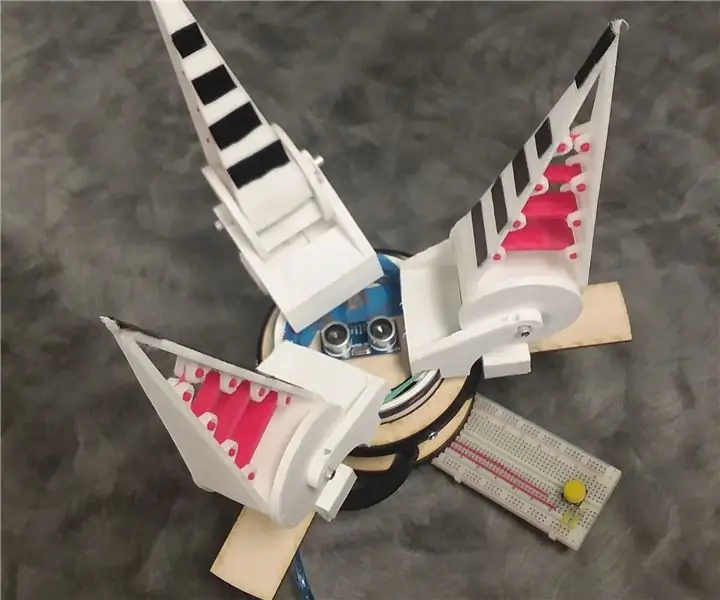
Table des matières:
- Étape 1: Outils et matériaux
- Étape 2: La griffe: extérieur
- Étape 3: La griffe: les ponts internes
- Étape 4: Le curseur
- Étape 5: Le tambour et le harnais
- Étape 6: pignon et couronne
- Étape 7: bras radiaux et carrousel
- Étape 8: Boîte de moteur de base
- Étape 9: Branchement des rails coulissants
- Étape 10: Arduino, fils et composants
- Étape 11: Code Arduino
- Étape 12: Test de circuit
- Étape 13: Assemblage de base: la griffe
- Étape 14: Assemblage de base: tambour et harnais
- Étape 15: Assemblage de base: les curseurs
- Étape 16: perçage
- Étape 17: Assemblage du PVC
- Étape 18: Assemblage de la base et du circuit
- Étape 19: Cacher les fils
2025 Auteur: John Day | [email protected]. Dernière modifié: 2025-01-23 14:46
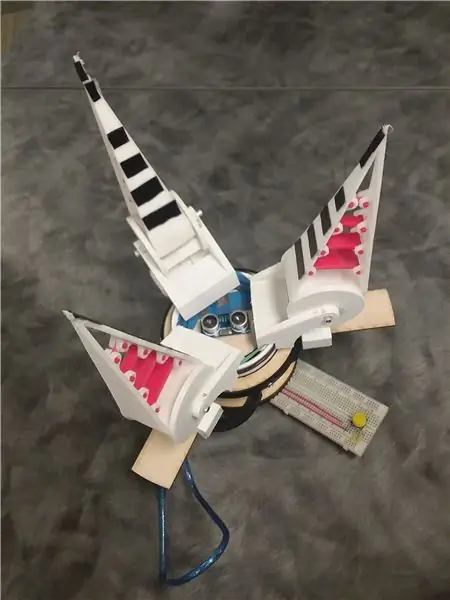
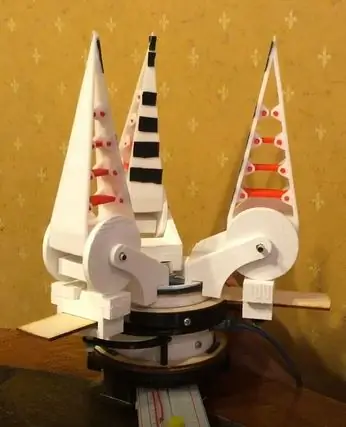
Cette instructable a été créée pour répondre aux exigences du projet du Makecourse à l'Université de Floride du Sud (www.makecourse.com).
