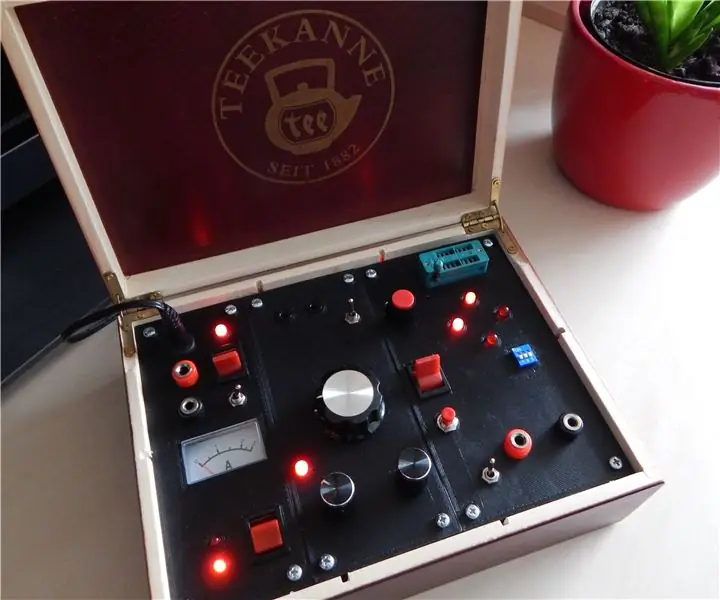
Table des matières:
- Étape 1: Théorie du contrôle CC et pas à pas
- Étape 2: schéma de circuit
- Étape 3: Schémas
- Étape 4: Composants et outils nécessaires
- Étape 5: Conception du panneau avant
- Étape 6: Impression 3D et peinture au pistolet
- Étape 7: Câblage du panneau
- Étape 8: Connecteurs de panneau
- Étape 9: PCB
- Étape 10: Arduino
- Étape 11: Assemblage et test
- Étape 12: Outro
2025 Auteur: John Day | [email protected]. Dernière modifié: 2025-01-23 14:45

Il y a quelques mois, un de mes amis m'a donné quelques imprimantes à jet d'encre et photocopieuses mises au rebut. J'étais intéressé par la récolte de leurs blocs d'alimentation, câbles, capteurs et surtout moteurs. J'ai récupéré ce que j'ai pu et je voulais tester toutes les pièces pour m'assurer qu'elles étaient fonctionnelles. Certains moteurs étaient évalués à 12 V, certains à 5 V, certains étaient des moteurs pas à pas et d'autres des moteurs à courant continu. Si seulement j'avais un appareil où je pourrais simplement connecter le moteur, régler la fréquence, le cycle de service et sélectionner une méthode pas à pas pour le tester.
J'ai décidé de le construire sans utiliser de processeur de signal numérique ni de microcontrôleur. L'humble 555 ou tl741 comme oscillateur, le compteur 4017 et de nombreuses portes logiques pour les modes de moteur pas à pas. Au début, je me suis beaucoup amusé à concevoir le circuit, ainsi qu'à concevoir le panneau avant de l'appareil. J'ai trouvé une boîte à thé en bois décente pour tout mettre à l'intérieur. J'ai divisé le circuit en quatre parties et j'ai commencé à le tester sur une maquette. Bientôt, les premiers signes de frustration sont apparus. C'était le bordel. Beaucoup de portes, beaucoup de circuits intégrés, de fils. Cela ne fonctionnait pas correctement et je réfléchissais entre deux options: Faire très simple - juste pour les moteurs à courant continu, ou le mettre de côté et le finir parfois plus tard… J'ai choisi la deuxième option.
Étape 1: Théorie du contrôle CC et pas à pas
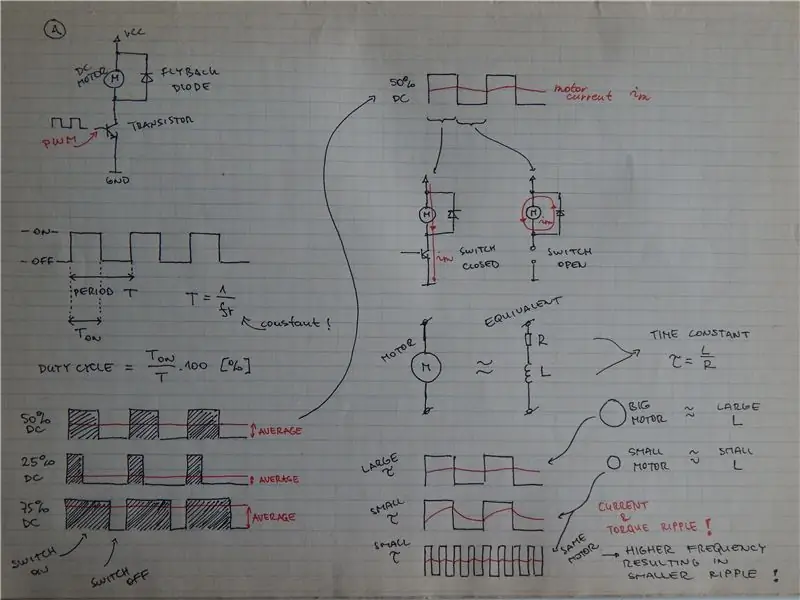
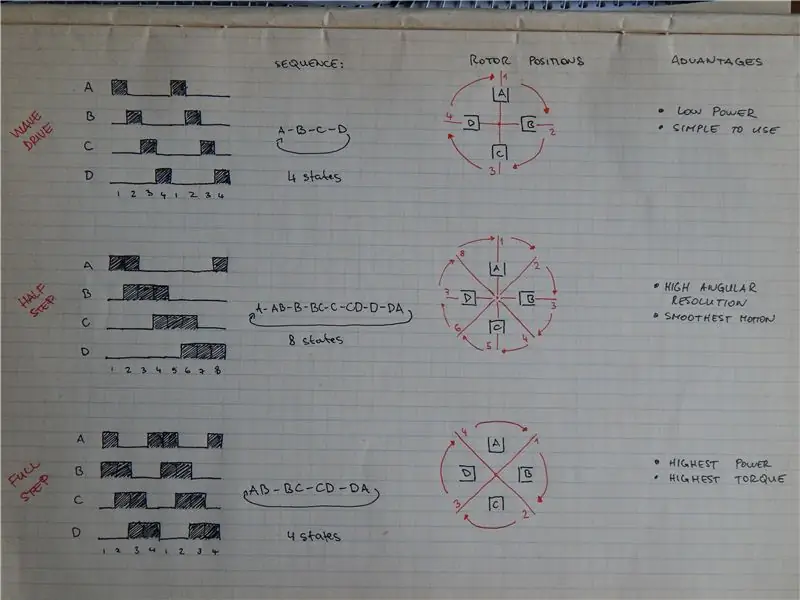
Docteur moteur
Le moyen le plus courant de contrôler un moteur à courant continu consiste à utiliser la modulation de largeur d'impulsion (PWM). PWM est appliqué à un interrupteur spécifique et allume et éteint le moteur. Sur l'image, vous pouvez voir la période de commutation indiquée et sa relation avec la fréquence, le temps de commutation est également indiqué. Le cycle de service est défini comme le temps de commutation divisé par la période totale. Si nous gardons la fréquence constante, la seule façon de changer le cycle de service est de changer le temps d'activation. En augmentant le rapport cyclique, la valeur moyenne de la tension appliquée au moteur augmente également. En raison de la tension plus élevée, un courant plus élevé traverse le moteur à courant continu et le rotor tourne plus rapidement.
Mais quelle fréquence choisir ? Pour répondre à cette question, examinons de plus près ce qu'est réellement un moteur à courant continu. De manière équivalente, il peut être décrit comme un filtre RL (négligeant EMF juste pour un instant). Si une tension est appliquée au moteur (filtre RL), le courant augmente avec une constante de temps tau égale à L / R. Dans le cas de la commande PWM, lorsque l'interrupteur est fermé, le courant circulant dans le moteur augmente et diminue pendant que l'interrupteur est éteint. À ce stade, le courant a le même sens qu'auparavant et traverse la diode flyback. Les moteurs de puissance plus élevée ont une inductance plus élevée et donc une constante de temps plus élevée que les moteurs plus petits. Si la fréquence est faible lorsque le petit moteur est alimenté, il y a une diminution rapide du courant pendant le temps d'arrêt, suivie d'une forte augmentation pendant le temps d'allumage. Cette ondulation de courant provoque également une ondulation du couple moteur. Nous ne voulons pas de cela. Par conséquent, lors de l'alimentation de moteurs plus petits, la fréquence PWM doit être plus élevée. Nous utiliserons ces connaissances dans la conception dans les étapes ultérieures.
