à imprimer.
Cette étape est assez longue et verbeuse, bien que les actions entreprises pour lisser l'impression soient assez simples. De nombreuses techniques ont été utilisées et essayées tout au long du processus, et je voulais partager toutes les leçons que j'ai apprises.
Astuce de pro 1: Nivellement du revêtement Utilisez une assiette en carton ou toute autre surface plane comme « palette » avant de peindre, au lieu de tremper le pinceau en mousse dans une tasse pleine d'époxy. Cela vous permettra de contrôler et d'appliquer un revêtement uniforme sur le travail d'impression.
Astuce de pro 2: utilisez un pinceau en mousse Je n'ai aucune connaissance préalable dans les arts ou quoi que ce soit qui s'y rapporte, alors quand il s'agissait de choisir un pinceau dans un magasin d'art local, je ne savais pas quoi choisir, alors j'ai demandé de l'aide. Un très bon point m'a été soulevé, si vous utilisez un pinceau typique, les traits des poils seront visibles, utilisez donc un pinceau en mousse car il n'y a pas de poils.
Astuce de pro 3: évitez le collage en mélangeant le bon rapport et en mesurant avec précision
Utilisez une balance pour mesurer le bon rapport de résine et de durcisseur. Contrairement aux conseils en ligne de mélanger plus de durcisseur pour qu'il sèche plus rapidement, utilisez toujours le bon rapport. C'est de la science simple, ou plutôt de la chimie. La résine et le durcisseur mélangés ensemble sont une réaction chimique - en fait, vous pouvez dire qu'il s'agit d'une réaction exothermique car l'époxyde se réchauffe lorsque vous les mélangez. Les ratios suggérés sont les ratios stoechiométriques qui permettent à toute la résine et au durcisseur de réagir ensemble pour former l'époxyde, ainsi tout excès ne réagira pas et vous vous retrouverez avec une couche collante.
Leçons apprises
1) Ne pas tremper dans l'eau une fois terminé
Je n'avais pas une bonne surface sur laquelle mettre les pièces imprimées en 3D, alors je l'ai juste placée sur du papier brouillon. Comme prévu, l'époxy s'est égoutté et a collé avec le papier. Ce n'est en fait pas difficile à enlever car vous pouvez simplement tremper le papier dans de l'eau et le frotter - c'est-à-dire si vous n'avez pas mis d'époxy sur la zone en contact avec le papier (vous ne devriez pas). Malheureusement, le fait de tremper l'impression époxy dans de l'eau lui donnait un aspect inégal, comme une voiture que vous avez essayé de laver mais que vous n'avez pas séchée correctement.
Il n'y avait rien que je puisse faire pour me débarrasser des taches même si je les ai séchées correctement. La seule solution était de poncer à nouveau le tout - et le ponçage de l'époxy n'est pas amusant du tout - jusqu'à ce qu'il soit lisse (poncer jusqu'à 2000 grains), puis de le recouvrir d'époxy, ce qui signifie plus d'attente.
Il y a une doublure argentée cependant, après avoir répété le processus fastidieux de lissage et d'époxy, le résultat final était nettement meilleur ! Je peux imaginer qu'il y a un point de rendements décroissants à cela et à un moment donné, il est inutile de le répéter, là où la première couche a le plus d'impact.
2) Ne pas chauffer le pistolet
N'utilisez PAS de pistolet thermique pour accélérer le durcissement de l'époxy. Le plastique se ramollira et se déformera même si vous le chauffez à distance. J'avais un échantillon de PLA et j'ai appris qu'il vaut mieux être patient et attendre.
3) Continuez à poncer
J'étais réticent à le poncer au début parce qu'il le faisait paraître blanc et rayé et je craignais que lorsque je le recouvre d'une couche d'époxy, il conserve sa couleur terne et rayée. J'avais tort. En fait, le poncer jusqu'à ce qu'il soit lisse et très rayé a donné les meilleurs résultats.
Comment ça marche?
Lorsque vous le poncez, vous vous débarrassez de toutes les imperfections et bosses, vous obtenez donc une impression lisse, mais cela ne comble aucun des espaces et des crevasses. Lorsque vous appliquez de l'époxy sur une impression, vous remplissez efficacement tous les espaces laissés par les couches et toutes les irrégularités de l'impression. Remarquez que si vous plongez la partie imprimée en 3D dans de l'eau, son apparence est beaucoup plus lisse lorsqu'elle est mouillée - c'est parce que l'eau a rempli les espaces, mais elle s'évapore. La résine le remplit durablement et ne laisse aucune décoloration puisqu'elle est incolore.
Étape 6: Assemblage [partiel]: Assemblage de la tête
![Assemblage [partiel]: Assemblage de la tête Assemblage [partiel]: Assemblage de la tête](https://i.howwhatproduce.com/images/011/image-30025-13-j.webp)
![Assemblage [partiel]: Assemblage de la tête Assemblage [partiel]: Assemblage de la tête](https://i.howwhatproduce.com/images/011/image-30025-14-j.webp)
![Assemblage [partiel]: Assemblage de la tête Assemblage [partiel]: Assemblage de la tête](https://i.howwhatproduce.com/images/011/image-30025-15-j.webp)
Il y a certains composants électroniques que vous n'avez pas besoin de souder grâce à la conception de PCB modulaire que j'ai fournie. Ce sont les servomoteurs et le module haut-parleur. Étant donné que le servomoteur et le module de haut-parleur sont indépendants du corps, nous pouvons les placer dans la tête et terminer l'assemblage de la tête.
Placez le haut-parleur sur le devant de la tête. Il y a des chevilles pour le haut-parleur à visser, mais comme ces deux pièces vont être prises en sandwich par le servo et les cheveux, il n'est pas nécessaire de les visser - et elles ne se sépareront pas à moins que vous ne les forciez.
