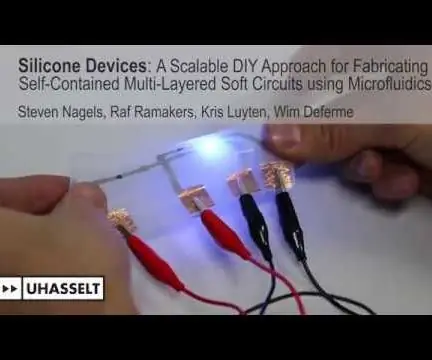
Table des matières:
- Étape 1: Démarrage de la découpe au laser + Plaques de transfert
- Étape 2: Préparation de la plaque de départ pour les composants
- Étape 3: Préparation de la plaque de transfert pour une adhérence sélective
- Étape 4: Placement des composants
- Étape 5: Application d'apprêt
- Étape 6: Moulage/lame enduite de silicone
- Étape 7: Collez la plaque de transfert
- Étape 8: Retirez la plaque de départ
- Étape 9: Masque de pochoir pour la couche conductrice supérieure
- Étape 10: Couche conductrice supérieure
- Étape 11: Bas à composants principaux
- Étape 12: Enduit de silicone pour moulage/lame
- Étape 13: Masque de pochoir pour la couche conductrice inférieure
- Étape 14: VIA de haut en bas
- Étape 15: Couche conductrice inférieure
- Étape 16: Enduit de silicone pour moulage/lame
- Étape 17: Tampons de contact
- Étape 18: Échantillon coupé gratuitement
- Étape 19: Admirez
2025 Auteur: John Day | [email protected]. Dernière modifié: 2025-01-23 14:46
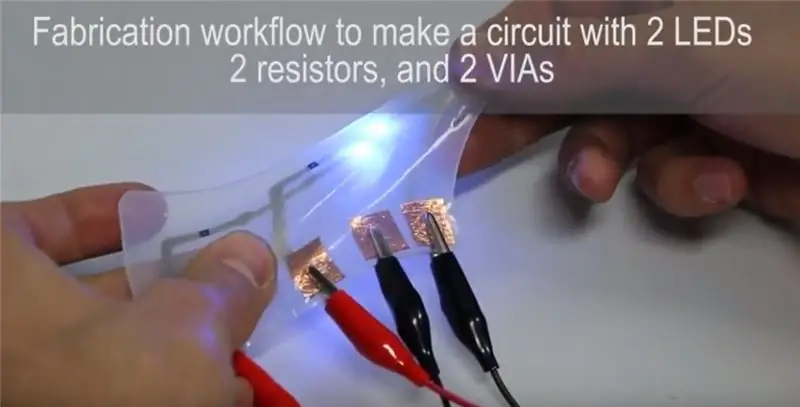

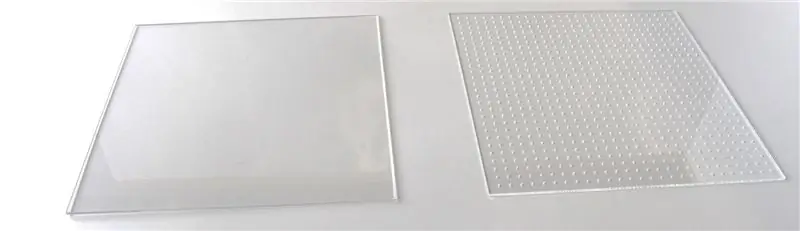
Les dispositifs en silicone offrent les premiers avantages de l'électronique souple et extensible grâce à une approche conviviale pour les fabricants. En suivant ce Instructable, vous apprendrez les compétences de base nécessaires pour créer vos propres circuits électroniques souples entièrement intégrés. Pensez à Baymax ! C'est une excellente vision future d'un robot mou qui ne deviendra réalité qu'en développant des circuits électroniques souples.
« Attendez Noagels… Qu'entendez-vous exactement par ce tour de passe-passe de « circuits électroniques souples » ? »
Eh bien, en bref, l'électronique extensible promet de naturaliser la façon dont nous sommes entourés et interagissons avec nos appareils. Ce sont littéralement des circuits électroniques souples et « extensibles » qui ouvrent de nouvelles possibilités dans l'interaction homme-machine et constituent une technologie de conduite clé derrière la robotique douce.
Les dispositifs en silicone représentent une approche de fabrication unique car ils apportent la technologie à la communauté Maker qui résidait auparavant dans des groupes de recherche scientifique. Bien sûr, le processus de fabrication démontré par Silicone Devices n'est pas la seule voie vers l'électronique extensible et souple et n'est pas non plus une toute nouvelle. La science fonctionne par étapes progressives. L'une de nos mesures est de rendre la technologie facile à mettre en œuvre et à atteindre les fabricants du monde entier. (Cela signifie vous. Ici, maintenant !) Grâce à notre approche de fabrication, vous pouvez créer vos propres circuits logiciels. Silicone Devices prend en charge l'inclusion de microcontrôleurs, de composants d'E/S et d'une source d'alimentation, le tout combiné dans un appareil autonome.
Ce travail a été réalisé grâce à la collaboration de Raf Ramakers, Kris Luyten, Wim Deferme et Steven Nagels (c'est moi) à l'Université de Hasselt, en Belgique. La technique présentée dans cette instructable est publiée dans le premier lieu de l'interaction homme-machine: les facteurs humains dans les systèmes informatiques (CHI 2018). Cette instructable vise à communiquer nos résultats de recherche au-delà de la communauté universitaire. Il y a des informations plus détaillées à lire, si vous le souhaitez: Voici la page du projet de Silicone Devices, la publication académique complète peut être trouvée ici, et un contexte plus général sur la fabrication de l'électronique extensible basée sur les interconnexions peut être trouvé ici.
Cependant - pour vous assurer de ne pas TL; DR - passons aux choses sérieuses !
Ce dont vous aurez besoin:
- Accès à une découpeuse laser CO2 d'un Fablab ou Makerspace (référence: un Trotec Speedy 100R 60W)
- Aérographe (de préférence) ou flacon pulvérisateur (alternative plus accessible)
- feuilles d'acrylique/PMMA/plexiglas (assez pour couper 2 carrés de 280x280mm) nous avons utilisé 3mm d'épaisseur, tout à partir de 1,5mm devrait fonctionner
- Autocollant en vinyle noir (assez pour couper 4 carrés d'environ 260x260mm) (nous avons utilisé MacTac 8900 Pro Matte black)
- Spray de démoulage (Voss Chemie Trennspray, Smooth-on Ease Release)
- Métal liquide: Galinstan (le mieux est de garder 10 g sous la main, en fonction de votre gaspillage, vous pouvez utiliser une quantité supérieure à 5 g)
- 2 pipettes jetables de 3 ml pour prélever le Galinstan de son récipient sur le pochoir
- Pinceau fin, tel que de cet ensemble
- Rouleau gommeux doux (également appelé brayer en caoutchouc, comme celui-ci)
- Apprêt silicone (testé avec l'apprêt silicone Bison, le promoteur d'adhérence 3M AP596 peut également fonctionner)
- Un tube de mastic silicone pas cher + distributeur (pistolet à calfeutrer)
- Silicone à durcissement rapide à 2 composants à base de platine (testé avec Siliconesandmore, alternative DragonSkin 10) En utilisant les fichiers de conception fournis, vous ne devez pas dépasser 150 g. La plupart des kits sont cependant vendus par quantités de 1kg.
- 3 tasses à mélanger (> 100 ml) et tiges d'agitation (6 "est le plus pratique)
- Échelle précise à 0,1 ou 0,001 gramme (ces portables font l'affaire)
- Revêtement de lame reconfigurable en hauteur ou version bricolage découpée au laser en hauteurs 1 mm, 1,5 mm et 2 mm (TODO, super court séparé Instructable à ce sujet)
- 2 LED à profil bas de taille 1206 (Digikey, Farnell)
- 2 résistances de 100 ohms de taille 2010 (Digikey, Farnell)
- Ruban cuivre ou aluminium. La feuille est encore meilleure (si la colle du ruban doit être lavée)
- Brucelles fines
- un couteau X-acto
-
Ruban Scotch Magic
Ce tutoriel est assez détaillé ! Ne vous laissez pas rebuter par le nombre d'étapes ou les longues descriptions. Étant donné que nous scellons notre système avec du silicone, il sera difficile de corriger les erreurs qui deviennent apparentes lors de la phase de test. Vous devrez donc lire attentivement chaque étape et la réussir dès le début. L'ensemble du processus ne devrait pas prendre plus de 2 heures si vous avez tous les outils à votre disposition en permanence et utilisez du silicone coulé avec un temps de durcissement de 15 minutes.
