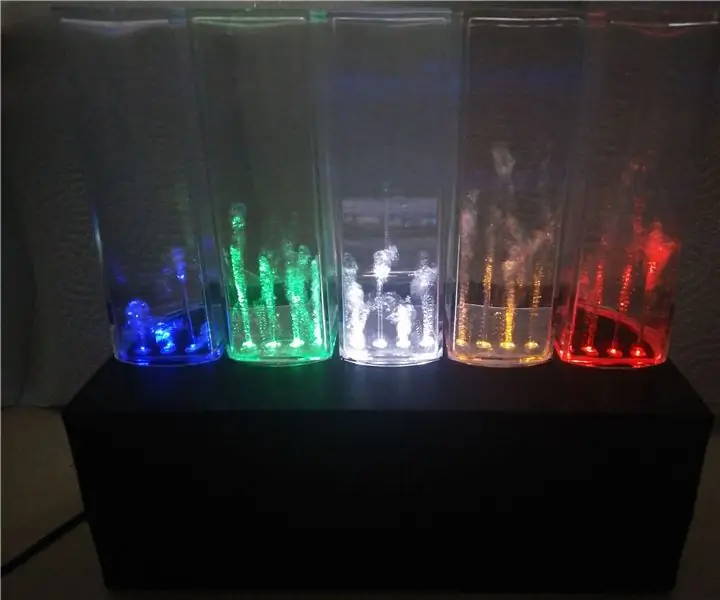
Table des matières:
- Étape 1: Pièces
- Étape 2: Démonter l'adaptateur Bluetooth
- Étape 3: Configuration de l'IC sur Perfboard
- Étape 4: Ajout de Mosfets
- Étape 5: Placement des diodes et des résistances 5W
- Étape 6: Ajout de Panel Jack et Bluetooth et de potentiomètres
- Étape 7: Préparation des haut-parleurs à eau
- Étape 8: Ajout des fils Arduino
- Étape 9: Les résistances du moteur et les potentiomètres
- Étape 10: Impression 3D
- Étape 11: Assemblage
- Étape 12: Le code
- Étape 13: Le produit final
2025 Auteur: John Day | [email protected]. Dernière modifié: 2025-01-23 14:46
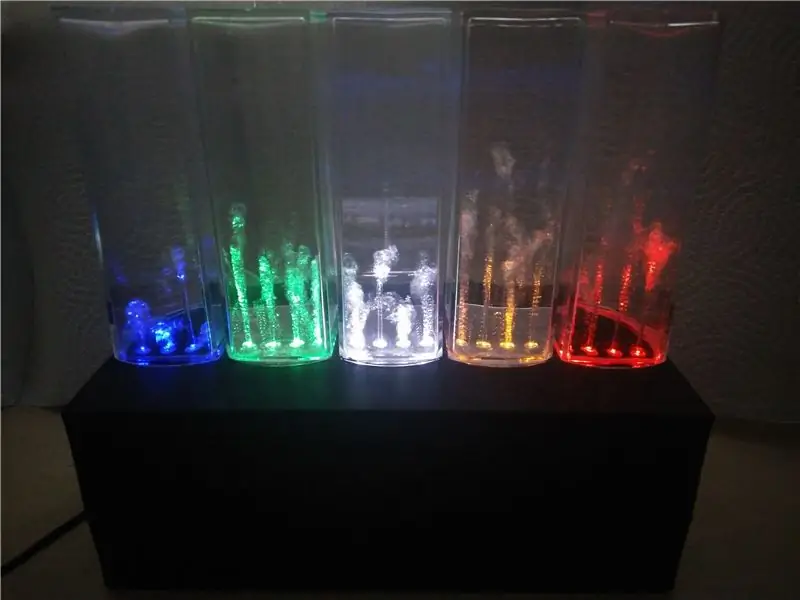
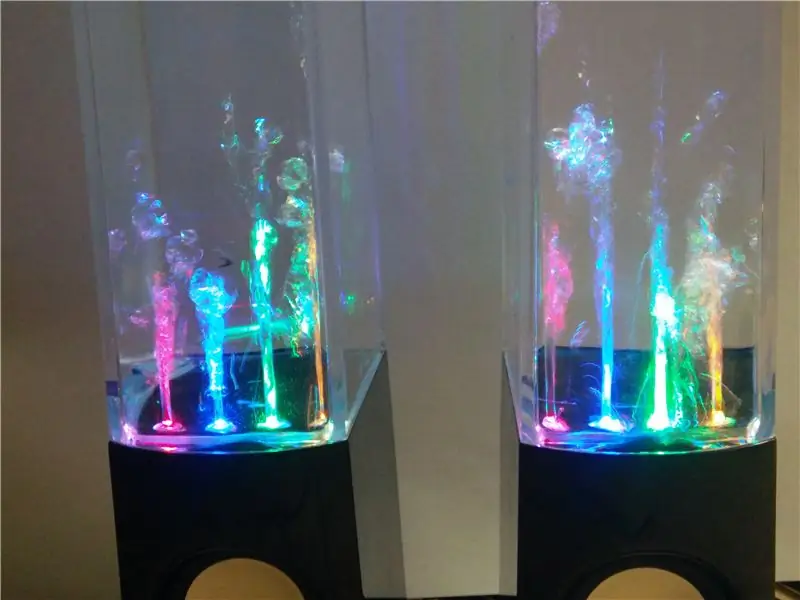
Dans mon premier Instructable, je vais passer en revue les étapes nécessaires pour créer des haut-parleurs d'eau qui agissent comme un égaliseur.
Les haut-parleurs à eau du magasin sont formidables à regarder, mais j'ai senti qu'ils pouvaient faire plus. il y a tant d'années, j'avais modifié un ensemble pour montrer la fréquence de lecture de la musique. A l'époque j'utilisais le Color Organ Triple Deluxe II, associé à un ensemble de potentiomètres photocellules et transistors j'ai pu obtenir un ensemble de 3 enceintes pour fonctionner.
Il y a quelques années, j'avais entendu parler de l'IC MSGEQ7 qui a la capacité de séparer l'audio en 7 valeurs de données pour un arduino à lire. J'utilise un arduino mega 2560 dans ce projet car il possède le nombre requis de broches PWM pour piloter cinq châteaux d'eau.
Ce projet utilise des compétences de soudure sur une carte de perfboard, un module Bluetooth, un arduino et des haut-parleurs d'eau standard. Tout au long du projet, j'ai remarqué certaines choses que j'aurais dû faire différemment, je ne manquerai donc pas de les souligner.
Commençons
Étape 1: Pièces
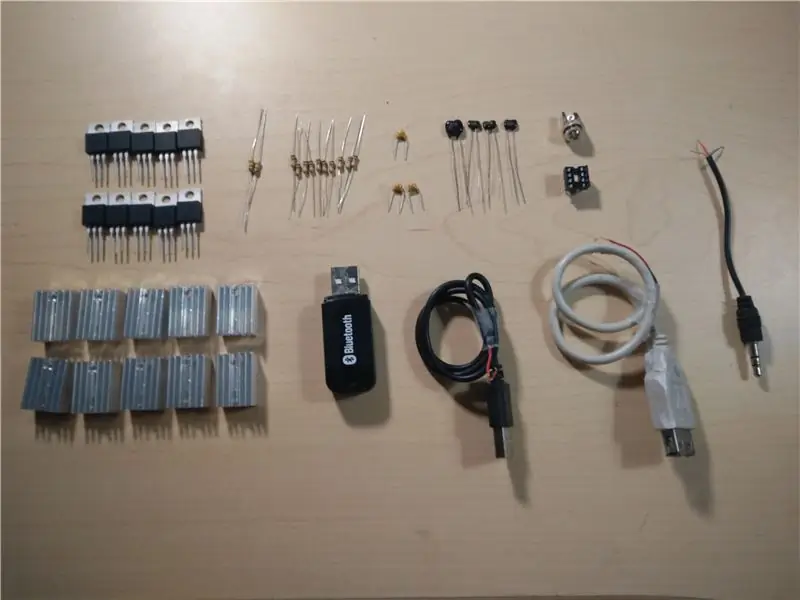
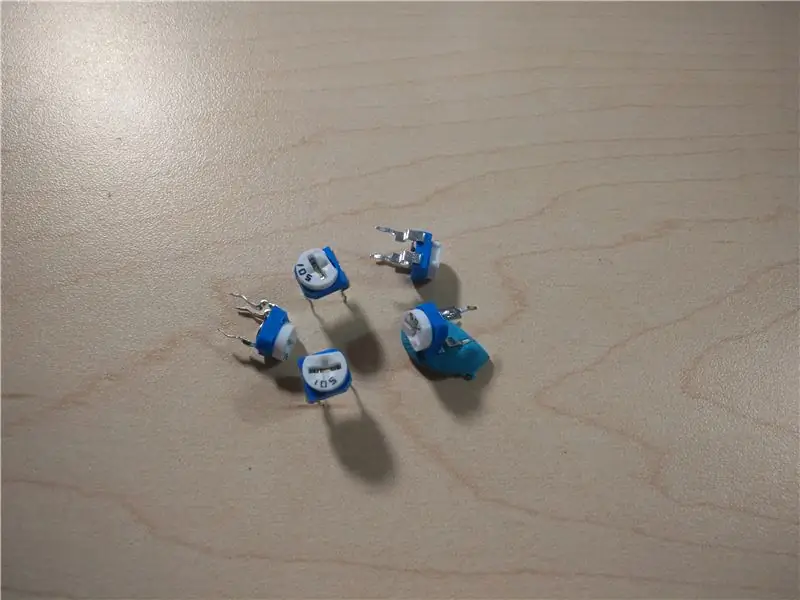
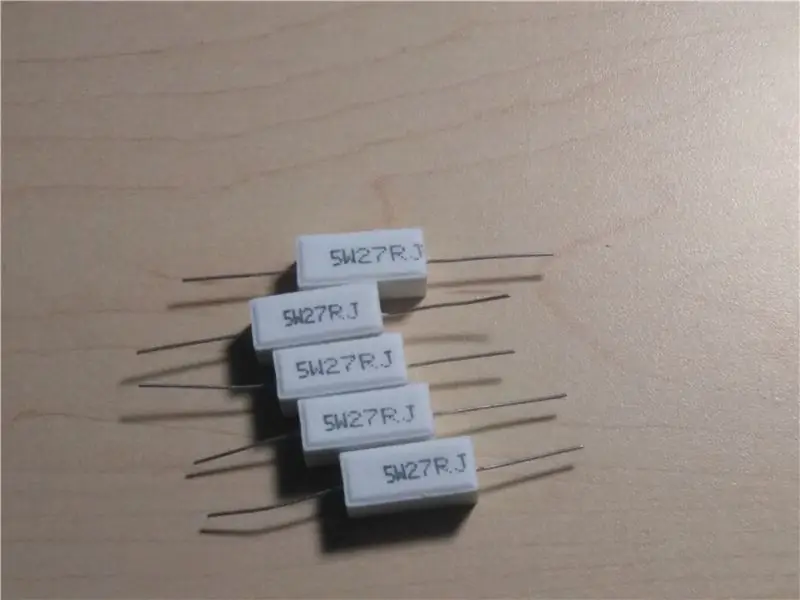
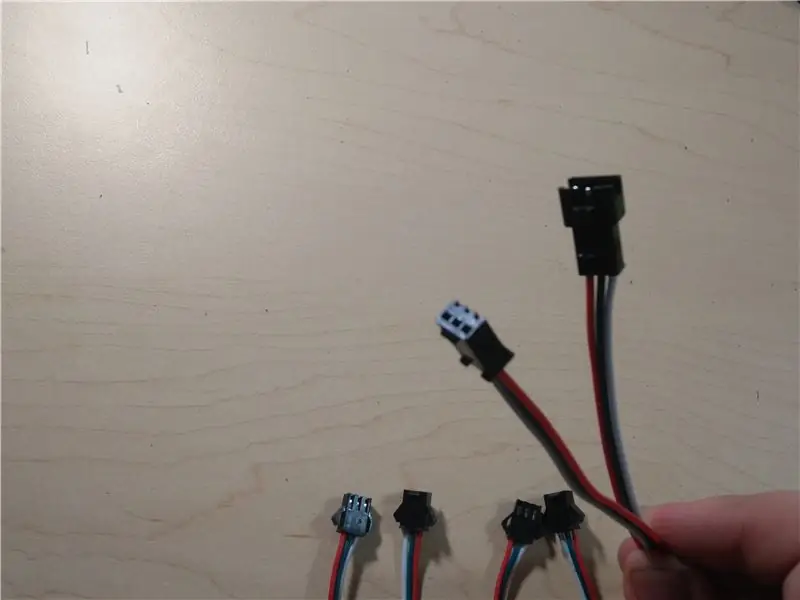
Il y a pas mal de pièces utilisées dans ce projet. De nombreuses pièces que j'avais autour du bureau, d'autres pièces ont été achetées dans un magasin de pièces local.
