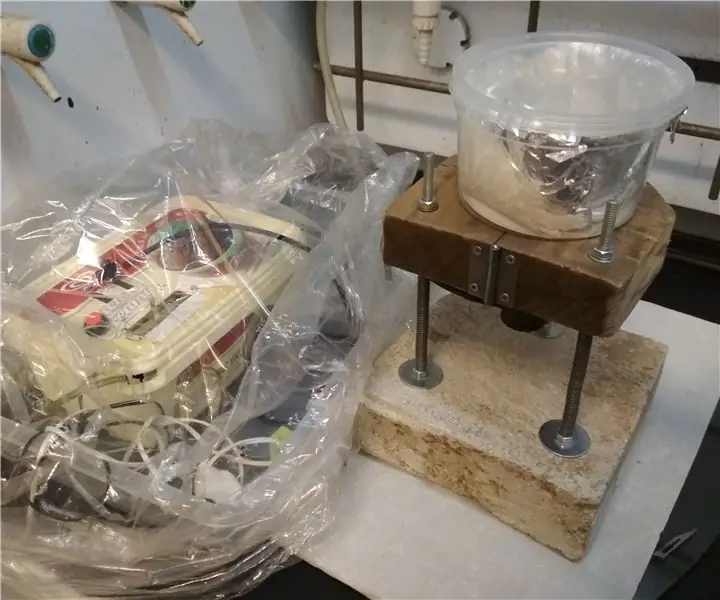
Table des matières:
- Fournitures
- Étape 1: avez-vous un moteur approprié ?
- Étape 2: Test de vitesse
- Étape 3: Échantillon de mandrin
- Étape 4: Construisez le support du moteur - Base et ressorts
- Étape 5: Construisez le support du moteur - Boîtier du moteur
- Étape 6: Construire le support moteur - Chambre
- Étape 7: Construire le circuit de contrôle
- Étape 8: Étalonnage et test
- Étape 9: Remerciements
2025 Auteur: John Day | [email protected]. Dernière modifié: 2025-01-23 14:45
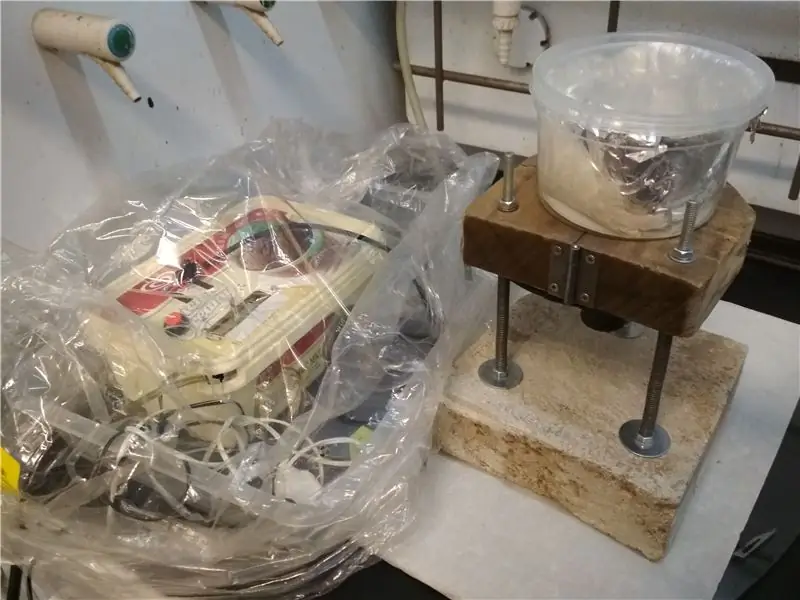
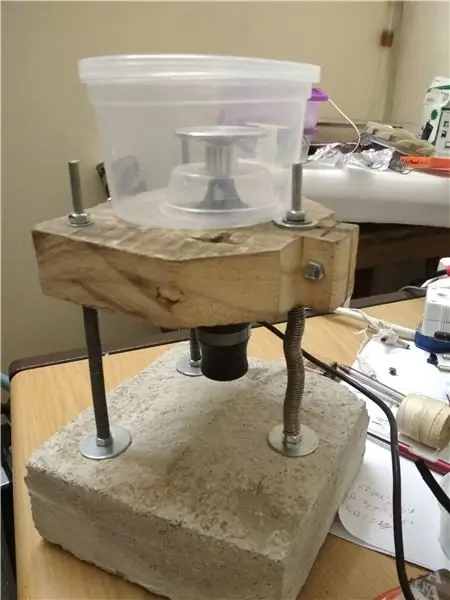
Tous les équipements ne sont pas faits pour durer, je suis étudiant/chercheur étudiant les matériaux en couches minces pour la technologie solaire. Une des pièces d'équipement dont je dépends s'appelle une tournette. Il s'agit d'un outil utilisé pour fabriquer des films minces d'un matériau à partir d'une solution liquide ou d'un précurseur. Ces films minces peuvent être superposés dans des dispositifs tels que des cellules de panneaux solaires ou des LED.
Dans mon université, nous avons eu de nombreux problèmes avec les produits commerciaux plus abordables qui sont disponibles pour l'équivalent de quelques milliers de dollars. Ces centrifugeuses commerciales utilisent un mandrin à vide pour maintenir les échantillons et les problèmes qu'ils ont rencontrés comprenaient des moteurs grippés, des mandrins à vide obstrués, des condensateurs fumants, entre autres, qui affectaient la rétroaction sur laquelle le contrôle de vitesse s'appuyait. Je ne suis pas au courant des problèmes que chaque groupe de recherche a rencontrés avec eux, mais je sais qu'il y en a généralement eu au moins un en cours de réparation ou en attente de réparation à un moment donné.
La conception que je partage est simple, elle utilisait initialement du ruban adhésif double face au lieu d'un mandrin à vide pour contenir les échantillons, elle a ensuite été mise à jour pour une conception plus facile à utiliser (voir l'étape 6). Il fonctionne depuis plus d'un an en utilisation légère. Il n'y a eu aucun problème à part un relais usé (ce n'était pas un nouveau relais une fois installé).
Le projet est principalement composé de pièces trouvées comme un moteur avec un courant nominal de 1 "leer" (500 mA), du béton, du bois de construction et des composants électroniques récupérés.
Fournitures
Je m'attends à ce que toute personne essayant ce projet fasse des variations, il s'agit donc d'une liste non exhaustive de ce qui est nécessaire pour le projet.