Le Flex Claw est le prochain meilleur projet pour tout étudiant, ingénieur et bricoleur qui attirera sûrement l'attention de votre public. Exploité entièrement par un Arduino Uno, le Flex Claw est une approche simplifiée d'une griffe à centrage automatique en n'utilisant qu'un seul moteur ! Mais ses capacités ne sont pas si simples, car sa structure à griffes est repensée pour s'adapter à n'importe quel objet de forme qu'elle contient ! Bien que sa construction soit principalement pratique, l'accès à une imprimante 3D avec un filament NinjaFlex et une compatibilité PLA est nécessaire.
Étape 1: Outils et matériaux
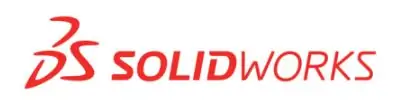
La première étape consiste à examiner toutes les pièces et éventuellement à faire des ajustements. Pour cela, je recommande fortement d'utiliser Solidworks car il est très convivial une fois que vous avez appris où se trouvent toutes les commandes. Si vous ne l'avez pas encore téléchargé, assurez-vous de vérifier auprès de votre école ou de votre lieu de travail les remises ou les codes d'accès gratuits. YouTube sera également votre meilleur ami si vous avez besoin de plus de clarté sur chaque fonctionnalité. Les prochaines étapes expliqueront comment concevoir les pièces pour le Flex Claw avec Solidworks qui doivent être imprimées en 3D.
Avant de collecter les matériaux, veuillez lire toutes les étapes et confirmer que celles énumérées ci-dessous conviennent au produit final souhaité, car tout ajustement personnalisé de la taille/des dimensions des pièces discutées peut être effectué, bien que non recommandé. Les matériaux suivants coïncident avec le processus de construction des étapes d'origine.
Outils:
- Imprimable en 3D compatible avec les filaments NinjaFleax et PLA.
-Coupe laser contreplaqué (recommandé pour les dimensions exactes, mais peut être contourné avec des compétences expérimentées)
- Perceuse électrique avec foret 3/16
- Dremel
- Kit Arduino Uno complet (fils, câble de connexion, etc.), comprenant un capteur de proximité, une lumière LED (avec la résistance correspondante), un bouton-poussoir et 2 moteurs pas à pas (un moteur plus puissant peut être nécessaire en fonction des résultats de la recherche et de la résistance au frottement).
Matériel:
- Feuille de contreplaqué 12" x 24" x 0,125"
-Pip PVC 4" diamètre extérieur, environ 5" de long, 0,125" mur
- Bande de poignée
- Vis 6/32" 1.5" long X 6, avec écrous respectés
- Tige en aluminium de 0,125 "de diamètre, 6" de long et une scie à métaux appropriée pour les coupes futures
- Prise de courant avec sortie d'au moins 2,5 A (un chargeur I-Phone/I-Pad fonctionne)
Étape 2: La griffe: extérieur
Maintenant que nous avons Solidworks, nous pouvons commencer à modéliser la conception de la griffe externe. Ceci est encouragé à être l'une des premières étapes puisque cette pièce doit être imprimée en 3D avec le filament NinjaFlex, qui prend plus de temps à former que la plupart des plastiques et a probablement besoin d'une source extérieure pour une imprimante 3D compatible avec ce filament.
La griffe est une caractéristique clé du projet car elle se plie en fait à la forme de tout objet tenu. En permettant un extérieur à paroi mince et très flexible, nous pouvons profiter de sa pliabilité naturelle pour maximiser la surface de contact pour une meilleure adhérence. Le revers de la médaille, cependant, est qu'il a toujours besoin de ponts rigides internes pour maintenir sa structure et appliquer les forces compressibles au contact (étape 3).
Ce sont les pièces pour faire une griffe, alors préparez-vous à imprimer 3 fois ce montant pour 3 griffes. Le bon conseil est que nous pouvons imprimer plusieurs parties en même temps tant qu'il y a assez de place sur le lit. Mais cela pourrait également augmenter la frustration si une pièce se détériore pendant le processus d'impression, alors nous devrions également arrêter l'impression pour le reste des pièces. Un trop grand nombre de pièces sur le lit peut également entraîner un durcissement excessif de la couche de plastique avant l'ajout de la couche suivante (puisque la machine doit contourner les autres pièces) et provoquer un pli au milieu de la pièce. L'expérience de vouloir que votre imprimante 3D puisse gérer est la meilleure chose à faire, mais gardez à l'esprit que plusieurs pièces peuvent être imprimées à la fois.
