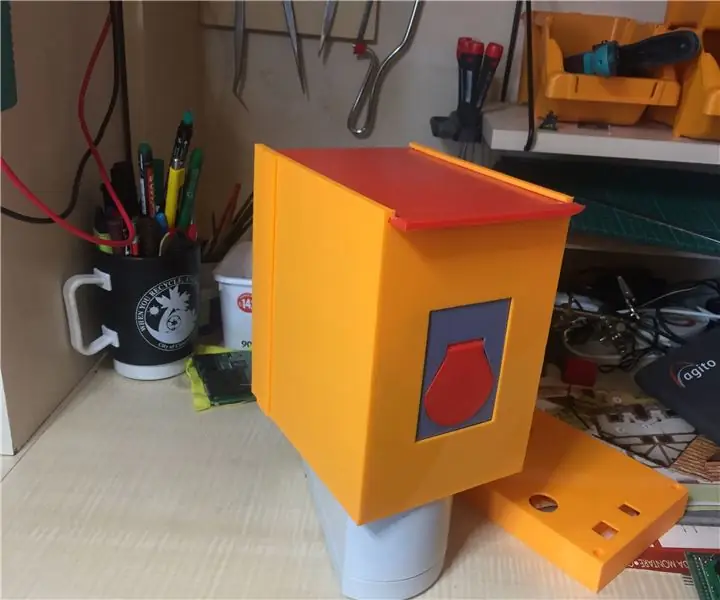
Table des matières:
2025 Auteur: John Day | [email protected]. Dernière modifié: 2025-01-23 14:45
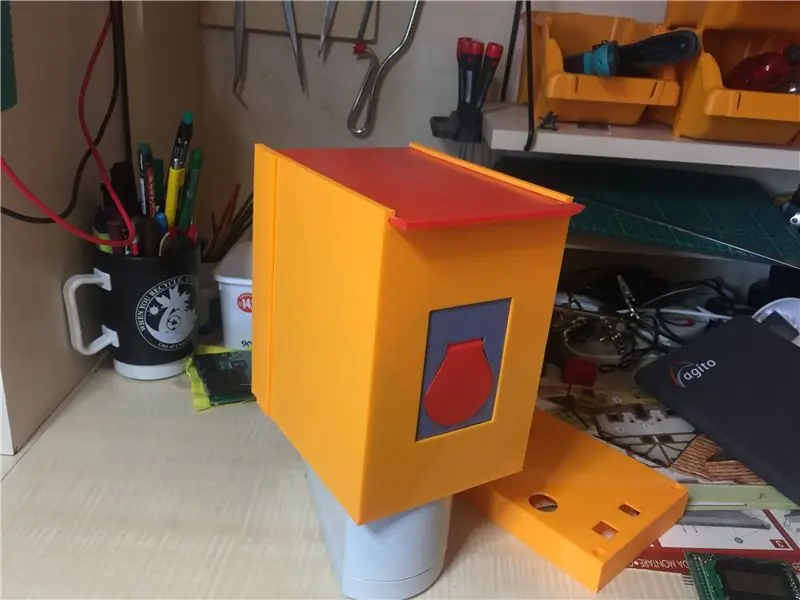
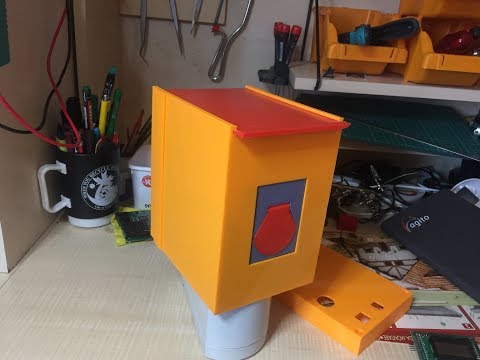
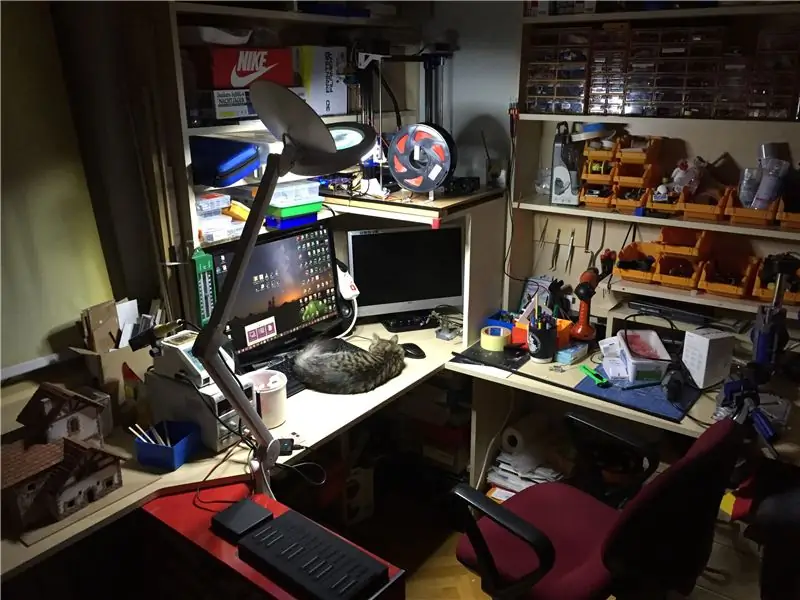
Projets Fusion 360 »
Si vous ne contrôlez pas la quantité de nourriture que votre chat mange, cela peut entraîner des problèmes de suralimentation et de surpoids. Cela est particulièrement vrai si vous êtes loin de chez vous et laissez à votre chat de la nourriture supplémentaire à consommer selon son propre horaire. D'autres fois, vous pouvez vous rendre compte que vous oubliez de la nourrir à temps et qu'il est impossible de rentrer chez vous.
