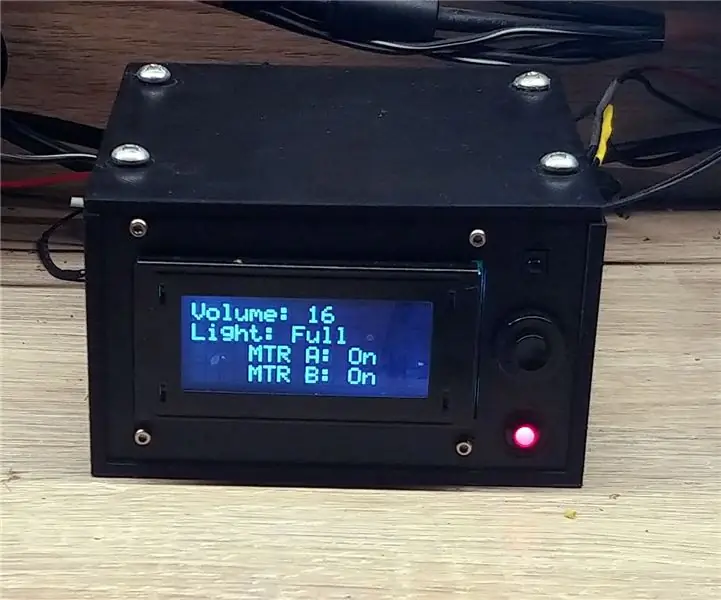
Table des matières:
2025 Auteur: John Day | [email protected]. Dernière modifié: 2025-01-23 14:46
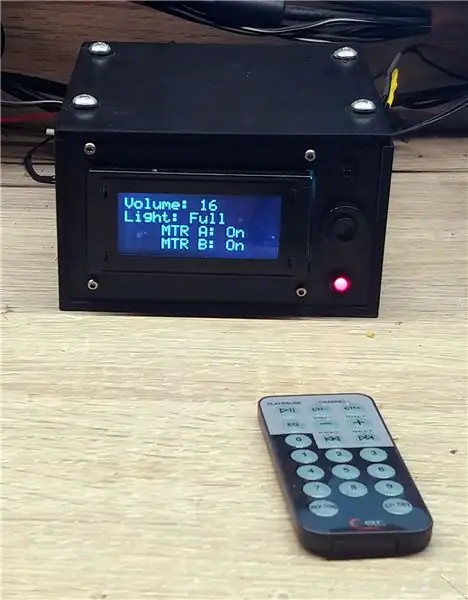
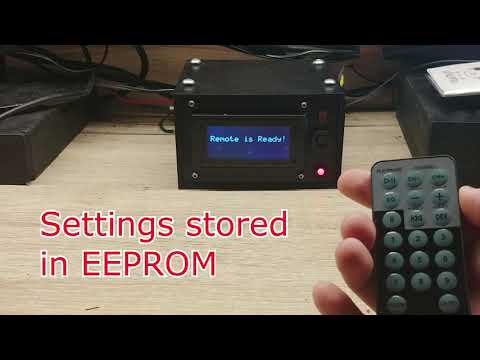
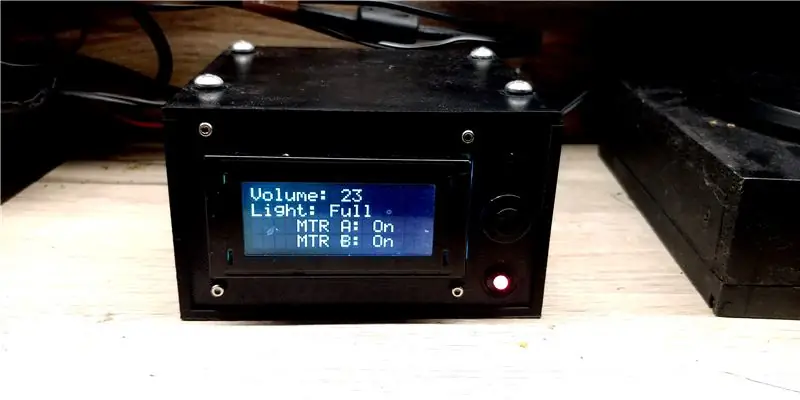
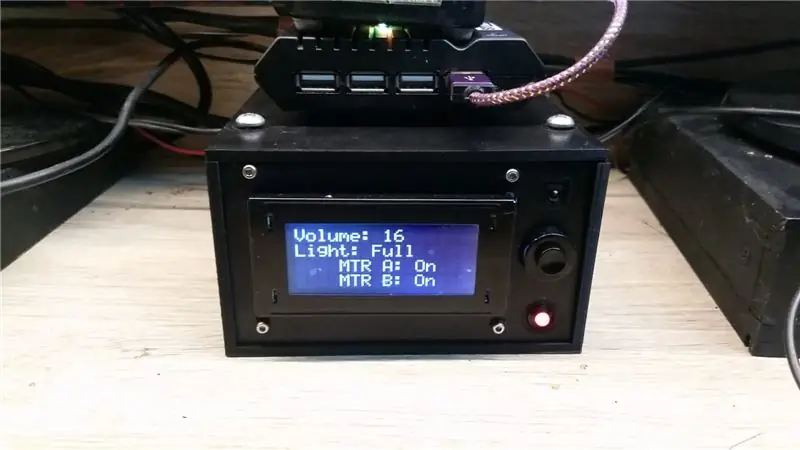
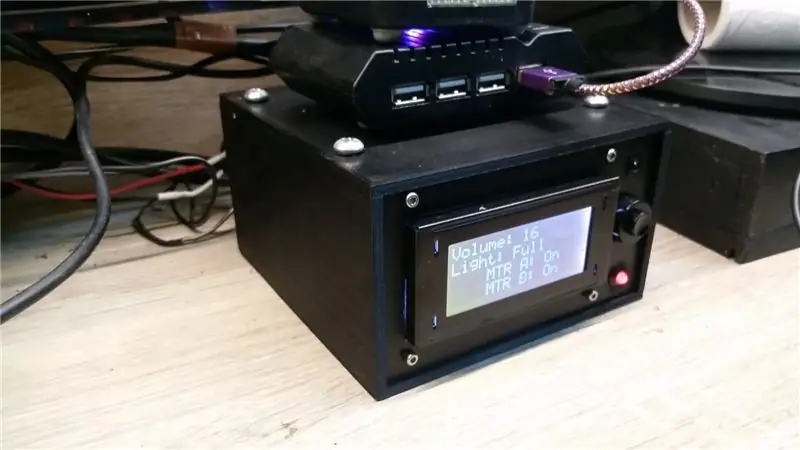
Récemment, j'ai rencontré un problème, ma paresse est devenue un énorme problème pour moi à la maison. Dès que je vais au lit, j'aime mettre une belle lumière LED avec des séries en cours de lecture sur mon PC. Mais… Si je veux éteindre ces choses, je dois me LEVER à chaque fois et les éteindre à la main. Ainsi, j'ai décidé de construire un contrôleur complet pour l'ensemble du bureau du PC, où je peux allumer et éteindre les moniteurs et la lumière, régler le volume des haut-parleurs et la luminosité de l'éclairage de la bande LED en appuyant sur un bouton correspondant de ma télécommande.