Étape 7: Électronique: Souder le PCB et la majeure partie de l'électronique
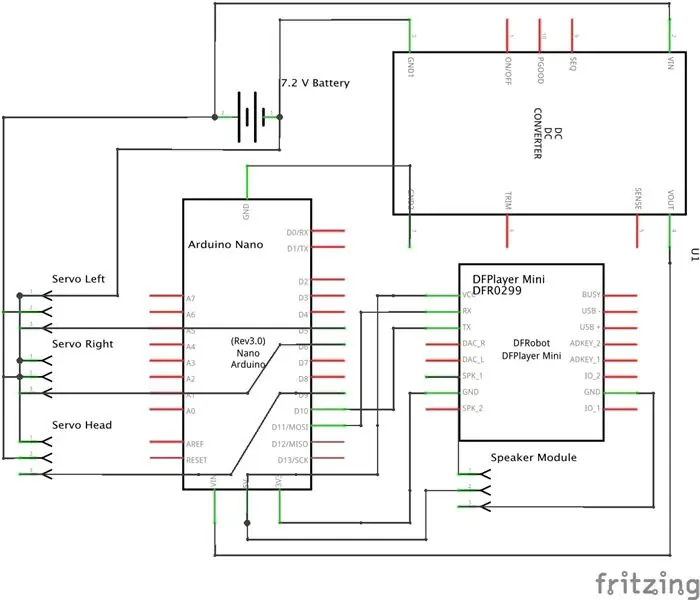
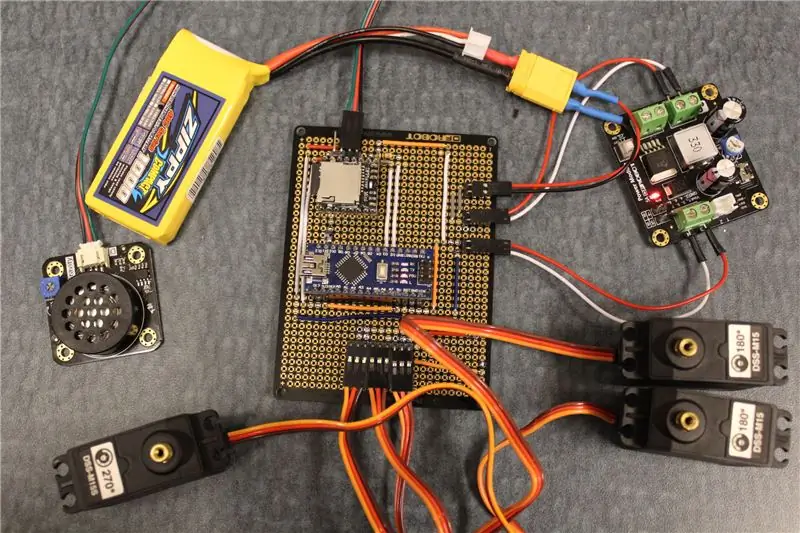
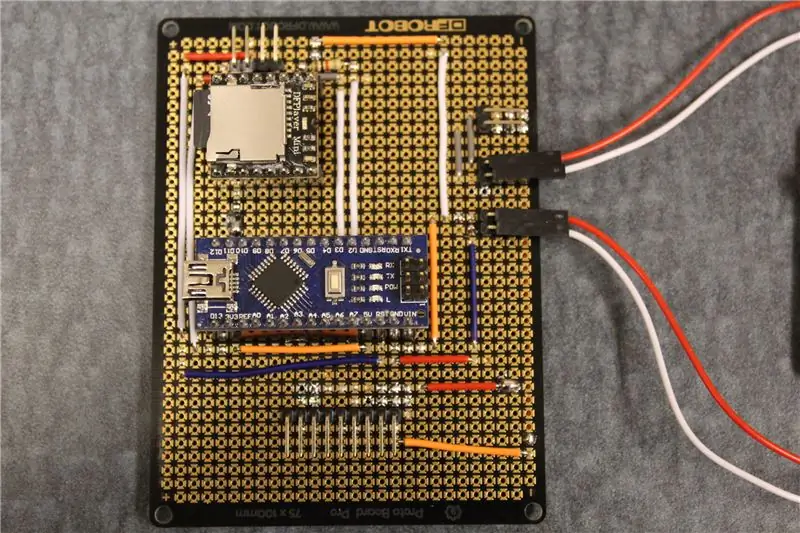
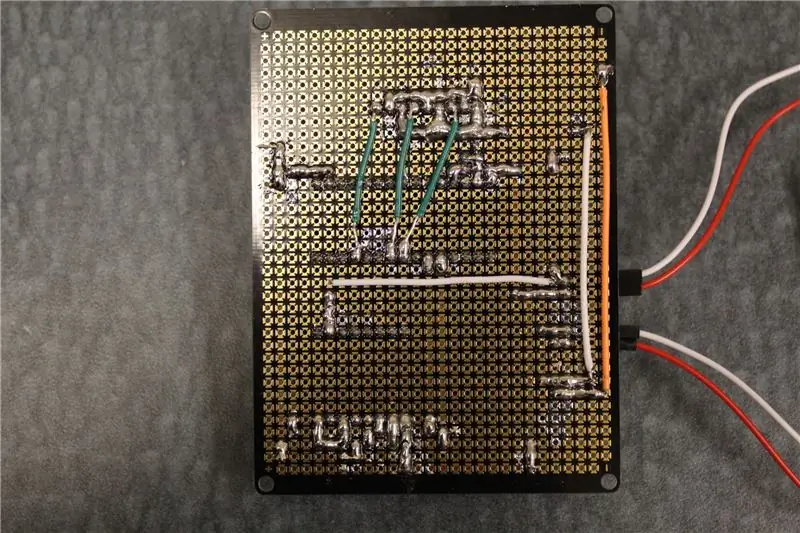
Soudez le PCB en vous basant sur le schéma fourni. J'ai également ajouté le document Fritzing afin que vous puissiez l'ouvrir sur Fritzing et exécuter le routage automatique pour le PCB et l'imprimer si vous ne souhaitez pas souder les chemins de bus vous-même.
Pour rendre les circuits plus propres et modulaires, j'ai utilisé quelques techniques notées ci-dessous:
- Utilisez des embases à broches femelles comme sockets IC personnalisés pour l'Arduino Nano et le DFPlayer Mini.
- Utilisez des embases mâles pour brancher les servomoteurs et les haut-parleurs. De cette façon, ils ne sont pas soudés directement sur le PCB et peuvent être retirés à tout moment.
- Ajoutez des embases mâles pour l'entrée de la batterie et l'entrée et la sortie du convertisseur abaisseur de tension. De cette façon, vous pouvez facilement router et ajouter plus de chemins de bus à la tension appropriée. Ce n'est pas nécessaire, mais cela simplifie le câblage et permet de réduire le nombre de fils qui pendent sur le convertisseur abaisseur de tension. Comme vous pouvez le voir, je n'ai utilisé que 2 paires.
Cela nécessite une quantité modérée d'expérience et de compétences en soudage en raison du nombre de connexions pontées que vous devez établir et de la proximité des broches les unes des autres.
Alors comment obtenir un bon résultat en soudant le PCB ?
