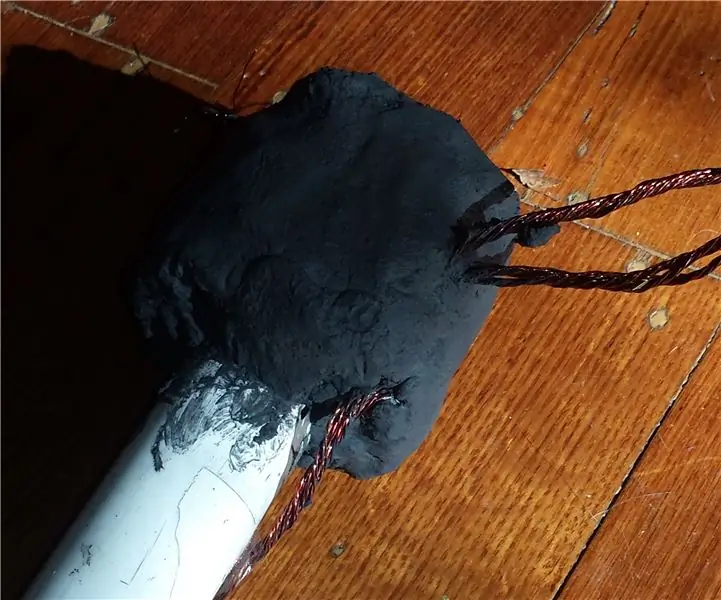
Table des matières:
- Étape 1: Qu'est-ce que la ferrite ?
- Étape 2: Pourquoi ne puis-je rien trouver pour mouler ma propre ferrite ?
- Étape 3: D'accord, mais à quoi sert ma ferrite maison ?
- Étape 4: Avantages et inconvénients
- Étape 5: Comment est-il fabriqué et de quoi ai-je besoin ?
- Étape 6: Comment l'utiliser sur des objets sensibles à l'humidité ou pour sceller dans l'électronique
- Étape 7: Comment pouvez-vous aider ?
- Étape 8: Mettez à jour
- Étape 9: Mettez à jour ! Peut-être le dernier de tous les temps…
2025 Auteur: John Day | [email protected]. Dernière modifié: 2025-01-23 14:46
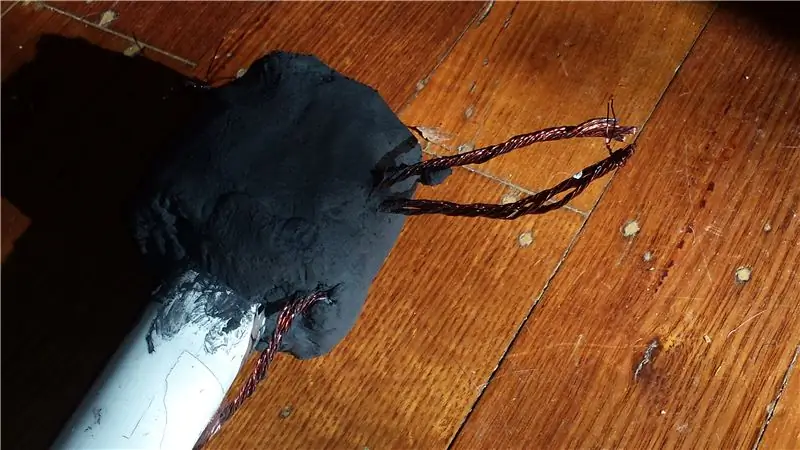
Mise à jour du 2018-05-09: je l'ai refait, profitez-en ! Mise à jour du 2015-03-07: j'ai trouvé la bonne solution - vérifiez la dernière étape !
Vous avez peut-être vu mon Instructable pour le chauffage à induction simple et avec mon premier, j'ai ressenti le besoin de trouver des moyens d'améliorer la puissance de sortie.
Les passionnés d'électronique savent déjà que la ferrite est largement utilisée pour les petits transformateurs, les bobines d'arrêt et même les antennes.
Avec cette grande variété, il est évident que vous trouverez de nombreux types de ferrite différents conçus pour un travail spécifique.
Des facteurs tels que le flux magnétique, la saturation du noyau et la plage de fréquences ne sont que quelques-uns des paramètres qui peuvent être importants pour de bonnes performances.
Ce que j'utilise pour mes besoins n'est peut-être même pas considéré comme de la ferrite par un professionnel, mais il fait plutôt bien le travail.
Ce Instructable est un travail en cours pour moi car je vais le mettre à jour et le compléter avec des images « en déplacement », donc chaque fois que je fais un nouveau lot ou essaie une nouvelle recette, vous verrez les résultats ici - alors restez au courant des mises à jour
Si mon temps le permet, je ferai la prochaine ferrite au cours du week-end à venir
Ce sera à base de plâtre et je prendrai aussi quelques photos et une courte vidéo
Veuillez poster vos commentaires ou améliorations et je mettrai à jour l'Instructable en conséquence
Étape 1: Qu'est-ce que la ferrite ?
La ferrite au sens commercial est un mélange comprimé principalement d'oxyde de fer et de liants.
Selon les propriétés nécessaires, de l'oxyde de zinc et même des métaux des terres rares sont ajoutés.
Habituellement produit sous des pressions et une chaleur extrêmes, ce qui donne une céramique semblable à la finlandaise.
Vous pouvez rechercher sur Wikipedia des informations plus détaillées car ce n'est pas si pertinent pour ce Instructable.
Étape 2: Pourquoi ne puis-je rien trouver pour mouler ma propre ferrite ?
Assez facile:
Il n'y a qu'une poignée de fabricants qui ont de la ferrite moulable ou usinable dans leur catalogue - et ils traitent très bien leurs formules !
