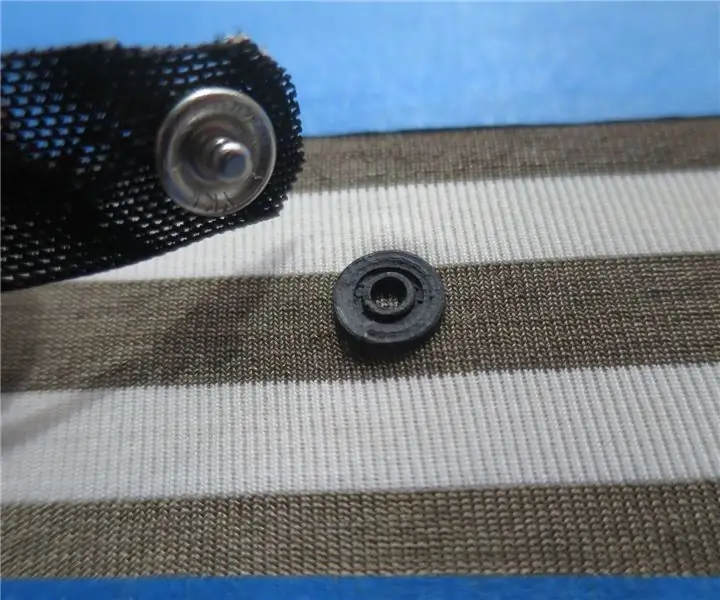
Table des matières:
- Étape 1: Fichiers Fusion360
- Étape 2: Test d'impression et configuration
- Étape 3: Impression 3D sur une trace de tissu conducteur
- Étape 4: Tester la conductivité
- Étape 5: Impression sur différentes surfaces
- Étape 6: Test d'impression multiple
- Étape 7: Lecture de la résistance
- Étape 8: rattacher les boutons-pression avec de l'époxyde conducteur
- Étape 9: Conclusion et prochaines étapes
2025 Auteur: John Day | [email protected]. Dernière modifié: 2025-01-23 14:46
Par rachelfreirewww.rachelfreire.comSuivre plus par l'auteur:
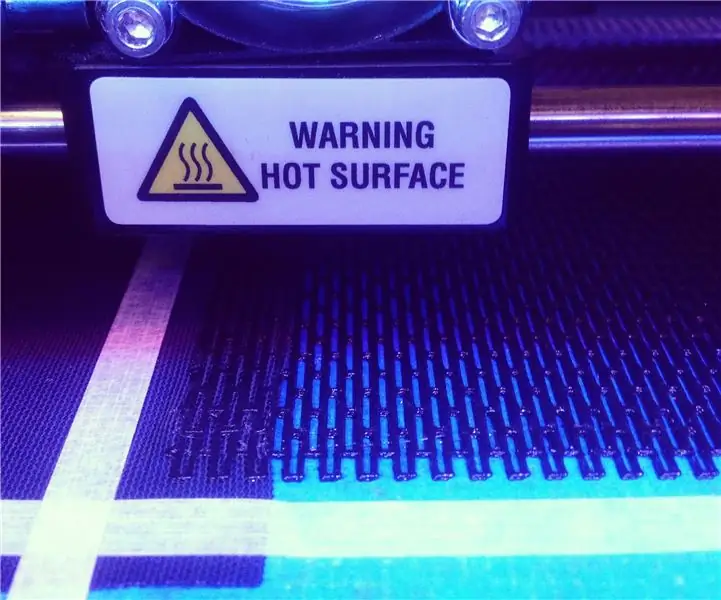
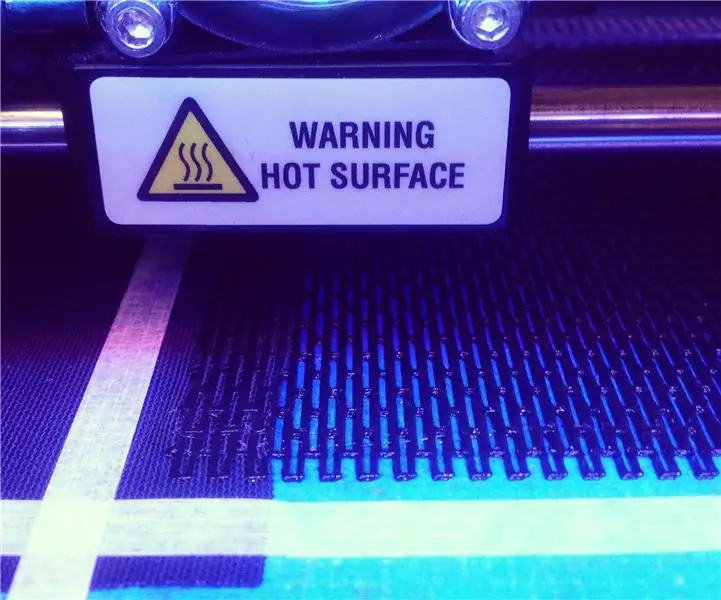
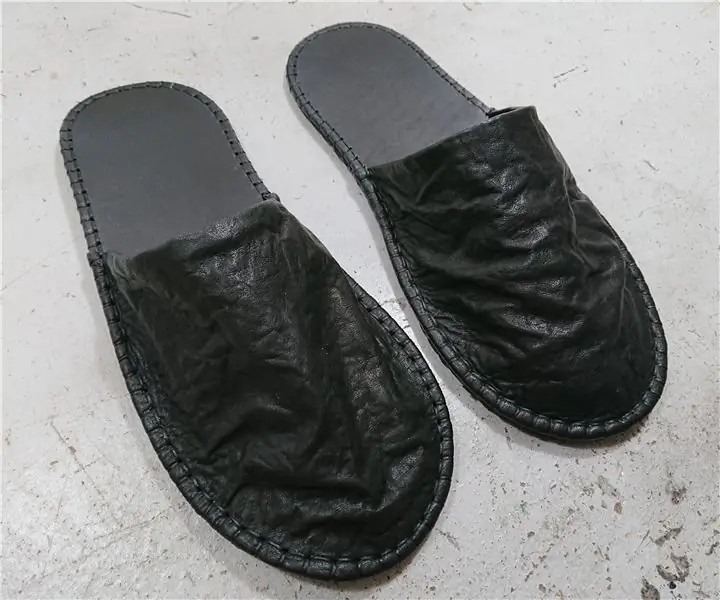
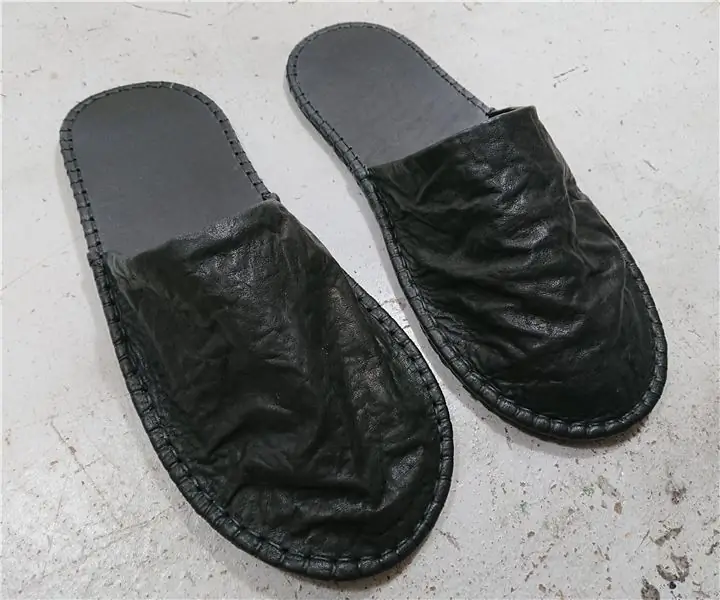
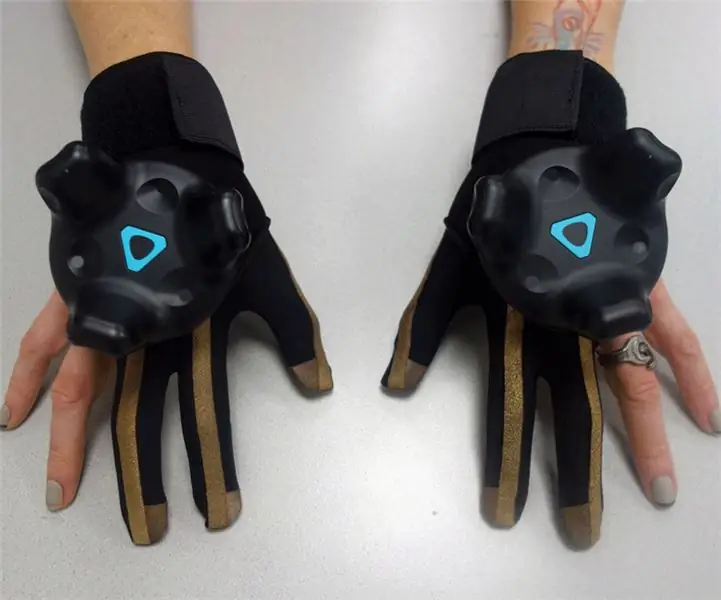
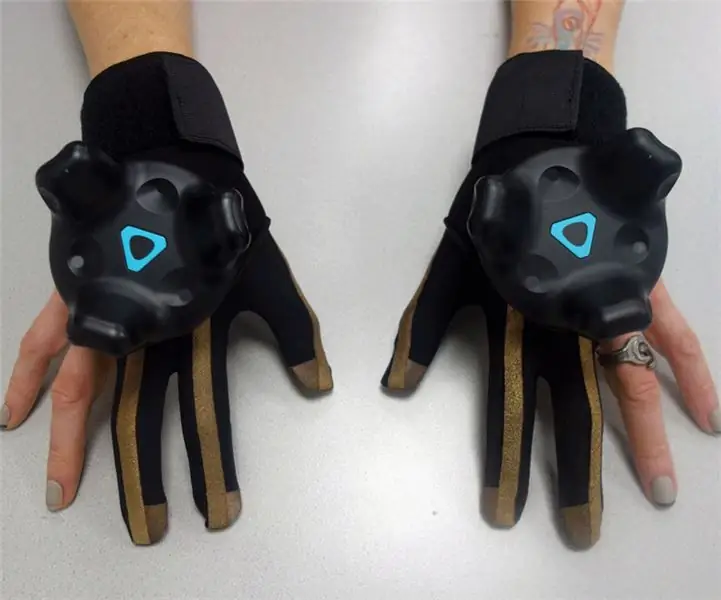
À propos: designer, ninja du cuir, explorateur technologique, ruineur de manucures En savoir plus sur rachelfreire »
Cette instructable documente ma première tentative d'impression 3D de boutons-pression conducteurs sur le tissu. Je voulais imprimer en 3D un bouton-pression femelle qui se connecterait à un bouton-pression mâle en métal ordinaire.