En plus des fichiers de pièce solidworks, vous trouverez en pièce jointe le dessin solidworks affichant les mesures utilisées. Bien que la plupart de ces longueurs puissent être modifiées pour mieux s'adapter à votre logement, tout changement devra ensuite être appliqué à d'autres pièces pour s'assurer que tout s'emboîte. Il est donc recommandé de réserver les ajustements jusqu'à ce que vous ayez examiné chaque étape et considéré le résultat final. Sinon, ce sont les étapes de base pour concevoir le modèle donné prévu.
Étape 3: La griffe: les ponts internes
Ensuite, les ponts internes pour la griffe. Alors que la conception de la griffe externe doit être imprimée avec NinjaFlex pour permettre la flexibilité, ces ponts doivent plutôt être imprimés avec un filament PLA. Ceux-ci seront rigides et agiront comme des os pour maintenir la structure de la griffe lorsqu'elle se plie et appliqueront les forces compressibles au contact.
En plus des fichiers de pièces solidworks, vous trouverez en pièce jointe le dessin solidworks des pièces affichant les mesures utilisées. Ce sont les dimensions qui sont compatibles avec le reste de la conception de la griffe afin que tout s'emboîte, alors assurez-vous que tous les ajustements personnels aux pièces précédentes sont appliqués à ces pièces si nécessaire. Sinon, ce sont les étapes de base pour concevoir le modèle donné prévu.
(Ce sont les pièces pour fabriquer une griffe, alors préparez-vous à imprimer en 3D 3 fois ce montant pour 3 griffes)
Étape 4: Le curseur
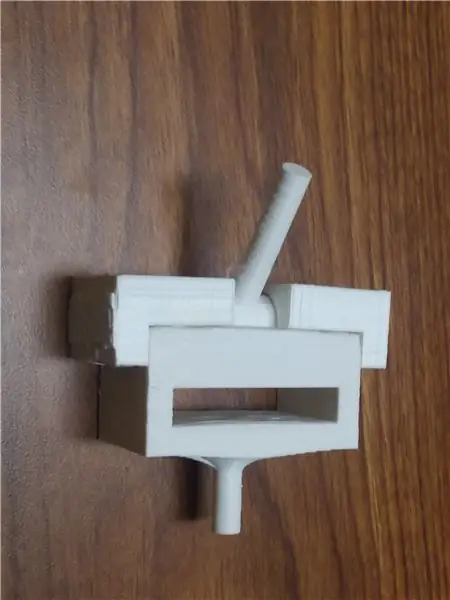
Le Slider est composé de 4 parties: 1 slider dominant, 1 tambour avec un poteau, et 2 "accessoires de slider". Avec la façon dont cela est conçu, le curseur peut envelopper complètement le tambour sans restreindre sa capacité à tourner dans sa rainure. Cela ne nécessite pas non plus de vis puisque les pièces jointes s'insèrent simplement dans le curseur principal et sur le tambour placé.
En plus des fichiers de pièces solidworks, vous trouverez en pièce jointe le dessin solidworks des pièces affichant les mesures utilisées. Ce sont les dimensions qui sont compatibles avec le reste de la conception de la griffe afin que tout s'emboîte, alors assurez-vous que tous les ajustements personnels aux pièces précédentes sont appliqués à ces pièces si nécessaire.
