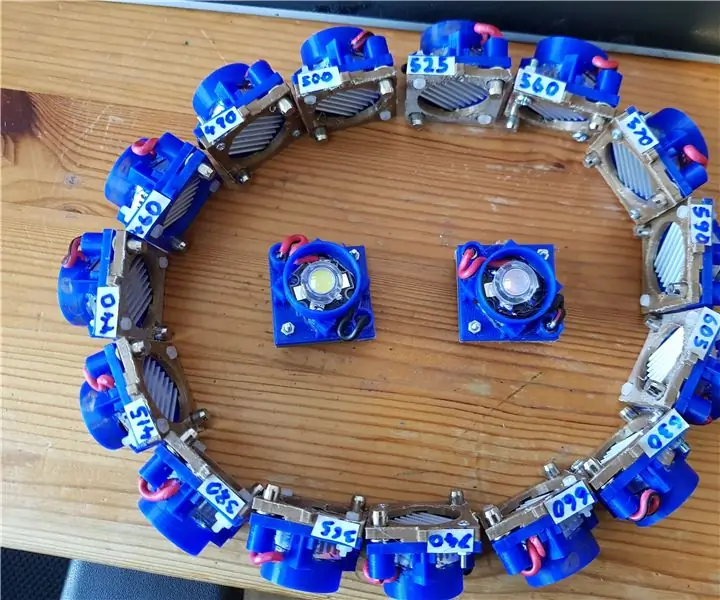
Table des matières:
- Fournitures
- Étape 1: Assemblage du boîtier
- Étape 2: Assemblage de la tête LED
- Étape 3: PCB principal
- Étape 4: Circuit d'encodeur
- Étape 5: Circuit d'alimentation à courant constant
- Étape 6: Circuit de gestion de l'alimentation
- Étape 7: Circuit de protection contre les pannes
- Étape 8: Assemblage
- Étape 9: Câble d'alimentation USB
- Étape 10: Option de modulation et couplage de fibre
- Étape 11: Alimentation de plusieurs LED
2025 Auteur: John Day | [email protected]. Dernière modifié: 2025-01-23 14:46
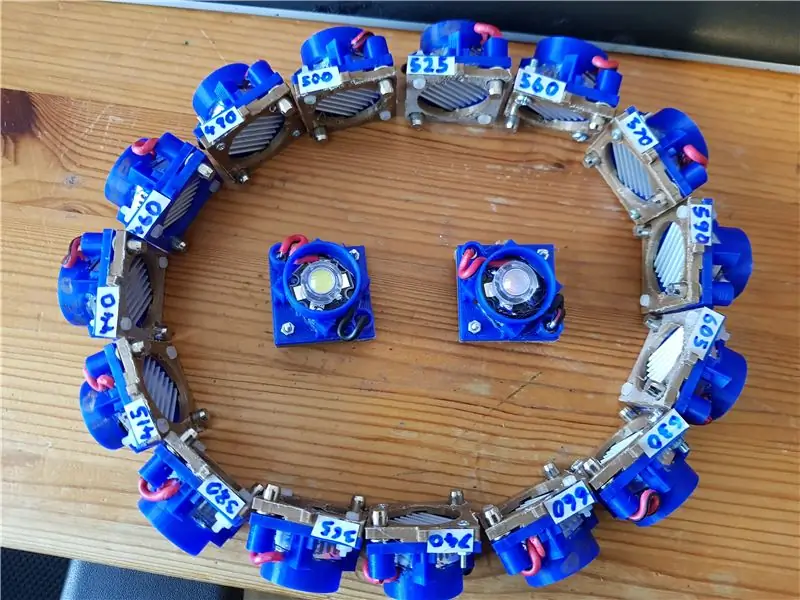
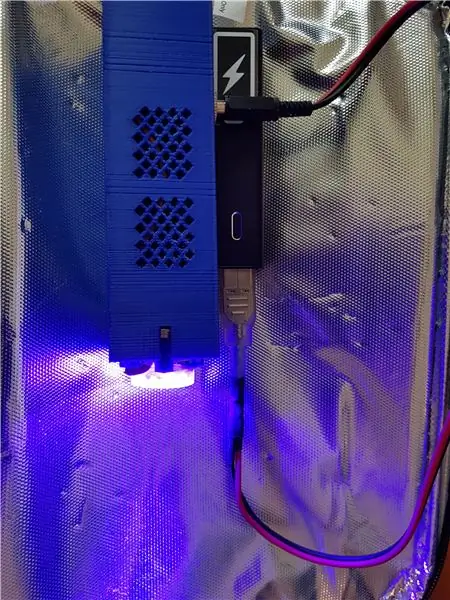
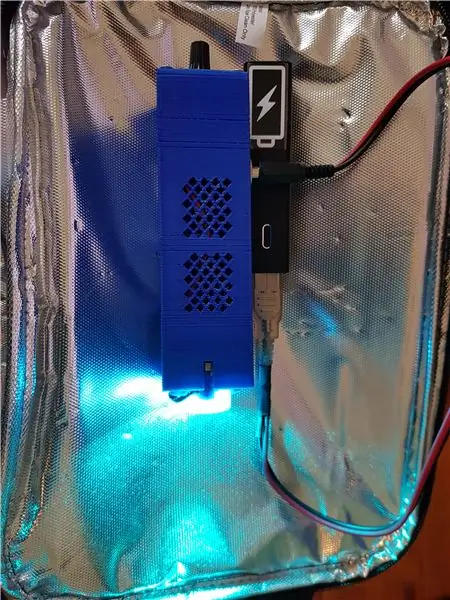
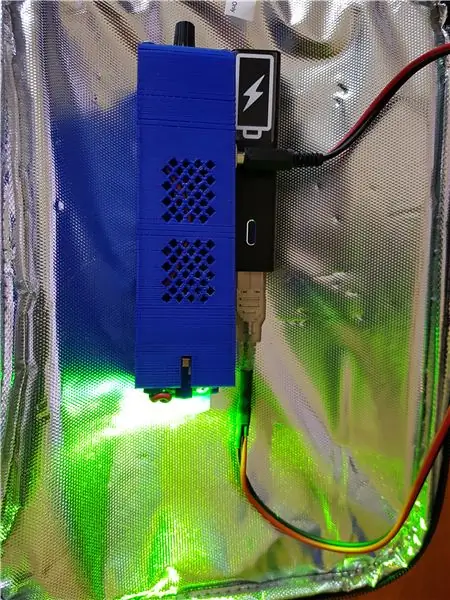
Nommée d'après Auguste Dupin, considéré comme le premier détective fictif, cette source de lumière portable fonctionne avec n'importe quel chargeur de téléphone ou bloc d'alimentation USB 5V. Chaque tête LED se clipse magnétiquement. Utilisant des LED étoiles 3W à faible coût, activement refroidies par un petit ventilateur, l'unité est compacte mais offre une large gamme de longueurs d'onde de haute intensité. Bien entendu, il prend également en charge les LED blanches pour un éclairage en couleur.
Les images ici montrent une sortie à 415 nm, 460 nm, 490 nm, 525 nm, 560 nm et 605 nm.