Moteur pas à pas
Si nous voulons contrôler un moteur pas à pas unipolaire, utilisé dans l'électronique de loisir, nous avons le choix entre 3 options de contrôle de base (modes) - Wave drive (WD), Half Step (HS) et Full Step (FS). La séquence des modes individuels et la position du rotor sont indiquées sur la figure (pour simplifier, j'ai indiqué un moteur à deux paires de pôles). Dans ce cas, Wave Drive et Full Step font tourner le rotor de 90 degrés et peuvent être obtenus en répétant 4 états. En mode Half Step, nous avons besoin d'une séquence de 8 états.
Le choix du mode dépend des exigences du système - si nous avons besoin d'un couple important, le meilleur choix est Full Step, si un couple inférieur est suffisant et peut-être que nous alimentons notre circuit à partir de la batterie, le mode wave drive est préféré. Dans les applications où nous voulons obtenir la résolution angulaire la plus élevée et le mouvement le plus fluide, le mode Half Drive est un choix idéal. Le couple dans ce mode est environ 30 % inférieur à celui du mode Full Drive.
Étape 2: schéma de circuit
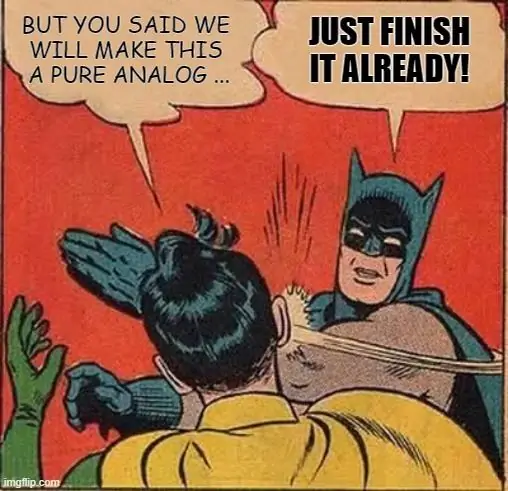
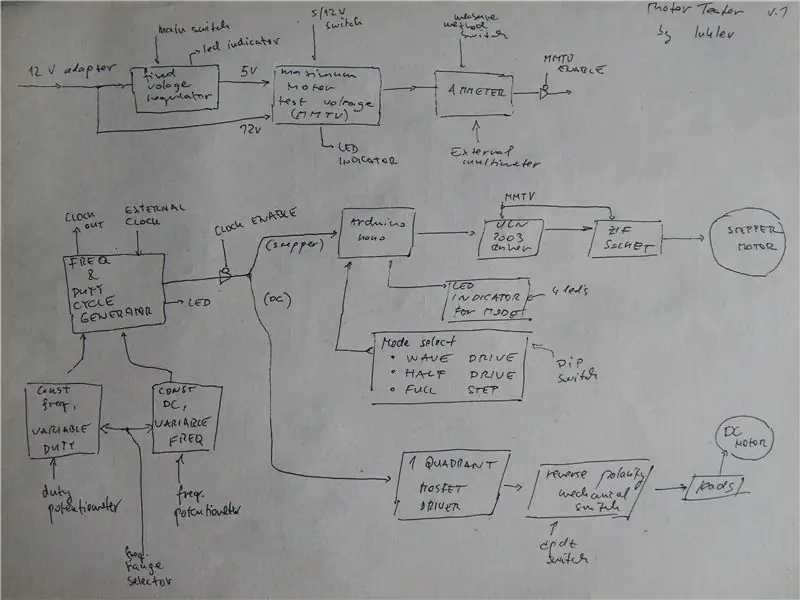
Ce mème simple décrit bien mon processus de réflexion lors de la conception.
La partie supérieure du schéma décrit l'alimentation - un adaptateur 12 volts, qui est réduit à 5 volts par un régulateur linéaire. Je voulais pouvoir choisir la tension de test maximale du moteur (MMTV) - soit 12 ou 5 volts. L'ampèremètre intégré contournera les circuits de commande et ne mesurera que le courant du moteur. Il serait également pratique de pouvoir basculer entre la mesure de courant interne et externe à l'aide d'un multimètre.
L'oscillateur fonctionnera selon deux modes: le premier est une fréquence constante et un rapport cyclique variable, et le second est une fréquence variable. Ces deux paramètres pourront être réglés à l'aide de potentiomètres, et un commutateur rotatif changera de mode et de plage. Le système comprendra également un commutateur entre l'horloge interne et externe via un connecteur jack 3,5 mm. L'horloge interne sera également connectée au panneau via une prise jack 3,5 mm. Un interrupteur et un bouton pour activer/désactiver l'horloge. Le pilote de moteur à courant continu sera un pilote mosfet à canal N à un seul quadrant. La direction sera modifiée à l'aide du commutateur mécanique dpdt. Les fils du moteur seront connectés via des prises bananes.
La séquence du moteur pas à pas sera contrôlée par un arduino, qui reconnaîtra également 3 modes de contrôle spécifiés par le commutateur DIP. Le pilote du moteur pas à pas sera uln2003. L'Arduino contrôlera également 4 LED qui représenteront l'animation des enroulements du moteur alimenté dans ces modes. Le moteur pas à pas sera connecté au testeur via une prise ZIF.
Étape 3: Schémas
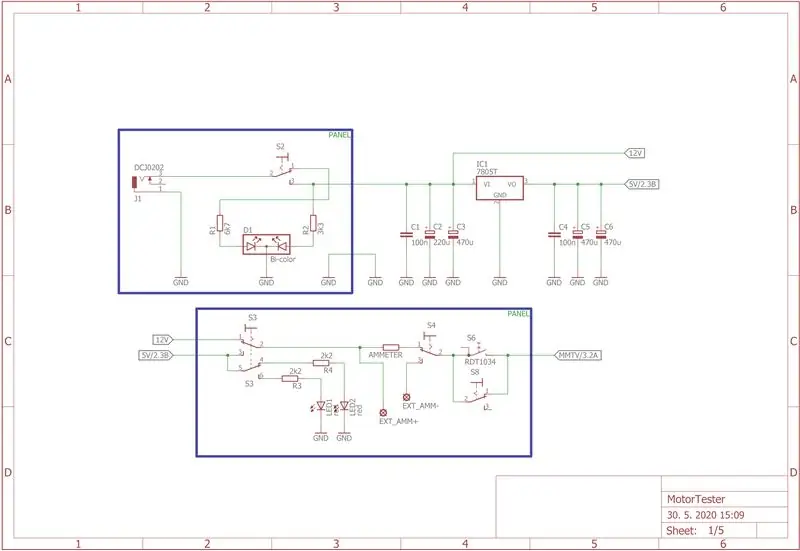
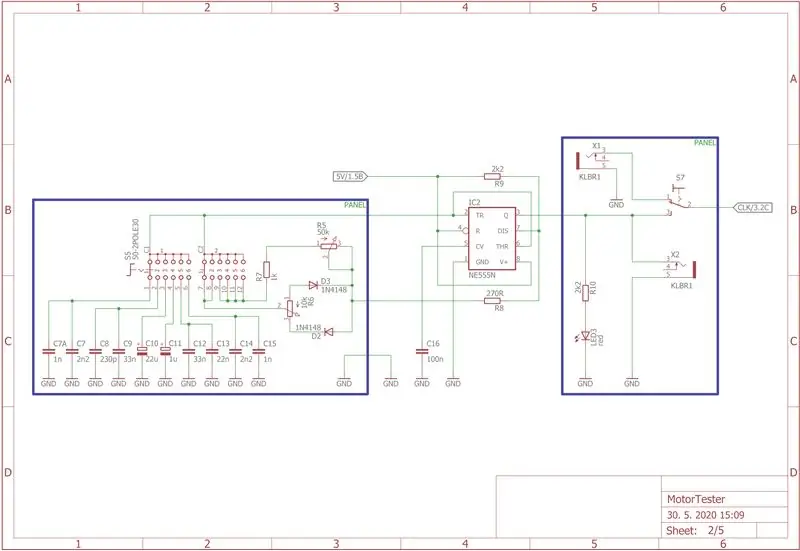
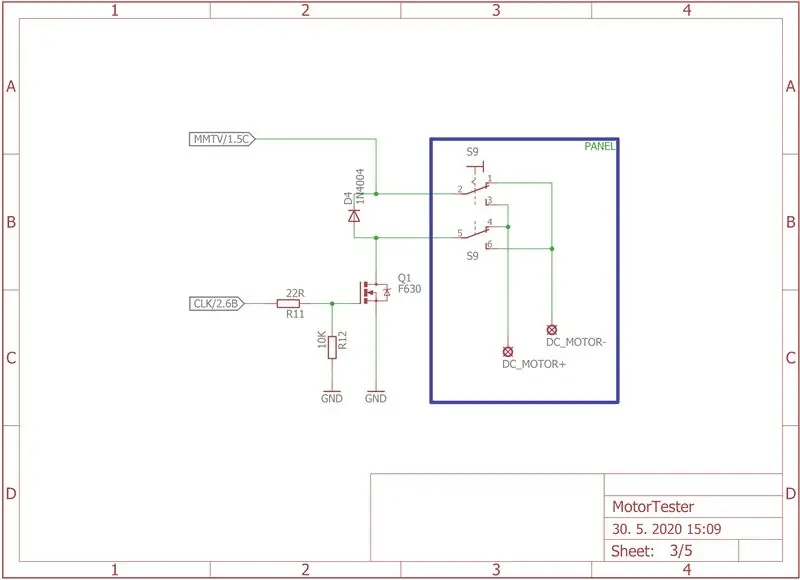
Les schémas sont divisés en cinq parties. Les circuits encadrés dans des cases bleues représentent les composants qui seront sur le panneau.
