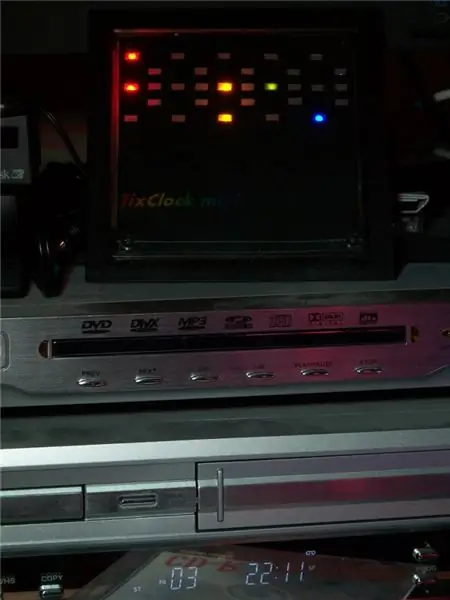
Table des matières:
2025 Auteur: John Day | [email protected]. Dernière modifié: 2025-01-23 14:46
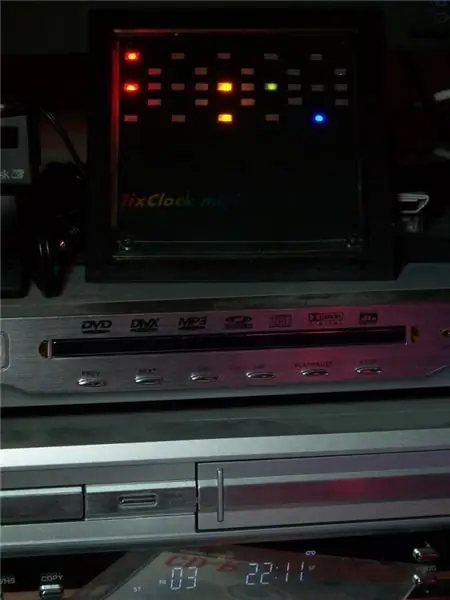
Un ensemble de LED change de façon aléatoire toutes les 10 secondes environ. Pour lire l'heure, il suffit de compter le nombre de points par chiffre. La photo principale montre l'heure, 22h11. Différentes couleurs sont attribuées à différents chiffres, rouge-10 heures, ambre-heures, vert-10 minutes, bleu-minutes. L'utilisation de superrights de 3 mm signifie que l'horloge peut être lue de jour comme de nuit (bien qu'elle soit lavée en plein soleil).
Avoir un motif aléatoire est beaucoup moins gênant que d'avoir des chiffres numériques qui vous regardent… ce serait également un excellent projet à ajouter aux panneaux avant ou de taille d'un mod PC.
Étape 1: Aperçu
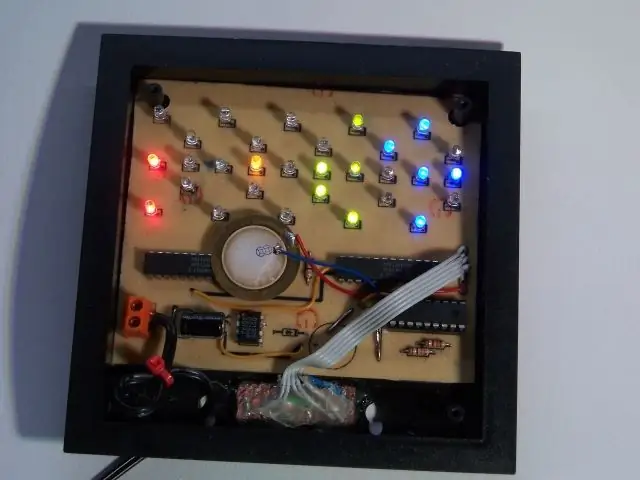
Ce projet a été inspiré de l'appareil TixClock que j'ai vu être annoncé chez ThinkGeek. C'était un peu gros pour mon application, je voulais une horloge au dessus de mon DVD car elle n'affichait pas l'heure lors de la lecture d'un DVD.