Le projet est un boîtier de contrôleur de bureau/établi PC, qui est actionné par une télécommande IR. Il existe de nombreux types de télécommandes infrarouges disponibles de nos jours, mais ce n'est pas un problème. Ce contrôleur est réglable et peut être associé à tout type de télécommande IR prenant en charge le protocole approprié pour notre capteur utilisé (nous aborderons cela plus tard).
Les fonctions de bureau d'ordinateur contrôlé sont:
- Contrôle de l'alimentation secteur: mise sous/hors tension du moniteur branché à 220 VAC
- Contrôle de l'alimentation CC: allumer/éteindre le moniteur branché sur l'alimentation CC (jusqu'à 48 V)
- Contrôle du volume audio: contrôle complet du volume stéréo transmis aux haut-parleurs
- LED Strip Lighting Control: Contrôle complet de la luminosité de l'éclairage de la bande LED
L'appareil dispose d'une interface utilisateur bien conçue et de compartiments mécaniques réglables, ce qui le rend facile à construire et à utiliser:
- Affichage: l'état en temps réel de tous les systèmes contrôlés est présenté sur l'écran LCD 16x4
- LED RVB: pour un retour supplémentaire pour le système, le but de ceci est de reconnaître à l'utilisateur qu'il y a un signal accepté reçu de la télécommande IR
- Système d'appairage: l'appareil contient un seul bouton-poussoir, qui doit être enfoncé pour le processus d'appairage. Lorsque le processus de couplage est lancé, nous pouvons coupler n'importe quelle télécommande infrarouge à notre appareil en suivant les instructions affichées sur un écran.
Après avoir couvert les bases, construisons-le !
Étape 1: Explication
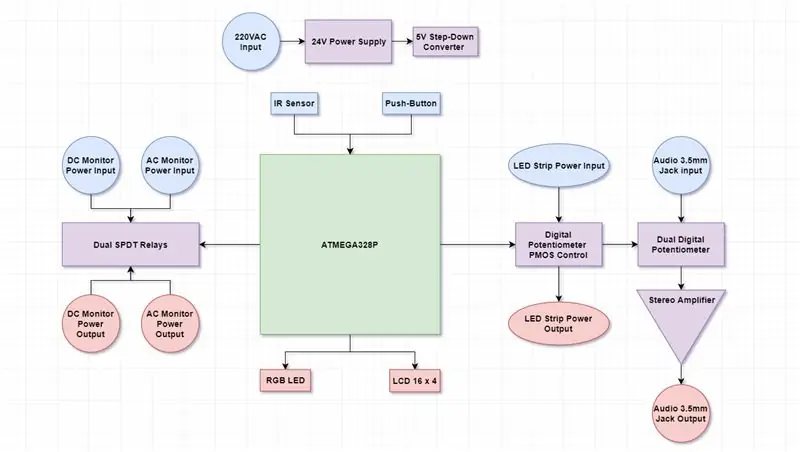
Le fonctionnement de l'appareil peut être considéré comme simple, en raison de son manque de complexité de conception. Comme on peut le voir dans le schéma fonctionnel, le "cerveau" est le microcontrôleur AVR, tandis que toutes les autres parties sont contrôlées par ce "cerveau". Afin d'organiser l'ensemble de l'image dans notre esprit, décrivons la conception bloc par bloc:
Unité d'alimentation: La source d'alimentation pour l'appareil qui a été sélectionné est le bloc d'alimentation à bande LED, capable de fournir une entrée 24VDC au système. Le microcontrôleur, les relais, les potentiomètres numériques et les amplificateurs audio fonctionnent tous à 5 V, c'est pourquoi le convertisseur abaisseur DC-DC a été ajouté à la conception. La principale raison du DC-DC au lieu du régulateur linéaire est la dissipation de puissance et le manque d'efficacité. Supposons que nous utilisions le LM7805 classique avec une entrée 24V et une sortie 5V. Lorsque le courant atteint des valeurs significatives, la puissance qui se dissipera sous forme de chaleur sur le régulateur linéaire sera énorme et pourra surchauffer, attachant un bourdonnement aux circuits audio:
Pout = Pin + Pdiss, donc à 1A on obtient: Pdiss = Pin - Pout = 24*1 - 5*1 = 19W (de puissance dissipée).
Microcontrôleur: Afin d'écrire le code aussi vite que possible, j'ai choisi l'ATMEGA328P basé sur AVR, qui est largement utilisé dans les cartes Arduino UNO. Selon les exigences de conception, nous utiliserons la quasi-totalité du support périphérique: interruptions, temporisateurs, UART, SPI et cetera. Comme il s'agit d'un bloc principal du système, il s'interconnecte avec toutes les pièces de l'appareil
-
Interface utilisateur: Le panneau avant de l'appareil contient toutes les pièces avec lesquelles l'utilisateur doit interagir:
- Capteur IR: Capteur pour décoder les données de la télécommande IR.
