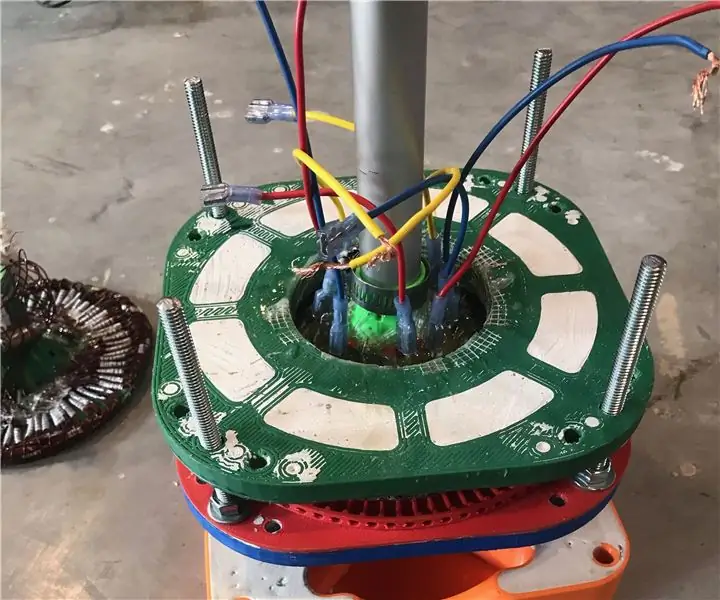
Table des matières:
2025 Auteur: John Day | [email protected]. Dernière modifié: 2025-01-23 14:46
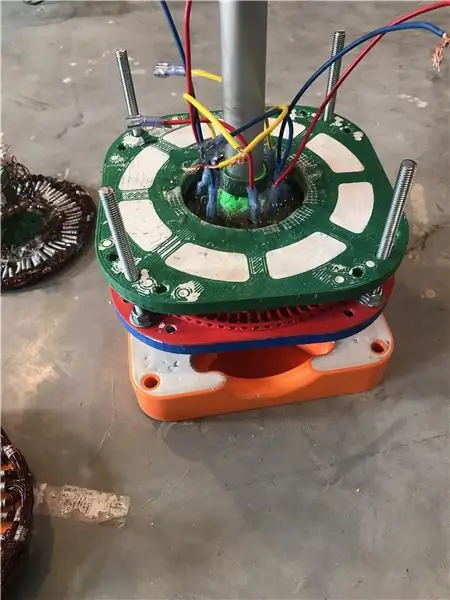
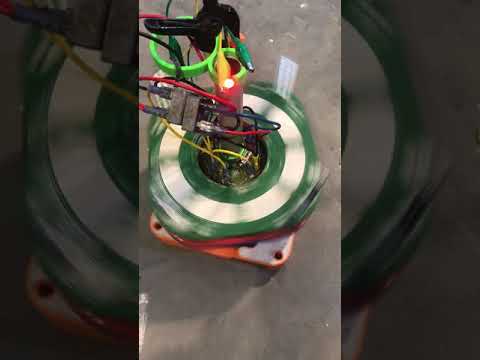
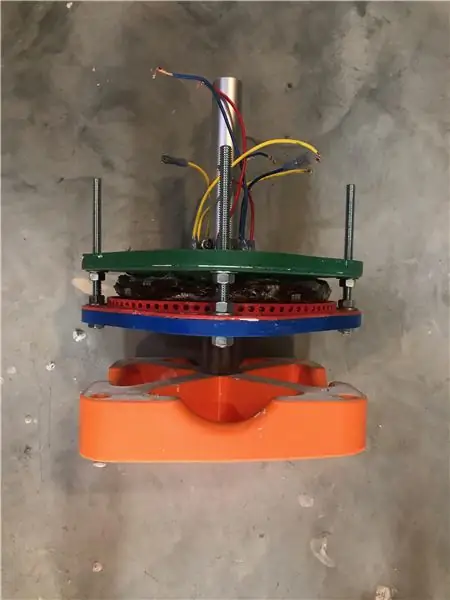
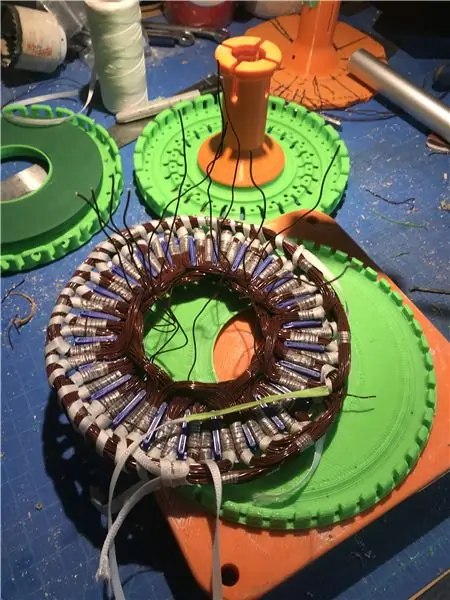
ARRÊTER!! A LIRE EN PREMIER !!! Ceci est un enregistrement d'un projet qui est encore en développement, n'hésitez pas à offrir votre soutien.
Mon objectif final est que ce type de moteur/alternateur puisse devenir une conception open source paramétrée. Un utilisateur devrait pouvoir entrer certains paramètres, tels que le couple, la vitesse, le courant, les volts/tr/min, les tailles d'aimant courantes et peut-être l'espace disponible, et une série de fichiers de coupe.stl et.dxf imprimables en 3D devrait être générée.
Ce que j'ai fait, c'est créer une plate-forme qui peut valider une conception simulée, qui peut ensuite être transformée en un appareil plus optimal par communauté.
C'est en partie l'une des raisons pour lesquelles j'ai configuré cela avec un dynamomètre. Un dynamomètre mesure le couple et la vitesse pour permettre de mesurer les hp ou les watts de l'arbre. Dans ce cas, j'ai construit l'alternateur avec un arbre stationnaire traversant, ce qui simplifie la configuration d'un système de dynamomètre et peut donc être configuré pour être entraîné en moteur par un RC ESC (j'espère) et le couple mesuré sur la sortie, ainsi que la vitesse, V et Amps, permettant de déterminer l'efficacité du moteur.
Pour mes besoins, il peut être entraîné par un moteur à vitesse variable (surplus de la perceuse sans fil, avec engrenage réducteur) et l'entrée de couple d'arbre mesurée, ainsi que V et Amps out, permettant de générer une efficacité réelle et les charges de turbine attendues à simuler.
Dans ce mode, j'espère utiliser un RC ESC capable de freinage régénératif, et peut-être un Arduino pour contrôler la charge que mon VAWT porte pour atteindre le MPPT (Multi Power Point Tracking).
