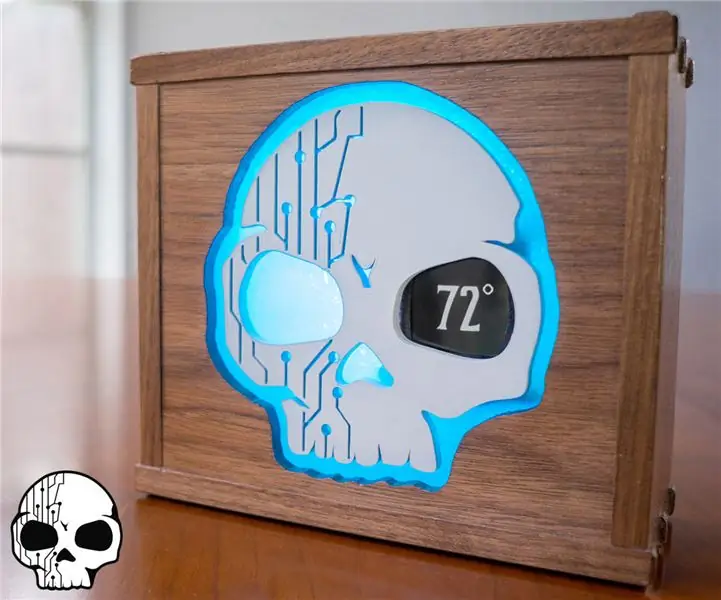
Table des matières:
2025 Auteur: John Day | [email protected]. Dernière modifié: 2025-01-23 14:46
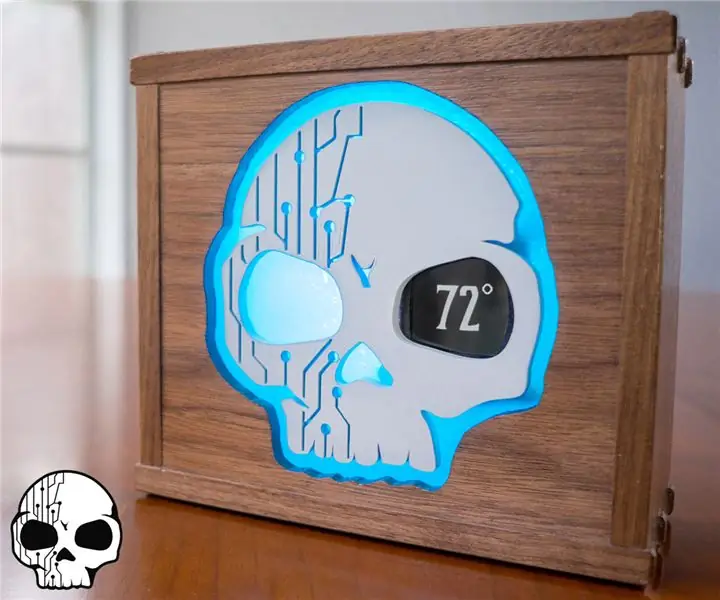
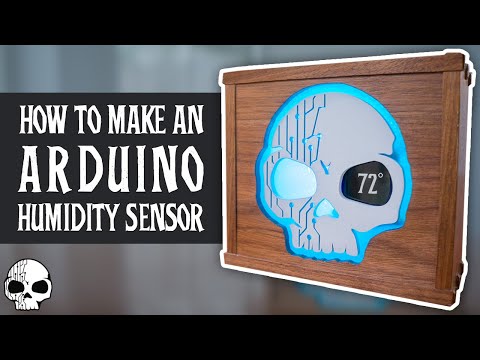
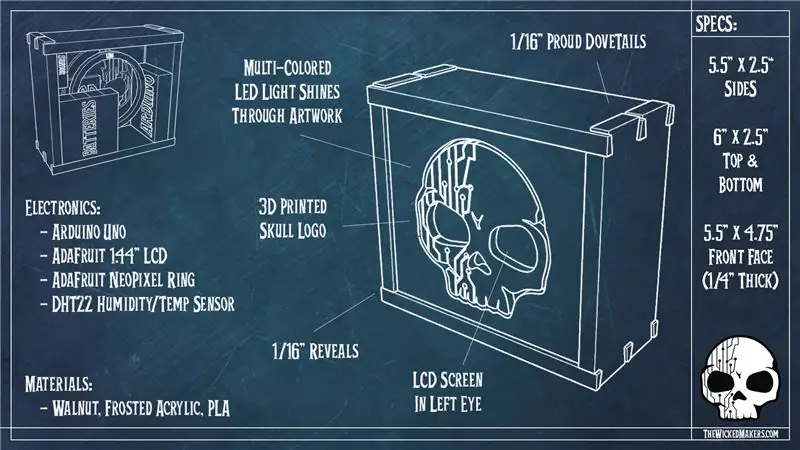
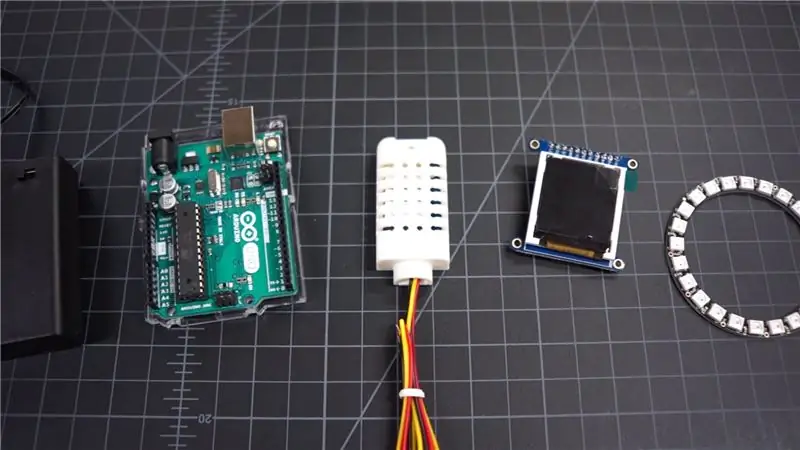
Nous vivons dans le centre du Texas et pendant la majeure partie de l'année, nous avons des fluctuations massives de l'humidité dans notre magasin. En tant que menuisiers, cela peut être difficile sur certains projets, nous avons donc construit un « capteur d'atelier » alimenté par Arduino pour nous donner un moyen visuellement attrayant de voir comment l'humidité change ! Il est fabriqué à partir de noyer et a une menuiserie en queue d'aronde et à mesure que l'humidité change, la couleur de l'éclairage change à travers le spectre de couleurs. Il dispose également d'un écran LCD dans l'un des yeux qui affiche la température de la pièce.