Le distributeur automatique de nourriture pour chats Diy peut fonctionner et distribuer une quantité précise de nourriture sèche à tout moment et peut être contrôlé avec votre téléphone portable partout dans le monde.
Ce projet est un projet d'apprentissage complet allant de l'impression 3D à la conception dans fusion360, de la programmation arduino aux bases de l'iot, de la conception électronique en eagle à la production de circuits imprimés recto verso.
Les principaux chapitres de cette instructable sont
Atelier: Cette partie n'est pas directement liée à la production proprement dite mais peut inspirer les lecteurs avec de petits biens immobiliers. Toute la conception, l'impression 3d, la production de pdb, les prototypes, la conception électronique et la fabrication sont effectués dans un atelier de 2x2m.
Prototypes: Une conception parfaite est presque impossible à réaliser. Cependant, chaque itération de conception -qui échoue- apporte de nouvelles idées, résout des problèmes et porte la conception à un niveau supérieur. Ainsi, bien qu'un jeu d'instructions n'inclue généralement pas les tentatives infructueuses, je les ai incluses brièvement car elles montrent la progression et la justification de la conception finale.
Conception mécanique: Conception de la mécanique et du conteneur.
Conception électronique: Ce projet est basé sur la carte Arduino Mega. Une unité d'alimentation, une unité d'horloge, une unité de commande de moteur à courant continu et une unité wifi ESP8266 sont assemblées sur une carte de circuit imprimé conçue sur mesure. Vous pouvez trouver Instructable connexe ici
Programmation: un peu de programmation Arduino de base. Un peu de programmation ESP8266. Un petit serveur Web a été créé à l'aide d'Arduino et d'esp8266.
Production: impression 3D de toutes les pièces conçues par fusion360 et assemblage. La plupart des pièces sont imprimées en 3D. à part le plastique, il y a une tige en métal et plusieurs vis en métal. Le reste est l'électronique et un moteur à courant continu.
Étape 1: Atelier
L'atelier contient tous les outils nécessaires à la production de circuits électroniques, à la fabrication de circuits imprimés, à l'impression 3D, à la peinture de modèles et à d'autres petits travaux de production. Il y a un ordinateur de bureau Windows qui est connecté à une imprimante 3D et également utilisé pour la création de musique électronique.
Bien sûr, plus d'espace est toujours mieux pour un amateur. Cependant, un placement dense d'outils et quelques astuces astucieuses telles que le placement d'une imprimante 3D au-dessus des écrans d'ordinateur peuvent créer un espace de travail pratique et agréable.
Bien qu'un atelier puisse ne jamais être la partie directe d'un Instructable, il convient de le mentionner ici comme l'étape principale du processus.
Étape 2: Prototypes
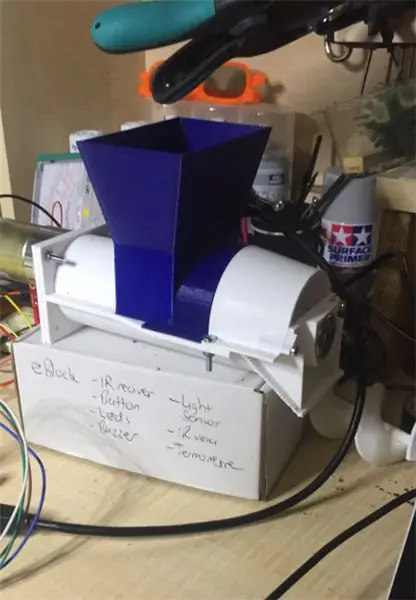
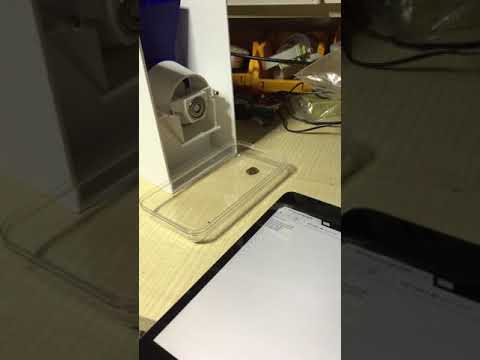
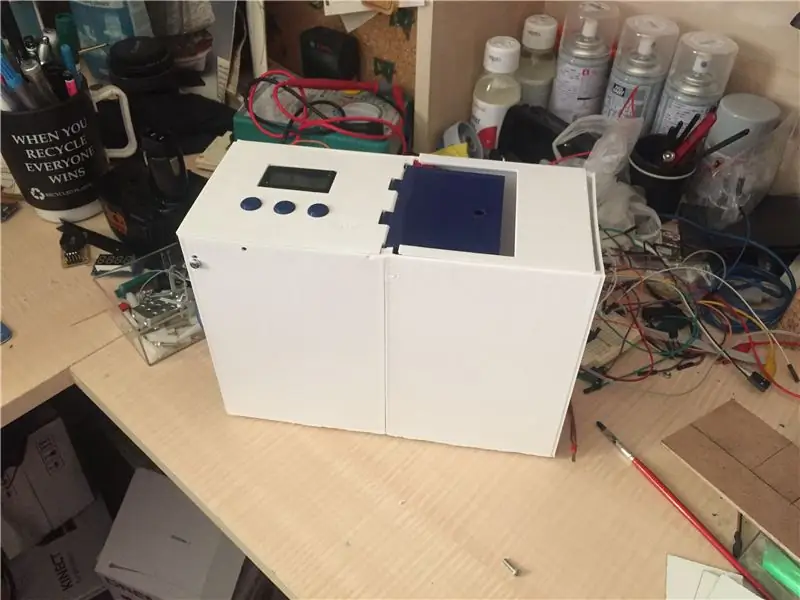
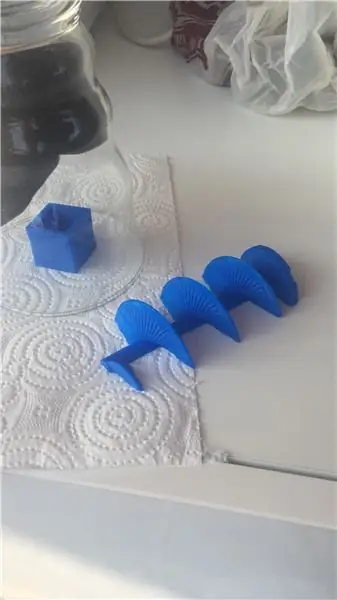