Le fichier a été modélisé dans Fusion360 et imprimé sur un Makerbot Rep2 et un Dremel en utilisant du PLA de graphène conducteur Black Magic 3D.
Les boutons-pression sont des boutons-pression YKK 'Snapet' ouverts (taille 12L) et mesurent 7,5 mm de diamètre. Ils sont souvent utilisés par les praticiens des eTextiles car ce sont les plus petits disponibles. Vous pouvez les acheter dans différentes tailles auprès de différents fournisseurs, mais ils semblent être une conception standardisée. Achetez la taille 12 ici.
Mon objectif est d'explorer des moyens de fabriquer un vêtement qui soit conducteur et extensible et n'utilise de préférence aucune pièce en métal dur. La fabrication de connecteurs compatibles avec les snaps achetables existants facilitera les tests et les itérations.
Ce test a fonctionné étonnamment bien et le fichier vaut la peine d'être imprimé, mais il a certainement besoin de beaucoup plus de réglages. Pour l'instant, il peut être imprimé et testé tel quel, mais il s'agit certainement d'une preuve de concept plutôt que d'un composant logiciel enfichable entièrement fonctionnel qui peut être imprimé de manière fiable, par ex. le PLA a tendance à rétrécir, et les snaps ont une durée de vie limitée.
Si vous imprimez ce fichier s'il vous plaît laissez un commentaire et dites-moi vos découvertes !!
Plus d'images ici:
Ces explorations font partie d'un projet plus vaste appelé Second Skin, une combinaison de prototypage pour les eTextiles. Je téléchargerai tous les fichiers, modèles et documentation au fur et à mesure qu'ils seront terminés. Vous pouvez suivre le projet ici, ou via mon site:
Vous devriez également consulter Rewear par Lara Grant. Elle a travaillé sur un système modulaire pour wearables basé sur une maquette de boutons-pression imprimés en 3D sur du tissu. Elle se concentre également sur la durabilité de ces techniques, ce que je considère également comme faisant partie intégrante de leur développement futur. Nous intégrerons bientôt nos expériences dans un site Web dédié aux connecteurs etextiles, alors assurez-vous de consulter également le site Web de Lara et Instructables !
Étape 1: Fichiers Fusion360
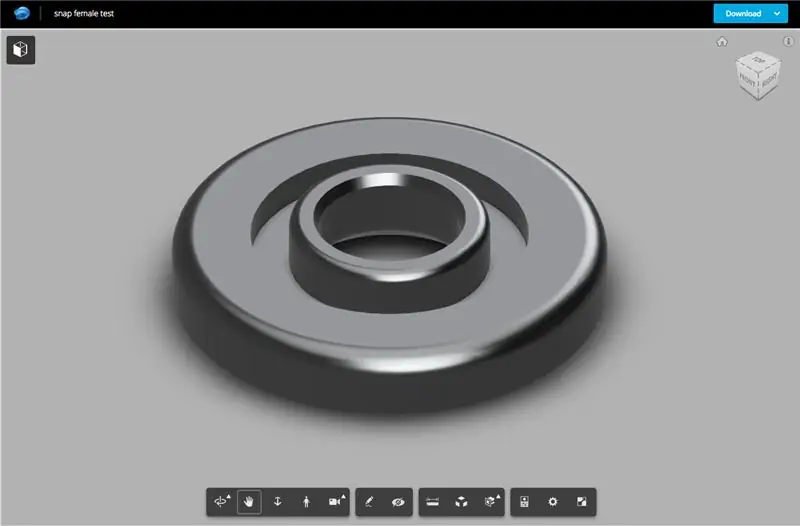
Le fichier a été modélisé assez rapidement à l'aide de Fusion360.
J'ai pris autant de mesures que possible à partir d'un composant logiciel enfichable existant et j'ai fait une conception approximative. Parce que le snap est si petit, certaines des proportions intérieures ont été faites à l'aide de conjectures et nécessiteront donc plus de jeu.
Lien pour télécharger la version actuelle ici:
Le fichier joint à ce Instructable était ma première tentative. Cela a plutôt bien fonctionné. Le fichier lié (ci-dessus) a été modifié, rendant la base de l'accrochage plus solide. l'idée étant que cela l'aiderait à mieux coller au tissu. Bien que cela ait quelque peu aidé, les deux fichiers valent toujours la peine d'être testés si vous souhaitez en imprimer une version. J'ai eu du succès et des échecs avec les deux.
Je soulignerai également que je suis un novice total en Fusion et que j'ai eu l'aide d'un ninja pour peaufiner le fichier de JON-A-TRON. Vous devriez absolument jeter un œil à ses cours d'impression 3D !
Si vous souhaitez utiliser des snaps plus grands (tels que 15 mm qui sont plus courants), je m'attendrais à ce que ce fichier puisse être redimensionné et imprimé aux dimensions correctes et s'accrochera également à des versions plus grandes de cette conception de snap. Je n'ai pas encore essayé cela car j'essaie de tout faire aussi petit que possible.
Ces snapets en métal sont étonnants, mais souvent les matrices sont difficiles à trouver. J'utilise des pinces Prym vario pour appliquer les boutons-pression à la main et il est difficile de trouver la matrice de serrage adaptée. J'ai donc créé un fichier de fusion imprimable pour les Snapets 12L;) Encore une fois, ce n'est pas parfait car les impressions 3D ont tendance à rétrécir et à se déformer et finalement à se casser. Mais je viens d'en imprimer de nouveaux quand cela arrive ! Des fichiers sont joints pour l'intérieur (partie connecteur) et l'extérieur (fixation de l'anneau) de la matrice. L'un est une fraction plus grand que l'autre. Si vous les utilisez à l'envers, le snap restera dans le dé.