De plus, les prix ne sont pas vraiment attractifs pour des personnes comme vous et moi.
Même si vous trouvez un fournisseur, vous devez indiquer le but et les propriétés magnétiques dont vous avez besoin ou faire vos propres calculs sur la base des fiches techniques fournies.
Étape 3: D'accord, mais à quoi sert ma ferrite maison ?
Comme dit au début, j'avais besoin de quelque chose pour mon chauffage par induction qui ne sature pas avec les champs magnétiques extrêmes impliqués et je voulais également une forme de blindage pour éviter les interférences.
Avec le mix actuel (à la fin des étapes), j'ai accompli les deux.
Je ne peux pas le recommander pour l'utilisation de bobines HF spécifiques ou similaires car je n'ai aucun moyen de vérifier les propriétés et les champs magnétiques avec mon équipement limité - désolé pour cela !
Mais si vous fabriquez vos propres électro-aimants, bobines d'induction ou avez besoin de diriger généralement des lignes de champ magnétique, cela pourrait être exactement ce dont vous avez besoin.
Également pour le blindage général des fréquences HF, cela devrait fonctionner assez bien, permettant de sceller complètement un circuit dans la ferrite afin qu'aucune fuite ne puisse se produire (ou mieux: devrait se produire).
Par exemple:
Un boulon de 8 mm dans ma bobine avec un manteau de ferrite prend environ 90 secondes pour devenir rouge, avec un manteau de ferrite autour de la bobine de travail, le temps est réduit à moins de 30 secondes.
Étape 4: Avantages et inconvénients
Eh bien, comme pour toutes les nouvelles choses, elles ne sont jamais vraiment parfaites;)
Je commencerai par les choses négatives d'abord:
* C'est très salissant à produire, donc des gants et un mélange extérieur sont fortement recommandés car vous ne voulez pas nettoyer la poussière d'oxyde de fer dans votre cuisine.
* Il n'est pas facile à mélanger car l'oxyde de fer est très fin et a tendance à ignorer toute liaison au début du mélange.
* Le mélange n'est pas encore parfait, vous devrez donc peut-être tester le mélange dans un petit lot pour vérifier s'il correspond à vos besoins.
Maintenant les bons morceaux:
* Vous pouvez le mettre dans n'importe quelle forme dont vous avez besoin. * Il peut être poncé ou percé une fois durci. * C'est un bon bouclier contre les interférences. * Une fois mélangé, il est facile à manipuler et à façonner. * Vous n'avez besoin d'aucun équipement spécial ni d'ingrédients coûteux.
* Vous pouvez facilement modifier le mélange pour l'adapter à vos besoins.
Étape 5: Comment est-il fabriqué et de quoi ai-je besoin ?
Outils et choses que vous devez avoir:* Gants en caoutchouc
* Un récipient de mélange approprié - j'utilise ceux pour mélanger le plâtre
* Cuillère, spatule ou similaire pour le mélange
* Une zone que vous nettoyez avec un nettoyeur haute pression ou qui ne se salit pas un peu
Des choses pour vous faciliter la tâche:
* Un peu de patience;)
Ingrédients:
* Oxyde de fer - le type noir également connu sous le nom de Fe3O4, couramment utilisé pour colorer le béton et assez bon marché
* Plâtre - Plâtre de Paris, mastic mural, ou un certain type de résine selon vos besoins (c'est le liant)
* De l'eau si vous utilisez du plâtre ou similaire, sinon vérifiez les instructions de votre résine
* Oxyde de zinc et d'autres choses que vous trouvez lors de la recherche de compositions de ferrite si vous en ressentez le besoin et que vous l'obtenez pas cher - totalement facultatif !
Comment le mélanger:
D'abord quelques explications;
Vous souhaitez utiliser le moins de liant possible, sinon les propriétés de votre ferrite pourraient ne pas être celles attendues.
Pour les applications à haute puissance, comme une bobine d'induction, vous aurez besoin d'une épaisse couche de ferrite car sinon le noyau saturera ou pourrait chauffer - cela ne nuit pas de l'utiliser trop épais et vous pouvez toujours en ajouter plus (autour) si la saturation est un problème, idem pour trop car vous pouvez poncer ou utiliser un fichier.
Ne mélangez que ce que vous pouvez gérer pendant le temps de durcissement !
Faites une estimation approximative du volume final dont vous avez besoin pour votre projet et ajoutez 20% de plus pour économiser. J'ai opté pour la version en plâtre car c'était ma première façon de le faire et parce que c'est la plus simple.
Ajoutez l'oxyde de fer dans votre récipient de mélange (mettez des gants maintenant si vous les avez oubliés;)) suivi d'environ un tiers de volume de plâtre. Mélangez bien à sec - pour des lots plus importants, l'utilisation d'un pot avec couvercle vous permet d'économiser beaucoup de noir la poussière vole partout !
Maintenant, ajoutez l'eau et continuez à mélanger comme vous le feriez pour du plâtre mormal afin qu'il n'y ait pas de grumeaux.
Ne vous inquiétez pas si vous avez utilisé trop d'eau car vous pouvez toujours ajouter de l'oxyde et du plâtre.
Sachez que ce mélange sèche un peu plus vite et peut produire des fissures dans des couches plus épaisses, il peut donc être nécessaire de travailler par petites étapes avec de nouveaux mélanges à accumuler (garder le mélange sec et n'utiliser avec de l'eau que ce dont vous avez besoin).
Vous pouvez maintenant le mettre dans un moule ou recouvrir ce dont vous avez besoin pour le protéger.