La durée de ce projet a été complètement sous-estimée. Cela a commencé avec une estimation de trois à cinq semaines. Il a été achevé en plus de 40 semaines. Comme je ne pouvais pas investir de temps en continu pour ce projet, je ne peux pas être sûr du temps réel consacré au projet, mais je suis sûr que chaque partie de ce projet a pris plus que prévu.
J'ai passé beaucoup de temps sur des prototypes.
Vis d'Archimède
Le prototypage a commencé avec des vis d'Archimède. C'était aussi mon premier projet Fusion 360. J'ai fabriqué et imprimé au moins 8 vis différentes tout en apprenant l'excellent logiciel appelé Fusion 360. (Fusion 360 est un logiciel gratuit pour les amateurs et bien que vous puissiez faire des choses assez sophistiquées, la courbe d'apprentissage n'est pas si raide) Les premières ont été coupées du milieu en deux. Je ne pouvais pas trouver un moyen d'imprimer en 3D un morceau de vis vertical. Après avoir imprimé deux moitiés, je les ai collées ensemble, ce qui est un moyen très inefficace et percutant de faire une vis d'archimède. Ensuite, j'ai réalisé que si j'ajoute des "canards de ventilateur" à l'imprimante, la qualité d'impression verticale s'améliore. Il existe de nombreux types différents de « canards de ventilateur », j'ai donc dû trouver la meilleure combinaison par essais et erreurs. Finalement, j'ai fini par obtenir une vis d'archimède presque parfaite imprimée en une seule pièce.
Conteneur d'alimentation
Un autre défi était la conception du conteneur d'alimentation. Les liquides peuvent être transférés par la vis sans aucun problème. Cependant, les matériaux solides comme la nourriture sèche pour chats posaient problème à cause des confitures. J'ai essayé de créer un espace de sécurité pour éviter les bourrages et j'ai également réalisé que l'ajout d'un mouvement vers l'arrière pour chaque mouvement vers l'avant de la vis réduisait considérablement les bourrages. La forme en demi-tube de la conception finale et le mouvement arrière contrôlé par logiciel ont complètement éliminé le risque de blocage.
La boîte
Au début du projet, j'ai imprimé toute la boîte dans l'imprimante. Comme la taille de l'imprimante était plus petite que la taille de la boîte, j'ai dû la diviser en morceaux, ce qui la rendait très faible et moche. Ensuite, j'ai envisagé une boîte en bois. Les murs du deuxième prototype étaient en bois. Quelques difficultés de production (je n'avais pas de place et d'outils appropriés pour couper et remodeler le bois) j'ai décidé de reconsidérer la boîte entièrement imprimée pour le troisième prototype (ou conception finale). J'ai rendu le design plus efficace et plus petit afin de pouvoir l'imprimer en une seule pièce. Théoriquement, cette approche a été travaillée. En pratique, l'impression de gros objets prend trop de temps et tout problème avec l'imprimante peut détruire le produit final à tout moment même le 14. heure de l'impression. Dans mon cas, j'ai dû arrêter l'impression avant la fin et j'ai dû concevoir et imprimer le segment manquant en tant que pièce supplémentaire. Pour le prochain prototype, je pense utiliser du plexi pour les parois de la boite.