- Source de courant
- Oscillateur
- Pilote CC
- Pilote pas à pas Arduino
- Pilote pas à pas Logic Gates
Fiche n° 5 est la raison pour laquelle j'ai laissé ce projet mentir. Ces circuits forment des séquences pour les modes de contrôle mentionnés précédemment - WD, HS et FS. Cette partie est remplacée par arduino complètement dans la feuille nr. 4. Les schémas complets d'Eagle sont également joints.
Étape 4: Composants et outils nécessaires

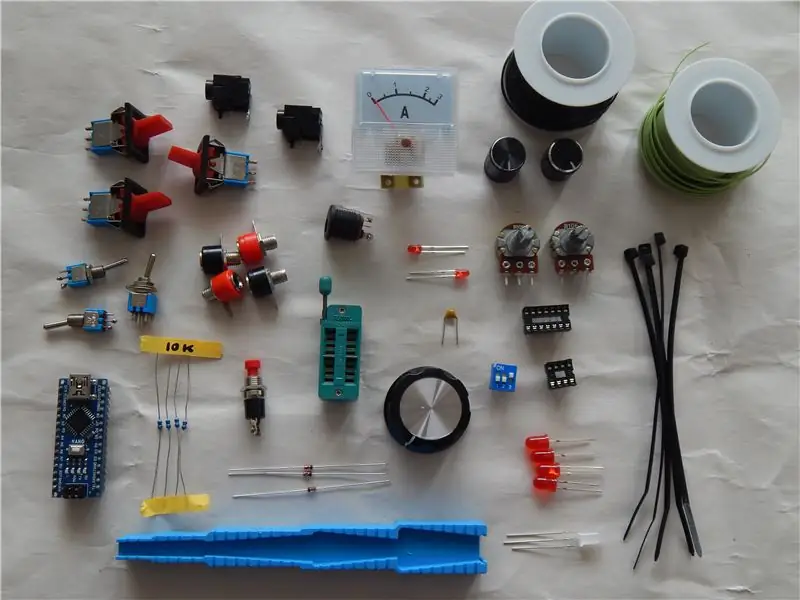
Composants et outils nécessaires:
- Multimètre
- Étrier
- Coupe-carton
- Marqueur
- Pince à épiler
- Pinces fines
- Pince coupante
- Pince à dénuder
- Fer à souder
- Souder
- Colophane
- Fils (24 awg)
- 4x interrupteur spdt
- 2x commutateur dpdt
- 4x prise banane
- Bouton poussoir
- Prise ZIF
- 2x jack 3,5 mm
- Connecteur CC
- Arduino nano
- Interrupteur DIP à 3 pôles
- 2x 3mm LED
- 5x5mm LED
- LED bicolore
- Boutons de potentiomètre
- Prises DIP
- PCB universel
- Connecteurs Dupont
- Attaches de câble en plastique
Et
- Potentiomètres
- Résistances
- Condensateurs
avec les valeurs que vous avez choisies, correspondant aux plages de fréquences et à la luminosité des LED.
Étape 5: Conception du panneau avant
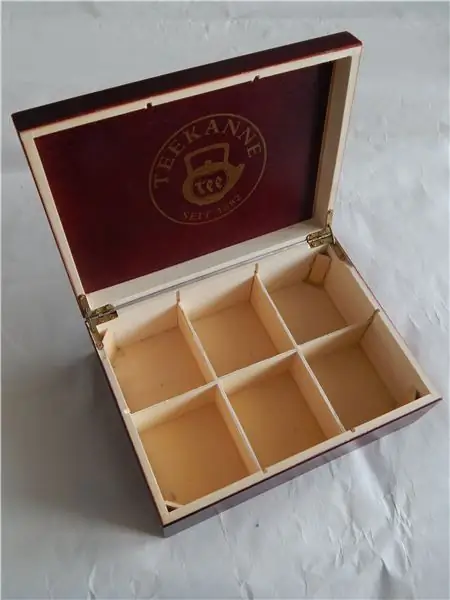
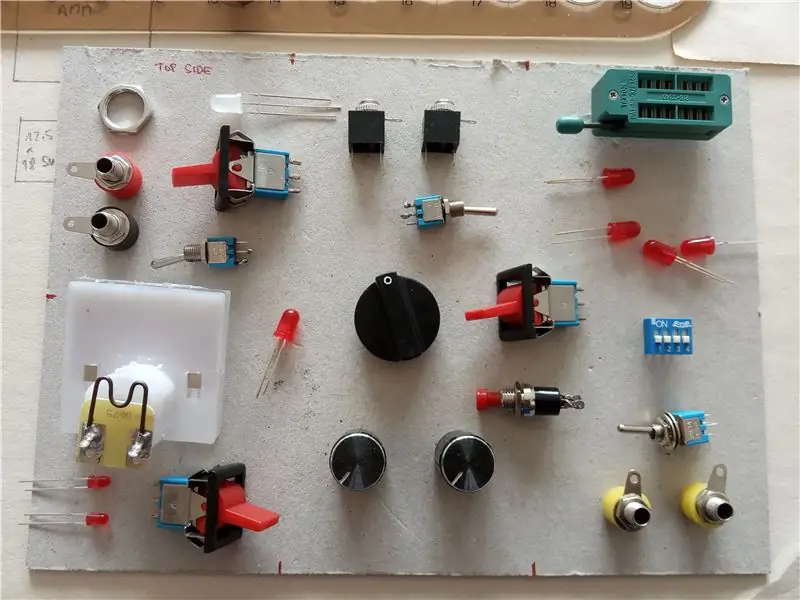
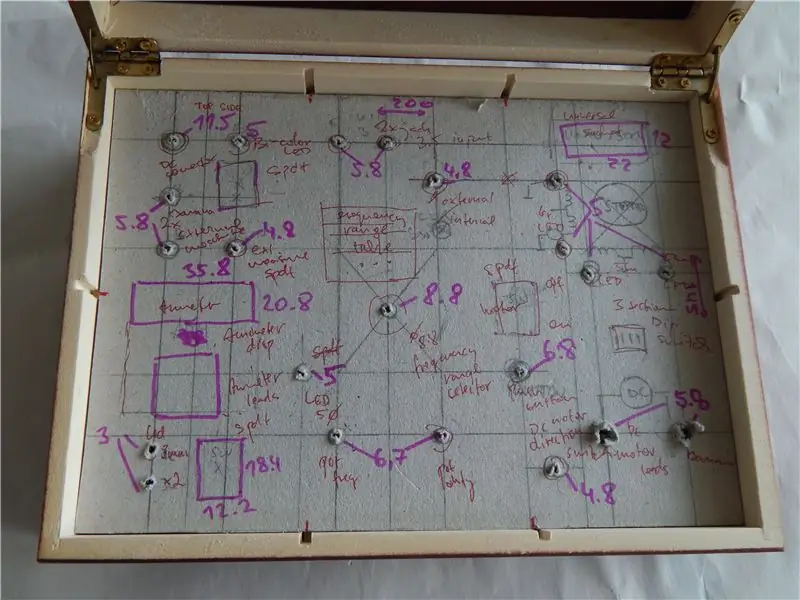
Le testeur a été placé dans une vieille boîte à thé en bois. J'ai d'abord mesuré les dimensions internes, puis j'ai découpé un rectangle dans du carton dur, qui a servi de gabarit pour le placement des composants. Lorsque j'étais satisfait du placement des pièces, j'ai mesuré à nouveau chaque position et créé une conception de panneau dans Fusion360. J'ai divisé le panneau en 3 parties plus petites, pour plus de simplicité dans l'impression 3D. J'ai également conçu un support en forme de L pour fixer les panneaux sur les côtés intérieurs de la boîte.