Laissez-le reposer dans un environnement humide pour éviter les fissures - je l'enveloppe simplement dans une serviette humide (très ancienne à cause de l'oxyde noir !).
Après environ 2 heures, vous pouvez continuer à le laisser sécher à l'air libre.
Le temps de durcissement final dépend de l'épaisseur et de l'humidité !
Pour l'humidité, réchauffez-le jusqu'à environ 30° Celsius et placez-le dans un récipient fermé qui était dans votre congélateur pour qu'il refroidisse. S'il n'est pas complètement sec, vous verrez une perte de brouillard se condenser à l'intérieur de votre récipient.
Étape 6: Comment l'utiliser sur des objets sensibles à l'humidité ou pour sceller dans l'électronique
Il n'y a qu'un seul moyen et ce en s'assurant que l'humidité n'y pénètre pas !
Soit le sceller d'abord à l'aide de peinture, de résine, etc., soit de fabriquer un moule pour la ferrite et d'y placer la pièce une fois complètement durcie.
Si ce n'est pas une option, vous devez utiliser une résine coulable ou moulable au lieu du plâtre.
Pour les compositions 2K, cela signifie que vous devez ajouter une quantité égale d'oxyde aux deux composants du mélange.
Bien que le Fe3O4 ne soit pas très réactif, il peut affecter le durcissement des résines 2K, alors faites d'abord un petit lot pour tester d'abord pour vous assurer qu'il durcit correctement et ne chauffe pas trop pendant le durcissement.
Il est très difficile de donner des rapports de mélange appropriés car les propriétés des différentes résines diffèrent trop, mais je descends d'un mélange 50/50 jusqu'à ce que je remarque que le mélange devient un problème ou que le durcissement n'est pas assez bon.
Mais généralement, je ne passe pas sous un mélange de 35% de résine à 65% d'oxyde.
Étape 7: Comment pouvez-vous aider ?
Vous pouvez aider à perfectionner la fabrication de la ferrite en publiant vos commentaires et vos recettes testées.
J'ajouterai plus de photos avec mon prochain lot et ajouterai une autre étape pour les mélanges collectés à partir des commentaires pour une référence facile pour tout le monde ici.
Étape 8: Mettez à jour

J'ai réalisé par le nombre de coups que je devais précipiter un peu les choses pour que cette instructable soit complète. Après avoir expérimenté des additifs pour réduire le risque de formation de fissures pendant le processus de séchage, j'ai décidé d'utiliser cette variation pour une vidéo sur la façon de faire le ferrite.
Pour vous donner une longueur d'avance sur la nouvelle recette, je vais la résumer ici afin que vous ayez une idée de ce qui se passe dans la vidéo.
1. Préparez-vous avec des gants et tout ce dont vous avez besoin, vous verrez les choses dans la vidéo.
2. N'essayez pas de suivre la vidéo tout de suite, regardez-la au moins deux fois et utilisez le bouton pause si je suis trop rapide dans la vidéo.
3. Ne le faites pas à l'intérieur car la poussière noire va partout !
4. Les ingrédients sont:
Plâtre de paris - ou tout autre plâtre de modelage que vous avez sous la main (Gypse).
Oxyde de fer noir
Un peu de colle à papier peint ou, si vous n'en trouvez pas dans votre région, utilisez de la colle à bois - cela aide à garder le mélange utilisable plus longtemps et ralentit le processus de séchage. Le produit fini ne se fissure pas aussi facilement.
De l'eau et quelques outils pour le mélange et le modelage - tout ce qui vous convient le mieux et la quantité que vous faites.
5. La colle doit être ajoutée à l'eau en premier et seulement en petites quantités pour la colle à papier peint, la colle à bois doit être ajoutée dans un volume d'environ 15% à l'eau.
Je pourrais sauter ce morceau dans la vidéo et préparer le mélange de colle à l'eau à l'avance car cela prend un certain temps avec de la colle pour papier peint.
Faire un mélange sec de plâtre et d'oxyde, je le fais avec une cuillère.
Selon le mélange, vous obtiendrez un assez bon ou un assez mauvais résultat en termes de stabilité mécanique.
J'essaie d'utiliser 3 à 5 parties de plâtre pour 4 parties d'oxyde, un mélange 50-50 semble bien fonctionner mais j'essaie toujours de rester en dessous pour avoir plus de ferrite que de plâtre dans le mélange.
Plus vous ajoutez d'oxyde, meilleures sont les propriétés magnétiques du produit fini, mais plus il est difficile à travailler et à durcir sans fissures.
Ajoutez de l'eau (déjà préparée avec de la colle) puis votre mélange sec dans un récipient de mélange approprié et mélangez bien jusqu'à ce qu'il y ait des grumeaux, gardez le mélange assez épais pour travailler avec mais pas si fin qu'il ne coule pas, à moins que vous ne fassiez un moulage.
Une fois que vous commencez à mélanger, l'horloge tourne car vous n'avez qu'un temps limité jusqu'à ce que le mélange devienne dur et devienne inutilisable.
Il est préférable de travailler avec de petits lots que vous pouvez appliquer correctement avant le début du séchage initial.
Important!!:
Vous devez utiliser des outils et des récipients propres car même de petites quantités de mélange durci gâcheront votre prochain lot !
Cela fera durcir le mélange beaucoup plus rapidement et peut provoquer des grumeaux dans le mélange lorsqu'il durcit plus rapidement que le reste.
J'essaie de laver mes outils et mes contenants avant que le plâtre ne durcisse complètement.
Comme vous pouvez le voir dans la vidéo, je n'en fais qu'une petite quantité pour mettre la première couche sur la bobine.
Je le fais de cette façon pour permettre un meilleur séchage car nous voulons éviter de capturer trop d'humidité avant d'ajouter la couche suivante.