Coeur:
Moteur à courant continu capable de pas moins de 4000 tr/min
Mandrin fait pour le moteur choisi (discuté plus tard)
Chambre:
Pot en plastique rond (j'ai utilisé un pot de yaourt)
Plastique épais ou alternative pour tapisser le fond de la baignoire
Essuie-tout
Ruban
Monter:
chute de pin 38x228 mm (typiquement utilisé pour les chevrons en toiture)
charnière de 30 mm de long
Caoutchouc ou mousse dure (montage moteur)
Boulon M6 avec tournevis à tête appropriée
Écrou M6
rondelle 6 mm
Base et suspension:
Base lourde (j'ai utilisé un bloc de béton coupé sur mesure)
Barre filetée M6
9x écrous M6 pour la barre filetée
3x ressorts longs diamètre 8 mm
rondelles 12x 6 mm
Bases des commandes:
Boîte à projet (j'ai utilisé un pot à glace, c'est une bonne excuse pour manger de la glace)
Alimentation 12V (j'en ai utilisé 2 pour que le moteur puisse être sur une source séparée)
1x diodes de redressement pour le moteur
Minuterie à 2 étapes:
2x MOSFET à canal n (comme IRF540)
2x 47 uF capuchon aluminium 35V
2x B500k pot double toboggan
Résistance 200K
Résistance 10K
2x diodes de redressement pour les relais
Contact momentané à bouton-poussoir
Relais SPST (minuterie marche/arrêt)
Relais DPDT (transition temporisateur vitesse 1/vitesse 2)
Circuit PWM:
1x minuterie NE555
1x résistance 1k
2x condensateurs 10nC
1x MOSFET canal n (comme IRF540)
1x dissipateur pour MOSFET
1x rondelle isolante en silicone pour le dissipateur thermique
www.mantech.co.za/ProductInfo.aspx?Item=14…
2x 10k pots (cycle d'utilisation)
1x diodes de redressement pour les relais
Test de vitesse du moteur:
Idéal:
tachymètre optique.
Alternative:
Ruban
Fil fin comme un objet dur (par exemple fil, cure-dent, trombone)
Ordinateur avec "Audacity" installé
Étape 1: avez-vous un moteur approprié ?
La plupart des centrifugeuses doivent fonctionner dans une plage de vitesse de 500 à 6 000 tr/min. Mon travail a besoin de 2000 et 4000 tr/min comme vitesses les plus importées, donc je pourrais me contenter d'un moteur à courant continu que j'avais qui traînait et qui fonctionnait dans la plage de 1100 à 4500 tr/min, mon moteur peut fonctionner plus lentement bien que les vitesses plus lentes soient moins fiables en raison de la résistance dans le moteur.
Trouvez un moteur et une alimentation adaptés si vous avez un moteur 12 V. Faites correspondre la tension requise par votre moteur et le courant de l'alimentation devrait idéalement être supérieur de 20% à celui requis par le moteur. Si vous avez un moteur 24 V, vous aurez besoin d'un convertisseur abaisseur ou d'une alimentation séparée pour fournir 12 V pour l'électronique.
Ensuite, nous voudrons tester les vitesses minimales et maximales que votre moteur peut supporter. Si vous avez une alimentation avec une tension sélectionnable/réglable, utilisez-la, sinon construisez le circuit PWM indiqué plus loin dans le circuit de contrôle (ou le circuit de contrôle complet).
Étape 2: Test de vitesse
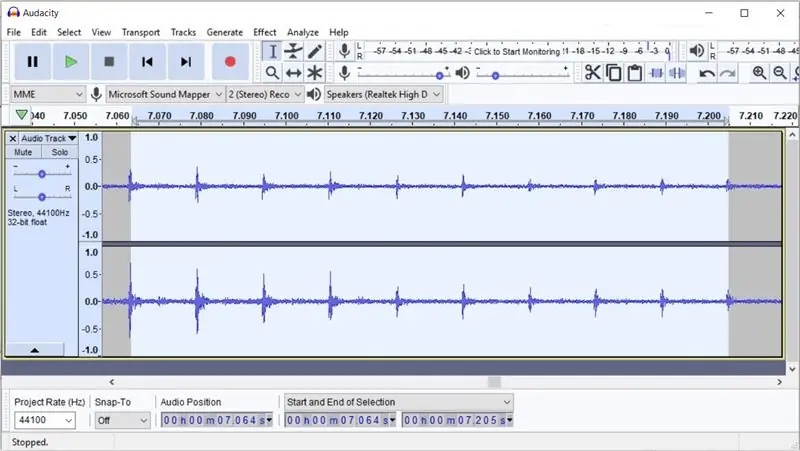
Un tachymètre optique est un excellent outil pour tester la vitesse d'un moteur si vous pouvez mettre la main sur un, je présente ici une méthode alternative.
Partie A
1. Préparez un ordinateur pour enregistrer de l'audio avec "Audacity" qui est un éditeur audio gratuit.
2. Enroulez du ruban adhésif autour de l'arbre de votre moteur (du ruban électrique ou du ruban adhésif fonctionnera bien).
3. Réglez le moteur à la vitesse la plus basse qu'il puisse gérer.
4. Lancez l'enregistrement audio.
5. Conformément à la vidéo de cette section, mettez une épingle en métal, un clou ou un trombone légèrement en contact avec le ruban pendant quelques secondes.
6. Arrêtez l'enregistrement.
7. Répétez l'opération pour la vitesse maximale.
8. Regardez l'audio et calculez le RPM.
Lorsque nous contactons la bande avec la broche métallique, nous voulons qu'elle se touche à peine. Plus vous rapprochez la goupille de l'arbre du moteur, plus le ruban doit se plier pour le passer et plus nous ralentissons ou prenons de l'élan du moteur. Si le contact entre la bande et la broche métallique est trop clair, il se peut que nous n'obtenions pas assez de volume dans l'enregistrement pour nous dire quand le contact est établi. Pour calculer les RPM à partir de l'audio dans Audacity (voir image en haut)
Partie B
1. Zoomez sur l'audio jusqu'à ce que vous puissiez voir des pics distincts de l'endroit où la broche entre en contact.
2. Cliquez avec le bouton gauche sur un pic et maintenez-le enfoncé, en déplaçant la souris de manière à ce que la zone sélectionnée couvre au moins 5 pics.
3. Comptez le nombre de pics.
4. Utilisez l'affichage de l'heure « Début et fin de section » au bas de la fenêtre pour obtenir le temps qu'il a fallu pour que ces pics/rotations se produisent.
5. (nombre de pics)/(temps en secondes) = tours par seconde
6. RPM = (tours par seconde)*60
Il est important de vous assurer que votre moteur peut fonctionner aux vitesses dont vous avez besoin avant de construire le boîtier pour ce moteur. Nous répéterons le test de vitesse à la fin pour un étalonnage ultérieur en omettant l'étape 7 de la partie A et en remplaçant l'étape 3 par la vitesse que nous testons.