Étape 6: Impression 3D et peinture au pistolet
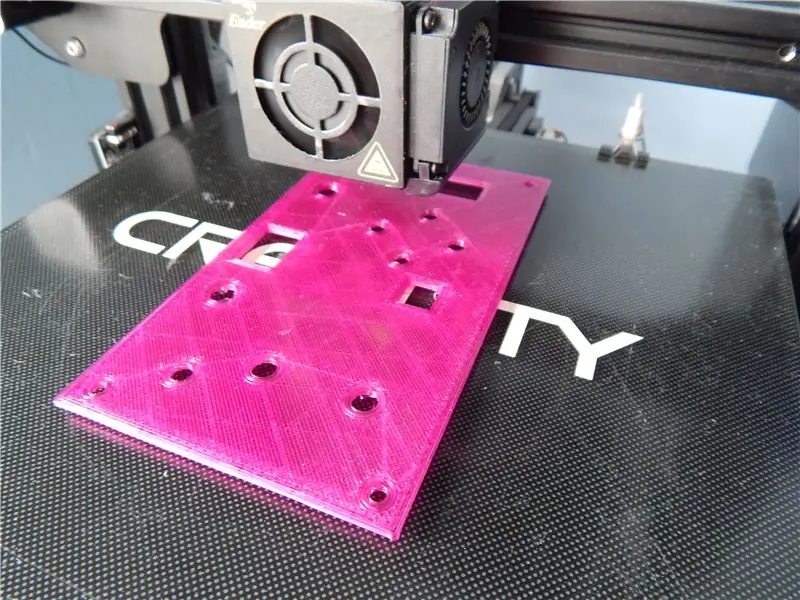
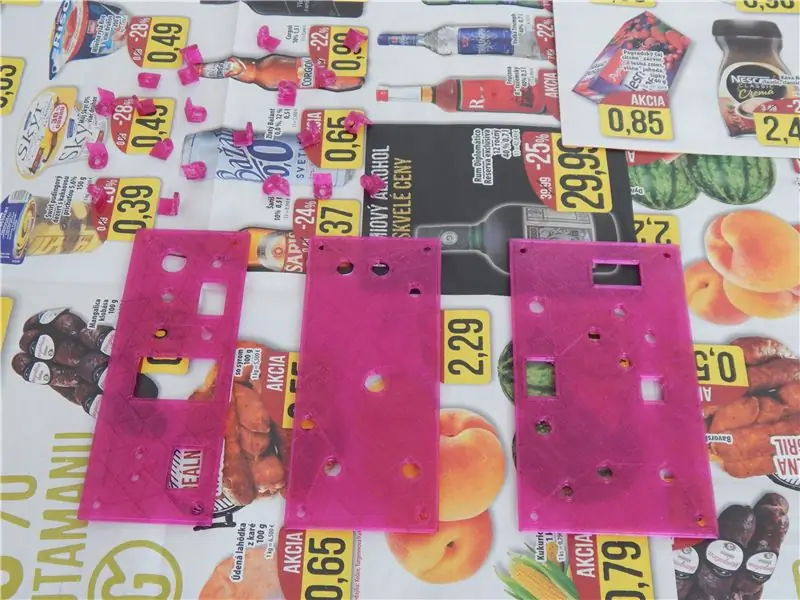
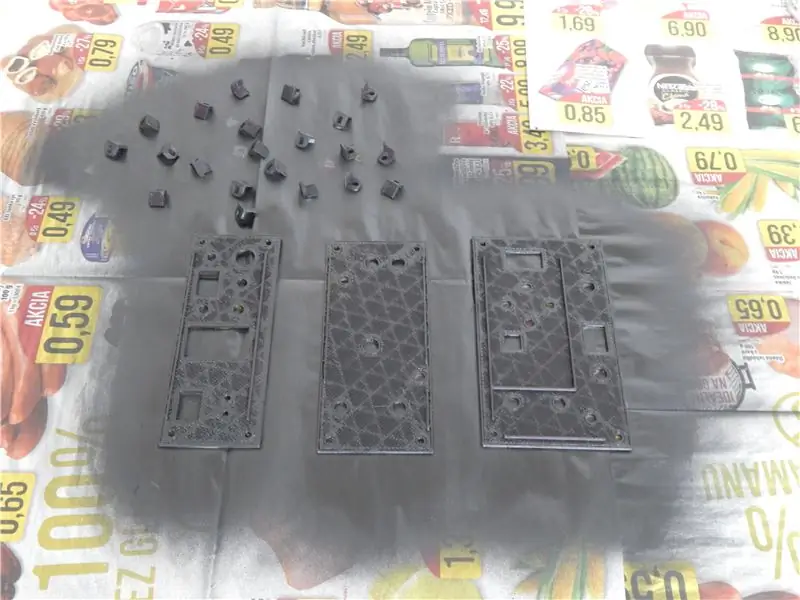
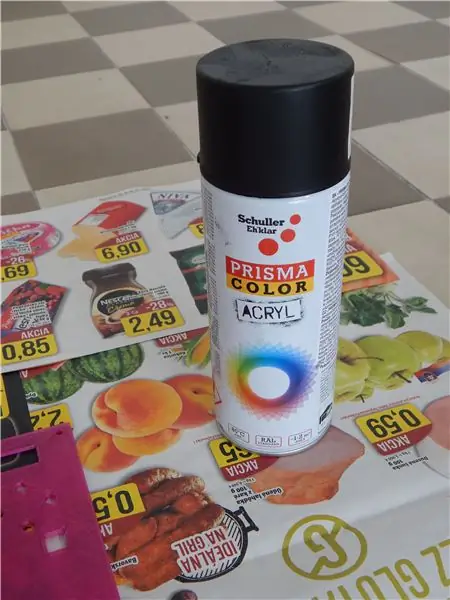
Les panneaux ont été imprimés à l'aide d'une imprimante Ender-3, à partir des matières résiduelles que j'avais à la maison. C'était un petg rose transparent. Après l'impression, j'ai pulvérisé les panneaux et les supports avec de la peinture acrylique noire mate. Pour une couverture complète, j'ai appliqué 3 couches, je les ai mises à l'extérieur pendant quelques heures pour sécher et aérer pendant environ une demi-journée. Attention, les vapeurs de peinture peuvent être nocives. Utilisez-les toujours uniquement dans une pièce aérée.