- Bouton-poussoir: est nécessaire pour coupler la télécommande infrarouge à l'appareil
- LED RVB: accessoire esthétique pour fournir un retour d'information sur la réception d'informations par le système
- LCD: représentation graphique de ce qui se passe à l'intérieur de l'appareil
Contrôle des moniteurs: afin de rendre l'appareil capable de commuter l'alimentation sur les moniteurs du PC, il est nécessaire de gérer des valeurs de tension élevées. Par exemple, mes moniteurs Samsung ne partagent pas du tout la configuration de l'alimentation: l'un est alimenté par 220 VAC tandis que l'autre est alimenté par son propre bloc d'alimentation de 19,8 V. Ainsi, la solution consistait à créer un circuit de relais pour chacune des lignes électriques du moniteur. Ces relais sont contrôlés par MCU et sont totalement séparés, ce qui rend la transmission de puissance du moniteur indépendante pour chaque moniteur
Contrôle de la lumière: j'ai une bande de LED, qui est fournie avec l'alimentation 24 VCC jointe, qui est utilisée comme entrée d'alimentation du système. Puisqu'il est nécessaire de conduire un courant important à travers la bande LED, son mécanisme de luminosité implique un circuit limiteur de courant basé sur un MOSFET, qui fonctionne dans une région linéaire de zone active
Contrôle du volume: ce système basé sur le passage des signaux audio sur les canaux GAUCHE et DROIT via des diviseurs de tension, où la tension appliquée est modifiée via le mouvement d'essuie-glace du potentiomètre numérique. Il y a deux circuits de base LM386 où à chaque entrée il y a un seul diviseur de tension (nous y reviendrons plus tard). L'entrée et la sortie sont des jacks stéréo 3,5 mm
Il semble que nous ayons couvert toutes les parties intégrantes des circuits. Passons aux schémas électriques…
Étape 2: Pièces et instruments
Tout ce dont nous avons besoin pour construire le projet:
Composants electroniques
-
Composants communs:
-
Résistances:
- 6x10K
- 1x180R
- 2 x 100R
- 1x1K
- 2x1M
- 2 x 10R
- Condensateurs:
-
- 1x68nF
- 2 x 10uF
- 4 x 100nF
- 2 x 50nF
- 3 x 47 uF
-
Divers:
- Diodes: 2 x 1N4007
- Tondeuse: 1 x 10K
- BJT: 3 x 2N2222A
- P-MOSFET: ZVP4424
-
Circuits intégrés:
- Microcontrôleur: 1 x ATMEGA328P
- Ampli audio: 2 x LM386
- Potentiomètre numérique double: 1 x MCP4261
- Potentiomètre numérique unique: 1 x X9C104P
- DC-DC: 1 x BCM25335 (peut être remplacé par n'importe quel appareil compatible DC-DC 5V)
- Amplificateur opérationnel: 1 x LM358
- Relais: double SPDT tolérant 5 V
- Alimentation externe 24V
-
Interface utilisateur:
- ACL: 1x1604A
- Capteur IR: 1 x CDS-IR
- Bouton poussoir: 1 x SPST
- LED: 1 x LED RVB (4 contacts)
-
Connecteurs:
- Borniers: 7 x 2 contacts TB
- Connecteurs carte à fil: câble 3 x 4 contacts + connecteurs de boîtier
- Audio: 2 connecteurs jack femelle 3,5 mm
- Bloc d'alimentation de sortie: 2 connecteurs d'alimentation 220 VAC (mâles)
- Prise CC: 2 x connecteurs mâles CC
- Bande LED et alimentation externe: 1 x connecteurs assemblés carte-à-fil à 4 contacts + câble
Composants mécaniques
- Filament pour imprimante 3D - PLA+ de n'importe quelle couleur
- 4 vis de 5 mm de diamètre
- Planche de prototypage d'au moins 9 x 15 cm
- Stock de fils non utilisés
Outils
- Imprimante 3D (j'ai utilisé Creality Ender 3 avec un lit de type verre attaché)
- Pistolet à colle chaude
- Pince à épiler
- Pince
- Coupeur
- Alimentation externe 24V
- Oscilloscope (facultatif)
- Programmeur AVR ISP (pour le clignotement du MCU)
- Visseuse électrique
- Fer à souder
- Générateur de fonctions (facultatif)
-
Étape 3: Schémas électriques
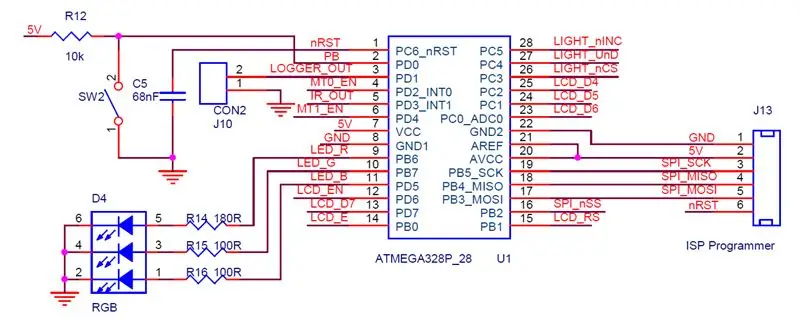
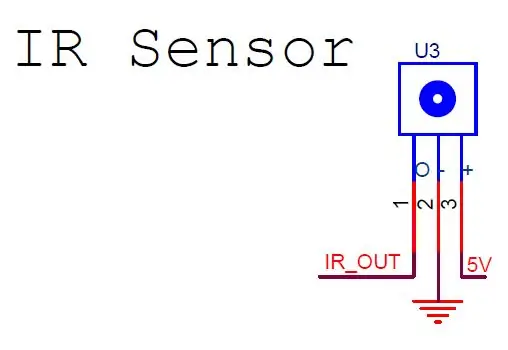
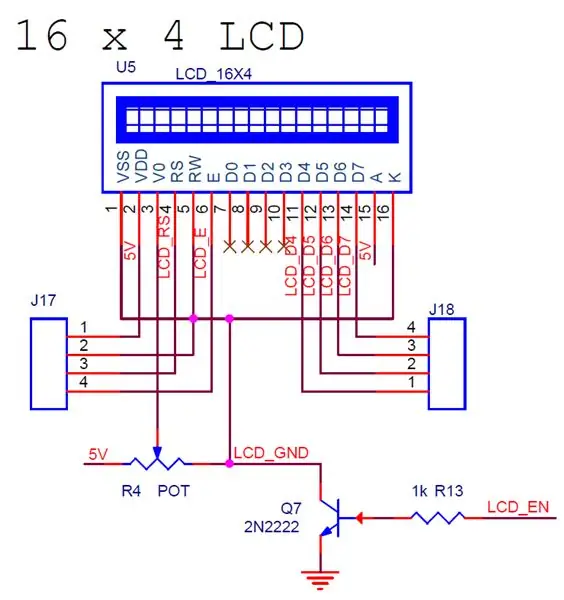
Le schéma de principe est divisé en circuits séparés, ce qui peut nous faciliter la compréhension de son fonctionnement:
Unité de microcontrôleur
Il s'agit d'un ATMEGA328P basé sur un AVR, comme il a été décrit ci-dessus. Il utilise un oscillateur interne et fonctionne à 8 MHz. J13 est le connecteur du programmeur. Il y a beaucoup de programmeurs dans le monde AVR, dans ce projet, j'ai utilisé un programmeur ISP V2.0 d'eBay. J10 est la ligne UART TX et est principalement utilisée à des fins de débogage. Lors de la construction d'une procédure de gestion des interruptions, il est parfois bon de savoir ce que le système doit nous dire de l'intérieur. D4 est une LED RVB qui est pilotée directement par le MCU, en raison de ses faibles intensités nominales. La broche PD0 est attachée à un bouton poussoir de type SPST avec un pull-up externe.
Capteur infrarouge
Le capteur IR utilisé dans ce projet est un capteur IR à trois broches à usage général disponible sur eBay, à des prix très avantageux. La broche du signal de sortie IR est connectée à la broche d'entrée d'interruption (INT1) du MCU,
ACL
L'affichage est une implémentation simple d'un affichage 1604A, avec une transmission de données à 4 bits. Toutes les broches de contrôle/données sont liées au MCU. Il est important de noter que l'écran LCD est connecté à la carte principale via deux connecteurs J17, J18. Afin d'activer/désactiver le module LCD, il existe un seul commutateur BJT, commutant la ligne de masse pour l'écran LCD.