Étape 3: Échantillon de mandrin
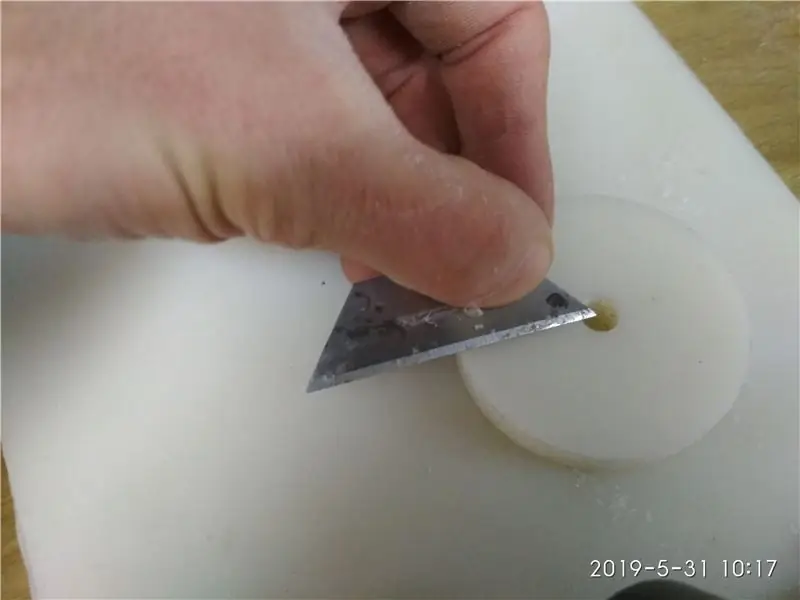
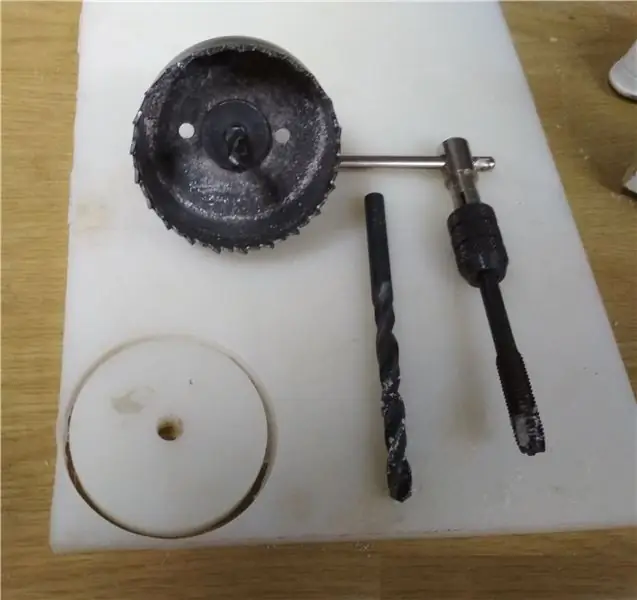
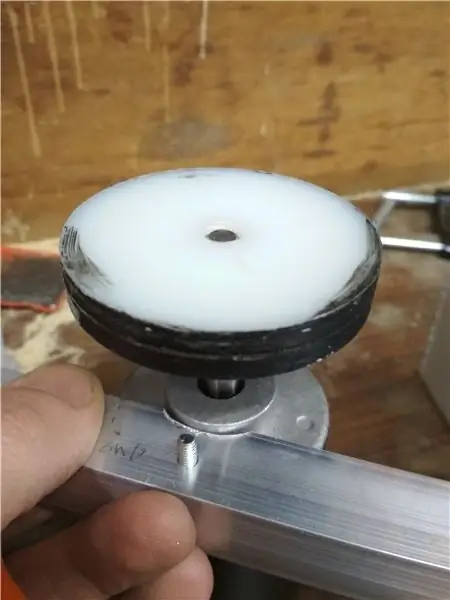
La partie la plus importante de cette construction est le mandrin d'échantillon. Pour le mandrin en aluminium, un de mes amis (Gerry) l'a tourné sur un tour, puis un filetage a été taraudé pour s'adapter à mon moteur spécifique (filetage impérial dans mon cas). Pour un moteur avec un pas de vis sur l'arbre, le montage du mandrin consiste simplement à le visser une fois celui-ci réalisé (lien). Je trouve cela plus facile bien qu'il y ait plus de chances d'avoir une précession lorsque le mandrin est monté. Si vous utilisez un moteur avec un arbre lisse, vous n'aurez aucun problème de "jeu" dans le filetage. Le défi ici est que l'arbre devra soit être collé ou encore mieux avoir une vis sans tête pour le serrer sur l'arbre.
Si vous avez accès à un tour à métaux et à une personne qualifiée pour l'utiliser, il est préférable de tourner le mandrin. Si votre moteur a un filetage, tapotez un filetage au centre du mandrin. Pour un moteur avec un arbre lisse, vous devrez utiliser quelque chose comme une vis sans tête pour appuyer contre le côté de l'arbre et le maintenir en place.
Une alternative montrée dans les images ci-dessus est de prendre une scie cloche et de couper un disque à l'aide d'une perceuse à colonne. Ensuite, utilisez un robinet pour enfoncer un fil dans le centre. Si vous avez un matériau mou vous pouvez enlever les bavures à l'aide d'un couteau, pour un matériau plus dur une lime conviendrait. Le haut du trou peut ensuite être rempli d'époxy ou une découpe d'une feuille de métal peut être époxydée à la surface.
SÉCURITÉ: L'utilisation de colle/époxy sur le mandrin n'est pas conseillée car si la colle échoue… où va le mandrin. Le mandrin tournera à grande vitesse pendant l'utilisation, faisant du mandrin une fine plaque de métal le transformera potentiellement en un disque de coupe. Je recommande d'utiliser un matériau d'au moins 5 mm d'épaisseur.