Étape 2: Test d'impression et configuration
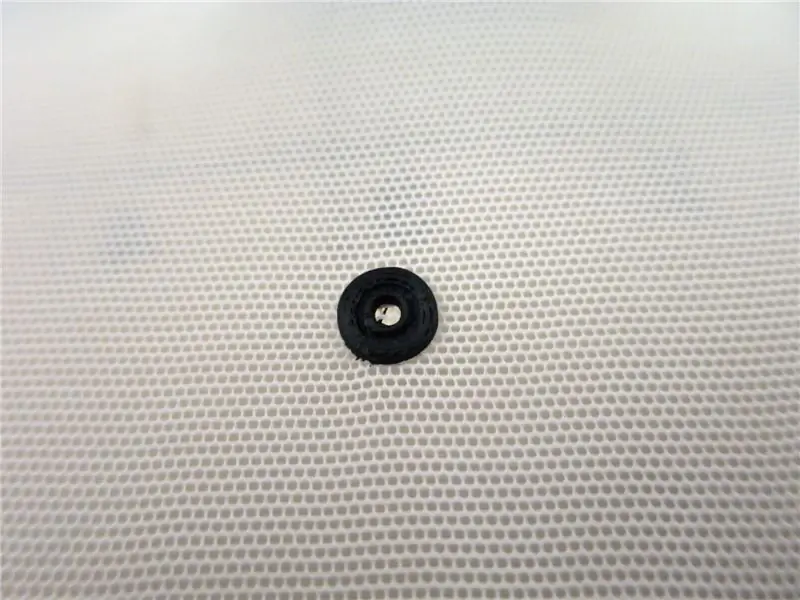
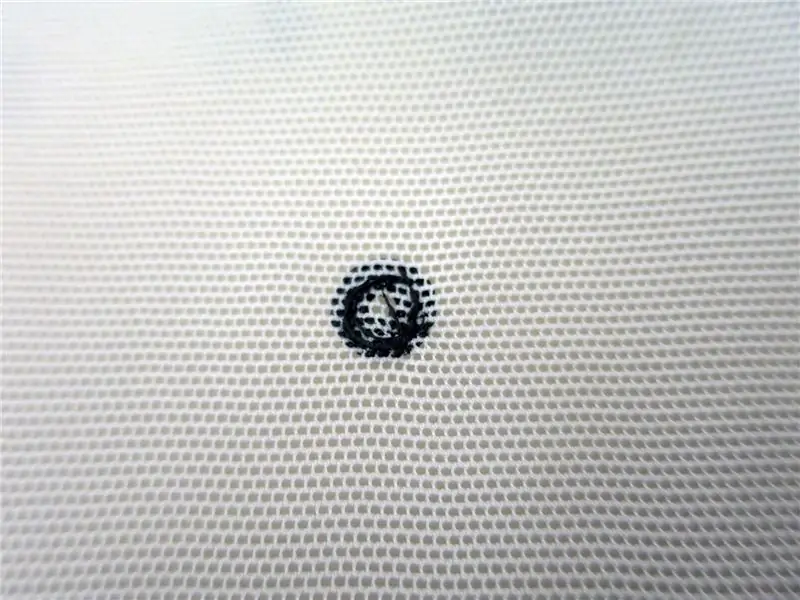
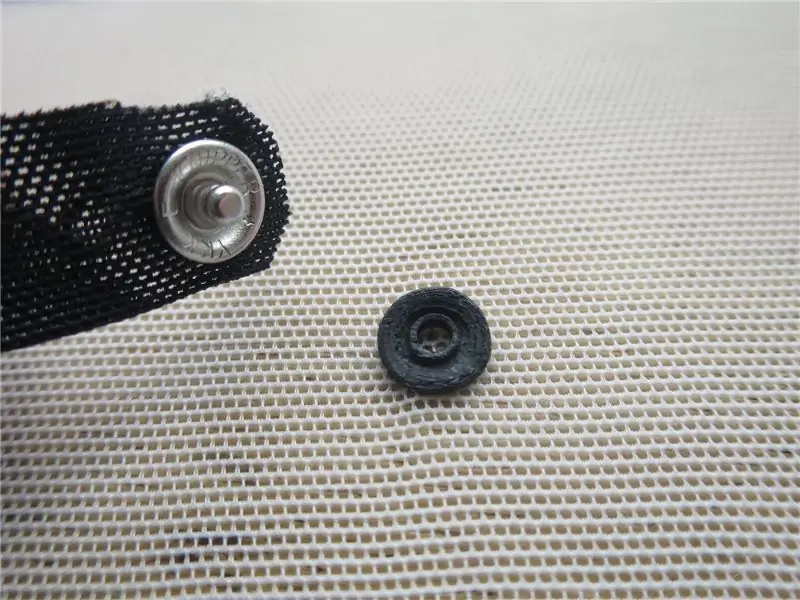
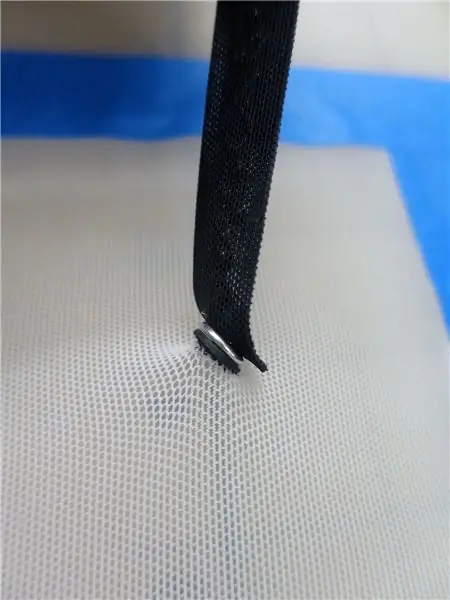
Ce premier cliché a été imprimé par Lara Grant. Elle travaille sur un projet similaire en créant un tissu instantané et a un excellent Instructable sur l'impression 3D sur le tissu. Vous devriez également consulter ses cours de wearables
Il s'agit d'un filament de graphène Black Magic 3D et a été imprimé sur une Makerbot Rep 2 avec la température d'impression et l'extrudeuse réglées sur 220°
Nous avons tous les deux testé une technique selon laquelle vous imprimez une couche de base de filament, mettez la machine en pause pour insérer le tissu, puis continuez l'impression. Cela signifie que le filament va fondre autour du tissu et créer un joint. Vous pouvez le voir dans la deuxième image; il y a du filament sur le dessous du tissu. Cette couche a d'abord été imprimée sur le lit, puis l'imprimante a été mise en pause et le tissu a été inséré. L'imprimante a ensuite été interrompue et l'impression s'est poursuivie.
Cela a fonctionné à merveille ! Première tentative en utilisant le fichier que j'avais fait 10 minutes plus tôt.. Et il s'est même cassé très bien!
Ce cliché que vous voyez ici a été imprimé sur powernet. C'est un matériau que j'utilise beaucoup et que j'utilise pour le projet connexe Second Skin qui utilise des circuits extensibles. Il est extensible dans les 4 sens et utilisé pour la lingerie et les vêtements de danse. Il fonctionne bien car il s'agit d'un maillage synthétique fin. Il est généralement fabriqué à partir de polyamide afin que le filament fonde la surface et y adhère bien. Le filament peut également fondre dans et autour de la surface du maillage micro-fin lui-même.
Powernet a une bonne résistance à la traction et s'il est tendu avec du ruban adhésif lorsque vous le posez sur le lit, il ne sera pas accroché par l'extrudeuse.