Munissez-vous d'un bon fer à souder avec contrôle de température et d'un PCB avec des pastilles carrées. Utilisez un fer à pointe biseautée (plat) pour augmenter le contact entre le composant et le tampon. J'aime aussi utiliser 2/3 d'étain et 1/3 de plomb car le plomb a une température de fusion plus basse, ce qui facilite un peu le soudage.
Étape 8: Électronique: Adaptateur de connecteur de batterie
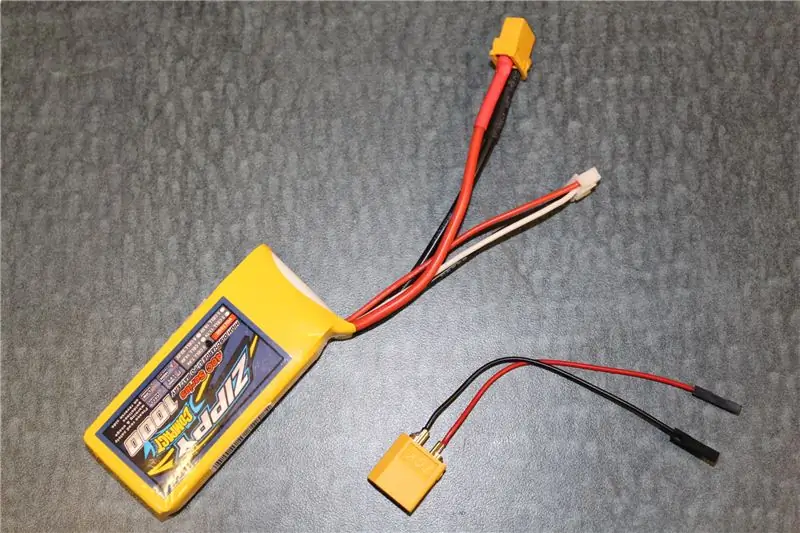
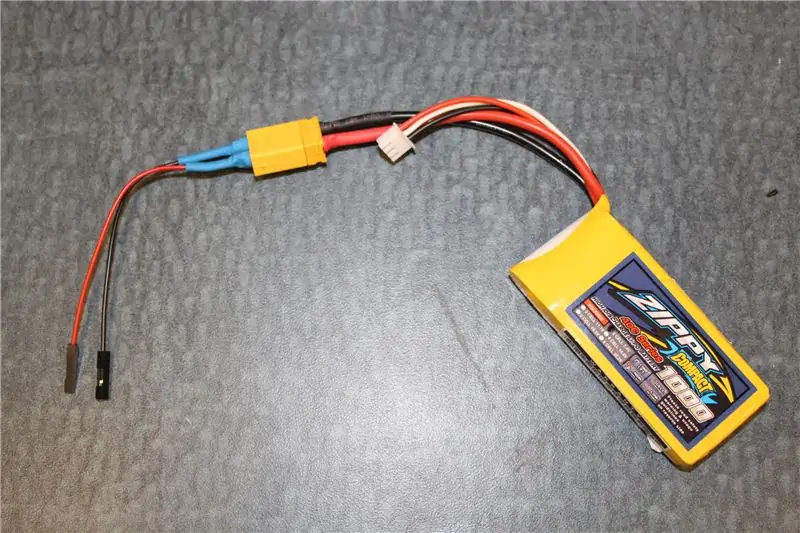
La sortie de la batterie LiPo 2 cellules se fait via le connecteur XT60, qui est une norme dans les avions RC. Je ne voulais pas le couper car le XT60 est la norme pour de nombreuses prises pour moteurs sans balais que j'utilise et peut également gérer jusqu'à 60 A de courant - dont j'ai besoin pour d'autres applications.
1. Souder XT60
J'ai donc opté pour une solution plus modulaire. Soudez un adaptateur XT60 avec un mâle XT60 à femelle JST (étiqueté ci-dessus) - négatif à négatif (fil noir) et positif à positif (fil rouge).
2. Sertissage/soudage des broches femelles JST sur XT60
Placez les broches non serties sur la pince à sertir et serrez-la pour qu'elle maintienne fermement les broches tout en permettant aux fils de glisser à travers - cela formera un cube ouvert. Insérez le fil dénudé sur le cube ouvert, puis sertissez-le. Répétez cette opération pour les fils rouge et noir, puis faites glisser les deux broches serties dans le boîtier JST.
Alternativement, vous pouvez simplement couper l'extrémité mâle du câble de démarrage M/F et souder le fil sur le XT60 comme je l'ai fait.
3. Rétractable à chaud les connecteurs
Assurez-vous de thermorétracter les connecteurs afin qu'ils ne se raccourcissent pas accidentellement. Ces batteries à base de lithium feront de beaux feux d'artifice, bien que moins agréables, si elles sont courtes.
Astuce de pro 1: Souder les XT60
Lorsque vous soudez les fils minces au XT60, étamez d'abord les fils, puis remplissez les cavités du XT60 avec de la soudure à moitié. En gardant le fer sur les connecteurs, plongez les fils étamés et retirez le fer, tout en maintenant le fil. Gardez-le immobile pendant quelques secondes et rétrécissez-le à la chaleur une fois qu'il est refroidi.
Astuce de pro 2: Prévention de la déformation du connecteur
Pour éviter que le connecteur XT60 ne se déforme sous l'effet d'une chaleur élevée, insérez les connecteurs femelle et mâle (connecteurs dessoudés PAS les batteries !) l'un à l'autre avant de souder. De cette façon, ils conserveront la forme du connecteur et empêcheront les conducteurs de bouger car il s'agit d'un ajustement serré.
Étape 9: Code: Compiler et télécharger le code
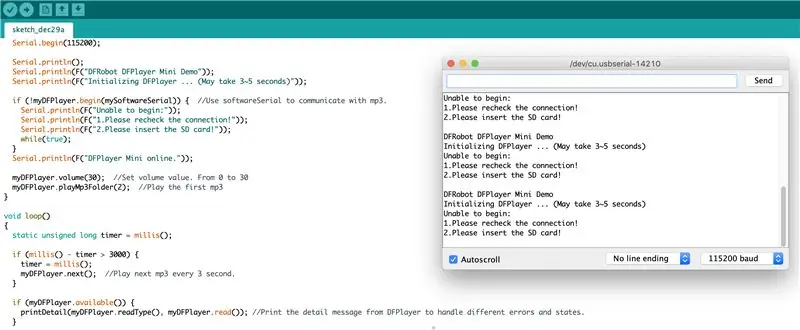
Téléchargez le code ci-joint et téléchargez-le sur l'Arduino Nano. Ceci est responsable de l'exécution de 4 modes de mouvements différents à partir du servo ainsi que des effets sonores en boucle via le module MP3. Le module MP3 joue les sons en fonction de l'ordre dans lequel les fichiers MP3 sont téléchargés sur la carte SD.