Arduino
J'ai commencé avec Uno. Il était plus petit et avait l'air assez pour mes besoins. Cependant, j'ai sous-estimé la complexité du développement logiciel. Uno n'a qu'une seule sortie série et depuis que j'utilisais cette sortie pour les communications esp8266, je n'avais pas de port de débogage pour enregistrer les variables de surveillance, etc. et il s'est avéré que sans débogage en temps réel, il était presque impossible de coder même un petit service Web. Je suis passé à Arduino Mega. (ce qui a changé le design de la boite)
Affiche
Pendant le développement du projet, j'ai essayé presque tous les types d'écrans sur le marché, y compris un petit écran oled. Chacun d'eux avait des avantages et des inconvénients. Oled était sympa mais avait l'air petit et cher par rapport à la conception globale. Les écrans LED 7 segments étaient lumineux mais présentaient peu d'informations. J'ai donc utilisé un écran LCD 8x2 pour la conception finale. Les futurs designs peuvent ne contenir aucun écran ou un écran oled plus grand qui a l'air bien.
Boutons
J'ai mis trois boutons pour contrôler l'appareil dans les premiers prototypes. Ensuite, j'ai décidé de ne pas les utiliser dans les conceptions suivantes car les assembler prenait du temps, je ne pouvais pas les rendre assez solides et ils ajoutaient une complexité supplémentaire à la convivialité de l'appareil.
Prototypes électroniques
J'ai réalisé plusieurs prototypes électroniques. Certains d'entre eux étaient sur la planche à pain, d'autres sur une planche à pain en cuivre. Pour la conception finale, j'ai réalisé un circuit imprimé personnalisé à l'aide d'une imprimante 3D modifiée. (voici l'instructable pour ce projet)
Étape 3: Concevoir les pièces en plastique
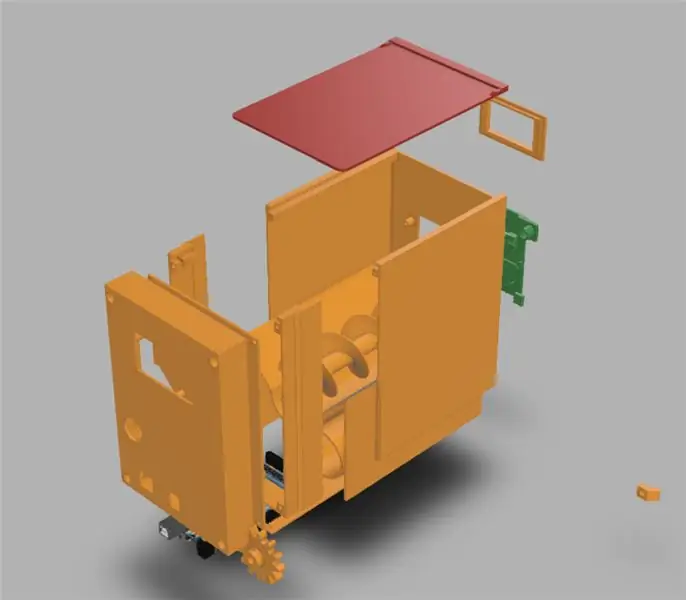
Vous pouvez trouver la conception de toutes les pièces 3D dans ce lien thingverse.
Vous pouvez également accéder au design Fusion 360 à l'adresse:
Étape 4: imprimer les pièces
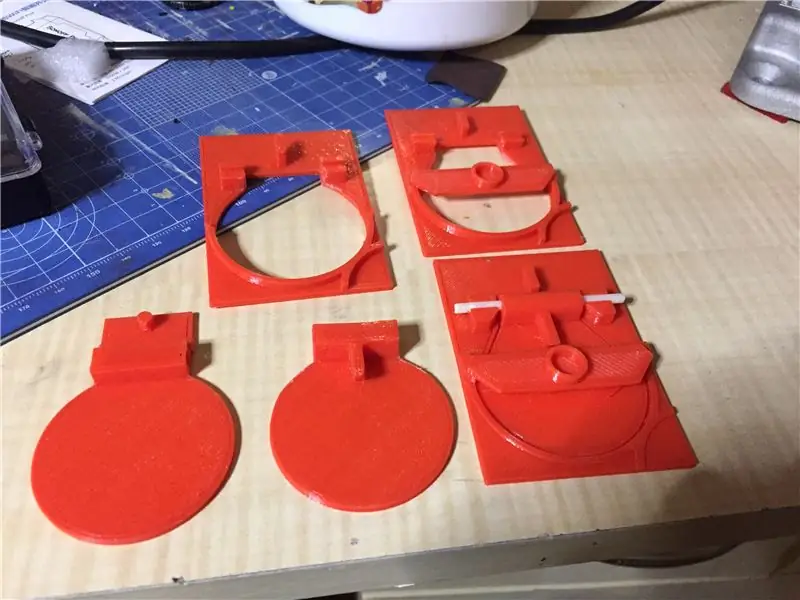
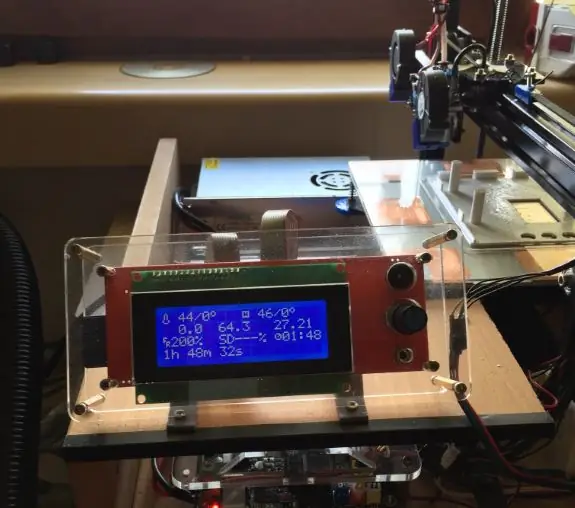
Toutes les pièces d'imprimante 3D peuvent être trouvées ici:
Être conscient. L'impression prend du temps. La boîte extérieure qui est la plus grande partie peut prendre jusqu'à 14 heures.