Étape 3: Impression 3D sur une trace de tissu conducteur
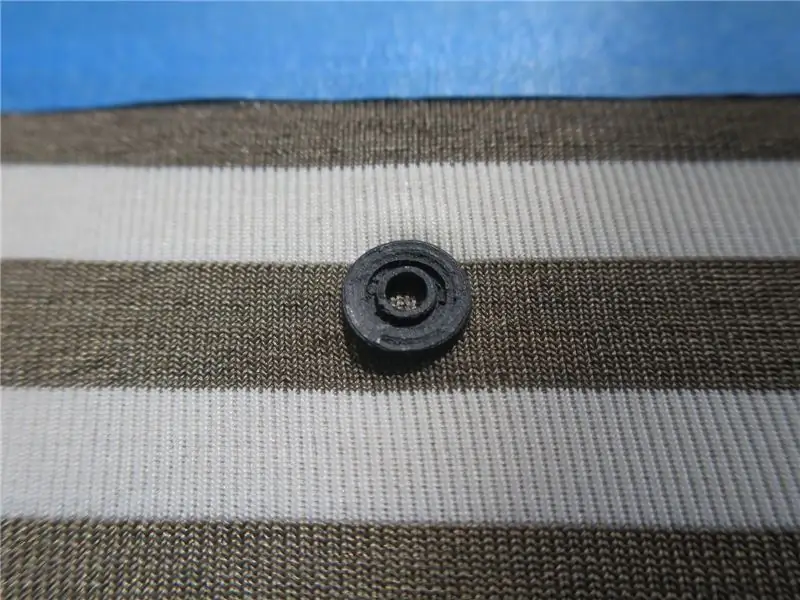
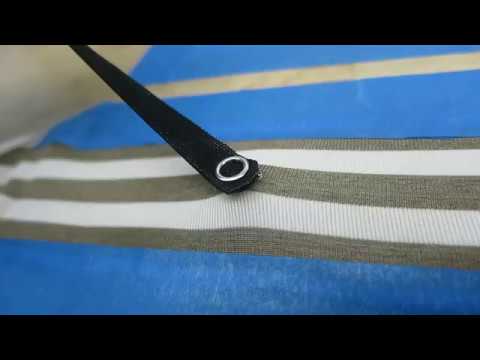
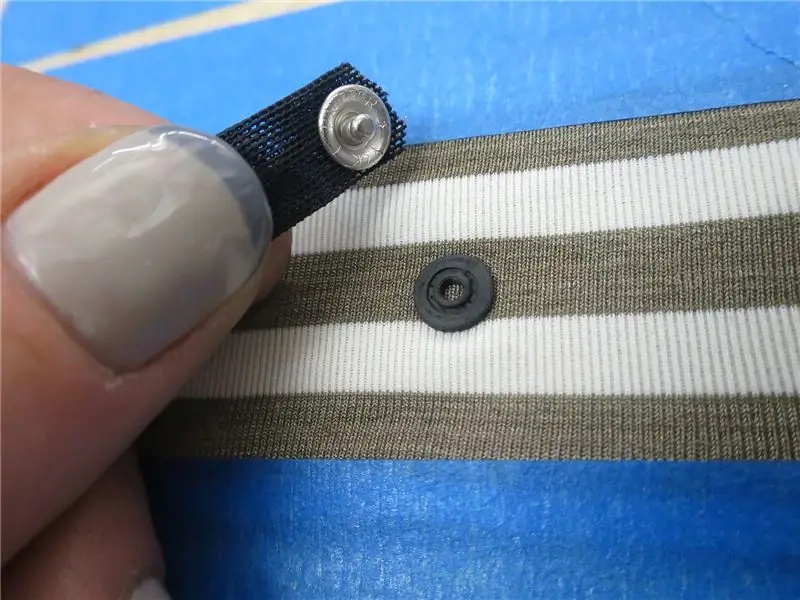
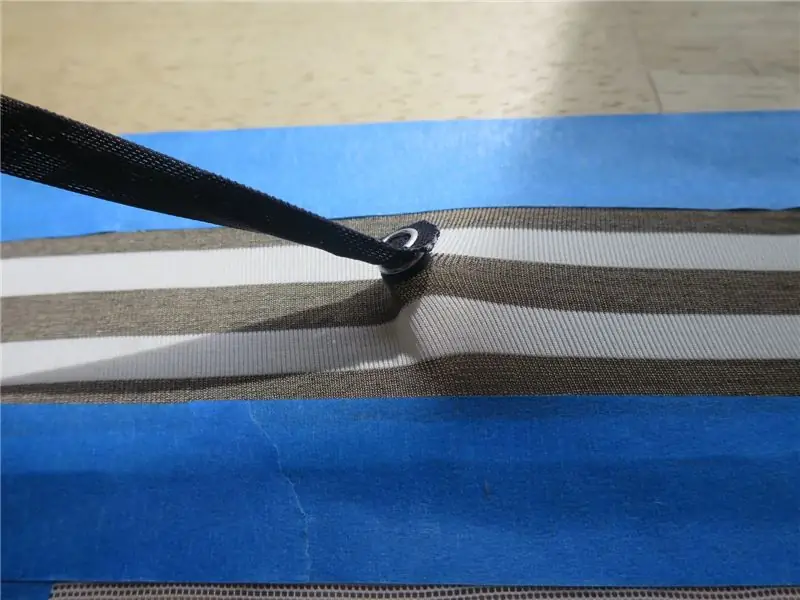
Ce tissu brillant est un jersey extensible tricoté avec des traces conductrices. Je crois que c'est la sorcellerie de Hannah Perner-Wilson et Mika Satomi de Kobakant et a été fait sur mesure. On m'en a donné au camp d'été eTextiles et nous avons décidé que ce serait une bonne chose pour tester la connexion électrique entre le tissu et l'imprimé.
C'est un tissu en jersey, et il semble que les fibres aient été enduites avant d'être tissées, plutôt que le revêtement conducteur étant imprimé après la fabrication. Il est trop épais pour imprimer à travers la surface (comme dans le test précédent) car le filament ne se connecterait pas de la même manière qu'il le fait à travers les trous du réseau électrique.
Nous avons configuré la Makerbot pour qu'elle imprime directement sur le tissu. ce que vous voyez ci-dessus est le premier test d'impression sur ce matériau.
De nombreuses personnes différentes ont testé l'impression 3D sur du tissu, et cela semble différer selon la nature de l'impression, les matériaux et les machines utilisées. La plupart des succès semblent impliquer des mailles car le tissage est lâche et le filament peut couler à travers le tissu pour créer une liaison.
Certaines personnes abaissent la buse de l'imprimante. Cela écrase l'extrudeuse dans le tissu et force le filament dans les fibres, mais peut entraîner le matériau. Une autre option consiste à élever le point de départ de l'extrudeuse pour démarrer l'impression, ce qui signifie que vous découpez l'impression de manière à ce qu'elle commence juste au-dessus de l'épaisseur du tissu. J'imagine que cela fonctionnerait bien si votre tissu était épais. Comme les nôtres sont assez fins et plats, nous avons imprimé directement sur le matériau avec les paramètres par défaut, en éteignant simplement les radeaux et tout support.
Cela a fonctionné à merveille ! Cela peut être dû à divers facteurs:- la surface de ce tissu particulier était idéale pour que l'impression adhère- l'extrudeuse se trouvait juste à la température parfaite à ce moment-là (ce filament peut être très incohérent)- les dieux de l'impression 3D étaient de bonne humeur et nous avons eu beaucoup de chance
De toute évidence, cela nécessite plus de tests.
Étape 4: Tester la conductivité

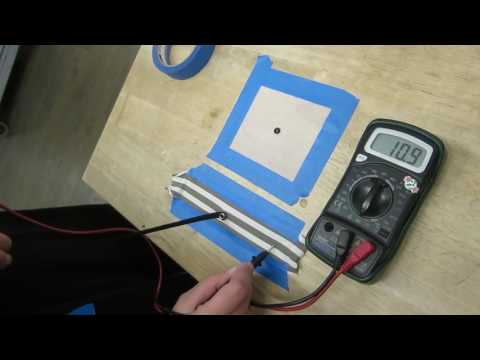
Ce test a utilisé un connecteur eTextile extensible fabriqué avec du fil conducteur Karl Grimm. À l'intérieur du connecteur noir se trouve un zigzag de fil conducteur isolé par des couches de tissu de chaque côté. Chaque extrémité a un snapet mâle. Tous ces matériaux ont une résistance assez faible.
La résistance à travers le connecteur de 30 cm, à travers le bouton-pression et à travers environ 8 cm de tissu conducteur semble être d'environ 10 ohms. C'était surprenant et semblait rester assez stable même lorsqu'il était étiré. Je ne suis pas sûr que ce soit une lecture précise et reproductible !