Vous devriez prendre votre temps pour le laisser sécher - soit naturellement, soit à l'aide d'un déshydrateur.
S'il reste trop d'humidité avant le durcissement final dans le four, des fissures massives se produisent.
Le meilleur moyen est de laisser sécher le produit fini pendant quelques jours avant de le mettre au four.
Si vous couvrez des pièces sensibles à l'humidité, il est préférable d'ajouter une couche de peinture comme barrière. Pour de meilleurs résultats, poncez rapidement la peinture pour obtenir une surface rugueuse, car cela aidera le mélange à adhérer.
Au cas où vous seriez pressé, essayez les mélanges de colles à carrelage flexibles de votre quincaillerie sans la colle dans le mélange.
Mais faites d'abord quelques tests à petite échelle pour vérifier si votre mélange produit des fissures en séchant. Mise à jour du 2015-03-07: j'ai expérimenté un peu plus avec beaucoup de liants différents (possibles). la cuisine ou la pharmacie locale (à des prix raisonnables) a fonctionné. tirez-moi dessus… Quoi qu'il en soit, je vais essayer d'expliquer: le silicate de sodium est un autre produit chimique « oublié » en termes d'utilisation domestique. Certains le savent peut-être encore grâce à l'expérience chimique « Chemical Garden ». et du miel chaud dans la consistance et le verre clair. Une fois séché, il devient dur comme de la pierre - une caractéristique utilisée pour les réparations sur le bois, la porcelaine et d'autres choses comme les carreaux résistants à la chaleur. Si vous connaissez "Green Sand Casting", vous êtes déjà familier avec juste en ajoutant un tout petit peu d'eau à ce mélange. J'ai fait la même chose avec avec l'oxyde noir. Commencé avec quelques cuillères à soupe d'oxyde et ajouté du silicate de sodium en petites quantités. Crée beaucoup de grumeaux et de petites boules, donc faire cela dans un petit broyeur à boulets pourrait être une bonne idée (à part le peu de nettoyage) Quoi qu'il en soit, si vous regardez les vidéos sur le moulage au sable de Grenn, vous verrez que le mélange a l'air presque sec mais qu'il garde sa forme lorsqu'il est pressé - j'ai essayé la même chose mais à la fin j'ai utilisé une forme de bloc et un petit marteau pour le compacter. (Cela rappelle Je dois mentionner pour retirer le mélange de ferrite de la forme après cette étape - je ne l'ai pas fait et il était impossible de retirer la substance durcie de la forme). Après cela, l'éprouvette est passée au four pendant environ 90 minutes à pleine chaleur - cela crée une "ferrite" agréable et dure. Pour obtenir, elle est suffisamment dure pour être utilisée, elle est placée dans un four et est lentement chauffée jusqu'à une orange éclatante. Après cela, le refroidissement a été effectué dans le four, préchauffé à plein. Le four a été tourné une fois la pièce insérée et laissée à refroidir complètement pendant la nuit. Le résultat était que 1. Je w comme incapable d'extraire la ferrite durcie de la boîte en métal que j'ai utilisée.2. C'est si dur que je ne pouvais pas percer dedans.3. Il ne se brise pas et ne se fissure pas. Je vais essayer de trouver plus de temps et d'oxyde noir et faire une courte vidéo du processus. En attendant, tous ceux qui suivent encore peuvent expérimenter car la seule chose qui compte est d'humidifier l'oxyde avec le silicate de sodium pour qu'il se lie correctement. Pendant le compactage, un peu d'excès peut être pressé, ce qui indique d'utiliser encore moins de silicate de sodium pour le prochain mélange. Le seul inconvénient est que vous devez fabriquer un petit four, un fondoir ou un four pour vous pouvez durcir complètement le mélange, qui est fondamentalement comme une céramique une fois durcie.
Étape 9: Mettez à jour ! Peut-être le dernier de tous les temps…
J'ai finalement fait des progrès vraiment décents:)Mes abonnés ici ont certainement beaucoup expérimenté aussi, mais il m'a fallu environ 2 ans pour finalement être touché par le poteau de clôture:)Résumons ce que nous savons encore en premier: l'oxyde de fer est assez bon pour beaucoup de matériaux de base de base. De nombreuses autres poudres minérales et métalliques peuvent être ajoutées pour la performance et nous avons la chance de pouvoir les rechercher la plupart sur Google et Wikipedia. Créer un formulaire n'est pas trop difficile non plus… Mais jusqu'à présent, nous avons eu du mal à créer quelque chose de vraiment durable. Plus maintenant…. Les noyaux de ferrite appropriés sont en céramique cuite, malheureusement la plupart d'entre nous n'auront pas