Cependant les LED utilisées sont 365nm, 380nm, 415nm, 440nm, 460nm, 490nm, 500nm, 525nm, 560nm, 570nm, 590nm, 605nm, 630nm, 660nm et 740nm. Sont également présentées une LED « blanc lumière du jour » et une LED à spectre complet PAR qui produit une lumière rose sans composante verte, destinée principalement aux applications horticoles.
Alimenté par une source de courant constant de précision à faible tension de chute, l'unité offre 100 réglages de luminosité via un encodeur rotatif et enregistre le dernier réglage de luminosité lorsqu'il est éteint, revenant ainsi automatiquement au dernier réglage de luminosité lorsqu'il est rallumé.
L'unité n'utilise pas PWM pour gérer la luminosité, il n'y a donc pas de scintillement, ce qui facilite son utilisation dans les situations où vous souhaitez photographier ou vidéo des images sans artefacts.
La source de courant constant dispose d'un amplificateur à large bande passante et d'un étage de sortie, permettant une modulation linéaire ou impulsionnelle jusqu'à plusieurs centaines de kilohertz ou même pour une modulation impulsionnelle jusqu'à près d'un mégahertz. Ceci est utile pour la mesure de fluorescence ou pour expérimenter la communication de données lumineuses, etc.
Vous pouvez également utiliser la source de courant constant pour piloter plusieurs LED. Par exemple, en utilisant une alimentation 24V, vous pouvez piloter 10 LED rouges avec une chute de tension de 2,2V par LED.
Notez que vous alimentez toujours le circuit de commande principal avec 5 V dans ce scénario, mais connectez le collecteur du transistor de puissance à une tension plus élevée. Pour plus d'informations, voir la dernière étape de cette instructable
Les applications incluent la médecine légale, la microscopie, l'examen de documents, la philatélie, l'entomologie, la fluorescence minérale, la photographie UV, IR et visuelle, la colorimétrie et la peinture lumineuse.
Fournitures
Dans presque tous les cas, il s'agit des fournisseurs que j'ai réellement utilisés, à l'exception d'un vendeur occasionnel qui ne stocke plus cet article ou qui n'est plus sur eBay/Amazon.
Cette liste couvre la plupart des éléments dont vous avez besoin, à l'exception des fils, des fiches d'alimentation mâles de 2,5 mm et des vis à métaux.
Dissipateurs thermiques de 20 mm pour les LED
www.ebay.co.uk/itm/Aluminium-Heatsink-for-…
La plupart des LED 3W sont alimentées par
futureeden.co.uk/
FutureEden fournit également les lentilles LED qui sont disponibles dans une gamme d'angles comprenant 15, 45 et 90 degrés. J'ai utilisé des lentilles de 15 degrés dans le prototype.
LED 560 nm et 570 nm
www.ebay.co.uk/itm/10pcs-3W-3-Watt-Green-5…
LED 490 nm
www.ebay.co.uk/itm/New-10pcs-3W-Cyan-490nm…
LED 365 nm
www.ebay.co.uk/itm/3W-365nm-UV-LED-ultravi…
Transistor de puissance D44H11
www.ebay.co.uk/itm/10-x-Fairchild-Semicond…
Goupilles d'étagère de 5 mm
www.amazon.co.uk/gp/product/B06XFP1ZGK/ref…
Ventilateur et radiateur
www.amazon.co.uk/gp/product/B07J5C16B9/ref…
PCB
www.amazon.co.uk/gp/product/B01M7R5YIB/ref…
Connecteurs magnétiques
www.ebay.co.uk/itm/Pair-of-Magnetic-Electr…
Prise de courant femelle 2,5 mm
www.ebay.co.uk/itm/2-5mm-x-5-5mm-METAL-PAN…
Diode Schottky BAT43
www.ebay.co.uk/itm/10-x-BAT43-Small-Signal…
Kit transistor petit signal (y compris BC327/337 utilisé dans ce projet)
www.ebay.co.uk/itm/200PCS-10-Value-PNP-NPN…
Encodeur rotatif (le vendeur que j'ai utilisé n'est plus sur eBay mais c'est le même appareil)
www.ebay.co.uk/itm/Rotary-Encoder-5-pin-To…
X9C104P (il s'agit d'un autre vendeur)
www.ebay.co.uk/itm/X9C104P-DIP-8-Intégrer…
TLV2770
www.mouser.co.uk/ProductDetail/texas-instr…
Moniteur de courant USB (en option)
www.amazon.co.uk/gp/product/B01AW1MBNU/ref…
Étape 1: Assemblage du boîtier
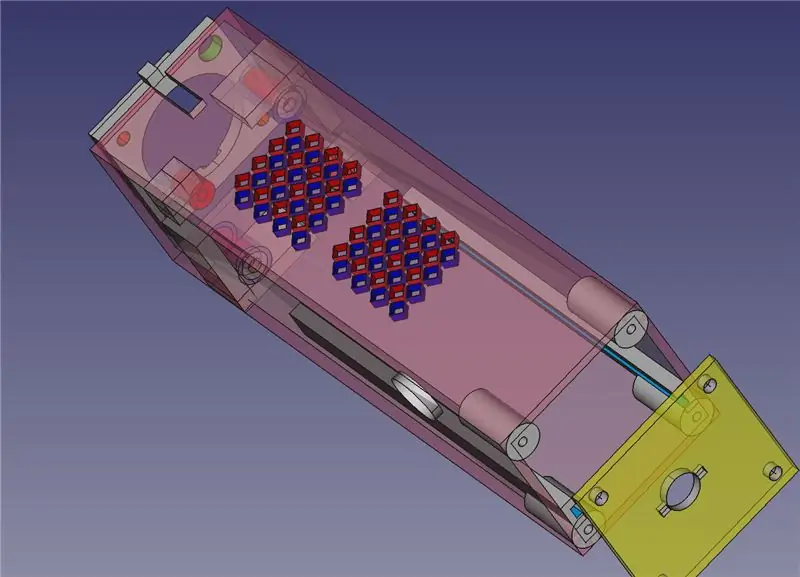
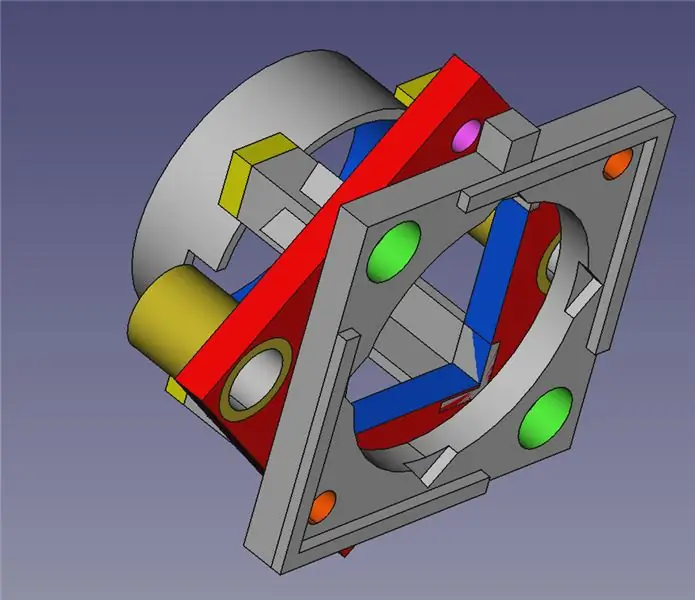
Le boîtier de l'unité principale et la tête LED sont imprimés en 3D. Une petite plaque arrière plate se fixe à l'arrière du boîtier pour soutenir l'encodeur. L'alimentation est fournie via une prise de courant standard de 2,5 mm. Un câble USB standard est coupé pour faire le câble d'alimentation.