Étape 5: Impression sur différentes surfaces
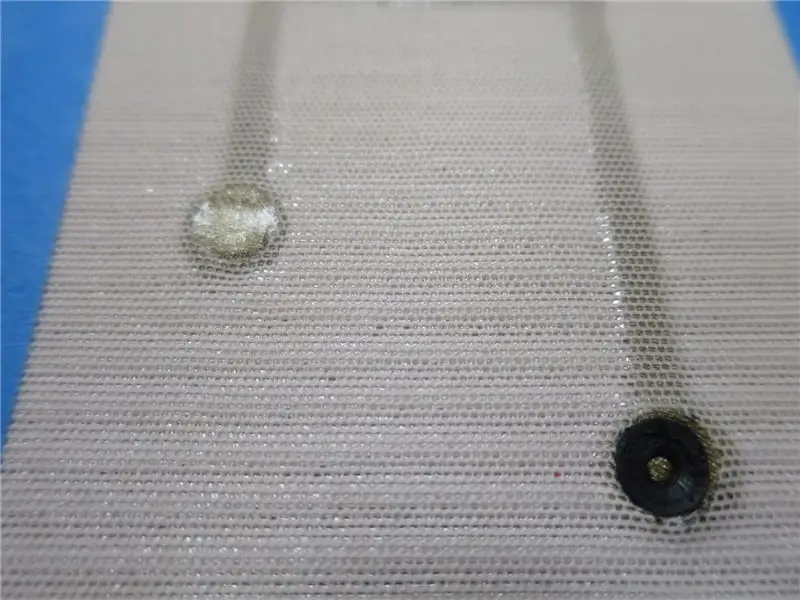
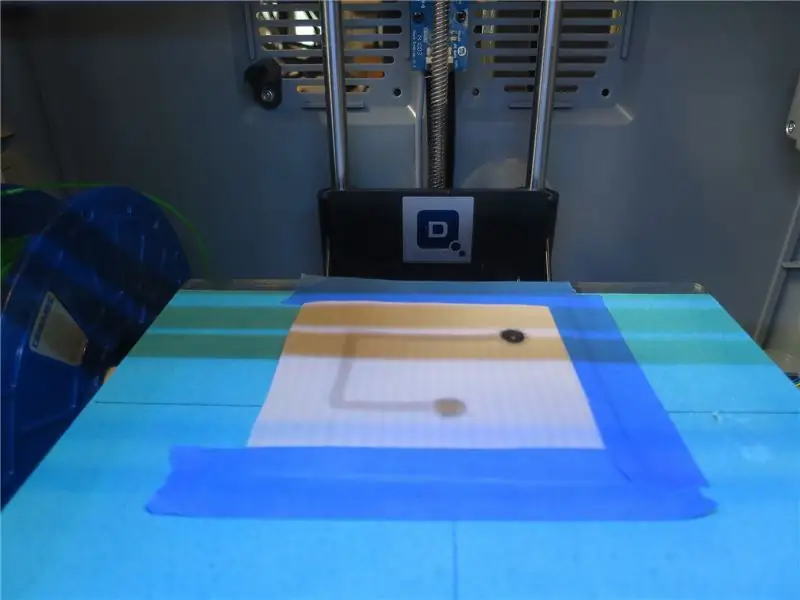
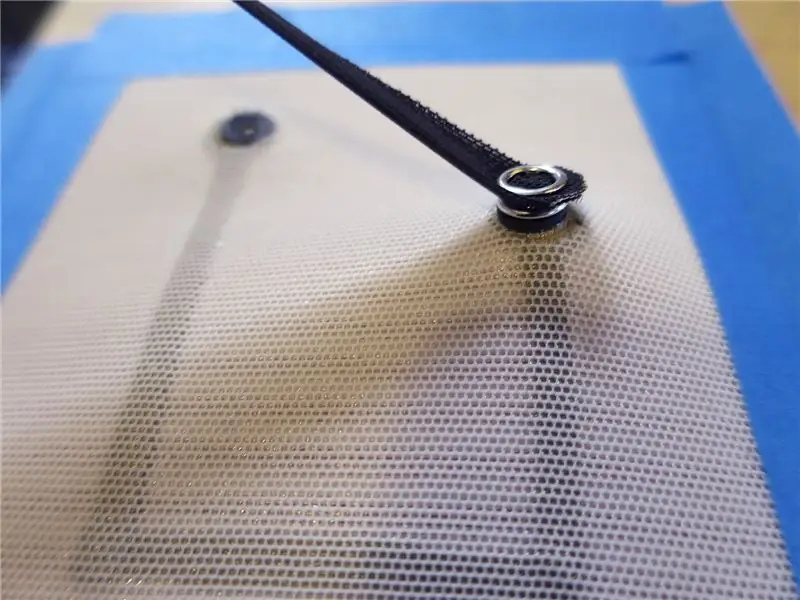
Ensuite, j'ai décidé d'essayer d'imprimer sur une Dremel. C'est principalement parce que le Makerbot avait une crise de nerfs, mais la variété est toujours bonne. Encore une fois, la température d'impression et l'extrudeuse ont été réglées à 220°
J'ai travaillé sur des traces conductrices collées, isolées et extensibles pour les eTextiles. Ces tissus utilisent des couches textiles collées avec la fusion Bemis SewFree, un film thermocollant ultra fin. Cela signifie que les échantillons de tissu étaient plus épais que les tests précédents. Les pistes conductrices sont isolées à l'intérieur du tissu powernet et n'ont que les extrémités exposées sous forme de pastilles rondes.
Lorsque j'ai imprimé le fichier pour la première fois avec les paramètres par défaut, il s'est écrasé sur la surface du tissu et a déformé l'impression. Vous pouvez voir le résultat dans la première image. Le snap n'a pas fonctionné cette fois.
Jonathon m'a montré comment découper le fichier dans Cura et augmenter la position de départ de l'extrudeuse de 0,4 mm.
Pour le test suivant, j'ai également ajouté une couche de collage SewFree à la surface sur laquelle j'allais imprimer. C'était pour voir si cela faisait une différence sur la façon dont l'impression adhère.
Cela a très bien fonctionné au début, comme vous pouvez le voir sur la dernière image. Malheureusement, après quelques boutons-pression, le bouton-pression s'est détaché du tissu et est tombé.
Étape 6: Test d'impression multiple
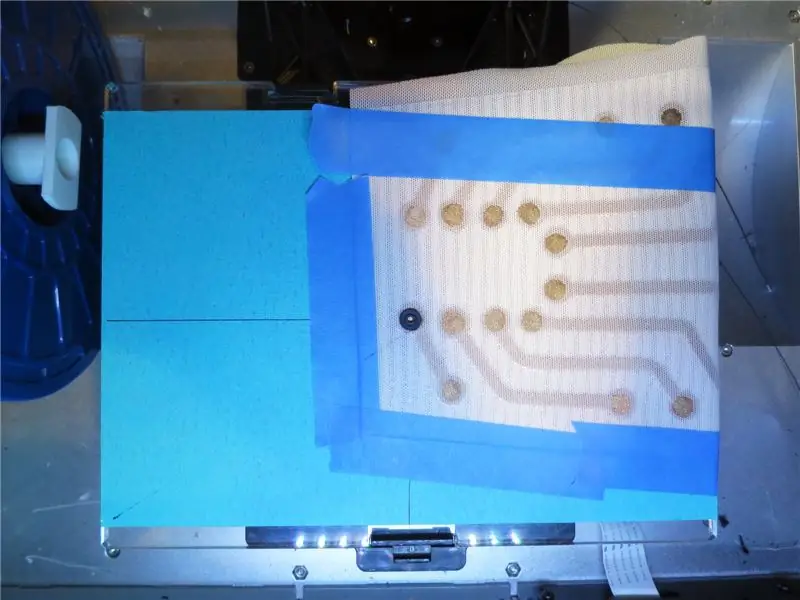
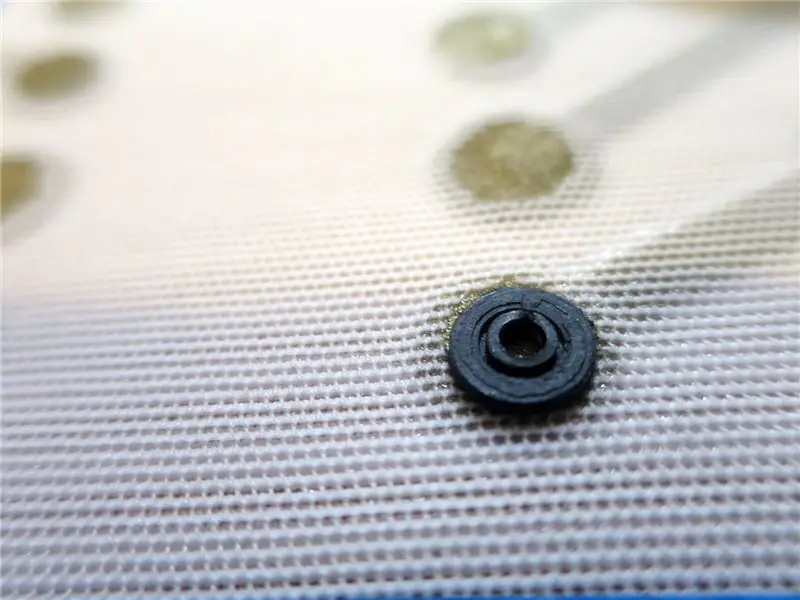
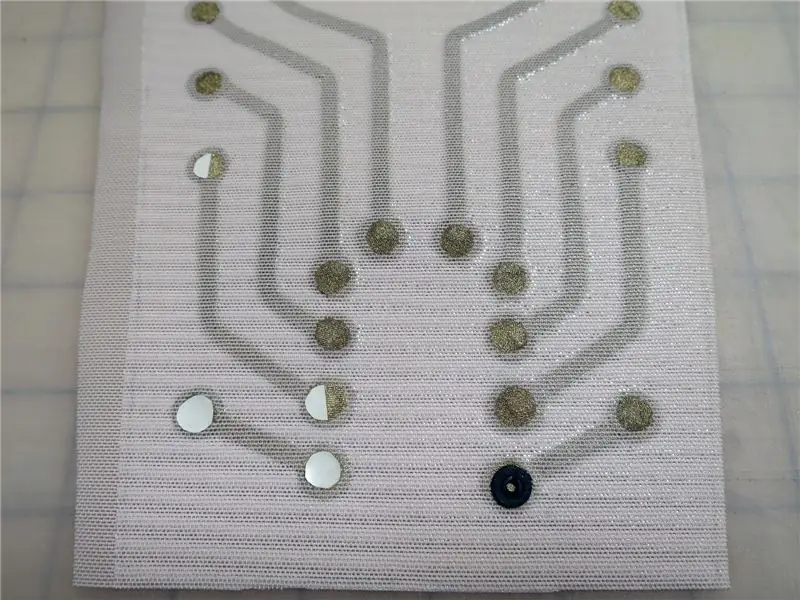
J'ai ensuite essayé d'imprimer plusieurs clichés pour voir comment le courant passait à travers deux clichés à chaque extrémité d'une trace conductrice. Comme je n'avais qu'un seul snap fonctionnel sur le test précédent, je n'ai pas pu vérifier. Peut-être que l'impression que Lara avait faite auparavant était un coup de chance. J'ai fait un panneau rapide pour essayer plusieurs impressions.