Ce tutoriel utilise une conception très basique d'un appareil en silicone, composé de 4 plots de contact, 2 LED et 2 VIA comme exemple de fonctionnement. Le résultat final est montré sur la photo et la vidéo en haut. Bien que cette conception soit assez basique, notre approche de fabrication DIY prend en charge de nombreux types de composants SMD et un nombre illimité de couches. Par conséquent, notre approche s'adapte aux circuits extensibles de toute complexité, comme le démontrent les exemples de conception dans la vidéo youtube liée au début de cette instructable.
Tous les fichiers de conception (regroupés en.zip) ici. Compilation d'instructions pdf simple et pratique ici.
Étape 1: Démarrage de la découpe au laser + Plaques de transfert
Dans un premier temps, vous devrez découper au laser des plaques de support rigides sur lesquelles travailler.
Pourquoi avez-vous besoin de 2 assiettes ? Eh bien, après avoir créé une couche de composants sur la plaque de départ lisse, nous allons coller la feuille de silicone avec les composants à l'intérieur de la plaque de transfert, retourner la pile, retirer la plaque de départ lisse et ainsi exposer les composants par leur dos. La plaque de transfert a de minuscules trous pour permettre à l'air de s'échapper quand à une couche de silicone humide à l'étape 7.
Exigences aux plaques de support:
• Doit être de taille égale pour un alignement correct lors de l'étape de transfert
• Taille: 280 x 280 mm
• Matériau: acrylique transparent (verre PMMA ou Plexi)
• Marquez la plaque de départ dans le coin supérieur gauche, la plaque de transfert en haut à droite
Étape 2: Préparation de la plaque de départ pour les composants
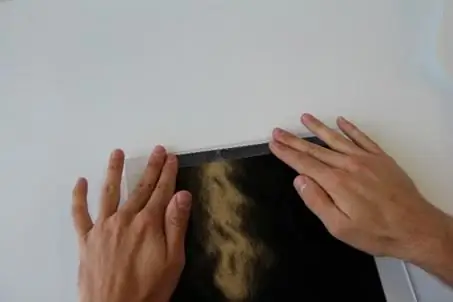
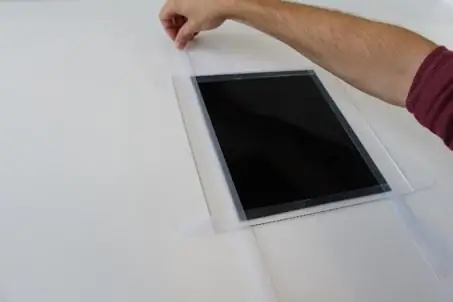
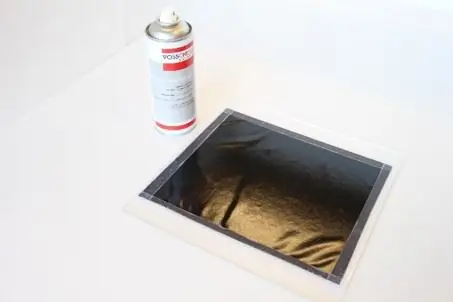
Nous allons commencer à construire notre circuit sur la plaque de départ lisse dans cette étape. Plus tard, cependant, nous voulons retirer cette plaque à nouveau. Par conséquent, vous devez commencer par pulvériser une fine couche de spray de démoulage sur toute la surface de la plaque de départ. Ensuite, prenez un autocollant en vinyle noir dont les dimensions sont de quelques centimètres sous celles de votre plaque de départ. Retirez ensuite le papier autocollant et placez l'autocollant à plat sur et au centre de la plaque de départ; côté collant vers le haut. Fixez l'autocollant en place avec du scotch (veillez à ne pas tirer trop fort sur le ruban car cela provoquerait des plis sur la surface de votre autocollant). Terminez avec une autre couche de spray de démoulage sur le dessus de la surface collante. Assurez-vous de maintenir la buse à environ 20 cm au-dessus de la surface et vaporisez une couche continue et lisse. Astuce: vaporisez deux fois et en quadrillage superposé !
Préparation de la plaque de départ:
• Découpez l'autocollant à la taille (environ 2 cm plus petit que les dimensions de la plaque)
• Mettez une charge statique sur l'autocollant et la plaque en frottant avec un chiffon en coton ou une serviette en papier, cela le fera reposer à plat plus uniformément
• Libérer la plaque de départ de pulvérisation (deux fois et dans un motif de grille)
• Autocollant scotch sur la plaque de départ, côté collant vers le haut
• Marquer les marques de placement des composants avec un cutter laser (P = 6-7) NE PAS COUPER À TRAVERS
• Libérer la feuille collante de pulvérisation (deux fois et dans un motif de grille)
Étape 3: Préparation de la plaque de transfert pour une adhérence sélective
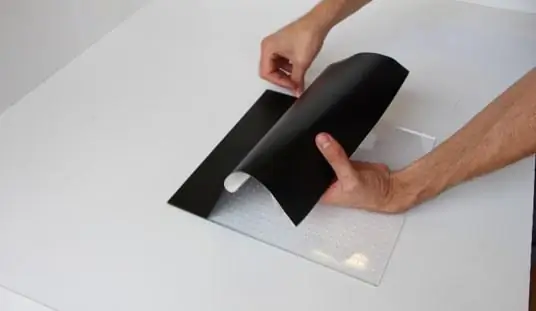
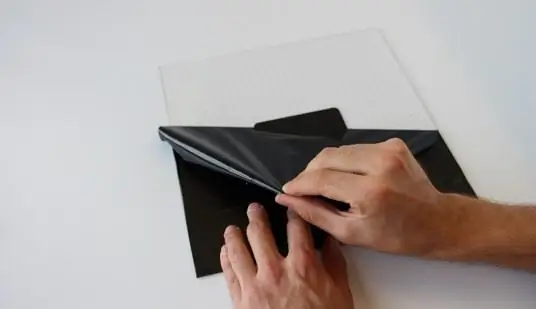
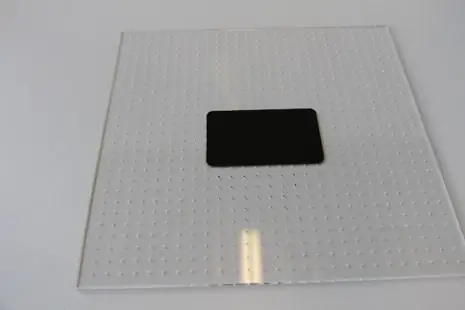
Pour garantir un alignement correct pendant toutes les étapes postérieures à l'étape 7, nous demanderons à notre silicone de créer une liaison solide avec la plaque de transfert à des emplacements en dehors du contour de notre circuit souple. Cette forte adhérence est obtenue en pré-traitant la plaque de transfert avec Bison Silicone Primer. À la fin du processus de construction, vous souhaiterez facilement séparer votre circuit logiciel de la plaque de construction et ainsi ne pas l'avoir collé. Nous devons donc garder la zone occupée par notre circuit souple exempte de matériau d'apprêt. Pour ce faire, nous recouvrons cette zone lors de la pulvérisation de l'apprêt avec un autocollant découpé sur mesure. Ce masque est obtenu en collant un autocollant (de manière normale, côté collant vers le bas) sur toute la surface de la plaque de transfert et en découpant ensuite au laser le contour du circuit + la forme de marge de 5 mm de l'autocollant. L'excès de matériau d'autocollant est retiré.
Gardez à l'esprit:
• Découper l'autocollant à la taille (dimensions de la plaque approximatives)
• Appliquer l'autocollant sans introduire de bulles d'air
• La conception doit être en miroir (la plaque sera placée face vers le bas)
• Couper le masque d'apprêt (contours du tableau + marge de 5 mm) avec un cutter laser (8-9 W)
• Retirez sélectivement l'autocollant pour exposer le plexi sous-jacent. Laissez les parties autocollantes qui couvrent la zone du circuit imprimé.