Tu auras besoin de:
REMARQUE: quantité de pièces entre parenthèses
(1) Arduino Mega 2560
(1) module Bluetooth USB
(1) prise DIP 8 broches
(1) MSGEQ7 - Je recommande de l'acheter chez Sparkfun Electronics car ebay regorge de fausses versions de ce circuit intégré
(1) Prise jack pour casque
(1) Câble pour casque avec extrémité femelle
(1) USB femelle standard avec une longueur de câble décente
(5) connecteur 3 fils (paires) généralement vendu comme connecteur 3 fils pour bandes LED ws2812b (voir image)
(10) FQP30N06L mosfet à canal N
(5) diode de blocage standard 1N4001
(4) DEL rouge de 3 mm
(4) LED jaune 3 mm
(4) DEL blanches de 3 mm
(4) LED verte de 3 mm
(4) DEL bleue de 3 mm
(10) 10k résistances 1/4 watt
(8) 100 résistances OHM
(8) résistances de 150 ohms
(5) 500 potentiomètres OHM
(5) potentimètres 2k OHM
(5) 27 résistances OHM 5 watts
(2) 100k résistances OHM
(2) condensateurs 100nF
(1) Condensateur 33pF - Doit être cette valeur; J'ai mis plusieurs condensateurs en parallèle pour atteindre cette valeur
(1) condensateur 10nF
(1) Interrupteur à bascule On - ON (le trou de montage était de 3 mm, généralement répertorié comme un mini interrupteur à bascule sur ebay)
(4) boulons 1/8 "x 1 1/2" (les miens étaient étiquetés comme des boulons de poêle de Home Depot, le fichier 3d est configuré pour cette taille d'écrou et de boulon)
(2) environ 12 de longueur de câble Ethernet
Les pièces imprimées en 3D, si vous ne possédez pas d'imprimante, les sites Web comme 3dhubs.com sont une excellente ressource.
Colle chaude
Soudure + Fer à souder
Broches d'en-tête mâles
Étape 2: Démonter l'adaptateur Bluetooth

A l'origine j'allais utiliser un câble USB mâle, mais la prise était cassée dessus, j'ai alors décidé de démonter l'adaptateur et de retirer le port USB. À l'aide d'un multimètre, j'ai pu trouver le sol en testant les broches de la coque extérieure du port USB. (ils sont connectés)
REMARQUE: en fait, j'ai dû changer cet adaptateur à mi-chemin du projet car il provoquait un bruit à haute fréquence sur le port audio, le nouveau n'est pas non plus à 100% meilleur. mais j'ai un récepteur différent qui fonctionne, il a cependant sa propre batterie et son interrupteur marche/arrêt, ce qui rend les haut-parleurs à eau moins plug and play. alors que ces récepteurs sont bon marché, payer plus ne signifie pas toujours que vous obtenez une haute qualité.
Étape 3: Configuration de l'IC sur Perfboard

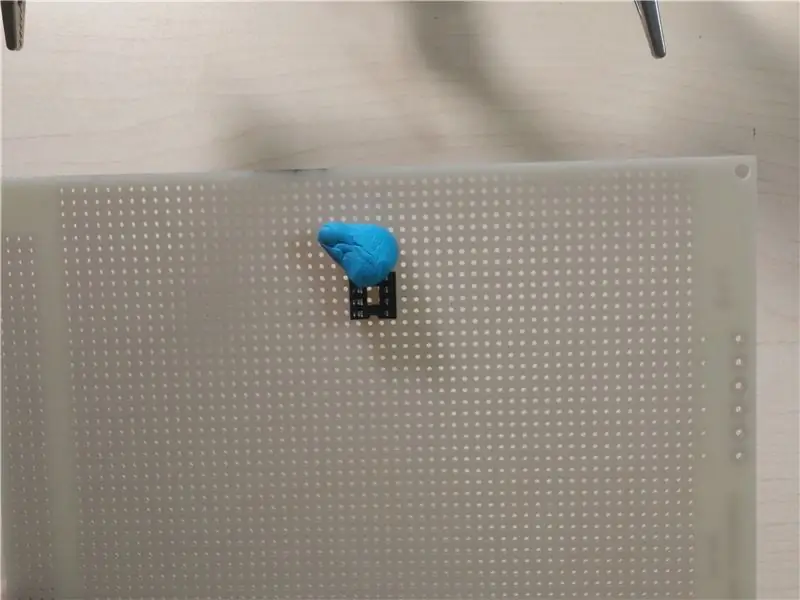
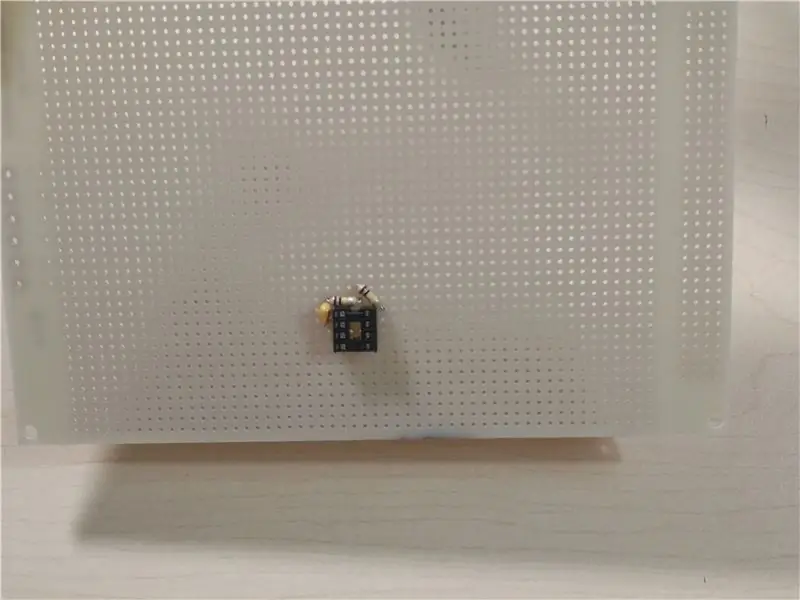
Dans cette étape, nous allons commencer la soudure perfboard de la prise IC DIP.
Le schéma montre comment toutes les pièces seront câblées, la broche de contrôle mosfet est étiquetée "PWM" car je viens de les câbler directement à une broche sur l'arduino, car je pourrais changer ce que chaque broche contrôlait à partir du code.
J'ai commencé par placer la prise DIP près d'un côté de la carte près du milieu de la carte.
ASTUCE: le collant aide à maintenir les pièces en place pendant le soudage.
J'ai ensuite ajouté le condensateur 100nF sur les broches 1 et 2 puis utilisé les deux résistances 100k OHM pour me connecter à la broche 8. J'ai ensuite utilisé 4 condensateurs en parallèle et ajouté le 100nF sur la broche 6. Ensuite, le câble audio mâle a été ajouté et câblé dans le Condensateur 10nF. La masse du câble audio était reliée à la masse.
J'ai inclus une image de l'arrière du panneau perforé, j'ai également ajouté des étiquettes sur le dessous afin qu'il soit plus facile de comprendre où les pièces ont été câblées.