Si vous souhaitez l'utiliser comme haut-parleur, utilisez simplement la fonction suivante pour lire des fichiers musicaux aléatoires en boucle.
myDFPlayer.randomAll();
Pour plus d'informations sur toutes les commandes qui peuvent être données au lecteur MP3, vous pouvez les trouver dans la spécification du fabricant.
Dans mon cas, il suffit de lire un fichier MP3 spécifique. La façon dont je me suis assuré que le module MP3 lit le fichier approprié plutôt que de me fier à la commande utilise la méthode intégrée, qui suppose qu'il se trouve dans le dossier appelé MP3 (non sensible à la casse):
monDFPlayer.playMP3Folder(1);
où l'argument 1 est le nom du fichier, 0001.mp3.
En utilisant la méthode qui repose sur l'ordre de téléchargement des fichiers:
monDFPlayer.play(1);
suppose qu'il se trouve dans le dossier racine et ne nécessite pas de nom de fichier spécifique.
Étape 10: Assemblage: ajustement des composants électroniques
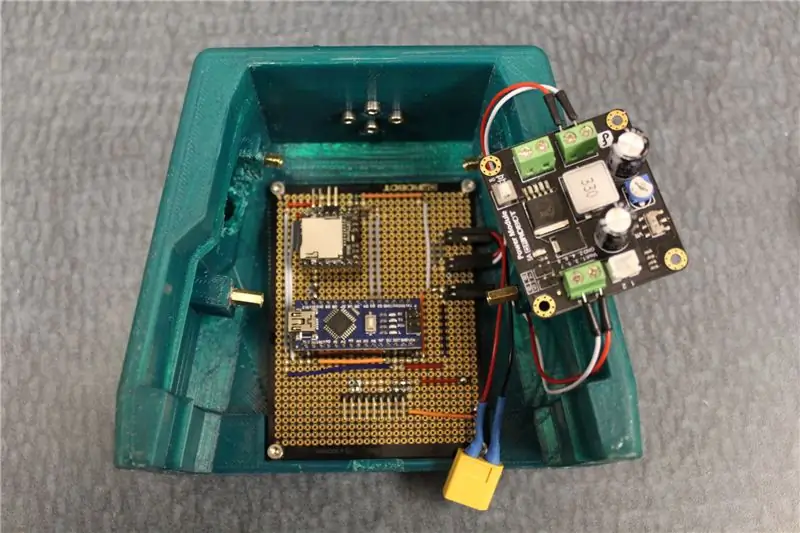
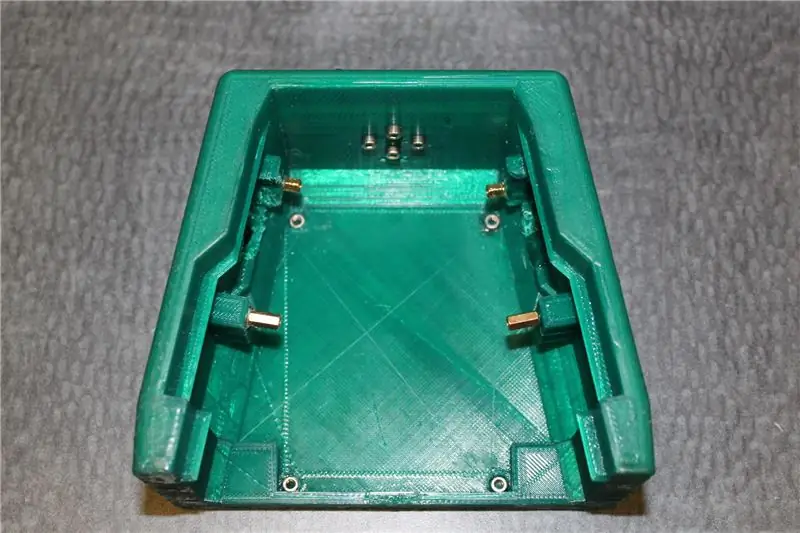
Nous allons commencer par le PCB et les composants électroniques, puis passer à la fixation des servomoteurs.
Tout d'abord, pour faciliter l'assemblage, G et débranchez les composants.
Remarquez comment il y a des extrusions coupées hexagonales pour fixer un écrou sur le corps et la tête de la pièce Lego. C'est là que l'écrou doit être collé à l'aide de colle CA - faites attention lors du collage de ne pas ajouter accidentellement de la colle sur les filets.
Ensuite, placez le PCB et alignez les trous sur les écrous et vissez-le avec des boulons M3. Cela devrait être une tâche plutôt rapide et triviale.