Le MPPT est utilisé dans le contrôle solaire et éolien, mais c'est un peu différent pour le vent. Avec l'énergie éolienne, un gros problème est que lorsque la vitesse du vent double de 10 km/h à 20 km/h, l'énergie disponible du vent augmente d'un cube, donc de 8 fois. Si 10W étaient disponibles à 10km/h, alors 80W sont disponibles à 20km/h. C'est bien d'avoir plus d'énergie, mais la sortie des alternateurs ne fait que doubler à mesure que la vitesse double. Donc, si vous avez l'alternateur parfait pour un vent de 20 km/h, sa charge peut être si forte qu'à 10 km/h il ne démarrera même pas.
Ce que fait MPPT, c'est d'utiliser un interrupteur à semi-conducteurs très résistant pour déconnecter puis reconnecter un alternateur très rapidement. Il vous permet d'ajuster la charge supportée par un alternateur, et le Multi, du MPPT, signifie que vous pouvez définir différentes charges pour différentes vitesses.
Ceci est très utile, car tous les types d'éoliennes collectent leur énergie maximale lorsque la charge est adaptée à l'énergie disponible ou à la vitesse du vent.
DONC
Ce n'est pas une recette, bien que je pense qu'elle pourrait être copiée à partir de ce que j'ai posté, et je serais heureux de fournir de plus amples informations, mais je suggère que la meilleure option serait de me suggérer des améliorations, avant la fin du concours Circuits et capteurs, afin que je puisse considérer, répondre et peut-être améliorer cette instructable.
Je continuerai à mettre à jour, réviser et ajouter des informations, donc si c'est intéressant maintenant, vous voudrez peut-être vérifier à nouveau dans un instant, mais j'espère en faire un peu avant la fin du concours Sensors les 29/19 juillet.
De plus, je ne suis pas une bête particulièrement sociale, mais j'aime bien une tape dans le dos de temps en temps, et c'est l'une des raisons pour lesquelles je suis ici:-) Dites-moi si vous aimez voir mon travail et voulez voir plus s'il vous plait:-)
Ce projet est né parce que je voulais une charge contrôlable pour tester mes conceptions de turbines, et je voulais qu'elle soit facilement reproductible, afin que d'autres puissent l'utiliser aussi. À cette fin, je me suis contraint à concevoir quelque chose qui pourrait être construit avec uniquement une imprimante FDM, aucune autre machine-outil n'était nécessaire. Il ne semble pas y avoir beaucoup de produits commerciaux qui répondent au besoin d'un alternateur à couple élevé, à faible vitesse et sans cogging, bien qu'il y en ait quelques-uns en provenance de Chine. En général, il n'y a pas beaucoup de demande parce que les systèmes d'engrenages sont si bon marché et l'électricité est si bon marché.
Ce que je voulais, c'était quelque chose qui produisait environ 12 V à 40-120 tr/min et environ 600-750 W à 120-200 tr/min. Je voulais également qu'il soit compatible avec les contrôleurs PMA triphasés bon marché du monde RC (contrôleurs de vitesse électroniques d'ESC). Une dernière exigence était qu'il s'agisse d'un coureur extérieur (le boîtier ou la coque avec des aimants tourne, tandis que l'arbre avec le stator est fixe), avec un arbre qui traverse tout le boîtier et un stator qui se fixe à l'arbre.
Cette instructable est un travail en cours, et je le publie pour que les gens puissent avoir une vue du processus, pas tellement parce que je pense qu'ils devraient le copier. Une chose clé que je changerais est que la plaque de support en fil que j'ai construite n'est pas assez solide pour canaliser correctement les champs magnétiques autour de l'anneau, donc une grande partie du flux magnétique payé dans ces aimants est gaspillée à l'arrière. Lorsque je refais la conception, ce que je ferai sous peu, je ferais probablement les plaques de support magnétiques sous forme de plaques d'acier découpées cnc. L'acier serait assez bon marché, beaucoup plus solide et simplifierait la plupart de cette construction. C'était intéressant de faire les composites FDM/fil/plâtre comme je l'ai illustré ici, et avec du PLA chargé de fer, les choses auraient été différentes aussi. J'ai cependant décidé que je voulais quelque chose qui durerait vraiment, donc des plaques d'acier.
J'ai bien avancé sur cette version, que je vais utiliser pour tester ce VAWT. Je ne suis pas encore tout à fait là en termes de performances à basse tension. Je pense que ma puissance / couple est dans la bonne fourchette, je mettrai à jour au fur et à mesure que les choses avancent, mais à ce stade, ce que j'ai a de bonnes chances d'être la charge contrôlable dont j'ai besoin. Lorsqu'il est en court-circuit, il semble pouvoir fournir une résistance de couple assez importante, plus que suffisant pour tester la turbine. J'ai juste besoin de mettre en place une banque de résistance contrôlée, et j'ai un ami qui m'aide avec ça.
Une chose que je vais aborder brièvement est que, comme beaucoup de gens maintenant, j'ai une imprimante 3D (utilisant le PLA) depuis quelques années, avec laquelle j'ai eu 20 à 30 kg de plaisir. Je trouve souvent cela frustrant, car les pièces de toute taille/résistance sont soit chères et très lentes à imprimer, soit bon marché, rapides et fragiles.
Je sais combien de milliers de ces imprimantes 3D existent, souvent ne faisant rien parce que cela prend trop de temps ou coûte trop cher pour fabriquer des pièces utiles. J'ai trouvé une solution intéressante pour des pièces plus solides et plus rapides à partir de la même imprimante et du même PLA.
Je l'appelle une "structure coulée", où l'objet imprimé (constitué d'une ou plusieurs pièces imprimées, et parfois de roulements et d'arbres), est constitué de vides conçus pour être remplis d'un liquide de remplissage durcissant. Bien sûr, certains des choix évidents pour un remplissage coulé seraient quelque chose comme de l'époxy chargé de fibres de verre coupées à brins courts, qui pourraient être utilisés pour des assemblages à haute résistance et légers. J'essaie aussi des idées à moindre coût et plus écologiques. L'envers de cet assemblage de "structure coulée", est que la cavité ou le vide que vous allez combler, peut comporter des éléments à haute résistance de petit diamètre, enfilés pré-tendus sur le "moule/bouchon" imprimé, ce qui rend la structure résultante un composite dans les matériaux et dans la structure, une partie de la peau stressée (la gaine PLA), mais avec un noyau à haute résistance à la compression qui comprend également des éléments à haute résistance à la traction. Je vais faire une deuxième instructable présentant cela, donc j'en parlerai ici, uniquement pour couvrir en quoi cela se rapporte à cette version.