Tous les articles sont imprimés en PLA avec un remplissage à 100 % et une hauteur de couche de 0,2 mm. Les fichiers STL sont inclus en tant que pièces jointes.
Imprimez l'assemblage du boîtier verticalement avec l'arrière du boîtier sur la plaque de base. Aucun support n'est requis.
Étape 2: Assemblage de la tête LED
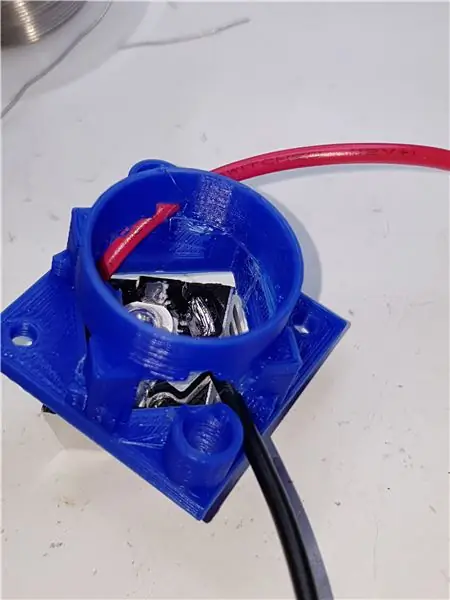
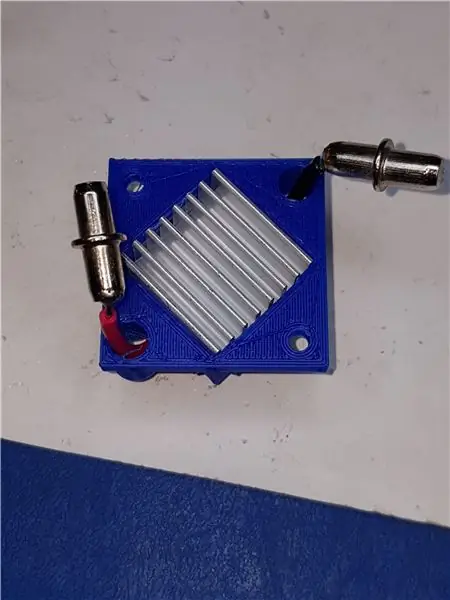
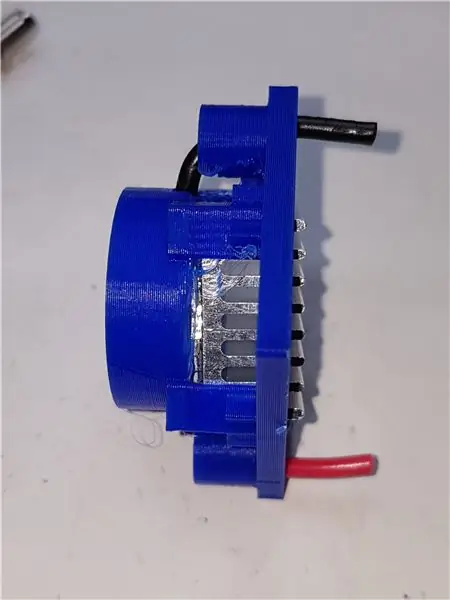
Chaque tête LED comprend deux pièces imprimées en 3D, la tête supérieure et la plaque de fixation arrière. Imprimez-les en PLA à 100% de remplissage et à une hauteur de couche de 0,2 mm. Aucun support n'est requis. La plaque de fixation arrière doit être imprimée avec la surface arrière plate touchant la plaque de base.
Notez que les images stl montrées précédemment ont la plaque arrière orientée à 180 degrés - le côté plat est la surface extérieure de la plaque arrière lorsque vous boulonnez les éléments ensemble.
Chaque assemblage de tête dispose ensuite d'un dissipateur thermique de 20 mm x 10 mm avec la presse fixée par LED installée dans l'assemblage supérieur. Les photos montrent comment l'assembler. Commencez par décoller le papier du tampon adhésif et collez la LED en prenant soin de maintenir le dissipateur thermique LED entièrement dans le contour du dissipateur thermique de 20 mm.
Soudez ensuite deux fils à la LED, puis poussez le dissipateur thermique dans l'assemblage de la tête supérieure, en prenant soin de vous assurer que les ailettes du dissipateur thermique sont orientées comme indiqué sur les photos. Il s'agit de maximiser le flux d'air pour le refroidissement.
Une fois que vous avez installé le dissipateur thermique, tirez les fils à travers et coupez comme indiqué sur la photo, en laissant environ 3/4 de pouce de fil. Dénudez et étamez les extrémités des fils.
La tête LED se connecte au boîtier via deux broches constituées de broches de tablette en acier nickelé. Ils sont parfaits pour le travail car ils ont une bride qui nous permet de les verrouiller en place.
À l'aide d'une pointe de fer à souder ciseau de plus grand diamètre, étamez le haut de chaque broche. Tenez les broches dans un étau ou idéalement dans l'un de ces petits gadgets d'établi, comme indiqué - ils sont également très pratiques pour fabriquer des câbles.
Attachez ensuite les fils aux broches, en vous assurant que les fils pointent vers le haut, comme illustré. Laisser refroidir.
Une fois les broches refroidies, fixez la plaque de fixation arrière à l'aide de 2 vis à métaux et écrous M2 de 12 mm. Assurez-vous avant de faire cela que les trous de montage de la plaque arrière ont été nettoyés avec un foret hélicoïdal ou un alésoir conique. Les broches en acier doivent pouvoir osciller légèrement. Ceci est important pour s'assurer que les contacts magnétiques sont fiables.
Remarque: j'ai utilisé des vis et des écrous en nylon pour certaines unités, puis en acier pour les autres. Ceux en acier ont probablement besoin de rondelles de blocage, car ils ont par ailleurs tendance à se dévisser avec le temps; les vis en nylon ont tendance à avoir plus de friction et c'est moins un problème.
En option, attachez une lentille à la LED si vous souhaitez collimater le faisceau, qui est par ailleurs assez large.