Comme il s'agissait d'un test, j'ai décidé d'imprimer chaque pression individuellement, plutôt que d'essayer d'imprimer plusieurs pressions sur un seul morceau de tissu.
Trois raisons: 1. Je ne voulais pas investir de temps dans la création d'un fichier de mise en page car le circuit de tissu sur lequel j'imprimais était fait de manière imprécise2. Les impressions échouent souvent 3. Je ne voulais pas que des filaments indésirables traînent sur le tissu
J'ai aligné chaque bouton-pression jusqu'à un point centralisé et les ai imprimés un par un. Chacun s'en sort parfaitement.
J'ai ajouté la fusion SewFree à certains des plots conducteurs. Vous pouvez le voir dans les images sous forme de cercles blancs et de demi-cercles. C'est le support papier qui se décolle. Je l'ai laissé allumé pour qu'il soit plus facile à voir sur les images. J'ai pensé qu'il serait bon de voir comment la fusion affectait l'adhérence sur la même impression. Ils se sont tous avérés assez similaires. La plupart sont restés bloqués et quelques-uns sont tombés. Je ne sais pas pourquoi, mais je suppose que cela est dû à des différences infimes dans l'épaisseur de la couche de tissu. Ils ont tous été imprimés en succession rapide sur la même imprimante avec les mêmes paramètres.
la résistance à travers une piste conductrice de 15 cm à travers deux boutons-pression résistifs était d'environ 50 ohms. Cela a été fait immédiatement après l'impression et semblait super conducteur, nous avions donc besoin de plus de tests.
Étape 7: Lecture de la résistance
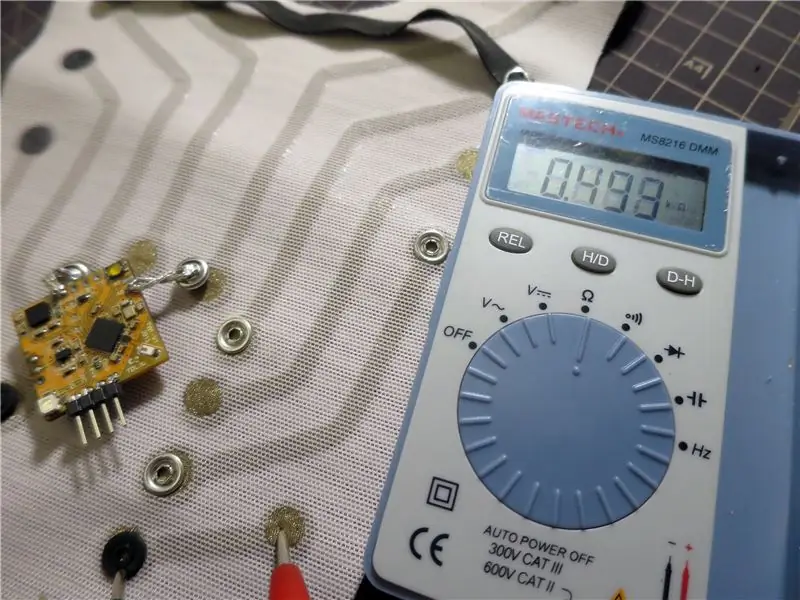
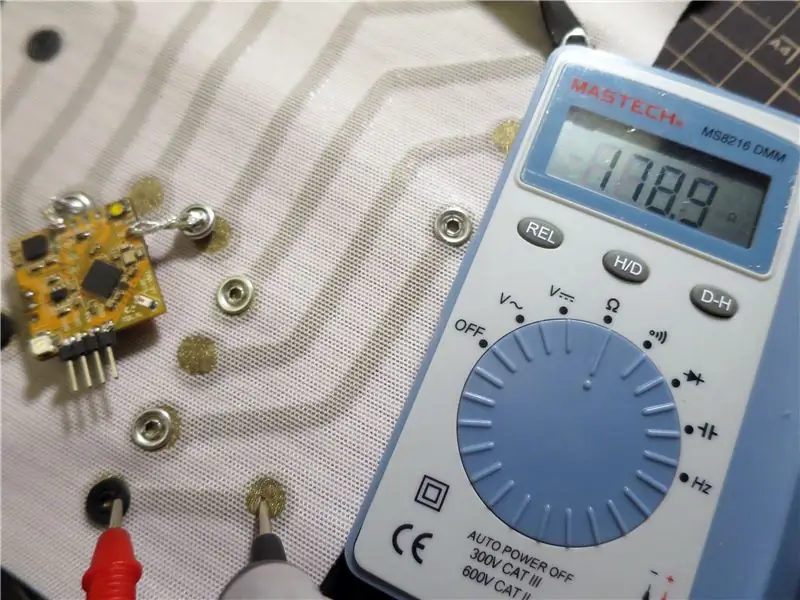
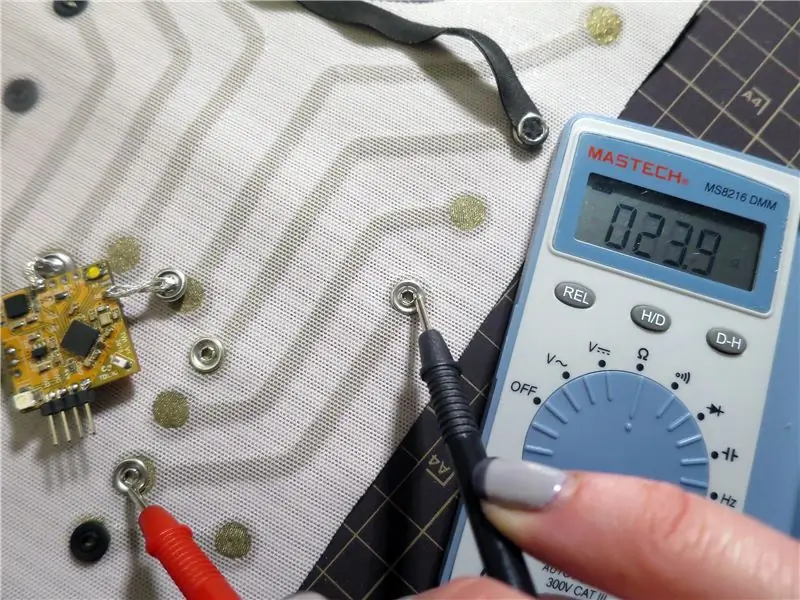
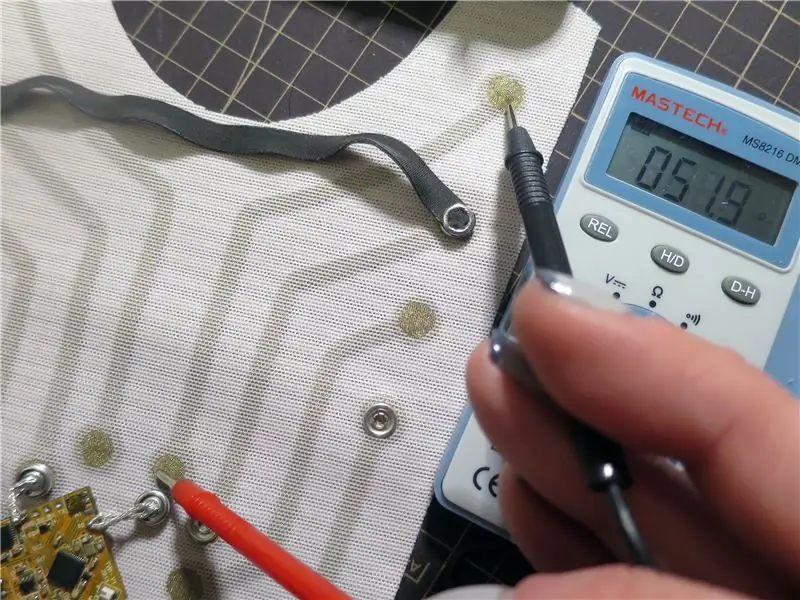
Les lectures que j'ai prises sur les clichés semblaient très différentes. Cela a également changé au fil du temps.