La conception est basée autour du boîtier, un boîtier « d'affichage » à profil bas de Jaycar Electronics (www.jaycar.com.au) numéro de catalogue HB6083. Si vous souhaitez mettre cette horloge dans un autre boîtier, vous devrez modifier la disposition du PCB. Un fichier zip avec le code source, des fichiers pcb au format EagleCad et quelques photos est inclus dans le projet. Certaines pistes sont un peu étroites et ont très peu de dégagement. J'ai construit cela à l'aide d'un film press-n-peel, donc cela peut être fait….faites juste attention à ne pas tacher les choses et vérifiez soigneusement le résultat, en grattant toutes les pistes floues qui pourraient en toucher une autre. Le PCB est conçu pour deux couches, mais je l'ai construit sur une carte simple face pour économiser les efforts. Il n'y a que quelques pistes sur le dessus, et celles-ci peuvent être traitées en utilisant un fil de connexion. Notez que l'image est un peu différente de la conception du PCB dans le fichier zip. Les modifications connectaient les broches d'activation des puces 74hc154 directement à la terre et une diode supplémentaire pour abaisser la tension aux bornes du supercap afin de la rapprocher des 3,3 V requis par la puce RTC. Quelques conseils pratiques lors de la création d'un panneau double face à l'aide de couches simples: - faire autant de travail de piste sur le côté inférieur que possible - lorsque vous posez une piste sur le dessus, amenez-la toujours vers un via, plutôt que de connecter la piste de la couche supérieure directement à un composant. - lors de l'utilisation du press-n-peel, imprimez la sérigraphie (à l'envers) et repassez-la sur le PCB après perçage et gravure. Cela vous donne non seulement le placement des composants, mais si vous imprimez également les pistes supérieures, c'est un guide facile pour le fil de raccordement. Notez les lignes noires dans le PCB ci-dessous… ce serait là où se trouveraient les pistes de la couche supérieure.
Étape 2: Conception du panneau avant
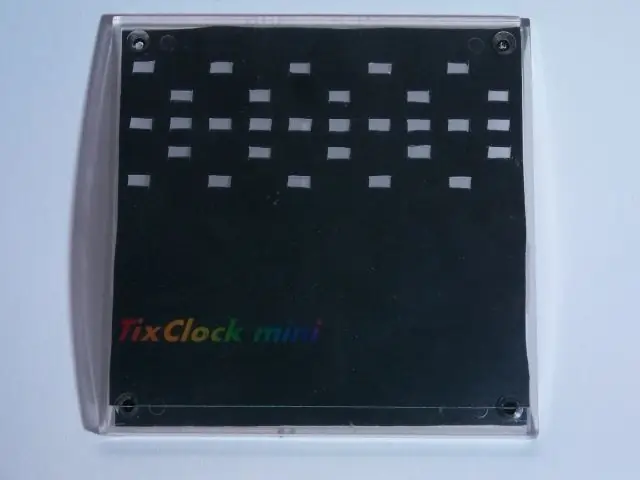
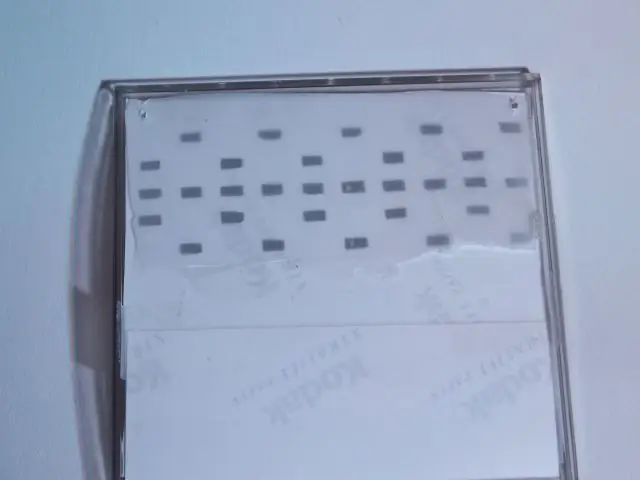
Une astuce pratique pour aligner les panneaux avant d'apparence cool avec vos dispositions de PCB consiste à imprimer une image de votre sérigraphie, puis à éditer tous les éléments qui ne sont pas sur le panneau avant. Dans ce cas je n'ai gardé que les leds. L'image a été éditée dans un éditeur de photos et du texte a été ajouté. En utilisant une imprimante photo, vous pouvez obtenir des motifs colorés (bien que la palette de couleurs soit un peu minime). Les trous de LED ont été découpés avec un couteau tranchant et du papier calque a été ajouté à l'arrière pour diffuser un peu la lumière.
