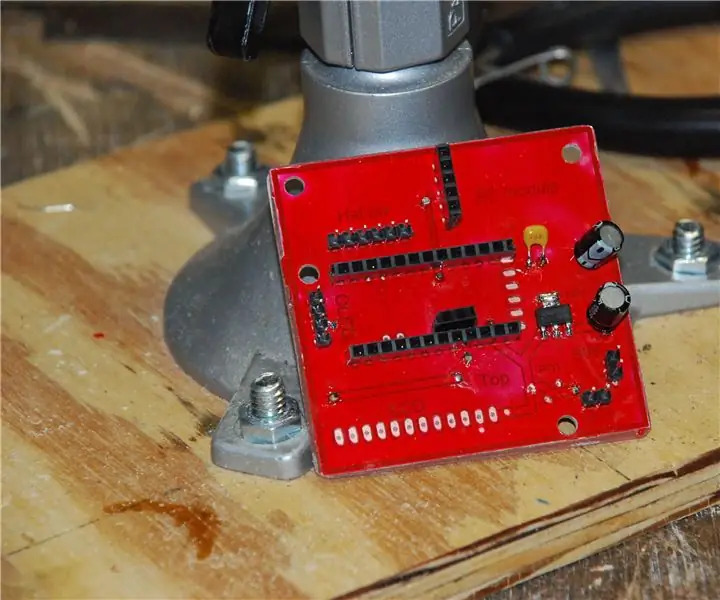
Table des matières:
- Étape 1: Matériel nécessaire
- Étape 2: Concevez votre circuit imprimé
- Étape 3: Sortir les Gerbers
- Étape 4: Conversion d'images CAM
- Étape 5: Édition d'images
- Étape 6: Imprimez la feuille maître
- Étape 7: Préparez le panneau enduit de cuivre
- Étape 8: Enregistrez les images de cuivre
- Étape 9: Transfert de toner
- Étape 10: gravez votre planche
- Étape 11: appliquer le masque de soudure
- Étape 12: percez votre planche
- Étape 13: Couper à la taille finale
- Étape 14: Remplissez votre tableau
2025 Auteur: John Day | [email protected]. Dernière modifié: 2025-01-23 14:46
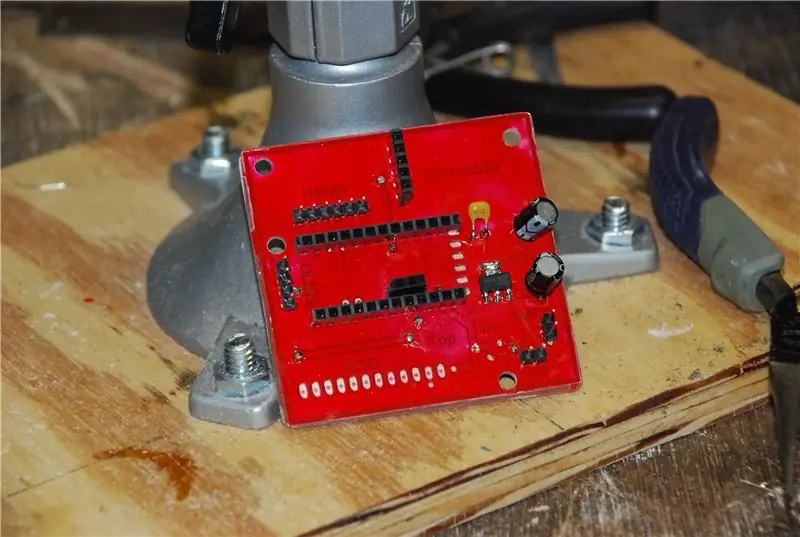
Ce qui suit décrit le processus par lequel je crée des circuits imprimés pour PC à usage unique et prototype. Il est écrit pour une personne qui a créé ses propres tableaux dans le passé et qui est familière avec le processus général.
Toutes mes étapes peuvent ne pas être optimales pour votre situation. J'ai développé ce processus par essais et erreurs en incorporant des techniques provenant de diverses sources. S'il vous plaît, prenez tout ce qui fonctionne pour vous et jetez ce qui ne fonctionne pas.
Une note de production: je suis de la vieille école et j'apprends mieux à partir d'instructions écrites et d'images, ils forment l'essentiel de cette instructable, j'ai inclus quelques vidéos pour certaines des étapes les plus complexes.
Étape 1: Matériel nécessaire
La liste suivante est longue mais, si vous fabriquez déjà vos propres cartes de circuits imprimés, vous pouvez avoir certains de ces éléments. La plupart des autres, à l'exception de la boîte d'exposition aux UV, peuvent être achetées en ligne.
Tu auras besoin de:
- Matériau PCB recouvert de cuivre
- Logiciel de conception de circuits imprimés (j'utilise le logiciel gratuit Eagle).
- Traducteur de fichiers Gerber - convertit les fichiers Gerber au format graphique Gerber2PDF
- Logiciel d'édition graphique (PhotoShop)
- Imprimante laser avec toner adapté à la technique de transfert de toner.
- Papier glacé pour imprimante laser (Agrafes #633215).