(Ce sont les pièces pour fabriquer une griffe, alors préparez-vous à imprimer en 3D 3 fois ce montant pour 3 griffes)
Étape 5: Le tambour et le harnais
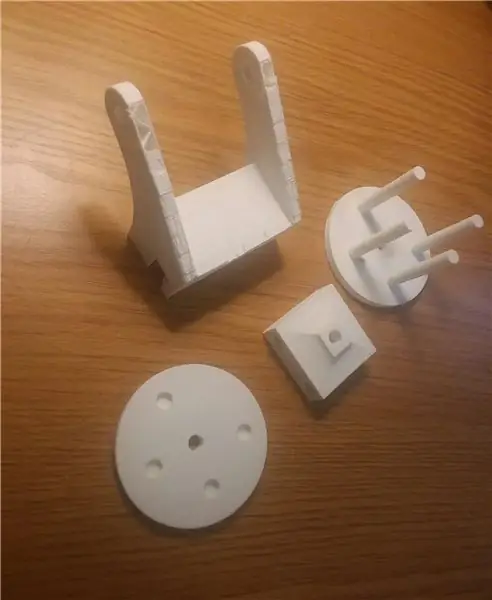
Le tambour et le harnais de tambour sont les intermédiaires pour connecter la griffe au curseur et lui permettent de tourner vers l'avant lorsque les curseurs se déplacent vers l'extérieur. Contrairement aux pièces précédentes qui doivent être imprimées en 3D, ces pièces peuvent être travaillées en utilisant à la place des tiges de bois et d'aluminium. Mais ce n'est pas recommandé car ceux-ci ont des mesures exactes qui permettent aux autres pièces de se connecter toutes ensemble, en particulier le harnais qui a une rainure inférieure qui doit s'adapter à l'épaisseur et à la courbure du rebord du tuyau en PVC. Veuillez vérifier ce paramètre pour le tuyau en PVC que vous possédez déjà ou en prendre note pour en trouver un qui vous convient.
Dans une prochaine étape, nous assemblerons ces pièces de sorte que le trou inférieur du connecteur du tambour s'adapte à l'arbre du tambour coulissant et que la paire de poteaux plus large du DrumHalf passe à travers les trous traversants à la base de l'extérieur de la griffe. Cela étant dit, ce sont les dimensions qui sont compatibles avec le reste de la conception de la griffe afin que tout s'emboîte, alors assurez-vous que tout ajustement personnel aux pièces précédentes est appliqué à ces pièces si nécessaire.
(Ce sont les pièces pour fabriquer une griffe, alors préparez-vous à imprimer en 3D 3 fois ce montant pour 3 griffes)
Étape 6: pignon et couronne
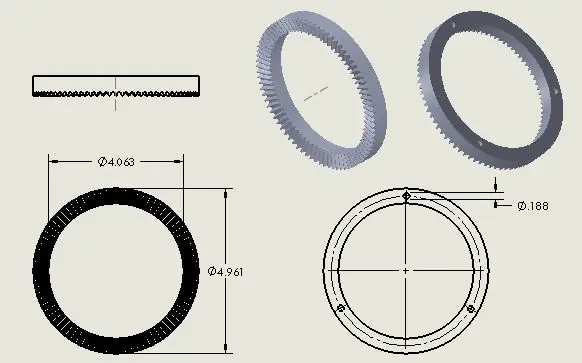
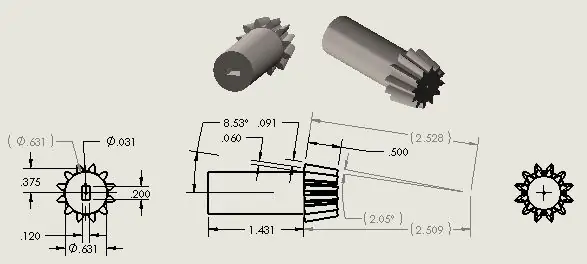
C'est là que la puissance entre en jeu. Le pignon Gear et la couronne ne doivent pas être changés pour l'impression 3D car ils sont très particuliers. Le moyeu de pignon a un ajustement complet uniquement pour le moteur pas à pas de base mentionné. Si un autre moteur veut être utilisé avec des dimensions d'arbre différentes, cela peut être ajusté dans le fichier de travail solide. Pour ce modèle, 2 moteurs pas à pas sont utilisés, alors assurez-vous d'imprimer 2 pignons.