Ma petite imprimante photo a créé des tirages un peu trop étroits pour s'adapter à l'ensemble du boîtier, donc une petite bande a été ajoutée pour le remplir. Cela semble OK dans ce cas parce que le panneau avant est si minime.
Étape 3: Commutateurs de contrôle
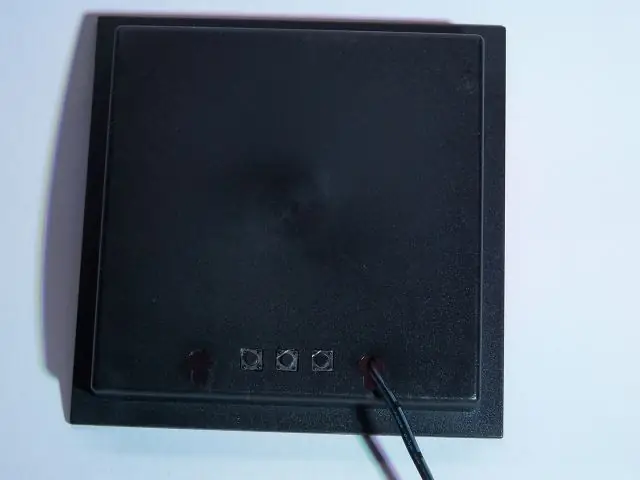
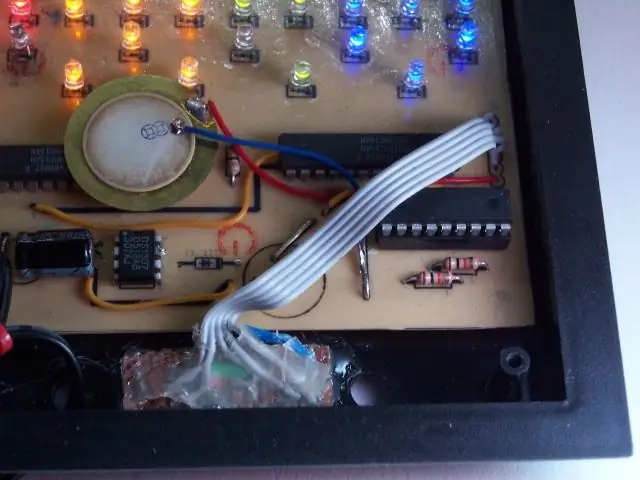
Vous devez pouvoir régler l'heure. J'ai utilisé trois micro-interrupteurs récupérés d'une vieille chaîne stéréo, je les ai montés sur un morceau de veroboard (ou de stripboard) et j'ai collé l'ensemble de commutateurs à l'aide de colle chaude sur le boîtier.
Le premier commutateur sélectionne le mode de réglage de l'heure, le second sélectionne le chiffre et le troisième incrémente le chiffre. Après avoir changé l'heure, sélectionnez à nouveau le premier commutateur et l'horloge fonctionnera. Le câble plat du commutateur a 5 lignes, vcc/gnd et les trois entrées de commutateur. Chaque interrupteur est momentanément fermé. Sur la taille se connecte à la terre, l'autre à la ligne d'entrée du commutateur et une résistance pullup à vcc. En d'autres termes, les entrées sont normalement hautes, puis tirées bas pour s'activer. Voir le schéma pour plus de détails sur le câblage. Une chose qui était utile dans l'utilisation de veroboard était que la carte elle-même était le gabarit de perçage pour les trous de commutation. De petits trous ont été percés exactement aux bonnes positions, puis équarris avec une lime. Il a fait un bon ajustement.