L'une de nos choses préférées est de combiner le travail du bois avec la technologie et c'était un projet vraiment amusant où nous avons fait exactement cela.
Ce projet comprend du travail du bois, de l'électronique et de l'impression 3D.
Pourquoi l'humidité est-elle importante dans le travail du bois?
La réponse simple est que le bois réagit aux changements de teneur en humidité de l'air en se dilatant et en se contractant. Même après qu'il soit complètement sec et même avec une finition dessus, presque tout le bois continue de " bouger ". Cela peut séparer les joints, empêcher les tiroirs de s'adapter et d'autres choses désagréables. Pour en savoir plus sur ce phénomène, nous vous recommandons une recherche google !
COMPOSANTS UTILISÉS:
- Arduino Uno
- Bague Néopixel Adafruit
- Écran LCD Adafruit 1,44"
- Capteur d'humidité DHT22
- 4x piles AA
- Carte Mini SD
LES OUTILS UTILISÉS:
- Imprimante 3D
- Routeur
- Couteau tout usage
- Déposer
- Pinces
- Fer à souder
- Souder
- Pistolet à colle chaude
- Mètre à ruban
- Crayon
- Ciseau
- Jauge de marquage
- Raboteuse (non requise)
- Dégauchisseuse (non requis)
- Scie à ruban (non requis)
- Scie à table (non requis)
- Outil rotatif / Dremel (non requis)
- Perceuse à colonne (non requise)
MATÉRIAUX:
- Noyer (Caisse en bois)
- Acrylique givré (diffuseur de lumière)
- PLA (Logo Crâne Imprimé 3D)
- Colle à bois
- Super colle
- Colle chaude
- Ruban de peintre bleu
- Ruban adhésif double face
- Gomme laque
Étape 1: L'étui: le bois
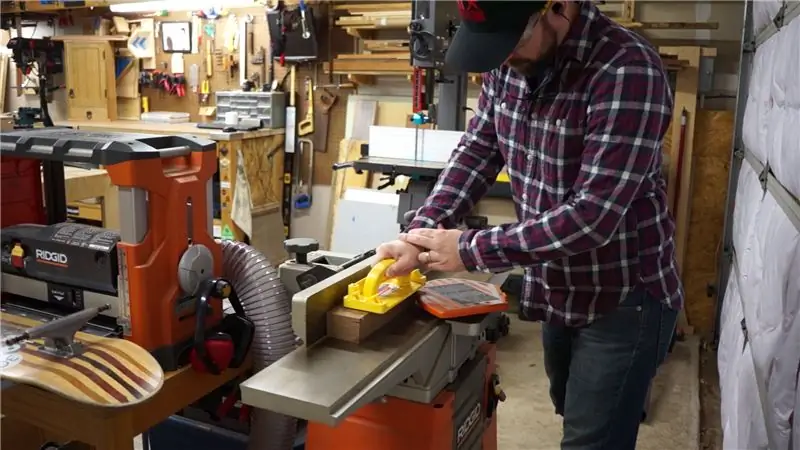
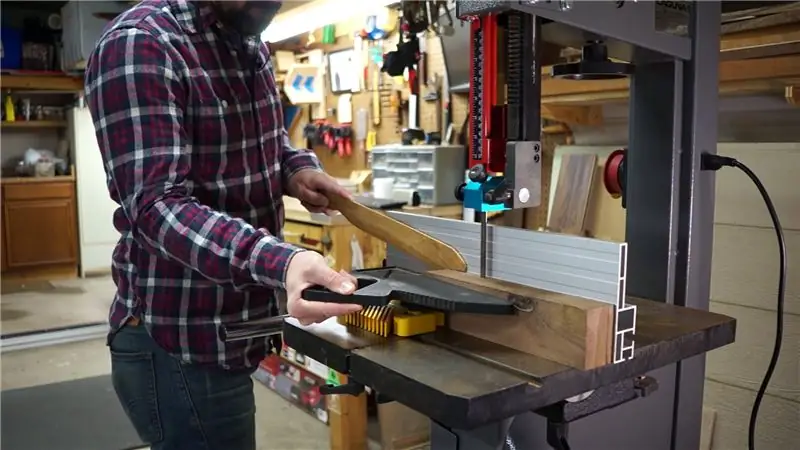
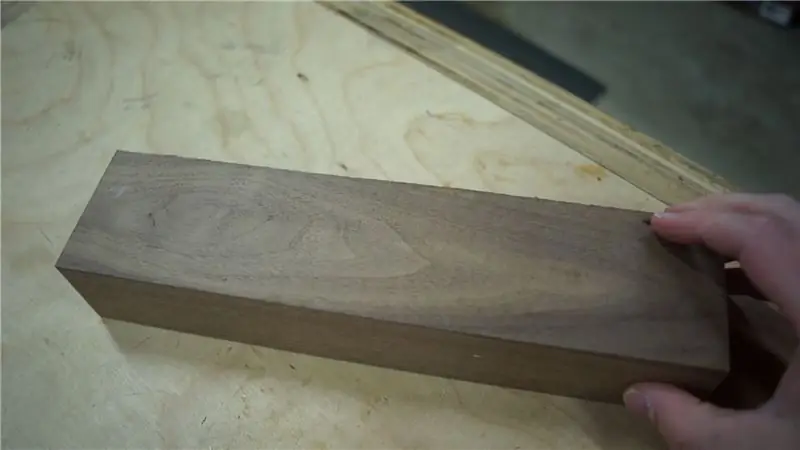
Pour construire le boîtier, nous avons utilisé du noyer qui est un bois dur brun foncé/gris. Pourquoi le noyer ? C'est facile à travailler, nous en avons eu, et cela a généralement l'air génial… ce qui en fait un excellent choix pour cela ! Avez-vous besoin d'utiliser du Noyer ? Non! Vous pouvez utiliser n'importe quelle essence de bois pour cela.
Le processus de fraisage du noyer consistait d'abord à l'aplatir et à le redresser sur la dégauchisseuse, à recouper des pièces plus petites de 3/8 d'épaisseur sur la scie à ruban, puis à les raboter à l'épaisseur finale à l'aide de la raboteuse.
Vous n'avez pas vos propres outils de fraisage ? Pas de soucis! Vous pouvez acheter du bois qui a déjà l'épaisseur que vous souhaitez utiliser et sauter cette première partie
Avec le noyer fraisé à plat, droit et à notre épaisseur finale, nous l'avons déchiré à la largeur finale sur la scie à table, puis nous l'avons coupé en travers à la longueur finale.
