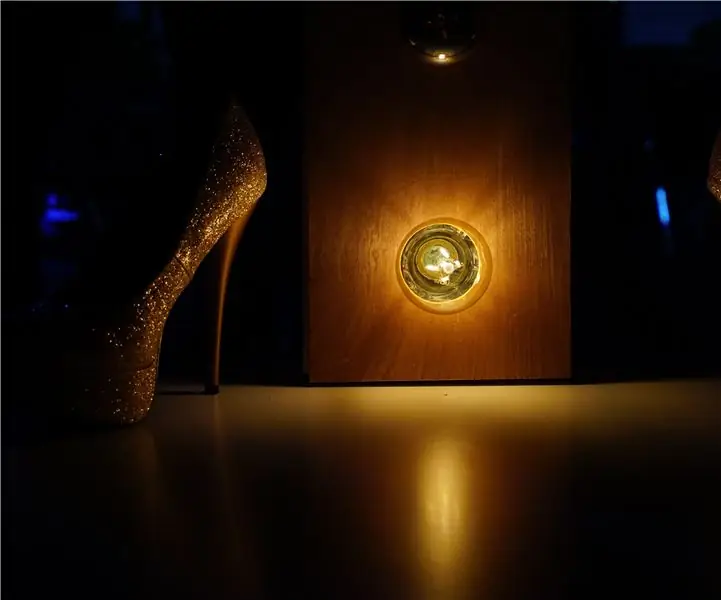
Table des matières:
- Fournitures
- Étape 1: Circuit 5V: Arduino
- Étape 2: Conception de la boîte
- Étape 3: Construire la boîte
- Étape 4: Installation des douilles dans la boîte
- Étape 5: Souder l'électronique basse tension
- Étape 6: Connexion des composants 220V
- Étape 7: Snappers magnétiques (facultatif)
- Étape 8: Ce que je ferais différemment
2025 Auteur: John Day | [email protected]. Dernière modifié: 2025-01-23 14:45
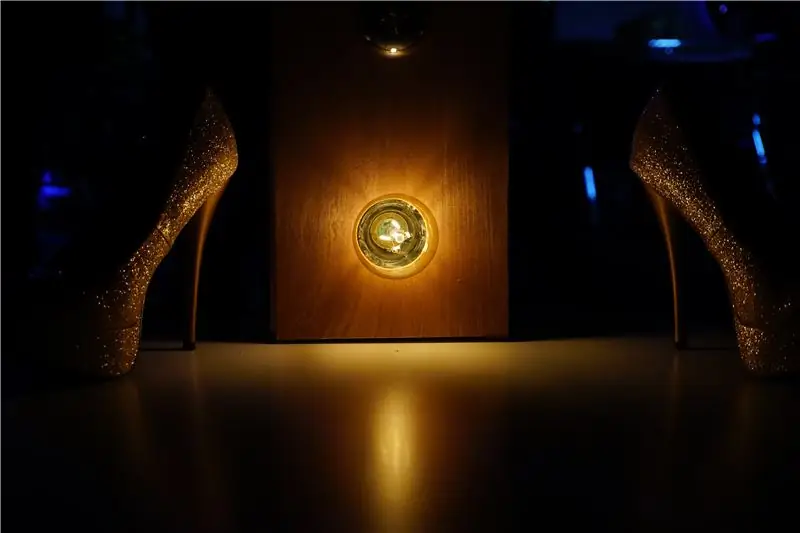
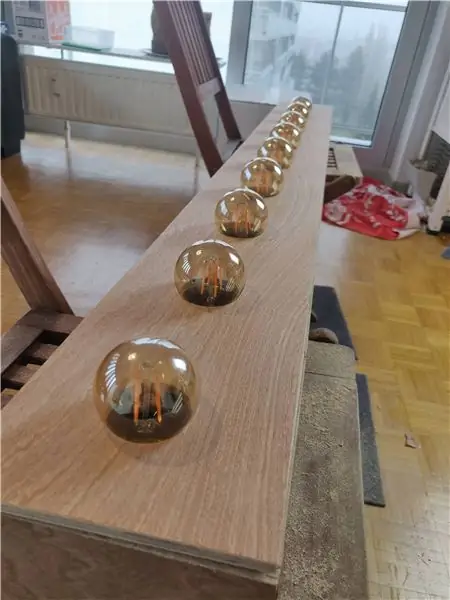
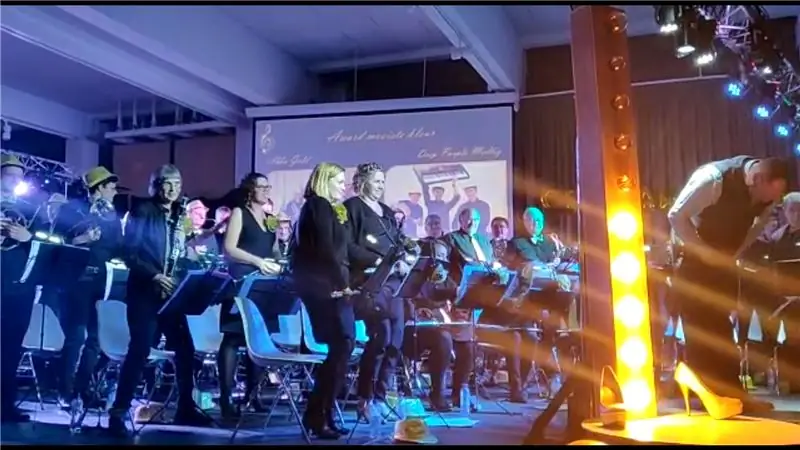
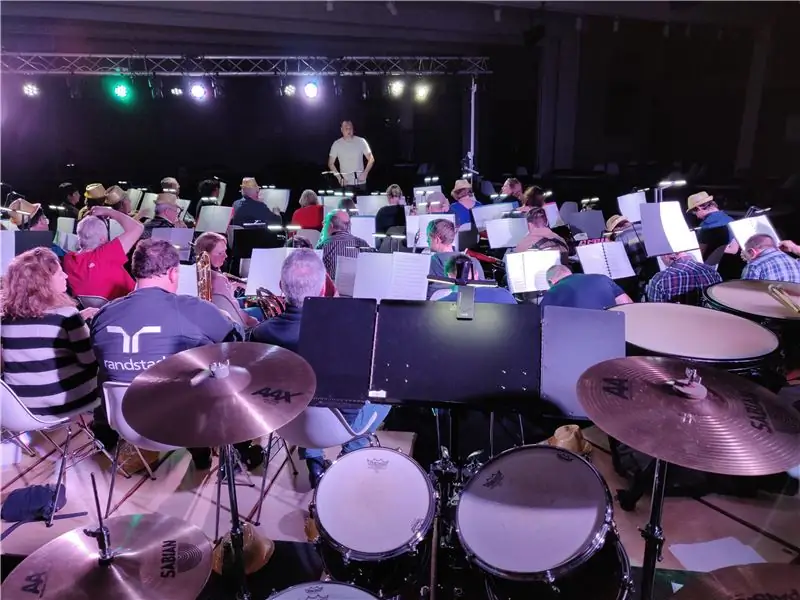
Depuis quelque part vers l'année 2001, j'ai commencé à prendre des cours de batterie. Après dix ans, en 2011, j'ai rejoint mon premier orchestre de concert et j'en suis devenu accro. Faire de la musique ensemble et jouer à un concert est exaltant. Maintenant, je suis dans un autre orchestre depuis déjà plus de 5 ans. Nous avons deux concerts par an et plusieurs commandes en parallèle.
Comme thème de notre concert du nouvel an, nous voulions organiser une cérémonie de remise des prix pour les meilleures chansons que nous avons jouées. La configuration était que nous jouions deux chansons dans chaque catégorie. Par exemple "Ice versus fire" pour lequel nous avons joué un medley de "Frozen" et un de "How to train your dragon". Le public devrait ensuite voter pour la meilleure chanson, qui recevrait ensuite un prix imprimé en 3D personnalisé.
Lors du brainstorming pendant les préparatifs, nous avons eu beaucoup d'idées sur la façon de faire voter le public, des votes papier aux applications. Mais toutes ces suggestions nécessitent l'arrêt du spectacle pour chaque récompense, tout en distrayant sérieusement le public. Lorsqu'un compteur d'applaudissements a été suggéré, nous savions tous que nous avions atteint l'or. Mais certaines recherches en ligne n'ont révélé aucune véritable solution prête à l'emploi. Alors je me suis courageusement levé, je me suis déclaré fabricant novice et j'ai affirmé que je pouvais facilement en construire un à partir de zéro pour un budget plutôt petit.