Étape 4: Assemblage final
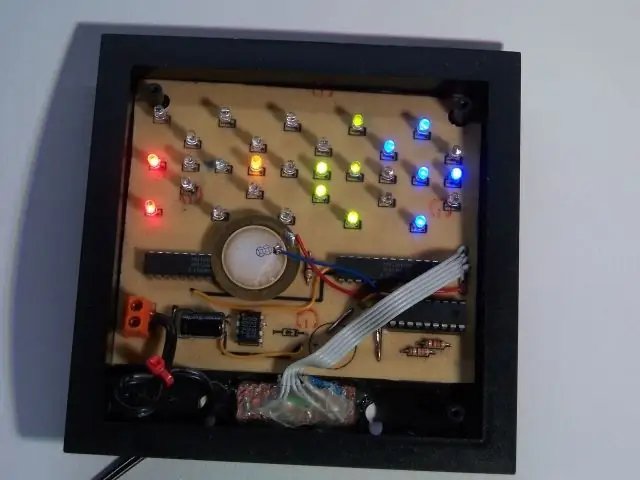
Le PCB a été conçu spécifiquement pour ce cas, il suffit donc de le glisser sur les poteaux de montage. Parce que l'espace était très restreint, l'ensemble du commutateur a été soudé directement au PCB et un buzzer piézo collé à chaud sur une puce. Si vous voulez un piézo plus fort, vous devrez ajouter un pilote car celui-ci est directement piloté par le microcontrôleur. Vous avez vraiment besoin de coller ou de fixer le piézo à quelque chose pour augmenter le volume.
Le câble d'alimentation a été attaché autour du poteau de montage inférieur comme un soulagement de traction. Je viens de le percer dans les trous de montage, mais vous pouvez utiliser un passe-fil approprié si nécessaire. C'est à peu près tout, l'appareil est alimenté par un plugpack 9V et se trouve au-dessus de mon lecteur dvd en changeant joyeusement les modèles.
Étape 5: À propos de la sauvegarde du micrologiciel et du Supercap
Ce firmware a été conçu avec le compilateur Sourceboost et utilise la bibliothèque Sourceboost I2C pour communiquer avec la puce RTC. J'ai dû modifier le pilote i2c pour utiliser des délais plus longs afin d'obtenir un fonctionnement fiable.
Le firmware initialise io, puis lit toutes les dix secondes environ (vous pouvez modifier cela dans le code si vous voulez une mise à jour plus rapide ou des temps de mise à jour aléatoires. J'ai trouvé cette période la moins gênante). Si des pressions de touche sont détectées, il entre dans la routine de changement d'heure jusqu'à ce qu'il soit quitté en appuyant sur le commutateur un. La conception comprend également un espace pour un supercap. Je n'ai pas testé