Le résultat de ce processus était quatre pièces qui étaient toutes parfaitement plates, droites et exactement de la taille que nous voulions. Puisque nous coupons des queues d'aronde, le fait d'avoir des pièces parfaitement dimensionnées nous facilitera grandement la tâche par la suite. Si les pièces ne sont pas de la même taille ou si elles ne sont pas carrées, les queues d'aronde ne s'emboîteront pas bien.
Étape 2: L'affaire: les queues d'aronde
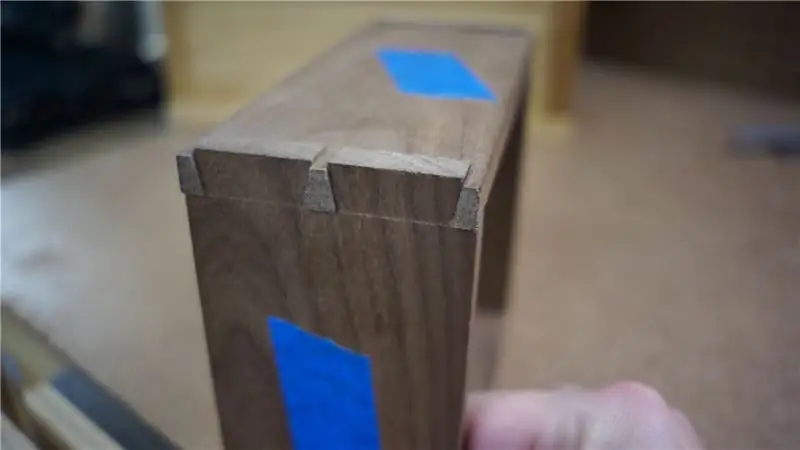
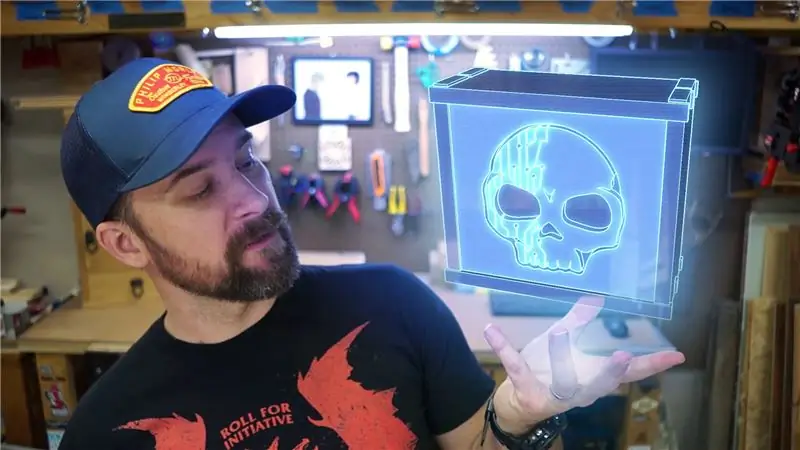
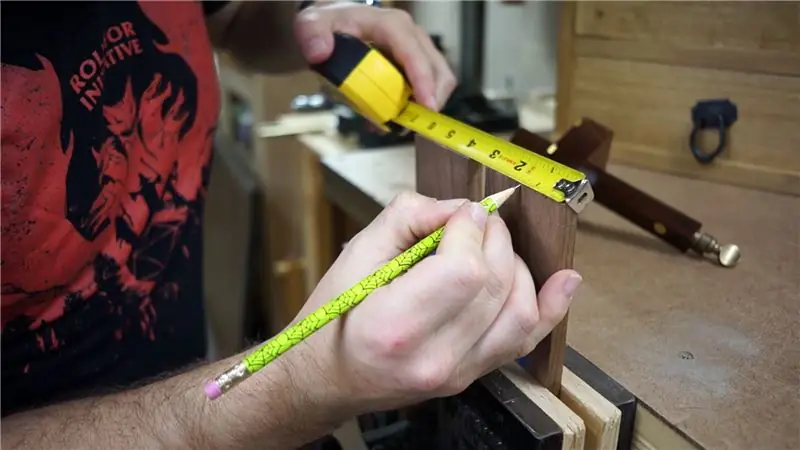
Comme le montrent les photos et la vidéo, une queue d'aronde est un joint où deux pièces se rejoignent au moyen d'un tenon en forme de queue d'aronde, appelé "queue", qui s'insère dans une mortaise entre deux "goupilles". C'est un joint stimulant et amusant à créer. De plus, ils ont l'air IMPRESSIONNANT.
Vous n'avez pas besoin d'utiliser des queues d'aronde pour cela… mais… mettez-vous au défi… essayez-le
Nous avons commencé par mesurer la taille et l'emplacement de nos broches et queues sur les planches. Nous utilisons ensuite un gabarit sur la scie à table pour faire nos coupes.
(Le gabarit que nous utilisons provient du magazine Fine Woodworking et il est vraiment facile à fabriquer. Il y a une vidéo fantastique sur YouTube qui vous montre comment le faire. Vous pouvez le trouver en recherchant « Queues d'aronde de scie à table » sur YouTube.)
Le premier gabarit a la lame de scie à table inclinée à environ 10 degrés pour couper les queues, puis le deuxième gabarit a la lame à 90 degrés mais incline la pièce au même angle qu'auparavant et évacue les déchets. Nous utilisons une lame de déchirure plate pour cela et si nous le faisons correctement, cela devrait s'adapter directement à la scie à table…..
Eh bien… Ils ne l'ont pas fait.:)
Nous avons dû faire quelques ajustements à l'aide d'un ciseau et utiliser intelligemment des morceaux de ferraille pour masquer les problèmes, mais ils ont finalement bien fonctionné.