Oh mon Dieu, je n'étais pas préparé au terrier de lapin dans lequel je tomberais.
Fournitures
Outils
- Votre perceuse sans fil préférée
- Foret circulaire et autres bits
- tournevis
- Imprimante 3D (en option)
Cas
- Contre-plaqué. (J'ai choisi un multiplex de 8 mm mais avec le recul j'aurais dû opter pour du 12 mm ou même plus épais)
- 4 X loquet de porte magnétique (facultatif avec le recul)
- Des vis
Électronique (5V)
- Arduino Nano
- Amplificateur de microphone à électret - MAX4466 avec gain réglable (ou similaire, selon vos besoins)
- Module de relais 2 X 5V 8 canaux
- Transformateur 220V à 5V
- fils, beaucoup de courts, et un fil à quatre brins de plusieurs mètres pour le contrôle 'à distance'
- deux interrupteurs
Électronique (220V)
- câbles électriques standard (les restes de la construction de la maison sont idéaux, mais mieux flexibles)
- Prise de courant alternatif avec fusible (facultatif mais fortement recommandé)
- Ampoules de votre choix
- Douilles d'ampoules
Étape 1: Circuit 5V: Arduino
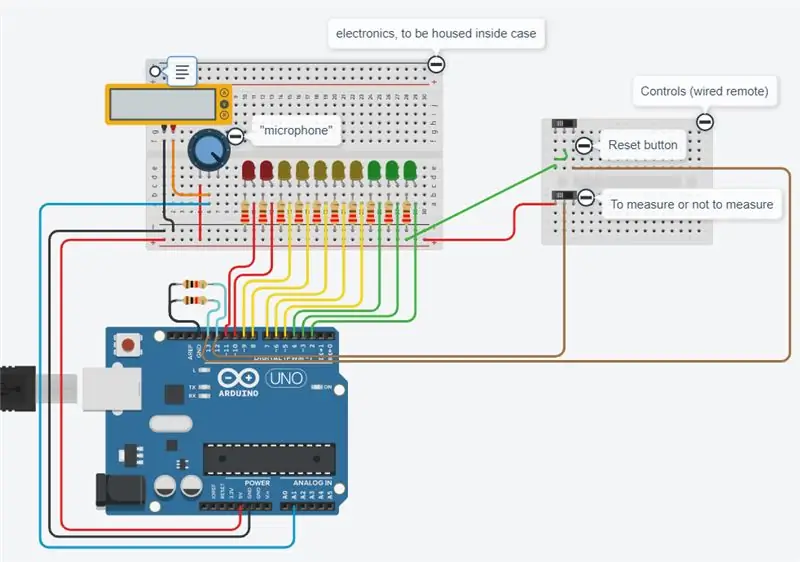
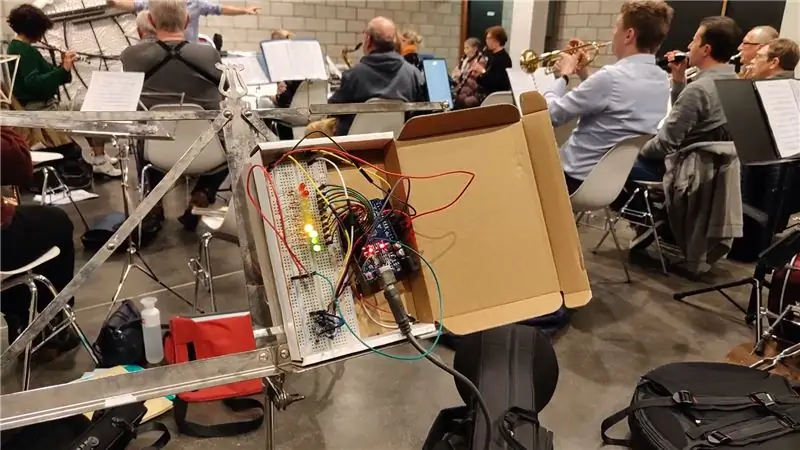
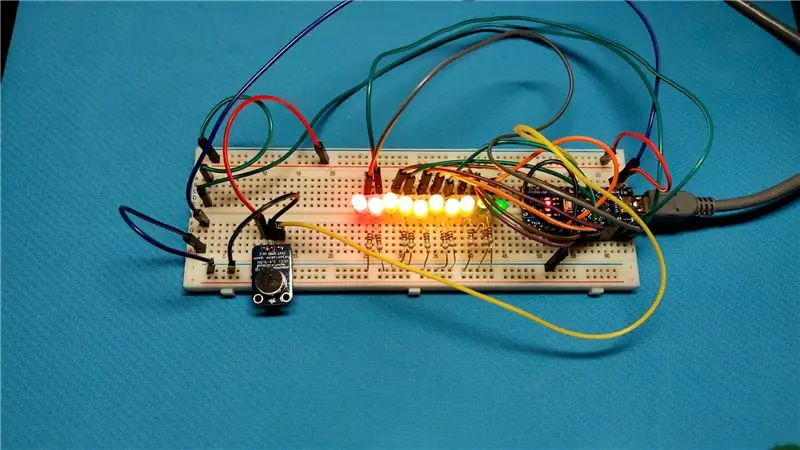
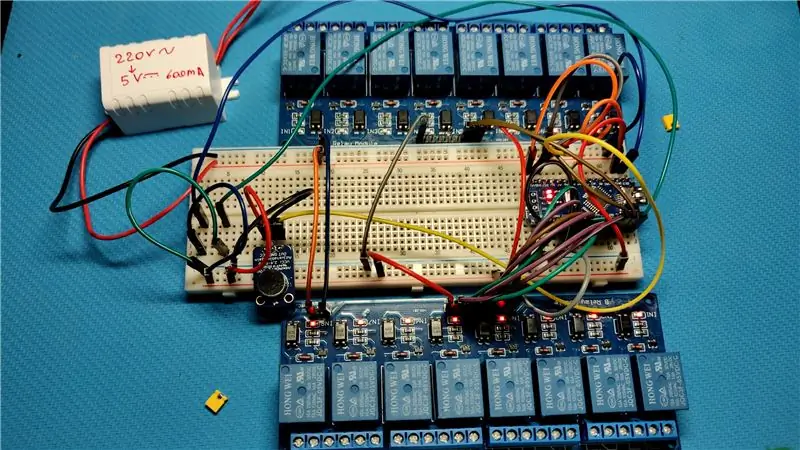
Il y a trois parties principales à cette construction: (1) l'électronique 5V qui fera la "réflexion dure": écouter et décider quand et quelles lumières allumer; (2) le boîtier pour tout s'adapter parfaitement, cache tous les «crimes», et (3) le circuit 220V qui est contrôlé par le circuit 5V.
Commençons par le circuit 5V puisque nous pouvons le construire à petite échelle.
Trouver des ressources en ligne n'a pas été une tâche facile. J'ai imaginé dix lumières, qui se sont allumées en fonction du volume des applaudissements, mais personne ne semblait avoir fait cela auparavant. Alors, j'ai commencé petit; Sur tinkerCAD, je crée une simulation en ligne de la façon dont je voulais que les pièces électroniques 5V ressemblent. Vous pouvez trouver ma conception très rudimentaire avec le code ici: https://www.tinkercad.com/things/8mnCXXKIs9M ou ci-dessous sur cette page en tant que fichier "Applause_1.0.ino".
Faire une version préliminaire en ligne et tester plusieurs codes Arduino sur cette simulation m'a vraiment aidé à avoir une meilleure vue de ce qui était nécessaire pour cette version. De cette façon, j'ai expérimenté en ajoutant un moyen de contrôler le comportement du programme: je me suis retrouvé avec deux commutateurs. Un interrupteur active et désactive la mesure, l'autre réinitialise le score à 0/10.
J'ai fourni tous les composants nécessaires: des LED, des résistances, un Arduino et surtout un microphone compatible Arduino.