Étape 7: Câblage du panneau
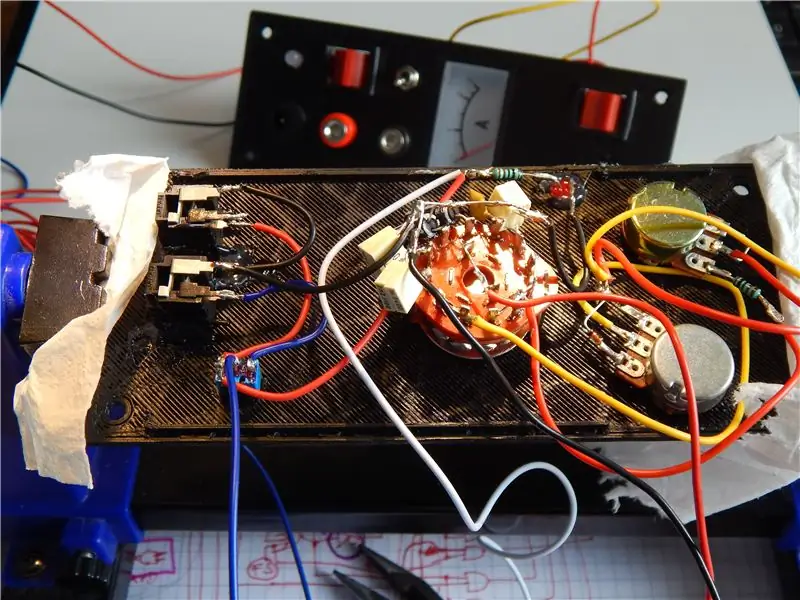
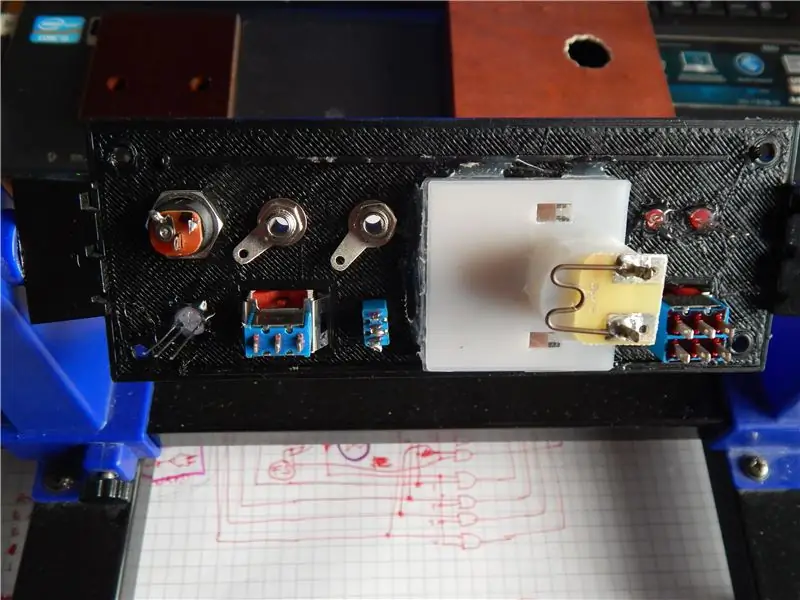
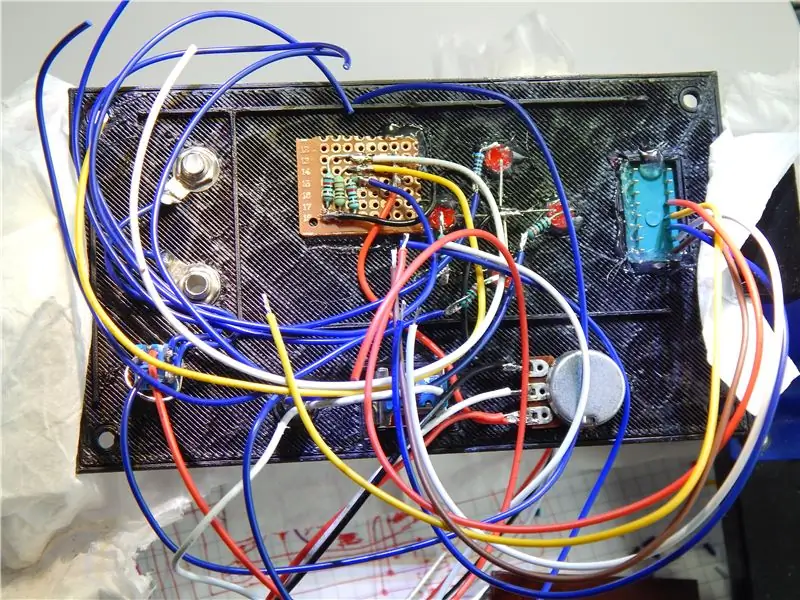
Personnellement, ma partie préférée, mais la plus longue (je m'excuse d'avance de ne pas avoir utilisé les tubes thermorétractables, j'étais pressé par le temps - sinon je les utiliserais certainement).
Les supports réglables aident beaucoup lors du montage et de la manipulation des panneaux. Il est également possible d'utiliser la troisième main, mais je préfère le titulaire. J'ai recouvert ses poignées d'une toile textile pour que le panneau ne se raye pas pendant le travail.
J'ai inséré et vissé tous les commutateurs et potentiomètres, LED et autres connecteurs dans le panneau. Par la suite, j'ai estimé la longueur des fils qui relieront les composants sur le panneau et aussi ceux qui serviront à se connecter au PCB. Ceux-ci ont tendance à être un peu plus longs et il est bon de les étendre un peu.
J'utilise presque toujours un flux de soudure liquide pour souder des connecteurs. J'en applique une petite quantité sur la broche, puis je l'étain et je la connecte au fil. Le flux élimine tout métal oxydé des surfaces, ce qui facilite beaucoup la soudure du joint.
Étape 8: Connecteurs de panneau
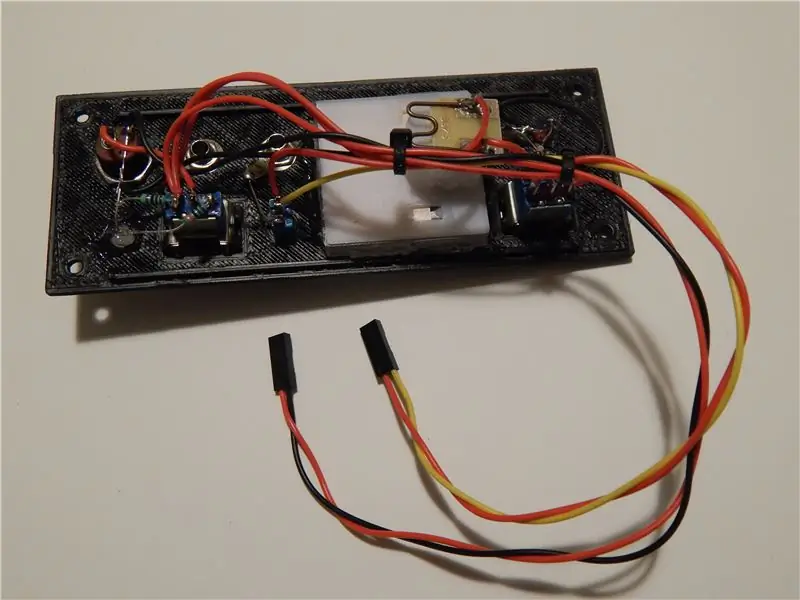
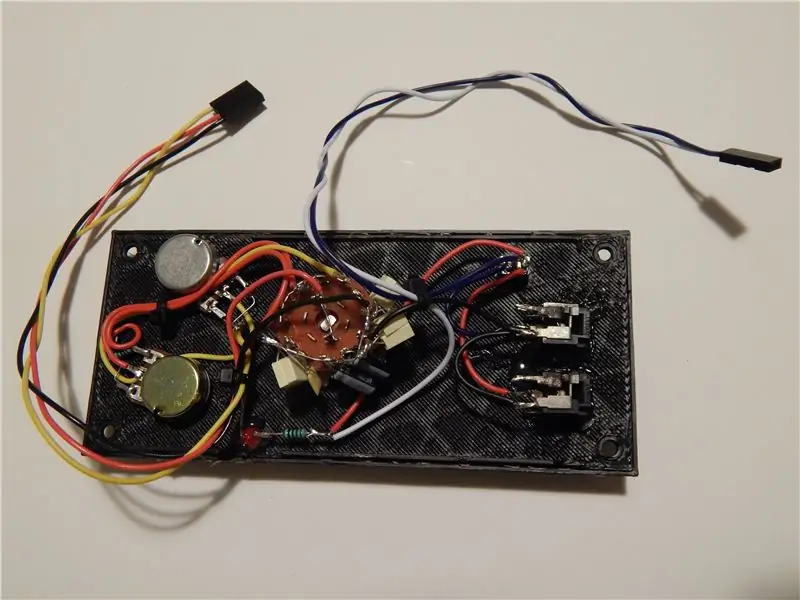
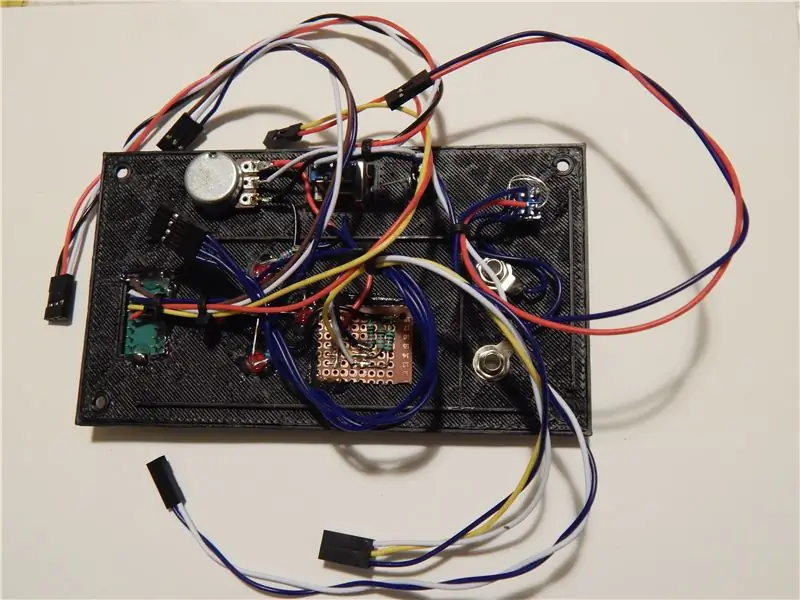
Pour connecter le panneau au pcb, j'ai utilisé des connecteurs de type dupont. Ils sont largement disponibles, bon marché et, surtout, suffisamment petits pour tenir confortablement dans la boîte choisie. Les câbles sont disposés selon le schéma, par paires, triplets ou quadruplets. Ils sont codés par couleur pour être facilement identifiés et faciles à connecter. Dans le même temps, il est pratique pour l'avenir de ne pas se perdre dans un enchevêtrement uniforme de fils. Enfin, ils sont fixés mécaniquement avec des serre-câbles en plastique.