Vous pouvez voir plus de détails sur cette partie dans la vidéo de l'étape 1
Étape 3: Le boîtier: Assemblage
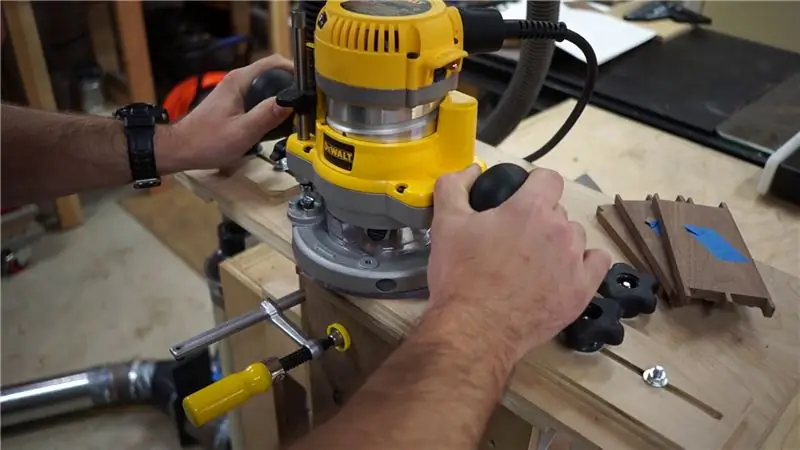
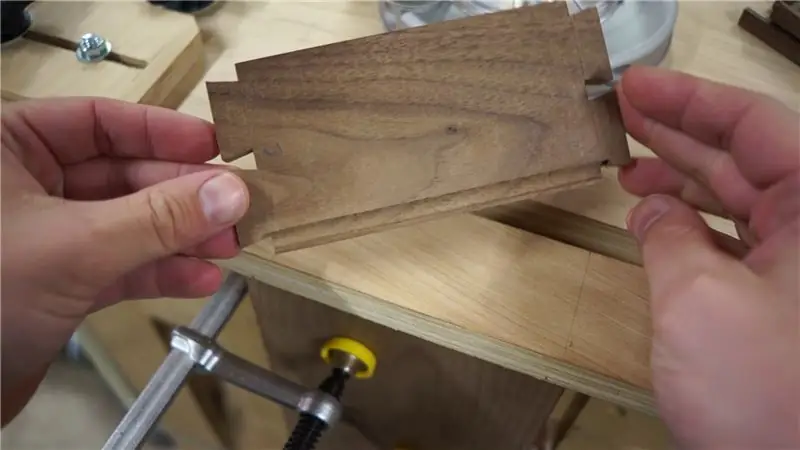
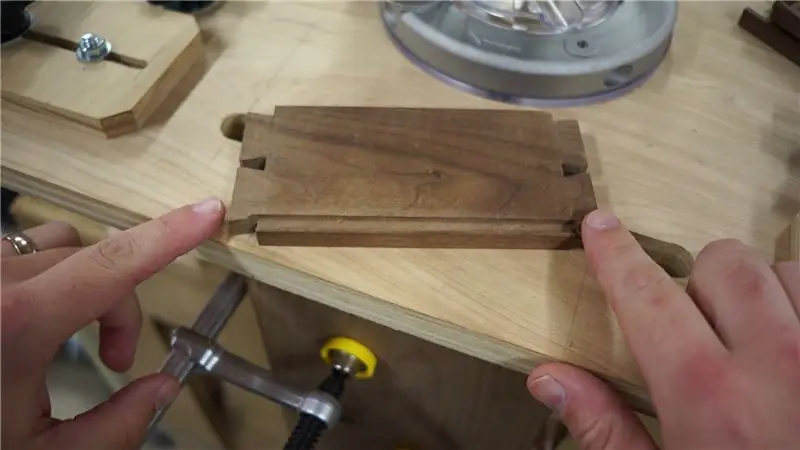
Le boîtier a un dos ouvert et le devant se trouve bien à l'intérieur d'une rainure "arrêtée" de 1/8 "de profondeur. Pour couper la rainure, nous avons utilisé une toupie.
C'est ce qu'on appelle un groove "arrêté" car il ne va pas d'un bout à l'autre. Il commence à mi-chemin et se termine juste avant d'arriver au bord. (Voir les images.)
Dans ce cas, si le sillon était allé jusqu'au bout, il aurait traversé les queues d'aronde et vous le verriez clairement. Comme nous ne le voulions pas, nous avons utilisé un groove arrêté.
Le dessus a été fabriqué à partir d'environ 1/4 de noyer d'épaisseur et déchiré et coupé en croix. À partir de là, nous avons fait notre premier ajustement à sec et tout allait bien!
Étape 4: Le crâne
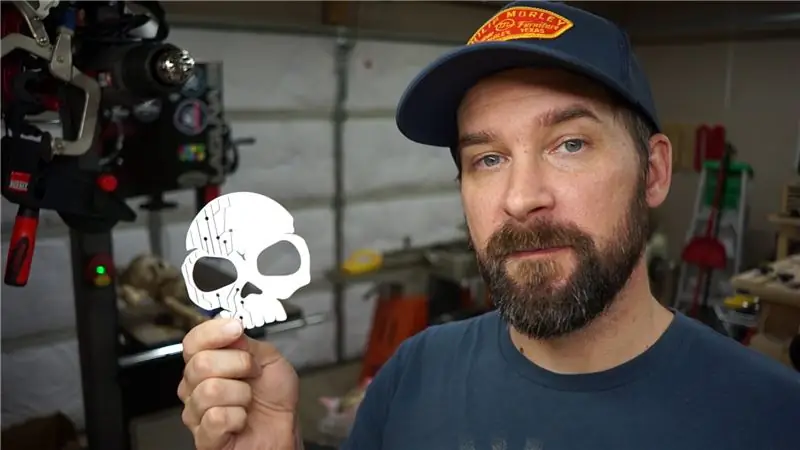
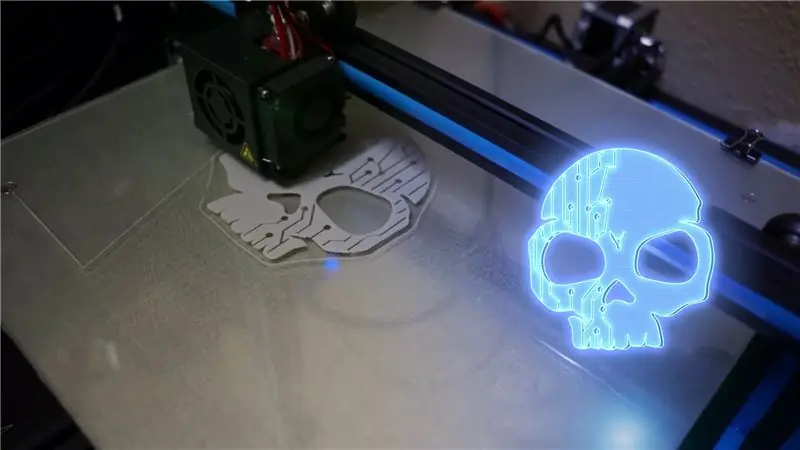
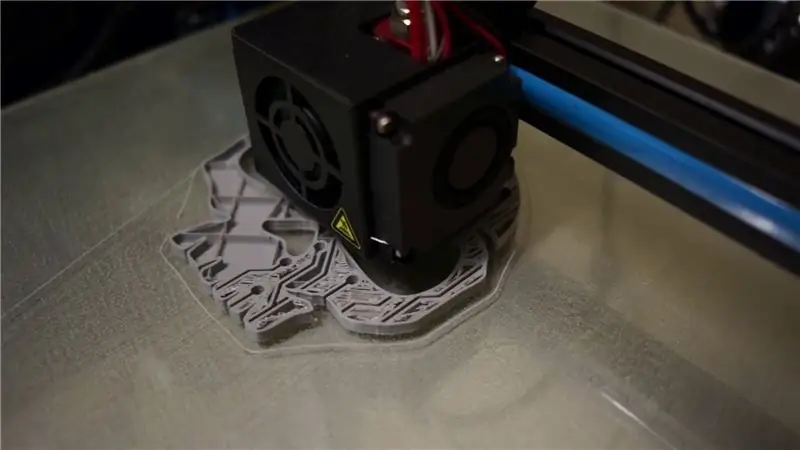
L'idée pour le devant du boîtier était d'avoir une découpe en forme de notre logo et de faire briller la lumière par derrière. Au début, nous avons essayé de faire sortir le logo du crâne d'un morceau de bois, mais… ce fut un désastre. Nous avons donc décidé d'imprimer le crâne en 3D et de le peindre en blanc, ce qui s'est avéré super !