J'ai construit le circuit et tout testé lors de la répétition suivante, pour me rendre compte que le microphone que j'ai acheté était bien trop sensible pour mon utilisation. Un seul coup à une proximité raisonnable, ou simplement le groupe en train de jouer, saturerait le microphone et donnerait une note de 10/10. Cela m'a conduit à rechercher un microphone à gain variable. J'ai finalement opté pour l'amplificateur de microphone Electret - MAX4466. Il a une toute petite vis à l'arrière avec laquelle vous pouvez régler le gain. (note latérale: j'ai également changé l'Arduino uno pour un Arduino Nano sans aucune raison particulière).
Le MAX4466 a mieux fonctionné mais a également atteint son maximum lors des applaudissements à proximité, j'ai donc décidé d'inclure également le temps des applaudissements comme variable de la formule au lieu de seulement le volume des applaudissements. J'ai aussi écrit un peu plus d'un code élégant pour cette version 2.0 du logiciel (même si je le dis moi-même). Si un seuil d'intensité sonore était dépassé, seule la première lumière s'allumait suivie d'une brève pause pendant laquelle aucune lumière ne pouvait s'allumer. Après avoir attendu, l'Arduino écouterait si le son était encore assez fort pour que la deuxième lumière s'allume, si c'est le cas, la lumière s'allume et la prochaine période d'attente se déclenche. Le temps d'attente augmentait à chaque fois qu'une nouvelle lumière s'allumait. Un applaudissement devrait durer 22,5 secondes à plein volume pour que les lumières affichent 10/10. Vous pouvez trouver le code sur tinkerCAD https://www.tinkercad.com/things/lKgWlueZDE3 ou ci-dessous en tant que fichier "Applause_2.0.ino"
Un test rapide avec les modules relais connectés au lieu des LED m'a appris que les relais étaient allumés lorsque le signal était BAS et éteints lorsque le signal était HAUT. Pas de problème, il suffit de désactiver certains ON et OFF dans le code et nous étions prêts à partir.
Avec tout ça réglé. Je pourrais commencer à tout souder ensemble. Mais j'avais besoin de savoir combien de temps devraient durer toutes les connexions à l'intérieur de la boîte. Construisons donc d'abord la boîte extérieure et organisons tous les composants dedans.
Étape 2: Conception de la boîte
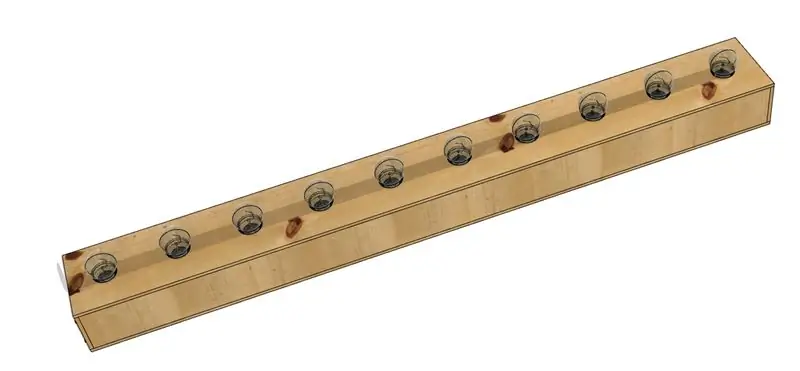
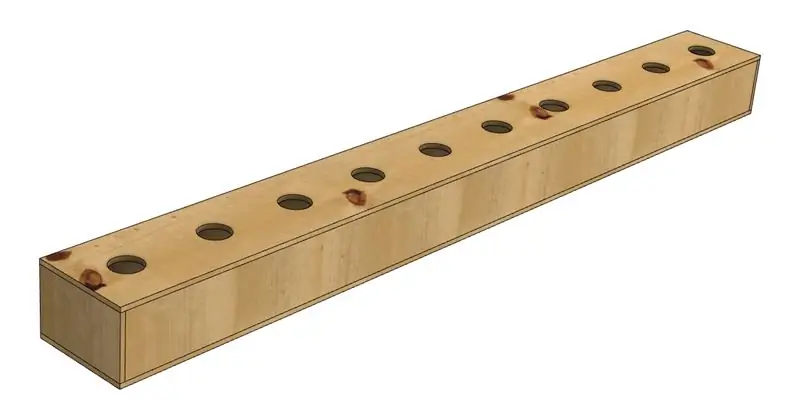
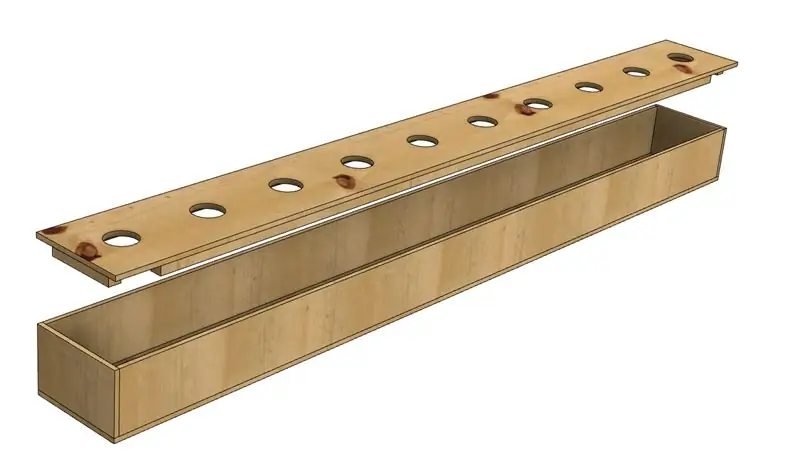
Un deuxième aspect de cette construction était son esthétique. Le compteur d'applaudissements serait au milieu de l'attention donc il devait au moins bien paraître. J'ai choisi de construire une caisse en bois car j'ai les outils de base pour cela et c'est relativement facile.
Ayant appris sur tinkerCAD que l'expérimentation dans le monde numérique est très pédagogique, j'ai également conçu la boîte de compteur d'applaudissements dans le populaire programme 3D-CAD Fusion360 avant d'acheter le matériel nécessaire.
Au cours de plusieurs itérations, j'ai finalement opté pour cette conception (voir photos). Il s'agit d'une simple boîte rectangulaire avec les lumières sortant des trous circulaires du panneau avant.
Les vis laides dans le panneau avant ont été évitées en ajoutant des barres de support à l'intérieur du panneau avant, où plus tard des loquets de porte magnétiques seraient vissés. Le système de fermeture magnétique est rétrospectivement plus un élément de sécurité qu'un élément vraiment nécessaire, car les barres maintenaient la plaque avant par simple friction, très bien.
J'ai également ajouté l'électronique à ma conception numérique. Cela a changé certaines choses, donc c'était déjà payant que je l'ai conçu pour la première fois dans Fusion360. Par exemple, la boîte devait être un peu plus large que les 15 cm initiaux pour que les relais s'adaptent latéralement. J'ai également fini par modéliser et imprimer en 3D des supports en plastique pour les douilles qui à leur tour maintiendraient les lumières en place. Cela m'a semblé être l'option qui me donnerait une marge de manœuvre suffisante pour de futures erreurs. (Je sais que ces supports peuvent également être achetés tels quels, mais cela m'a coûté trois fois plus cher et j'avais un budget limité)
J'ai ajouté le fichier F360 de ma conception finale ici pour que vous puissiez vous y référer et jouer avec.