Étape 1: Liste des matériaux et processus
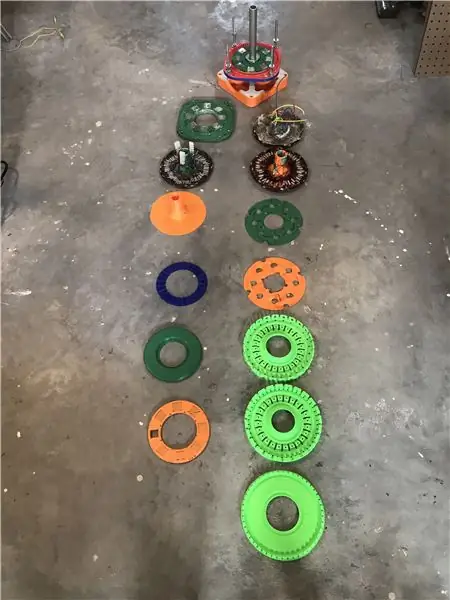
Le PMA se compose de 3 assemblages, chaque assemblage contenant ou utilisant une variété de pièces et de matériaux.
Du haut (côté palier) vers le bas (côté stator), 1. Support de roulement et groupe de roulements supérieur
2. Stator
3. Réseau magnétique inférieur
1. Le support de roulement et le tableau magnétique supérieur
Pour cela, j'ai utilisé des pièces imprimées en 3D énumérées ci-dessus
- Mag supérieur 150mm8pole et support de roulement CV5.stl,
- plaque intérieure côté roulement
- plaque extérieure côté roulement
- Roulement à alignement automatique d'identification de 1 "(comme utilisé dans les blocs d'oreiller standard ++ ajouter un lien Internet),
- 25' de fil d'acier galvanisé 24g
- 15' de fil d'acier galvanisé 10g
- 2 rouleaux de laine d'acier grossière
En option, le fil d'acier lourd et la laine d'acier pourraient être remplacés par des plaques de support en acier, découpées au laser / au jet d'eau, ou une plaque de support magnétique imprimée en 3D pourrait être possible (mais un fil d'acier lourd est toujours une bonne idée car il résistera à la déformation plastique sur temps). J'ai essayé de couler une plaque de support avec de l'époxy chargé de poudre d'oxyde de fer et j'ai eu un certain succès. L'amélioration du couplage de flux entre les aimants du réseau latéralement en utilisant une plaque de support plus efficace devrait augmenter les volts à des régimes inférieurs. Il est également bon de garder à l'esprit qu'il s'agit du principal composant structurel et que la plaque arrière transfère les forces des aimants aux poteaux de levage. Les forces magnétiques tirant les plaques l'une vers l'autre peuvent atteindre des centaines de livres, et les forces augmentent de façon exponentielle (cube, à la troisième puissance) à mesure que les plaques se rapprochent. Cela peut être très dangereux, et des précautions doivent être prises avec les outils et autres objets qui pourraient être attirés par la plaque assemblée ou son dos !
J'ai utilisé environ 300 pieds de fil magnétique revêtu de 24 g dans les enroulements que je couvrirai en détail plus tard.
Étape 2: Fabrication des plaques magnétiques
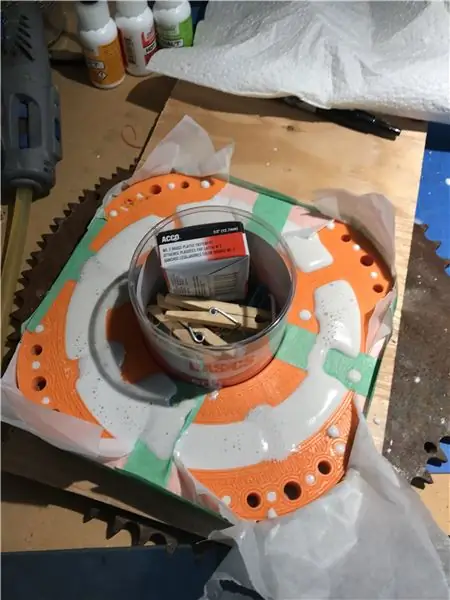
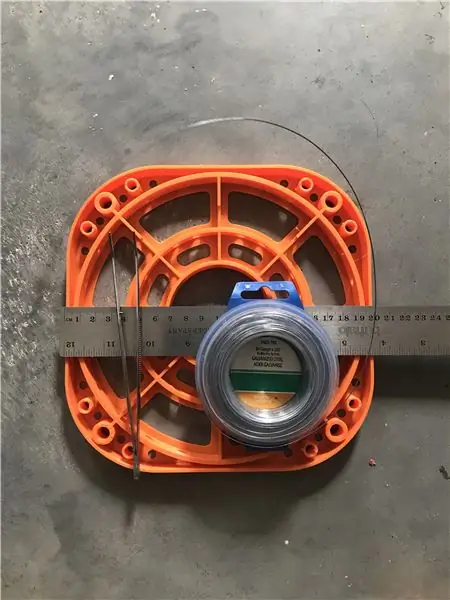
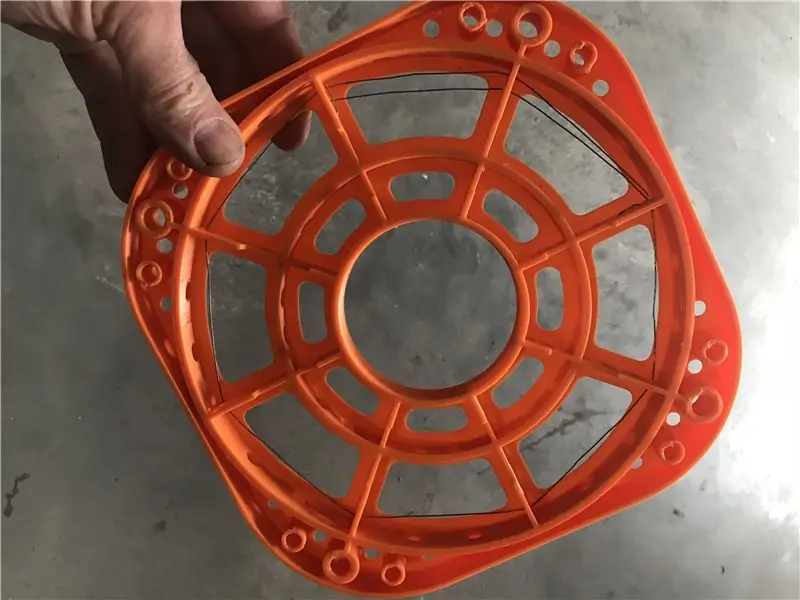
Dans cet alternateur à flux axial, pour minimiser le cogging et maximiser la sortie, j'utilise deux réseaux d'aimants, un de chaque côté des bobines du stator. Cela signifie qu'aucun noyau magnétique n'est nécessaire pour attirer le champ magnétique à travers les enroulements en cuivre, comme le font la plupart des géométries moteur/alternatif. Il existe des conceptions de flux axiaux qui utilisent des noyaux de ferris, et je pourrais essayer quelques expériences de cette façon à l'avenir. J'aimerais essayer un matériau chargé de fer imprimable en 3D.