La vis d'Archimède est la partie spéciale que vous devez imprimer verticalement. Vous aurez peut-être besoin d'un bon souffleur d'air (canard amusant) pour refroidir le filmanet fondu lorsqu'il s'écoule de la buse.
Étape 5: Concevoir un circuit et fabriquer un circuit imprimé
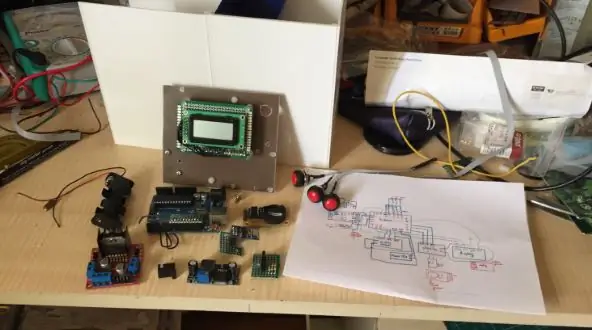
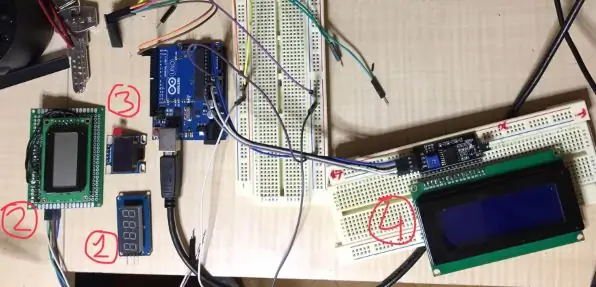
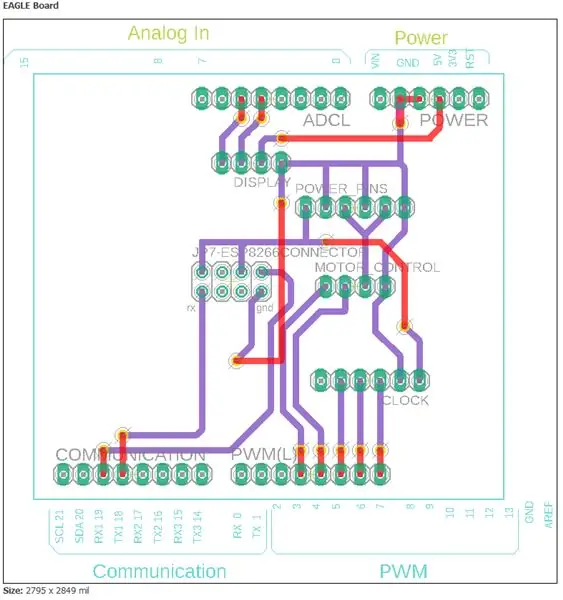
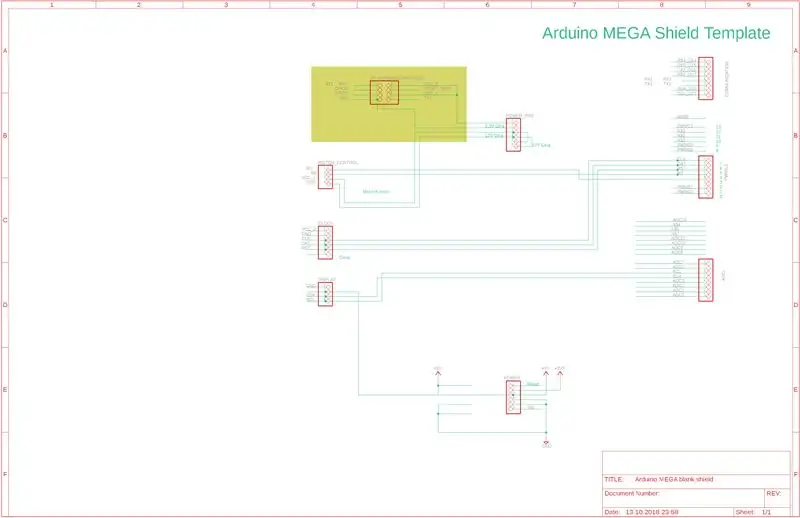
La fabrication de PCB pour ce projet est décrite ici.
Les fichiers de conception de circuit EAGLE sont
La plupart des pièces sont des modules électroniques tels que:
- L'horloge,
- commande de moteur à courant continu,
- contrôle d'affichage,
- affichage,
- esp8266,
- méga arduino
- convertisseur de puissance
Il existe de nombreuses variétés différentes de ces modules. La plupart d'entre eux ont des entrées/sorties similaires, il sera donc facile d'adapter la conception actuelle de l'aigle. Cependant, certaines modifications peuvent être nécessaires.