cela, mais en installer un devrait permettre à l'horloge de gérer les pannes de courant pendant une courte période. Dans le micrologiciel, une fois les données RTC lues, une routine prend les valeurs numériques et attribue une sélection aléatoire de LED actives à ce chiffre, le même nombre que la valeur numérique. Ceux-ci sont conservés dans un tableau. Une routine d'interruption prend une valeur de la table à la fois et les envoie aux puces du pilote LED, et une LED est allumée (en fait deux, une par puce). L'entrée suivante de la routine en obtient une autre et ainsi de suite. Lorsqu'elles sont exécutées suffisamment rapidement, les LED actives dans le tableau semblent toutes s'allumer en même temps. Vous pouvez modifier la synchronisation de la routine d'interruption pour la rendre plus rapide si vous le souhaitez. Amusez-vous bien, et si vous en faites quelque chose de cool, envoyez-moi une photo. Philip Pulle www.rgbsunset.com
Conseillé:
MINI ALIMENTATION PORTABLE MULTI TENSION AVEC USB, LAMPE DE POCHE, TESTEUR DE COMPOSANTS ET CHARGEUR INTÉGRÉ : 6 étapes
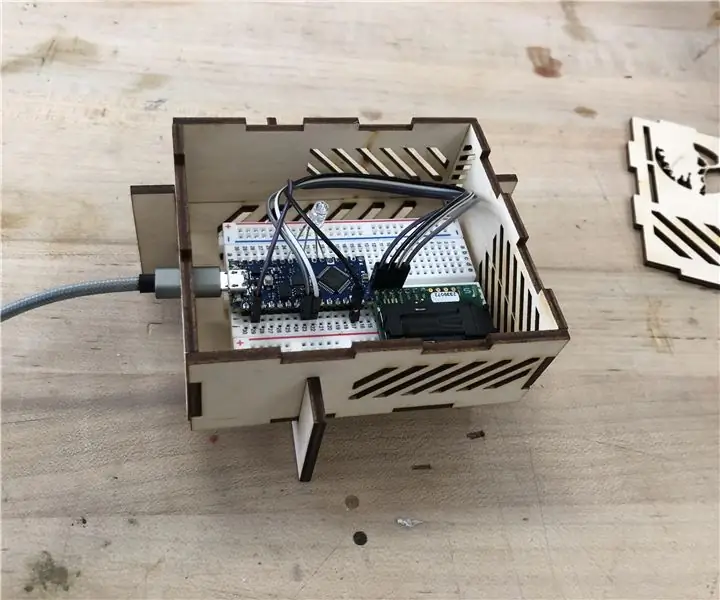
PORTABLE MINI MULTI VOLTAGE PSU AVEC USB, LAMPE DE POCHE, TESTEUR DE COMPOSANTS ET CHARGEUR INTÉGRÉ : Bienvenue dans mon premier instructable ! Avec cette instructable, vous êtes en mesure de transformer un powerbank solaire douteux/bon marché (avec quelques pièces supplémentaires) en quelque chose d'utile. Quelque chose que vous pouvez utiliser tous les jours, comme je le fais, parce que c'est vraiment super à utiliser ! La plupart des av
Mini oscilloscope CRT alimenté par batterie : 7 étapes (avec photos)
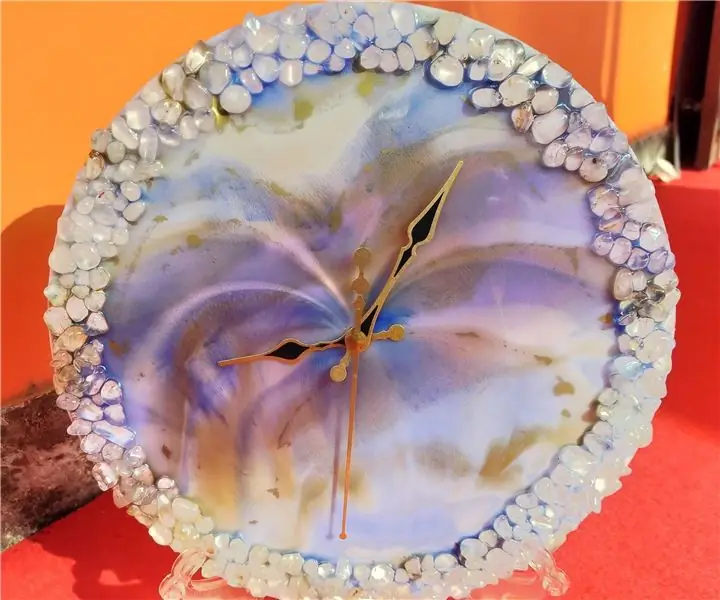