Étape 4: Placement des composants
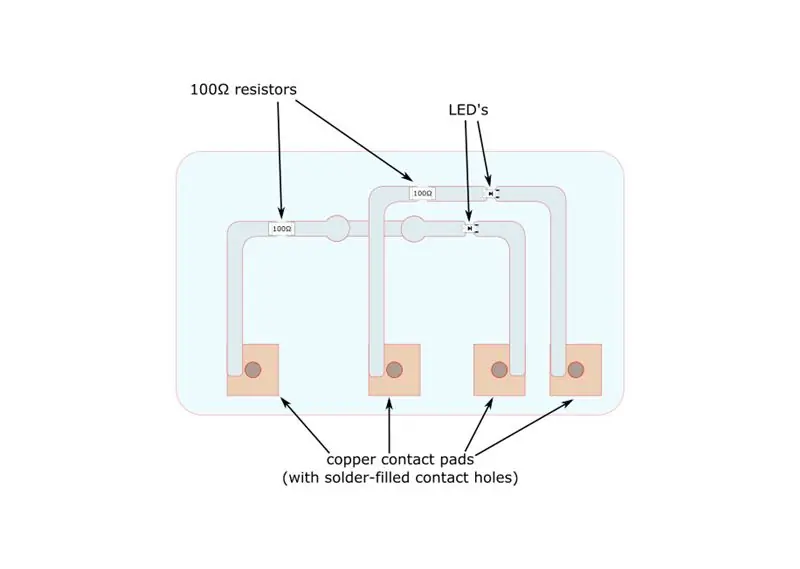
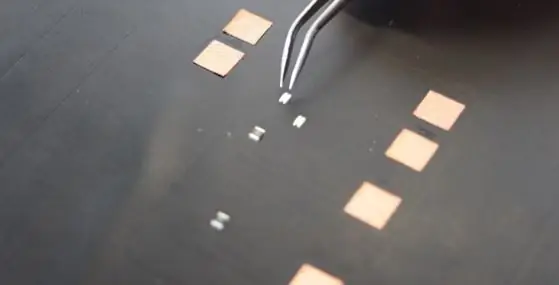
Une caractéristique quelque peu contre-intuitive consiste à commencer par les composants avant les traces conductrices. Placez les deux résistances et LED comme indiqué dans l'image fournie ici.
Pourquoi plaçons-nous les composants en premier ? Nous avons besoin que nos composants soient bien réticulés avec le silicone qui les entoure. Sur le dessus et les côtés, c'est facile à réaliser. Sur la face inférieure, cependant, nous voulons lier notre silicone au composant partout sauf sur les points qui seront en contact avec des traces conductrices. Une façon d'y parvenir est, par conséquent, a) d'intégrer et de lier la face supérieure des composants dans une feuille de silicone, b) de retourner la pile pour exposer les plots de contact de chaque composant, c) d'appliquer des traces conductrices et seulement ensuite d) de lier la surface inférieure du composant exposé restant à une seconde couche de silicone de coulée. Ces étapes a) b) c) et d) sont discutées plus loin dans l'Ible.
Directives générales pour cette étape:
•Placez les composants selon la conception du circuit sur la plaque de départ. Poussez fermement le composant à travers la couche anti-adhésive pulvérisée dans la couche adhésive de l'autocollant. De cette façon, il reste en place.
• Les composants doivent être SMD. De préférence taille 2010 ou plus. L'espacement sur les broches voisines d'un circuit intégré ne peut pas être inférieur à 0,8 mm. Les packages TQFN sont la limite inférieure.
• Chaque composant placé doit avoir ses plots de contact dans le plan avec la couche adhésive de l'autocollant
Étape 5: Application d'apprêt
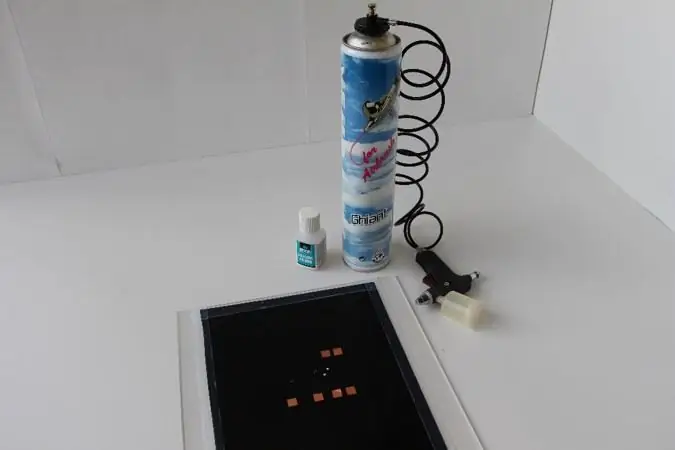
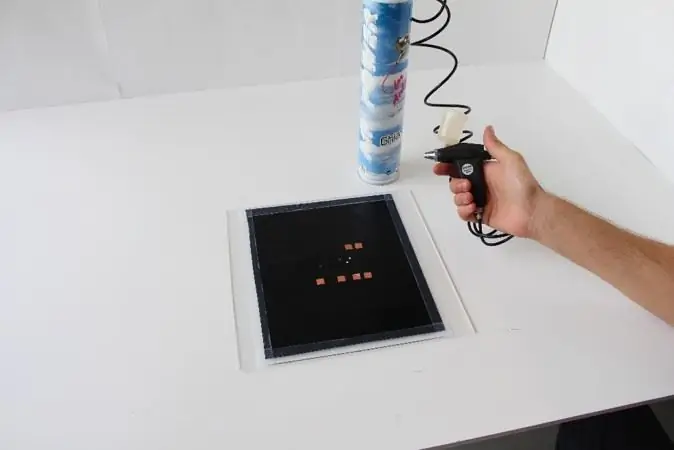
L'application du primaire est une étape cruciale à ne pas négliger. Sans une bonne adhérence entre le composant et le silicone environnant, la contrainte créerait un ajustement lâche du silicone autour de chaque composant. Cet ajustement lâche permettrait alors au métal liquide de s'écouler à travers les plots de contact et donc d'introduire des shorts. Une fine couche uniforme de Bison Silicone Primer doit recouvrir complètement toutes les parties exposées du composant à plat sur l'autocollant.
Pour votre considération:
• Utilisez l'apprêt silicone Bison et l'aérographe (Sealey Tools AB931)
• Pulvériser les composants sur la plaque de départ avec une fine couche sous tous les angles
• Laissez sécher et passez immédiatement à l'étape 6 pour une réticulation optimale
Étape 6: Moulage/lame enduite de silicone
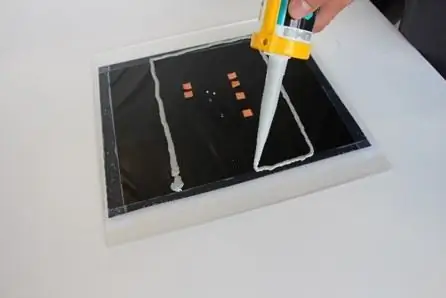
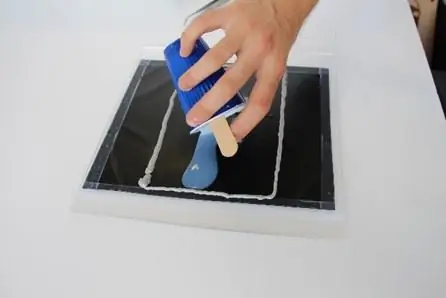
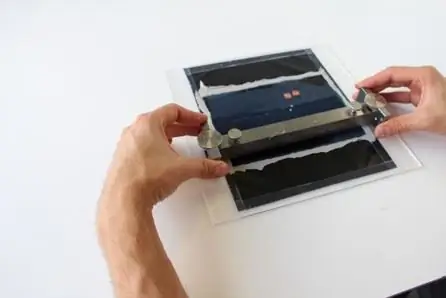
Prochaine étape: couler du silicone autour et sur nos composants ! L'épaisseur de cette couche doit être d'environ 300 microns de plus que l'épaisseur de votre composant le plus épais. Pour les composants indiqués au début de cet Ible, cela signifie 1 mm. Pour atteindre cette épaisseur requise, nous utiliserons une barre d'inondation que nous balayons sur la surface exactement à cette hauteur. (Pour les esprits curieux: le terme de jargon pour cela est le revêtement de la lame).