Dans ce cas, j'ai choisi un réseau d'aimants à 8 pôles dans un cercle d'environ 150 mm, en utilisant des aimants en terres rares de 1 "x1" x 0,25". Cette taille visait à garantir que toutes les pièces s'adapteraient sur un lit d'impression de 210 mm x 210 mm. En général, j'ai d'abord dimensionné cet alternateur en comprenant que plus le diamètre est grand, mieux c'est en termes de volts par tr/min, il est donc aussi grand que conviendrait confortablement à mon lit d'impression. aimants, plus les aimants sont éloignés du centre, plus ils voyagent vite, et il y a aussi plus de place pour le cuivre ! Toutes ces choses peuvent s'additionner rapidement ! Cependant, une conclusion à laquelle je suis arrivé est que dans cette gamme de taille, un Le système de flux pourrait être une meilleure construction à la maison. Les petits rotors n'ont pas beaucoup de place et les choses peuvent devenir assez serrées, surtout si vous faites un arbre traversant comme je l'ai fait dans cette conception. Aussi si votre aimant (longueur radiale) est petit par rapport au diamètre de votre rotor, comme dans celui-ci, (environ 6 "de diamètre à 1" aimant), puis le windi ng devient un peu étrange avec l'enroulement d'extrémité interne n'étant que d'environ la moitié de la longueur de l'extérieur.
Retour à l'instruction ! La façon dont j'ai assemblé les plaques magnétiques de cet alternateur consiste d'abord à coller la plaque magnétique (verte) sur la bride/plaque d'appui rouge. J'ai ensuite placé la plaque magnétique sur quelques fines couches de contreplaqué (environ 0,75 d'épaisseur) et placé les deux sur une plaque d'acier lourde, pour permettre aux aimants de serrer l'assemblage en place. Ensuite, j'ai enroulé du fil d'acier sur le à l'arrière des plaques magnétiques. Cela ne s'est pas passé tout à fait comme je l'avais espéré. Le fort champ magnétique a tiré le fil vers le centre des aimants, et je n'ai pas réussi à plier chaque rangée de fil pour s'adapter parfaitement à l'endroit suivant, sans bousculer le premier tour. J'avais espéré pouvoir simplement enrouler le fil et le flux magnétique le bloquerait. Ensuite, j'ai essayé de couper des anneaux de fil, et c'était mieux, mais encore loin de ce que j'avais espéré en termes d'obtention d'une belle plaque de support cohérente à partir de fil. Des moyens plus complexes d'y parvenir sont possibles et pourraient valoir la peine d'être expérimentés dans le futur. J'ai également essayé d'utiliser de la laine d'acier, compactée dans le champ magnétique, comme plaque de support ou flux chemin de retour. Cela semblait fonctionner, mais la densité de fer réelle ne semblait pas être très élevée, alors je di ne testez pas son efficacité, en partie parce que je pensais que la structure du fil était importante pour les charges mécaniques sur les plaques magnétiques. La laine d'acier peut également valoir la peine d'être étudiée ultérieurement, mais les plaques d'acier découpées au jet d'eau sont probablement la prochaine option que j'essaierai.
Ensuite, j'ai pris la pièce orange imprimée en 3D et j'ai tissé du fil à travers et autour d'elle, le long de ce qui me semblait être les directions de la charge la plus élevée, boulon à boulon et boulon à centrer plusieurs fois sur chaque coin. Je l'ai également enroulé autour des trous de boulons où toute la tige filetée passe en tant que poteaux de levage pour maintenir et régler l'espacement entre les plaques.
Après avoir été convaincu que la plaque magnétique et la bride étaient assez bonnes et que la plaque de support orange était enfilée de manière satisfaisante avec du fil de renforcement, j'ai joint les deux avec de la colle. Des précautions doivent être prises car ce joint de colle devra être étanche ou fermé. J'ai eu des fuites les deux premières fois, et c'est un gâchis, ça gaspille beaucoup de plâtre et c'est plus de stress que nécessaire. Je recommanderais de garder un peu d'adhésif bleu ou d'autres chewing-gums comme un adhésif non permanent pour colmater rapidement les fuites. Une fois les pièces jointes, remplissez avec le matériau de renfort de votre choix. J'ai utilisé un plâtre dur, modifié avec de la colle PVA. Le plâtre est censé atteindre 10 000 psi en compression, mais pas beaucoup en tension (donc le fil). J'aimerais essayer l'époxy avec du verre haché et du cabosil, ou du béton et des adjuvants.
Une chose pratique à propos du plâtre, c'est qu'une fois qu'il donne un coup de pied, vous avez un peu de temps où il est dur, mais fragile et les fuites ou les taches peuvent facilement être grattées ou renversées.
Dans cette conception, il y a deux plaques magnétiques. L'un a un roulement, une unité d'alignement automatique de bloc d'oreiller standard de 1 . J'ai pressé le mien dans le réseau d'aimants dès le début. Pour l'application pour laquelle je l'ai conçu, un deuxième roulement sera situé dans la turbine au-dessus de l'alternateur, donc je n'utilisait que le seul roulement à alignement automatique. Ce fut un peu pénible à la fin. Ces pièces pourraient également être assemblées avec chaque plaque magnétique ayant un roulement, si les fils de sortie du stator étaient conduits à l'intérieur à travers l'arbre monté. Cela permettent de monter des hélices contrarotatives sur un arbre/tube commun non rotatif.