Étape 3: PCB principal
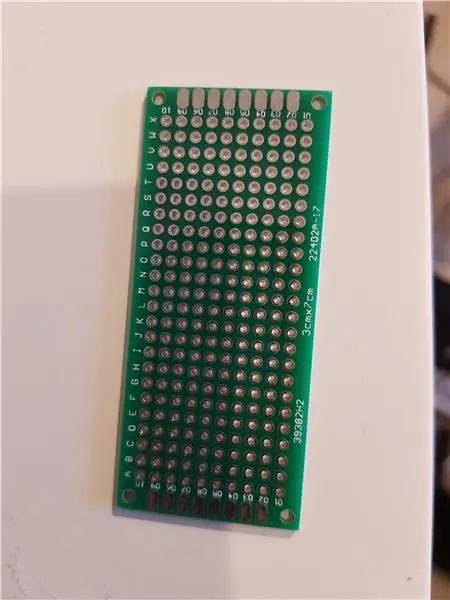
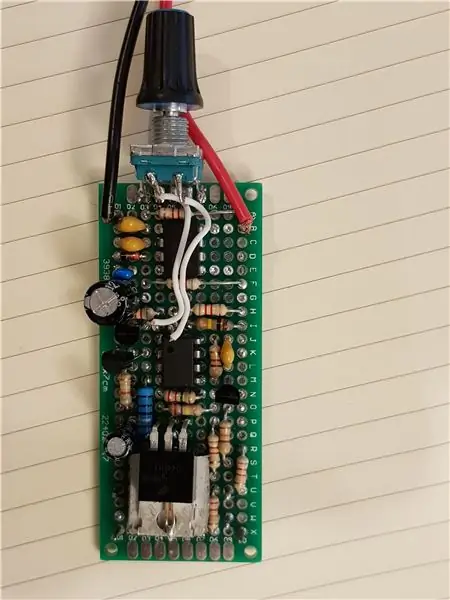
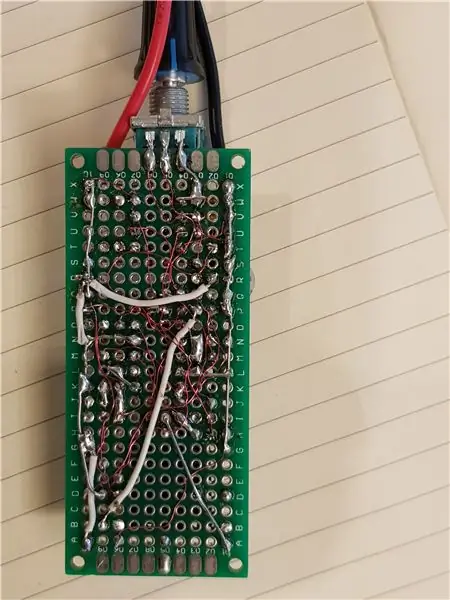
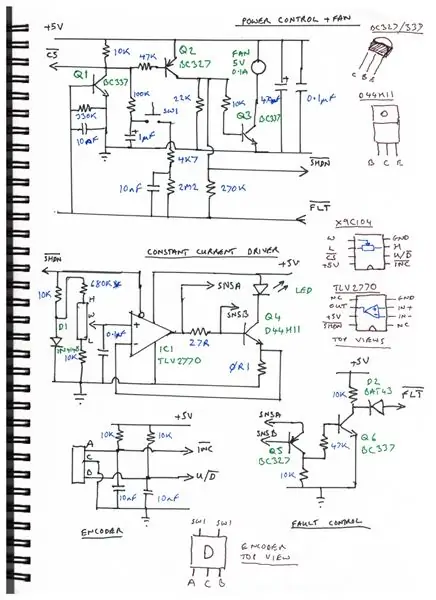
Le circuit imprimé principal est construit à l'aide d'une carte matricielle de 30 x 70 mm. Ce sont des panneaux en fibre de verre de haute qualité largement disponibles avec une matrice de trous traversants de 0,1 pouce.
Le câblage point à point utilise ce qu'on appelle un « fil à crayon », qui est un fil de cuivre émaillé d'environ 0,2 mm. L'isolation fond avec une panne de fer à souder normale.
L'encodeur rotatif est soudé directement à l'extrémité de la carte. Notez que les broches de l'encodeur sont câblées au bas de la carte.
Dans les étapes ci-dessous, vous allez construire des parties individuelles de l'ensemble du circuit et les tester avant de continuer. Cela garantit que le circuit imprimé fini doit fonctionner correctement.
Les photographies montrent la planche lors du montage. Le fil de crayon peut être vu à l'arrière, reliant la plupart des composants. Un fil plus épais est utilisé lorsque des courants plus élevés sont impliqués. Certains fils de composants coupés sont utilisés pour créer un rail d'alimentation et de terre en haut et en bas de la carte.
Remarque: l'espace est restreint. Montez les résistances verticalement pour économiser de l'espace. La disposition ici "a évolué" au fur et à mesure que la carte était assemblée et j'étais un peu optimiste quant à l'espace requis et j'aurais dû monter toutes les résistances verticalement et non horizontalement comme indiqué.
Les connexions sont effectuées à l'aide de « veropins », mais vous pouvez également utiliser une boucle de fil de composant, avec les extrémités évasées en dessous; Cependant, cela prend deux trous par connexion plutôt qu'un avec une broche.
Étape 4: Circuit d'encodeur
J'ai dessiné le circuit sous forme de plusieurs schémas séparés. C'est pour que vous puissiez voir clairement ce que fait chaque partie. Vous devez construire le circuit par étapes, en vérifiant que chaque partie fonctionne correctement avant d'ajouter la partie suivante. Cela garantit que l'ensemble fonctionnera correctement sans beaucoup de dépannage fastidieux.
Avant de commencer, un mot sur la soudure. J'utilise de la soudure au plomb, pas du sans plomb. En effet, la soudure sans plomb est beaucoup plus difficile à travailler dans les scénarios de soudure à la main. Il se conserve mal et est généralement douloureux. La soudure au plomb est assez sûre et vous ne serez pas exposé à des fumées dangereuses lorsque vous travaillez avec. Faites preuve de bon sens et lavez-vous les mains après avoir soudé et avant de manger, de boire ou de fumer. Amazon vend des rouleaux de soudure au plomb de bonne qualité.
L'interface de l'encodeur
C'est assez simple. L'encodeur a trois broches, A, B et C (communes). Comme vous pouvez le voir, nous mettons la broche C à la terre et nous remontons les broches A et B via des résistances de 10K. Ensuite, nous ajoutons des condensateurs de 10 nF à la terre pour lisser le rebond de contact, ce qui peut provoquer un fonctionnement erratique.
Les broches A et B se connectent ensuite aux broches INC et U/D sur le circuit intégré du pot numérique. (X9C104). Connectez ce circuit et câblez également les broches d'alimentation et de terre du X9C104. Ajoutez également les condensateurs de découplage de puissance 470 uF et 0,1 uF.
Les broches de l'encodeur doivent être soudées au bas du circuit imprimé; le trou de la plaque arrière s'alignera alors avec l'arbre du codeur.
Câblez temporairement la broche CS du X9C104P à +5V. Nous allons le connecter à une autre partie du circuit plus tard.
Connectez maintenant 5 V au circuit et à l'aide d'un multimètre, vérifiez que la résistance entre les broches H et W du X9C104P varie en douceur entre presque 0 ohms et 100 K ohms lorsque vous faites tourner l'encodeur.