Le silicone coulé seul n'est pas visqueux. Je ne garderais pas la forme après lui avoir donné une certaine hauteur. Par conséquent, une sorte de « piscine » de mastic acrylique plus visqueux (mastic silicone) est appliquée. Nous ne voulons pas étaler ce mastic dans notre échantillon: c'est pourquoi nous appliquerons deux revêtements et du milieu vers l'extérieur.
Liste à puces:
• Placez le kit de mastic acrylique autour du périmètre de la feuille de silicone requis
• Mélanger 2 composants de silicone de poly-addition de platine dureté Shore 15
• Verser dans le mastic « piscine », en commençant par le milieu et sur tous les composants
• lame enduite d'une couche de silicone d'une hauteur de 300 um > composant le plus haut
• Attendez que le silicone durcisse
Étape 7: Collez la plaque de transfert
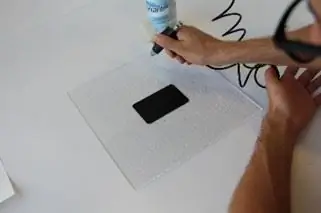
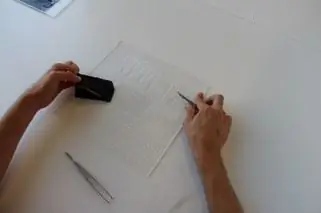
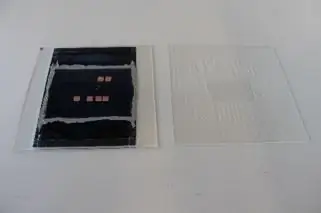
Hé, vous faites un excellent travail jusqu'à présent ! Normalement, à ce stade, une feuille de silicone remplie de composants vous sourit. Les composants doivent être entièrement recouverts de silicone et avoir leurs contacts inférieurs à plat sur la plaque de support en verre plexi avec un autocollant en vinyle entre les deux. Retournons maintenant cette pile et exposons ces contacts !
*insérer l'avertissement de désalignement ici*
Ce que nous avons à ce stade est une feuille de composants qui sont placés exactement (vous avez fait un travail précis, n'est-ce pas ?) selon un design numérique aligné sur le coin supérieur gauche de votre plaque de support. Nous devons maintenant placer une deuxième plaque sur le dessus, y adhérer la dalle de silicone, retourner la pile et retirer la première plaque de support - le tout sans perdre cet alignement des coins ! Vous verrez que c'est plus facile qu'il n'y paraît. Assurez-vous d'avoir un bon étau ou un coin droit autour duquel vous pouvez pousser les plaques en alignement.
Nous devons d'abord vaporiser notre deuxième plaque support (celle avec les trous d'aération) sur laquelle vous avez déjà placé un autocollant en vinyle et découpé en forme pour former un masque d'apprêt. Pulvériser de manière uniforme et continue. Ensuite, retirez l'autocollant du masque d'apprêt.
Prenez maintenant votre plaque avec la dalle remplie de composants. Alignez son coin supérieur gauche dans votre étau ou coin droit. Ensuite, mélangez un peu plus de silicone (environ 50 ml feront l'affaire). Versez-le sur la plaque de silicone et étalez-le en une couche plus ou moins égale. Ensuite, prenez la deuxième plaque de support (avec des trous d'aération) que nous venons d'amorcer. Son coin droit a été marqué quelques pas en arrière. Placez-le sur le dessus de la première plaque, côté pulvérisé vers le bas et avec le coin marqué également vers le bas en alignement avec le marquage en haut à gauche sur la plaque de départ. Appuyez vers le bas, faites sortir les bulles d'air et continuez à aligner les plaques entre les deux. Presser plus de silicone à travers les trous permet d'obtenir moins de bulles d'air et une meilleure adhérence. Par coïncidence, cependant, cela signifie également plus de difficultés pour vous lorsque vous déplacez les plaques plus loin dans l'alignement. Alors alignez d'abord, puis commencez à évacuer l'air.
Enfin, attendez que le silicone durcisse.
Un aperçu de la liste restreinte:
•Pulvériser la plaque de transfert avec l'apprêt. Retirer le masque d'apprêt
• Mélanger 2 composants de silicone de poly-addition de platine de dureté Shore 15
•Appliquer une couche uniforme sur le composant maintenant durci contenant une feuille de silicone, env. 1 mm d'épaisseur
• Plaque de transfert, côté apprêté vers le bas
• Aligner avec la plaque de départ
• Appliquer une pression, faire sortir l'air
• Double vérification de l'alignement
• Attendez que le silicone durcisse
Étape 8: Retirez la plaque de départ
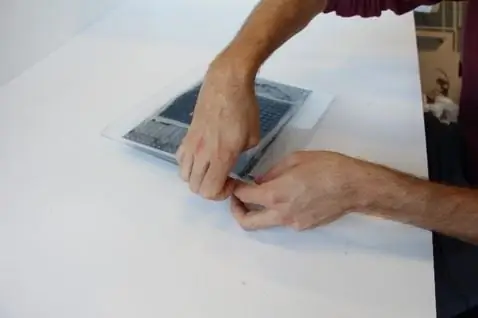
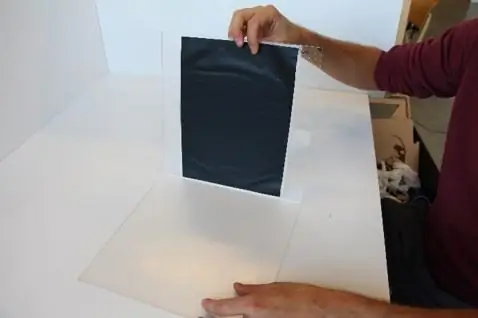
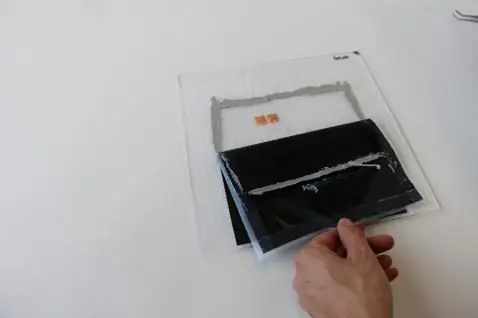
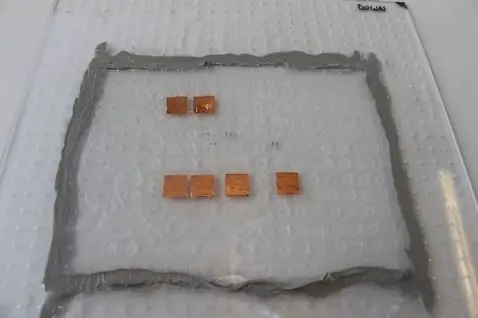
La partie cruciale est terminée. Travaillons maintenant jusqu'au moment où nous pouvons vérifier vos compétences en alignement !
Prenez votre sandwich plexi-silicone-sticker-plexi, utilisez un couteau tranchant pour desserrer le scotch sur les bords de votre vinyle autocollant. La plaque de départ en verre plexi devrait se détacher facilement maintenant. Si ce n'est pas le cas, utilisez un objet plat entre l'autocollant et votre plaque ou entre les deux plaques pour desserrer la pile. Veillez à ne pas déchirer votre pile de silicone de la deuxième plaque (avec des trous) car cela introduirait des désalignements.
Si les composants ont été placés correctement - conformément à l'autocollant - et que le processus de silicone a été effectué avec suffisamment de soin pour ne pas déchirer les composants; vous devriez maintenant avoir vos composants avec leurs dos bien exposés !
Utilisez un multimètre pour mesurer la valeur de chaque composant. (les résistances mesurent les ohms, les LED utilisent le réglage de la diode pour les allumer). De cette façon, vous pouvez vérifier électriquement si aucun film mince d'adhésif autocollant ou de silicone coulé ne recouvre les plots de contact - à peine visible à l'œil nu.