Étape 11: Assemblage: Montage des servomoteurs
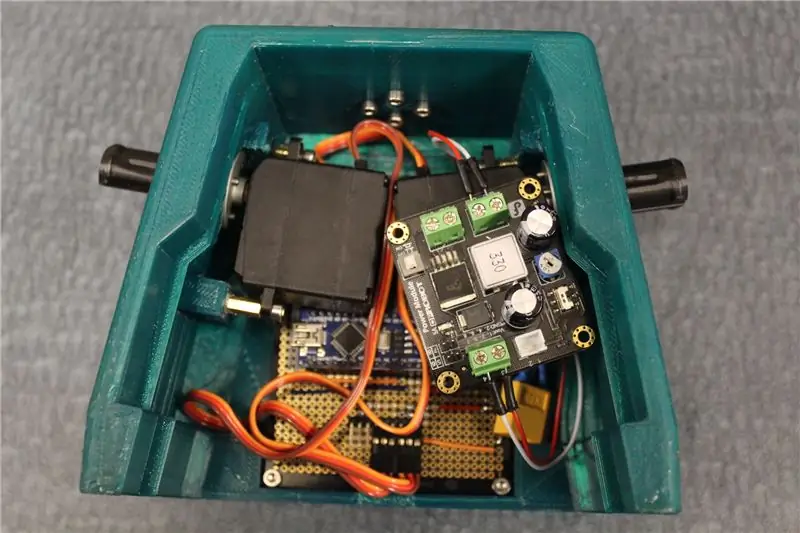
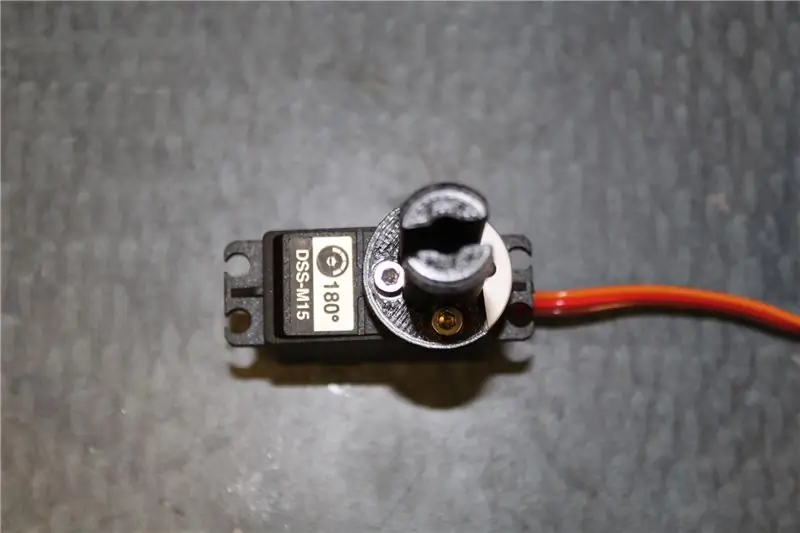
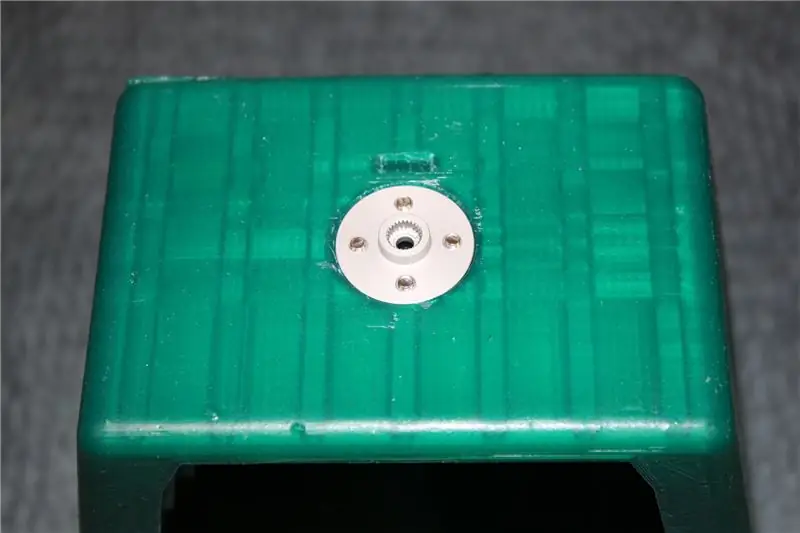
Il y a deux choses qui doivent être physiquement attachées aux servomoteurs (1) Le palonnier circulaire en métal (étiqueté ci-dessus) et (2) Le corps du servo au corps de la pièce Lego. Les vis utilisées pour l'ensemble de ce projet sont standardisées; ce sont tous des écrous et boulons M3.
Il y a 3 cornes de servo qui doivent être fixées dans le corps. Un pour la tête et deux pour les axes du bras qui seront entraînés par le servomoteur. Il y a un ordre particulier dans lequel ils doivent être assemblés de sorte que vous n'ayez pas à positionner vos mains de manière maladroite.
- Visser le palonnier de la tête en haut du corps à l'aide de 4 vis m3 vers le palonnier.
- Vissez les goupilles du bras sur le palonnier du servo puis sur le servomoteur à 180 degrés à l'aide des vis fournies avec le servo. Vissez-le vers la corne car les trous sur la corne sont filetés.
- Placez des entretoises sur les côtés du corps où le servo doit être monté. Les entretoises doivent combler l'écart entre le servo et la plate-forme de montage en raison d'une erreur de conception. Cela sera corrigé et vous n'avez pas besoin de faire cette étape.
- Ensuite, vissez simplement le châssis des servomoteurs et le palonnier sur le corps comme indiqué sur les images. Si vous n'utilisez pas d'entretoises, vous aurez besoin de vis autotaraudeuses qui seront fournies avec le servomoteur. Les servos dans le corps sont assez serrés, vous devez donc les manipuler jusqu'à ce que vous puissiez les insérer tous les deux.
Étape 12: Assemblage: enclenchez les pattes
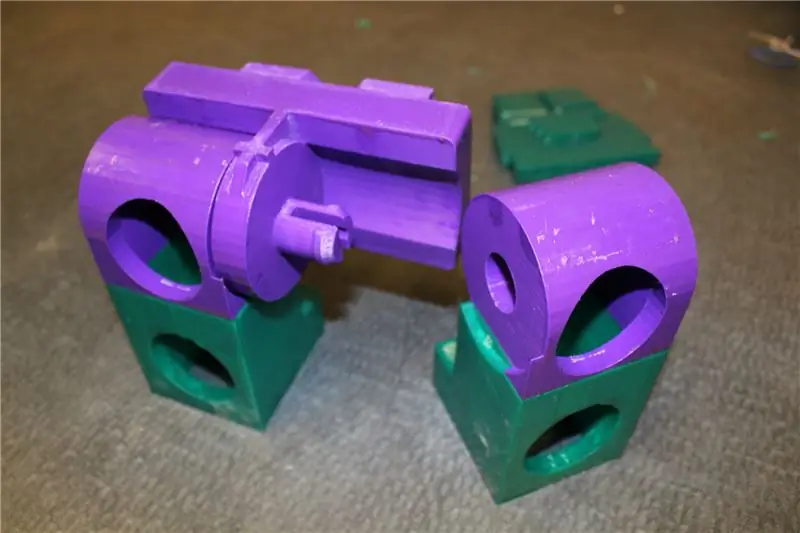
La dernière chose que nous devons faire est simplement d'assembler toutes les pièces ensemble comme le Lego classique.
- Collez les deux moitiés des jambes, en dessous (PLA vert) et au-dessus du genou (PLA violet) ensemble à l'aide de colle CA
- Attachez les jambes ensemble aux hanches. Si c'est un peu têtu, serrez légèrement les deux broches ensemble et poussez les jambes sur la hanche.
C'est pourquoi j'utilise un filament de qualité (j'ai utilisé CCTree d'Amazon pour les pièces violettes et il n'est étonnamment pas cassant et de couleur vive pour le prix).