Étape 4: Construisez le support du moteur - Base et ressorts
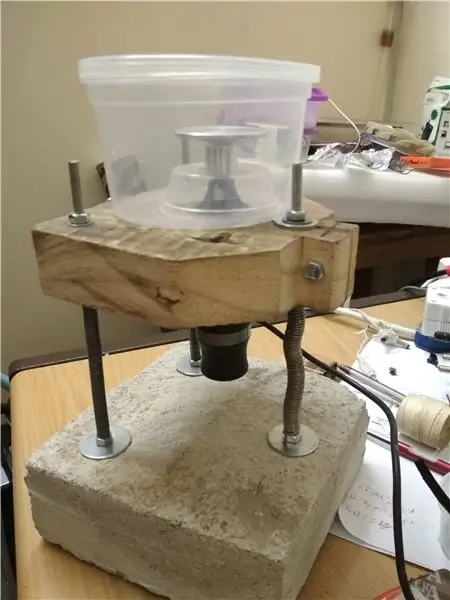
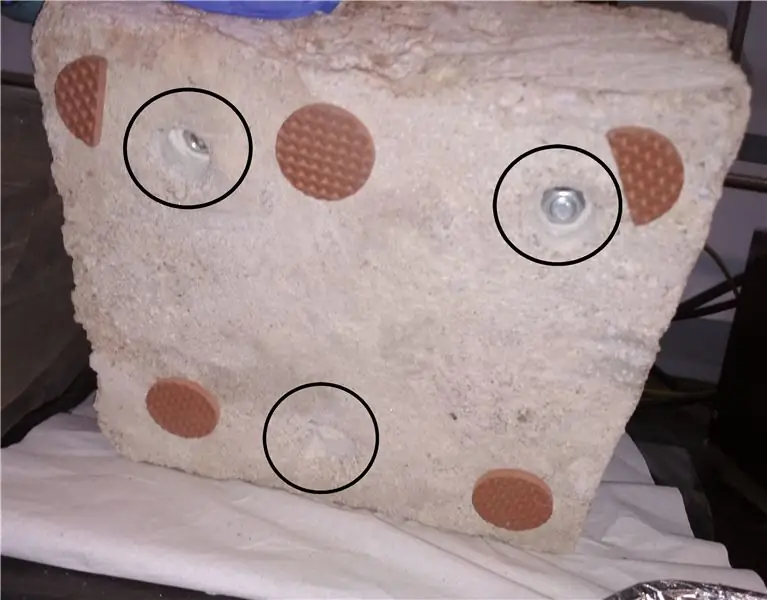
Le support moteur doit servir à 2 fins, maintenir le moteur en place et amortir les vibrations. Le montage que vous réaliserez sera spécifique à votre moteur. Je vais décrire ce que j'ai fait pour vous donner une idée de la façon de faire le vôtre. Certains moteurs ont une ventilation sur le côté, alors soyez conscient de l'endroit et gardez-le à l'écart pour le refroidissement.
Base et ressortsTrouvez une base lourde assez grande pour le projet. J'ai trouvé une section de béton d'une épaisseur appropriée et l'ai coupée à la bonne taille à l'aide d'une meuleuse d'angle diamantée. Des pavés de béton ou une plaque de métal épaisse devraient tout aussi bien fonctionner. Si vous le pouvez, essayez de trouver quelque chose qui n'a pas besoin d'être coupé.
Les pierres dans le béton rendent le perçage difficile et signifient parfois que les trous dérivent sur le côté. J'ai donc percé des trous dans la base pour la barre filetée avant de marquer les trous sur le boîtier du moteur (si vous avez un matériau plus souple, l'ordre n'aura pas d'importance).
1. Percez les trous pour la barre filetée avec un foret à maçonnerie du diamètre de la barre filetée.
2. Utilisez un foret à maçonnerie beaucoup plus gros pour contre-enfoncer l'extrémité de la barre filetée, la rondelle et l'écrou qui seront sous la base.
3. Marquez les trous sur le bloc de bois du boîtier du moteur pour la barre filetée ou sur un morceau de papier à utiliser plus tard comme gabarit.
4. Coupez la barre filetée à longueur, limez le bord coupé et vérifiez que le fil est toujours bon. Placer un écrou sur la barre avant de couper. Lorsque ce correctif est supprimé, il peut réparer/aligner le fil, s'il n'est pas trop endommagé par la suite.
5. Placez les barres à travers le béton suivies d'une rondelle et d'un écrou de chaque côté.
6a. Si vous avez réussi à trouver des ressorts suffisamment longs et rigides pour supporter le moteur et le boîtier, vous pouvez les placer suivis d'une rondelle épaisse. Une rondelle épaisse est nécessaire car une rondelle fine peut se coincer dans le filetage. Vous pouvez fabriquer vos propres rondelles en perçant un trou dans un morceau de métal approprié et en finissant le trou avec une lime.
6b. Si vous préférez ne pas utiliser de ressorts, un écrou et une rondelle peuvent être utilisés à la place, l'inconvénient est que cela ne servira pas à amortir les vibrations du moteur.
Étape 5: Construisez le support du moteur - Boîtier du moteur
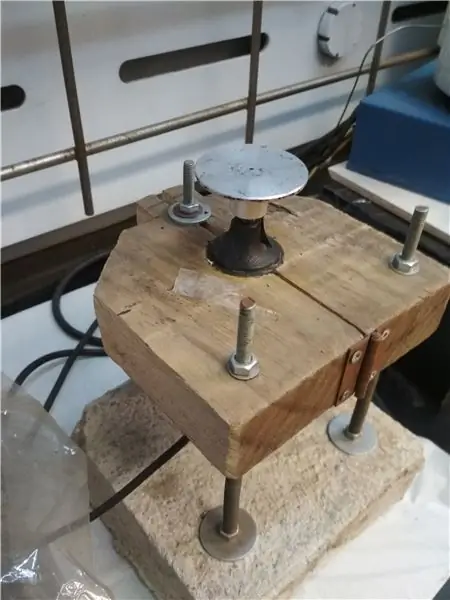
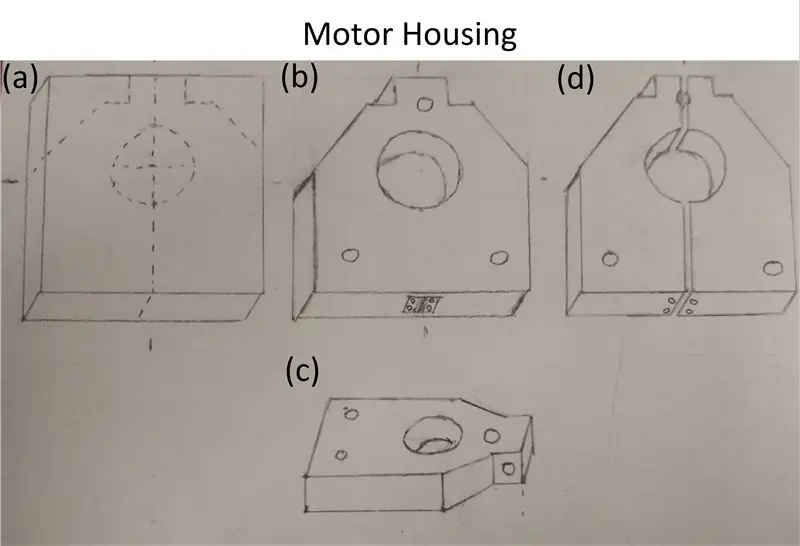
Le boîtier du moteur était fait comme une pince, des morceaux de pin étaient articulés avec une cavité au centre et un écrou et un boulon pour le fixer solidement. Le bois utilisé pour mon logement était une chute d'un chevron de section 38x228 mm.
1. Déterminez la taille du bois dont vous avez besoin pour votre moteur et marquez-le comme dans (a) de la photo ci-dessus.
2. Marquez un trou pas plus petit que le diamètre de votre moteur, nous avons besoin d'un peu d'espace pour la bande de caoutchouc qui sera entre le moteur et le boîtier. L'assemblage est indulgent sur la taille du trou en raison de la fixation comme la pince (charnière et boulon).