- Film transparent pour imprimantes laser (C-Line no60837).
- Bâton de colle hydrosoluble, colle cyanoacrylate, ruban de peintre.
- Fil floral fin (~ 26 gage) et épingles droites.
- Outils à main pour couper, façonner et percer les cartes de circuits imprimés.
- Un fer à repasser standard.
- Matériel de nettoyage des circuits imprimés (essuie-tout, éponges, détergent, Bar Keepers Friend, solvants).
- Liquide de chlorure ferrique (40%).
- Acide citrique, en poudre (nuts.com).
- Old CrockPot avec revêtement en céramique ou en verre (pas en métal).
- Qt. taille sac de congélation en plastique avec fermeture à glissière.
- Peinture de masque de soudure durcissable aux UV (ebay ou amazon).
- Coffret d'exposition aux UV (Maison ?).
Étape 2: Concevez votre circuit imprimé

J'utilise la version gratuite d'Eagle car les tailles de planches sont assez modestes et limitées à 2 côtés. Je suis généreux avec les tailles de mes traces et les distances entre elles (taille de trace de 24 mil min et 15 mil entre).
La plupart de mes composants passent par le trou, mais j'utilise occasionnellement des CMS ou une combinaison. J'essaie d'acheminer les traces vers les en-têtes de broches au bas de la carte. Je n'utilise pas de trous traversants plaqués donc j'ajoute des vias supplémentaires reliant les traces supérieures au fond où le composant ne peut pas être soudé des deux côtés. Ceux-ci seront remplis de petits morceaux de fil mince soudés en place.
Lorsque j'ai terminé la mise en page et le routage, j'ajoute plusieurs grands vias près des coins de la carte pour servir de trous de montage et d'indicateurs d'enregistrement pour les cartes à 2 faces.
Lorsque vous avez terminé, je vous suggère d'imprimer une grande copie de la carte pour référence dans le placement des composants et le marquage des trous.
J'utilise le processeur CAM d'Eagles pour créer les images de la carte qui seront imprimées sur papier pour le cuivre et sur film transparent laser pour les masques de soudure.
Étape 3: Sortir les Gerbers
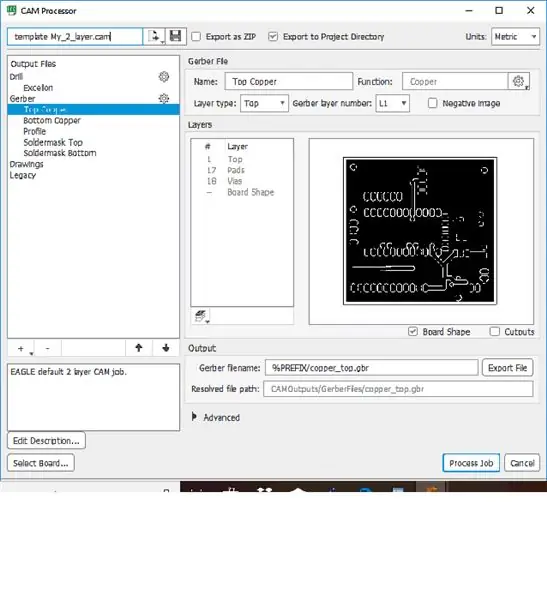
J'aime utiliser des polygones de remplissage pour créer un plan au sol en bas et V+ en haut, donc je n'imprime pas directement les images de la carte mais j'utilise la sortie CAM d'Eagle. Je n'utilise pas de pochoirs en pâte à souder depuis que je soude à la main les quelques composants SMD que j'utilise sur mes cartes.
Pour faciliter la création des images CAM, j'ai créé un modèle personnalisé pour la sortie CAM simple et double face contenant les fichiers de sortie dont j'ai besoin. J'ajoute toujours la forme de la planche aux Gerbers en cuivre mais pas aux masques.
Je place généralement les fichiers Gerber dans le dossier Projet lors du traitement du travail afin qu'ils puissent être consultés si nécessaire à une date ultérieure.
Étape 4: Conversion d'images CAM
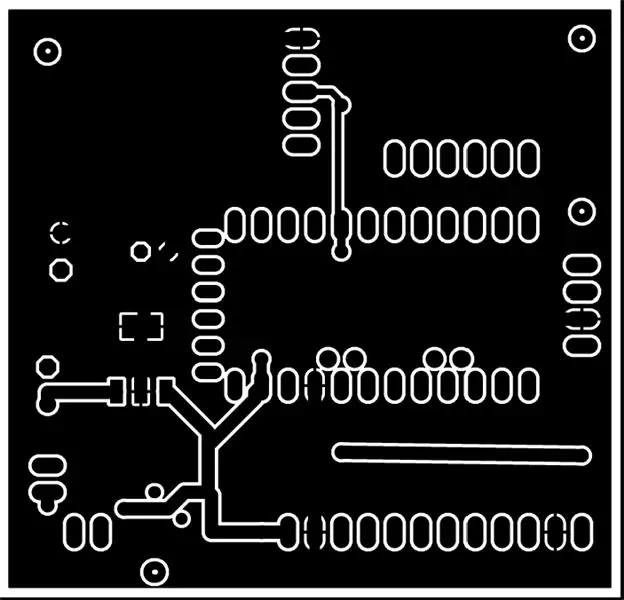
La création de la sortie à l'aide du processeur CAM d'Eagle introduit plusieurs obstacles à la création des masques de cuivre et de soudure.