Étape 4: Ajout de Mosfets
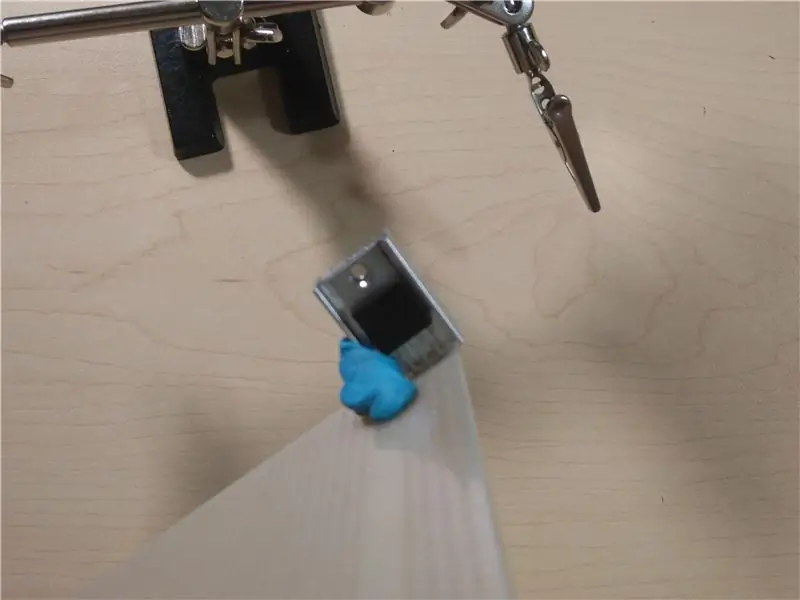
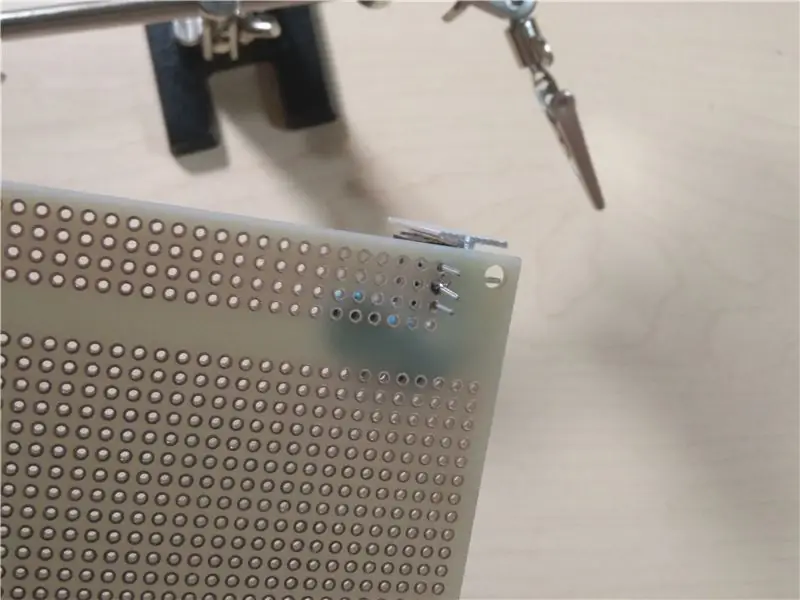
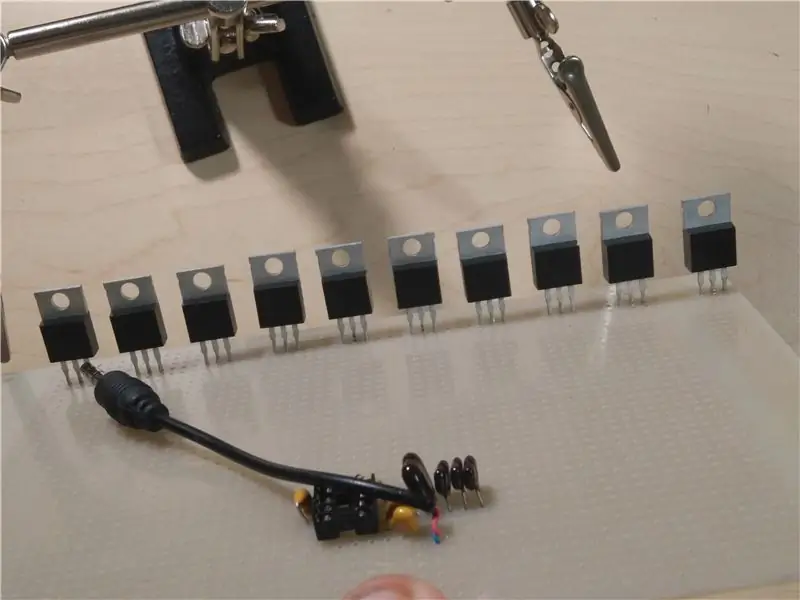
L'étape suivante que j'ai prise consistait à ajouter les mosfets, alors que j'ajoutais des mosfets.
Je commencerais simplement par appliquer de la soudure sur la broche du milieu, ce qui permet des ajustements.
Une fois les mosfets en place, j'ai commencé à ajouter les résistances de tirage 10k OHM, j'ai utilisé les pattes de résistance pour faire le pont entre les broches nécessaires.
Étape 5: Placement des diodes et des résistances 5W
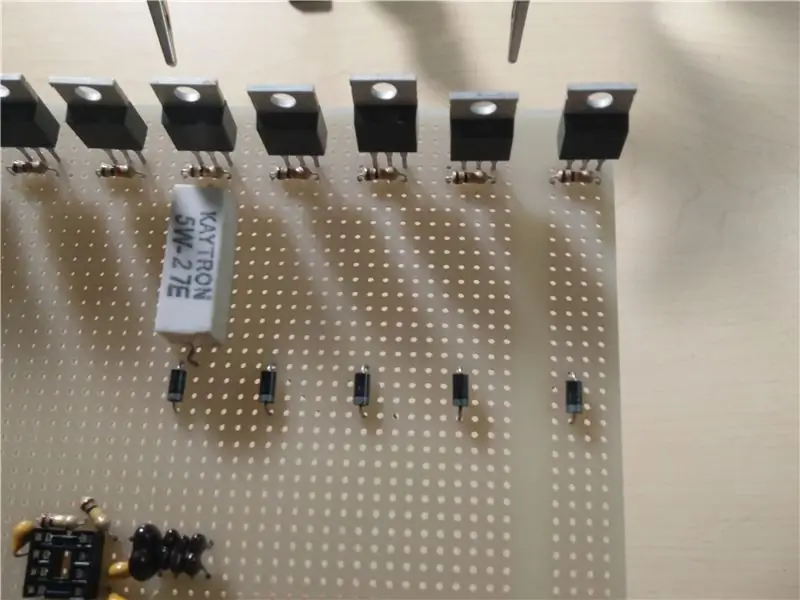
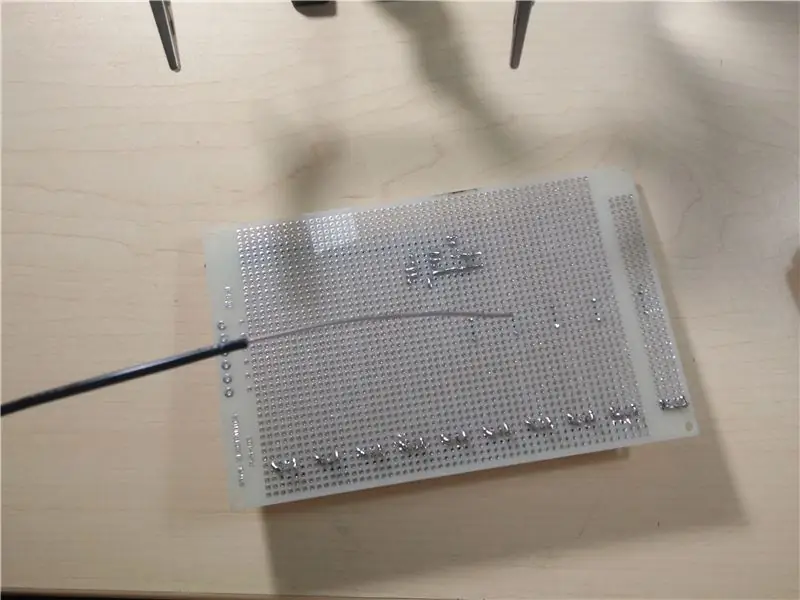
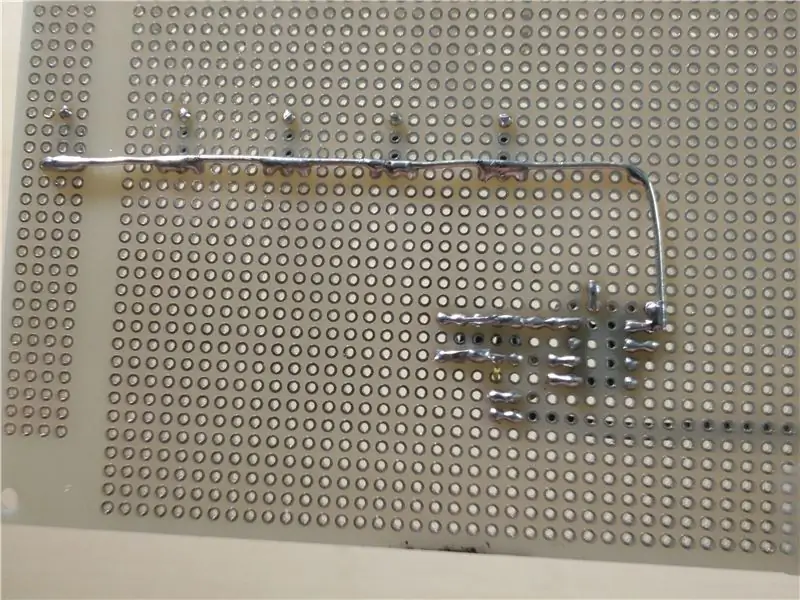
Au moment de cette étape, j'attendais toujours que des résistances de 5W me soient expédiées, j'ai donc récupéré une résistance de la version précédente des haut-parleurs à eau afin de pouvoir assurer l'espacement nécessaire pour placer les diodes.
Une fois les diodes placées, j'ai commencé à dénuder le fil solide 18AWG pour qu'il serve de barres omnibus positives et négatives.
Un fil AWG solide a été placé sur le côté positif des diodes, puis acheminé vers la broche 1 de la prise IC.
une autre pièce a été utilisée pour passer du côté négatif du condensateur 33pF et des boucles autour des mosfets. Un autre morceau plus petit a été bouclé du négatif des condensateurs 33pF à la broche 2 sur la prise IC.