Étape 3: Construire la boîte
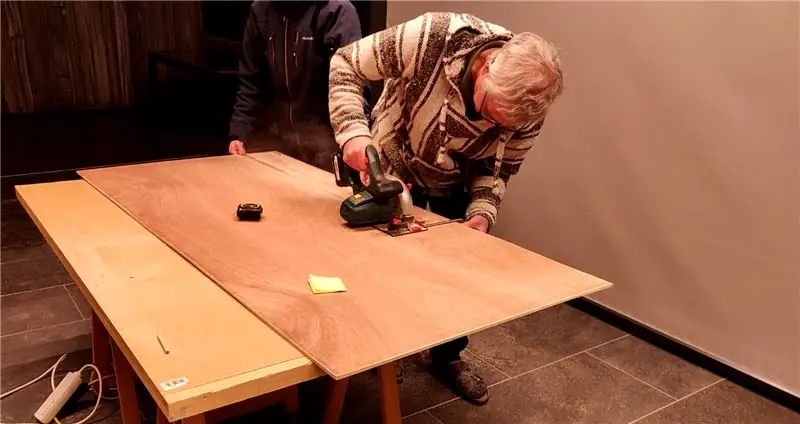
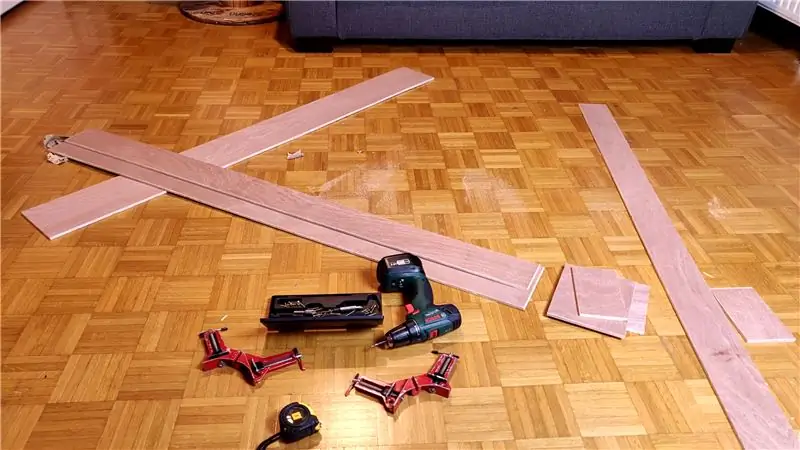
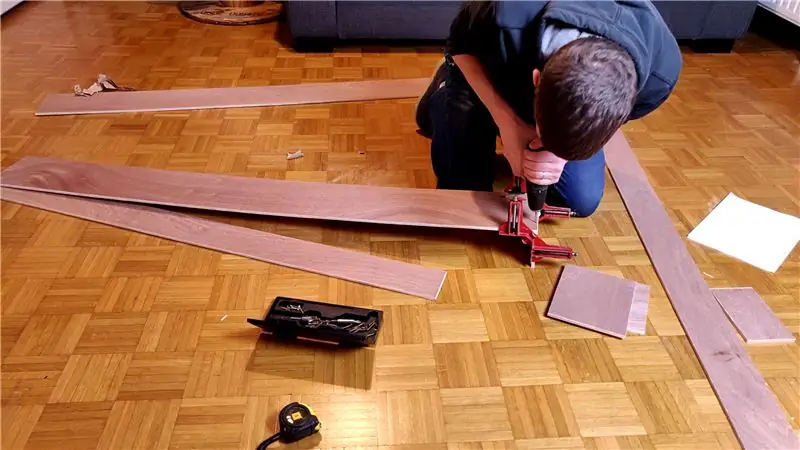
Une fois la conception numérique finalisée, il était temps d'aller à la quincaillerie, d'acheter une grande feuille de contreplaqué et de commencer à couper. Comme je ne possédais pas vraiment d'outils aussi « sophistiqués », je suis allé chez mes parents un week-end et j'y ai coupé le bois sur mesure.
Mon design a cependant fini par produire une feuille coupée assez exotique:
- 2 fois 16,6x150cm pour le recto et le verso
- 2 fois 16,6x10,2cm pour le haut et le bas
- 2 fois 10,2x148,4cm pour les côtés
Les barres de support à l'intérieur du panneau avant étaient des restes et ont été utilisées comme telles, sinon la longueur préférée aurait été de 134 cm et 12 cm.
Une fois à la maison, j'ai disposé toutes les pièces sur le sol et à l'aide de pinces d'angle (empruntées), j'ai commencé à percer des trous et à visser les planches ensemble. N'oubliez pas que les vis ne vont que dans le haut, le bas et l'arrière du compteur pour des réactions purement esthétiques.
Le perçage pilote des trous et le vissage de toutes les planches ensemble était une tâche précaire car le contreplaqué n'avait que 8 mm d'épaisseur, je me suis souvent maudit de penser que 8 mm serait assez épais.
Le panneau avant avait besoin de trous soigneusement espacés d'environ 5 cm de diamètre. J'ai marqué la ligne médiane de la planche avant et j'ai commencé d'un côté. Le centre du premier trou était à 8 mm (l'épaisseur du matériau) + 75 mm (la moitié de 150 mm) du bord de la planche. Tous les autres trous sont distants de 150 mm. Au final je n'étais qu'à 2mm quand j'ai marqué le dixième trou… c'était une bonne journée !
Le seul foret circulaire que j'ai pu emprunter était de 51 mm, plus qu'assez proche pour que je puisse commencer à percer avec plaisir.
Les guides de la plaque avant ont été collés en place à l'intérieur de la plaque avant avec une simple colle à bois.
Étape 4: Installation des douilles dans la boîte
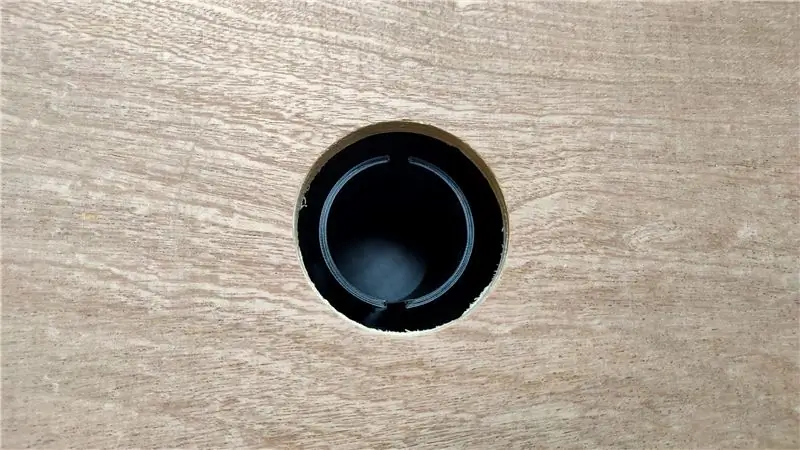
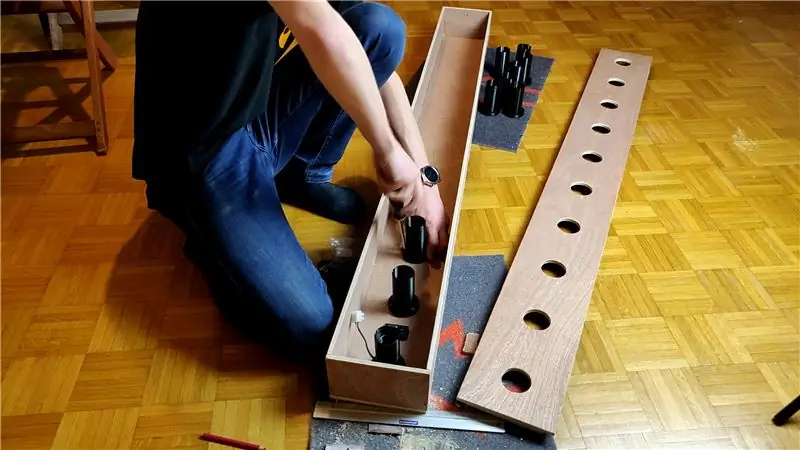
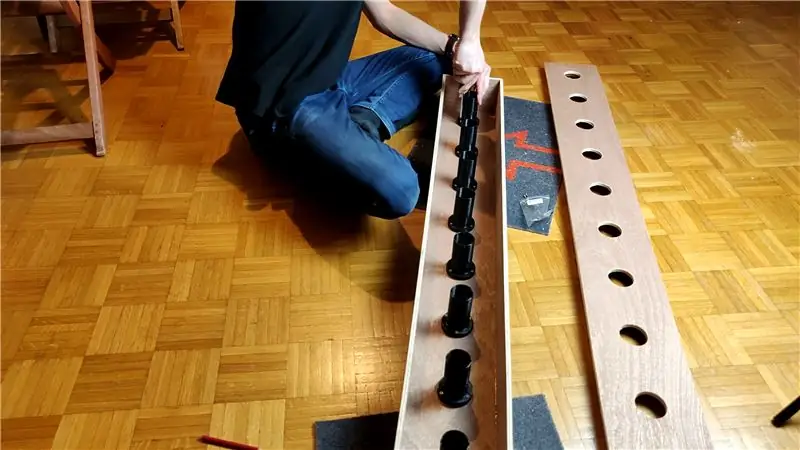
Les premiers composants qui sont montés dans notre boîte nouvellement construite sont les supports de prise de lumière. La raison en est que les supports doivent être centrés sous chaque trou de la plaque avant. Parce que le support maintient les douilles en position, qui à leur tour auront les ampoules vissées dessus, et les ampoules sont littéralement la seule chose qui dépasse du panneau avant et sont donc la seule chose qui ne peut pas être déplacée vers une autre position à l'intérieur de notre boîte. Puisque leur position est fixe, ils devraient entrer en premier, pour être sûr que je ne fasse pas une erreur stupide plus tard.