Étape 5: Circuit d'alimentation à courant constant
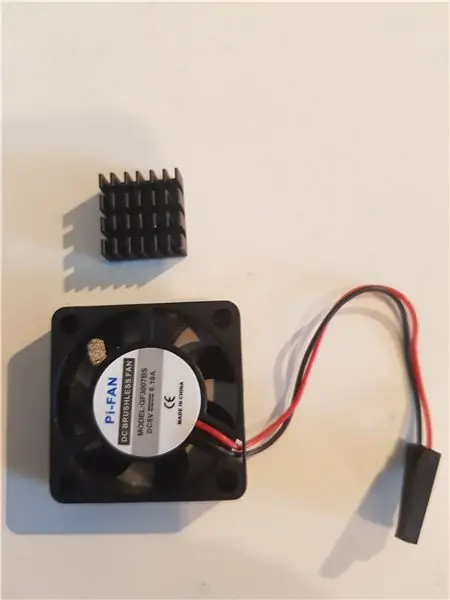
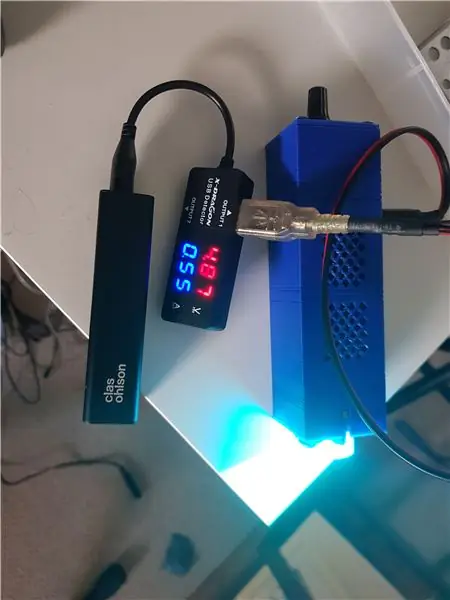
Une fois que vous êtes sûr que les circuits du codeur fonctionnent, il est temps de construire la section d'alimentation à courant constant. Connectez l'alimentation et la terre de l'amplificateur opérationnel TLV2770, puis câblez comme indiqué, en vous connectant aux broches H, W et L du X9C104P.
Assurez-vous de connecter la résistance de détection de courant de 0,1 ohm directement à la broche de terre du TLV2770, puis connectez en étoile les composants restants à la terre à ce point (cathode 1N4148, résistance 10K, condensateur 0,1 uF). Connectez ensuite ce point de masse au rail de masse sur le circuit imprimé. Cela garantit que les petites résistances entre le rail de terre et la résistance de détection de courant ne sont pas vues par l'amplificateur opérationnel comme des tensions de détection erronées. N'oubliez pas qu'à 750 mA, la tension aux bornes de la résistance de 0,1 ohm n'est que de 75 mV.
Connectez temporairement la ligne SHDN au +5V. Nous allons le connecter à une autre partie du circuit plus tard.
Le ventilateur de refroidissement que nous utilisons est destiné à un Raspberry Pi. Il est livré, de manière pratique, avec un ensemble de dissipateurs thermiques, dont l'un sera utilisé pour le transistor de puissance principal.
Le transistor de puissance D44H11 doit être monté perpendiculairement à la carte, collé au plus grand dissipateur thermique fourni avec le kit de ventilateur Raspberry Pi.
La résistance 680K peut avoir besoin d'être ajustée pour s'assurer que le courant maximum à travers les LED ne dépasse pas 750mA.
Connectez à nouveau +5V et une LED d'alimentation, montée sur un dissipateur thermique. Vérifiez maintenant que vous pouvez facilement changer le courant à travers la LED en tournant l'encodeur. Le courant minimum est choisi pour être d'environ 30 mA, ce qui devrait être suffisant pour garantir que la plupart des blocs d'alimentation de téléphone portable 5 V ne s'éteindront pas automatiquement à une luminosité minimale.
Le moniteur de courant USB en option est un accessoire utile ici, mais si vous l'utilisez, vous devrez évidemment d'abord brancher le câble d'alimentation, comme indiqué dans la section suivante.
Remarque: les LED à longueur d'onde plus courte deviendront assez chaudes à un courant élevé car nous ne refroidissons pas encore le dissipateur thermique par ventilateur, alors gardez le temps d'exécution assez court (quelques minutes) pendant les tests.
Comment ça marche: la tension aux bornes de la résistance de détection de courant est comparée à la tension de référence. L'ampli-op ajuste sa sortie pour s'assurer que les deux entrées sont à la même tension (en ignorant la tension de décalage d'entrée de l'ampli-op). Le condensateur de 0,1 uF à travers le potentiomètre numérique sert à deux fins; il filtre le bruit de la pompe de charge à 85 kHz du dispositif X9C104 et garantit également qu'à la mise sous tension, le courant de demande est nul. Une fois que l'amplificateur opérationnel et la rétroaction se sont stabilisés, la tension aux bornes du condensateur augmentera jusqu'à la tension de demande. Cela empêche les pointes de courant de démarrage à travers la charge.
Le transistor D44H11 a été choisi car il a des valeurs nominales de courant adéquates et un gain minimum élevé d'au moins 60, ce qui est bon pour un transistor de puissance. Il a également une fréquence de coupure élevée qui facilite la modulation à grande vitesse de la source de courant si nécessaire.
Étape 6: Circuit de gestion de l'alimentation
Le circuit de gestion de l'alimentation transforme principalement l'interrupteur-poussoir à action momentanée de l'encodeur rotatif en un interrupteur d'alimentation à bascule.
Les transistors BC327 et BC337 sont utilisés car ils ont un gain assez élevé et un courant de collecteur maximal de 800 mA, ce qui est pratique pour le commutateur de ventilateur où le ventilateur consomme environ 100 mA. J'ai acheté un kit bon marché de divers transistors à petit signal qui comprend une large gamme de dispositifs utiles. Notez que dans le prototype, ces transistors ont le suffixe -40 indiquant le bac de gain le plus élevé. Bien que je doute que cela ait beaucoup d'importance et que vous devriez obtenir des appareils similaires si vous achetez le même kit, soyez-en conscient.
L'alimentation est contrôlée en basculant la broche SHDN sur l'amplificateur opérationnel TLV2770. Lorsque la broche SHDN est basse, l'opamp est désactivé et lorsqu'elle est haute, l'opamp fonctionne normalement.
Le circuit de gestion de l'alimentation contrôle également la ligne CS sur le potentiomètre numérique X9C104. Lorsque l'alimentation est coupée, la ligne CS passe au niveau haut, garantissant que le réglage actuel du pot est réécrit dans sa mémoire flash non volatile.
Comment ça marche: initialement la jonction de la résistance 100K et du condensateur 1uF est à +5V. Lorsque l'interrupteur momentané est enfoncé, la tension de haut niveau est transférée via le condensateur de 10 nF à la base de Q1, qui s'allume. Ce faisant, il tire ensuite le collecteur vers le bas, ce qui entraîne également l'activation de Q2. Le circuit se verrouille ensuite via la résistance de retour de 270K, garantissant que Q1 et Q2 restent tous les deux activés et que la sortie SHDN est élevée.