- Vous devez convertir les fichiers Gerber en images imprimables.
- Le processeur Cam supprime les indicateurs de composant et de trou de passage.
La première étape consiste à convertir les fichiers Gerber en une sorte de fichier image que je peux ensuite éditer et imprimer. J'utilise un utilitaire nommé Gerber2PDF Gerber2PDF link.
Le fichier.exe téléchargé est placé dans le répertoire Eagle CAM. Je transfère ensuite les fichiers Gerber que je souhaite convertir du répertoire Project vers le répertoire CAM avant d'exécuter Gerber2PDF à partir de la ligne de commande Windows.
Voir la documentation Gerber2pdf pour la syntaxe pour sélectionner et convertir des fichiers spécifiques.
J'ai inclus le fichier texte que j'utilise pour exécuter le processus gerber2pdf que vous devez télécharger.
N'hésitez pas à modifier ce fichier en fonction de vos besoins. Coupez les commandes et collez-les dans l'utilitaire de ligne de commande DOS pour convertir les Gerbers.
Une fois que j'ai des fichiers PDF individuels pour chaque masque de cuivre et de soudure dont j'ai besoin, j'aborde le problème des trous manquants dans les composants de la carte, les vias et les trous d'enregistrement. J'utilise PhotoShop pour importer les PDF et éditer les fichiers de cuivre pour ajouter les trous nécessaires sous forme de petits cercles blancs remplis.
Étape 5: Édition d'images

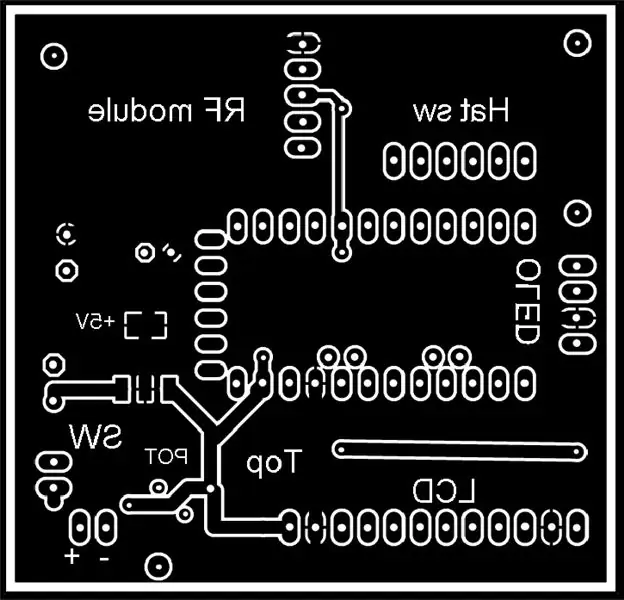
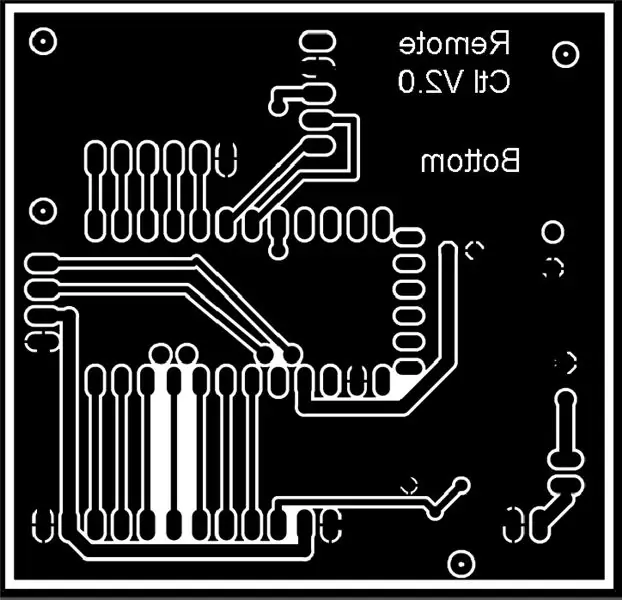
J'utilise PhotoShop pour importer les PDF et éditer les fichiers de cuivre pour ajouter les trous nécessaires sous forme de petits cercles blancs remplis. Vous pouvez utiliser votre propre logiciel de conversion et d'édition graphique en suivant les instructions ci-dessous.
Modifiez les fichiers PDF pour ajouter des marques de trous de repérage (voir Flèches) sur les deux côtés des planches à 2 faces. Gardez les trous de repérage très petits pour rendre le repérage plus précis, mais suffisamment grands pour voir lorsque vous imprimez les images en cuivre. Je n'ajoute que les trous des composants en haut car je vais percer principalement de ce côté. Notez que l'image en cuivre supérieure doit être retournée horizontalement (miroir) à ce stade afin que les pastilles correspondent après avoir été gravées. Vous pouvez également ajouter du texte imprimé à ce stade. Assurez-vous que tout texte que vous ajoutez apparaît en miroir sur le cuivre supérieur et inférieur afin qu'ils soient correctement transférés sur votre tableau (voir les exemples ci-dessus).