Nous avons également imprimé en 3D un contour légèrement plus grand que le crâne, utilisé du ruban adhésif double face pour le fixer à l'avant, puis utilisé un couteau tranchant pour tracer le contour dans le bois. Avec la "ligne de couteaux" nette et définie, nous avons ensuite utilisé le routeur pour éliminer les déchets au milieu. Nous avons utilisé une mèche de toupie droite de 1/16" et sommes allés incroyablement lentement pour dérouter jusqu'à la ligne.
Pour les derniers détails, nous avons utilisé une petite lime à main et nettoyé toutes les marques d'outils ou les taches manquées.
De là, nous avons collé le boîtier en bois et une fois la colle sèche, nous avons chanfreiné les queues d'aronde et les bords du boîtier avec un ciseau et un rabot.
Étape 5: Le diffuseur de lumière et la finition Shellac
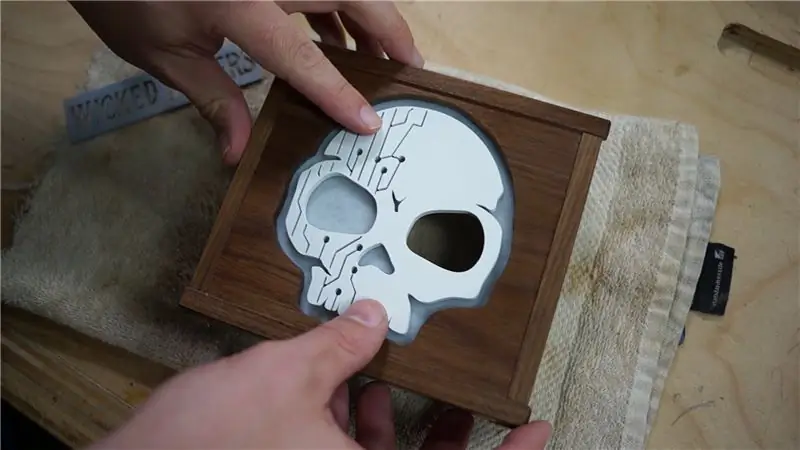
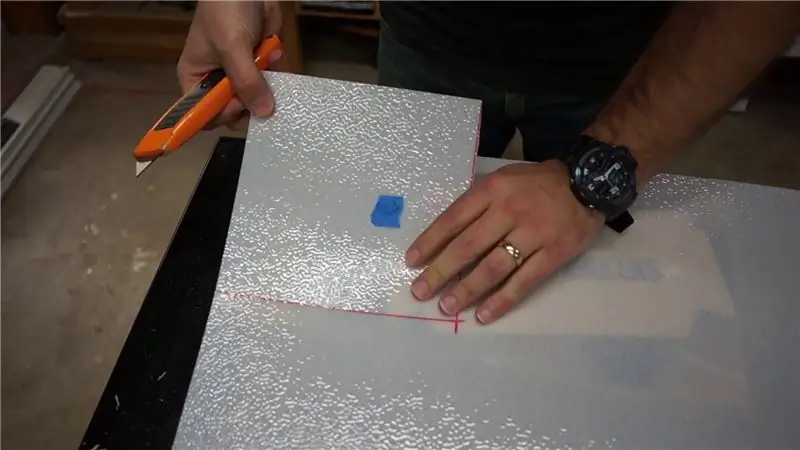
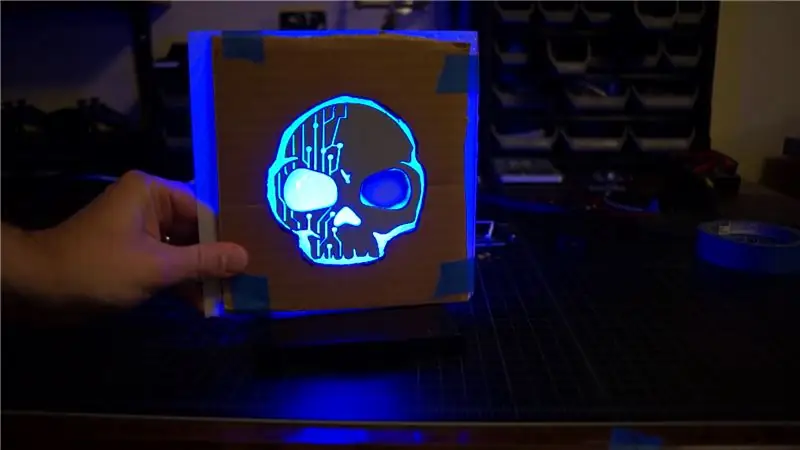
Derrière le crâne allait se trouver un morceau de plastique blanc givré. C'était là pour "diffuser" la lumière derrière elle pour l'aider à s'étendre davantage et à mieux paraître. Nous avons trouvé une petite feuille de plastique au magasin à grande surface et en avons découpé un morceau pour tenir dans notre valise.