l'équipement, sans parler des connaissances pour cela. Un liant approprié serait idéal et je pense en avoir trouvé un. Que diriez-vous d'utiliser quelque chose qui peut être dissous dans l'eau et qui sèche comme du verre ? Silicate de sodium:) ou l'obtenir sous forme liquide, les préparations sont sli très différent. Voici la manière de faire de base: Vérifiez d'abord comment le liquide sèche. Alors, soit mélangez de la poudre avec de l'eau, soit étalez votre scellant directement avec un pinceau sur du carton. Vous remarquerez qu'en fonction de la concentration, le liquide sèche différemment. Trop et vous obtenez une belle croissance cristalline. Trop peu et vous obtenez juste une couverture légèrement brillante sur le carton. Obtenez-le juste et vous finirez avec une couche dure, comme du vernis. Appliquer plusieurs couches sur le préalablement séché, il faut former un verre comme un couvercle sans croissance de cristaux ou formation de taches blanches. C'est la concentration que vous souhaitez utiliser pour lier le mélange de ferrite. La préparation de la ferrite est principalement réduite à s'assurer qu'elle est aussi fine que possible et en morceaux gratuit. Vous pouvez le passer au tamis fin si vous le souhaitez, mais la poudre de la quincaillerie ou du magasin d'art est généralement assez bonne. Le seul problème majeur avec l'oxyde de fer sous forme de poudre est que les particules refusent généralement de se mouiller ou d'accepter tout " colle e" revêtement". La solution simple à ce problème m'a donné beaucoup de maux de tête…Eh bien, jusqu'à ce que je réalise à quel point cela peut être simple dans la réalité si vous arrêtez de penser trop compliqué LOLTprenez un récipient de préférence qui n'est plus utilisé ou juste une bouteille de soda et remplissez le quantité de mélange de ferrite dont vous avez besoin. Assurez-vous de pouvoir le fermer et le sceller correctement ! Vous verrez pourquoi je préfère les bouteilles de soda ici… Vous ne devez jamais remplir à plus de 1/4… Ajoutez maintenant de l'eau, de préférence de l'eau distillée ou au moins déminéralisée, veuillez ne pas utiliser d'eau du robinet. Vous verrez que rien de vraiment mélanges, donc ajoutez assez d'eau pour permettre une bonne secouage. D'accord, je n'ai pas dit de le secouer mais maintenant que vous l'avez vu, vous avez vu que le résultat est toujours aussi nul…. Ajoutez quelques gouttes de liquide vaisselle et réessayez;) Si dedans sans doute ajouter une cuillère à café d'une valeur ou deux. Soudain, le secouage crée une bouillie ou si vous aviez l'habitude de beaucoup d'eau un liquide noir. Mais plus de grumeaux qui flottent, toute la poudre est maintenant vraiment humide. Séchage de la ferrite… de l'eau savonneuse, il est donc préférable de laisser reposer la bouteille pendant la nuit. Maintenant, la majeure partie de l'eau peut être renversée. J'ai essayé de faire sortir le mélange de ferrite humide de plusieurs manières et, à part couper la bouteille, les vibrations semblent bien fonctionner. Un moteur de vibration d'un vieux contrôleur de jeu ou d'un jouet jeté de votre petite amie fera des merveilles pour faire couler la boue le b cou de loutre. Étalez-le sur du papier sulfurisé avec des serviettes en papier autour pour absorber l'eau - ou faites-le à l'extérieur et laissez l'eau s'écouler. Le reste peut être aplati un peu et si vous avez besoin d'accélérer les choses, laissez-le sécher au four à 70-80°C - ne le laissez pas atteindre le point d'ébullition car cela gâcherait le savon et nous avons besoin de ce couvercle de savon ! Une fois sec, cassez-le et séchez-le à nouveau jusqu'à ce que vous puissiez l'écraser à nouveau poudre dans un mortier ou un moulin à café mis au rebut - faites attention à la poussière et faites-le à l'extérieur !! Notre mélange de ferrite savonneuse peut maintenant être utilisé avec toutes les colles et peintures à base d'eau, comme la colle à bois PVA ou la peinture standard de la quincaillerie. L'inconvénient est que toutes ces choses ont tendance à rétrécir assez mal et ne fournissent qu'une dureté plus ou moins caoutchouteuse. Le silicate de sodium sèche cependant littéralement comme du verre ! Bien sûr, ce serait trop facile si le reste était simple: (Le gros problème auquel nous sommes confrontés est aussi caractéristique principale du silicate de sodium: il scelle vraiment bien. Ainsi, faire une tige de ferrite serait aussi simple que mélanger la ferrite avec juste assez de mélange de silicate de sodium pour créer une substance semblable à du