Copiez et collez chaque image de cuivre et de masque dans une feuille maître vierge pleine page (à la même résolution que les PDF) qui sera imprimée sur votre imprimante laser. Vous pouvez également souhaiter ajouter un texte d'identification du tableau à la feuille maîtresse.
Le fait de placer plusieurs copies des images de cuivre sur la feuille maître économisera du papier et permettra des erreurs dans le processus de transfert de toner. Faites de même pour les fichiers de masques de soudure en ajoutant au moins 2 copies de chaque masque, ils seront combinés plus tard.
Étape 6: Imprimez la feuille maître
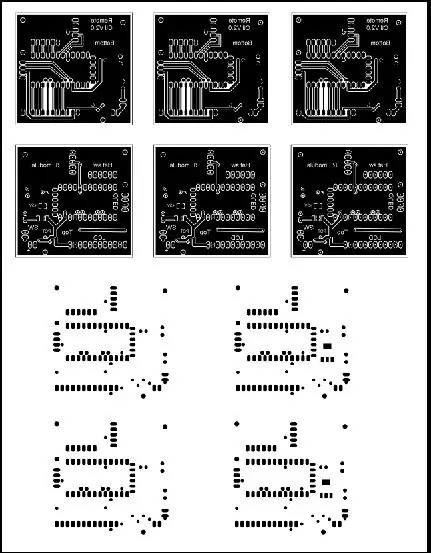
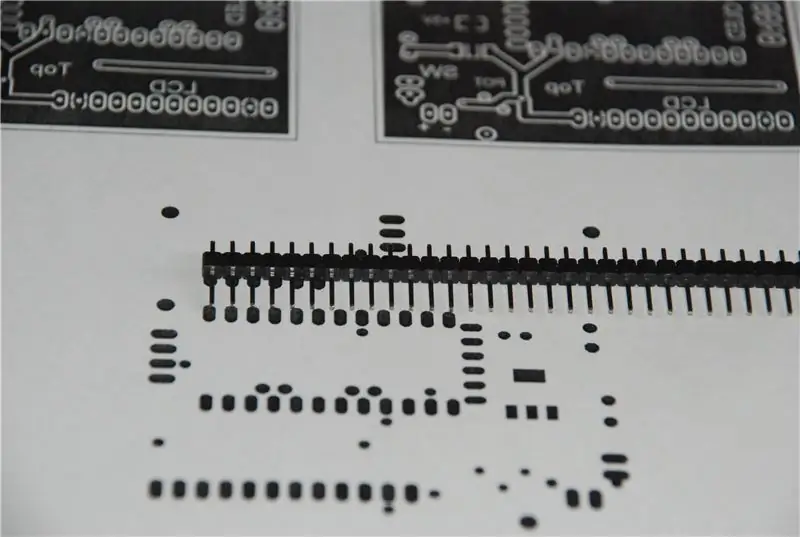
Les images de cuivre de la feuille maîtresse imprimées seront transférées sur les PCB préparés à l'aide du transfert thermique du toner. J'utilise du papier brillant laser couleur Premium de Staples (#633215) pour le processus de transfert. Il est fiable, peu coûteux et clairement visible (pas comme les pages de magazine). Il accepte le toner laser avec peu ou pas d'erreurs, transfère rapidement le toner sur le cuivre et se libère proprement en quelques minutes de trempage dans l'eau tiède. Si des masques de soudure doivent être générés, au moins deux copies de chaque masque sont imprimées sur un film transparent pour imprimante laser (C-Line n°60837).