Comme je l'ai mentionné précédemment, il existe des douilles d'éclairage disponibles dans le commerce avec un support intégré pour les monter perpendiculairement à un mur, mais celles-ci coûtent 4 fois plus cher que les simples qui sont conçues pour être simplement suspendues au plafond sans même faire une faible tentative pour regarde jolie. J'ai donc opté pour un support bon marché et imprimé en 3D pour les prises. (fichier STL ci-dessous). Lors de la conception 3D, je me suis assuré qu'il y aurait suffisamment d'espace de « mouvement » pour placer les douilles à différentes profondeurs.
J'ai imprimé un seul support pour vérifier la conception. Après cela, j'ai imprimé 9 supports à la fois, remplissant complètement toute ma plaque de construction et finissant par durer plus de 50 heures.
J'ai marqué arbitrairement le haut et le bas de la plaque avant et de la boîte (rappelez-vous que j'ai eu un énorme écart de 2 mm entre la conception numérique et la réalité). Ensuite, j'ai commencé le processus fastidieux consistant à centrer un support avec le couvercle en place, à soulever soigneusement l'avant, à marquer sa position avec un crayon et à passer au support suivant. Quand tout a été dit et fait, j'ai revérifié chaque position avant de finalement les visser dans la plaque arrière.
Une note sur les vis: la conception de mon support a une base assez épaisse, c'est fait exprès pour s'assurer que mes vis de 16 mm de long ne dépassent pas l'arrière de ma plaque arrière de 8 mm. Encore une autre raison d'opter pour un contreplaqué plus épais. (Oubliez "vivre, aimer, rire" c'est "vivre, aimer et apprendre").
Quoi qu'il en soit, les douilles étaient à côté. J'ai choisi la hauteur préférée à laquelle je voulais que les ampoules dépassent du panneau avant, puis j'ai mesuré la profondeur à laquelle les douilles devraient se trouver, encore une fois en positionnant soigneusement tout pendant que l'avant est fermé et en le soulevant et en mesurant. Un petit détail: j'ai d'abord dû dévisser et casser un morceau de l'extrémité du câble de toutes les douilles qui servaient de soulagement de traction pour les câbles lorsqu'ils étaient affreusement suspendus au plafond, mais comme je les montais dans des supports imprimés personnalisés, ils ne m'ont servi à rien. Pire encore, la décharge de traction a fait résister les câbles à la courbure serrée dans laquelle je les forçais, faisant ainsi parfaitement son travail, …
J'ai collé toutes les douilles dans les supports et l'ai laissé reposer pendant la nuit avec des élastiques retenant la pression. Bien sûr, j'ai fabuleusement oublié que j'ai acheté 9 ampoules normales et une grosse pour la dixième lumière, cette plus grande lumière est plus sphérique qu'en forme de poire, nécessitant une douille qui est placée plus près de l'avant de la boîte que toutes les autres lumières.(Vis et apprend)
J'ai donc été obligé de casser la colle, (seulement casser légèrement mon impression 3D) pour libérer la douille et la repositionner. Après de copieuses quantités de colle à la fois pour fixer le support et le joindre à la douille à la bonne hauteur, le montage des douilles a été fait.
J'ai également vissé les connecteurs des douilles d'éclairage sur l'un des côtés de la plaque arrière.
Étape 5: Souder l'électronique basse tension
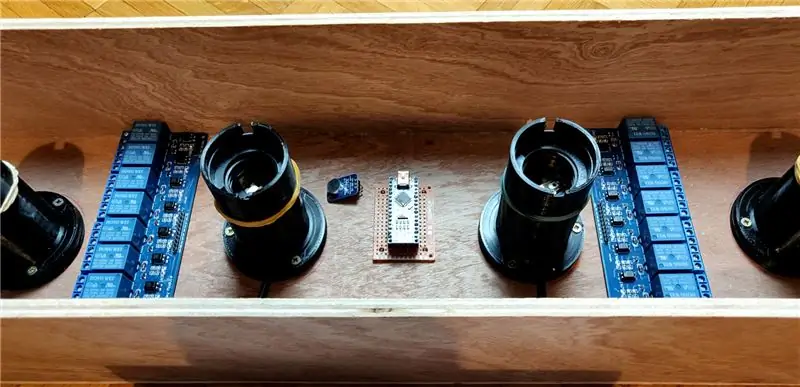
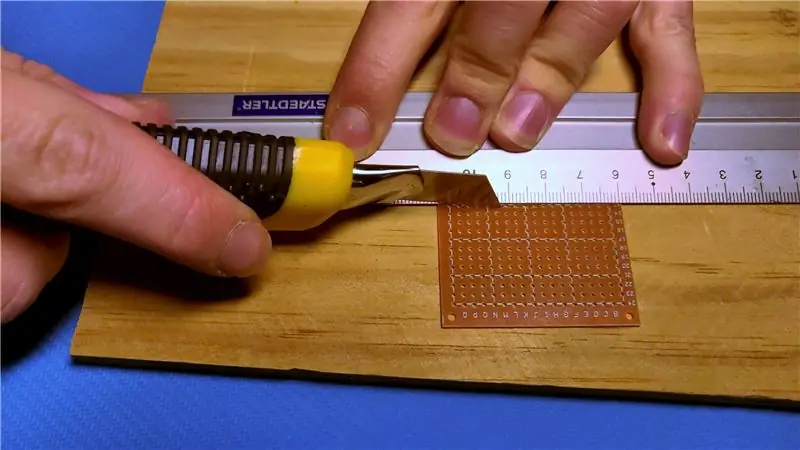
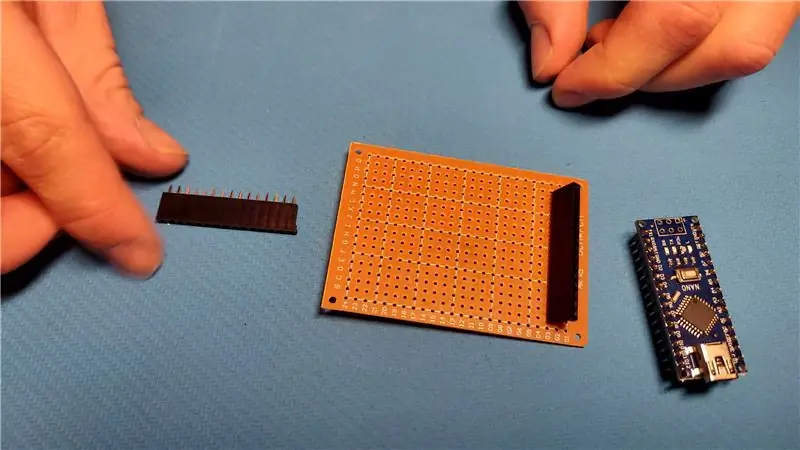
L'ordre du jour suivant consiste à « monter à sec » toute l'électronique basse tension dans la boîte pour avoir une idée de la durée des connexions soudées entre les pièces.
J'ai commencé par placer l'Arduino au milieu entre les lumières 5 et 6 et disposer les relais dans les endroits adjacents au-dessus et en dessous.
J'ai réalisé qu'aucune vis à bois ne passerait à travers les trous de l'Arduino nano. Ceci est rapidement résolu en soudant des en-têtes femelles sur une planche à pain soudable. Les en-têtes contiendront l'Arduino et certains trous percés dans le circuit imprimé accepteront les vis à bois sans se plaindre. Cette carte soudable abritera également les en-têtes pour le microphone à connecter, les connecteurs (avec câbles) pour aller aux relais et le long câble pour le boîtier de télécommande.
À propos de la boîte à distance; J'avais besoin de deux interrupteurs au bout d'un très très long câble. Je suis loin au fond de la scène en tant que percussionniste, alors que le compteur serait tout au devant de la scène. J'ai acheté 20 m de fil à 4 brins qui sont généralement utilisés pour souder des bandes LED. Pour loger les deux commutateurs, j'ai conçu et imprimé en 3D une simple boîte (fichiers STL et F360 ci-dessous) mais n'importe quelle boîte rectangulaire avec quelques découpes pour les composants et les fils fera l'affaire.