À ce stade, la jonction de la résistance 100K et du capuchon 1uF est maintenant abaissée par Q1. Par conséquent, lorsque l'interrupteur momentané est à nouveau enfoncé, la base de Q1 est tirée vers le bas, l'éteignant. Le collecteur monte à +5V en éteignant Q2 et la sortie SHDN passe maintenant au niveau bas. À ce stade, le circuit revient à son état initial.
Assemblez le circuit de gestion de l'alimentation et connectez-y l'interrupteur momentané de l'encodeur. Vérifiez que SHDN bascule à chaque fois que vous appuyez sur le commutateur et que lorsque SHDN est bas, CS est haut et vice-versa.
Connectez temporairement le ventilateur de refroidissement au collecteur de Q3 et au rail +5V (qui est le fil positif du ventilateur) et vérifiez que lorsque SHDN est élevé, le ventilateur s'allume.
Connectez ensuite le circuit de gestion de l'alimentation à l'alimentation à courant constant et connectez CS au potentiomètre numérique X9C104P, en supprimant la liaison de masse temporaire. Connectez SHDN au TLV2770 et supprimez également le lien temporaire vers cette broche.
Vous devriez maintenant être en mesure de confirmer que le circuit s'allume correctement et s'allume et s'éteint lorsque l'interrupteur de l'encodeur est enfoncé.
Étape 7: Circuit de protection contre les pannes
Comme la plupart des alimentations à courant constant, il y a un problème si la charge est déconnectée puis reconnectée. Lorsque la charge est déconnectée, Q4 sature alors que l'amplificateur opérationnel tente de faire passer le courant à travers la charge. Lorsque la charge est reconnectée, parce que Q4 est complètement activé, un courant transitoire élevé peut la traverser pendant plusieurs microsecondes. Bien que ces leds 3W soient assez tolérantes aux transitoires, elles dépassent toujours les valeurs nominales de la fiche technique (1A pour 1ms) et si la charge était une diode laser sensible, elle pourrait facilement être détruite.
Le circuit de protection contre les défauts surveille le courant de base via Q4. Lorsque la charge est déconnectée, elle atteint environ 30 mA, ce qui provoque une augmentation suffisante de la tension aux bornes de la résistance de 27 ohms pour activer Q5, ce qui entraîne l'activation de Q6 et son collecteur tombe alors presque à la terre. La diode Schottky (choisie parce que sa tension directe de 0,4 V est inférieure aux 0,7 V requis pour allumer un transistor) abaisse ensuite la ligne FLT, éteignant Q1 et Q2 et coupant ainsi l'alimentation.
Cela garantit que la charge ne peut jamais être connectée sous tension, évitant ainsi les transitoires potentiellement dommageables.
Étape 8: Assemblage
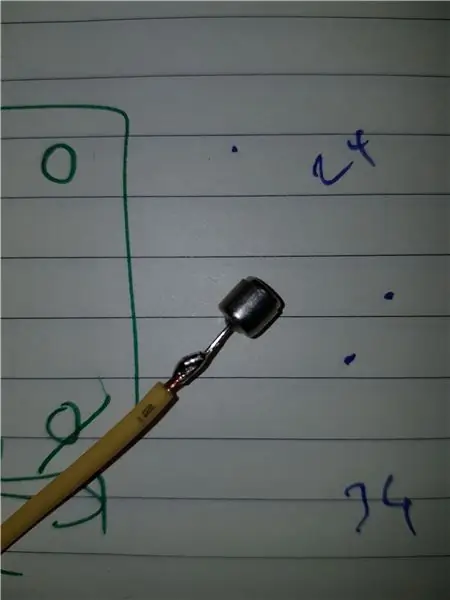
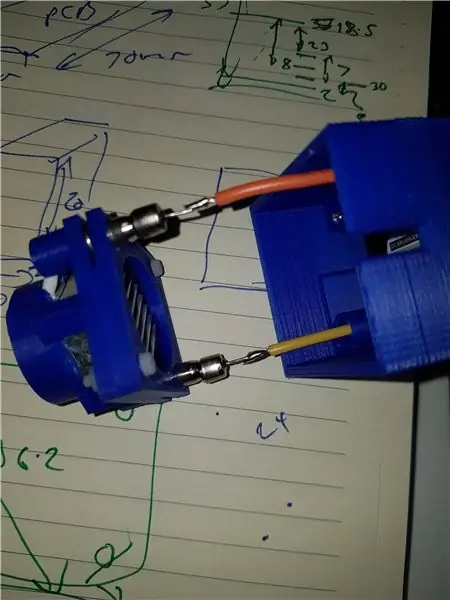
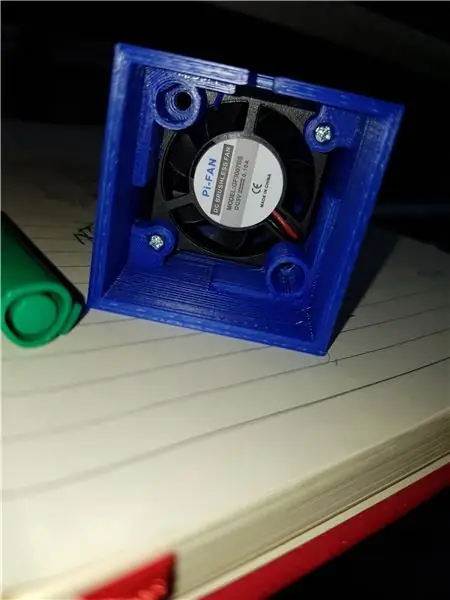
Soudez les coupleurs magnétiques à une courte longueur de fil raisonnablement solide (environ 6 pouces de long), en vous assurant que le fil passera dans les trous du boîtier.
Assurez-vous que les trous du boîtier sont propres - utilisez une perceuse hélicoïdale pour vous en assurer, et une perceuse plus petite pour vous assurer que les trous de fil à l'arrière sont également propres.
Maintenant, à l'aide d'une tête LED, fixez les coupleurs aux broches de la tête et insérez-les dans le boîtier. La tête LED doit s'adapter de telle sorte que lorsque vous regardez la rainure de clavette, il y ait un petit espace entre la rainure de clavette et le boîtier. Une fois que vous êtes sûr que les coupleurs s'ajustent correctement, placez une petite goutte d'époxy à l'arrière de chacun, insérez-le avec la tête LED et placez-le à l'écart pendant que la colle durcit. J'ai câblé mes assemblages de tête LED de sorte qu'avec la plaque arrière de l'assemblage de tête tournée vers vous et la rainure de clavette pointant vers le haut, la connexion positive se trouve sur votre droite.
Une fois la colle durcie, retirez la tête puis installez le ventilateur, avec l'étiquette visible, c'est-à-dire que le flux d'air pousse l'air sur le dissipateur thermique de la tête. J'ai utilisé deux vis à métaux M2 X 19 mm et un tournevis pour monter le ventilateur, c'est délicat mais faites-le glisser par l'arrière du boîtier et vous devriez alors pouvoir tout aligner et fixer.