En plus des fichiers de pièces solidworks, vous trouverez en pièce jointe le dessin solidworks des pièces affichant les mesures utilisées. Ce sont les dimensions qui sont compatibles avec le reste de la conception de la griffe afin que tout s'emboîte, alors assurez-vous que tous les ajustements personnels aux pièces précédentes sont appliqués à ces pièces si nécessaire.
Étape 7: bras radiaux et carrousel
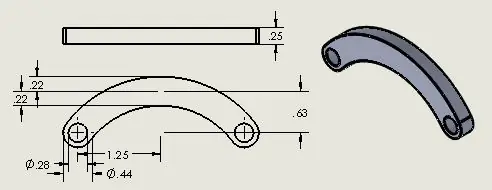
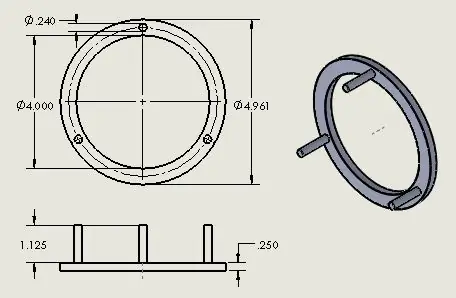
Le carrousel est ensuite placé sur la couronne dentée et fait pivoter le lien de rayon vers et loin du curseur, en le poussant d'avant en arrière. Bien qu'il s'agisse d'une conception simple, il n'est pas recommandé de remplacer le carrousel par du bois et des tiges d'aluminium légèrement supportées, car l'ensemble de la pièce doit être suffisamment solide pour tourner autour du tuyau en PVC sans bouger. Au total, 3 maillons de rayon sont nécessaires.
En plus des fichiers de pièces solidworks, vous trouverez en pièce jointe le dessin solidworks des pièces affichant les mesures utilisées. Ce sont les dimensions qui sont compatibles avec le reste de la conception de la griffe afin que tout s'emboîte, alors assurez-vous que tous les ajustements personnels aux pièces précédentes sont appliqués à ces pièces si nécessaire.
Étape 8: Boîte de moteur de base
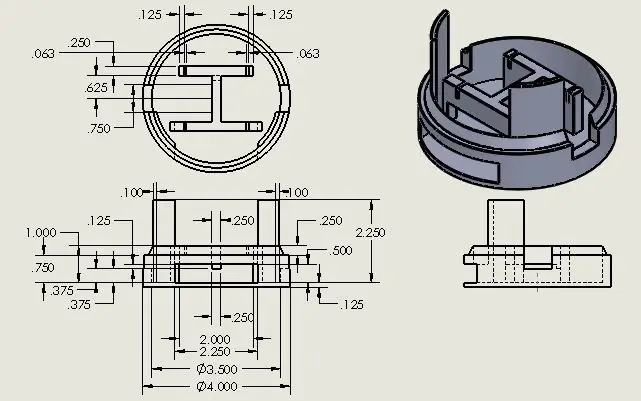
Mis à part la griffe individuelle, cette partie peut être la deuxième plus complexe. L'impression 3D sera votre meilleure amie si elle n'a pas déjà fait ses preuves. Cette base, bien qu'elle soit mesurée pour s'adapter particulièrement au raccord de tuyau en PVC que j'ai utilisé (et que je recommande) avec un diamètre extérieur de 4 ", des parois de 0,25" d'épaisseur et un bord incliné près du bord. Veuillez vérifier les dimensions et les modifier pour mieux s'adapter au tuyau que vous utilisez. Les tuyaux sont également généralement vendus en vous informant du diamètre intérieur. Donc, dans ce cas, si j'ai besoin d'un tuyau de 4" de diamètre extérieur qui a des parois de 0,25" d'épaisseur, je devrais être à la recherche d'un raccord de 3,5". Quoi qu'il en soit, vous ne pouvez pas vous tromper en allant au magasin avec une règle à la main.
Cette base est destinée à s'adapter à deux moteurs pas à pas 28BYJ-48 5VDC pour l'Arduino Uno. Bien que ces moteurs soient plus faciles à encoder, ils ne sont pas mieux connus pour leur force. La réduction du frottement aide grandement en appliquant du graphite en poudre ou d'autres lubrifiants secs sur les curseurs annulaires. Sinon, si un moteur plus puissant est accessible, une conception majeure modifiée par rapport à la base doit être effectuée et est encouragée à le faire après avoir utilisé cette conception avec 2 moteurs pas à pas de base afin que vous puissiez voir comment la disposition finale entraînera des changements notables.