Étape 9: PCB
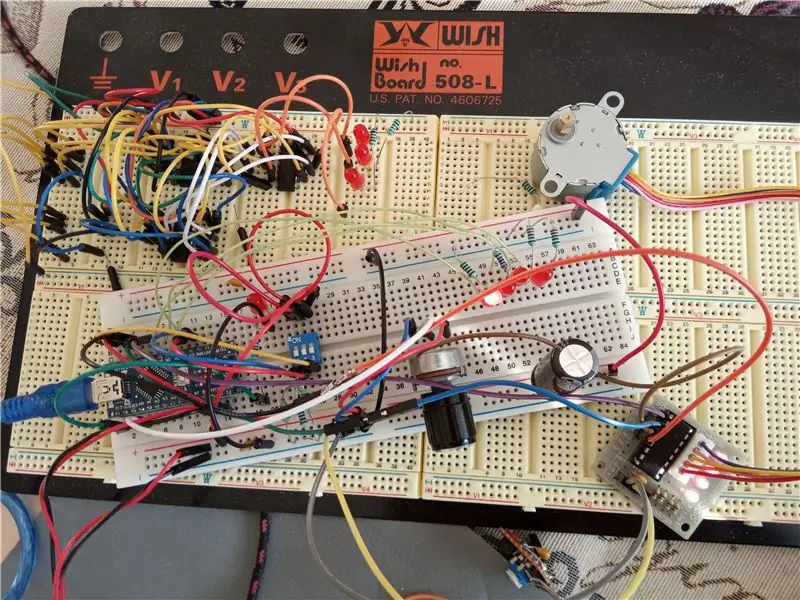
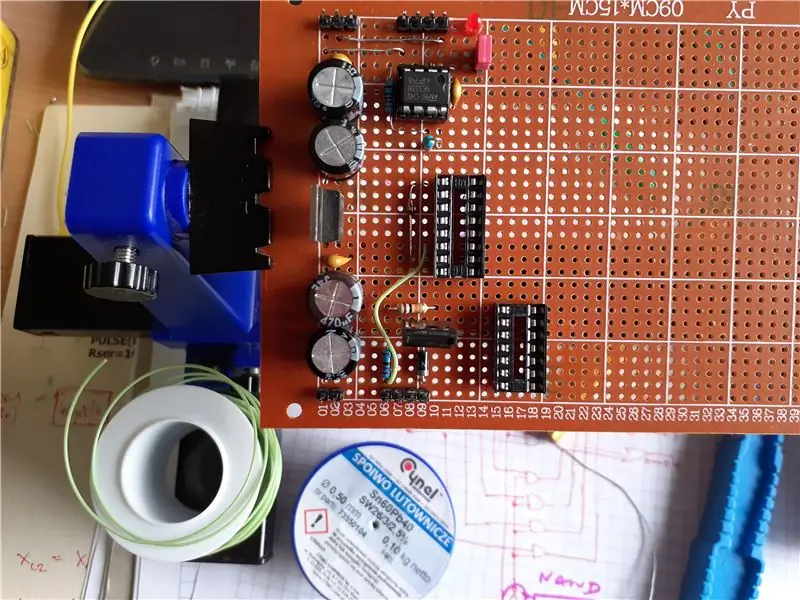
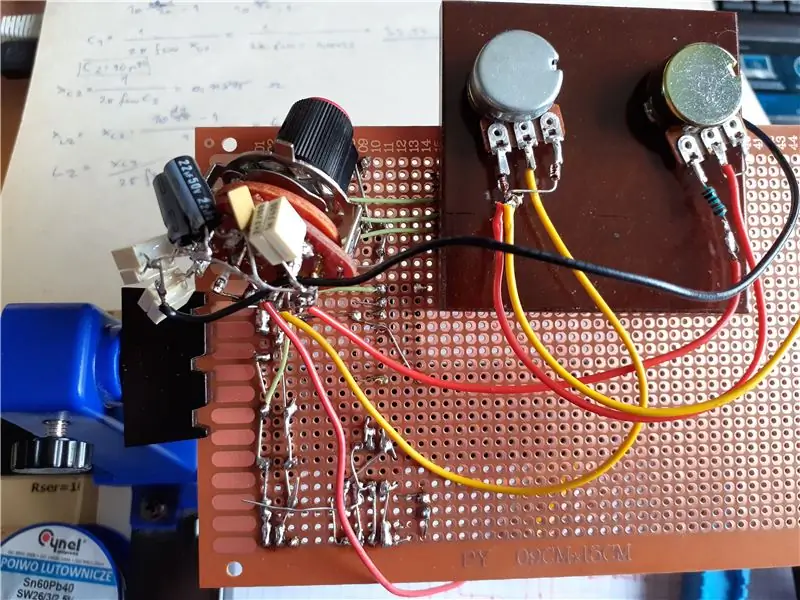
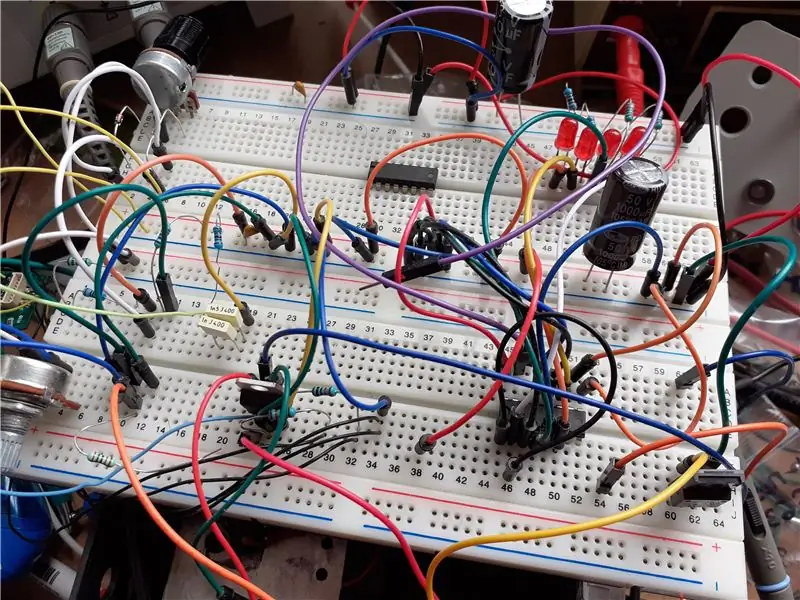
Comme la partie du schéma qui se trouve à l'extérieur du panneau n'est pas étendue, j'ai décidé de faire un circuit sur un circuit imprimé universel. J'ai utilisé un circuit imprimé standard de 9x15 cm. J'ai placé les condensateurs d'entrée avec le régulateur linéaire et le dissipateur thermique sur le côté gauche. Par la suite, j'ai installé des sockets pour le compteur IC 555, 4017 et le pilote ULN2003. La prise pour le compteur 4017 restera vide car sa fonction est prise en charge par arduino. Dans la partie inférieure se trouve un pilote pour le mosfet F630 à canal N.
Étape 10: Arduino
La connexion du système avec arduino est documentée dans la feuille de schémas nr. 4. la disposition suivante des broches a été utilisée:
- 3 entrées numériques pour commutateur DIP - D2, D3, D12
- 4 sorties numériques pour indicateurs LED - D4, D5, D6, D7
- 4 sorties numériques pour pilote pas à pas - D8, D9, D10, D11
- Une entrée analogique pour potentiomètre - A0
Les indicateurs LED qui représentent les enroulements individuels du moteur s'allument lentement au fur et à mesure que les enroulements sont réellement alimentés. Si la vitesse de clignotement des LED correspondait aux enroulements du moteur, nous la verrions comme un éclairage continu de chacun d'eux. Je voulais obtenir une représentation simple et claire et des différences entre les modes individuels. Par conséquent, les indicateurs LED sont contrôlés indépendamment à des intervalles de 400 ms.
Les fonctions de contrôle du moteur pas à pas ont été créées par l'auteur Cornelius sur son blog.