mastic, couper la tête de la seringue et la remplir hermétiquement. Une fois pressée, vous avez une tige que vous pouvez laisser sécher. à l'extérieur au mieux, l'intérieur sera alors scellé et restera humide pour toujours. Eh bien,au moins plusieurs mois et puis tout craquer lentement… Sachez simplement mon niveau de frustration: pour la dernière étape, j'ai gaspillé environ 3 kg d'oxyde de fer dans une quantité infinie de petits lots et d'expériences… J'ai trouvé deux façons dont ils montrent au moins un approche faisable du problème. Numéro un: accumulation de matériau. Pour éviter que l'humidité ne soit piégée lors du séchage ou du durcissement, cela peut aider à gaspiller beaucoup. Laissez-moi vous expliquer…En supposant que vous vouliez faire un noyau comme un tore de plus de 5 cm de diamètre. Ici, je créerais un gabarit en carton, juste un anneau et les deux parois annulaires. Le diamètre extérieur et intérieur doit être juste au-dessus/en dessous de ce dont vous avez besoin si les dimensions sont vraiment vitales. Remplissez une fine couche sur le fond et séchez-le au four à moins de 90°C. Ajouter un autre et faire de même. Pour que cela fonctionne le mélange doit être le plus sec possible, cherchez comment préparer du "sable vert" et vous voyez ce que je veux dire. Doit être possible de former une boule dans votre main et si vous essayez de l'ouvrir, vous devriez obtenir deux pièces avec une ligne de rupture claire. Le mélange sèche également à l'air, alors gardez-le couvert et mélangez-le de temps en temps! Une fois que vous avez suffisamment rempli, commencez à lisser la surface avec les derniers ou les deux derniers remplissages. Laissez le tout sécher à nouveau pendant quelques heures au four. Ensuite monter la chaleur à 180°C pendant deux heures. Cela devrait donner un noyau vraiment dur et durable que vous pouvez maintenant poncer ou limer pour enlever le carton. L'utilisation d'un moule en silicone est certainement utile si vous voulez faire plus d'un noyau. Numéro deux: Tout risquer… Pour les noyaux plus petits ou tout ce qui est assez plat, vous pouvez essayer de cette façon. Faites un moule en acrylique épais, comme une plaque d'au moins 4 mm. Faites-le de sorte que vous ayez des encoches pour tout assembler comme vous le faites vraiment Je ne veux pas la coller ensemble. La plaque inférieure doit être percée de nombreux petits trous. J'ai utilisé un filtre en acier inoxydable comme gabarit et percé à travers les trous de la grille. Vous ne voulez pas de trous de plus de 1 mm, de préférence en dessous si vous pouvez utiliser un cutter laser pour créer votre moule. Ces trous sont essentiels pour drainer le liquide tout en gardant le mélange insi du moule. Couper du papier filtre pour couvrir le fond et les côtés de votre moule. Pour le fond, vous voulez deux couches. Avec un test de couvercle de presse approprié si vous pouvez vraiment l'insérer à l'intérieur sans aucun espace - il doit être aussi serré que possible sans se coincer. C'est l'heure d'un test: Avec le papier filtre en place et le moule sur une surface qui vous permet de sécher, remplissez votre moule de morceaux de citron ou d'orange - pelez d'abord s'il vous plaît… Si vous appuyez assez fort, le jus devrait s'écouler le trous de drainage, un peu de jus autour du couvercle de la presse aussi mais pas de pulpe ou quoi que ce soit qui sort du dessus. Dans ce cas, vous pouvez nettoyer votre désordre et être heureux. Si beaucoup de matière sortait de l'espace autour du couvercle de la presse dont vous avez besoin pour en faire un nouveau et réessayez. Une fois sec et propre, ajoutez à nouveau les papiers de classement, puis remplissez avec votre mélange de ferrite / silicate de sodium. Assurez-vous encore que c'est comme du bon sable vert, pas grumeleux, pas coulant. Utilisez une cheville ou similaire taper et appuyer sur le mix pour une compression de base et s'assurer que tous les coreners sont compressés à l'identique al - encore une fois comme faire un jet de sable grees. Une fois assez plein, ajoutez le couvercle et fournissez autant de pression que possible. Je commence généralement par ajouter simplement des poids sur le dessus jusqu'à ce que le pire écoulement soit terminé. En fonction de la taille, j'ai utilisé un morceau de bois et un marteau ou un étau pour presser ce que je peux. Parfois, il peut être utile d'essuyer le moule avec un chiffon imprégné d'huile, mais la plupart des formes de base se détachent très facilement sans coller. Prenez grand soin de retirer le