Cette base est également destinée à incorporer une planche à pain en la faisant glisser dans la fente rectangulaire sur le côté. Avec cela, une section transversale d'une largeur de 2,25" et d'une hauteur de 0,375" a été prévue, car il s'agit d'une taille standard pour la plupart des planches à pain. Encore une fois, comme pour les moteurs, si un pain de taille différente veut être utilisé à la place, veuillez attendre d'avoir pris tous les détails de la disposition finale du circuit pour ensuite apporter des modifications.
Étape 9: Branchement des rails coulissants
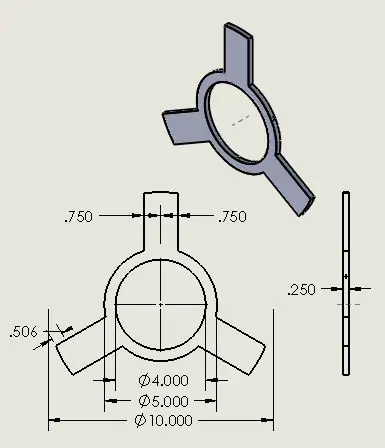
Cet anneau sera percé dans le tuyau en PVC afin d'être le plus stable possible pour que les curseurs puissent glisser. Cette pièce est généralement trop grande pour être imprimée en 3D, je vous recommande donc fortement d'avoir accès à un coupe-bois laser ou de développer vos compétences avec des bords arrondis dans l'atelier de menuiserie. Avec cela, l'épaisseur peut varier pour mieux s'adapter aux curseurs, mais assurez-vous de laisser encore une certaine marge de manœuvre. Dans une étape ultérieure, nous passerons en revue les meilleures façons de le fixer sur la structure.