Étape 11: Assemblage et test
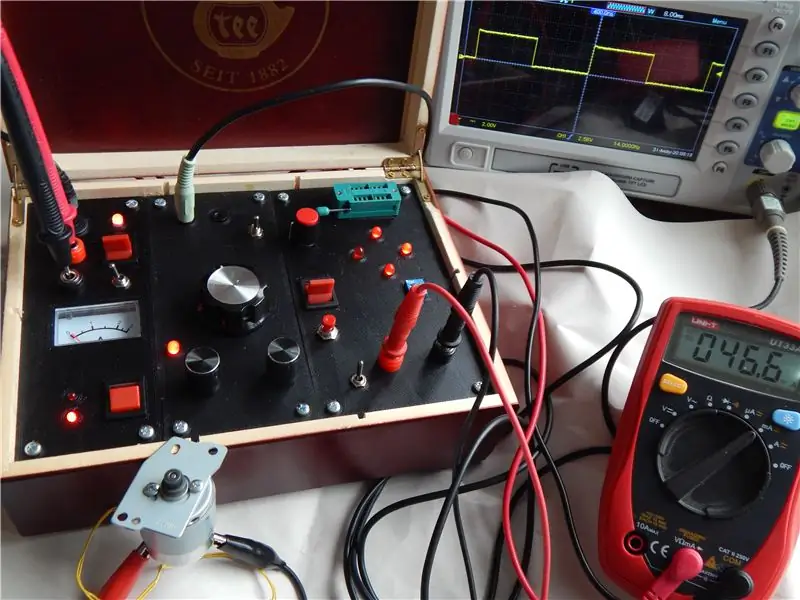
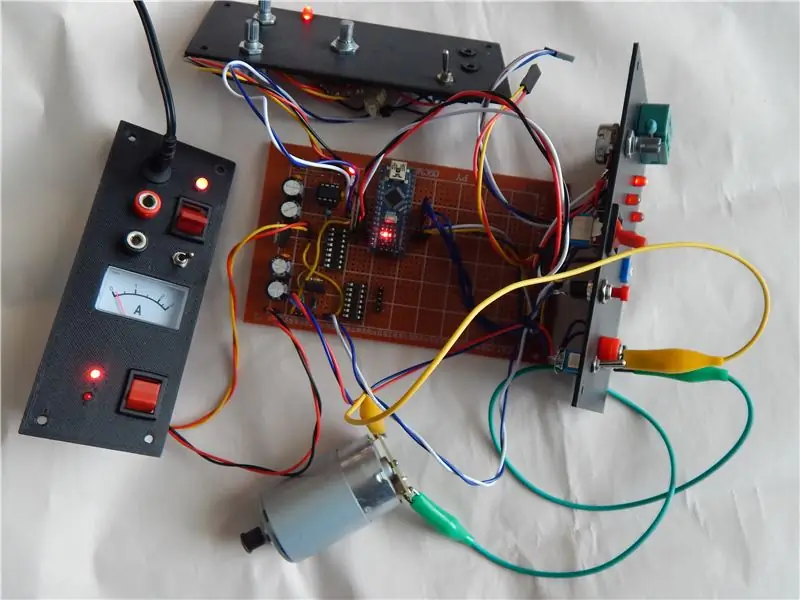
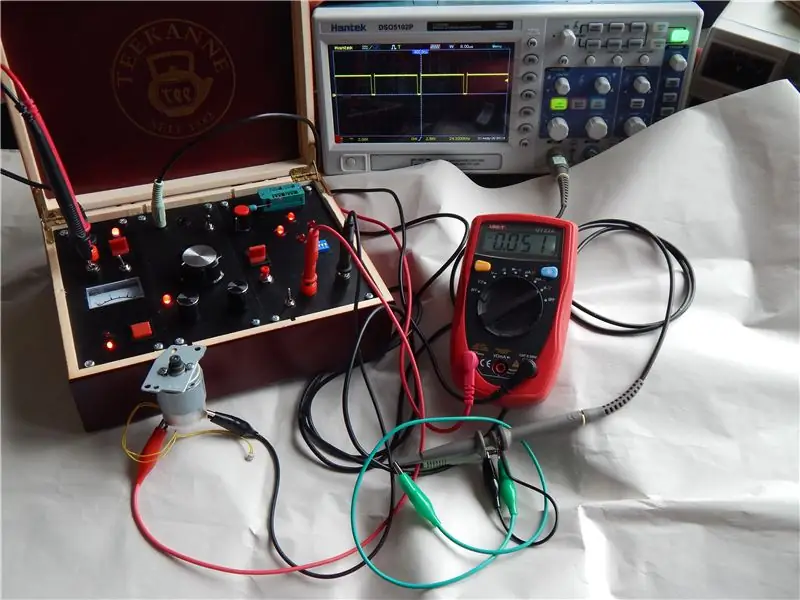
Enfin, j'ai connecté tous les panneaux au circuit imprimé et j'ai commencé à tester le testeur. J'ai mesuré l'oscillateur et ses plages avec un oscilloscope, ainsi que le contrôle de la fréquence et du rapport cyclique. Je n'ai pas eu de gros problèmes, le seul changement que j'ai fait était d'ajouter des condensateurs céramiques en parallèle aux condensateurs électrolytiques d'entrée. Le condensateur ajouté permet d'atténuer les interférences haute fréquence introduites dans le système par des éléments parasites du câble adaptateur CC. Toutes les fonctions du testeur fonctionnent selon les besoins.
Étape 12: Outro
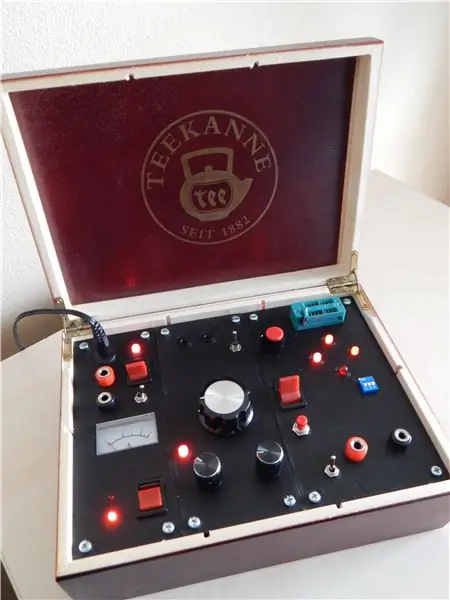
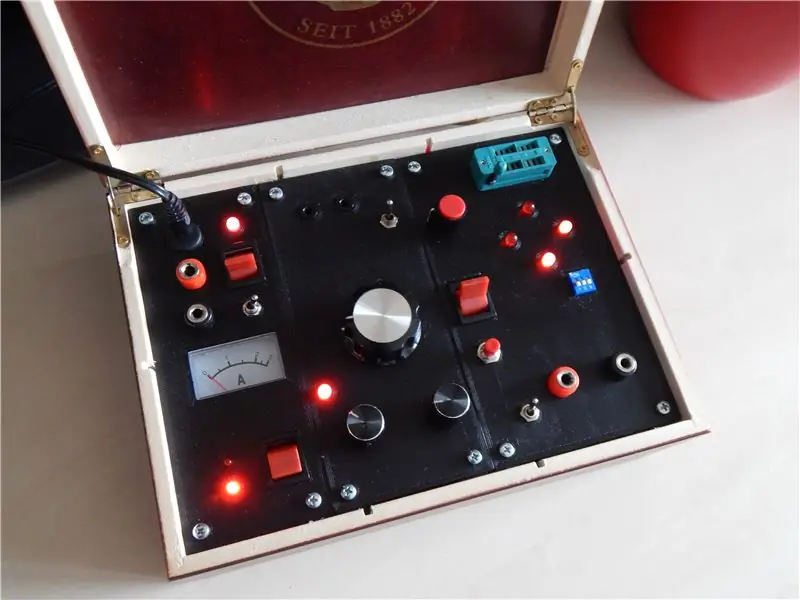
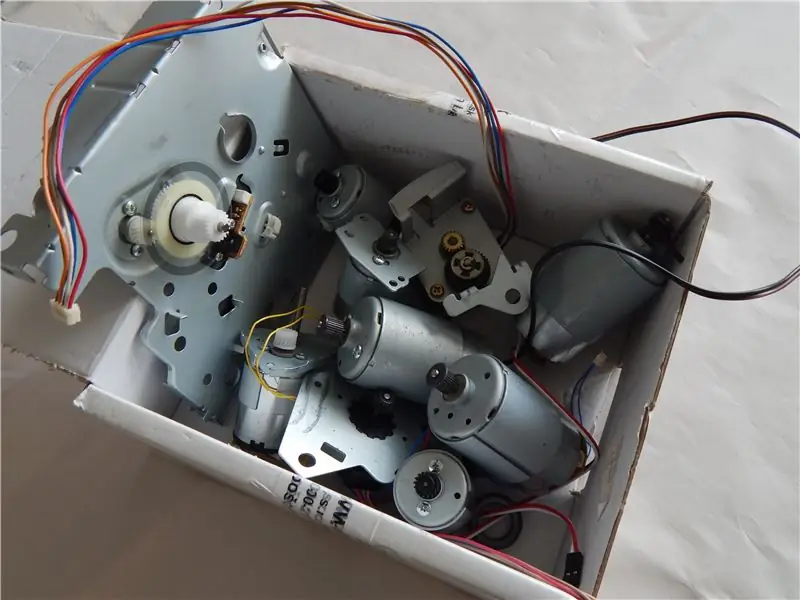
Maintenant, je peux enfin tester simplement tous les moteurs que j'ai réussi à récupérer au fil des ans.