Étape 8: rattacher les boutons-pression avec de l'époxyde conducteur
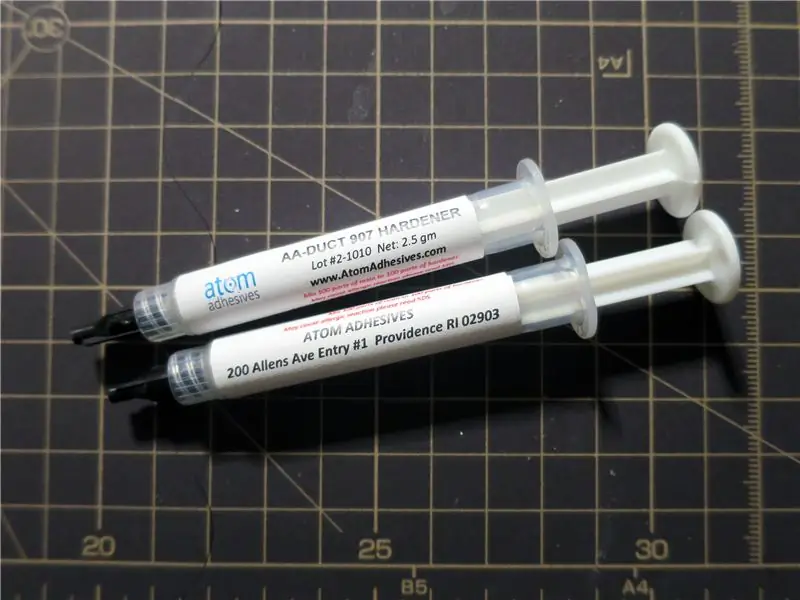
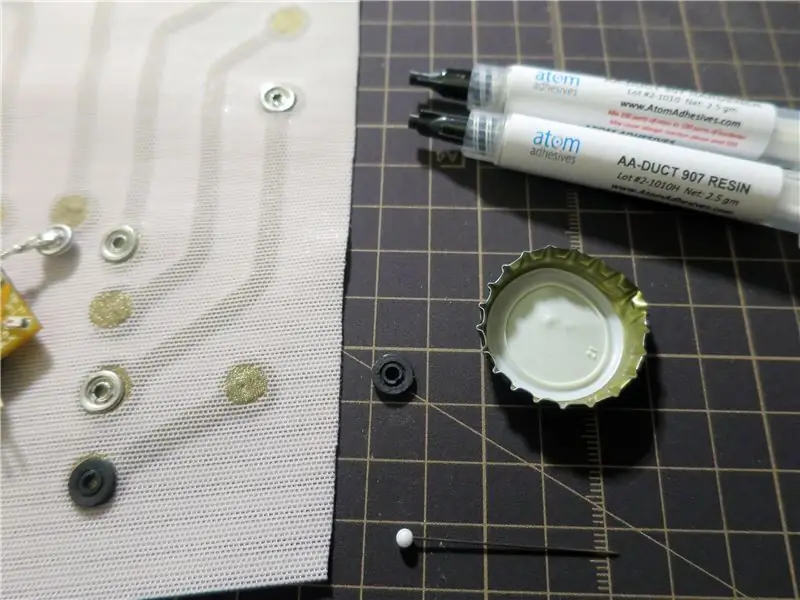
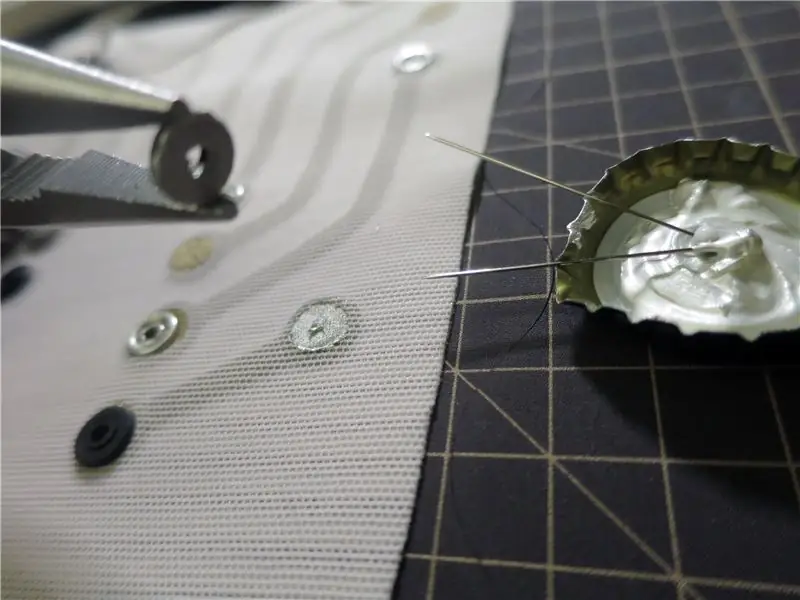
Certains boutons-pression sont tombés après une petite utilisation. Ils n'adhèrent pas aussi bien au matériau collé qu'avec les tests précédents.
À ce stade, cela vaut la peine d'étudier une autre option: les boutons-pression peuvent-ils être imprimés puis collés au tissu par la suite.
Il est peut-être vrai que les boutons-pression peuvent être imprimés sur certains tissus mais doivent être collés sur d'autres. Cela pourrait encore être une option viable.
J'ai utilisé de l'époxy conducteur et recollé deux des boutons-pression en place pour voir si la colle peut créer une liaison et conduire de manière fiable.
Malheureusement, cela n'a pas du tout bien adhéré au tissu. L'époxy est assez crayeux et n'aime pas la matière synthétique dense. Bien que la colle ait permis à une petite quantité de courant de circuler, les boutons-pression sont tombés après un seul coup.
Étape 9: Conclusion et prochaines étapes
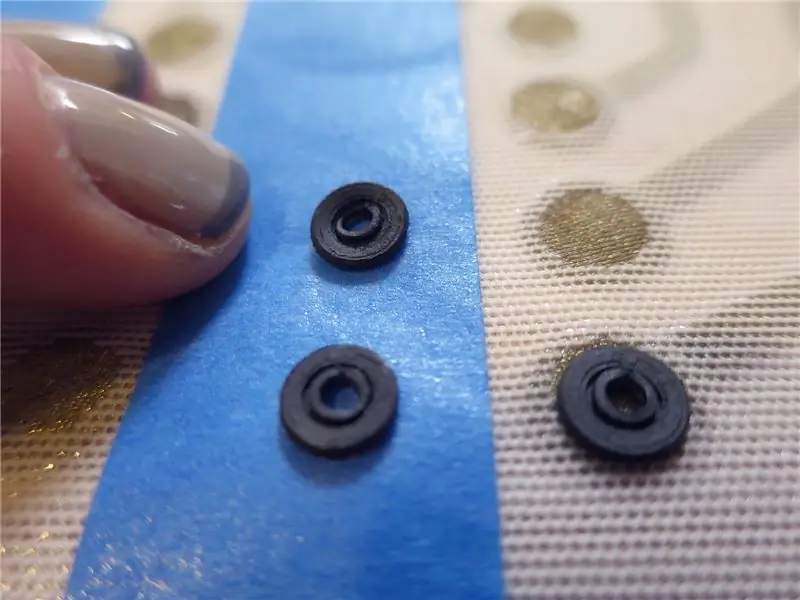
Ce design instantané a très bien fonctionné pour un premier test. Il s'enclenche en toute sécurité, peut conduire une petite quantité de courant et constitue une bonne preuve de concept.
Malheureusement, ils n'ont pas donné une conductivité constante. Certains étaient ok et d'autres ne fonctionnaient pas du tout. Il semble que l'utilisation de tissus tissés serrés soit un problème, donc cela ne fonctionne pas si bien pour mes tissus contrecollés. Utiliser un tissage plus ouvert comme le maillot, et surtout le powernet semble la meilleure option. Le problème avec cela est que moins un tissu est dense, plus la conductivité est mauvaise pour les textiles.