Étape 13: Assemblage: Torse
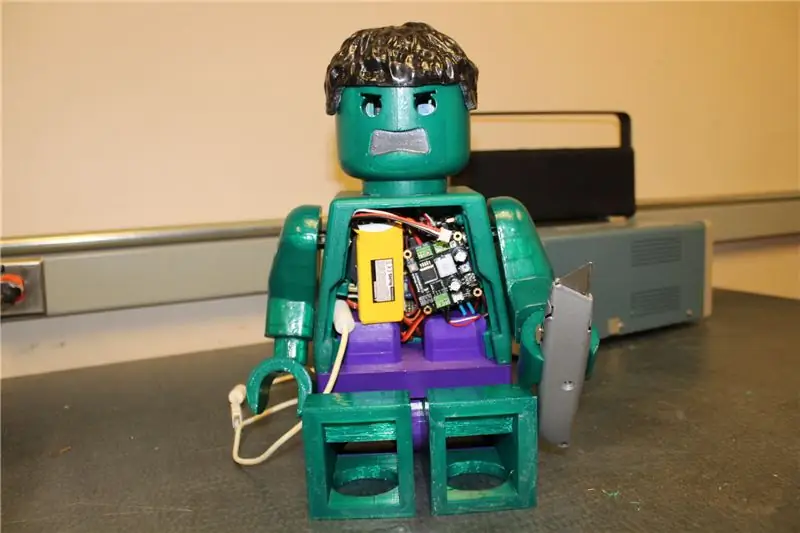
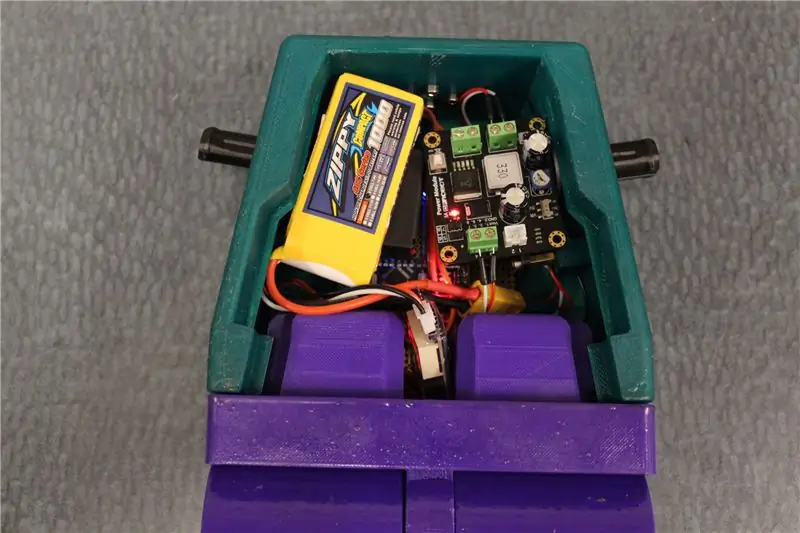
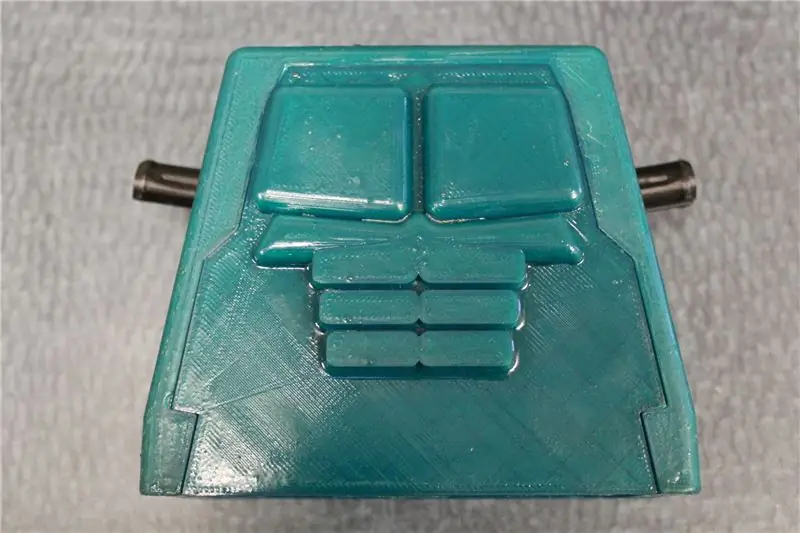
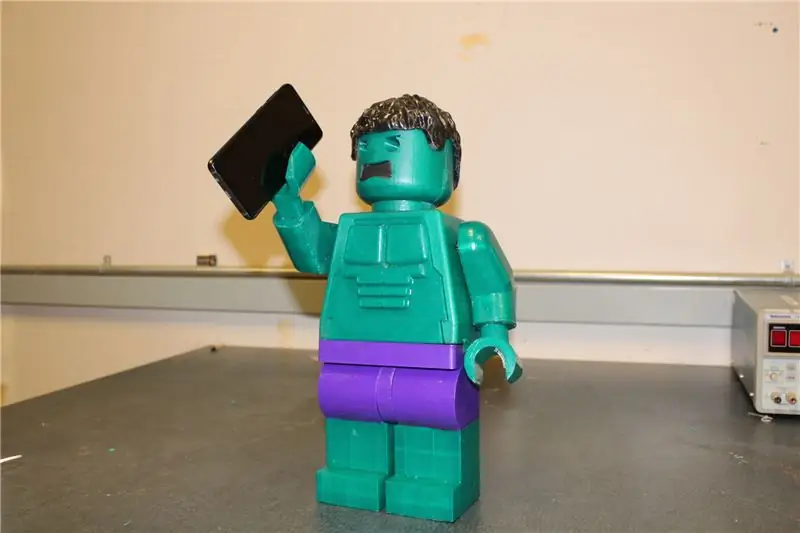
- Poussez les mains contre les bras - les bras peuvent nécessiter un ponçage en fonction des tolérances de l'impression 3D.
- Fixez les bras ensemble aux broches des bras, tout comme les jambes au
- Enfoncez les fils du haut-parleur et du servo dans le trou du corps et branchez-le aux en-têtes de broche appropriés que vous avez soudés.
- Vissez le servo de tête sur le palonnier du corps pour terminer l'assemblage. Ensuite, placez la plaque thoracique sur le dessus du corps.
Vous avez terminé! Allumez-le et profitez de votre méga figurine Lego Hulk !