En bref:
• Desserrez l'autocollant sur un côté du sandwich plexi-silicone + autocollant-plexi
• Décollez la plaque de départ et l'autocollant des composants intégrés en silicone
• Vérifiez les composants pour une exposition non obstruée des tampons conducteurs
• Étant donné que nous avons inversé la pile, toutes les étapes ultérieures doivent être effectuées avec des calques de conception mis en miroir (tous les fichiers de ce didacticiel ont déjà été préparés en conséquence, aucune autre adaptation n'est nécessaire)
Étape 9: Masque de pochoir pour la couche conductrice supérieure
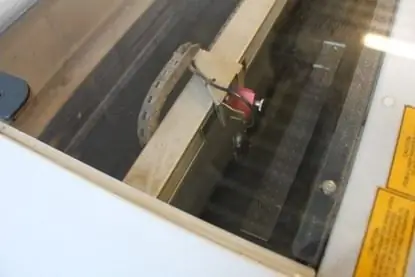
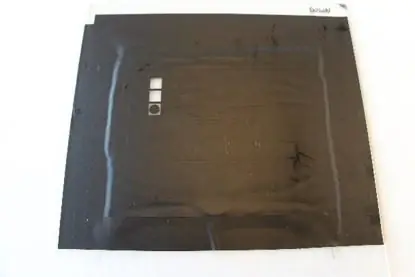
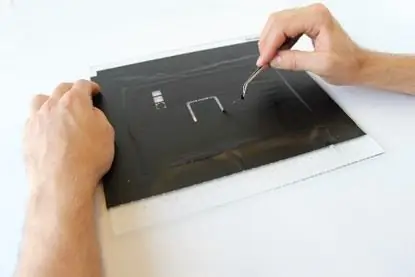
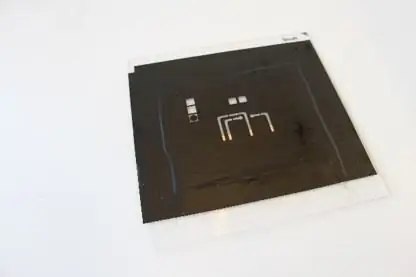
Votre moment de vérité ! Vérifions à quel point vous avez réussi aux étapes précédentes.
Appliquez un nouvel autocollant pour recouvrir complètement votre dalle de silicone avec les contacts des composants exposés. Placez la plaque dans votre découpeuse laser pendant que son marquage est visible dans le coin supérieur droit et découpez la première couche de circuit à travers l'autocollant.
Si le pochoir que nous avons coupé ensuite s'aligne bien avec vos composants, vous avez bien fait toutes les étapes précédentes. Si c'est le cas.. Bon sang. Les problèmes sont très probablement liés au fait que votre autocollant ne repose pas à plat lors de l'application de silicone et/ou à un désalignement important de la deuxième plaque de support par rapport à la première plaque de support de 2 pas en arrière. Mesurez combien de mm vous avez perdu et vous pouvez corriger cela en plaçant la conception dans le logiciel de découpe laser.
Un résumé, pour votre commodité:
• Découper l'autocollant à la taille (dimensions de la plaque approximatives)
• Appliquer l'autocollant sans introduire de bulles d'air
• Calibrer le laser pour couper avec précision l'autocollant (8-9W)
• Couper les traces de circuit en cuivre supérieures avec un cutter laser
• Retirez l'autocollant dans les zones qui doivent être rendues conductrices (traces de circuit, pastilles)
Étape 10: Couche conductrice supérieure
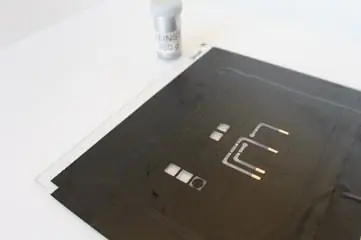
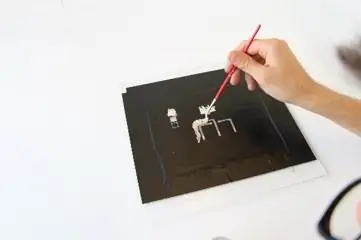
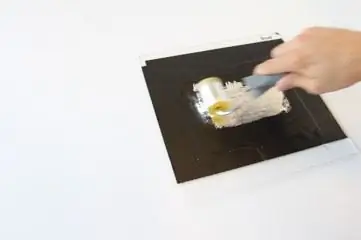
Nous allons travailler avec le métal liquide dans cette étape. Assurez-vous que votre espace de travail est entièrement recouvert (avec du papier journal par exemple). Lorsque vous renversez du métal liquide, il devient difficile de le nettoyer. Il n'y a pas de vrai solvant pour cela et il ne trempe pas dans les éponges ou les serviettes en papier. Le mieux est de travailler vraiment très proprement et juste après de jeter les journaux sur lesquels vous auriez pu renverser. Il est préférable de porter des gants ou de se laver les mains par la suite. Il y aura des frottis.
À ce stade, vous devriez avoir un pochoir correctement défini. Assurez-vous qu'il adhère bien au silicone sur les bords. Nous ne voulons pas que du métal liquide coule en dessous.
Prenez maintenant le métal liquide et un pinceau fin. Appliquez le métal liquide sur les ouvertures du pochoir en frottis courts (images pour référence). Cela devrait être plus une action de trempage que de maculage. Le métal liquide doit être forcé en contact étroit afin qu'il puisse bien adhérer. Une fois que vous avez recouvert le motif de votre pochoir, prenez le rouleau et faites rouler le surplus de métal liquide sur le côté. Cela peut être récupéré avec une petite pipette en plastique.
En bref:
• Assurez-vous que votre autocollant adhère bien autour des bords des zones exposées
• Nettoyer les tampons en silicone et composants exposés avec de l'alcool isopropylique
• Utilisez un pinceau pour couvrir grossièrement toutes les zones exposées avec Galinstan
• Utilisez le rouleau pour transformer le galinstan appliqué en un revêtement uniforme
• Récupérer l'excès de galinstan dans son conteneur
• Retirez soigneusement le pochoir autocollant
•Si lors du retrait le Galinstan coule vers des zones où il ne devrait pas être, votre revêtement était trop épais. Nettoyer la surface et recommencer à l'étape 9.
Étape 11: Bas à composants principaux
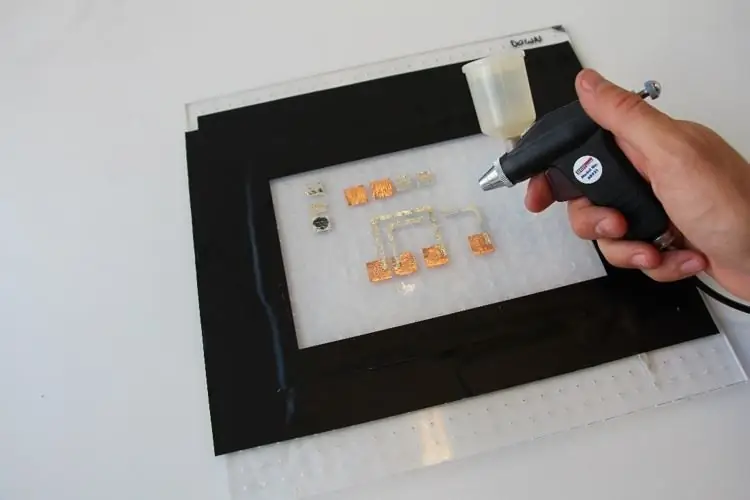
Cette étape est assez explicite. Vous avez déjà appliqué l'apprêt deux fois auparavant. Il suffit de le refaire. L'accent n'est pas mis sur la feuille de silicone mais sur les faces inférieures des composants et en particulier les pièces sur lesquelles aucun métal liquide n'est imprimé. Laissez l'apprêt sécher et immédiatement après, passez à l'étape 12.
• Utilisation de l'apprêt silicone Bison et de l'aérographe (Sealey Tools AB931)
• Vaporisez le fond des composants exposés avec une fine couche d'apprêt
•Laisser sécher et immédiatement après continuer avec l'étape 12
Étape 12: Enduit de silicone pour moulage/lame
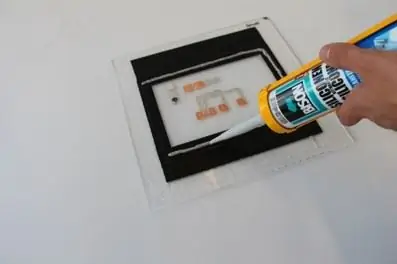
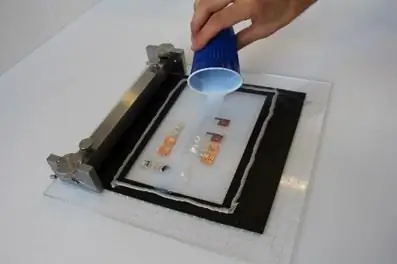
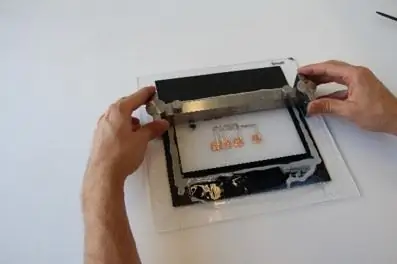
Celui-ci est également plus du même que vous l'avez fait auparavant. Le plus important ici est la hauteur sur laquelle vous enduisez la lame. La couche précédente (couche de composant) était de 1 mm (la led recommandée était de 0,7 mm d'épaisseur + 0,3 mm comme suggéré précédemment). Pour chaque couche de circuit, une hauteur de 0,5 mm de silicone est ajoutée sur le dessus afin de laisser une marge suffisante pour les revêtements inégaux avec du métal liquide. La hauteur sur laquelle vous enduisez ici la lame devient donc 1 mm + 0,5 mm = 1,5 mm.