Étape 6: Ajout de Panel Jack et Bluetooth et de potentiomètres
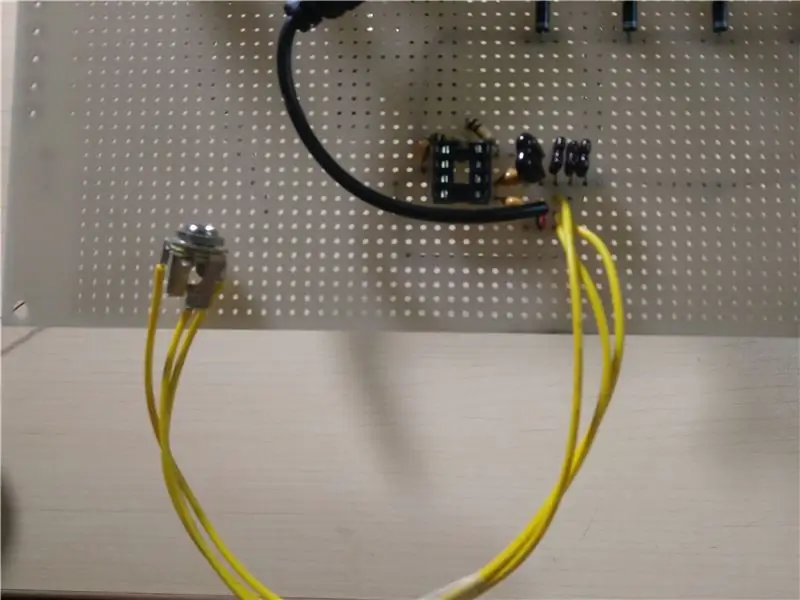
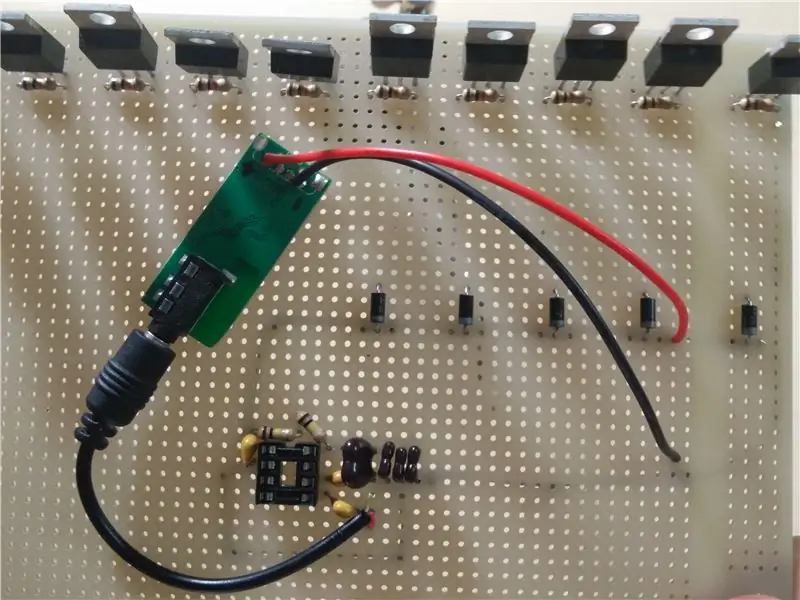
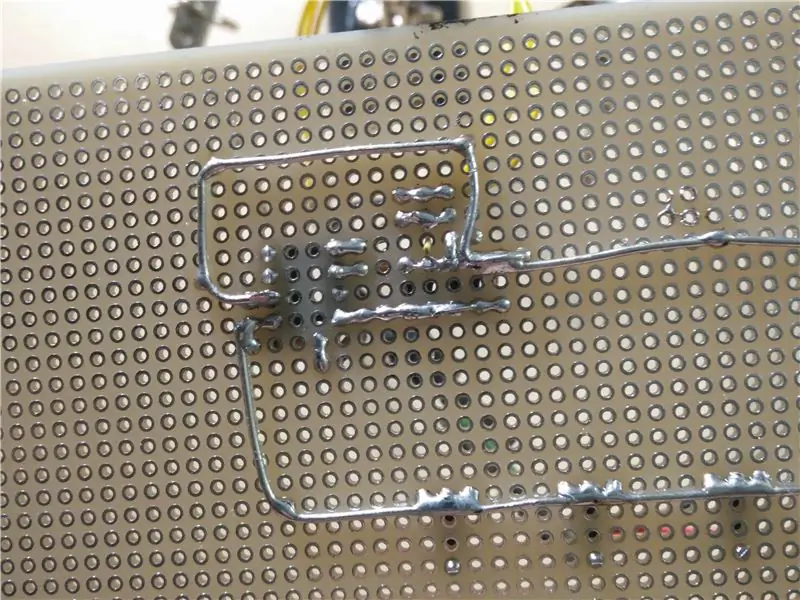
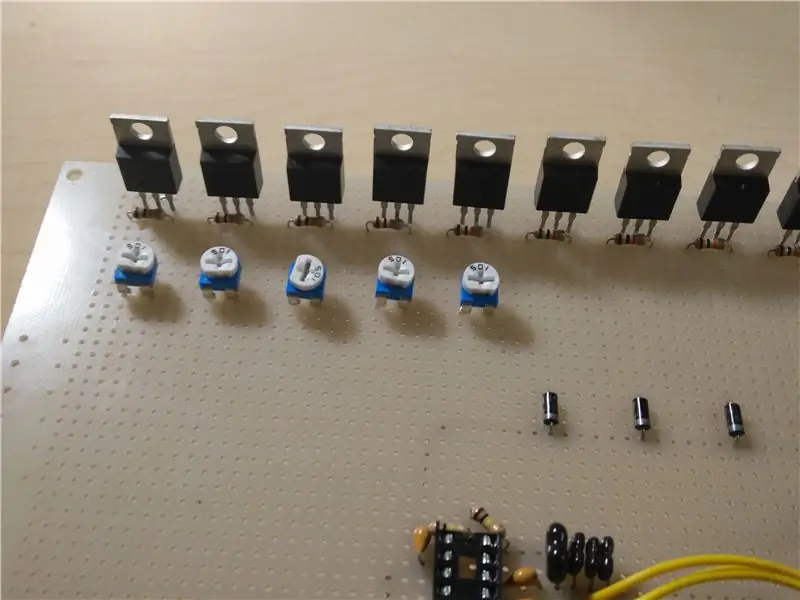
Utilisez un fil de raccordement toronné 20AWG pour attacher la prise du panneau aux mêmes connexions que le câble audio mâle. J'ai ensuite ajouté des fils pour l'alimentation et la terre pour l'adaptateur Bluetooth, en utilisant la barre omnibus en fil AWG solide sur la face inférieure.
J'ai ensuite ajouté les potentiomètres 500 OHM qui permettent un contrôle supplémentaire de la luminosité des LED (ceux-ci sont nécessaires mais je trouve que certaines couleurs de LED peuvent en surpasser d'autres, alors je les ai ajoutés pour ajuster leur luminosité)
J'ai utilisé un excès de métal provenant de fils de condensateur recadrés pour combler la distance entre le potentiomètre et la broche centrale des mosfets
Étape 7: Préparation des haut-parleurs à eau
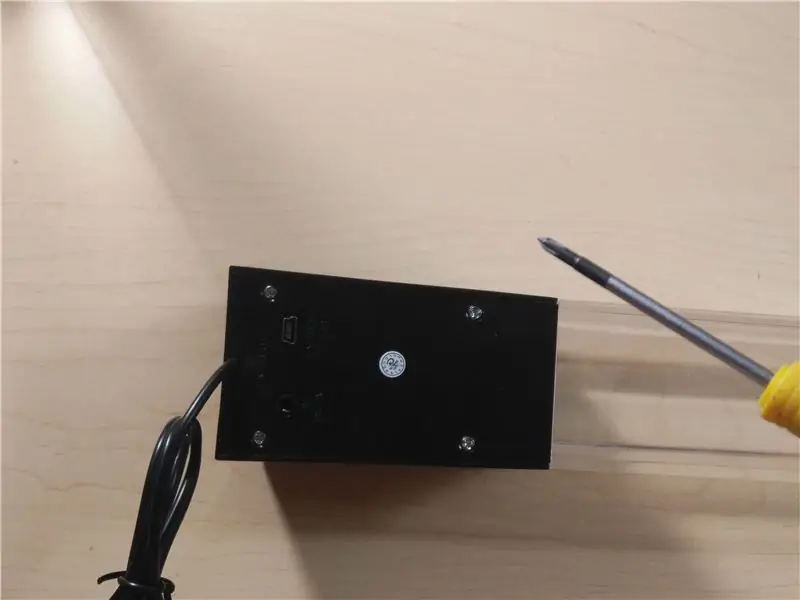
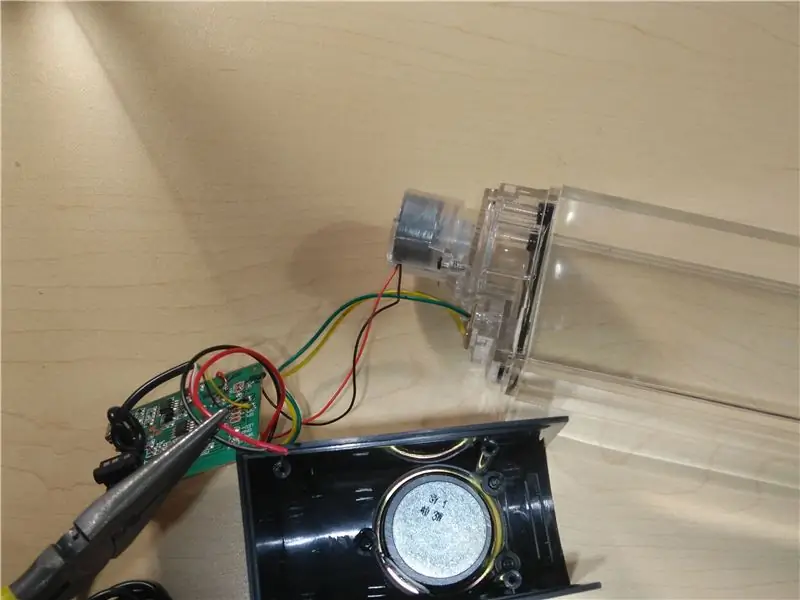
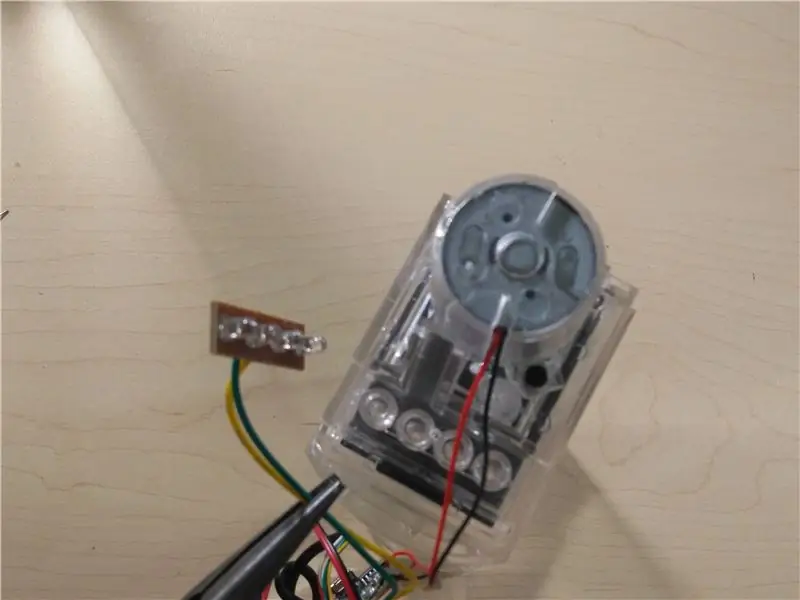
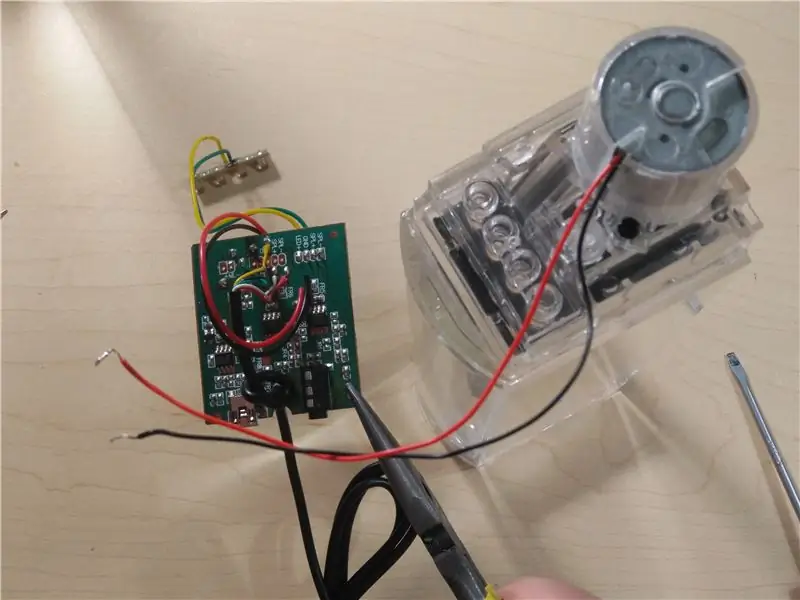
J'ai commencé par utiliser un petit tournevis pour retirer les petites vis à l'arrière du boîtier du haut-parleur à eau, après avoir retiré le circuit imprimé, j'ai localisé les fils du moteur. à l'aide de couteaux affleurants, je les ai coupés aussi près que possible du circuit imprimé.