Étape 14: Votez pour moi
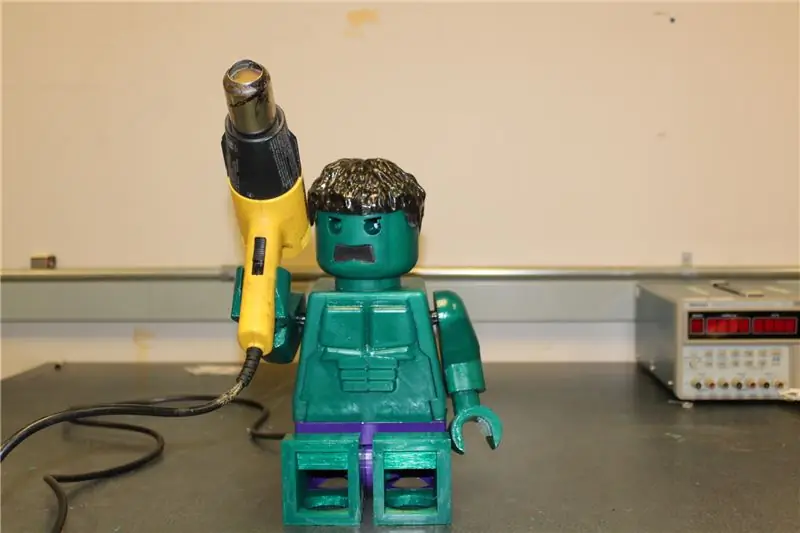
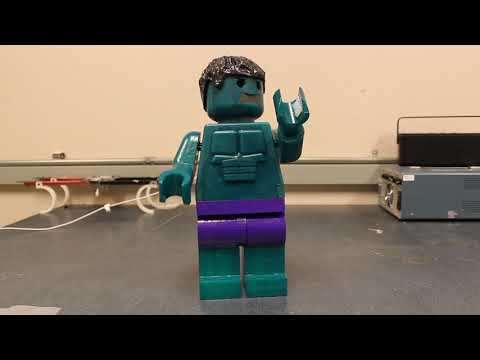
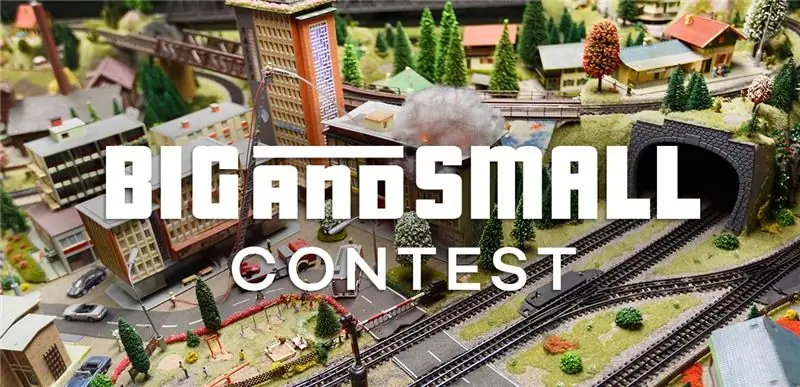
J'ai participé au concours Big and Small, donc vos votes seraient très appréciés si vous l'aimiez.
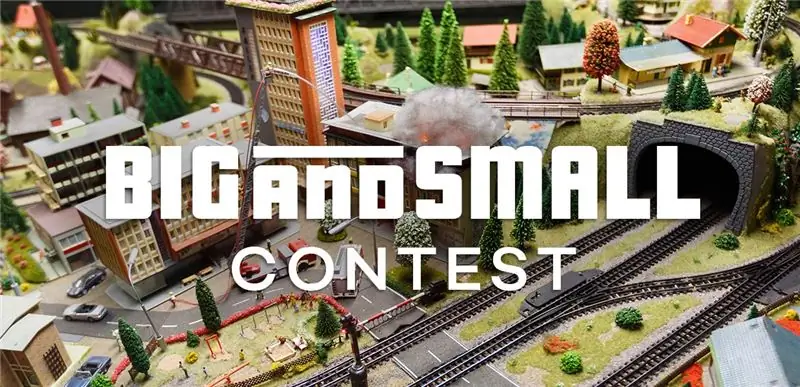
Deuxième prix du Grand et Petit Concours
Conseillé:
AVION RC GÉANT : 9 étapes (avec photos)
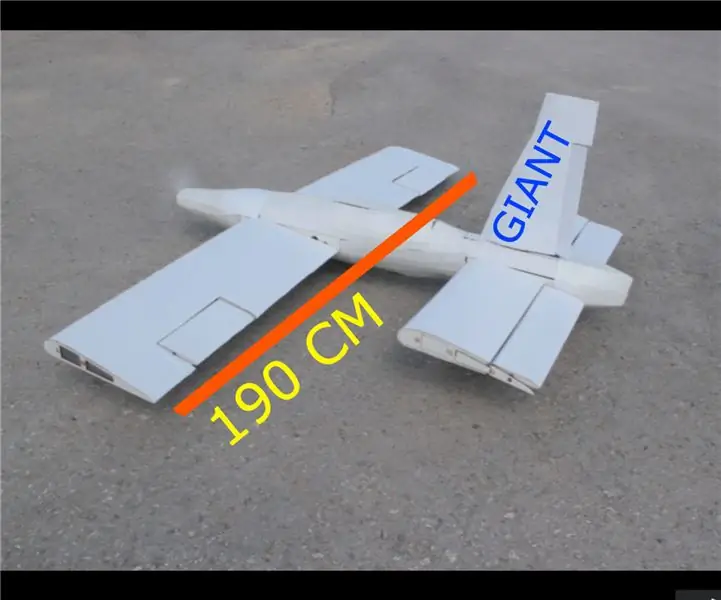
AVION GEANT RC : Salut tout le monde, je suis Ensar. Aujourd'hui, je vais écrire sur mon plus long projet. Je l'ai fait à l'automne 2018 et aujourd'hui j'ai une énergie à vous raconter. Je vais vous donner des fichiers DXF pour la gravure laser, et des codes Arduino. Veuillez vous abonner à ma chaîne YouTube. Je spé
Compteur de CO2 analogique géant : 6 étapes (avec photos)
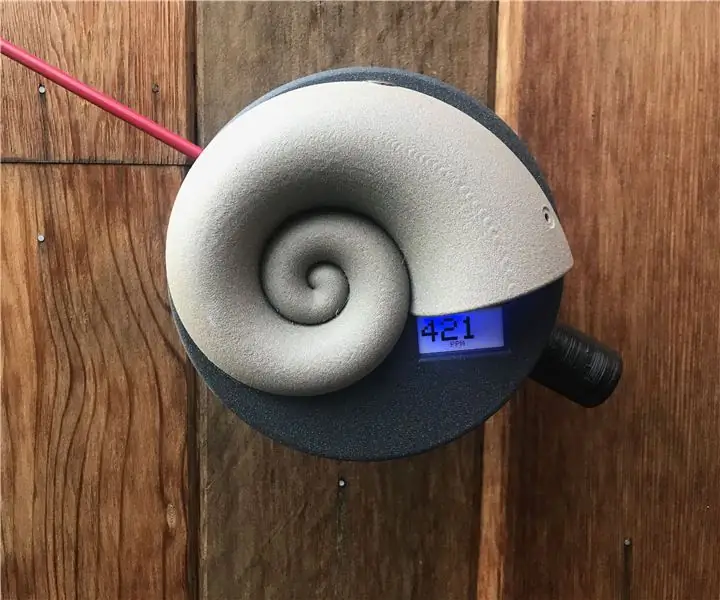
Compteur de CO2 analogique géant : L'atmosphère actuelle au-dessus d'une montagne à Hawaï contient environ 400 ppm de dioxyde de carbone. Ce nombre est extrêmement important pour tous ceux qui vivent à la surface des planètes. Nous sommes maintenant entourés soit de négateurs de cette inquiétude, soit de ceux qui tordre leur
Gamepad rétro géant : 11 étapes (avec photos)
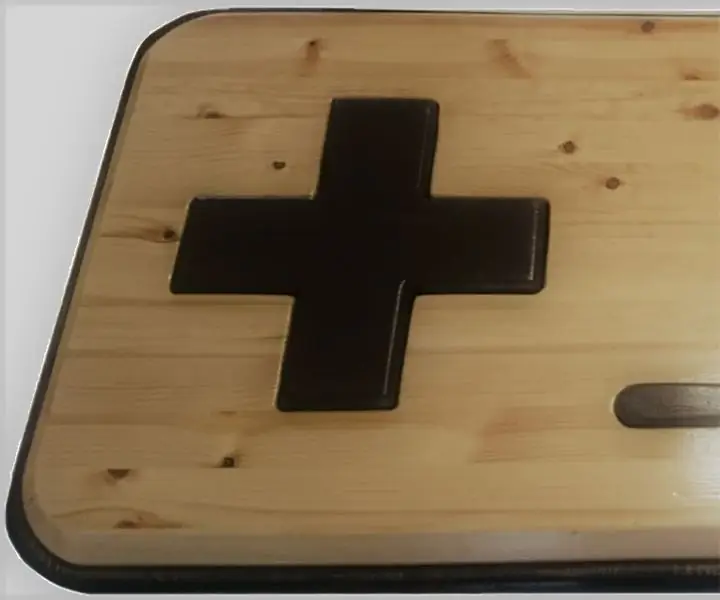