Il y a pas mal de problèmes pratiques avec le PLA. Il a tendance à se déformer et à rétrécir. Certains des boutons-pression ont fonctionné immédiatement, certains ont eu besoin de quelques fermetures forcées initiales avant de se conformer, apparemment pour étirer un peu l'impression. Certains semblaient trop petits pour se casser du tout. Tout était un peu incohérent.
J'ai également lu que la conductivité de ces matériaux peut changer avec le temps. Dans ce cas, je dirais que la pression du claquement lui-même peut affecter cela. Le passage du courant à travers le snap peut également augmenter de façon permanente la résistance. Cela impliquera certainement plus de tests.
il y a un assez bon aperçu des filaments Black Magic 3D ici
Je veux utiliser cette idée instantanée dans une conception de gant. Je veux trouver un moyen de faire des connecteurs détachables pour les capteurs d'étirement. L'idée serait que ce fichier snap puisse être intégré directement dans un capteur imprimé en 3D pour le connecter à un circuit.
En revue, j'ai trouvé ce processus intéressant et instructif. Il n'est pas assez stable pour produire des résultats mesurables cohérents et j'aimerais explorer davantage dans des expériences plus contrôlées.
Si vous essayez l'un de ces tirages, s'il vous plaît laissez un commentaire !
Conseillé:
Impression de chèques sans logiciel spécial ni imprimante avec MS Excel (impression de chèques bancaires) : 6 étapes
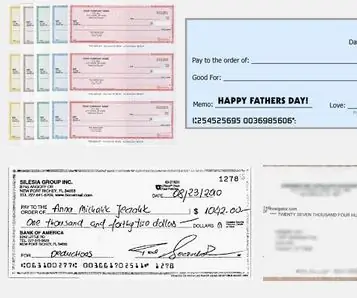
Impression de chèques sans logiciel spécial ni imprimante avec MS Excel (impression de chèques bancaires) : il s'agit d'un simple classeur Excel, qui sera très utile à toute entreprise pour rédiger de nombreux chèques bancaires. vous n'avez besoin que d'un ordinateur avec MS Excel et d'une imprimante normale. Oui, maintenant vous pouvez
Créez votre propre relais à semi-conducteurs : 4 étapes (avec photos)
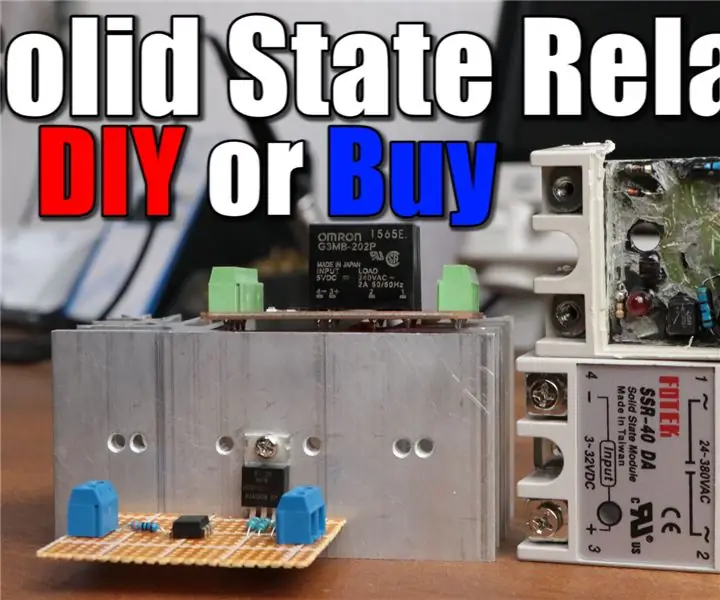
Créez votre propre relais à semi-conducteurs : dans ce projet, nous examinerons les relais à semi-conducteurs, découvrirons comment ils fonctionnent et quand les utiliser et à la fin, nous créerons notre propre relais à semi-conducteurs DIY. Commençons
Servo-testeur 16 canaux avec Arduino et impression 3D : 3 étapes (avec photos)
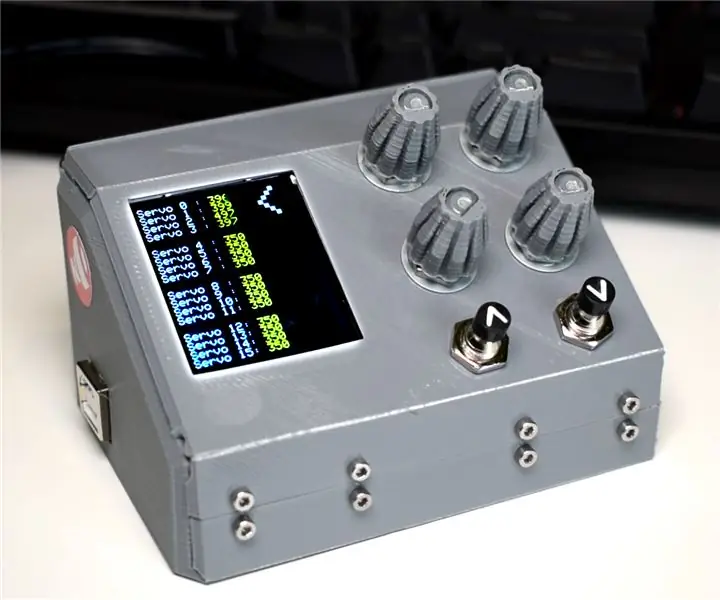
Testeur de servomoteurs à 16 canaux avec Arduino et impression 3D : à peu près tous les projets que j'ai réalisés récemment m'ont obligé à tester certains servos et à expérimenter leurs positions avant de les intégrer à l'assemblage. Je fais généralement un testeur de servo rapide sur une planche à pain et j'utilise le moniteur série dans l'ardui
Créez un diaporama dynamique de vos clichés avec Photo Story 3: 16 étapes
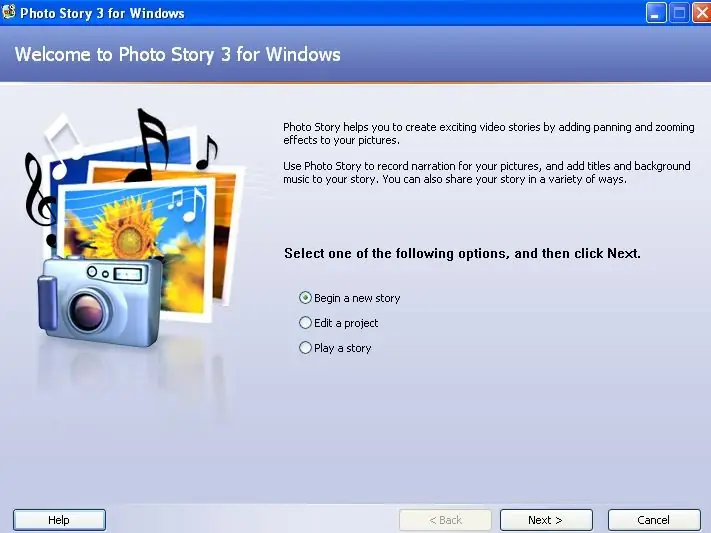
Créez un diaporama dynamique de vos clichés avec Photo Story 3: C'est une façon de créer un diaporama de photos nice.wmv avec des effets de panoramique et de zoom en utilisant principalement un logiciel gratuit. Je m'attends à ce qu'il existe des moyens plus faciles, mais je n'ai pas pu trouver d'instructable sur le sujet. Ma méthode fait un peu le tour des maisons, mais ça marche
Contrôle PC super facile de 110 Vca à l'aide d'un relais à semi-conducteurs Crydom : 3 étapes (avec photos)
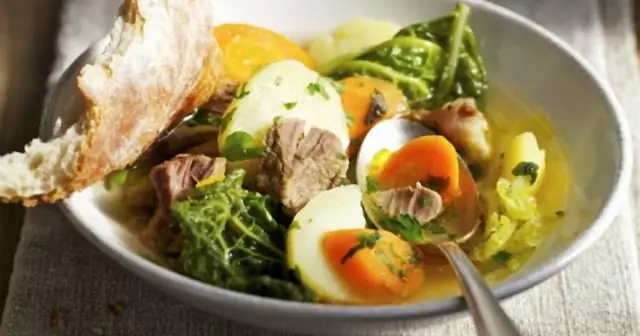
Contrôle PC super facile de 110 Vca à l'aide d'un relais à semi-conducteurs Crydom : je m'apprête à m'essayer à la soudure sur plaque chauffante. Par conséquent, j'avais besoin d'un moyen de contrôler 110Vac depuis mon PC. Cette instructable montre comment contrôler facilement 110Vac à partir d'un port de sortie série sur un PC. Le port série que j'ai utilisé était de type USB