Étapes détaillées en bref:
• Placez le kit de mastic acrylique autour du périmètre de la feuille de silicone requis
• Mélanger 2 composants de silicone de poly-addition de platine de dureté Shore 15
• Verser dans le mastic « piscine », en commençant par le milieu et sur tous les composants
• la lame recouvre une couche de silicone d'une hauteur de 0,5 mm > épaisseur actuelle de la pile
• Attendez que le silicone durcisse
Étape 13: Masque de pochoir pour la couche conductrice inférieure
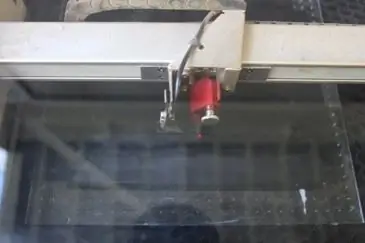
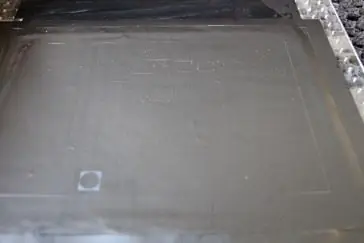
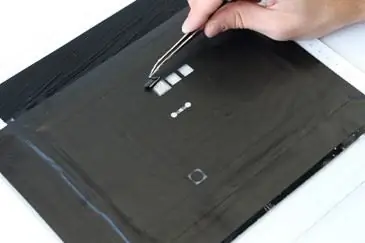
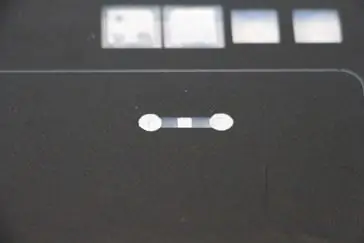
Et nous sommes maintenant pleinement entrés dans les parties faciles ! Ce que vous trouvez ici n'est que répétition. Chaque couche de circuit que vous appliquez par-dessus est une répétition des étapes effectuées pour les couches de circuit précédentes. Ici, vous devez créer un masque de pochoir pour la couche de circuit 2.
Sans trop de précisions:
• Découper l'autocollant à la taille (dimensions de la plaque approximatives)
• Appliquer l'autocollant sans introduire de bulles d'air
• Couper les traces de circuit en cuivre inférieures avec un cutter laser (W à étalonnage)
• Retirez l'autocollant dans les zones qui doivent être rendues conductrices (traces de circuit, pastilles)
• Assurez-vous que votre autocollant adhère bien autour des bords de la zone exposée
• Nettoyer le silicone exposé avec de l'alcool isopropylique
Étape 14: VIA de haut en bas
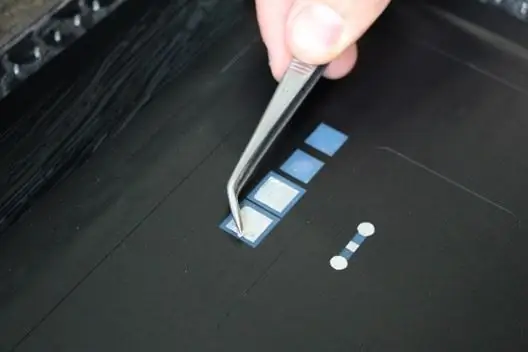
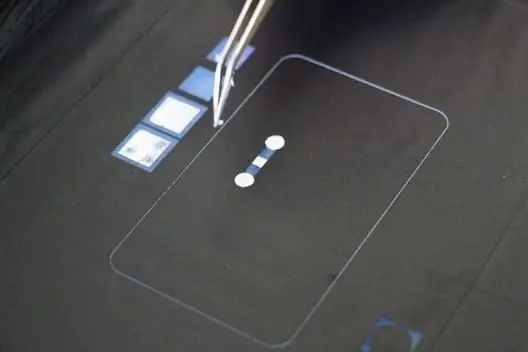
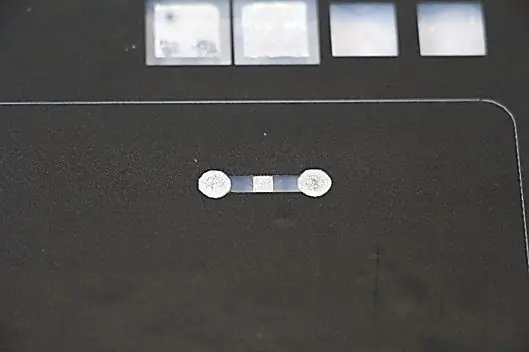
La seule nouveauté réside dans les endroits où nous avons besoin d'une connexion entre 2 couches de circuit successives. Dans le jargon, ceux-ci s'appellent Vertical Interconnect Access ou VIA en abrégé. Pour créer un via, vous devez découper une ouverture dans le silicone recouvrant une couche de circuit précédente. Lorsque vous imprimez ensuite un nouveau métal liquide sur le dessus pour la couche de circuit suivante, il s'écoulera dans cette ouverture et se connectera électriquement.
Vous devrez d'abord calibrer (voir: calibrage) le laser pour couper avec précision la couche de revêtement en silicone au-dessus de la couche de circuit précédente. Ensuite, il suffit de découper les VIA selon le fichier fourni ci-joint. Retirez chaque découpe de couche de revêtement en silicone avec une pince à épiler et passez à l'étape suivante: imprimer une nouvelle couche de circuit de métal liquide par-dessus !
Création de VIA, une version courte:
• Avec le masque de pochoir de couche conductrice inférieur prêt
• Calibrer le laser pour couper avec précision à travers la couche de silicone pour exposer la couche conductrice supérieure (12-17 W)
• Coupez les VIA dans tout le silicone là où les couches conductrices supérieure et inférieure doivent être interconnectées
• Retirez le silicone découpé pour exposer la couche conductrice supérieure
Étape 15: Couche conductrice inférieure
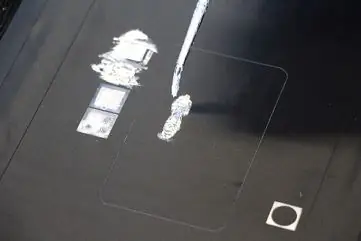
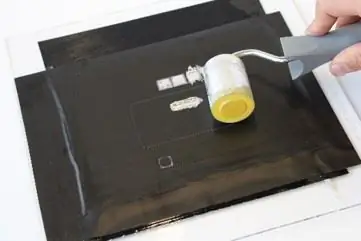
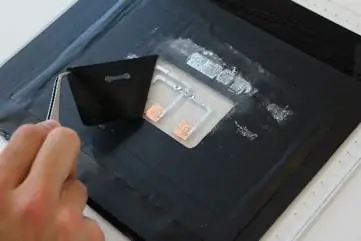
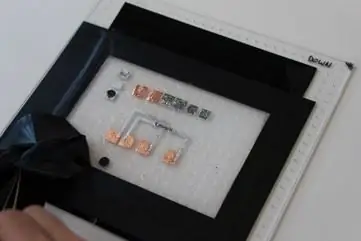
Encore une fois, assurez-vous que votre espace de travail est couvert lorsque vous travaillez avec du métal liquide. Cela facilitera grandement la gestion des déversements.
L'impression de cette couche est à nouveau une répétition des efforts précédents. Assurez-vous que le pochoir adhère bien au silicone sur les bords. Nous ne voulons pas que du métal liquide coule en dessous. Utilisez à nouveau l'action de trempage pour appliquer du métal liquide sur les ouvertures du pochoir avec un pinceau fin. Prenez le rouleau et roulez le surplus de métal liquide sur le côté. Récupérez de grosses gouttes de métal liquide avec une pipette en plastique.