Vous pouvez maintenant monter la prise d'alimentation de 2,5 mm et connecter tous les fils au PCB, en laissant suffisamment de mou pour que vous puissiez facilement le câbler, puis le glisser dans le boîtier sur les rails imprimés dans le boîtier.
L'assemblage de la plaque arrière est fixé avec quatre petites vis autotaraudeuses. Notez que la position de l'arbre du codeur n'est pas tout à fait centrée sur la plaque, alors assurez-vous de la faire pivoter jusqu'à ce que les trous de vis s'alignent.
Étape 9: Câble d'alimentation USB
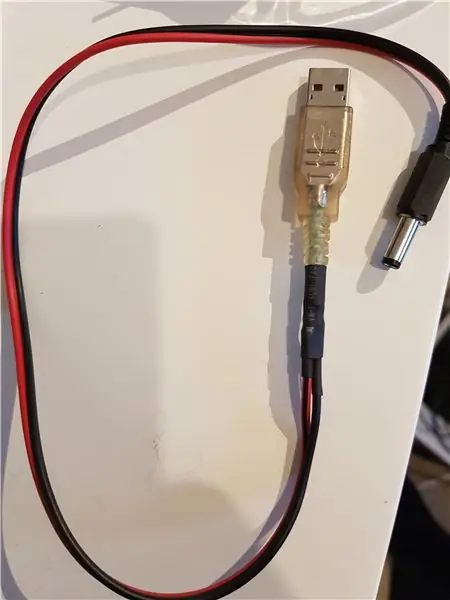
Le câble d'alimentation est fabriqué à partir d'un câble USB bon marché. Coupez le câble à environ 1 pouce de la plus grande prise USB et dénudez-le. Les fils rouge et noir sont l'alimentation et la masse. Connectez-y un câble en forme de 8 plus épais, en utilisant une gaine thermorétractable pour isoler, puis à l'autre extrémité, soudez une prise d'alimentation standard de 2,5 mm.
Nous avons coupé le câble USB parce que les fils sont trop fins pour transporter le courant et sinon, la tension chutera trop.
Étape 10: Option de modulation et couplage de fibre
Pour moduler la source de courant, déconnectez le condensateur 0,1 uF et la broche W de l'entrée non inverseuse de l'amplificateur opérationnel et connectez cette entrée à la terre via une résistance de 68 ohms. Connectez ensuite une résistance de 390 ohms à l'entrée non inverseuse. L'autre extrémité de la résistance est alors l'entrée de modulation, avec 5V conduisant la LED à plein courant. Vous pouvez installer quelques cavaliers sur la carte pour faciliter le passage de l'encodeur à la modulation externe.
Vous pouvez utiliser le STL du projet Angstrom pour les coupleurs de fibre 3 mm si vous souhaitez connecter les LED à la fibre, par exemple pour la microscopie, etc.
Étape 11: Alimentation de plusieurs LED
Vous pouvez utiliser le pilote à courant constant pour piloter plusieurs LED. Les LED ne peuvent pas être connectées en parallèle car une LED prendrait la majeure partie du courant. Par conséquent, vous connectez les LED en série, puis vous connectez l'anode de la LED supérieure à une source d'alimentation appropriée, en laissant le circuit de commande principal fonctionner toujours sur 5V.
Il est plus facile dans la plupart des cas d'utiliser une alimentation séparée pour les LED et de laisser tout le reste fonctionner sur un chargeur de téléphone standard.
Pour calculer la tension, prenez le nombre de LED et multipliez par la chute de tension pour chaque LED. Prévoyez ensuite une marge d'environ 1,5 V. Par exemple, 10 LED avec une chute de tension de 2,2 V chacune nécessitent 22 V, donc une alimentation 24 V fonctionnerait bien.
Vous devez vous assurer que la tension aux bornes du transistor de puissance n'est pas trop élevée, sinon elle deviendra trop chaude - comme conçu ici, elle chute de près de 3 V dans le pire des cas (conduisant une LED infrarouge avec une faible tension directe) donc c'est le maximum que vous devriez viser à moins que vous ne vouliez utiliser un dissipateur thermique plus grand. Dans tous les cas, je maintiendrais la tension à moins de 10 V, car vous commencez à entrer dans les limites de courant en fonction de la zone de fonctionnement sans transistor.
Notez que les émetteurs à longueur d'onde plus courte ont des tensions directes plus élevées, les LED 365 nm chutant de près de 4 V. La connexion de 10 d'entre eux en série entraînerait une chute de 40 V et une alimentation standard de 48 V nécessiterait un dissipateur thermique plus grand sur le transistor de puissance. Alternativement, vous pouvez utiliser plusieurs diodes 1A en série avec les LED pour faire chuter la tension supplémentaire à 0,7 V par diode, disons 8 pour chuter de 5,6 V, puis cela ne laisse que 2,4 V aux bornes du transistor de puissance.
Je me méfierais d'utiliser des tensions plus élevées que cela. Vous commencez à avoir des problèmes de sécurité si vous entrez en contact avec l'alimentation. Assurez-vous d'installer un fusible approprié en série avec les LED; comme conçu ici, l'alimentation 5V a une limitation de courant sûre et nous n'en avons pas besoin, mais dans ce scénario, nous voudrions certainement une protection contre un court-circuit. Notez que court-circuiter une chaîne de LED comme celle-ci entraînera probablement une fusion assez spectaculaire du transistor de puissance, alors soyez prudent !. Si vous souhaitez alimenter plus de LED, vous avez probablement besoin d'un ensemble parallèle de sources de courant. Vous pouvez utiliser plusieurs copies du pilote à courant constant (avec son propre circuit de protection contre les pannes) et partager un encodeur commun, un circuit de commande de puissance et une référence de tension entre eux, chaque copie aura son propre transistor de puissance et pilotera, disons, 10 LED. L'ensemble du circuit peut être mis en parallèle car les pilotes à courant constant gèrent chacun une chaîne de LED dans ce scénario.