3. Percez un avant-trou puis percez le trou à l'aide d'une scie cloche. La scie cloche que j'ai utilisée ne coupe que d'environ 22 mm de profondeur, j'ai donc percé à mi-chemin de chaque côté.
4. Marquez et percez les trous pour la barre filetée qui supportera le carter du moteur. Ceux-ci doivent être au moins 1 mm plus épais que la barre filetée pour permettre un mouvement libre.
5. Vissez la charnière selon (b) sur la photo ci-dessus, puis retirez-la. C'est pour faire les trous.
6. Découpez la forme comme en (b) de la photo ci-dessus, j'ai utilisé une scie à dos.
7. La forme nous permet d'avoir un boulon en face de la charnière. Percez le trou pour le boulon comme indiqué en (c) de la photo ci-dessus. Le trou doit être environ 2 mm plus large que le boulon pour permettre une ouverture et une fermeture faciles de l'assemblage.
8. Coupez la pièce dans le sens de la longueur comme en (d) de la photo ci-dessus, puis revissez la charnière.
9. Enveloppez le moteur avec une bande en caoutchouc et placez-le dans le boîtier, l'insert et serrez un écrou, un boulon et une rondelle pour maintenir le boîtier fermé, assurez-vous que cela est ferme mais pas trop serré. Si votre moteur a une ventilation sur le côté, assurez-vous de ne pas bloquer son flux d'air.
10. Placez le boîtier du moteur sur la base. Assurez-vous que les ressorts sont en place avec une rondelle sur le dessus. Placez une rondelle et un écrou sur les 3 barres filetées pour maintenir le moteur. Un tampon en caoutchouc supplémentaire peut être placé entre le boîtier du moteur et la rondelle sur le dessus pour mieux réduire les vibrations.
11. Serrez les 3 écrous à l'aide d'un niveau à bulle pour vous guider.
Étape 6: Construire le support moteur - Chambre
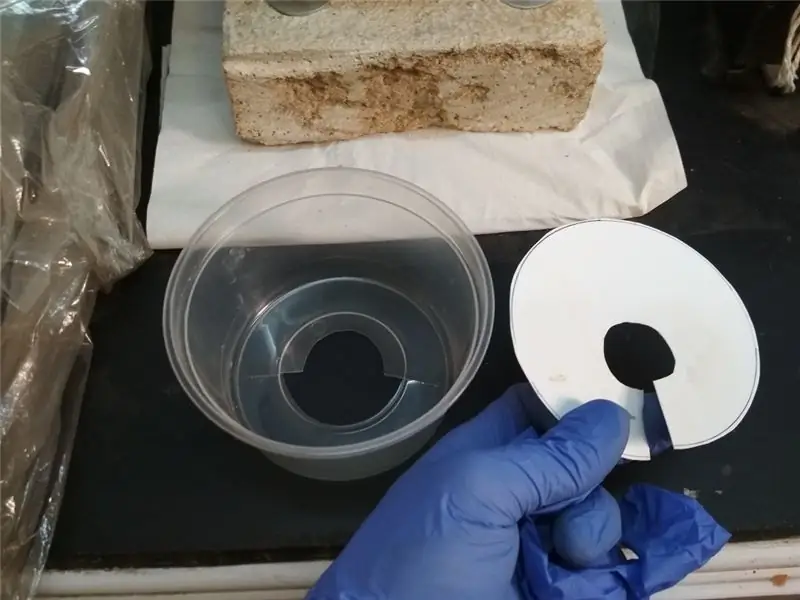
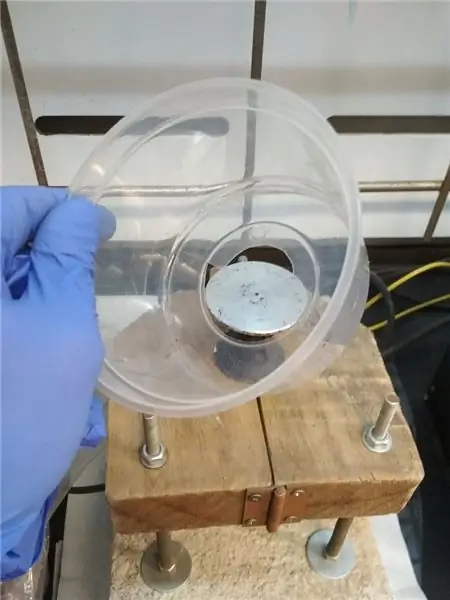
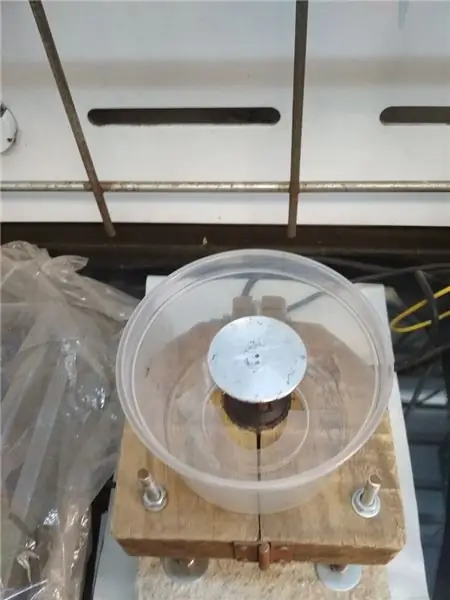
Pour fabriquer la chambre, j'ai utilisé un pot de yaourt transparent et une feuille de plastique épaisse.
1. Utilisez un couteau pour découper une forme dans la base du récipient à travers laquelle vous pouvez faire passer le mandrin (pour un mandrin qui ne sera pas retiré pour le nettoyage). J'ai coupé une diagonale à travers la base du conteneur permettant plus d'espace pour manœuvrer le conteneur pour s'adapter sur le mandrin sans agrandir le trou au centre.
2. Fixez le conteneur en place avec un peu de ruban adhésif à l'extérieur du conteneur. Je préfère cela à un montage permanent pour un nettoyage plus facile.
3. Placez une serviette en papier au fond du récipient pour absorber le liquide pendant le revêtement par centrifugation, puis couvrez la chambre de papier d'aluminium. Utilisez un peu de ruban adhésif là où cela est nécessaire pour éviter que cela ne touche l'arbre ou le mandrin. Ce « pansement » doit être changé périodiquement. La feuille attrape la majeure partie du liquide et la serviette en papier absorbe la plupart de ce qui passe à travers la feuille.
Bonus: après avoir utilisé la méthode du ruban adhésif double face pour attacher les échantillons, j'ai pris un indice d'Ossila (ils ont du matériel de laboratoire de qualité) et j'ai découpé une ancienne carte de crédit pour faire un montage sans vide/sans ruban pour mes échantillons.