Après avoir mesuré la distance entre les composants et pris un excès généreux sur cette distance, j'ai chauffé le fer à souder et j'ai commencé à souder.
Souder toutes les connexions demande de la patience, et surtout de la concentration pour bien faire les choses. J'ai inclus le schéma de câblage que j'ai utilisé pour effectuer toutes les connexions, mais sachez que votre câblage peut être un peu différent si vous utilisez des composants différents. (Ou si j'ai fait une erreur dans mon schéma)
En fin de compte, mon câblage donnait l'impression qu'un oiseau essayait de nicher là-bas. Néanmoins, miraculeusement aucune erreur n'a été commise et rien n'a commencé à fumer lors de la mise sous tension.
Avec tout ce qui est connecté, je pouvais visser chaque carte de circuit imprimé au panneau arrière sur des entretoises imprimées en 3D. Ces entretoises remplissaient deux fonctions: (1) il est toujours judicieux de laisser de l'espace entre les circuits imprimés et la plaque sur laquelle vous les montez. Et (2) me suis-je déjà plaint d'avoir des vis de 16 mm et du contreplaqué de 8 mm, et que je suis donc constamment en danger de visser des vis directement à travers le bois ? Oui, les entretoises ont également fait en sorte que mes vis n'atteignent pas l'autre extrémité de la boîte en contreplaqué.
[REMARQUE] Avec le recul, je recommanderais en fait d'utiliser 5 relais par module de relais. Mon idée d'utiliser deux modules de relais à 8 canaux était de permettre un relais cassé, dans ce cas, je devrais simplement changer les connexions et le compteur d'applaudissements serait à nouveau opérationnel. Cela répartirait également un peu mieux les connexions 220V sur les deux modules, rendant la gestion des câbles un peu plus… gérable. (Vis et apprend)
Étape 6: Connexion des composants 220V
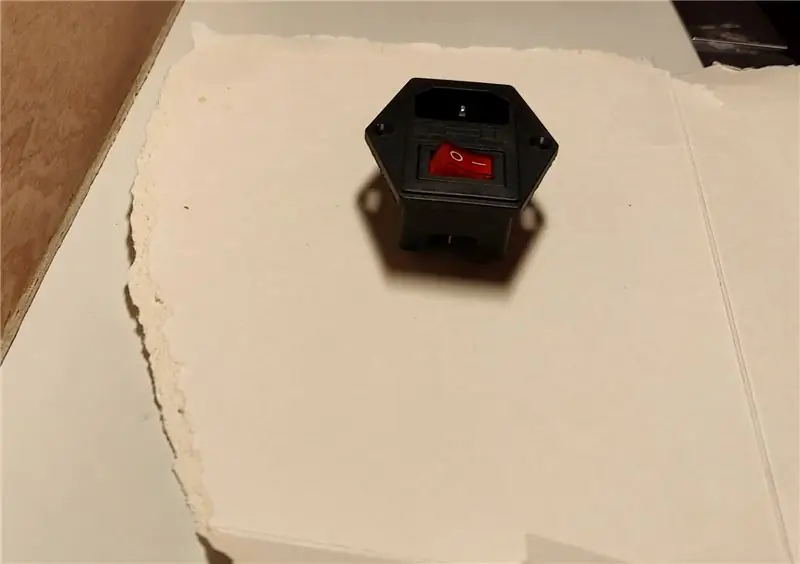
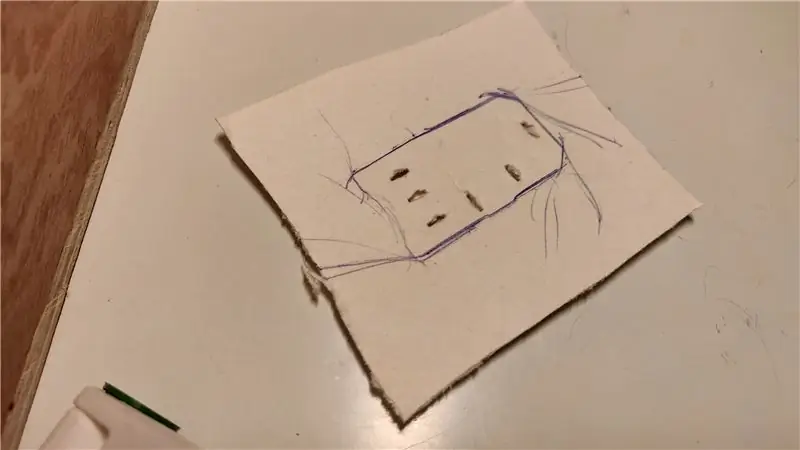
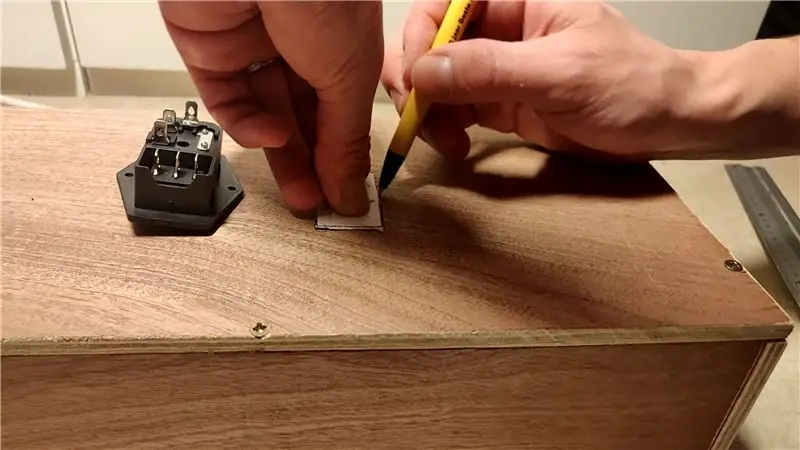
Une fois tous les composants basse tension en place, il est temps de travailler sérieusement et d'installer le circuit de tension principal.
Il va sans dire qu'en travaillant avec les fils, vous ne les connectez en aucun cas au secteur !!!!!
Avec le technicien qui installerait et contrôlerait les lumières du spectacle pour notre prochain concert, nous avons décidé d'utiliser une prise de courant à fusible comme entrée d'alimentation pour le compteur d'applaudissements. Cela a permis de s'assurer que tout câble de n'importe quelle longueur serait capable de s'adapter et d'alimenter notre compteur.
Cela ajouterait également une couche de sécurité à notre configuration: ces connecteurs sont équipés d'un fusible qui saute au-dessus d'un certain ampérage, garantissant que rien ne se cache si ce n'est pas censé le faire.
Pour installer cette prise, nous avions besoin de ses mesures exactes. Il a cependant une forme assez complexe. Donc, la chose la plus simple que j'ai pu trouver, c'est d'appuyer la prise d'alimentation sur un morceau de carton et de tracer les contours de la prise. Les lignes de contour peuvent ensuite être découpées pour produire un gabarit qui peut être transféré sur le bois.
Lors du marquage et de la découpe de l'emplacement de la fiche, gardez à l'esprit qu'il y a déjà des composants installés à l'intérieur du compteur qui ne peuvent plus être déplacés, ce qui limite les emplacements possibles où la fiche peut sortir de la boîte. Il en va de même pour le trou de sortie du fil de 20m de long pour la 'télécommande'.
Normalement, vous découperiez le trou avec une scie sauteuse, mais je ne possède pas un tel appareil et j'étais impatient, alors j'ai simplement percé des trous le long des contours et j'ai simplement découpé le trou avec une lame tranchante. Cela fonctionne, mais je ne peux pas le recommander car je me suis presque coupé les doigts.
Il ne reste plus qu'à tout câbler ensemble. J'ai fait un schéma de câblage du circuit 220v pour une référence facile. Le fil chaud est connecté à toutes les lumières en parallèle tandis que le fil neutre est interrompu par les relais avant de se connecter aux lumières. C'est aussi simple que ça. Assurez-vous simplement que vous câblez la bonne lumière au bon relais, ou vous devrez reconnecter soit l'extrémité de commande 5V, soit les fils 220v pour corriger votre erreur.