REMARQUE: les fils des moteurs ne sont pas réparables, faire trop d'erreurs lors de la coupe et du dénudage des extrémités pourrait endommager le moteur/les fils
J'ai ensuite utilisé une petite pince à bec effilé pour retirer le circuit imprimé avec des LED. J'opte pour avoir une couleur par boîtier d'eau par rapport aux 4 couleurs utilisées dans le produit du magasin.
Je plie ensuite les fils positifs des LED presque au ras de manière à ce qu'ils se croisent, je commence par plier les LED de sortie de sorte que les LED de niveau s'étendent d'un bout à l'autre. Utiliser du collant pour maintenir les LED en place; Je plie ensuite les deux LED internes mais recadre leurs fils car ils n'ont pas besoin d'être aussi longs. Avec les LED maintenues par du sticky tack, je ne peux pas souder les fils positifs ensemble.
Je peux maintenant recadrer les fils négatifs des LED et recadrer également les résistances. (J'ai choisi de positionner les LED de manière à ce que leurs bandes de couleur soient toutes orientées dans la même direction; c'était purement cosmétique) En utilisant les fils des résistances, je les plie de la même manière que j'ai fait pour les fils positifs des LED.
J'ai utilisé de la colle chaude pour maintenir les LED en place. Ensuite, attachez le connecteur à 3 fils. Le moteur et les LED partagent un point positif commun. les connecteurs correspondants sont ensuite connectés à la carte perforée, le positif d'un côté de la diode et le négatif du moteur de l'autre côté de la diode. Le négatif des LED est câblé à une patte sur le potentiomètre.
Les LED rouges et jaunes avaient une résistance de 150 OHM
Les LED blanches, vertes et bleues avaient une résistance de 100 ohms
Ces valeurs de résistance devraient permettre à chaque LED de fonctionner à 20mA
Étape 8: Ajout des fils Arduino
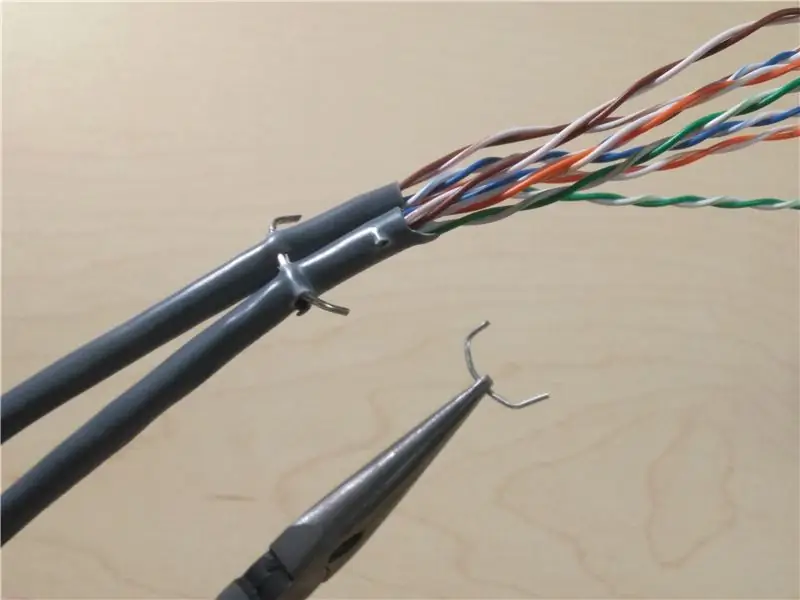
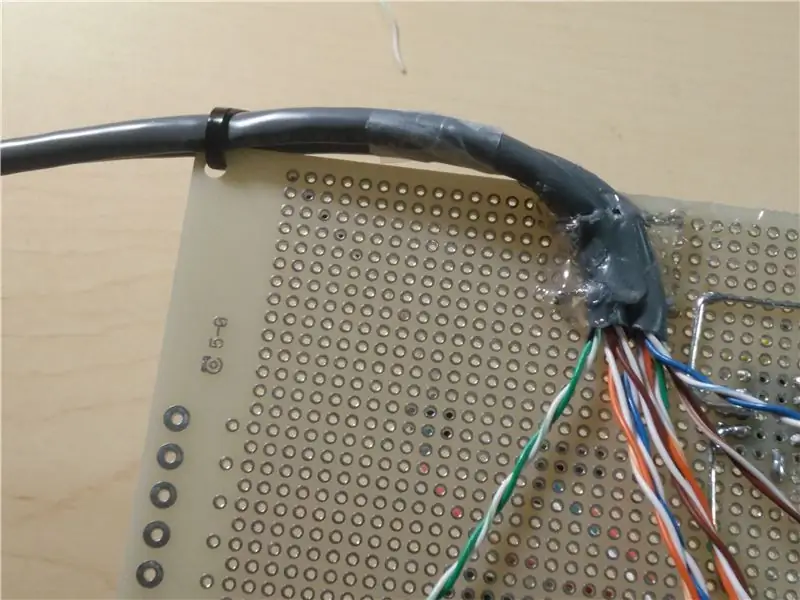
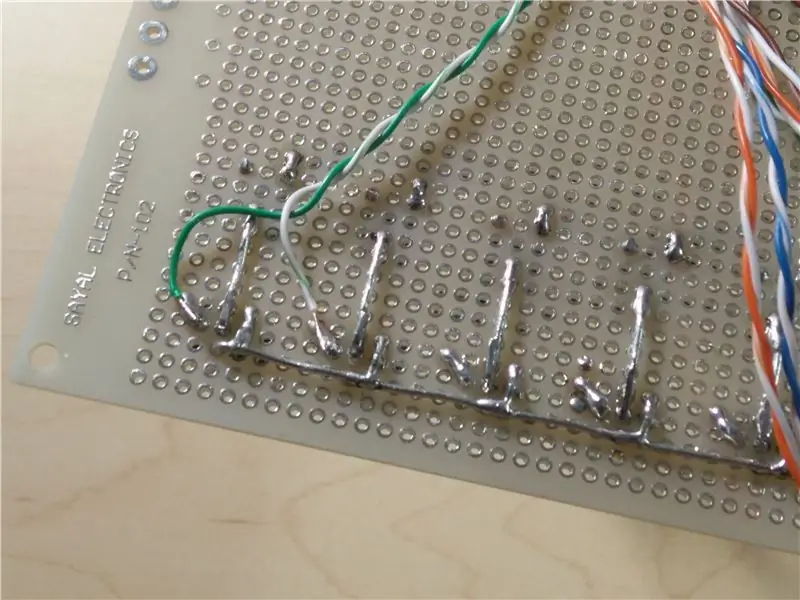
J'ai utilisé deux longueurs de câble Ethernet, environ 12 pouces de câble (x 2) J'ai utilisé 15 fils au total (1 de rechange)
J'ai utilisé une partie du fil à âme solide qui a épargné le câble pour aider à fixer le câble au panneau perforé, j'ai fini par avoir besoin de colle chaude pour le maintenir en place. Une attache zippée dans le coin a aidé à diriger le fil vers l'arduino qui serait positionné à côté du panneau perforé une fois placé dans le boîtier.
Les fils étaient placés au hasard, mais je me suis assuré qu'ils pouvaient atteindre l'endroit dont ils avaient besoin, certains étaient plus longs que d'autres, ceux qui étaient trop longs étaient coupés à la bonne taille. En utilisant les en-têtes, j'ai pu souder les autres extrémités du fil aux broches, cela me permet de démonter l'arduino si j'en ai besoin. J'ai fini par ajouter de la colle chaude plus tard pour m'assurer que les fils ne cassent pas les broches, mais je le fais après que toutes les fonctions aient été testées.
J'ai ajouté des fils pour le contrôle IC et un fil pour le 5v+ et la masse.
Après cela, j'ai fait un test pour voir si les lumières et le circuit intégré fonctionnaient correctement, car j'attendais toujours les résistances de 5w par la poste.