Manette de jeu rétro géante : nous avons donc décidé de créer une manette de jeu géante qui fonctionne… . J'avais déjà la plupart des matériaux qui traînaient autour de moi
Machine à dessiner Polargraph à grande échelle avec tête de stylo rétractable : 4 étapes (avec photos)
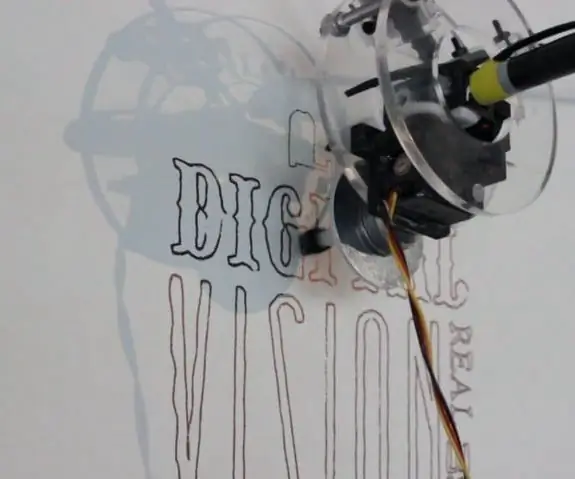
Machine à dessiner Polargraph à grande échelle avec tête de stylo rétractable : * L'installation à grande échelle de cette machine a été conçue et exécutée avec Rui Periera Il s'agit d'une conception pour le dessin open source Polargraph (http://www.polargraph.co.uk/) projet. Il dispose d'une tête de stylo rétractable et de matériel pour lui permettre de
Parler à Pick et discuter avec l'intelligence artificielle à l'aide de Cleverbot : 14 étapes (avec photos)
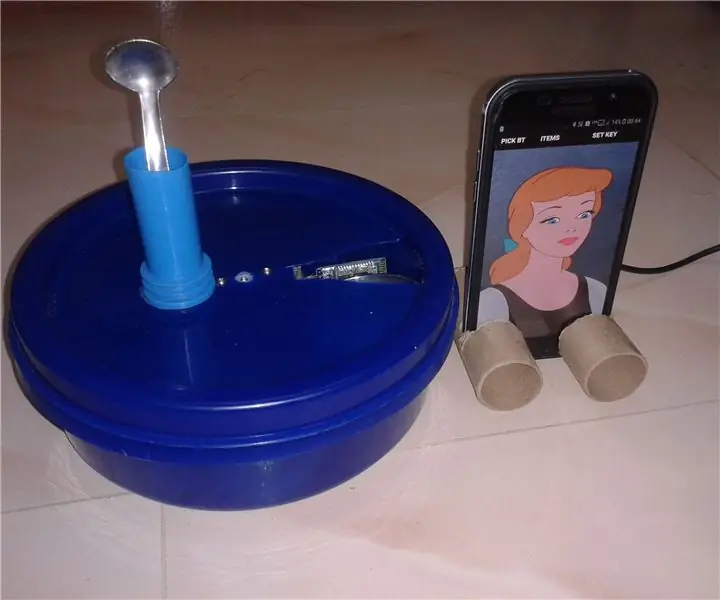
Parler à Pick et discuter avec l'intelligence artificielle à l'aide de Cleverbot : Ici, j'essaie non seulement la commande vocale, mais aussi le chat en intelligence artificielle avec l'ordinateur à l'aide de Cleverbot. En fait, l'idée est venue lorsque les enfants ont trouvé des couleurs mélangées dans la boîte à colorier lorsqu'ils ont pris la couleur d'une couleur à la plus proche. Mais enfin mettre en œuvre