Étape 3: Création du stator

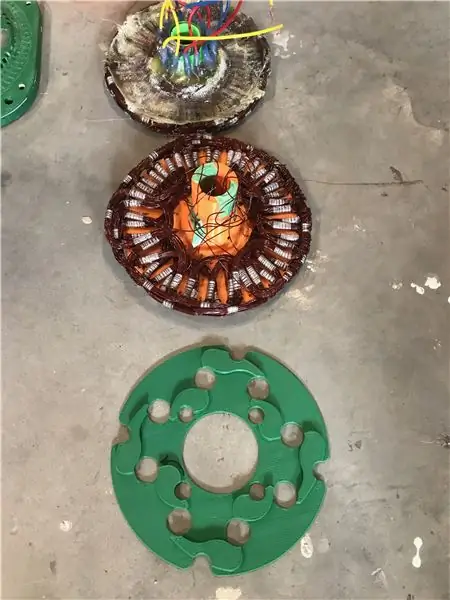
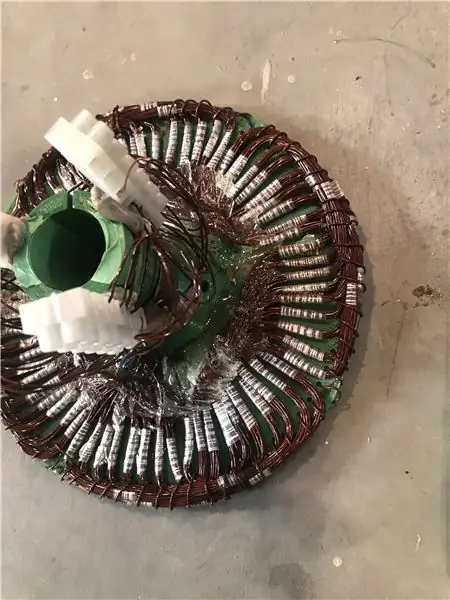
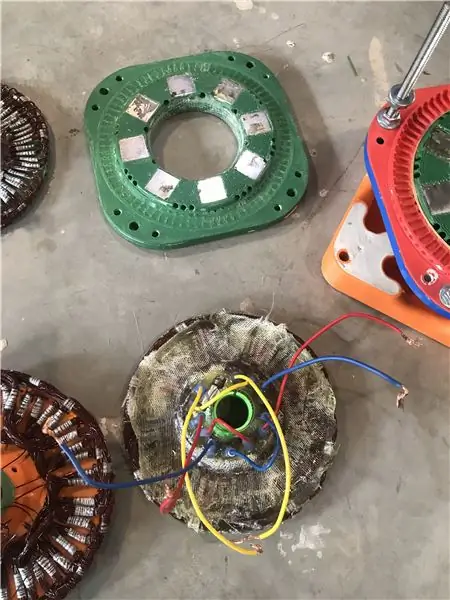
En accord avec mon thème d'essayer d'expliquer ce que j'ai fait, et pourquoi cela semblait être une bonne idée à l'époque, le stator nécessitera un peu plus d'espace.
Dans un PMA, généralement les enroulements sont fixes, tandis que les ensembles magnétiques tournent. Ce n'est pas toujours le cas, mais presque toujours. Dans un assemblage à flux axial, avec la compréhension de la "règle de la main droite" fondamentale, il est entendu que tout conducteur rencontrant un champ magnétique tournant aura un courant et une tension générés entre les extrémités du fil, la quantité de courant utile étant proportionnelle à la direction du terrain. Si le champ se déplace parallèlement au fil (par exemple, dans un cercle autour de l'axe de rotation), aucun courant utile ne sera généré, mais des courants de Foucault importants seront générés, résistant au mouvement des aimants. Si le fil est perpendiculaire, la tension et le courant de sortie les plus élevés seront atteints.
Une autre généralisation est que l'espace à l'intérieur du stator, à travers lequel le flux magnétique passe en rotation, pour une puissance de sortie maximale, doit être rempli d'autant de cuivre, tous disposés radialement, que possible. C'est un problème pour les systèmes de flux axial de petit diamètre, car dans ce cas, la zone disponible pour le cuivre près de l'arbre est une fraction de la zone au bord extérieur. Il est possible d'obtenir 100% de cuivre dans la zone la plus intérieure rencontrée par le champ magnétique, mais dans cette géométrie, cela ne vous donne peut-être que 50% sur le bord extérieur. C'est l'une des principales raisons de rester à l'écart des conceptions de flux axiaux qui sont trop petites.
Comme je l'ai dit précédemment, cette instructable ne concerne pas la façon dont je le referais, mais plutôt pour pointer dans certaines directions qui semblent prometteuses et montrer certains des nids-de-poule qui peuvent être atteints sur ce chemin.
En concevant le stator, je voulais le rendre aussi flexible que possible en termes de volts de sortie par tr/min, et je voulais qu'il soit triphasé. Pour une efficacité maximale, en minimisant les courants de Foucault générés, toute "jambe" (chaque côté d'une bobine doit être considérée comme une "jambe") ne doit rencontrer qu'un aimant à la fois. Si les aimants sont proches les uns des autres ou se touchent, comme c'est le cas dans de nombreux moteurs rc à haut rendement, pendant que la "jambe" traverse l'inversion du flux magnétique, des courants de Foucault importants se développeront. Dans les applications de moteur, cela n'a pas autant d'importance, car la bobine est alimentée par le contrôleur lorsqu'elle est aux bons emplacements.
J'ai dimensionné le réseau d'aimants avec ces concepts à l'esprit. Les huit aimants du réseau mesurent chacun 1" de diamètre et l'espace entre eux est de 1/2". Cela signifie qu'un segment magnétique mesure 1,5" de long et qu'il a de la place pour 3 x 1/2" "jambes". Chaque "jambe" est une phase, donc à tout moment, une branche voit un flux neutre, tandis que les deux autres voient un flux croissant et un flux décroissant. Sortie triphasée parfaite, bien qu'en donnant autant d'espace au point neutre (pour minimiser les courants de Foucault) et en utilisant des aimants carrés (ou en forme de tarte), le flux atteint presque un pic au début, reste élevé, puis tombe rapidement à zéro. Ce type de sortie est, je pense, appelé trapézoïdal et peut être difficile pour certains contrôleurs que je comprends. Des aimants ronds de 1" dans le même appareil donneraient plus d'une véritable onde sinusoïdale.
Généralement, ces alternateurs maison ont été construits à l'aide de "bobines", des faisceaux de fils en forme de beignet, où chaque côté du beignet est une "jambe" et un certain nombre de bobines peuvent être attachées ensemble, en série ou en parallèle. Les beignets sont disposés en cercle, avec leurs centres alignés avec le centre du chemin magnétique. Cela fonctionne, mais il y a quelques problèmes. Un problème est que, puisque les conducteurs ne sont pas radiaux, une grande partie du conducteur ne passe pas à 90 degrés par rapport au champ magnétique, de sorte que des courants de Foucault sont générés, qui apparaissent sous forme de chaleur dans la bobine et une résistance à la rotation dans le réseau magnétique.. Un autre problème est que parce que les conducteurs ne sont pas radiaux, ils ne s'assemblent pas aussi bien. La sortie est directement proportionnelle à la quantité de fil que vous pouvez insérer dans cet espace, donc la sortie est réduite par des "jambes" non radiales. Bien qu'il soit possible et parfois fait dans les conceptions commerciales, pour enrouler une bobine avec des "jambes radiales, jointes en haut et en bas, il faut 2 fois plus d'enroulement d'extrémité qu'un enroulement en serpentin où le haut d'une jambe est joint au haut de la jambe appropriée suivante, puis le bas de cette jambe est joint à la jambe appropriée suivante, et ainsi de suite.