Étape 9: Les résistances du moteur et les potentiomètres
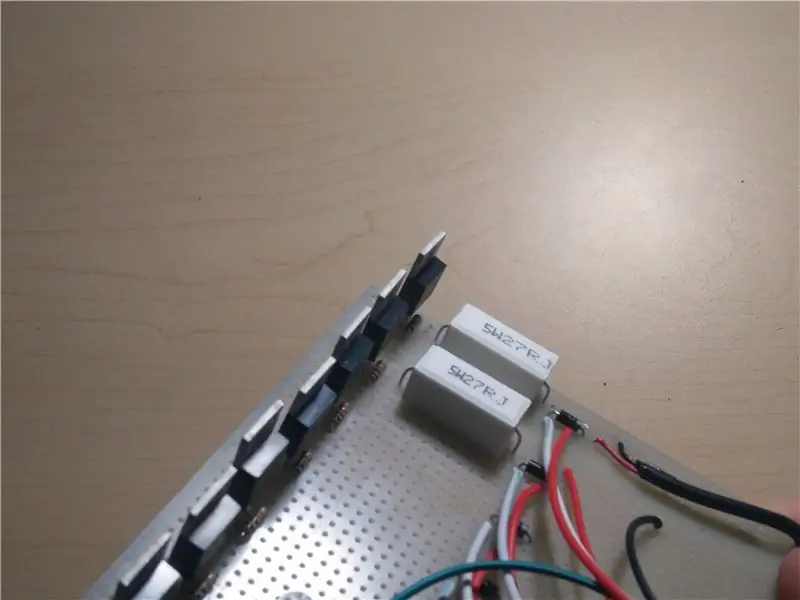
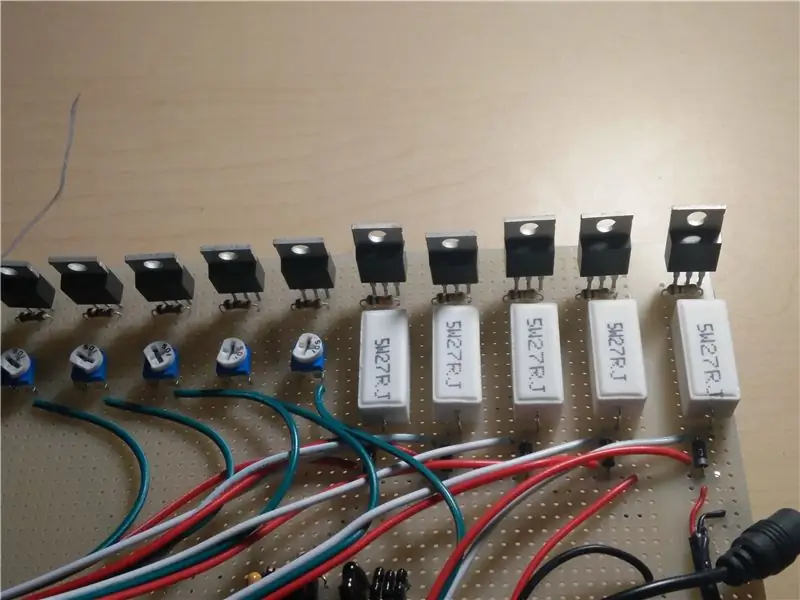
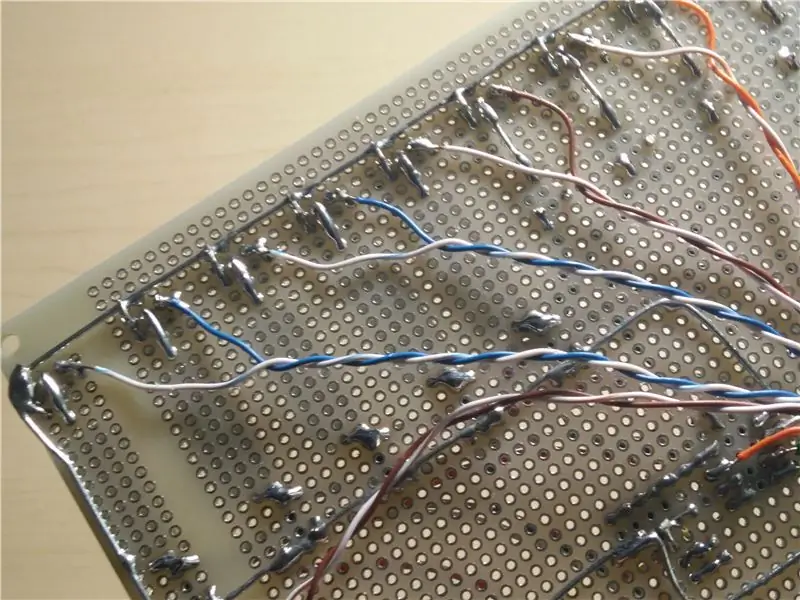
J'ai ajouté les résistances de 5W entre la diode et la broche centrale du mosfet. J'utilise les fils de la résistance se plier pour combler l'écart.
Je trouve que les moteurs sont plus réactifs lorsqu'ils sont pulsés et actionnés rapidement lorsque l'eau coule déjà lentement. C'est là que le potentiomètre 2k entre en jeu. Le potentiomètre est câblé à l'aide d'un fil de raccordement 20AWG à la résistance 5w (ne pas attacher ce fil avant la résistance 5W car le potentiomètre ne peut pas gérer la puissance du moteur)
Une autre jambe du potentiomètre est pliée et à l'aide d'un autre morceau de fil solide 18AWG, je peux connecter une seule broche de tous les potentiomètres à la terre.
REMARQUE: j'avais initialement essayé de ne pas utiliser les potentiomètres, mais j'ai constaté que l'utilisation de PWM sur ces moteurs provoque de terribles retours haute fréquence qui provoquent des interférences avec le circuit intégré.
Étape 10: Impression 3D
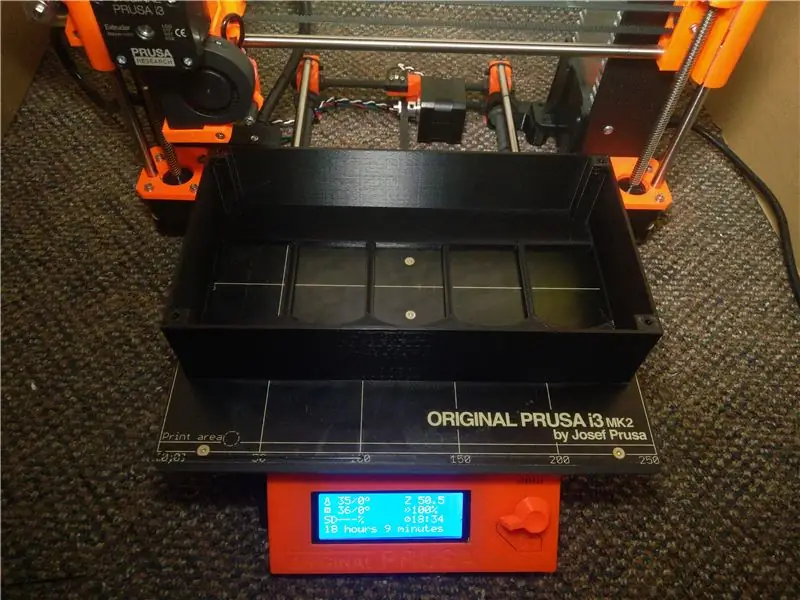
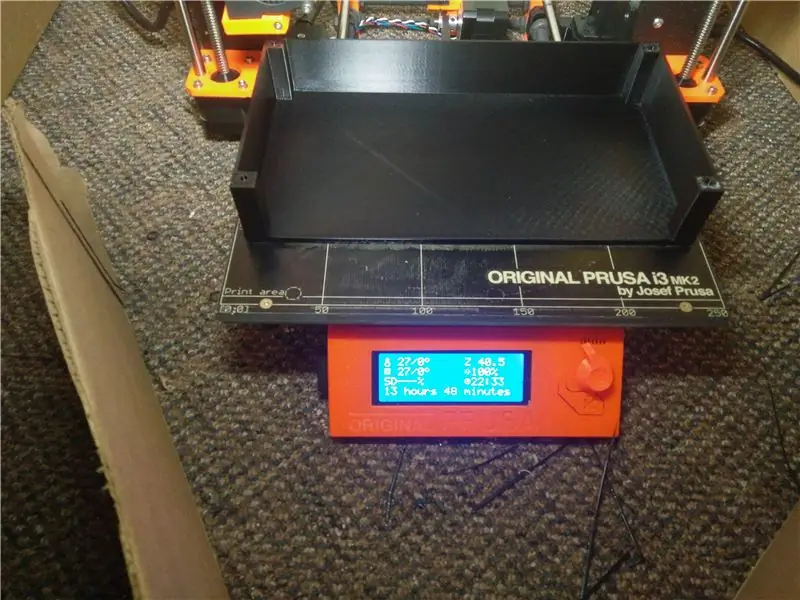
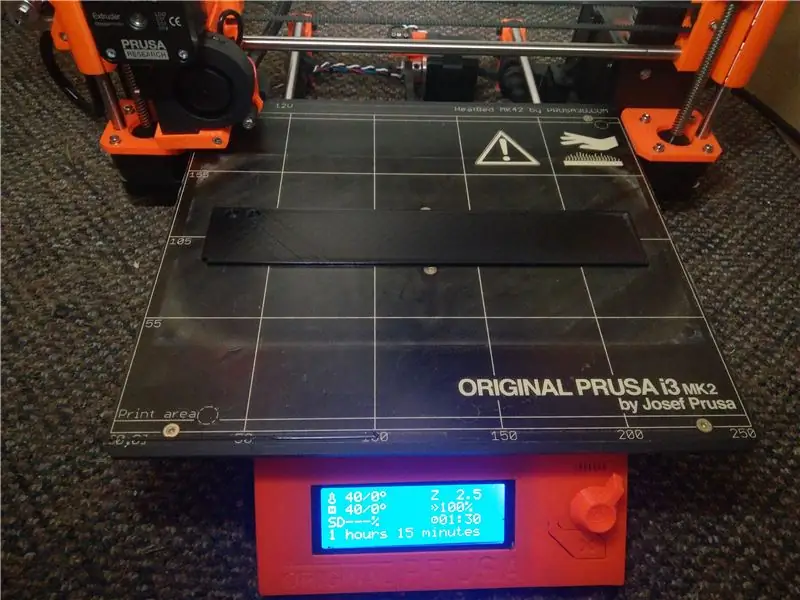
J'ai imprimé un total de 3 parties, le panneau supérieur, inférieur et arrière. Les fichiers STL que j'ai ajoutés ne sont cependant que deux parties (haut et bas), ce qui rendra les choses plus faciles à suivre pour quelqu'un. Je l'ai fait car j'ai trouvé qu'essayer d'ajouter le panneau après coup n'avait pas l'air aussi bien. Je fais principalement un panneau arrière parce que je n'étais pas sûr de ce que je voulais au dos. Dans mon cas, j'ai décidé d'ajouter un interrupteur marche/arrêt.
Au total, vous regardez 36 heures d'impression 3D. J'utilise l'ABS dans mon imprimante car je trouve qu'il est très facile de peindre et de poncer. De plus, lorsque je fais des assemblages, je peux utiliser de l'acétone pour souder des pièces ensemble.
La première partie que je recommande d'imprimer est le fichier de test de mesure 3D, il s'agit d'un petit morceau de 15 minutes qui vous permet de vous assurer que le haut-parleur à eau s'adaptera, j'ai parcouru environ 8 itérations jusqu'à ce que j'aie le bon profil pour s'adapter au haut-parleur. En faisant cela, cela m'évite de perdre une impression de 18 heures. le dessus a des fentes pour 1/8 "x 1 1/2" J'ai dû utiliser un petit fichier car le pontage sur mon imprimante 3D est un peu serré.