En plus des fichiers de pièces solidworks, vous trouverez en pièce jointe le dessin solidworks des pièces affichant les mesures utilisées. Ce sont les dimensions qui sont compatibles avec le reste de la conception de la griffe afin que tout s'emboîte, alors assurez-vous que tous les ajustements personnels aux pièces précédentes sont appliqués à ces pièces si nécessaire.
Étape 10: Arduino, fils et composants
Étape 11: Code Arduino
Étape 12: Test de circuit
Étape 13: Assemblage de base: la griffe
Étape 14: Assemblage de base: tambour et harnais
Étape 15: Assemblage de base: les curseurs
Étape 16: perçage
Étape 17: Assemblage du PVC
Étape 18: Assemblage de la base et du circuit
Conseillé:
FLEXBALL - une boule PCB flexible de cent pixels avec WiFi : 6 étapes (avec photos)
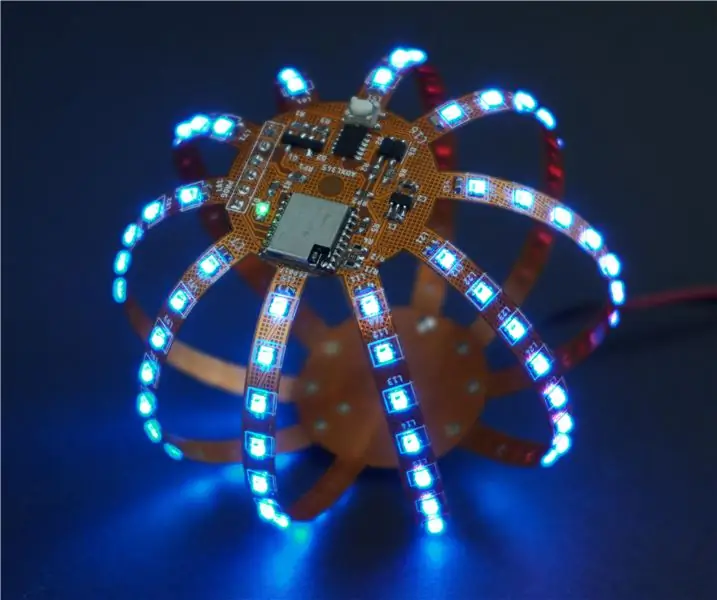
FLEXBALL - une boule PCB flexible de cent pixels avec WiFi : Bonjour les fabricants, c'est le fabricant moekoe ! Flexball est basé sur un PCB flexible qui est équipé de 100 LED adressables WS2812 2020. Il est contrôlé par un ESP8285-01f - le plus petit module basé sur ESP d'Espressif. De plus, il dispose d'un accéléromètre ADXL345
Énorme matrice de LED transparente flexible de moins de 150 $. Facile à faire. : 8 étapes (avec photos)
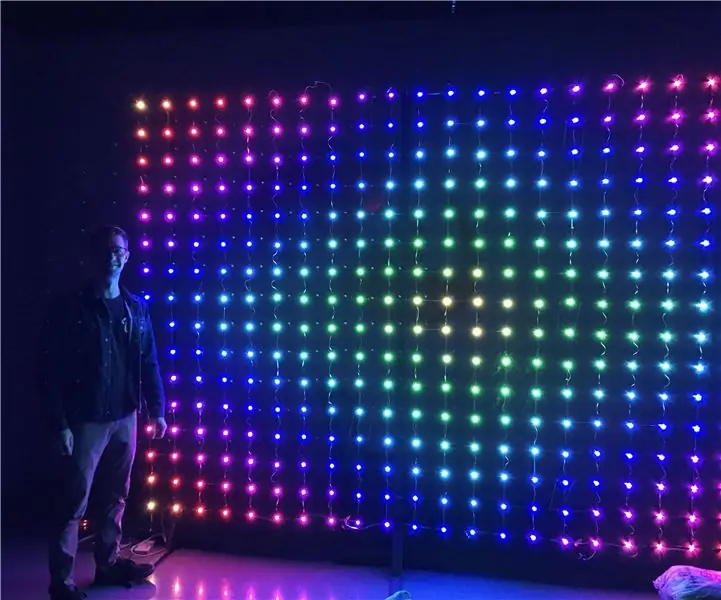
Énorme matrice de LED transparente flexible de moins de 150 $. Facile à faire. : Je veux commencer par dire que je ne suis pas un professionnel, je n'ai pas de diplôme en électronique. J'aime simplement travailler de mes mains et comprendre des choses. Je dis cela pour être encourageant pour vous tous, non professionnels comme moi. Vous avez la capacité de