Mini oscilloscope CRT alimenté par batterie : Bonjour ! Dans ce Instructable je vais vous montrer comment faire un mini oscilloscope CRT alimenté par batterie. Un oscilloscope est un outil important pour travailler avec l'électronique; vous pouvez voir tous les signaux qui circulent dans un circuit et résoudre les problèmes
Comment créer un lecteur MP3 avec écran LCD à l'aide d'Arduino et du module de lecteur MP3 Mini DFPlayer : 6 étapes
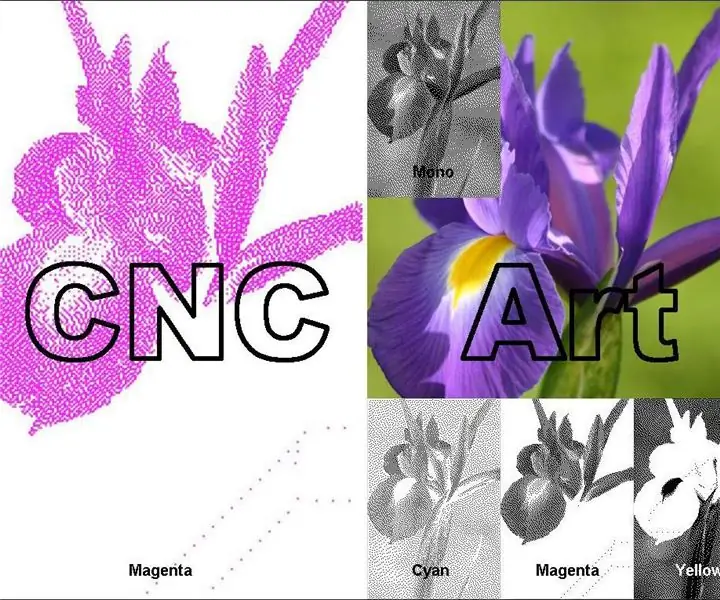
Comment créer un lecteur MP3 avec écran LCD à l'aide d'Arduino et du module de lecteur mini MP3 DFPlayer : Aujourd'hui, nous allons créer un lecteur MP3 avec écran LCD à l'aide d'Arduino et du module de lecteur mini MP3 DFPlayer. Le projet peut lire les fichiers MP3 sur la carte SD et peut faire une pause et jouez de la même manière que l'appareil il y a 10 ans. Et aussi il a la chanson précédente et la chanson suivante amusante
Mini haut-parleur recyclé : 7 étapes (avec photos)
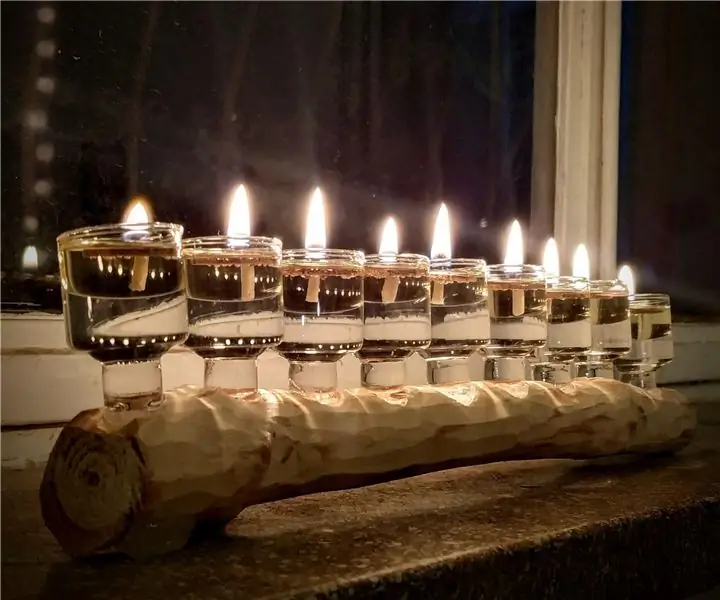
Mini haut-parleur recyclé : Salut les gars, c'est encore Matthias et aujourd'hui, nous fabriquons un mini haut-parleur recyclé. Le volume ne sera pas très fort car il n'a pas d'amplificateur mais vous pouvez toujours contrôler le volume avec un téléphone ou un ordinateur. S'amuser
DIY - Créez un mini système de haut-parleurs USB avec PAM8403 et carton - Vis en or : 5 étapes
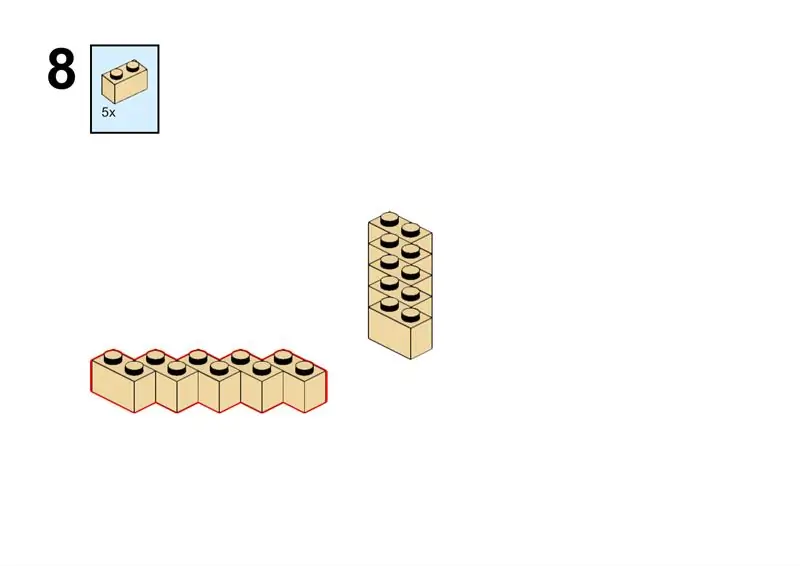
DIY - Créez un mini système de haut-parleurs USB avec PAM8403 et carton | Vis en or : aujourd'hui, je vais vous montrer comment créer un mini système de haut-parleurs USB avec un module amplificateur PAM8403 et du carton. C'est très facile avec des matériaux bon marché