Étape 11: Assemblage
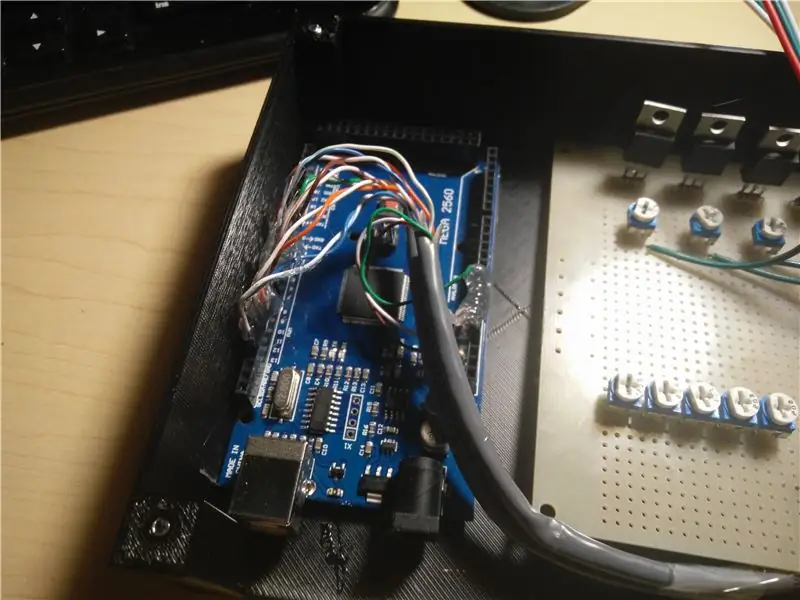
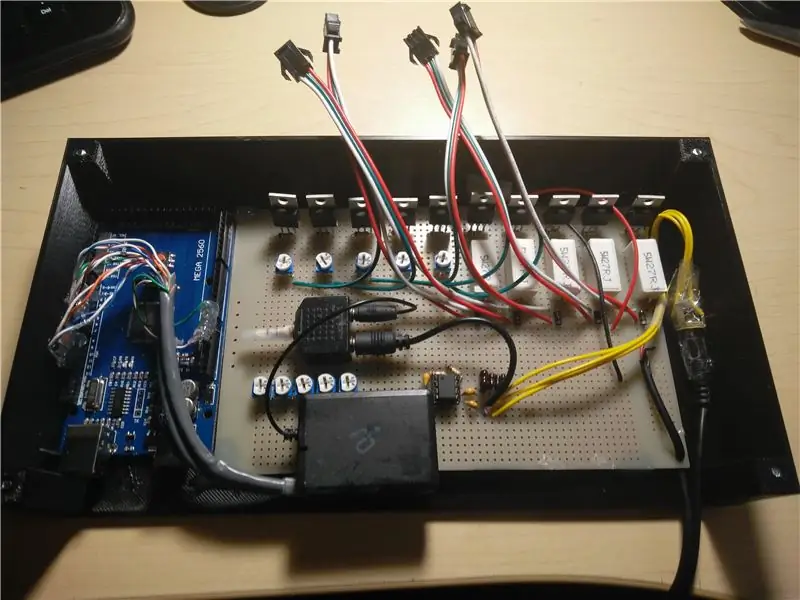
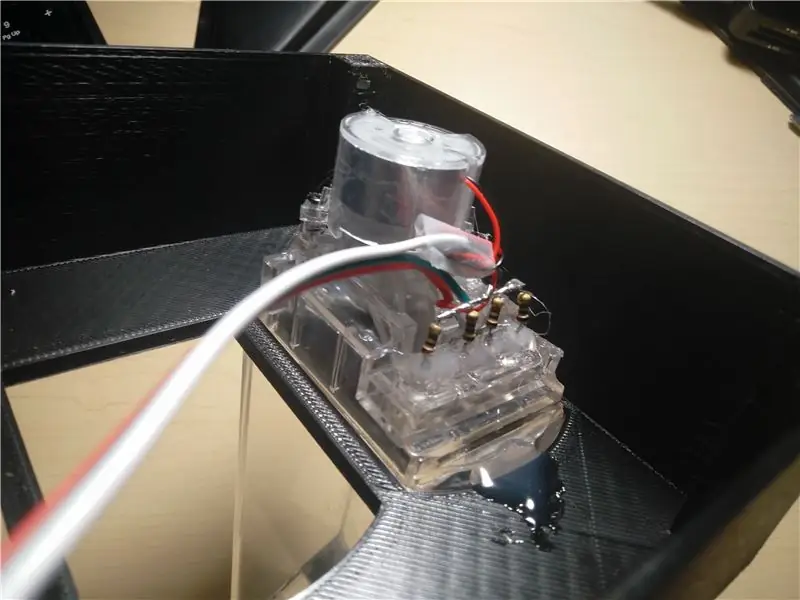
J'ai commencé par utiliser de la colle chaude sur les têtes de fil pour les fils, c'est pour m'assurer qu'ils ne se cassent pas. J'ai ajouté la colle chaude après m'être assuré que les moteurs fonctionnaient avec la programmation. J'ai utilisé une petite quantité de colle chaude dans les deux coins de l'arduino afin qu'elle puisse être retirée plus tard en cas de besoin. des entretoises et des inserts filetés pourraient également être conçus dans l'impression 3D.
Comme vous pouvez le voir sur la photo, j'ai un autre module Bluetooth attaché, j'ai utilisé ce module en attendant un nouveau par la poste. Le problème principal du déclenchement erroné des haut-parleurs n'est pas entièrement la faute des modules Bluetooth, les moteurs ne semblent pas aimer fonctionner sur PWM.
J'ai ajouté les châteaux d'eau à la pièce supérieure et je l'ai fixé avec de la colle chaude. J'en ai utilisé une petite quantité car je prévois de démonter les haut-parleurs plus tard et de poncer puis d'enduire le plastique transparent mais il fait trop froid pour pulvériser de la peinture là où je suis en ce moment. La prise et l'interrupteur du panneau ont ensuite été ajoutés au panneau arrière, j'avais en fait ajouté le câble d'alimentation USB plus tôt, mais maintenant que l'impression 3D est d'une seule pièce, le câble doit être acheminé à travers le boîtier puis câblé en place, vous pouvez voir où je câblé l'USB sur la photo, il passe à travers le panneau perforé et soudé à la barre omnibus en fil AWG solide. La seule différence par rapport à la photo est qu'avec le commutateur, le positif ira d'abord au commutateur, puis au panneau perforé.
Étape 12: Le code
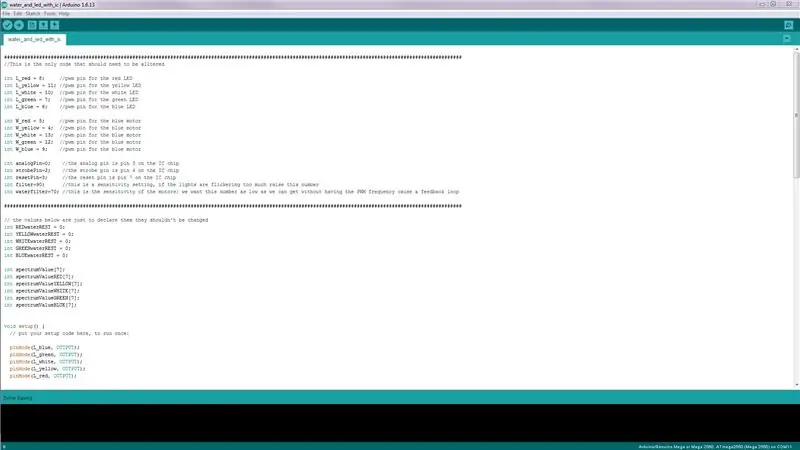
Le code que j'ai ajouté est pour la plupart simple. Le code devrait fonctionner tel quel.
La seule chose qui aurait besoin d'être changée sont les variables en haut du code. Ils sont clairement signalés par des commentaires.
REMARQUE:
Sur la base d'une astuce, j'ai pris le temps d'apprendre et d'essayer d'ajuster la fréquence PWM sur l'arduino mega. Bien que le changement de fréquence ait aidé à éliminer le bruit du moteur qui provoquait une boucle de rétroaction, cela m'a cependant obligé à modifier de nombreuses autres parties du code, le timing a dû être modifié, la sensibilité a dû être augmentée.
Le problème de la modification de la fréquence PWM créée est que la synchronisation a dû être augmentée pour compenser le faux déclenchement qui a commencé à se produire et que les valeurs ont dû être modifiées, rendant les haut-parleurs moins sensibles. Je pense que la meilleure chose à ce stade serait d'essayer le pilote de moteur de mon itération précédente de ce projet dont on parle davantage à la dernière étape.
Étape 13: Le produit final
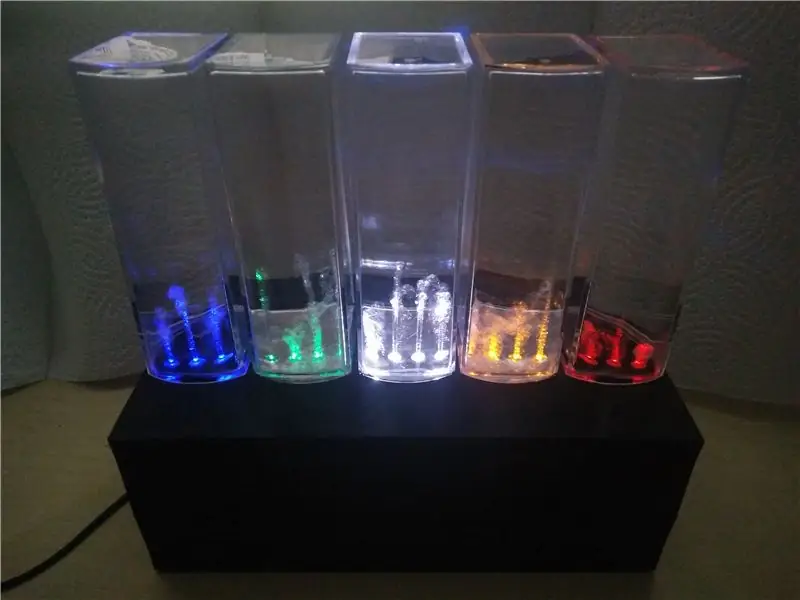
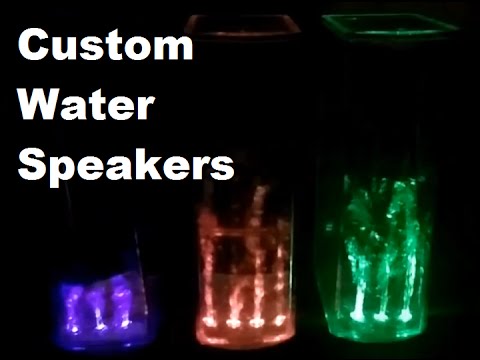
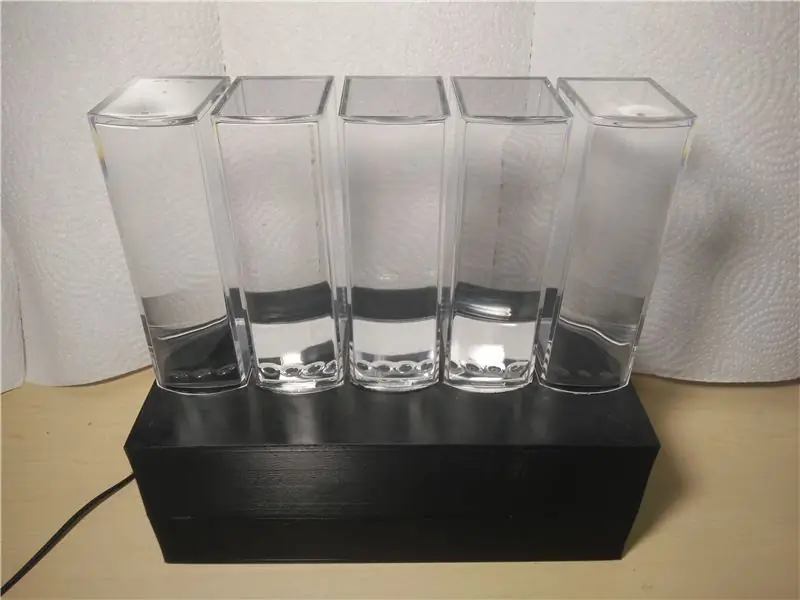
Le dernier élément est vraiment intriguant à regarder. Cet article est mieux regardé dans un éclairage de pièce faible à sombre. Malheureusement, mon appareil photo actuel est incapable d'enregistrer dans des conditions de faible éclairage. C'est parce que je pourrais utiliser un bon appareil photo pour montrer mes projets que j'ai participé au concours d'auteur pour la première fois, j'espère que les gens ont apprécié ce projet et choisiront de voter pour moi.