Étape 7: Construire le circuit de contrôle
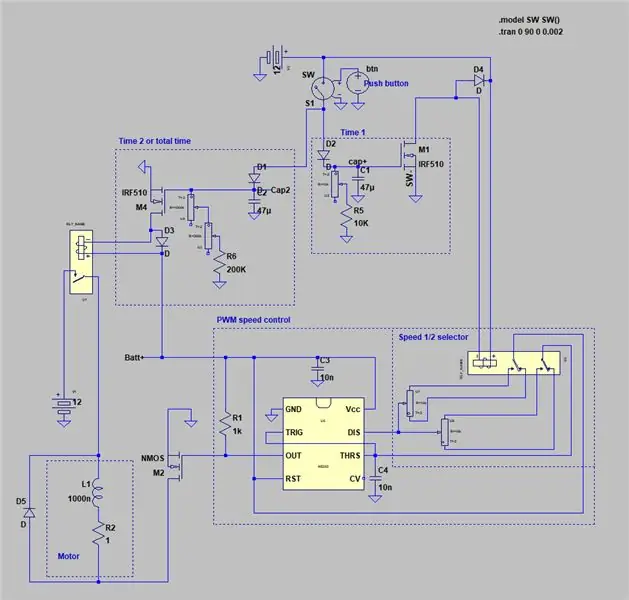
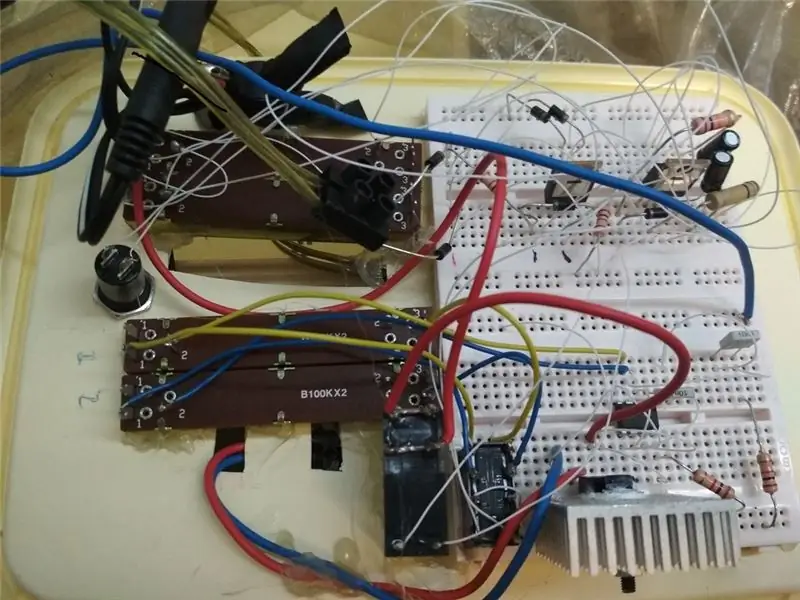
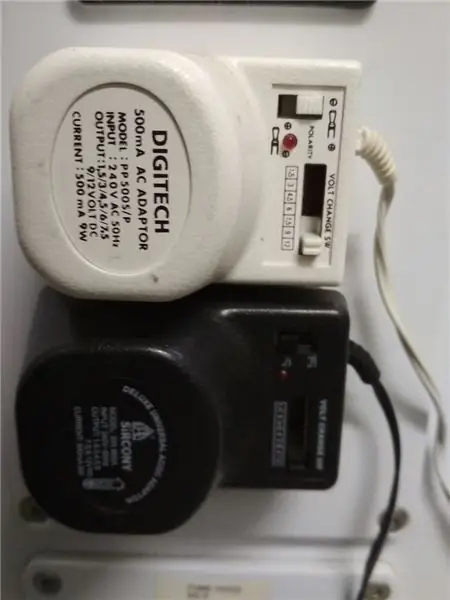
En regardant les images ci-dessus, vous verrez des schémas de circuit soignés et une mise en œuvre de la planche à pain. J'ai utilisé des alimentations 12V 500mA séparées pour le moteur et le circuit de commande car le moteur est conçu pour 500mA, en règle générale, il est préférable d'avoir 20% de capacité supplémentaire sur votre alimentation. Si vous avez une alimentation qui peut fournir suffisamment de courant pour les deux, tant mieux.
Plutôt que d'expliquer étape par étape, regardons ce que fait chaque section.
Le circuit de contrôle du temps allume et éteint la tournette et contrôle dans lequel des 2 étages/états se trouve le circuit PWM et quand commuter.
Cela se fait en alimentant 2 relais via des transistors MOSFET. Un relais SPST contrôle l'activation et la désactivation, et un relais DPDT contrôle lequel des deux pots définit le cycle de service du circuit PWM.
Le circuit PWM est simplement une minuterie NE555 en fonctionnement astable. Le rapport cyclique est contrôlé par des pots, où le rapport de la résistance réglée à la valeur du pot est le rapport cyclique (voir "bloc sélecteur de vitesse" dans le schéma).
Charger:
Les MOSFET sont utilisés car ils permettent de commuter un courant électrique négligeable via leur borne de grille. Cela nous permet de stocker la charge dans des condensateurs pour alimenter les MOSFETS qui à leur tour pilotent les relais. Un bouton poussoir à contact momentané est utilisé pour charger les condensateurs. Des diodes sont utilisées entre le contact momentané et les condensateurs pour empêcher le passage de courant d'un condensateur à l'autre.
Décharge:
Le principe de contrôle du temps des 2 étages est la décharge des condensateurs à travers une résistance. Cette résistance est fixée par des pots, plus la résistance est élevée plus la décharge est lente. Cela suit idéalement τ = RC, où est la période ou le temps, R est la résistance et C est la capacité.
Dans le circuit de temps utilisé, il y a 2 pots doubles de 500K, cela signifie que pour chaque pot il y a 2 jeux de bornes. On en profite pour câbler le deuxième pot en série avec lui-même et en série avec l'un des premiers borniers de pots. De cette façon, lorsque nous définissons la résistance sur le premier pot, cela ajoutera la résistance équivalente au second. Le premier pot est limité à 500K tandis que la façon dont le second est câblé, il aura une résistance jusqu'à 1000K plus la valeur du premier pot. Pour inclure une résistance minimale, j'ai en outre ajouté une résistance de valeur fixe à chaque ligne selon le schéma de circuit.