Étape 6: Écrire un logiciel
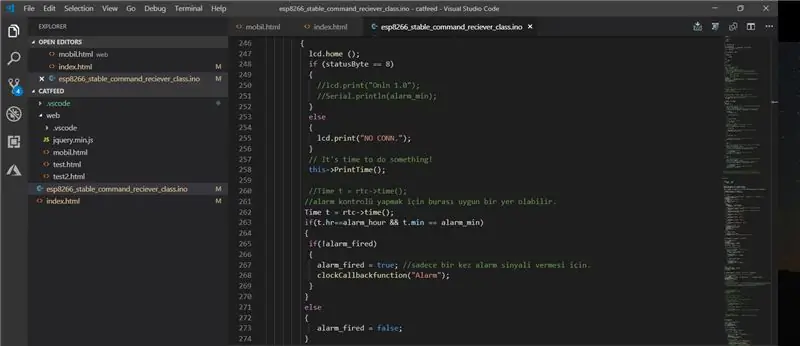
Vous pouvez trouver le code complet ici.
Ce code peut ne pas fonctionner sur certaines définitions de carte Arduino. J'ai utilisé les cartes Arduino AVR 1.6.15. Les plus récents n'ont pas fonctionné (ou ont travaillé avec des problèmes mineurs ou majeurs)
J'ai également ajouté un exemple de code html. Les pages HTML peuvent être utilisées pour tester les capacités de connexion wifi de l'appareil.
L'appareil accepte de simples commandes d'url html. Par exemple: pour commencer l'alimentation, vous pouvez simplement envoyer "https://192.168.2.2.40/?pin=30ST" depuis le navigateur. (IP peut changer en fonction des paramètres de votre réseau local) En plus de démarrer et d'arrêter l'appareil, vous pouvez régler l'heure et régler l'alarme en utilisant le même format avec des paramètres différents.
Cette commande html est reçue par esp8266 et analysée par le logiciel. Le logiciel agit comme un simple serveur Web. Il exécute des commandes et renvoie 200 en cas de succès.
Cette méthode de contrôle n'est pas la manière la plus élégante de contrôler les périphériques iot. Ici, vous pouvez trouver de meilleurs moyens de communication IOT tels que MQTT. Je prévois de réviser le logiciel pour inclure un meilleur protocole.