Il y a un Instructable sur la façon de connecter vos fils à la prise de courant à fusible qui explique tout mieux que je ne le pourrais jamais, alors sautez là-bas, mais n'oubliez pas de revenir ici (https://www.instructables.com/id/Wire- Up-a-Fused-AC-Male-Power-Socket/)
[REMARQUE] Pour connecter les fils neutres aux relais placés au centre, j'ai connecté un fil à la prise à fusible et je l'ai divisé en dix avant de le connecter aux relais. J'avais l'intention de passer par les câbles neutres aux relais, en connectant chaque entrée de relais en parallèle les unes aux autres. Cependant, les bornes relais n'acceptaient pas plus d'un câble m'obligeant à trouver une autre solution. Pour effectuer cette division, il est conseillé d'utiliser un connecteur quelconque. Je n'avais pas ça (et j'étais impatient) et j'ai juste attaché tous les câbles ensemble dans un gros nœud avant d'en isoler l'enfer. Je ne recommande pas ce « nœud » pour des raisons de sécurité électrique. NOTAMMENT en raison de sa proximité avec la carte Arduino. Cela semble pourtant bien fonctionner.
Étape 7: Snappers magnétiques (facultatif)
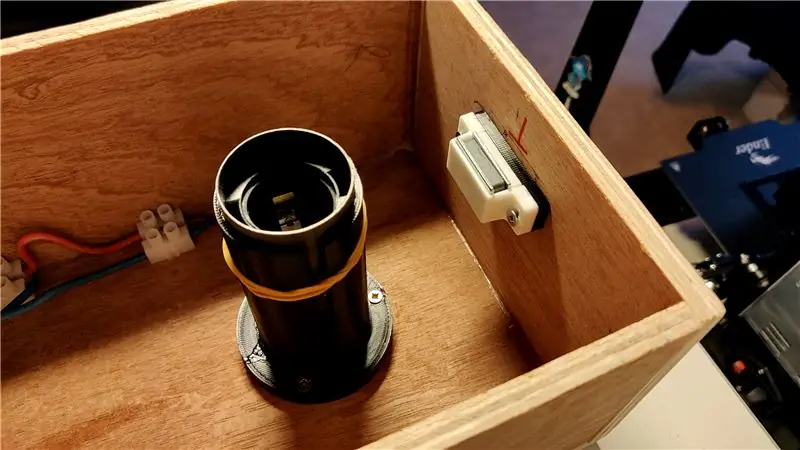
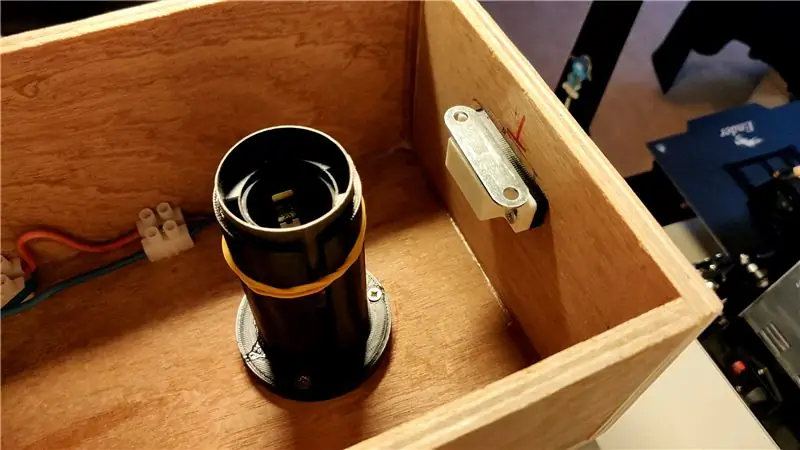
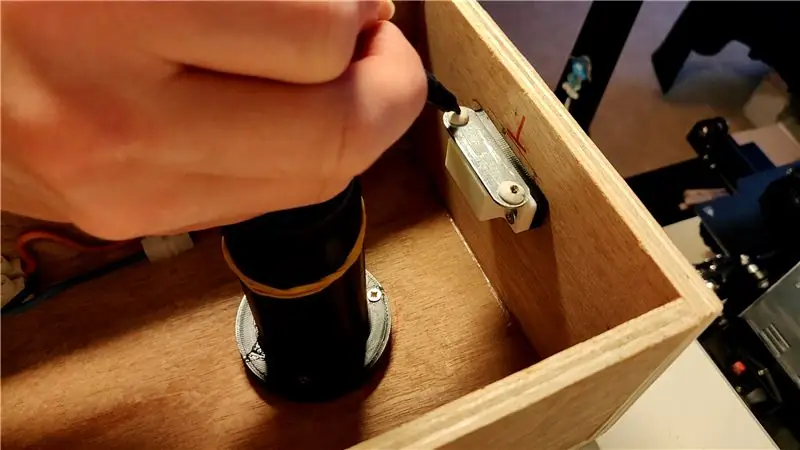
Cette étape est totalement facultative, car les guides du panneau avant maintiennent suffisamment la plaque avant par simple friction. J'ai décidé d'inclure les snappers juste comme une caractéristique de sécurité, afin que le panneau avant ne se détache pas sans que je veuille qu'il se détache
Je suis resté éveillé de nombreuses nuits en pensant à la meilleure méthode pour tenir le panneau avant de la boîte à sa place. En fin de compte, j'ai pensé à utiliser des ferme-portes magnétiques. Je doute que ce soit le terme officiel pour ces appareils astucieux, mais vous les reconnaîtrez tout de suite. Les vivaneaux magnétiques sont le plus souvent utilisés pour garder les portes de placard fermées sans utiliser de serrure.
J'ai attaché la partie magnétique à la coque extérieure du compteur d'applaudissements (haut, bas, panneau gauche ou droit). Cela a été fait au moyen d'une entretoise et de vis personnalisées imprimées en 3D (yadda yadda yadda, vis longues, bois fin, vous connaissez l'histoire maintenant ☺)
Les plaques métalliques étaient vissées au bois des guides. C'était aussi la première fois que le bois était en fait assez épais pour ne pas utiliser d'espace (yay). J'ai eu quelques problèmes avec la détermination de la position des plaques métalliques. J'ai trouvé une solution:
- Fixez la partie magnétique à la boîte
- placer la plaque métallique sur l'aimant dans sa position parfaite
- sur les trous de l'assiette, placez une petite boule de "Pritt-buddy" (une sorte de colle type chewing-gum pour fixer les affiches aux murs sans punaises, un chewing-gum ordinaire ferait probablement aussi l'affaire)
- avec un marqueur à alcool faire un point sur la balle Pritt-buddy à l'endroit où se trouvent les trous
- fermer le couvercle, transférant ainsi une partie de l'encre du marqueur sur le bois
- Soulevez le couvercle et tadaa ! Vous avez fait un petit marquage où vos vis doivent aller
- retirez les copains et la plaque et vissez-la dans sa position correcte, essayez d'abord
- étape 8: profit
J'ai placé quatre vivaneaux magnétiques dans la boîte: un en bas, un en haut, un au milieu à gauche, un au milieu à droite.
Les vivaneaux que j'ai choisis avaient une force de maintien de 6 kg. Avec quatre d'entre eux, ils ont fourni suffisamment de force pour soulever presque toute la boîte par le seul panneau avant.
Étape 8: Ce que je ferais différemment
En faisant ce compteur d'applaudissements, j'ai souvent maudit mon passé pour avoir pris des décisions stupides, je vais énumérer ici les leçons les plus importantes que j'ai apprises:
-
UTILISEZ DU CONTREPLAQUÉ PLUS ÉPAIS. Sérieusement, fabriquer une boîte en contreplaqué de 8 mm est possible, mais cela pose de nombreux défis et impose certains compromis à faire.
- Tout d'abord, le perçage pilote de tous les trous pour les vis est un défi car il n'y a pas de tolérance pour les forets mal inclinés.
- Deuxièmement, les vis que j'avais étaient de 16 mm (ai-je déjà mentionné cela?). Cela m'a obligé à prendre des distances lors du vissage dans le bois pour empêcher les vis de sortir de l'autre côté, mais en même temps, cela signifiait que les vis ne pénétraient pas assez profondément pour obtenir suffisamment de traction pour maintenir certains composants.
- ….