Source de courant
Tous les circuits internes, à l'exception de la bande LED, fonctionnent à 5V. Comme il a été mentionné précédemment, la source d'alimentation 5V est un simple module DC-DC (Ici eBay m'a aidé à trouver la solution), qui convertit 24V en 5V, sans problème de chauffage, qui pourrait se produire sur le régulateur linéaire. Les condensateurs C[11..14] sont utilisés pour la dérivation et sont nécessaires pour cette conception en raison du bruit de commutation présent sur les lignes d'alimentation CC-CC - à la fois en entrée et en sortie.
Contrôle du moniteur
Les circuits de contrôle du moniteur ne sont que des systèmes de commutation de relais. Étant donné que j'ai deux moniteurs, l'un est alimenté à partir de 220 VCA et le second à partir de 19,8 V, une implémentation différente est requise.. (N'oubliez pas de fixer une diode inverse pour une décharge de courant appropriée !). À 220 VCA, le relais commute les lignes LIGNE et NEUTRE et à 19,8 V, le relais commute uniquement la ligne d'alimentation CC - puisqu'il a sa propre alimentation, les lignes de masse sont partagées pour les deux circuits.
Contrôle du volume audio
Je voulais utiliser des amplificateurs audio LM386 comme tampons pour les diviseurs de tension, pour une transmission soignée du signal audio. Chaque canal - gauche et droit provient d'une entrée jack audio 3,5 mm. Étant donné que le LM386 implémente au minimum une configuration de pièces avec un gain standard de G = 20, il existe une résistance de 1 MOhm pour les deux canaux. De cette façon, nous pouvons réduire la quantité totale de puissance pour les canaux d'entrée du système de haut-parleurs:
V(out-max) = R(max) * V(in) / (R(max) + 1MOhm) = V(in) * 100K/1,1M.
Et le gain total est: G = (Vout / Vin) * 20 = 20 / 11 ~ 1,9
Le diviseur de tension est un simple réseau de potentiomètre numérique, où l'essuie-glace transmet le signal au tampon LM386 (U2 est le circuit intégré). L'appareil partage le SPI pour tous les circuits périphériques, où seules les lignes ENABLE sont séparées pour chacun d'eux. Le MCP4261 est un circuit intégré de potentiomètre numérique linéaire 100K 8 bits, ainsi chaque étape de l'augmentation du volume est exprimée: dR = 100 000 / 256 ~ 390 Ohm.
Les broches A et B pour chaque canal GAUCHE et DROITE sont liées à GND et 5V. Ainsi, à la position de l'essuie-glace en bas, tout le signal audio est transmis à GND via la résistance de 1 MOhm MUTING volume de l'appareil.
Contrôle de la luminosité de la bande LED:
L'idée du contrôle de la luminosité est similaire au contrôle du volume, mais ici nous avons un problème: le potentiomètre numérique peut transmettre uniquement des signaux dont les amplitudes ne dépassent pas 5V à GND. Ainsi, l'idée est de placer un simple tampon Op-Amp (LM358) après le diviseur de tension du potentiomètre numérique. et une tension de commande liée directement à un transistor PMOS.
X9C104P est un seul potentiomètre numérique 8 bits d'une valeur de 100KOhm. Nous pouvons obtenir un calcul pour la tension de grille en suivant simplement des règles algébriques pour le flux de courant:
V(gate) = V(essuie-glace) * (1 + R10/R11) = 2V(essuie-glace) ~ 0 - 10V (ce qui est suffisant pour allumer/éteindre et contrôler la luminosité)
Étape 4: Création d'un boîtier 3D
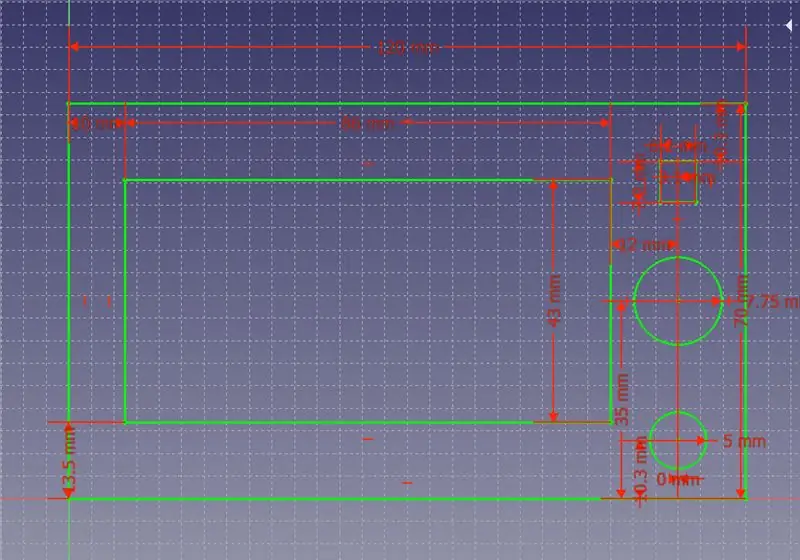
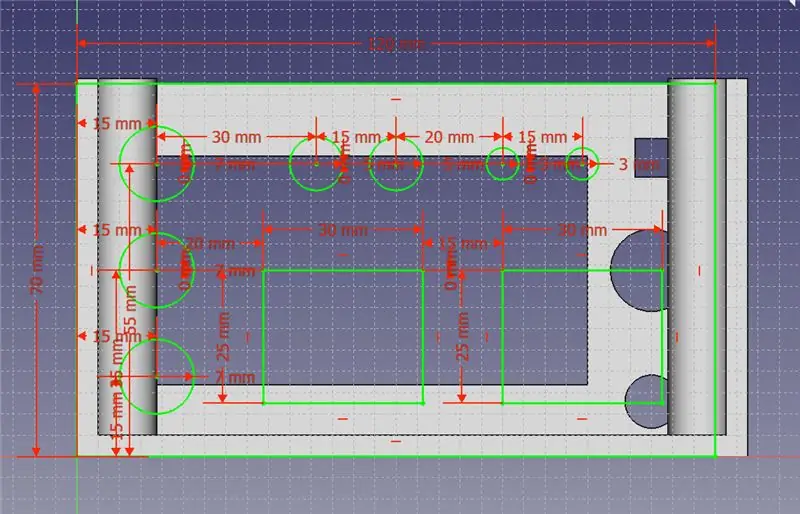
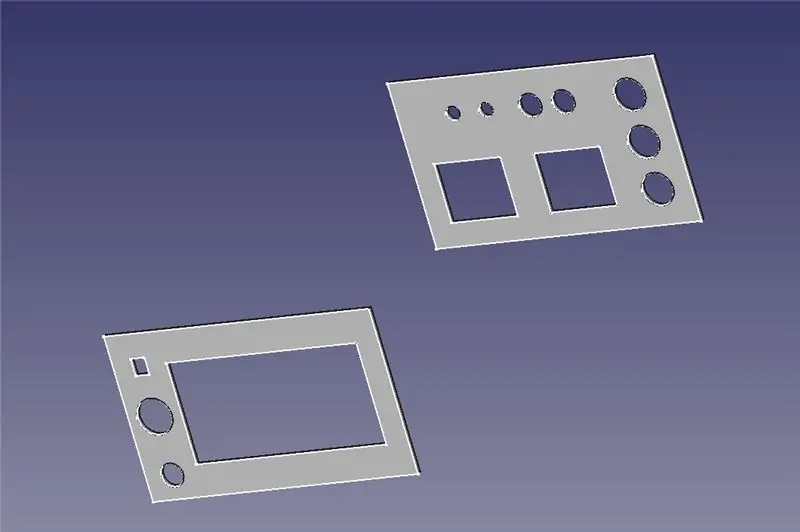
Pour le boîtier de l'appareil, j'ai utilisé un FreeCAD v0.18 qui est un excellent outil même pour les novices comme moi.