Une autre version TL;DR:
• Utilisez un pinceau pour couvrir grossièrement toutes les zones exposées avec Galinstan
• Utilisez le rouleau pour transformer le galinstan appliqué en un revêtement uniforme
• Retirez soigneusement le pochoir autocollant
•Si lors du retrait le Galinstan coule vers des zones où il ne devrait pas être, votre revêtement était trop épais. Nettoyer la surface et recommencer à l'étape 13.
• Utilisez le pinceau pour retoucher chaque VIA et assurez-vous que les couches conductrices supérieure et inférieure se connectent
Étape 16: Enduit de silicone pour moulage/lame
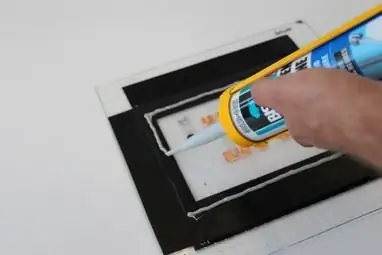
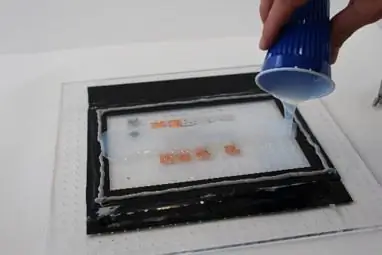
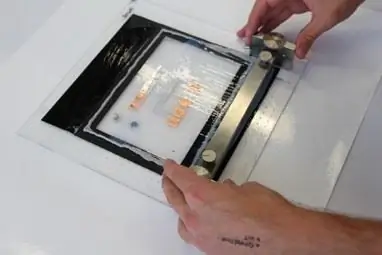
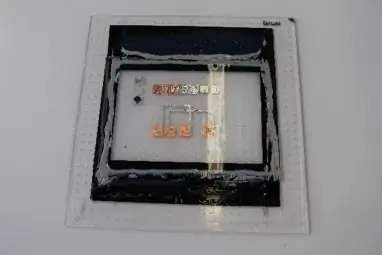
Vous pouvez commencer à vous enthousiasmer maintenant ! Il s'agit de notre dernière couche de silicone de coulée, ce qui signifie que votre circuit souple est presque terminé ! Cela, vous l'avez déjà fait deux fois auparavant. Je vais donc faire court et vous dire quelle hauteur vous devriez viser pour le revêtement de la lame. Nous avons déjà une couche de composant de 1 mm d'épaisseur et une première couche de circuit de 0,5 mm d'épaisseur. Cette couche de circuit doit également avoir une épaisseur de 0,5 mm. Par conséquent, enduisez la lame à 2 mm d'épaisseur totale dans cette étape !
Voie rapide:
• Placez le kit de mastic acrylique autour du périmètre de la feuille de silicone requis
• Mélanger 2 composants de silicone de poly-addition de platine de dureté Shore 15
• Verser dans le mastic « piscine », en commençant par le milieu et sur tous les composants
• lame enduite d'une couche de silicone d'une hauteur de 500 um > épaisseur actuelle de la pile
• Attendez que le silicone durcisse
Étape 17: Tampons de contact
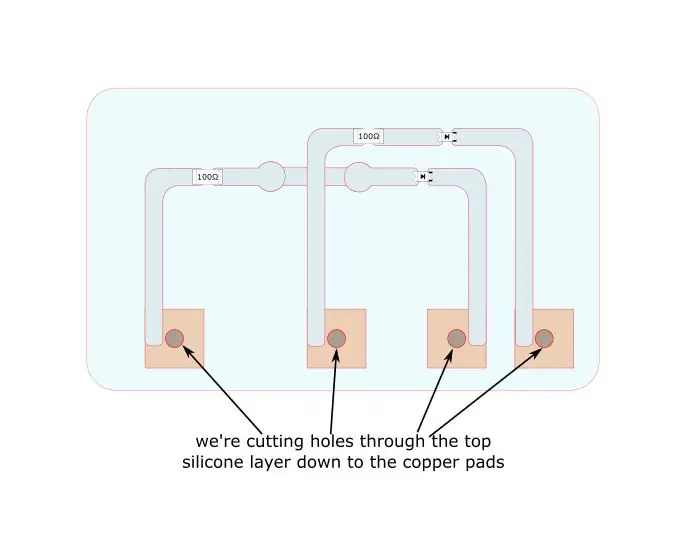
Alors que les dispositifs en silicone peuvent intégrer l'alimentation (batterie) et le traitement (microcontrôleur), pour la simplicité de cet exemple, nous ajoutons des connecteurs externes pour alimenter les LED. Dans cette étape, nous allons couper le silicone jusqu'aux contacts que nous avons intégrés à l'intérieur. Encore une fois, vous devrez calibrer le laser (voir: calibrage) afin de ne pas endommager les couches sous-jacentes. Lorsque vous avez fait les coupes, arrachez les découpes en silicone avec une pince à épiler. Ensuite, grattez les résidus de silicone en excès de vos contacts et nettoyez-les avec des cotons-tiges et appliquez de la soudure sur les contacts pour plus de fiabilité.
Plaquettes de contact, une petite histoire:
• Calibrer le laser pour couper à travers la couche de silicone et exposer les contacts du ruban de cuivre (20-30 W)
• Couper les contacts de circuit avec un coupeur laser
• Enlevez le silicone dans les zones découpées
• Nettoyez les tampons de cuivre exposés avec un solvant à séchage rapide
•Appliquez de la soudure sur les pastilles exposées jusqu'à ce que les contacts soient au niveau du silicone. Continuez à ressouder tout en grattant l'excès de silicone de vos contacts et en nettoyant la saleté jusqu'à ce que votre soudure adhère au tampon.
Étape 18: Échantillon coupé gratuitement
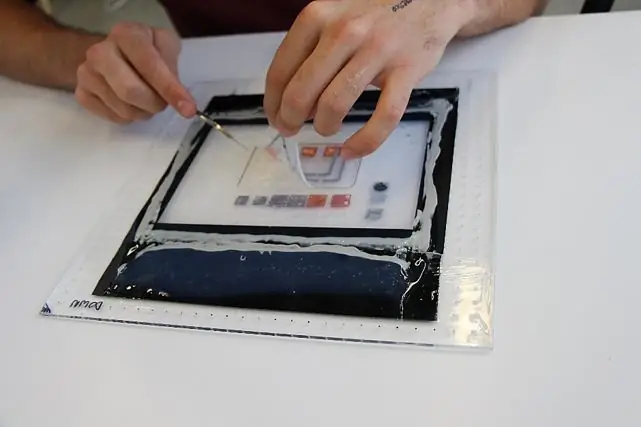
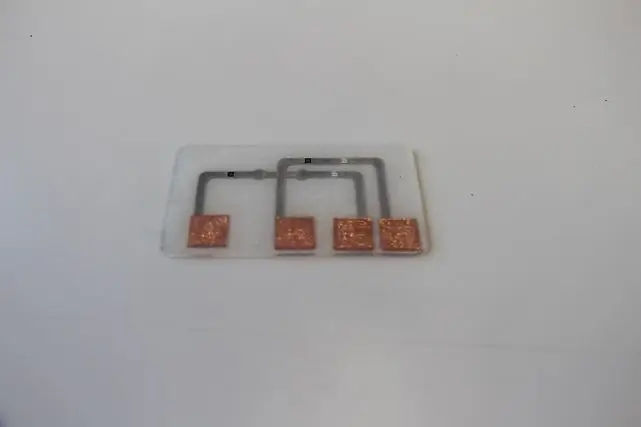
Il est temps de libérer votre circuit mou de sa plaque support ! Étant donné que notre plaque de transfert n'a pas été recouverte d'un apprêt sous notre circuit souple, tout ce que nous avons à faire est de couper les côtés et nous pouvons l'enlever. Utilisez le fichier de coupe ci-joint pour couper l'échantillon. Continuez à répéter les coupes avec une puissance croissante jusqu'à ce que l'échantillon se libère. Le décalage Z de votre laser doit être de -1 (la moitié de la hauteur de la pile). Lorsque la découpe de l'échantillon est complètement réalisée, soulevez un coin d'un côté, puis coupez votre circuit souple libre de toutes les pièces jointes en dessous qui ont été formées dans les trous d'aération de la plaque de support. Regardez-le bien: votre premier appareil en silicone ! Un circuit conformable, extensible et doux !