Avant d'imprimer sur du papier glacé ou des transparents, imprimez une copie des images sur du papier ordinaire. Cette copie sera utilisée pour le dimensionnement de la carte et l'alignement du cuivre recto-verso. C'est une bonne idée de vérifier les distances correctes entre les plaquettes pour SMD et les autres composants (voir photo ci-dessus). Faites cela pour les images de cuivre et de masque. J'ai fait des erreurs dans le processus de copier-coller plus d'une fois et, après avoir gravé, masqué et percé le PCB, je n'ai pas pu remplir les cartes finies
Étape 7: Préparez le panneau enduit de cuivre
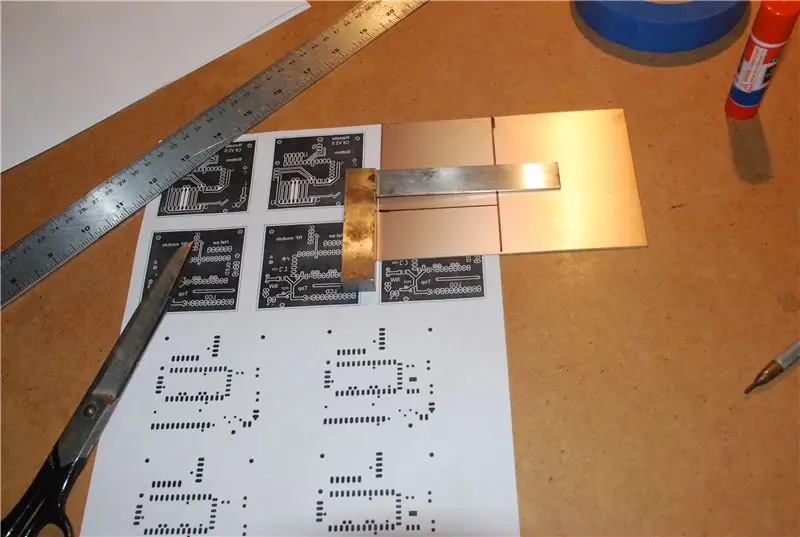
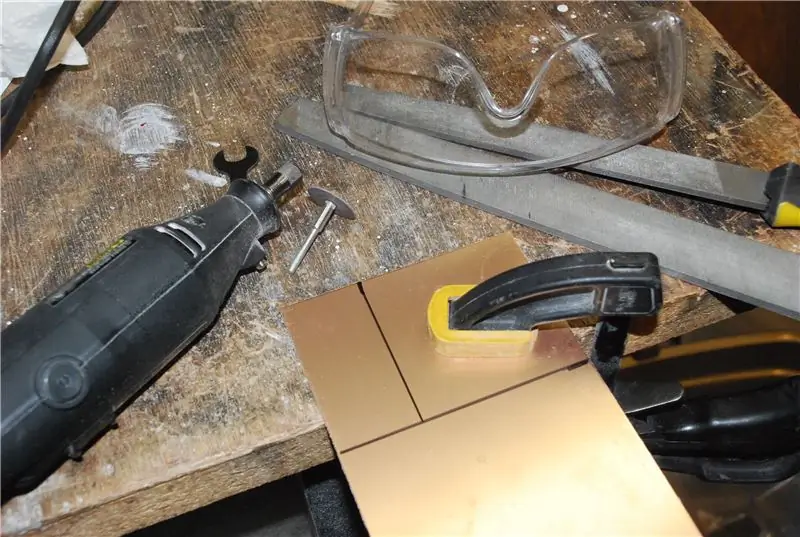
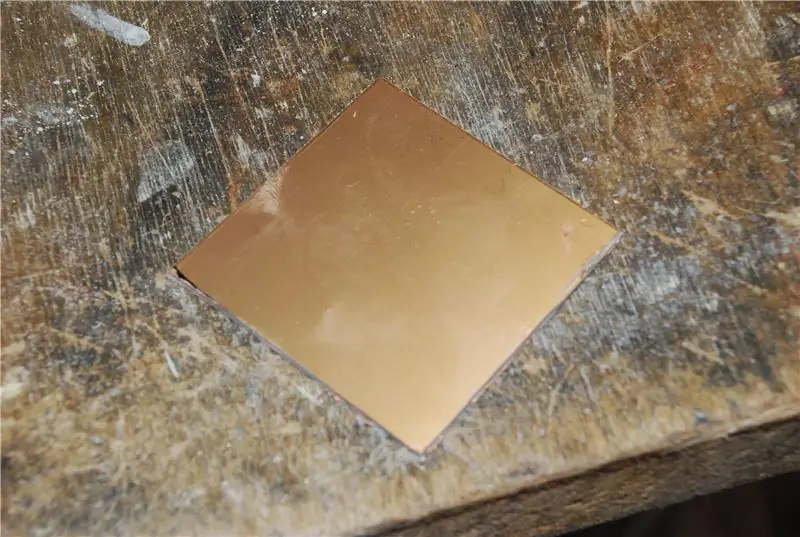
Les planches de cuivre (simple ou double face) sont coupées à une forme grossière (~ un demi-pouce tout autour) en utilisant une image de l'impression sur papier ordinaire comme guide (j'utilise un outil Dremel avec une meule à tronçonner).
Les bords sont limés lisses pour les aplatir et les coins arrondis. Je lime ensuite les bords supérieur et inférieur à un angle de 45 degrés pour éliminer les bavures ou la netteté (vérifiez avec votre doigt après le limage).
L'étape suivante consiste à nettoyer les planches pour éliminer toute huile ou graisse. Un détergent et de l'eau chaude feront l'affaire. Enfin pour enlever l'oxydation et créer une surface qui acceptera le transfert et sera facile à souder, je saupoudre le cuivre d'un peu de pâte "Bar Keepers Friend" et frotte doucement avec une éponge humide, puis rince avant de sécher avec un essuie-tout.
Si les planches sont recto-verso, les images devront être enregistrées exactement. J'ai trouvé que le meilleur moyen pour moi était de coller une copie sur papier ordinaire de l'image en cuivre du bas sur un côté du tableau (paradoxalement ce sera le haut) et de percer soigneusement les centres des vias d'enregistrement avec une perceuse #70. Une perceuse à colonne avec un étau pour tenir le foret fonctionne bien.