Nous avons d'abord fait un test pour nous assurer que tout allait bien et que tout était génial ! Nous n'étions pas sûrs à 100% que ce plastique diffuserait correctement la lumière, mais heureusement, il l'a fait.
Ensuite, nous avons utilisé du ruban adhésif double face pour maintenir temporairement l'impression 3D du crâne en place afin que nous puissions obtenir le positionnement de l'œil gauche. Cela allait être remplacé par un écran LCD, nous devions donc retirer le plastique. Nous avons utilisé un marqueur pour délimiter la zone à enlever, puis nous avons nettoyé les déchets en en perçant la majeure partie sur la perceuse à colonne, puis en nettoyant la ligne avec un tambour de ponçage et un outil rotatif.
Avant de coller le plastique dépoli, nous avons fini le boîtier avec Shellac. Nous avons utilisé 3 couches puis l'avons poli avec de la laine d'acier et de la cire en pâte.
Avec le boîtier fini à l'intérieur et à l'extérieur, nous pourrions utiliser de la super colle pour fixer le plastique de l'intérieur.
Étape 6: L'électronique
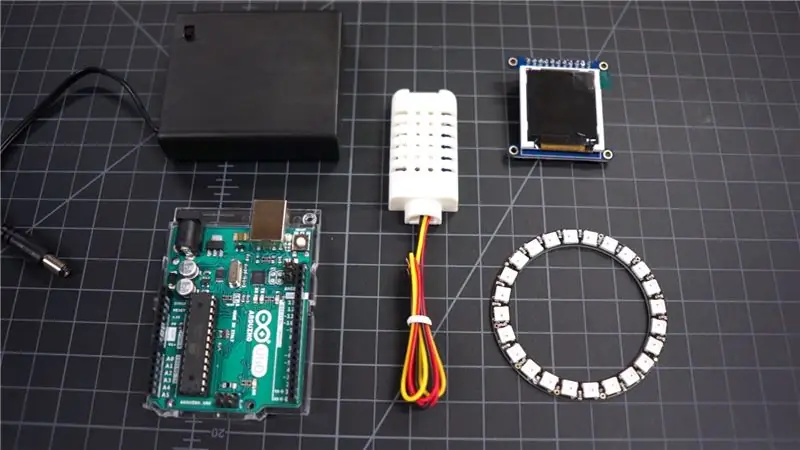
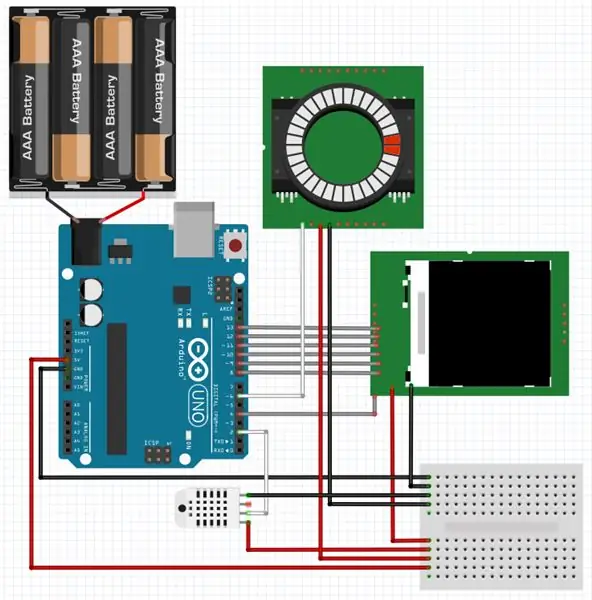
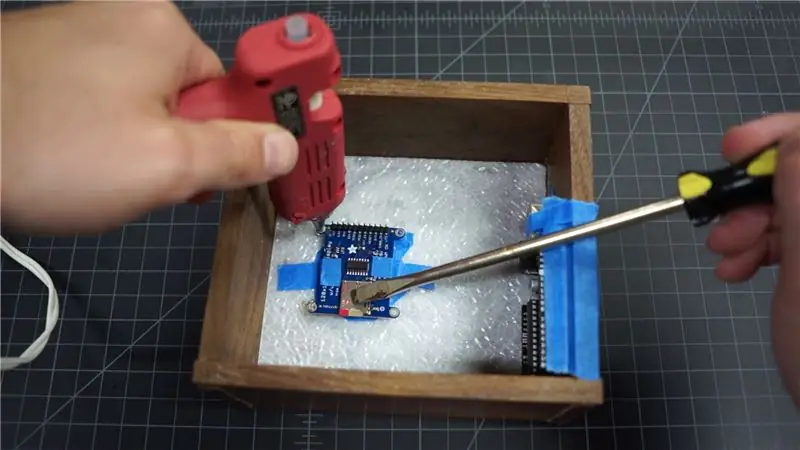
Les composants que nous devions installer étaient la batterie (4x AA), le capteur d'humidité et de température, l'écran LCD, l'anneau lumineux et bien sûr l'Arduino Uno. Nous avons passé beaucoup de temps à "prototyper" pour voir comment tout cela fonctionnerait et une fois que les choses fonctionnaient, nous devions trouver comment tout mettre dans la caisse en bois. Nous avions fait une partie de cela en parallèle de sorte que lorsque nous avons construit le boîtier, nous savions à quel point il était grand.
Nous avons utilisé du ruban adhésif bleu pour ajuster la position des composants et nous assurer qu'ils s'adapteraient, puis nous avons utilisé de la colle chaude pour maintenir l'écran LCD et le boîtier en plastique de l'Arduino sur le côté. Le boîtier/support en plastique est utile car nous pouvons tirer l'Arduino à l'intérieur et à l'extérieur si nécessaire.
L'anneau LED Neopixel a été collé à chaud sur la batterie, le capteur d'humidité a été collé à chaud en haut à gauche du boîtier en bois, puis une petite planche à pain a été collée à chaud au bas du boîtier en bois qui servirait de jonction d'alimentation.
La seule soudure que nous devions faire concernait l'alimentation, l'entrée de données et les fils de terre sur l'anneau Neopixel. Nous avons également utilisé un pistolet thermique et des tubes thermorétractables pour aider à gérer les fils et à les maintenir en place. Une fois la soudure terminée, nous avons collé à chaud la batterie sur le boîtier en bois, ce qui a permis à l'anneau lumineux d'être exactement centré et exactement là où il devait être pour diffuser correctement la lumière. (S'il est trop près du plastique, il ne s'étale pas autant que vous perdez une partie de l'effet.)