L'autre facteur important dans les alternateurs à flux axial de ce type (aimants rotatifs au-dessus et au-dessous du stator) est l'espace entre les plaques. Il s'agit d'une relation de loi cubique, lorsque vous réduisez la distance entre les plaques de 1/2, la densité de flux magnétique augmente de 8x. Plus vous pouvez rendre votre stator fin, mieux c'est !
Dans cet esprit, j'ai fabriqué un gabarit d'enroulement à 4 lobes, mis en place un système pour mesurer environ 50 pieds de brins de fil et enroulé le gabarit 6 fois, créant des faisceaux de fils d'environ 6 mm de diamètre. Ceux-ci que je place sur l'anneau d'espacement bleu, en les attachant à travers les trous de sorte que les extrémités des fils sortent par l'arrière. Ce n'était pas facile. Cela a été un peu aidé en ayant soigneusement scotché les paquets pour qu'ils ne se détachent pas, et en prenant mon temps et en utilisant un outil de formage en bois lisse pour pousser les fils en place. Une fois qu'ils étaient tous attachés en place, l'anneau d'espacement bleu a été placé dans le plus grand des bacs de formage vert clair, et à l'aide de l'outil de formage de beignet vert foncé, de l'autre côté du bac vert clair, soigneusement pressé à plat avec un étau d'établi. Cette cuve de formage a une rainure dans laquelle les torsades du fil d'attache peuvent s'asseoir. Cela prend du temps et de la patience pendant que vous tournez soigneusement d'environ 1/5 de tour, appuyez, faites pivoter et continuez. Cela forme le disque plat et mince, tout en permettant aux enroulements d'extrémité de s'empiler. Vous remarquerez peut-être que mon enroulement à 4 lobes a des "jambes" droites mais les connexions intérieures et extérieures ne sont pas rondes. Cela était censé faciliter leur empilement. Ça n'a pas si bien marché. Si je le faisais à nouveau, je ferais suivre des chemins circulaires aux enroulements intérieurs et extérieurs.
Après l'avoir aplati et mince, et les bords emballés, j'ai enroulé un ruban plat autour du bord pour le compacter, et un autre en haut, en bas et autour de chaque jambe, puis à celui d'à côté également. Une fois cela fait, vous pouvez retirer les fils d'attache et passer au plus petit bac de pressage, puis revenir à l'étau et le presser aussi fin et plat que possible. Une fois qu'il est plat, retirez-le de la cuve de la presse. Au lieu du processus complexe consistant à cirer et à enduire soigneusement des moules comme celui-ci avec des composés antiadhésifs, j'utilise généralement quelques couches de film étirable (de la cuisine). Posez quelques couches au fond du moule et posez la fibre de verre sur le film étirable. Ajoutez ensuite le tube de montage du stator, qui s'adapte au sommet de la cuve de formage vert clair, mais avec la couche de film étirable et de fibre de verre entre les deux. Remettez ensuite l'enroulement du stator en place pour abaisser à la fois le film étirable et la fibre de verre et verrouillez le tube de montage du stator en place. Revenez ensuite à l'étau et appuyez à nouveau à plat. Une fois qu'il s'intègre bien dans la baignoire, avec le film étirable et la fibre de verre pris en sandwich, puis un tissu en fibre de verre est ajouté (avec un trou au centre pour le tube de montage du stator).
Maintenant, il est prêt à verser le matériau de liaison, l'époxy ou la résine polyester sont couramment utilisés. Avant cela, une préparation minutieuse est importante car une fois que vous avez commencé ce processus, vous ne pouvez pas vraiment vous arrêter. J'ai utilisé une plaque de base imprimée en 3D que j'avais déjà faite, avec un trou de 1" au centre et une plaque plate autour. J'ai utilisé un morceau de 16" de tube en aluminium de 1", que le tube de montage du stator s'adapterait et serait maintenu perpendiculairement à la plaque plate. La cuve de formage verte, l'enroulement du stator et le tube de montage du stator ont été glissés vers le bas pour s'asseoir sur la plaque plate. Avant de mélanger l'époxy, j'ai d'abord préparé 4 morceaux de film rétractable et j'ai soigneusement placé un 5ème morceau sur le vert foncé formant un beignet, de sorte qu'il aurait le moins de plis sur la face contre l'enroulement du stator. Après avoir mélangé l'époxy et l'avoir versé sur le tissu en fibre de verre, j'ai soigneusement posé le film étirable autour du tube de 1 "et placé le vert formant un anneau au-dessus. J'avais également préparé quelques vieux disques de frein, qui donnaient du poids, et je m'asseyais bien sur le beignet vert en formation. Après cela, j'ai mis un pot inversé sur les disques de frein, et sur le pot j'ai empilé environ 100 livres de trucs. Je l'ai laissé pendant 12 heures et il est sorti d'environ 4 à 6 mm d'épaisseur.