Étape 8: Enregistrez les images de cuivre
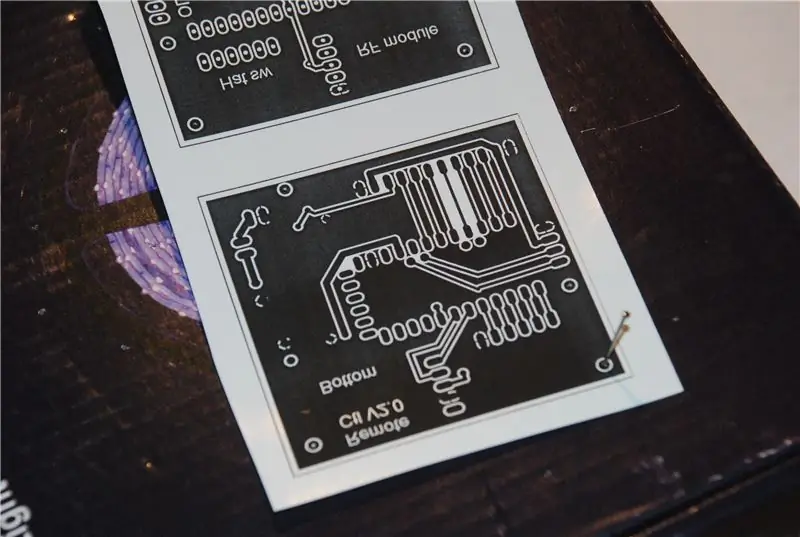
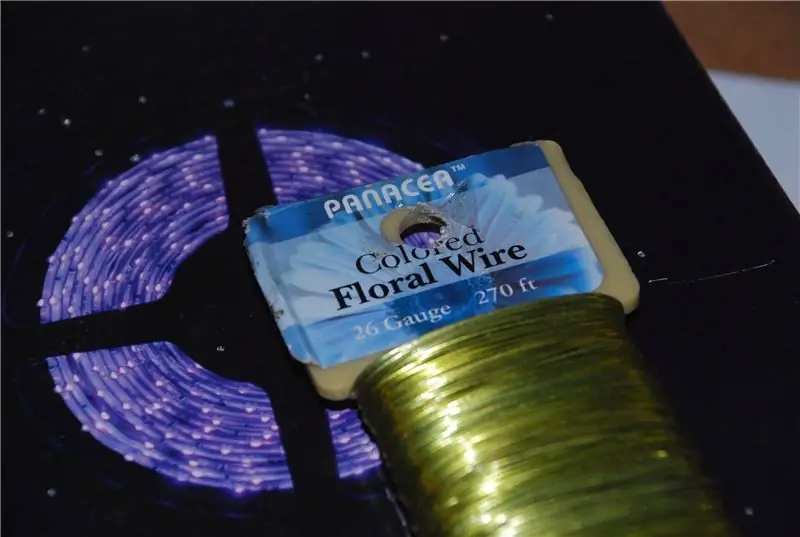
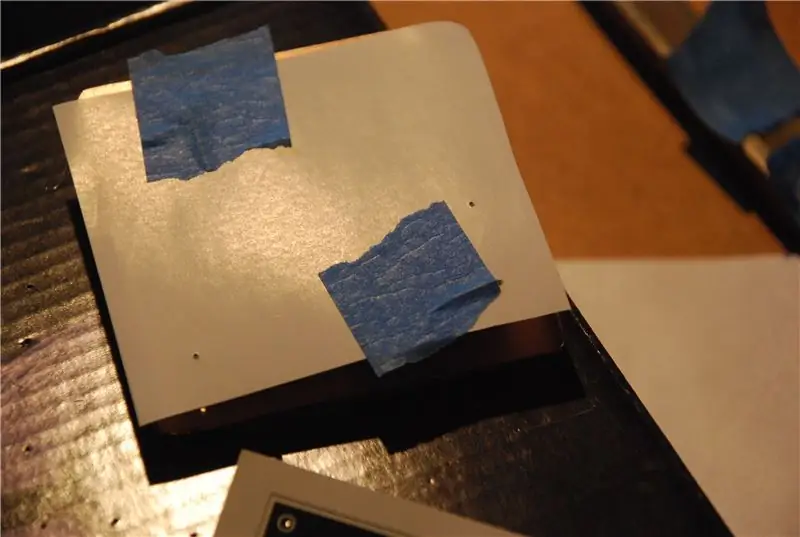
Pour les panneaux simple face, le processus est assez simple. Il suffit de découper une copie de l'image en cuivre dans le papier glacé et de la coller délicatement sur le côté de l'image du tableau vers le bas à l'aide de ruban de peintre (ruban bleu). Je place ensuite la planche sur un morceau de contreplaqué recouvert de 2 couches de papier essuie-tout et recouvre la planche de deux autres couches.
Pour les planches à deux faces, le processus est plus compliqué. Je nettoie d'abord les trous d'enregistrement dans le tableau avec une épingle droite. L'étape suivante consiste à découper une image en cuivre supérieure et une image inférieure dans le papier glacé et à percer exactement le centre de tous les trous d'enregistrement avec une épingle droite.