- il suffit d'utiliser du bois plus épais
Conseillé:
Comment fabriquer une antenne double biquade 4G LTE en quelques étapes faciles : 3 étapes
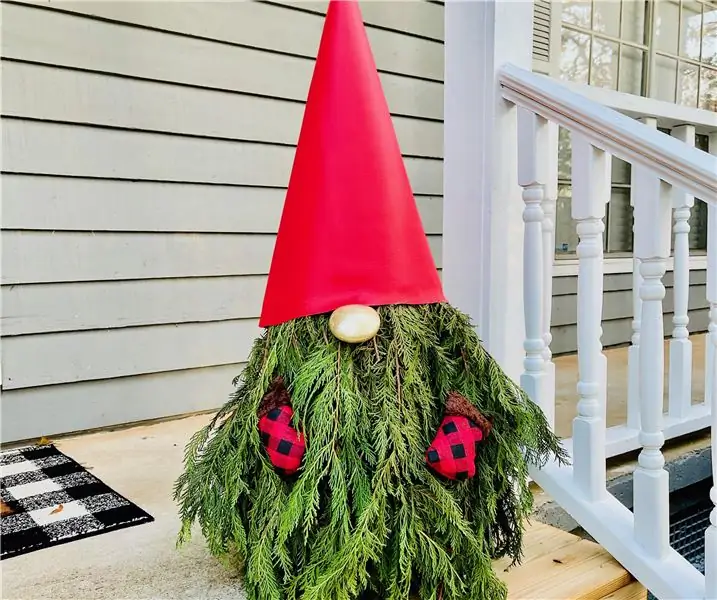
Comment créer une antenne double biquade 4G LTE Étapes faciles : La plupart du temps, je n'ai pas une bonne force de signal pour mes travaux quotidiens. Donc. Je recherche et essaye différents types d'antenne mais ne fonctionne pas. Après une perte de temps, j'ai trouvé une antenne que j'espère fabriquer et tester, car ce n'est pas un principe de construction
Game Design dans Flick en 5 étapes : 5 étapes
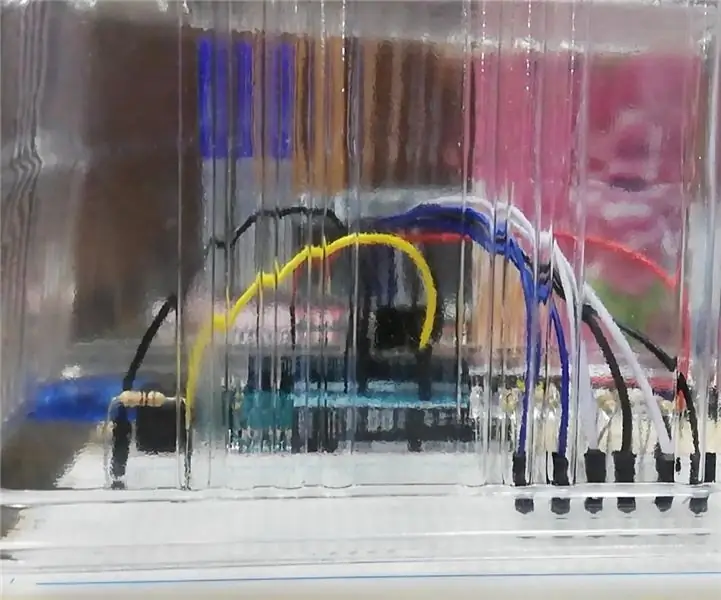
Game Design dans Flick en 5 étapes : Flick est un moyen très simple de créer un jeu, en particulier quelque chose comme un puzzle, un roman visuel ou un jeu d'aventure
Système d'alerte de stationnement en marche arrière Arduino - Étapes par étape : 4 étapes
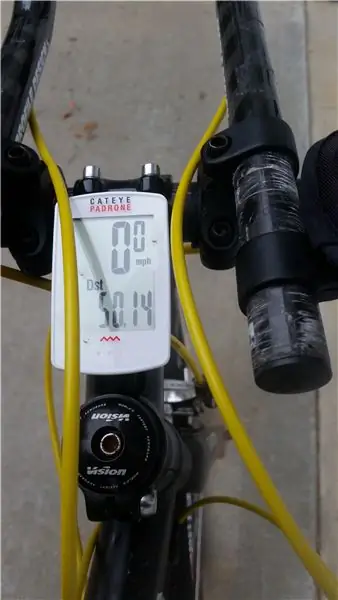
Système d'alerte de stationnement en marche arrière Arduino | Étapes par étape : dans ce projet, je vais concevoir un circuit de capteur de stationnement inversé pour voiture Arduino simple à l'aide d'un capteur à ultrasons Arduino UNO et HC-SR04. Ce système d'alerte de marche arrière basé sur Arduino peut être utilisé pour une navigation autonome, une télémétrie de robot et d'autres r
Comment faire des applaudissements ? Interrupteur marche/arrêt -- Sans aucun IC : 6 étapes
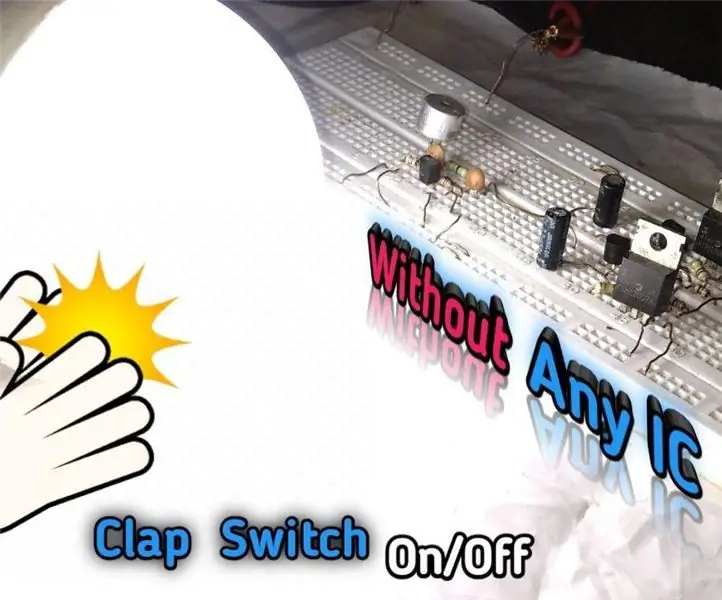
Comment faire des applaudissements ? Interrupteur marche/arrêt || Sans aucun circuit intégré : il s'agit d'un coup sur l'interrupteur sans aucun circuit intégré. Vous pouvez applaudir ? La première fois, puis l'ampoule ? ON et applaudir la deuxième fois l'ampoule ? DÉSACTIVÉ. Ce circuit basé sur une bascule SR. Composants 1. Transistors BC547 NPN (4 pièces) 2. Résistances 10k (5 pièces)3. 1K de résistance
Interrupteur à applaudissements avec transistor BC547 : 14 étapes
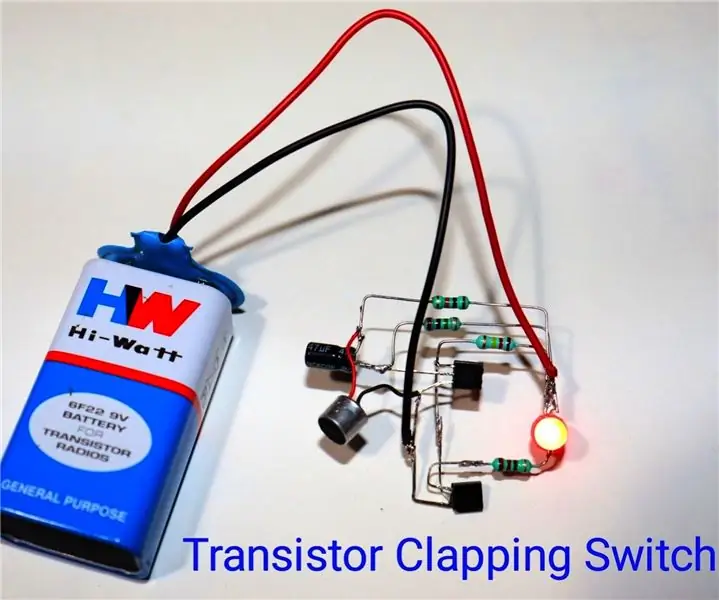
Clapping Switch avec BC547 Transistor: Hii Friend, aujourd'hui, je vais faire un circuit de Clapping switch avec BC547 Transistor