J'ai utilisé Microsoft Visual Code comme éditeur. J'ai commencé avec Arduino IDE mais je suis passé à VSCode. Je vous conseille vivement d'écrire du code sur plus de 100 lignes, ne pensez même pas à utiliser Arduino IDE.
Étape 7: Assembler
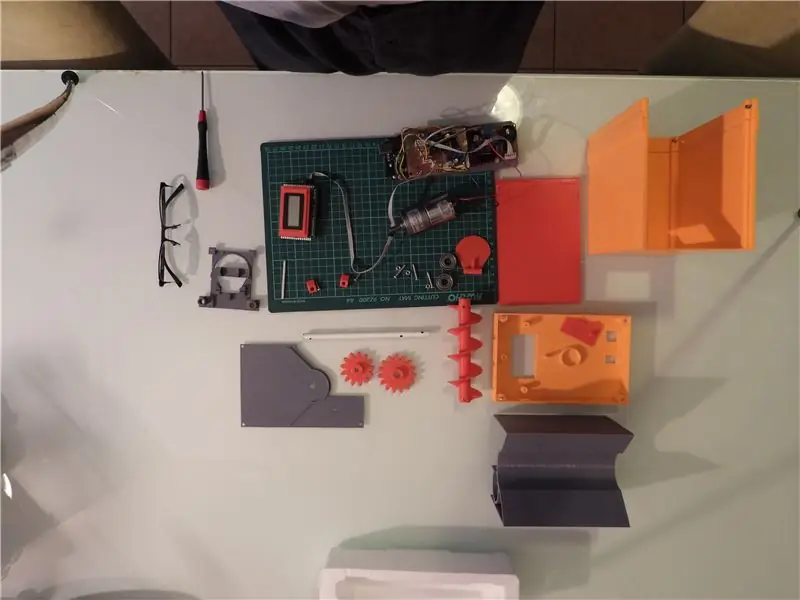
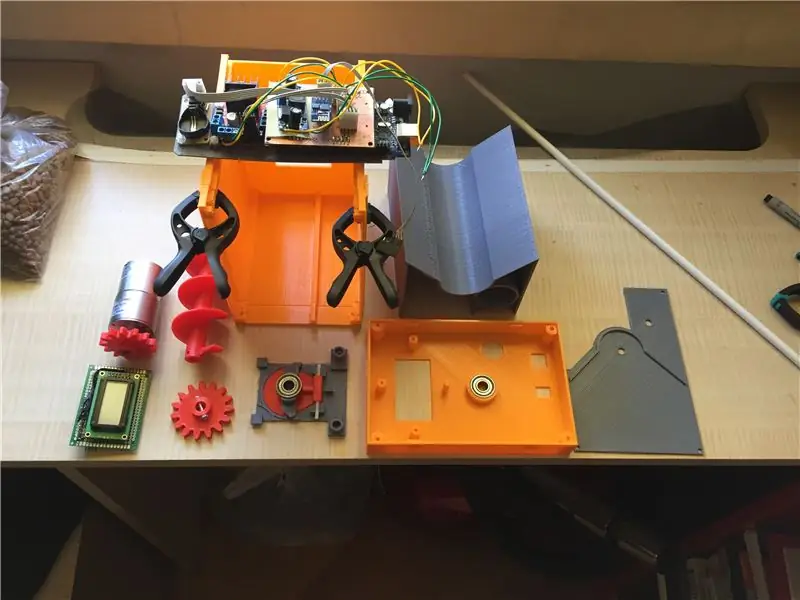
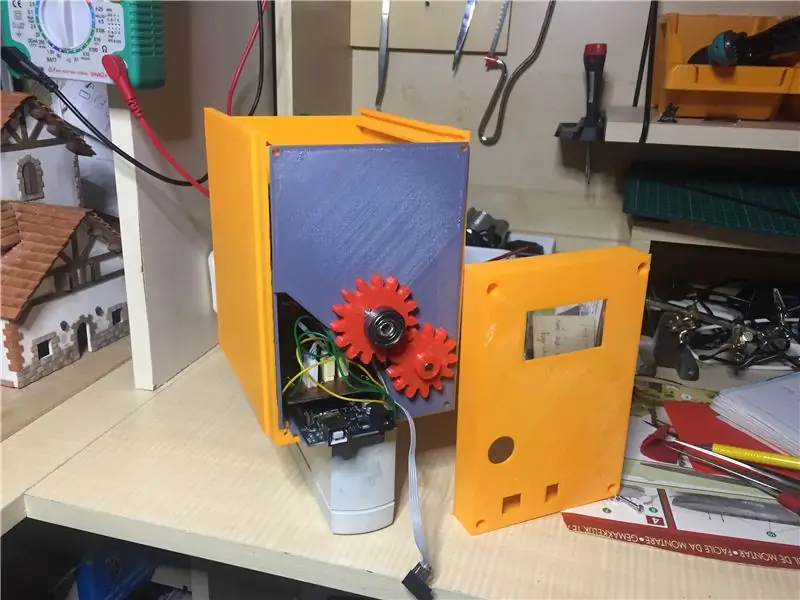
La vidéo d'assemblage détaillée et la vidéo du prototype fonctionnel sont ici
Conseillé:
Sourino - le meilleur jouet pour chats et enfants : 14 étapes (avec photos)
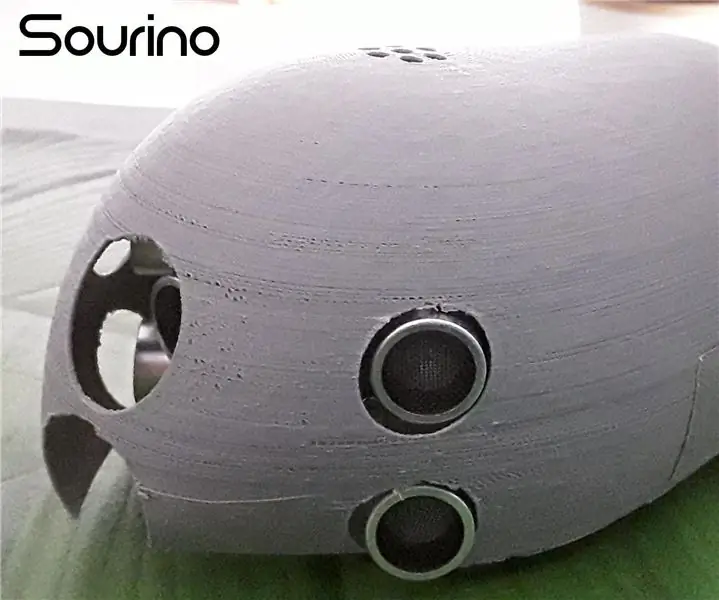
Sourino - le meilleur jouet pour chats et enfants : Imaginez de longues fêtes avec des enfants et un chat jouant à Sourino. Ce jouet émerveillera les chats et les enfants. Vous apprécierez de jouer en mode télécommandé et de rendre fou votre chat. En mode autonome, vous apprécierez de laisser Sourino se déplacer autour de votre chat
Distributeur automatique avec échelle pour confirmer l'article (Raspberry Pi): 5 étapes
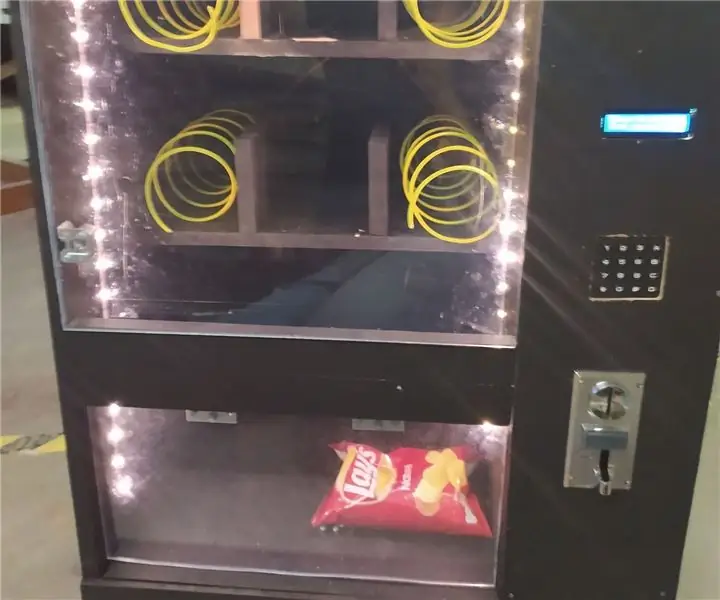
Distributeur automatique avec échelle pour confirmer la chute de l'article (Raspberry Pi): Bienvenue collègue fabricant, pour un projet scolaire, j'ai décidé de fabriquer un distributeur automatique de collations. Notre mission était de créer un dispositif recréable qui utilisait au moins 3 capteurs et 1 actionneur. Je suis allé faire un distributeur automatique en partie parce que j'avais accès à certains