Type de boîtier
J'ai voulu créer une boîte où il y a une seule coque qui va souder la carte soudée. Le panneau avant contient toutes les pièces de l'interface utilisateur et le panneau arrière contient tous les connecteurs de l'électronique du bureau. Ces panneaux sont insérés directement dans une coque principale avec un assemblage à 4 vis au niveau du capot supérieur.
Dimensions
Probablement l'étape la plus importante de la séquence. Il est nécessaire de prendre en compte toutes les distances et régions de coupure appropriées. Comme on le voit sur les photos, tout d'abord les dimensions qui ont été prises sont sur les panneaux avant et arrière:
Panneau avant: régions de coupure pour LCD, commutateur, LED et capteur IR. Toutes ces dimensions sont dérivées de la fiche technique du fabricant pour chaque pièce. (Dans le cas où vous souhaitez utiliser une pièce différente, il est nécessaire de rassurer toutes les régions coupées.
Panneau arrière: deux trous pour prises audio 3,5 mm, deux connecteurs d'alimentation 220 V à 3 lignes, deux prises mâles pour l'alimentation CC et des trous supplémentaires pour la bande LED et l'alimentation de l'appareil
Coque supérieure: Cette coque est utilisée uniquement pour attacher toutes les pièces ensemble. Étant donné que les panneaux avant et arrière sont insérés dans la coque inférieure.
Coque inférieure: la base de l'appareil. Il contient les panneaux, la carte électronique soudée et les vis fixées au capot supérieur.
Concevoir les pièces
Une fois les panneaux créés, nous pouvons passer à la coque inférieure. Il est recommandé d'assurer le logement des pièces complètement après chaque étape. La coque inférieure est une forme extrudée simple à base de rectangle, avec des poches symétriques près des bords de la coque (voir photo 4).
Après l'étape de poche, il est nécessaire de créer une base à 4 vis pour la fixation du couvercle. Ils ont été conçus comme une insertion de cylindres primitifs de rayon différent, où le cylindre découpé est disponible après l'opération XOR.
Nous avons maintenant une coque inférieure complète. Afin de créer une couverture appropriée, il est nécessaire de faire un croquis sur le dessus de la coque et de créer les mêmes points de cylindre (je n'ai attaché que des points à percer, mais il est possible de créer des trous de diamètres fixes).
Une fois l'ensemble du boîtier de l'appareil terminé, nous pouvons le vérifier en assemblant les pièces ensemble.
Étape 5: Impression 3D
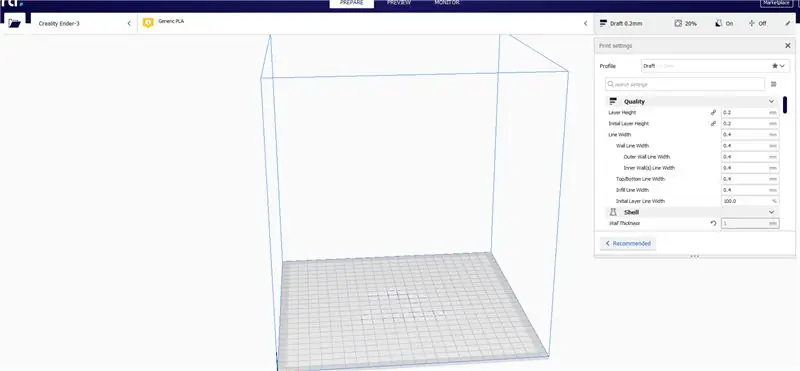
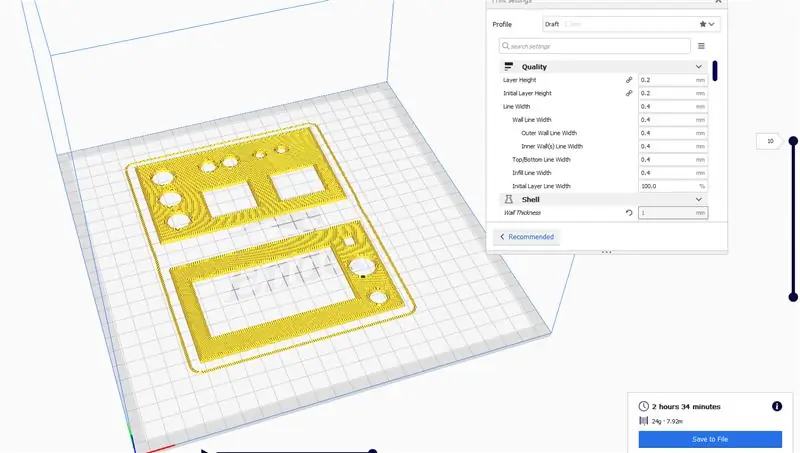
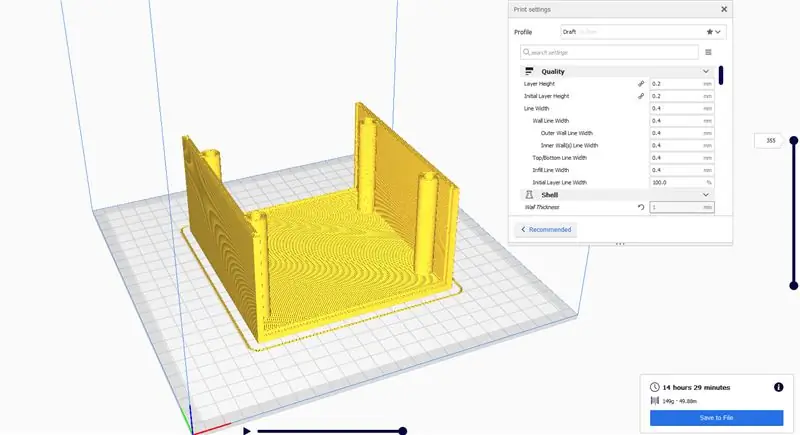
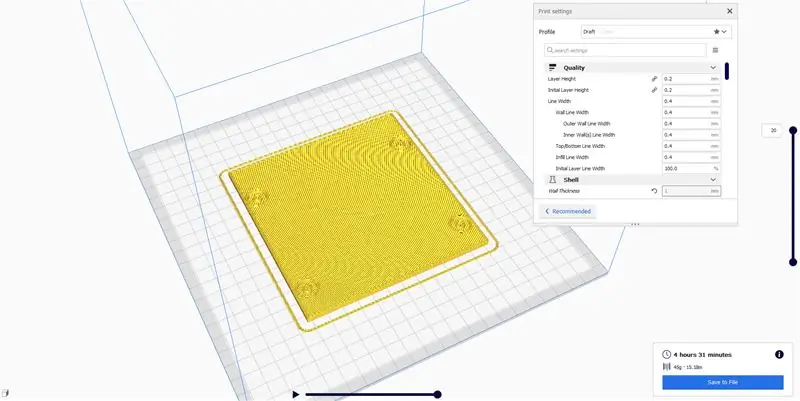
Enfin, nous sommes là et pouvons avancer vers l'impression. Des fichiers STL sont disponibles pour ce projet, basés sur ma conception. Il peut y avoir un problème avec ces fichiers à imprimer, car aucune tolérance n'est prise en compte. Ces tolérances peuvent être ajustées dans l'application slicer (j'ai utilisé un Ultimaker Cura) pour les fichiers STL.