La batterie dispose d'un petit interrupteur marche/arrêt qui permet de basculer l'alimentation du projet, nous nous sommes donc assurés qu'il soit accessible. Le pack s'ouvre également vers l'arrière afin que nous puissions remplacer les piles si nécessaire.
De là, tous les composants étaient prêts pour le câblage final.
La programmation de l'Arduino était relativement facile. Il vérifie la température et l'affiche à l'écran. Il vérifie également l'humidité et ajuste la couleur des LED en fonction de son humidité. Le plus humide est quand il est violet, ce qui signifie 95%+ d'humidité. C'est trop souvent violet… mais c'est le centre du Texas pour vous !
Étape 7: les résultats
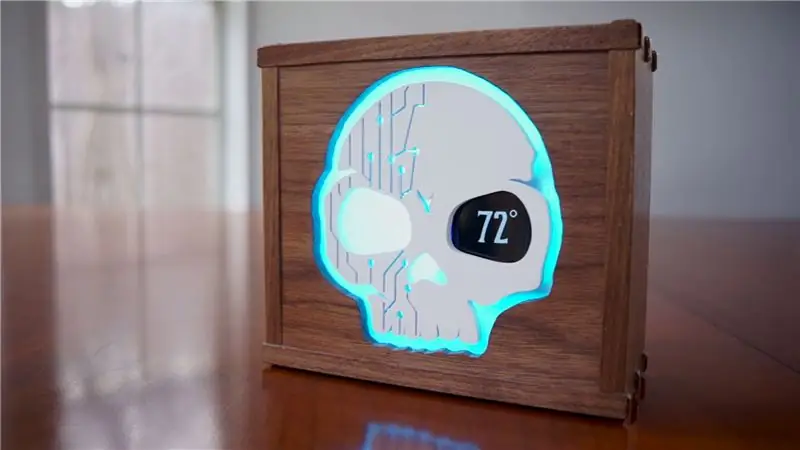
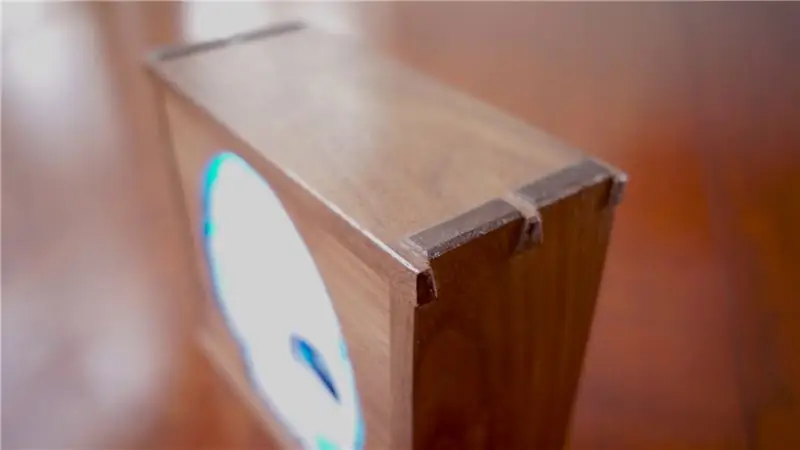
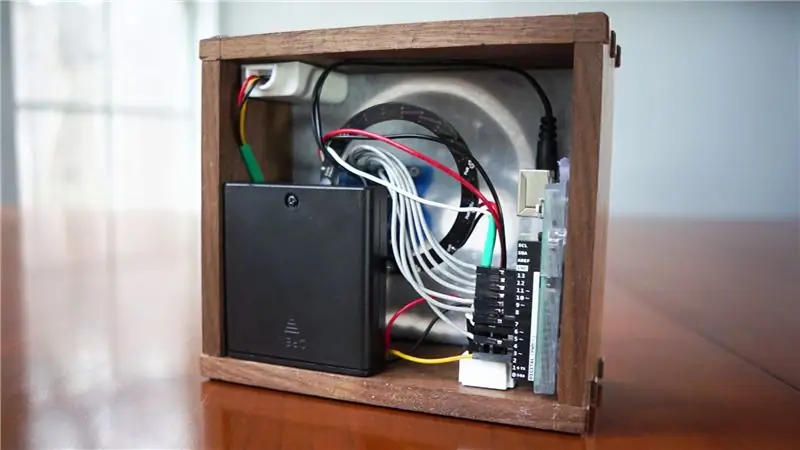
Comme Jaimie le mentionne dans la vidéo, ce projet a pris BEAUCOUP PLUS LONGTEMPS que nous ne le pensions lorsque nous l'avons commencé. Mais, il s'en est vraiment bien sorti. Il vit désormais dans notre boutique et nous permet de savoir en un coup d'œil à quel point il fait humide dans la boutique.
Pour une raison quelconque, nous ADORONS mélanger le travail du bois fin et la technologie. C'est tellement amusant.
Ce que nous préférons dans ce projet interdisciplinaire, c'est qu'il nous rappelle que lorsque vous mélangez la créativité et la passion de créer des trucs géniaux, il n'y a vraiment aucune limite à ce que vous pouvez inventer et fabriquer.
Maintenant… va faire quelque chose !
Merci d'avoir lu! Vous voulez voir plus de nos trucs?