LAMPE SOLAIRE SANS FIL AVEC BRAS FLEXIBLE MAGNÉTIQUE : 8 étapes (avec photos)
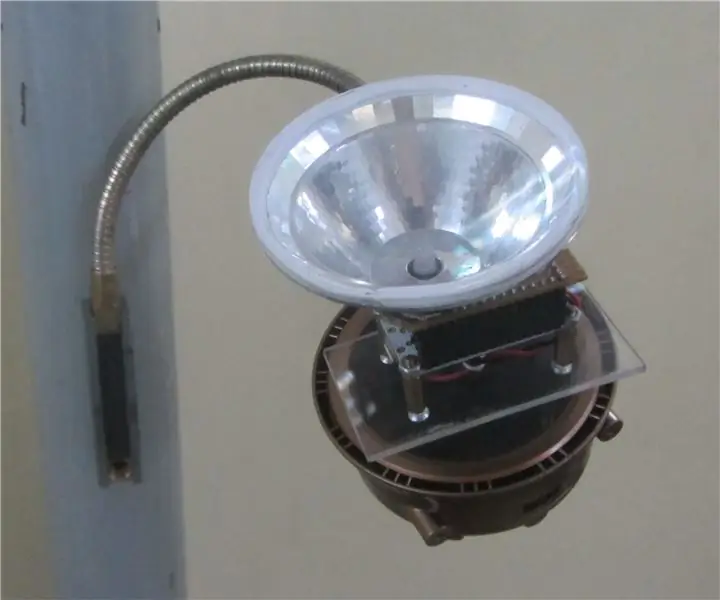
LAMPE SOLAIRE SANS FIL AVEC BRAS FLEXIBLE MAGNÉTIQUE : Ce projet a été réalisé à partir d'une lampe cassée & nœudMCU. Cette lampe décorative peut être ajustée dans toutes les directions & fixé sur des matériaux magnétiques ou posé sur la table. Il peut être contrôlé en deux modes comme suit :- Mode de contrôle sans fil, comme
Ordinateur portable flexible : 5 étapes (avec photos)
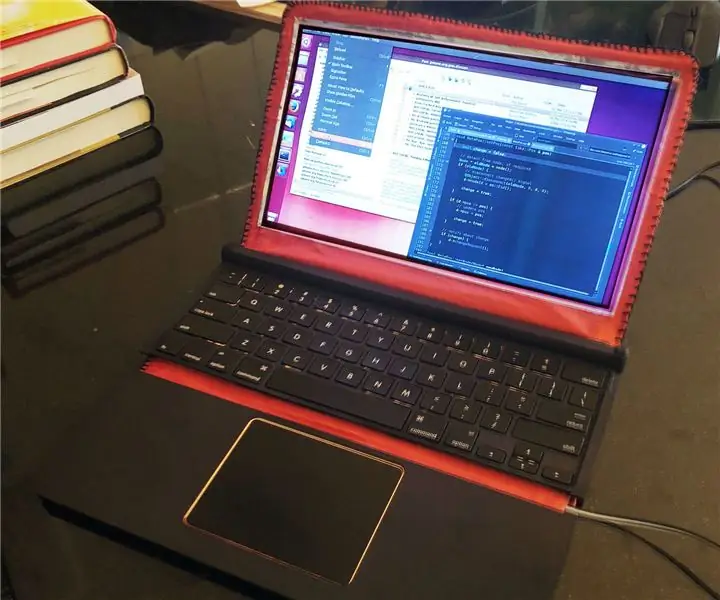
Ordinateur portable flexible : C'était un petit projet rapide que j'ai fait pour garder mes compétences de conception et de prototypage pointues et partager quelque chose qui n'est pas sous NDA ou en cours de licence à quelqu'un. Je le soumets au défi des conseils pro et c'est vraiment un guide pour
Pong jouant à l'écran flexible sur une chemise : 8 étapes (avec photos)
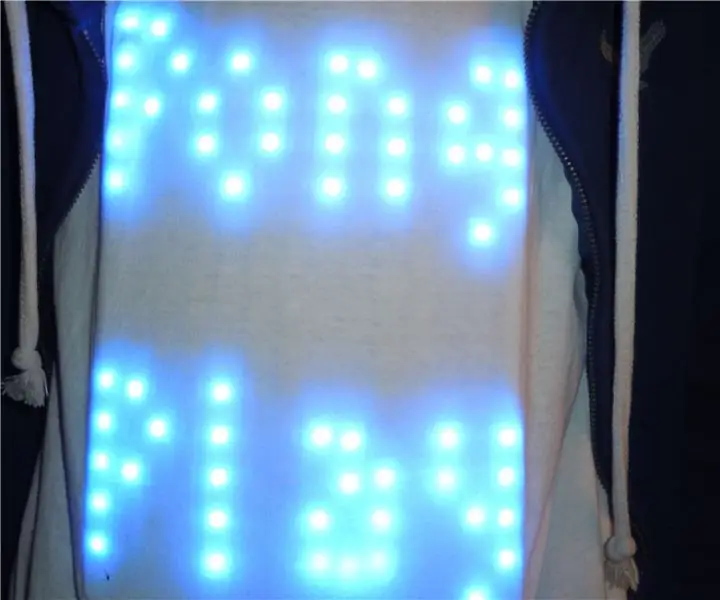
Pong jouant un écran flexible sur une chemise : c'est mon costume d'Halloween pour l'année 2013. Il est en préparation depuis environ un an et sa création a pris pas mal d'heures de travail. L'écran fait 14 x 15 pixels, donc une résolution assez faible, mais il peut quand même faire des choses amusantes. C'est physiquement fle