Les pièces décrites ont été imprimées sur Creality Ender 3, avec lit de verre. Les conditions ne sont pas loin des standards, mais doivent être prises en compte:
- Le diamètre de la buse: 0.4mm
- Densité de remplissage: 50 %
- Support: Il n'y a aucun besoin d'attachement de support du tout
- Vitesse recommandée: 50 mm/s pour le projet
Dès que les pièces du boîtier sont imprimées, il est nécessaire de les vérifier dans la vraie vie. S'il n'y a pas de problème lors de la fixation des pièces du boîtier, nous pouvons passer à l'étape d'assemblage et de soudure.
Il y a un problème avec la visionneuse STL dans les instructables, je suggère donc de la télécharger d'abord:)
Étape 6: Assemblage et soudure
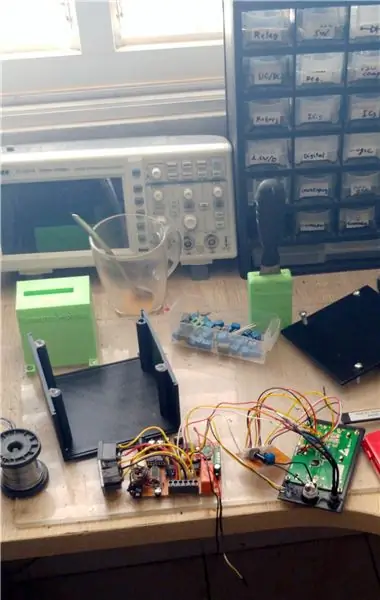
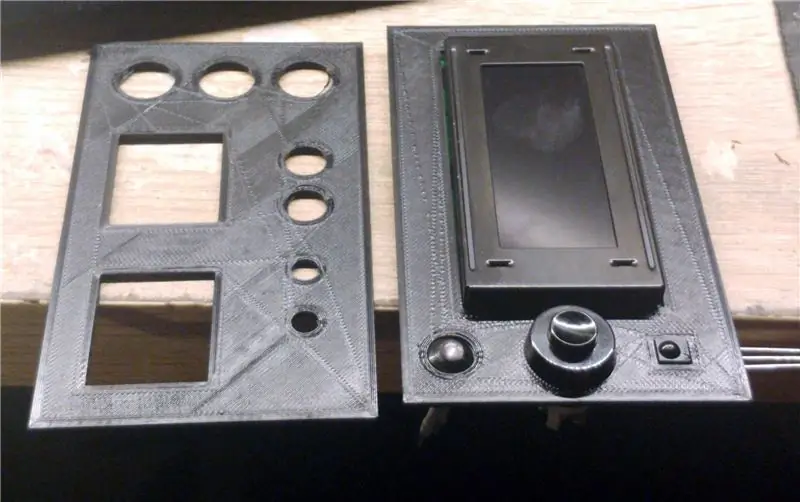
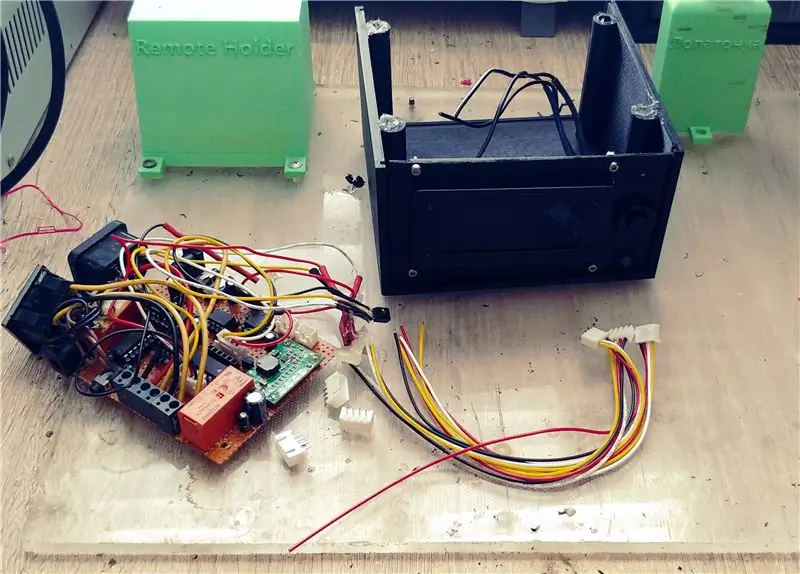
Le processus de soudure est difficile, mais si nous séparons la séquence en différents circuits, il nous sera beaucoup plus facile de la terminer.
- Circuit MCU: Doit être soudé en premier avec son connecteur de programmation femelle. À ce stade, nous pouvons réellement tester son fonctionnement et sa connectivité.
- Circuit audio: Le deuxième. N'oubliez pas de fixer les borniers sur la carte soudée. Il est très important d'isoler le chemin de retour des circuits audio des circuits numériques - en particulier les circuits intégrés de potentiomètre numérique, en raison de leur nature bruyante.
- Circuits de surveillance: similaire au circuit audio, n'oubliez pas de fixer le bornier aux ports d'E/S.
- Connecteurs et panneau d'interface utilisateur: les dernières choses qui doivent être connectées. Le panneau d'interface utilisateur est connecté à la carte soudée via un connecteur Board-To-Wire, où les fils sont soudés directement dans les pièces externes.
Après le processus de soudure, il y a une séquence simple de pièces jointes mécaniques. Comme il a été remarqué ci-dessus, il est nécessaire de mettre 4 vis (j'en ai utilisé un de 5 mm de diamètre) aux coins, celles présentes sur le boîtier. Après cela, il est nécessaire de connecter les pièces de l'interface utilisateur et les connecteurs du panneau arrière au monde extérieur. L'outil préféré est un pistolet à colle chaude.