Ensuite, j'ai coupé des morceaux de fil de fleuriste ou d'artisanat minces (~ 26 gages) assez petits pour passer à travers les trous d'enregistrement (environ 3/4 de pouce de longueur). Je passe ce fil d'abord à travers l'arrière de l'un des trous d'enregistrement dans le papier supérieur, puis à travers le tableau. À ce stade, je plie le fil et j'utilise un petit morceau de ruban adhésif pour éviter que le fil ne tombe lorsque je retourne la planche. Enfin, poussez-le par l'avant des trous de papier inférieurs de sorte que les images soient face au cuivre.
Chaque fil est ensuite plié pour maintenir les papiers et le carton ensemble. Lorsque tous les trous sont terminés, suivez la procédure pour le panneau simple face ci-dessus.
Étape 9: Transfert de toner
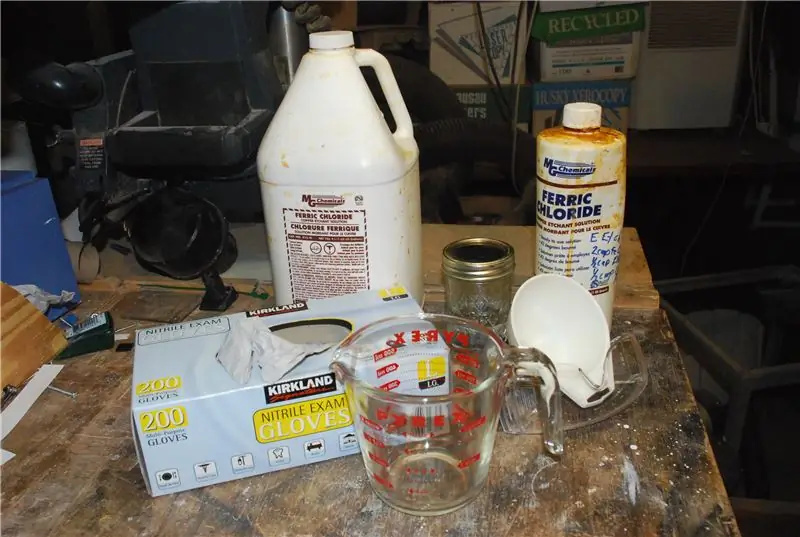
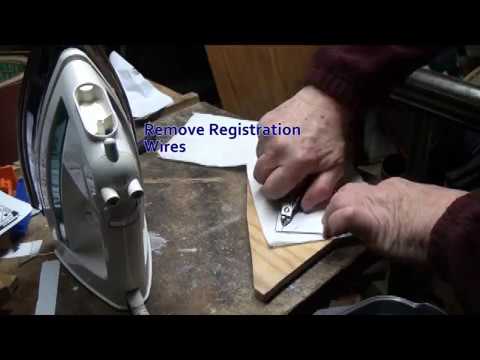
Maintenant que la carte est prête pour le transfert de toner. Cette vidéo du processus de transfert peut rendre les instructions suivantes plus claires.
J'applique un fer à repasser à linge sec réglé juste en dessous de la température la plus élevée pour coller le papier sur la planche à l'aide de la pointe pointue du fer. Veillez à placer la pointe entre les fils sur les planches à double face et à clouer les deux côtés afin que le papier ne se sépare pas de la planche lors de la manipulation. Attention, la planche devient brûlante. Sur les planches recto-verso, je coupe les fils au ras d'un côté, puis je tire les autres extrémités à travers le papier et le carton avant l'étape suivante.
Retirez tout ruban adhésif avant d'appliquer le fer avec une pression de chaque côté pendant environ 1 minute sans mouvement, sauf si la planche est trop grande pour une couverture complète du fer. Cela fera tremper la planche et collera le toner. Pour assurer le transfert du toner, j'enlève la serviette en papier sur le dessus et je tiens le bord du fer à un angle de 45 degrés par rapport à la planche, puis j'applique une pression tout en me déplaçant sur la planche. Je le fais de chaque côté au moins plusieurs fois. À ce stade, vous devriez voir une légère image du toner au dos du papier.
L'étape suivante consiste à faire tremper la planche et le papier dans l'eau jusqu'à ce que le papier flotte. Je frotte généralement doucement le dos du papier pour enlever le revêtement d'argile pour faciliter le processus et décoller doucement le papier après quelques minutes, un léger brossage sous l'eau avec une brosse à poils doux ou vos doigts assureront le revêtement d'argile du brillant le papier est retiré du cuivre avant la gravure. L'eau se troublera avec des particules d'argile microscopiques.
Séchez, inspectez et retouchez avec un marqueur Sharpee et un couteau si nécessaire. Si une réparation importante est nécessaire à ce stade, vous voudrez peut-être retirer le toner et en réappliquer avant de graver (assurez-vous de nettoyer à nouveau la carte).