noyau de le moule et n'essayez même pas de retirer le papier. La clé est maintenant de forcer l'eau restante à sortir sans laisser sécher l'extérieur, donc si dans le doub ayez un vaporisateur avec de l'eau distillée prêt pour empêcher le papier de sécher - vous besoin de garder l'extérieur humide jusqu'à ce que tout soit fait! Pour un petit noyau, le four est l'option préférée mais avec le noyau sur un petit support dans un bocal avec un peu d'eau au fond. Le remplissage de vapeur empêche l'extérieur du noyau de forment une couche de verre et la chaleur chassera la majeure partie de l'eau du noyau interne. I Si vous avez quelque chose de haut comme un bocal à spaghetti ou que vous pouvez alors élever le noyau et utiliser plus d'eau est vraiment utile. Comme nombre à partir duquel je vais vous donner un exemple qui a très bien fonctionné pour moi: le noyau était d'environ 8 mm d'épaisseur et comme un tore avec un diamètre extérieur de 9cm. J'ai utilisé 250ml d'eau avec le noyau à presque 20cm de haut dans un pot à spaghetti. Comme ça il ne restait que peu de place au "plafond" de mon four. Chaleur d'environ 90-120° (mon four aspire dans cette plage) n'a été appliqué que par le bas. Le noyau a reçu une dernière pulvérisation juste avant de placer le pot dans le four préchauffé. Après environ 10 minutes, j'ai ouvert le four pour un premier contrôle du niveau d'eau et pour laisser un peu de vapeur. Une fois que tout s'est évaporé, j'ai laissé le four à la même température pendant encore 2 heures. Sans laisser le noyau ou le four refroidir beaucoup, le noyau a ensuite été retiré du bocal et placé sur un tamis en acier inoxydable à l'envers. Temp a été porté à 200°C pendant encore 2 heures. Le noyau résultant n'avait qu'un léger cristal f ormations à l'extérieur qui ont été facilement enlevées par du papier de verre fin. Je ne pouvais pas le casser à la main et une chute d'environ 50 cm sur un carreau n'a pas non plus causé de dommages visibles, même après l'avoir essayé plusieurs fois. Cependant, un léger coup avec un marteau lorsqu'il se tenait debout, il n'avait aucun problème à le casser. Au moins, les fissures montraient que le noyau était complètement durci. Compte tenu de la petite quantité de liant sous forme de silicate de sodium qui restait, j'appelle cette recette finale pour le moment. Quelques mots de sagesse:Bien que le résultat le produit est assez durable, le silicate de sodium se dissoudra dans l'eau et d'autres produits chimiques. Une couche appropriée de peinture acrylique durable ou une couche de résine est donc indispensable si vous voulez éviter une défaillance prématurée. Mais je pense que même avec cela, c'est toujours très soigné moyen de créer un noyau de ferrite maison plus durable. Moyens possibles pour améliorer encore le durcissement et la dureté…. Le silicate de sodium a de nombreuses propriétés intéressantes et qu'il durcit comme le vrai verre est un bon bonus. Trouver les bons oxydes, poudres métalliques ou même sel s pour faire fonctionner une ferrite comme vous le souhaitez, il faut beaucoup de creuser et d'expérimenter. La meilleure option pour commencer est de rechercher les compositions répertoriées pour les noyaux bien connus. étant donné la fréquence et la saturation. Encore une fois, je laisse les expériences avec cela à mes disciples de confiance et j'espère qu'ils reprendront là où j'ai essayé de fournir les points de départ. Une bobine Rodin avec un tore en ferrite personnalisé peut-être?;) Quoi qu'il en soit… Le silicate de sodium forme une structure cristalline très dure avec le ciment. L'ajout d'une infime quantité de ciment Portland fin en poussière et encore moins de lessive a donné une solution de silicate de sodium qui crée des revêtements encore plus durables. Le problème est de trouver le bon équilibre pour éviter efflorescence cristalline indésirable pendant le durcissement et pour empêcher la poudre de ciment de se déposer trop rapidement. Dans les tests, les tests se sont terminés avec une solution de silicate de sodium très épaisse et très corrosive, une petite quantité de ciment et un peu de lessive pour l'obtenir davantage dans le PH neutre gamme. Les résultats ont montré un grand potentiel, mais je n'aime pas l'exigence d'une protection complète du corps et du visage et les risques liés à la manipulation de solutions corrosives et à leur mélange. et est toujours largement utilisé pour sceller les cheminées fissurées. Donc, si vous avez remarqué un problème dans votre ancienne cheminée en brique dans votre