Il sera très utile de vérifier le logement des pièces dans le boîtier imprimé. Si tout semble bon, nous pouvons passer à l'étape de programmation.
Étape 7: Programmation
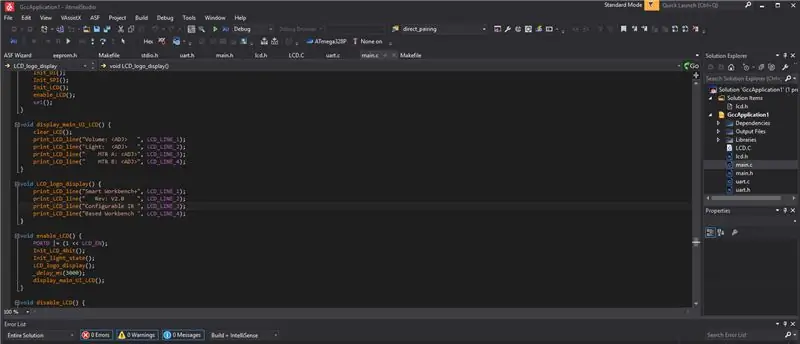

Cette étape est amusante. Comme il y a une variété de choses qui doivent fonctionner, nous utiliserons un total de 5 services du MCU: interruption externe, périphériques SPI, UART pour la journalisation, minuteries pour un comptage précis et EEPROM pour stocker nos codes à distance IR.
L'EEPROM est un outil essentiel pour nos données stockées. Afin de stocker les codes de télécommande IR, il est nécessaire d'effectuer une séquence d'appuis sur les boutons. Après chaque séquence, le système se souviendra des codes indépendamment de l'état, que l'appareil soit alimenté ou non.
Vous pouvez trouver l'ensemble du projet Atmel Studio 7 archivé en tant que RAR au bas de cette étape.
La programmation est effectuée par AVR ISP Programmer V2, 0, via une simple application appelée ProgISP. C'est une application très conviviale, avec une interface utilisateur complète. Sélectionnez simplement le fichier HEX approprié et téléchargez-le sur le MCU.
IMPORTANT: Avant toute programmation du MCU, assurez-vous que tous les paramètres appropriés sont définis en fonction des exigences de conception. Comme la fréquence d'horloge interne - par défaut, il a son fusible diviseur actif au réglage d'usine, il doit donc être programmé au niveau logique HAUT.
Étape 8: Couplage et test
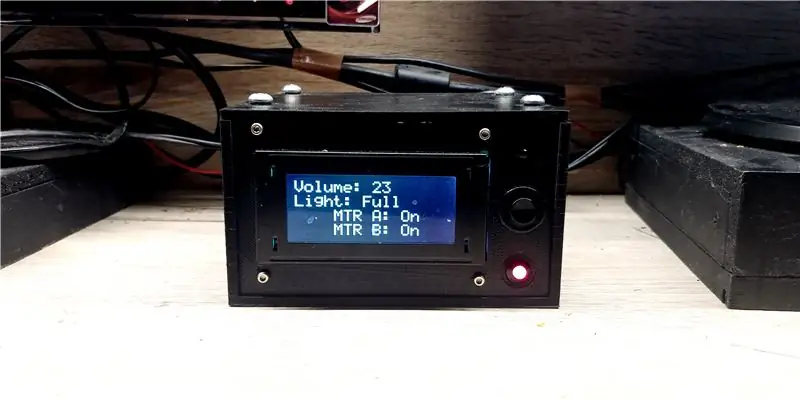
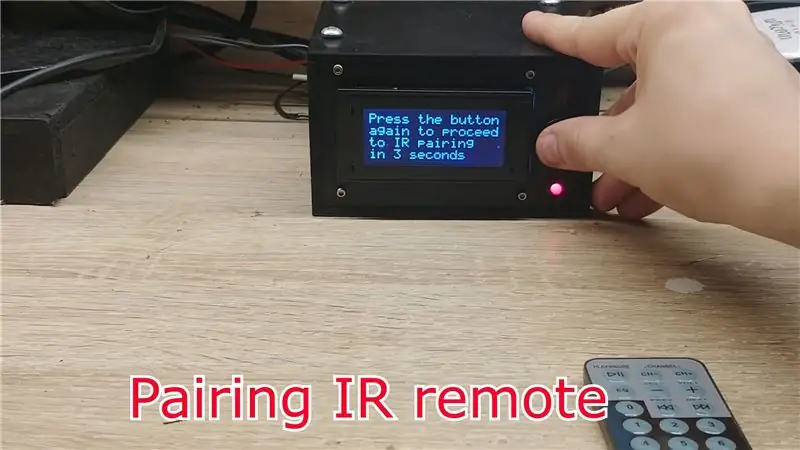
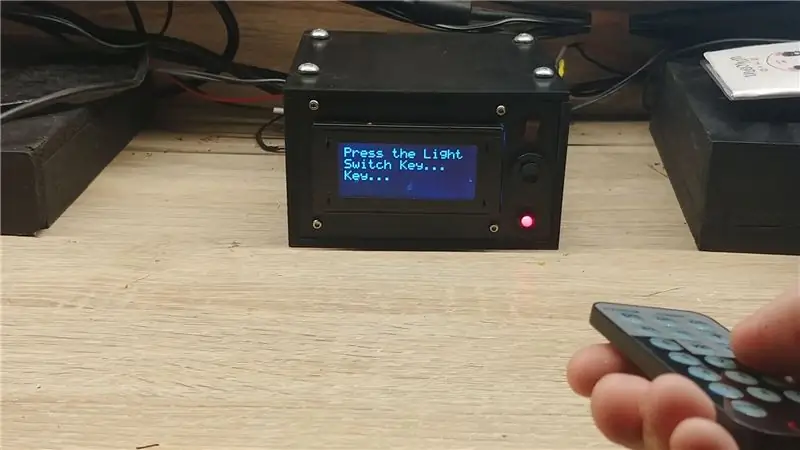
Nous sommes enfin là, après tout le travail acharné qui a été fait:)
Afin d'utiliser correctement l'appareil, une séquence d'appariement est nécessaire, ainsi l'appareil "se souviendra" de la télécommande IR connectée qui serait utilisée. Les étapes du jumelage sont les suivantes:
- Allumez l'appareil, attendez l'initialisation de l'affichage de l'interface utilisateur principale
- Appuyez sur le bouton pour la première fois
- Avant que le compteur n'atteigne zéro, appuyez une autre fois sur le bouton
- Appuyez sur la touche appropriée pour laquelle vous souhaitez avoir une fonction spécifique, selon l'appareil
- Redémarrez l'appareil, assurez-vous qu'il répond maintenant aux clés qui ont été définies.
Et c'est tout!
J'espère que vous trouverez cette instructable utile, Merci d'avoir lu!