Étape 8: Étalonnage et test
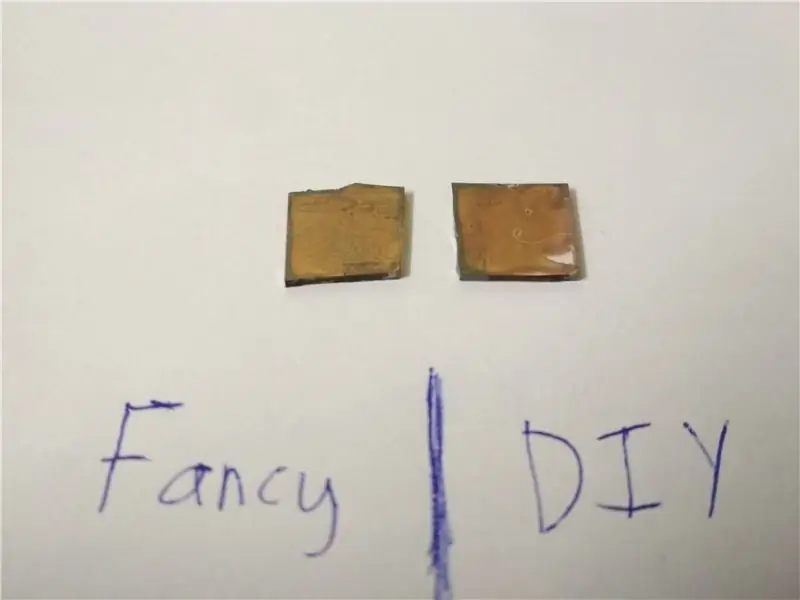
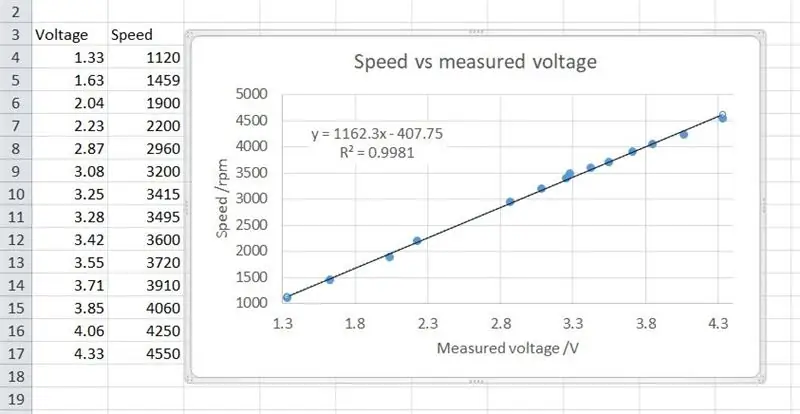
Après avoir terminé la tournette, j'ai commencé à la tester. L'image des échantillons ci-dessus a un échantillon (hybride-pérovskite) réalisé sur une tournette coûteuse sur la gauche et la tournette décrite dans ce Instructable sur la droite. Ces centrifugeuses étaient réglées à la même vitesse.
La tournette peut être calibrée soit par rapport à la tension, soit par rapport à la position de vos pots de vitesse. J'ai d'abord calibré en utilisant la tension puis en marquant les vitesses/positions que j'utilise le plus souvent sur les pots.
Lors de l'étalonnage avec la tension, je ne sais pas si différents multimètres liront le signal PWM comme la même tension, à cause de cela, j'utilise toujours le même multimètre avec lequel j'ai étalonné si je dois régler la tournette à une vitesse qui n'a pas d'associé marquage. La tension a été lue à la sortie fournie au moteur. Le multimètre n'a pas été connecté pendant la mesure de la vitesse pour éviter que le multimètre ne réduise le courant fourni au moteur.
1. Dans la section sur les tests de vitesse, le processus de test de vitesse a été détaillé. Répétez ce processus à différentes positions sur les pots de contrôle de vitesse, essayez d'inclure les vitesses auxquelles vous avez l'intention d'utiliser la tournette et les vitesses minimale et maximale. Environ 5 mesures devraient suffire. Pour chaque vitesse, notez la position et/ou la tension.
2. Mettez les vitesses et les tensions d'étalonnage dans Microsoft Excel, puis tracez un graphique
3. Ajoutez une ligne de tendance à vos données. Utilisez l'ajustement le plus simple qui expliquera la tendance des données, idéalement un polynôme linéaire ou du 2e ordre.
3a. Pour ce faire dans Excel, sélectionnez votre graphique tracé, accédez à l'onglet mise en page dans le ruban d'options
3b. Cliquez sur l'icône « Ligne de tendance ».
3c. Sélectionnez « plus d'options de courbe de tendance »
3d. Choisissez votre option et cochez "Afficher l'équation sur le graphique" et "Afficher la valeur R au carré sur le graphique"
J'espère que vous avez un bon ajustement, maintenant vous pouvez utiliser l'équation pour calculer le RPM à partir de la tension fournie au moteur.
Depuis et le lecteur est probablement un scientifique…
Technique de la pipette: Dans la vidéo, j'ai utilisé la micro-pipette en biais, cela m'a aidé à garder mon bras hors de la vidéo. Idéalement, la pipette doit être verticale et aussi proche de l'échantillon/du substrat sans le toucher que vous pouvez répéter de manière fiable.
Qualité du film: Certaines des caractéristiques des films minces déposés sur l'image peuvent être évitées en filtrant les solutions précurseurs avant utilisation (comme l'utilisation d'un filtre PTFE de 33 um). La couleur plus claire du film vue de la tournette « fantaisie » peut être le résultat de la vitesse de montée en puissance et de l'atmosphère. La centrifugeuse « fantaisie » a été fabriquée pour fonctionner uniquement avec un débit élevé de gaz inerte, car les films ont été enduits par centrifugation dans de l'azote sur la centrifugeuse « fantaisie » et de l'air dans la centrifugeuse de bricolage.
Étape 9: Remerciements
Cette brève section donne le contexte de l'endroit où j'étudie et des groupes qui soutiennent mes recherches qui se concentrent sur le photovoltaïque hybride-pérovskite.