Étape 4: Tests et capteurs
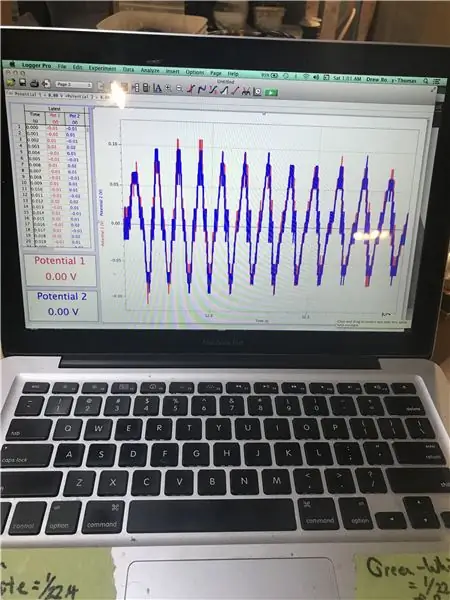
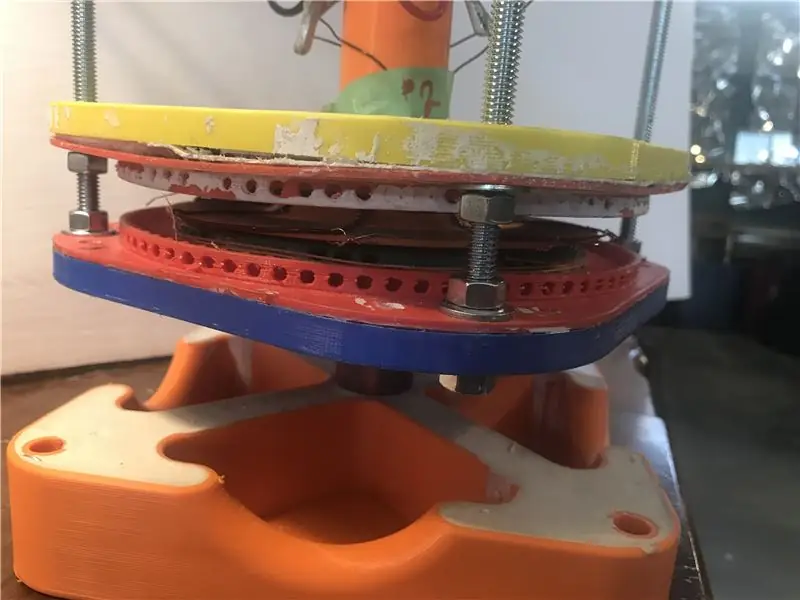
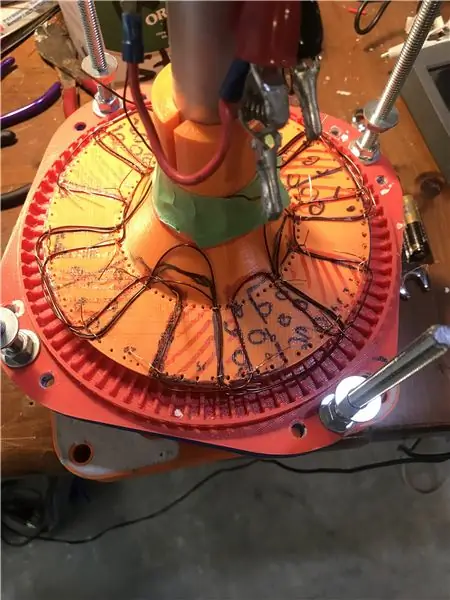
Il existe un certain nombre d'entrées et de sorties mesurables de l'alternateur, et les mesurer toutes en même temps n'est pas facile. J'ai beaucoup de chance d'avoir des outils de Vernier qui rendent cela beaucoup plus facile. Vernier fabrique des produits de niveau éducatif, non certifiés pour un usage industriel, mais très utiles pour les expérimentateurs comme moi. J'utilise un enregistreur de données Vernier, avec une variété de capteurs plug and play. Sur ce projet, j'utilise des sondes de courant et de tension à effet hall pour mesurer la sortie de l'alternateur, un capteur optique pour donner la vitesse de l'alternateur et une cellule de charge pour mesurer le couple d'entrée. Tous ces instruments sont échantillonnés environ 1000 fois par seconde et enregistrés sur mon ordinateur portable, en utilisant l'enregistreur Vernier comme dispositif d'intercommunication AD. Sur mon ordinateur portable, le logiciel associé peut exécuter des calculs en temps réel basés sur les entrées, en combinant les données de couple et de vitesse pour donner la puissance de l'arbre d'entrée en temps réel en watts et les données de sortie en temps réel en watts électriques. Je n'en ai pas fini avec ces tests, et l'avis de quelqu'un qui a une meilleure compréhension serait utile.
Un problème que j'ai est que cet alternateur est vraiment un projet parallèle, et donc je ne veux pas y passer trop de temps. Dans l'état actuel des choses, je pense que je peux l'utiliser pour une charge contrôlable pour ma recherche VAWT, mais j'aimerais éventuellement travailler avec des gens pour l'affiner, afin qu'elle corresponde efficacement à ma turbine.
Lorsque j'ai commencé la recherche VAWT il y a environ 15 ans, j'ai réalisé que tester les VAWT et d'autres moteurs principaux est plus complexe que la plupart des gens ne le pensent.
Un problème principal est que l'énergie représentée dans un fluide en mouvement est exponentielle par rapport à sa vitesse de mouvement. Cela signifie que lorsque vous doublez la vitesse d'un flux, l'énergie contenue dans le flux augmente 8x (elle est au cube). C'est un problème, car les alternateurs sont plus linéaires et en général, si vous doublez le régime d'un alternateur, vous obtenez environ 2 fois plus de watts.
Cette inadéquation fondamentale entre la turbine (dispositif de récupération d'énergie) et l'alternateur (puissance de l'arbre à puissance électrique utile) rend difficile le choix d'un alternateur pour une éolienne. Si vous choisissez un alternateur adapté à votre éolienne qui générera le plus d'énergie disponible à partir de vents de 20 km/h, il ne commencera probablement même pas à tourner avant 20-25 km/h car la charge sur l'éolienne de l'alternateur sera trop élevée.. Avec cette correspondance d'alternateur, une fois que le vent est supérieur à 20 km, non seulement la turbine ne captera qu'une fraction de l'énergie disponible dans le vent à plus grande vitesse, mais la turbine peut survitesse et être endommagée car la charge fournie par l'alternateur n'est pas élevée assez.
Au cours de la dernière décennie, une solution est devenue plus économique en raison de la baisse du prix de l'électronique de commande. Au lieu d'essayer de faire correspondre une plage de vitesses, le concepteur calcule la vitesse maximale à laquelle l'appareil est censé fonctionner et choisit un alternateur en fonction de la quantité d'énergie et de la vitesse idéale de la turbine à cette vitesse, ou un peu au-dessus. Cet alternateur, s'il est connecté à sa charge, fournirait normalement trop de couple à basse vitesse, et la turbine surchargée ne captera pas toute l'énergie qu'elle pourrait avoir si elle était correctement chargée. Pour créer la charge appropriée, un contrôleur est ajouté qui déconnecte momentanément l'alternateur de la charge électrique, permettant à la turbine d'accélérer à la bonne vitesse, et l'alternateur et la charge sont reconnectés. C'est ce qu'on appelle le MPPT (Multi Power Point Tracking). Le contrôleur est programmé de telle sorte que lorsque la vitesse de la turbine change (ou que la tension de l'alternateur augmente), l'alternateur est connecté ou déconnecté, un millier de fois par seconde environ, pour correspondre à la charge programmée pour cette vitesse ou cette tension.