Conseillé:
Samytronix Pi : ordinateur de bureau DIY Raspberry Pi (avec GPIO accessible) : 13 étapes (avec photos)

Samytronix Pi : Ordinateur de bureau DIY Raspberry Pi (avec GPIO accessible) : Dans ce projet, nous allons créer un ordinateur de bureau Raspberry Pi que j'appelle Samytronix Pi. Cette construction d'ordinateur de bureau est principalement composée de feuilles acryliques découpées au laser de 3 mm. Samytronix Pi est équipé d'un moniteur HD, de haut-parleurs et surtout d'un accès
DIY LED Light - Lampe d'ambiance de bureau moderne avec télécommande : 8 étapes (avec photos)
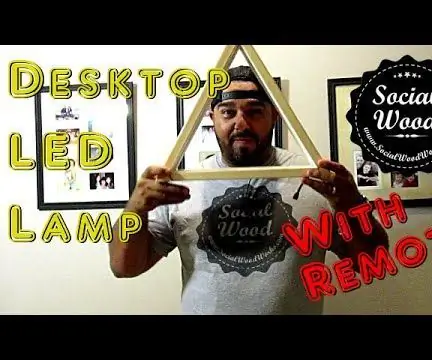
DIY LED Light - Lampe d'ambiance de bureau moderne avec télécommande: Dans cet article, je vais passer en revue le processus que j'ai utilisé pour construire cette impressionnante lampe d'ambiance à LED en forme de pyramide. J'ai utilisé de l'érable pour la structure principale et des épines en acajou pour plus de résistance. Pour les lumières, j'ai utilisé des lumières LED RVB qui viennent dans une bande de 16 pieds t
Support d'ordinateur portable bon marché / Convertisseur d'ordinateur portable en ordinateur de bureau : 3 étapes
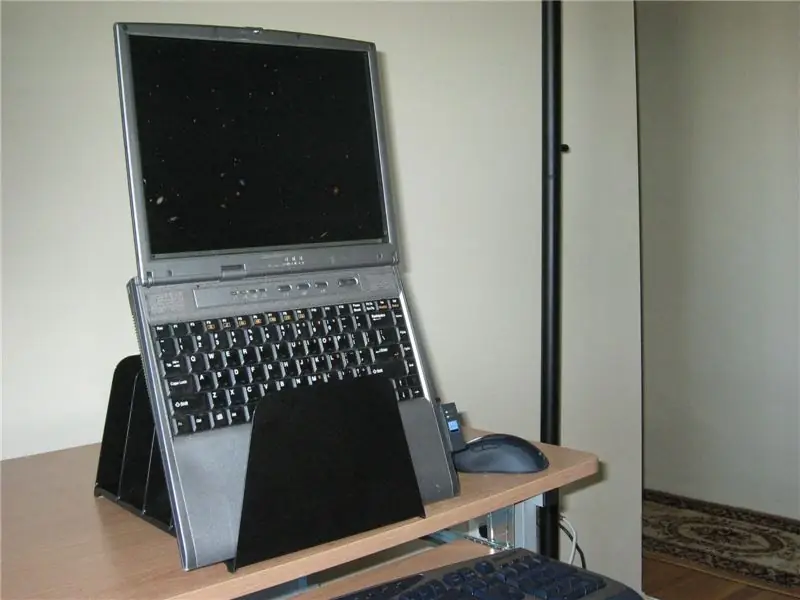
Support d'ordinateur portable bon marché / Convertisseur d'ordinateur portable en ordinateur de bureau : je me retrouve à utiliser mon ordinateur portable pendant de longues périodes. Cela devient inconfortable au bout d'un moment. Le clavier et l'écran doivent idéalement être séparés pour réduire la fatigue du cou lors d'une utilisation prolongée. Si vous êtes un utilisateur d'ordinateur portable à temps plein, je vous suggère de construire s
Comment transformer votre téléphone portable LG EnV 2 en un modem commuté portable pour votre ordinateur portable (ou ordinateur de bureau): 7 étapes
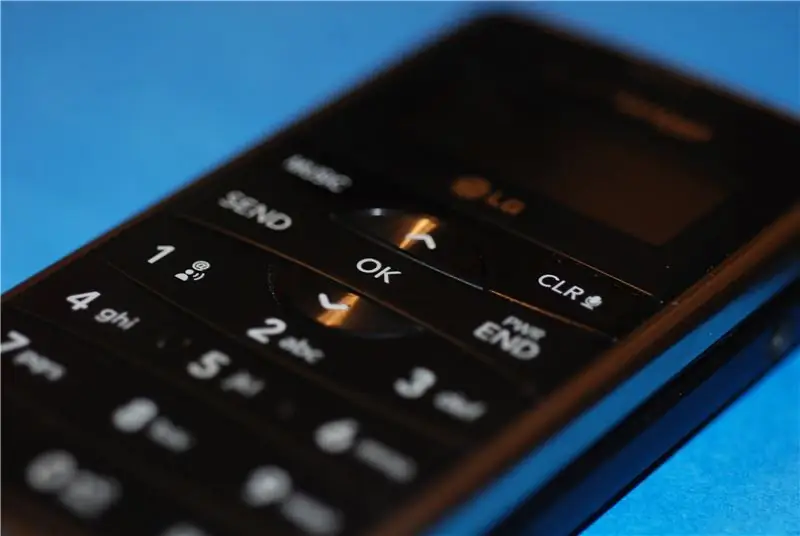
Comment transformer votre téléphone portable LG EnV 2 en un modem commuté portable pour votre ordinateur portable (ou ordinateur de bureau): Nous avons tous à un moment donné besoin d'utiliser Internet là où cela n'était tout simplement pas possible, comme dans la voiture , ou en vacances, où ils facturent une somme d'argent coûteuse par heure pour utiliser leur wifi. enfin, j'ai trouvé un moyen simple d'obtenir
Ordinateur de bureau de refroidissement pour ordinateur portable : 5 étapes
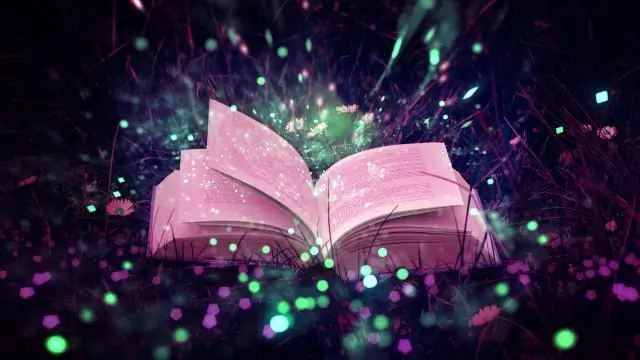
Ordinateur de bureau de refroidissement pour ordinateur portable : ce Instructable vous montrera comment j'ai refroidi mon ordinateur portable et tout ce qui l'entoure. Il y a tellement de façons différentes de le faire que je vais juste être général avec les descriptions et les éléments que j'ai utilisés. Si votre bureau est chaud à cause de votre ordinateur portable, cela résoudra le problème