Conseillé:
Rhéomètre à faible coût : 11 étapes (avec photos)
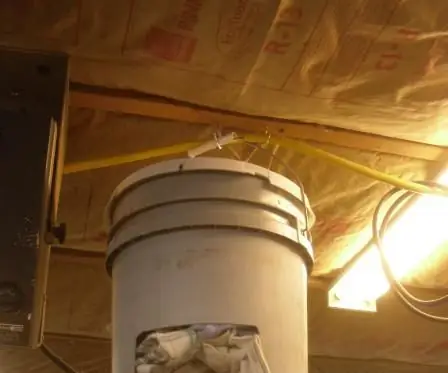
Rhéomètre à faible coût : le but de cette instructable est de créer un rhéomètre à faible coût pour trouver expérimentalement la viscosité d'un fluide. Ce projet a été créé par une équipe d'étudiants de premier cycle et des cycles supérieurs de l'Université Brown dans la classe Vibration of Mechanical Systems
LUMIÈRE LED PORTABLE (Simple, Faible Coût et Magnifiquement Conçu): 5 Étapes (avec Photos)
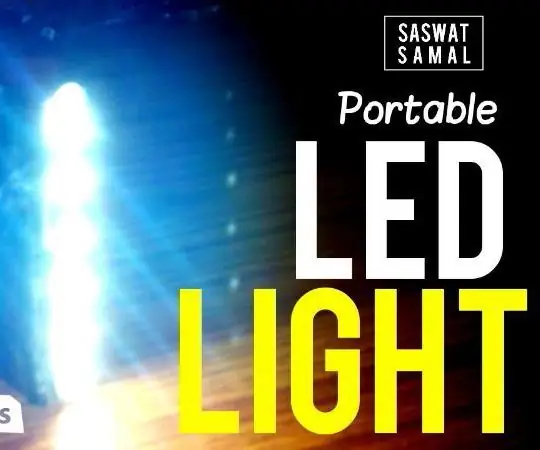
LUMIÈRE LED PORTABLE (simple, économique et magnifiquement conçue) : il s'agit d'un projet très économique et facile à réaliser. Il peut être fabriqué facilement avec un coût inférieur à 100 (moins de 2 $). Cela peut être utilisé dans de nombreux endroits comme en cas d'urgence, en cas de panne de courant, lorsque vous êtes à l'extérieur….bla..bla.. bla..Alors.. Qu'est-ce que tu
Générateur de formes d'onde à faible coût (0 - 20 MHz) : 20 étapes (avec images)
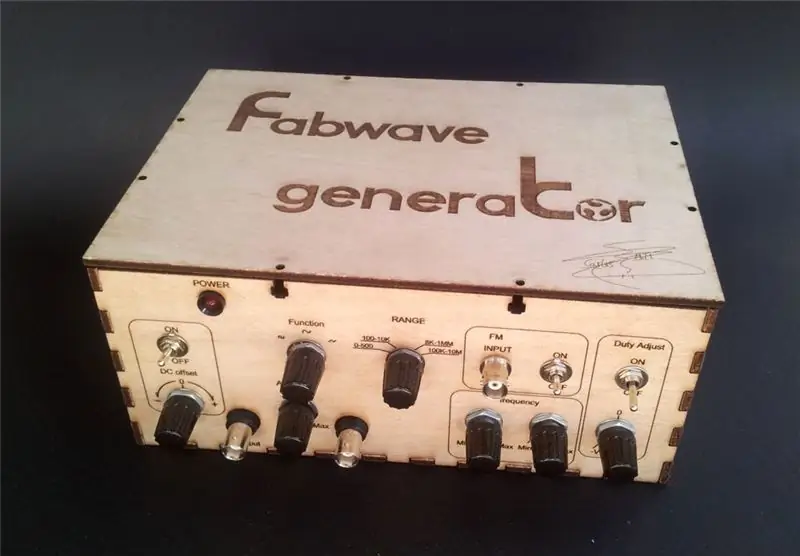
Générateur de forme d'onde à faible coût (0 - 20MHz): ABSTRATH Ce projet vient de la nécessité d'obtenir un générateur d'onde avec une bande passante supérieure à 10 Mhz et une distorsion harmonique inférieure à 1%, le tout avec un prix de revient bas. Ce document décrit une conception d'un générateur d'ondes avec une bande passante supérieure
Mesure des longueurs d'onde laser : 4 étapes (avec photos)
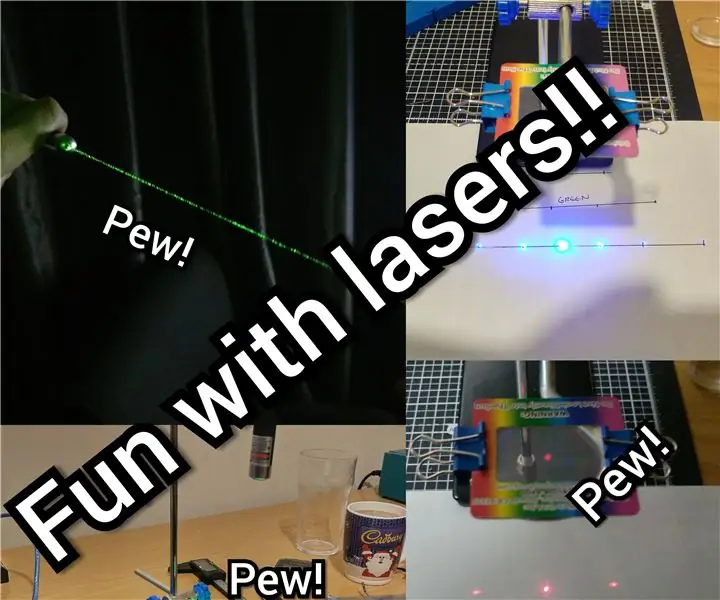
Mesure des longueurs d'onde laser : Salut à tous, bienvenue dans un autre instructable ! Cette fois, je voulais faire un instructable vraiment facile que vous pouvez faire comme projet de soirée ou de week-end. Dans le cadre de mon apprentissage continu de la spectrophotométrie, j'ai expérimenté des réseaux de diffraction et
UDuino : Carte de développement compatible Arduino à très faible coût : 7 étapes (avec photos)
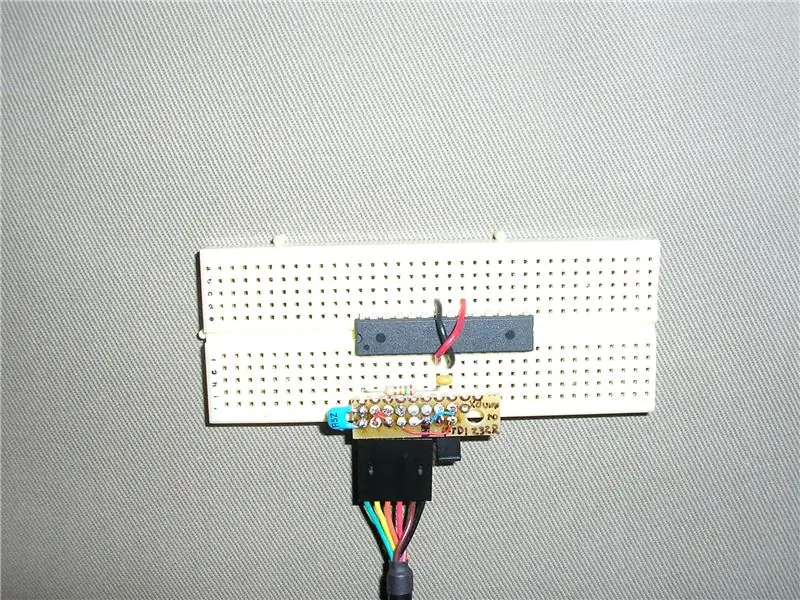
UDuino : Carte de développement compatible Arduino à très faible coût : les cartes Arduino sont idéales pour le prototypage. Cependant, ils deviennent assez chers lorsque vous avez plusieurs projets simultanés ou que vous avez besoin de beaucoup de cartes contrôleurs pour un projet plus important. Il existe d'excellentes alternatives moins chères (Boarduino, Freeduino) mais e