Si vous êtes intéressé par la théorie, le schéma ou quoi que ce soit à propos du testeur, n'hésitez pas à me contacter.
Merci pour votre lecture et votre temps. Restez en bonne santé et en sécurité.
Conseillé:
Expériences PWM de moteurs à courant continu aléatoires + Dépannage de l'encodeur : 4 étapes
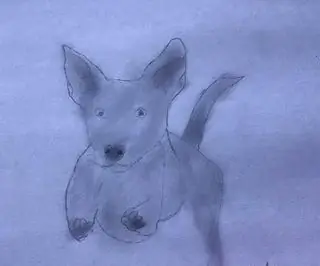
Expériences PWM de moteurs à courant continu aléatoires + Dépannage de l'encodeur : Il y a souvent des moments où les déchets de quelqu'un sont le trésor d'un autre, et ce fut l'un de ces moments pour moi. Si vous m'avez suivi, vous savez probablement que j'ai entrepris un énorme projet pour créer ma propre imprimante 3D CNC à partir de ferraille. Ces pièces étaient
Moteur pas à pas contrôlé par moteur pas à pas - Moteur pas à pas en tant qu'encodeur rotatif : 11 étapes (avec photos)
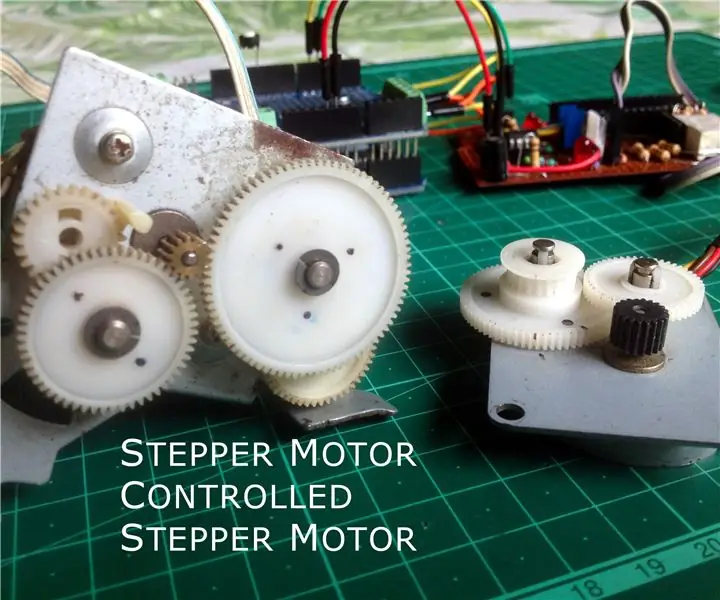
Moteur pas à pas contrôlé par moteur pas à pas | Moteur pas à pas en tant qu'encodeur rotatif : Vous avez quelques moteurs pas à pas qui traînent et vous voulez faire quelque chose ? Dans ce Instructable, utilisons un moteur pas à pas comme encodeur rotatif pour contrôler la position d'un autre moteur pas à pas à l'aide d'un microcontrôleur Arduino. Alors sans plus tarder, allons-y
Contrôle des moteurs à courant continu avec Arduino et L293 : 5 étapes (avec photos)
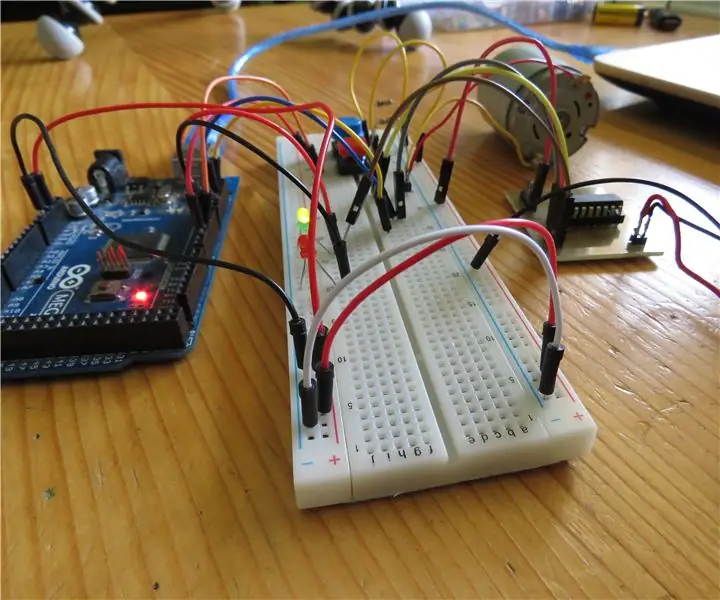
Contrôle des moteurs à courant continu avec Arduino et L293 : un moyen facile de contrôler les moteurs à courant continu.Tout ce dont vous avez besoin, c'est de connaissances en électronique et en programmation Si vous avez des questions ou des problèmes, vous pouvez me contacter sur mon courrier : [email protected] ma chaîne YouTube : https ://www.youtube.com/channel/UCuS39O01OyP
Conduite de moteurs à courant continu à l'aide d'un pont en H : 9 étapes
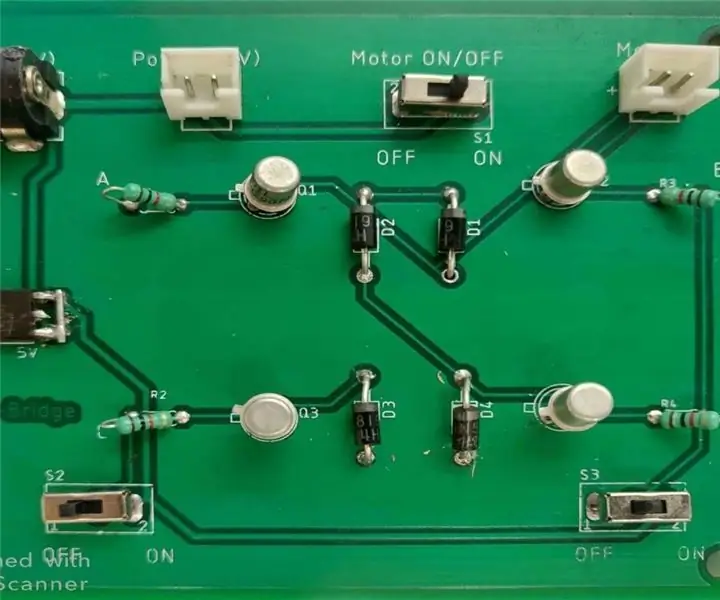
Conduite de moteurs à courant continu à l'aide d'un pont en H : Bonjour les gars ! Dans ce instructable, je vais vous montrer comment construire un pont en H - un circuit électronique simple qui nous permet d'appliquer une tension pour charger dans les deux sens. Il est couramment utilisé dans les applications robotiques pour contrôler les moteurs à courant continu. En utilisant H Brid
Contrôle des moteurs à courant continu avec le L298N à l'aide du microcontrôleur CloudX : 3 étapes
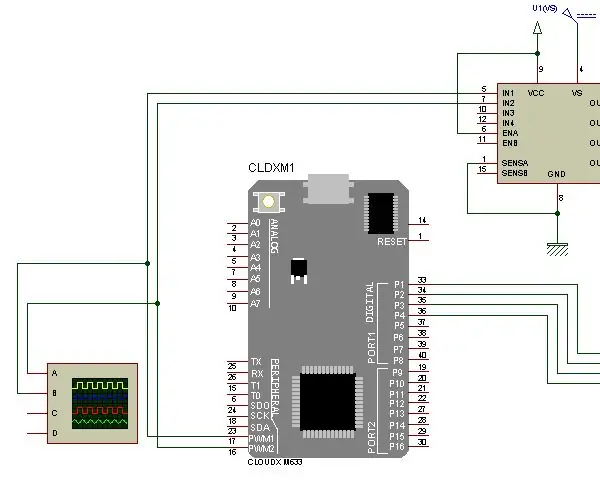
Contrôle des moteurs à courant continu avec le L298N à l'aide du microcontrôleur CloudX : Dans ce projet, nous expliquerons comment utiliser notre pont en H L298N pour augmenter et diminuer la vitesse du moteur à courant continu. Le module pont en H L298N peut être utilisé avec des moteurs ayant une tension comprise entre 5 et 35 V CC. Il existe également un régulateur 5 V intégré, donc si votre