Conseillé:
Impression de circuits imprimés personnalisés avec une imprimante 3D : 7 étapes (avec photos)
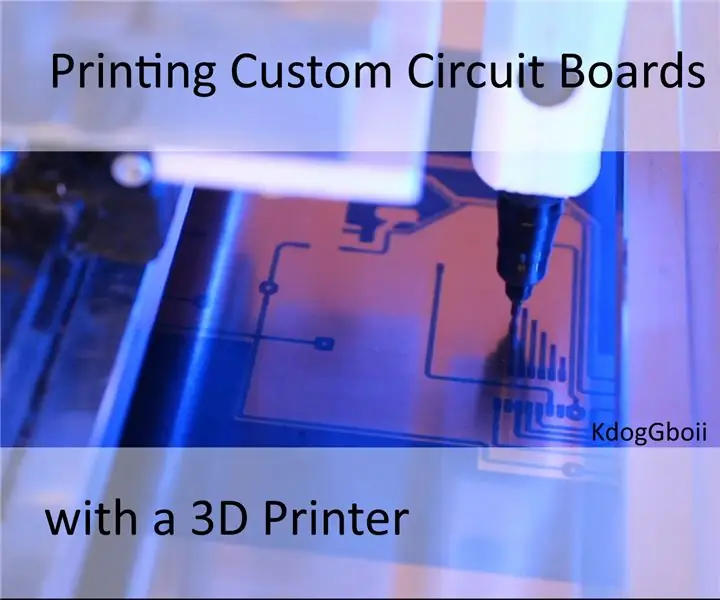
Impression de circuits imprimés personnalisés avec une imprimante 3D : Si ce n'est pas la première fois que vous voyez une imprimante 3D, vous avez probablement entendu quelqu'un dire quelque chose du genre : 1) Acheter une imprimante 3D2) Imprimez une autre imprimante 3D3) Renvoyez l'original 3D imprimante4) ????????5) ProfitMaintenant, n'importe qui w
Faire des circuits imprimés avec des lasers : 4 étapes (avec photos)
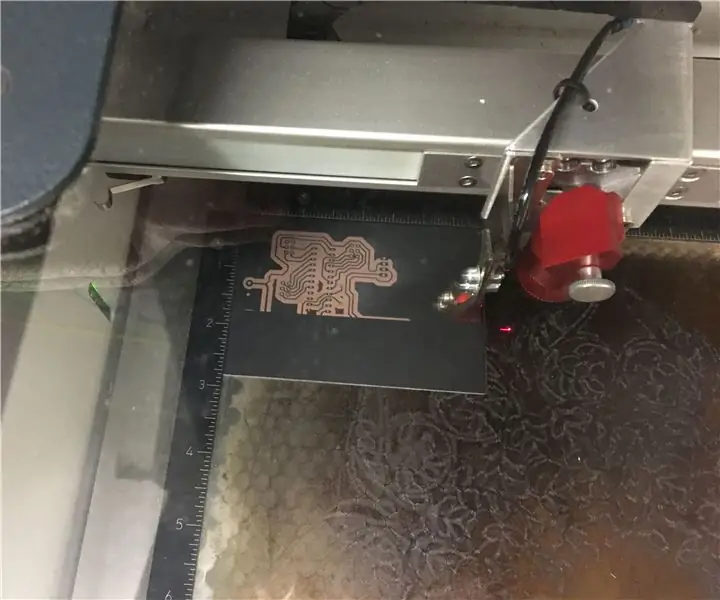
Fabriquer des circuits imprimés avec des lasers : Un circuit imprimé fait maison n'est aussi bon que le masque que vous y mettez. Quelle que soit la méthode que vous utilisez pour effectuer la gravure proprement dite, vous devez toujours coller une image de votre circuit sur la carte et vous assurer qu'elle laisse des traces nettes, propres et solides derrière
Conception de circuits imprimés avec des étapes simples et faciles : 30 étapes (avec images)
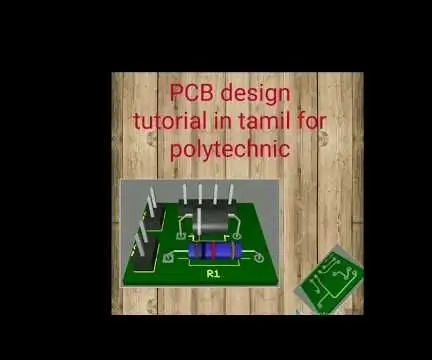
Conception de circuits imprimés avec des étapes simples et faciles : BONJOUR AMIS Son tutoriel très utile et facile pour ceux qui veulent apprendre la conception de circuits imprimés, commençons
Auto-exciter un alternateur sans générateur de courant continu, batterie de condensateurs ou batterie : 5 étapes (avec photos)
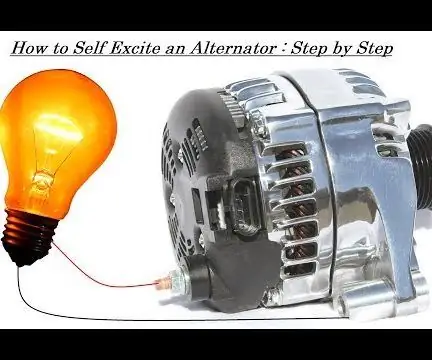
Auto-exciter un alternateur sans générateur de courant continu, batterie de condensateurs ou batterie : Salut ! alternateur avec une batterie de 12 volts mais à la place, il s'allumera tout seul pour que vous
Création de circuits imprimés avec une imprimante JET D'ENCRE : 8 étapes (avec photos)
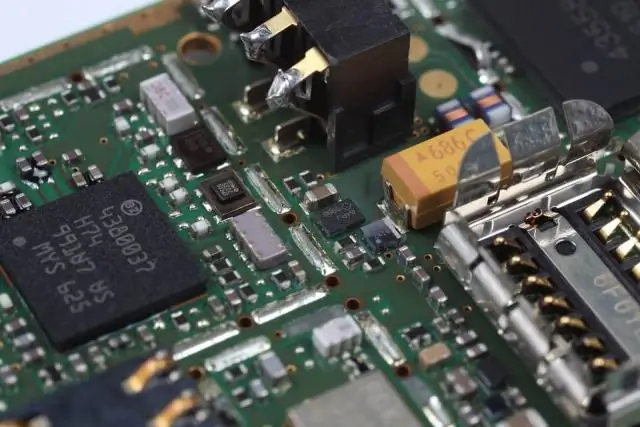
Création de cartes de circuits imprimés avec une imprimante JET D'ENCRE : Lorsque j'ai commencé à chercher comment graver mes propres cartes de circuits imprimés, chaque Instructable et tutoriel que j'ai trouvé utilisaient une imprimante laser et repassaient le motif d'une manière ou d'une autre. Je ne possède pas d'imprimante laser mais j'ai une encre bon marché