Échantillon coupé gratuitement en puces:
• Calibrer le laser pour couper à travers la pile complète de silicone (40-60W)
• Couper le contour de l'échantillon avec un cutter laser
• Soulevez l'échantillon de la plaque tout en le coupant manuellement sans les attaches en silicone qui se sont formées dans les trous d'aération de la plaque de transfert
Étape 19: Admirez
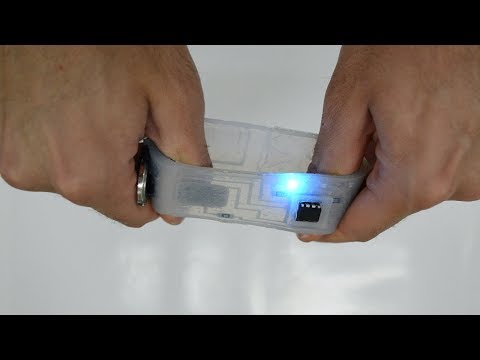
Branchez maintenant votre appareil en silicone à une alimentation 5V. Chaque chemin de connecteur-résistance-led-connecteur a un besoin séparé de puissance. Vous pouvez connecter les deux en parallèle. Gardez simplement un œil sur la polarité de votre led et adaptez vos connexions électriques en conséquence. Une fois votre circuit logiciel alimenté, la led bleue devrait s'allumer.
Donnez du peps à votre circuit ! Si vous l'avez bien fait, vous devriez facilement atteindre 50 % de déformation sans endommager le circuit. Le principal point de défaillance sera vos plaquettes de contact car elles sont constituées de feuilles rigides qui se déchirent avec des contraintes élevées.
Les adjectifs suivants correspondent à votre appareil en silicone:
•Souple
• Doux/extensible
• Auto-guérison
•Translucide
• Entièrement encapsulé
Domaines d'application que je prévois: patchs de biosurveillance (sur la peau), wearables, dispositifs en silicone intégrés dans les textiles, circuits électroniques qui couvrent des articulations mécaniques, électronique de pilotage ou de détection pour les robots mous, …
Quelles applications semblez-vous adaptées à ces types uniques de circuits souples ? Faites-le moi savoir dans les commentaires! J'ai hâte de voir ce que vous proposez. Faites-moi savoir si vous construisez quelque chose d'unique. Qui sait, je pourrais peut-être vous donner quelques conseils !
Bonne chance pour l'expérimentation, À votre santé, Noagel
Conseillé:
Restaurer Game Boy ou appareils électroniques similaires : 7 étapes (avec photos)
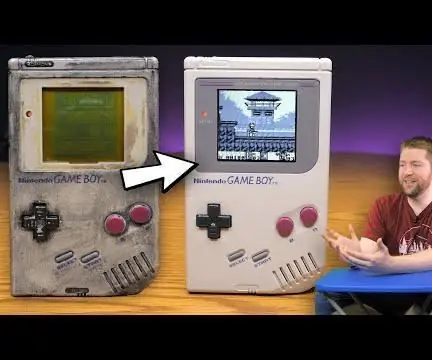
Restaurer Game Boy ou appareils électroniques similaires : Tout d'abord, merci d'avoir consulté mon tutoriel ! Vous êtes génial. Deuxièmement, j'ai consacré beaucoup de temps à la vidéo YouTube, alors regardez-la aussi, elle explique tout. Vidéo:
Interrupteur Tuchless pour appareils électroménagers -- Contrôlez vos appareils ménagers sans interrupteur : 4 étapes
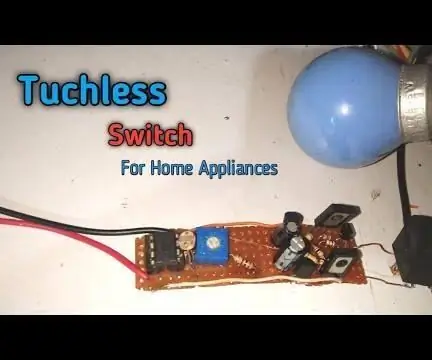
Interrupteur Tuchless pour appareils électroménagers || Contrôlez vos appareils ménagers sans Tuch aucun interrupteur : il s'agit d'un interrupteur Tuchless pour les appareils ménagers. Vous pouvez l'utiliser dans n'importe quel lieu public afin de lutter contre tout virus. Le circuit basé sur le circuit de capteur sombre fabriqué par un ampli-op et un LDR. Deuxième partie importante de ce circuit SR Flip-Flop avec séquence
Comment contrôler les appareils ménagers avec la télécommande du téléviseur avec fonction de minuterie : 7 étapes (avec images)
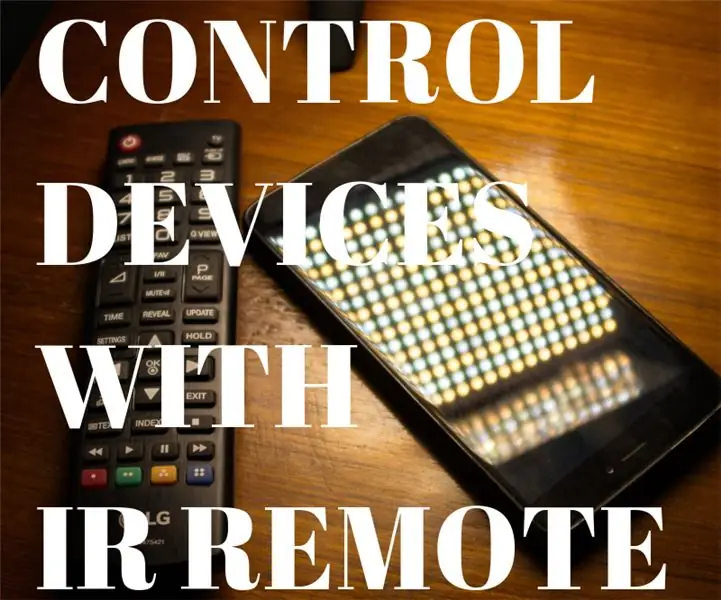
Comment contrôler les appareils ménagers avec la télécommande du téléviseur avec fonction de minuterie : Même après 25 ans de son introduction sur le marché grand public, la communication infrarouge est toujours très pertinente ces derniers jours. Qu'il s'agisse de votre téléviseur 4K 55 pouces ou de votre système audio de voiture, tout a besoin d'une télécommande IR pour répondre à nos
Comment faire un polyèdre en silicone ? : 4 étapes (avec photos)
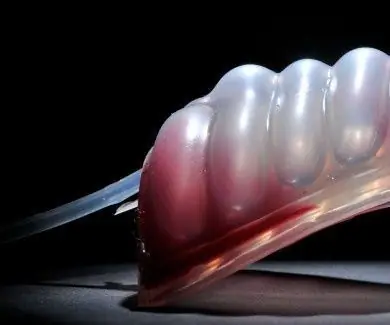
Comment faire un polyèdre en silicone ? : En tant que matériau souple à fort potentiel, le silicone est toujours utilisé pour explorer la plasticité des matériaux et l'espace qu'il crée. Ici, je voudrais partager mon expérience de fabrication d'un dodécaèdre en silicone. La partie la plus importante de ce travail est la
Contrôlez les appareils ménagers depuis votre smartphone avec l'application Blynk et Raspberry Pi : 5 étapes (avec photos)
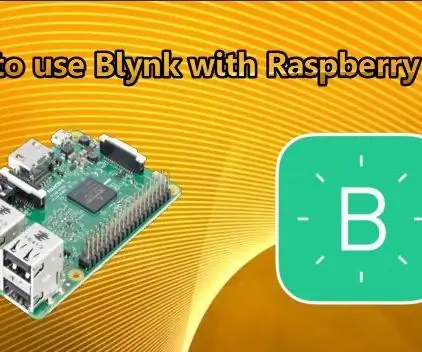
Contrôlez les appareils ménagers depuis votre smartphone avec l'application Blynk et Raspberry Pi : Dans ce projet, nous allons apprendre à utiliser l'application Blynk et Raspberry Pi 3 afin de contrôler les appareils ménagers (cafetière, lampe, rideau de fenêtre et plus encore… ). Composants matériels : Raspberry Pi 3 Relay Lamp Breadboard Wires Applications logicielles : Blynk A