J'ai ajouté une vidéo de la version originale des enceintes afin que vous puissiez voir à peu près à quoi elles ressemblent.
Prochaines étapes
J'aimerais essayer d'utiliser le circuit de commande de moteur d'origine que j'ai créé dans la version 1, qui utilise des transistors et des photocellules pour voir si cela permettrait aux moteurs de mieux fonctionner, cela devrait éliminer les problèmes que j'ai rencontrés avec le bruit de fréquence activé les moteurs en raison de l'utilisation du signal de commande PWM. Je pourrais également ajouter des haut-parleurs sur le côté du boîtier avec leur propre contrôle de volume.
Vous remarquerez peut-être également que l'intérieur des châteaux d'eau est de couleurs différentes. à une seule couleur, mais ils se vendent 40 $ la paire.
Conseillé:
Un compteur de température, de conductivité et de niveau d'eau de l'eau de puits en temps réel : 6 étapes (avec photos)
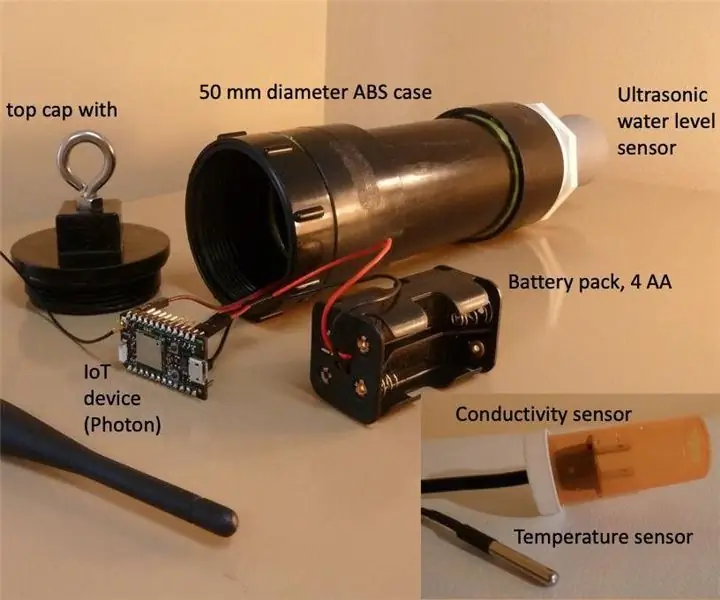
Un compteur de température, de conductivité et de niveau d'eau de l'eau de puits en temps réel : ces instructions décrivent comment construire un compteur d'eau en temps réel à faible coût pour surveiller la température, la conductivité électrique (CE) et les niveaux d'eau dans les puits creusés. Le compteur est conçu pour être suspendu à l'intérieur d'un puits creusé, mesurer la température de l'eau, EC et
Porte-bouteille d'eau pour rappel d'eau : 16 étapes
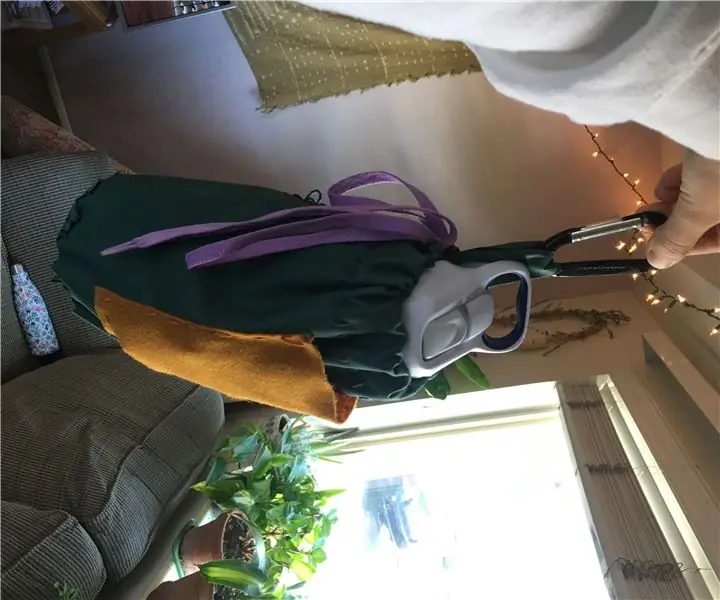
Rappel d'eau Porte-bouteille d'eau : Vous oubliez jamais de boire votre eau ? Je sais que oui ! C'est pourquoi j'ai eu l'idée de créer un porte-bouteille qui vous rappelle de boire votre eau. Le porte-bouteille d'eau a une fonction où un bruit retentira toutes les heures pour vous rappeler t
Système d'alarme de consommation d'eau/moniteur de prise d'eau : 6 étapes
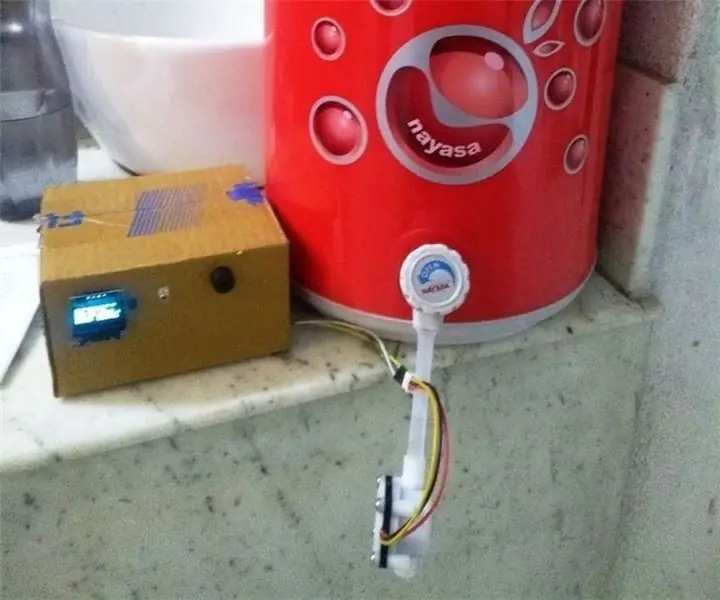
Système d'alarme de consommation d'eau/moniteur de prise d'eau : nous devrions boire une quantité d'eau suffisante chaque jour pour rester en bonne santé. Il existe également de nombreux patients à qui l'on prescrit de boire une quantité spécifique d'eau tous les jours. Mais malheureusement, nous avons manqué l'horaire presque tous les jours. Alors je conçois
Économisez de l'eau et de l'argent avec le moniteur d'eau de douche : 15 étapes (avec photos)
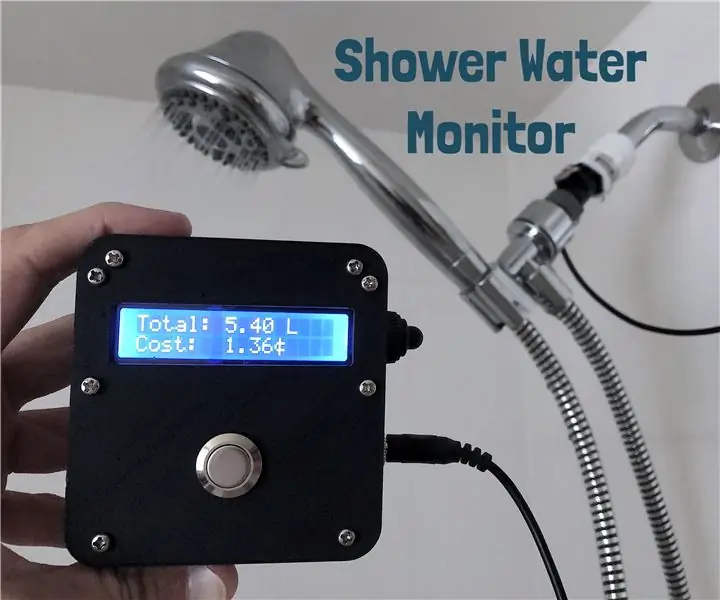
Économisez de l'eau et de l'argent avec le moniteur d'eau de douche : qu'est-ce qui utilise le plus d'eau - un bain ou une douche ? Je sais que quand je suis sous la douche, parfois mon esprit vagabonde, pensant à un cool
Jupe d'égaliseur réactive au son portable : 21 étapes (avec photos)
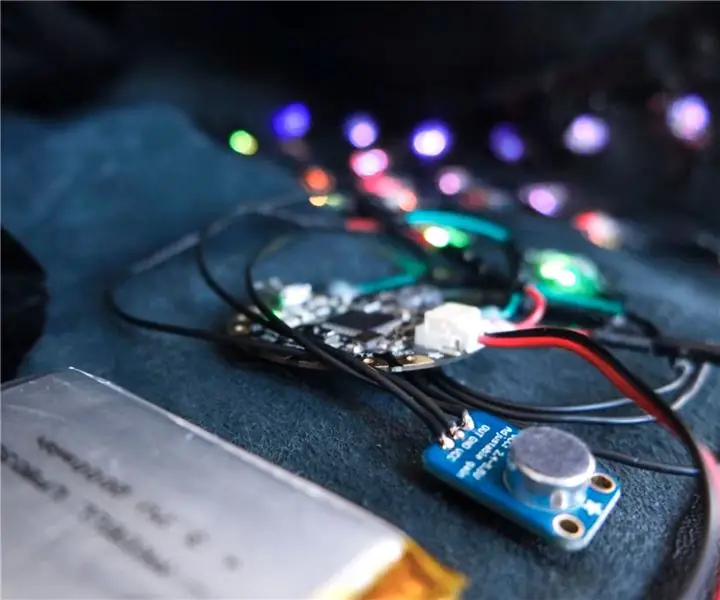
Jupe Wearable Sound Reactive Equalizer : Depuis un certain temps, j'ai voulu concevoir une pièce qui interagit avec le son. La jupe Equalizer a une électronique intégrée qui réagit au niveau de bruit de son environnement. Les LED intégrées sont disposées comme des barres d'égalisation pour mettre en évidence le son réactif