cabane de cachette préférée, faites un mélange de ciment avec environ 50% de l'eau remplacée par un scellant au ciment et votre prochain hiver verra la fumée sortir par la cheminée plutôt que par les fissures à l'intérieur de votre cabine. Bien que je l'aie utilisé pour réparer les fissures dans ma fonderie maison merdique… Comme vous le savez maintenant, le silicate de sodium forme une surface semblable à du verre quand durci. J'ai fait une petite expérience avec un morceau de bois. À l'aide d'une chambre à vide, je l'ai complètement trempé avec un scellant pour béton. la couche massive de cristaux à l'extérieur. La chose n'était pas seulement dure comme de la pierre, mais elle avait également l'air vraiment bien dans les zones que j'ai essayé de polir. L'eau et la plupart des produits chimiques ne l'ont en aucune façon affecté. Et bien, en essayant de le brûler dans mon tambour n'a pas fonctionné non plus. Il s'est fissuré, il a carbonisé mais c'était comme mettre une brique dans le feu… Mais la meilleure chose que j'ai essayée a été de faire l'impossible. Avez-vous déjà essayé de réparer un morceau de porcelaine fissuré ? maintenant… Oui, nous avons tous laissé tomber quelque chose en céramique ic qui a causé beaucoup de problèmes avec un être cher… J'ai abusé d'une vieille assiette qui était déjà la dernière de l'ensemble. Oups, je l'ai laissée tomber sur les tuiles…. pièces ensemble, seulement ce qui était nécessaire pour remettre la plaque ensemble sans trous ni pièces manquantes. J'aurais dû essayer un coup de marteau pour obtenir deux ou trois pièces mais j'ai compris qu'une fois que j'ai pensé que laisser tomber était le meilleur moyen… Mais cela a montré que si vous perdez suffisamment de temps à aligner le tout sur une plaque dans votre four, vous pouvez cuire la plaque ensemble pièce par pièce. Quelques couches finales des deux côtés pour obtenir une finition lisse et remplir les petits morceaux manquants et la plaque enven survit au lave-vaisselle…
Conseillé:
Fabriquez votre propre capteur d'humidité du sol avec Arduino !!! : 10 étapes
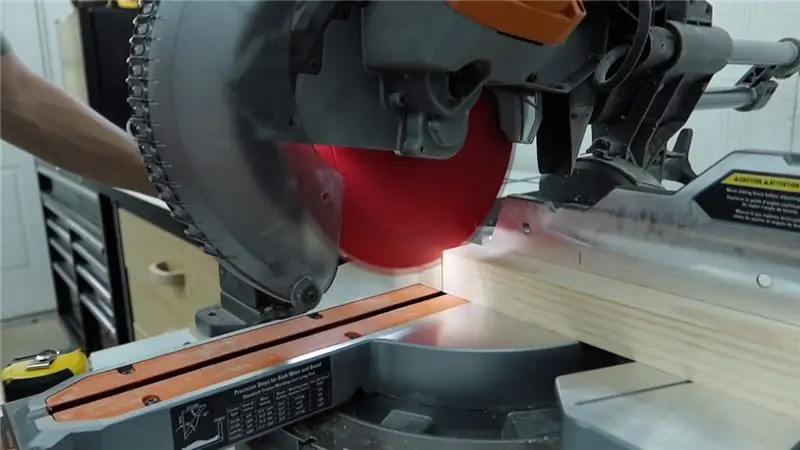
Faites votre propre capteur d'humidité du sol avec Arduino !!! : À PROPOS !!! Dans cette instructable, nous allons interfacer un capteur d'humidité du sol FC-28 avec Arduino. Ce capteur mesure le contenu volumétrique de l'eau à l'intérieur du sol et nous donne le niveau d'humidité en sortie. Le capteur est équipé à la fois d'ana
Créez votre propre affichage MQTT EInk pour l'heure, les actualités et les données environnementales : 7 étapes
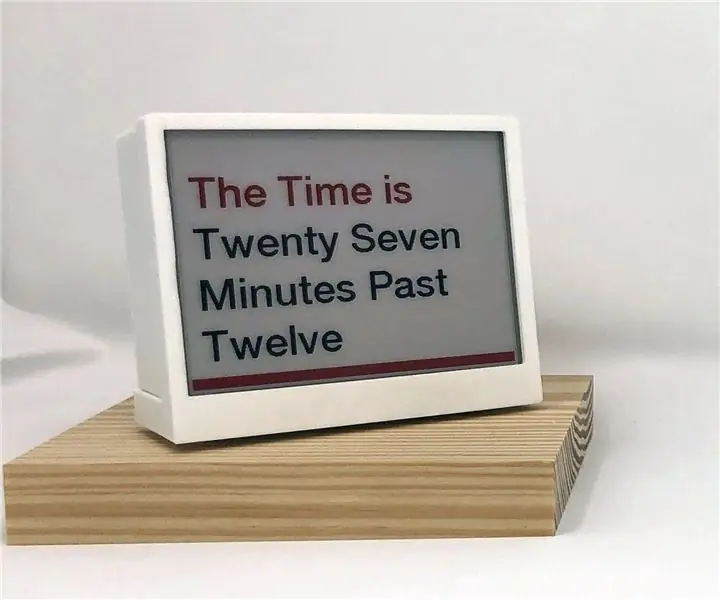
Créez votre propre affichage MQTT EInk pour l'heure, les actualités et les données environnementales : « LE » est un mini affichage d'informations MQTT pour l'heure, les actualités et les informations environnementales. Utilisant un écran eInk de 4,2 pouces, son concept est simple : afficher les informations par rotation, en se mettant à jour toutes les deux minutes. Les données peuvent être n'importe quel flux - f
Fabriquez votre propre monopode pour appareil photo avec une bouteille en liège : 3 étapes
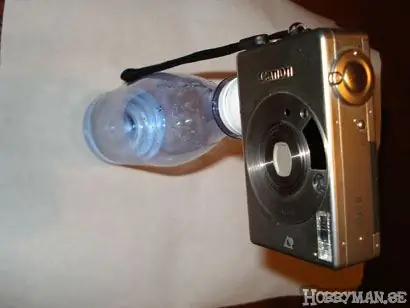
Fabriquez votre propre monopode pour appareil photo avec une bouteille en liège : Ce tutoriel est si facile à faire et aussi très bon marché. Tout ce dont vous avez besoin pour réussir est une vis de trépied de 6 mm de long (1/4") et un bouchon de bouteille. IMPORTANT. Vous devez avoir le filetage exakt sur la vis à cet effet ou vous détruirez le filetage de votre appareil photo
Fabriquez votre propre sacoche pour ordinateur portable XO : 11 étapes (avec photos)
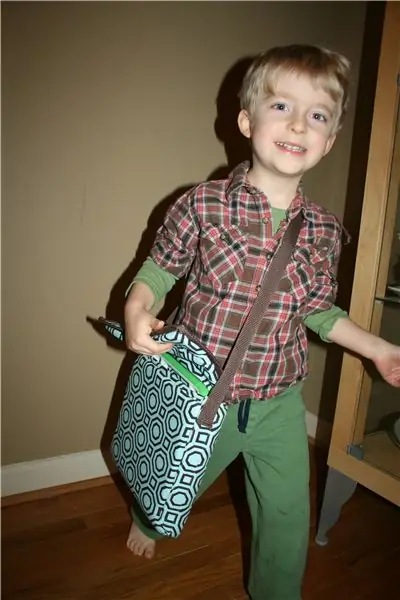
Fabriquez votre propre sac pour ordinateur portable XO : Le produit fini est un sac pour ordinateur portable personnalisé pour un ordinateur portable OLPC XO, mais ces instructions pourraient probablement être modifiées pour de nombreux appareils électroniques portables. Le noyau du sac est en mousse haute densité, renforcé de carton. Le sac est t
Fabriquez votre propre machine de nettoyage de disques professionnelle pour moins de 80 $ et économisez jusqu'à 3 000 $ et plus. : 6 étapes (avec photos)
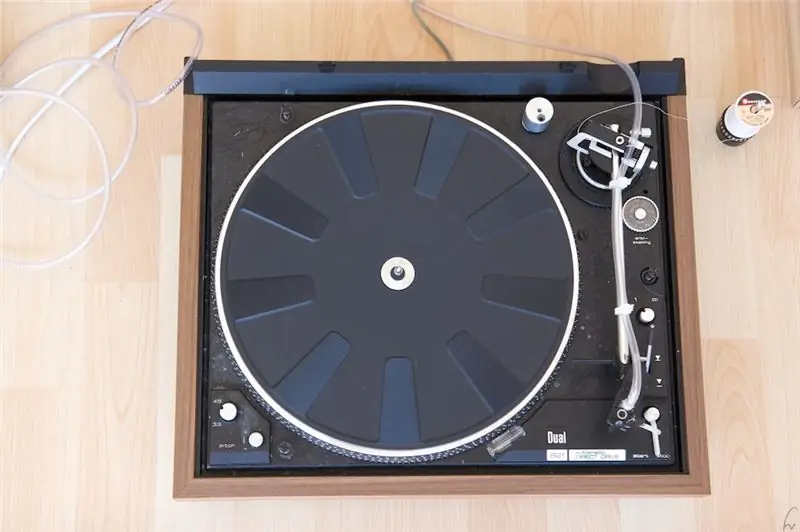
Fabriquez votre propre machine de nettoyage de disques professionnelle pour moins de 80 $ et économisez jusqu'à 3 000 $ et plus. : Excusez mon anglais. Comment nettoyer correctement les enregistrements ! Il existe de nombreuses façons de contourner Internet. Des moyens moins chers comme le Knosti ou le Discofilm mais aussi