Le distributeur automatique de pilules : 10 étapes (avec photos)
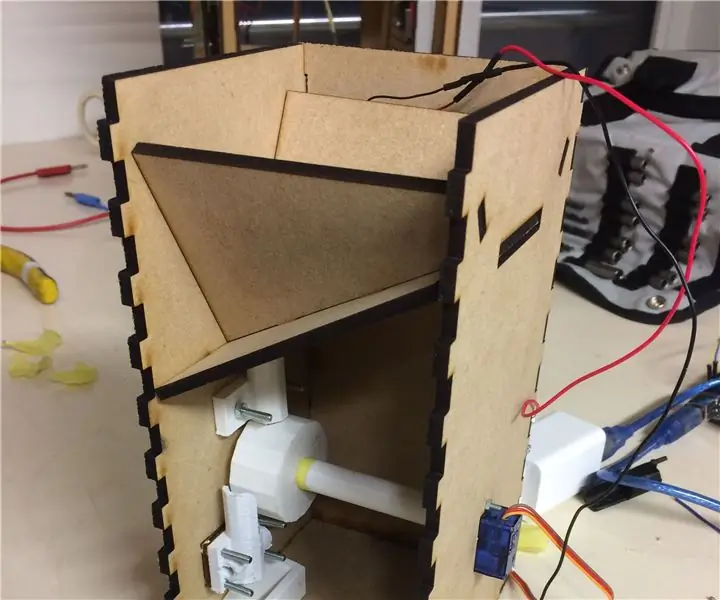
Le Pilulier Automatique : Nous sommes les premiers étudiants en Master Génie Electro-mécanique de la Faculté d'Ingénierie de Bruxelles (en abrégé "Bruface"). Il s'agit d'une initiative de deux universités situées au centre de Bruxelles : l'Université Libre de Bruxelles (UL
DISTRIBUTEUR DE PILULES AUTOMATIQUE : 14 étapes (avec photos)
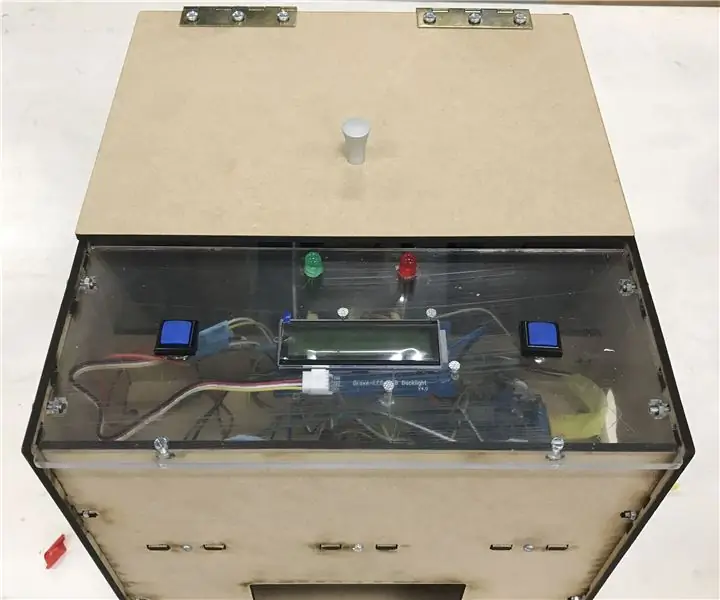
DISTRIBUTEUR DE PILULES AUTOMATIQUE : Il s'agit d'un robot distributeur de pilules capable de fournir au patient la quantité et le type de pilules médicamenteux corrects. Le dosage de la pilule s'effectue automatiquement à l'heure exacte de la journée, précédé d'une alarme. Lorsqu'elle est vide, la machine se recharge facilement
Distributeur automatique--Distributeur de bonbons-- Arduino Bluetooth contrôlé--DIY : 11 étapes (avec photos)
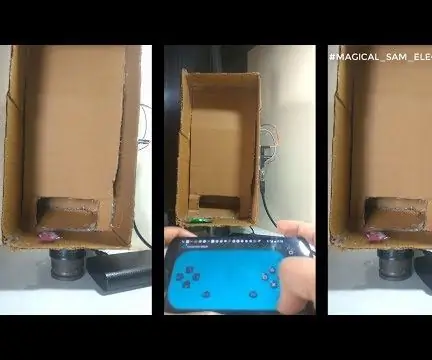
Distributeur automatique||Distributeur de bonbons|| Arduino Bluetooth Controlled||DIY: Dans ce instructable, je montre comment construire un distributeur automatique à l'aide d'un Arduino.FAIRE COMMENTER CE QUE VOUS PENSEZ À CE POINT D'INSTRUCTION, AFIN QUE JE PUISSE AMÉLIORER DANS MON AUTRE INSTRUCTABLEVoir le didacticiel vidéo pour une meilleure compréhension de l'ent