Conseillé:
Capteur de température et d'humidité à énergie solaire Arduino en tant que capteur Oregon 433 mhz : 6 étapes
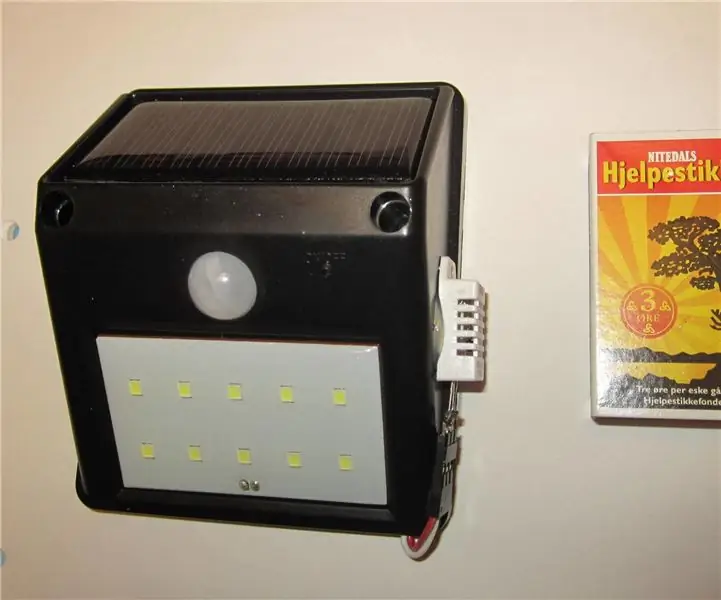
Capteur de température et d'humidité à énergie solaire Arduino en tant que capteur Oregon à 433 mhz : il s'agit de la construction d'un capteur de température et d'humidité à énergie solaire. Le capteur émule un capteur Oregon de 433 mhz et est visible dans la passerelle Telldus Net. Capteur de mouvement à énergie solaire" d'Ebay. Assurez-vous qu'il est écrit 3.7v pâte
Moniteur d'humidité sans fil (ESP8266 + capteur d'humidité) : 5 étapes
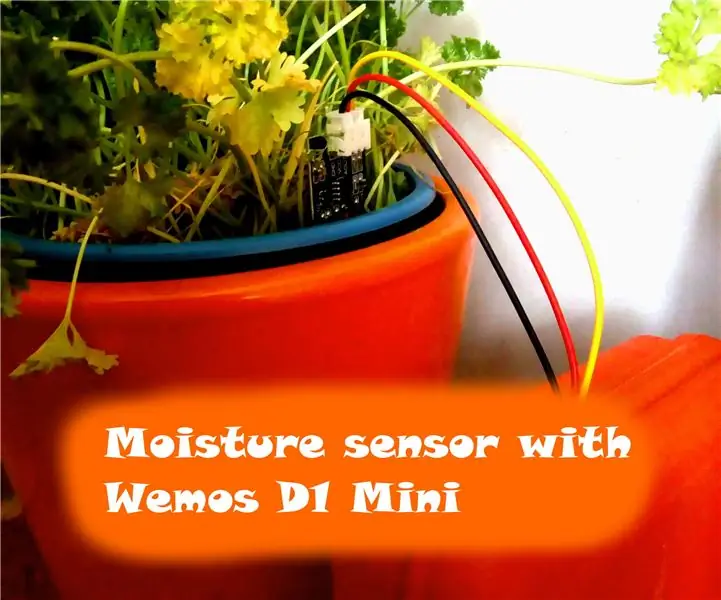
Moniteur d'humidité sans fil (ESP8266 + capteur d'humidité) : j'achète du persil en pot, et la majeure partie de la journée, le sol était sec. J'ai donc décidé de faire ce projet, sur la détection de l'humidité du sol en pot avec du persil, pour vérifier, quand j'ai besoin de verser de l'eau. Je pense que ce capteur (Capacitif d'humidité v1.2) est bon bec
Capteur d'humidité pour plantes DIY avec Arduino : 6 étapes (avec photos)

Capteur d'humidité pour plantes bricolage avec Arduino : voir ce projet sur mon site Web ! Ce projet calculera la teneur en eau du sol autour d'une plante en mesurant la constante diélectrique (la capacité du sol à transmettre de l'électricité) et vous alertera avec une LED rouge lorsque le la plante a besoin de plus d'eau o
Robot Arduino avec queue, assemblage de queue : 11 étapes
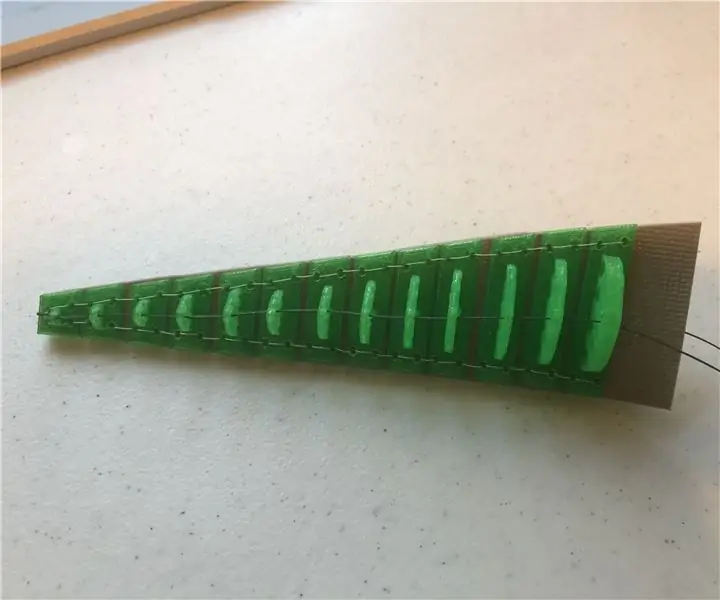
Robot Arduino avec queue, assemblage de la queue : cette instructable vous montre comment imprimer et assembler la queue
Queue oscillante à fil souple (cours TfCD, TU Delft): 5 étapes (avec photos)
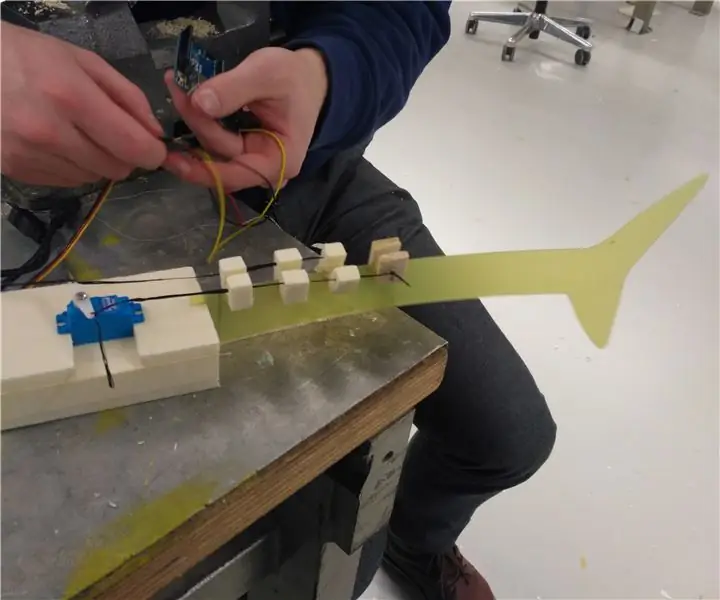
Queue oscillante à fil souple (cours TfCD, TU Delft) : une exploration technologique a été exécutée pour déterminer la possibilité d'actionner un robot poisson avec un corps actif à fil et une queue souple. Nous utilisons un matériau à la fois solide pour servir de colonne vertébrale et flexible, créant un pli uniforme