- Université du Witwatersrand, Afrique du Sud
- National Research Foundation (NRF), Afrique du Sud
- GCRF-START. Royaume-Uni
- Gerry (qui a usiné le mandrin de la tournette en aluminium)
Conseillé:
Transformez presque tout en haut-parleur : 13 étapes (avec photos)
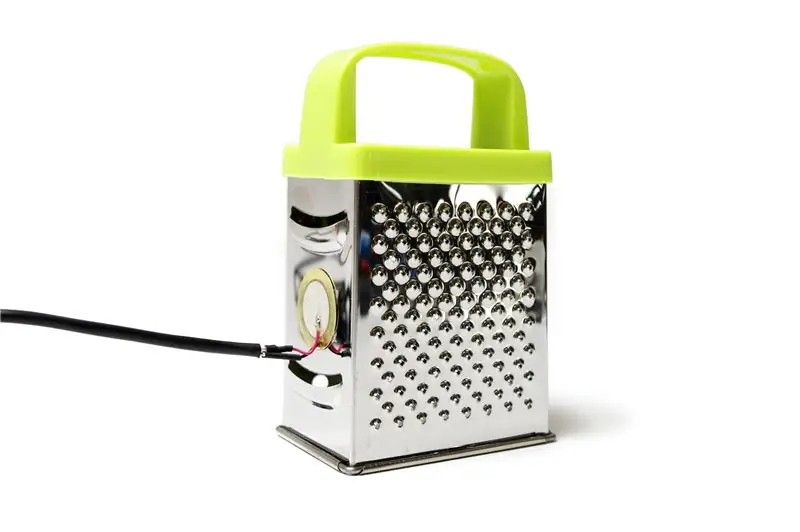
Transformez presque n'importe quoi en haut-parleur : Vous pouvez transformer presque n'importe quel objet en haut-parleur en utilisant un disque piézo et une poignée de composants supplémentaires. Bien que cela puisse sembler magique, il existe en fait une explication technique assez simple. En entraînant un disque piézo à l'aide d'un amplificateur, le disque
(presque) Programmeur universel MIDI SysEx CC (et séquenceur) : 7 étapes (avec photos)
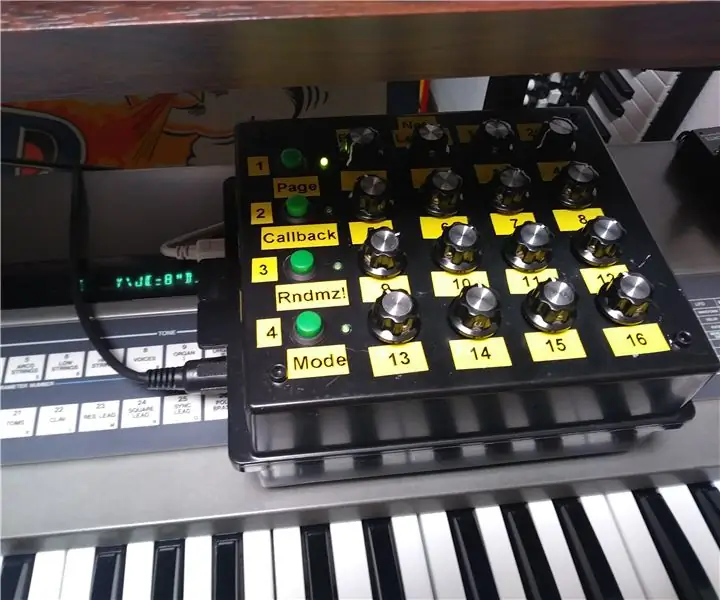
(presque) Universal MIDI SysEx CC Programmer (et Sequencer…) : Au milieu des années 80, les fabricants de synthés ont lancé un programme "moins c'est mieux" processus qui a conduit à des synthés barebones. Cela a permis de réduire les coûts du côté du fabricant, mais a rendu le processus de patching fastidieux voire impossible pour l'utilisation finale
Alimentation de banc variable analogique bricolage avec limiteur de courant de précision : 8 étapes (avec photos)
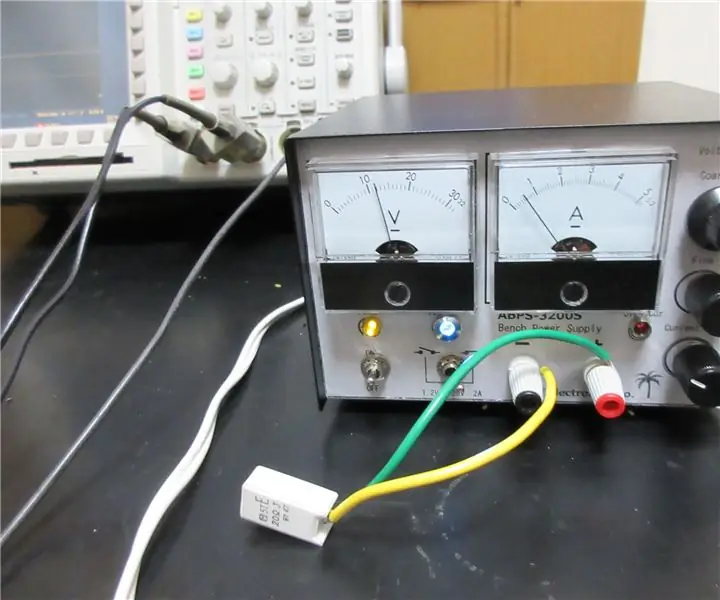
Alimentation de banc variable analogique bricolage avec limiteur de courant de précision : dans ce projet, je vais vous montrer comment utiliser le célèbre LM317T avec un transistor de puissance Booster de courant et comment utiliser l'amplificateur de détection de courant Linear Technology LT6106 pour un limiteur de courant de précision. Ce circuit peut permettre vous d'utiliser jusqu'à plus de 5A
Timing Gear et Chain Clock - Presque gratuit ! : 5 étapes (avec photos)
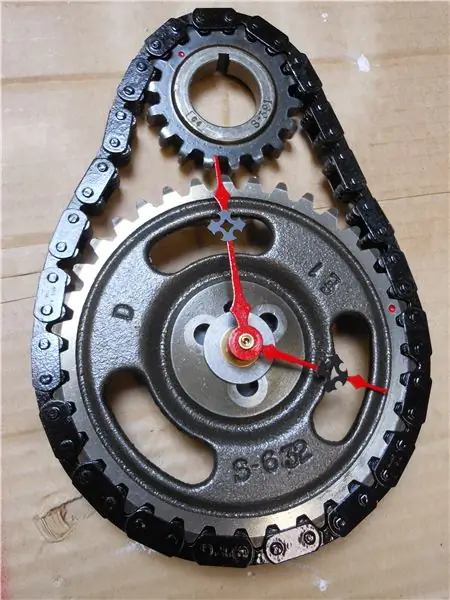
Engrenage de synchronisation et horloge à chaîne - Presque gratuit ! : J'espère que lorsque vous avez changé le jeu de synchronisation de votre voiture, vous n'avez pas jeté les anciens engrenages et la chaîne. J'ai failli le faire, mais ma femme m'a montré ceci : http://www.uncommongoods.com/product/auto-timing-chain-and-gears-wall-clock 125 $ US plus frais de port.
Circuits GPIO Raspberry Pi : Utilisation d'un capteur analogique LDR sans ADC (convertisseur analogique-numérique) : 4 étapes
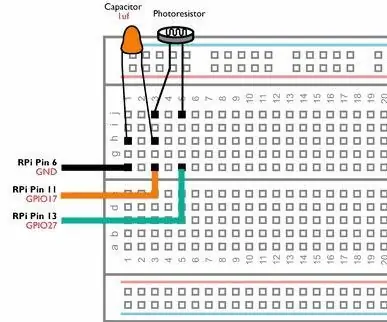
Circuits GPIO Raspberry Pi : Utilisation d'un capteur analogique LDR sans ADC (convertisseur analogique-numérique) : Dans nos précédents Instructables, nous vous avons montré comment vous pouvez lier les broches GPIO de votre Raspberry Pi aux LED et aux commutateurs et comment les broches GPIO peuvent être hautes ou Faible. Mais que faire si vous souhaitez utiliser votre Raspberry Pi avec un capteur analogique ? Si nous voulons utiliser un