Étape 10: gravez votre planche
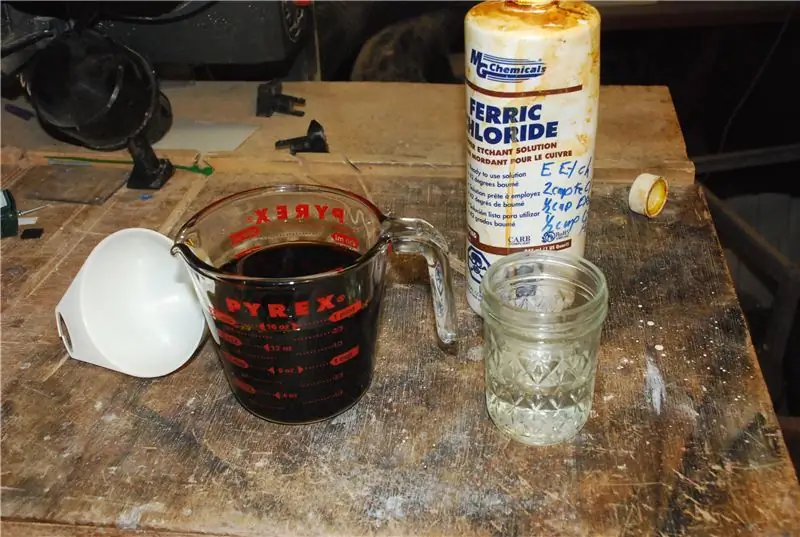
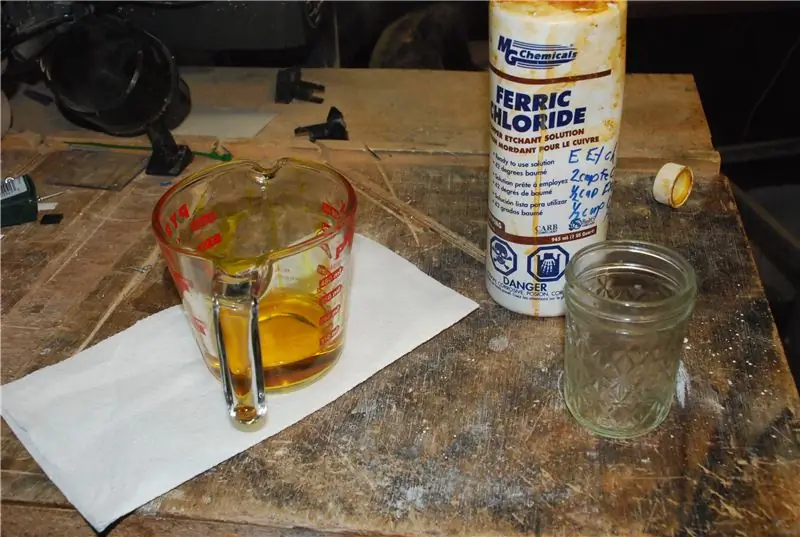
Mon procédé de gravure est peut-être le moins conventionnel. Il nécessite une mijoteuse remplie à moitié avec de l'eau réglée sur le réglage élevé et chauffée (au moins 1 heure) jusqu'à ce qu'elle soit chaude. La prochaine étape inhabituelle consiste à graver la planche à l'intérieur d'un sac de congélation de bonne qualité avec une fermeture à glissière. Enfin, j'utilise un Edinburgh Etch à base de chlorure ferrique qui est préparé comme suit: Obtenez de l'acide citrique sec (également connu sous le nom de sel aigre souvent utilisé comme conservateur alimentaire} à partir d'une source en ligne (NUTS.com) ou locale. Préparez une solution d'acide citrique en dissolvant 1/4 tasse de poudre dans 3/4 tasse d'eau tiède, mettre de côté pour refroidir. Pour faire le décapant, ajouter 1/2 tasse de cette solution à 2 tasses de solution de chlorure ferrique à 40%. Ajouter l'acide C'est le décapage d'Edimbourg. La solution de décapage est deux fois plus rapide que le décapage au chlorure ferrique ordinaire et ne se bouchera pas et ne formera pas de boue.
AVERTISSEMENT: N'utilisez PAS de décapant à base de peroxyde d'hydrogène avec cette méthode. Il génère de l'hydrogène gazeux qui est explosivement inflammable et fera éclater le sac.
Assurez-vous d'utiliser des gants et des vêtements de protection (un tablier imperméable) avant de mélanger ou d'utiliser le décapant. Il tachera et mangera encore les tissus et la peau ! Ouvrez le sac avec le circuit imprimé, j'ajoute généralement de l'eau dans le sac d'abord pour tester les fuites, puis je vide cette eau. Ajoutez suffisamment d'agent de gravure pour graver votre circuit, ne remplissez pas trop, vous pouvez toujours en ajouter plus tard mais cela peut être salissant. Vous constaterez que vous utiliserez moins de décapant qu'avec d'autres méthodes et comme il est jeté après utilisation, le décapant est toujours frais. Pressez autant d'air que possible hors du sac sans renverser, puis fermez-le solidement de manière à ce qu'il soit étanche à l'air.
Éteignez la mijoteuse. Placez maintenant le sac dans l'eau chaude jusqu'à ce que la planche soit immergée et plate. Vérifiez la progression de la gravure au moins toutes les 5 minutes jusqu'à ce que tout le cuivre exposé soit complètement nettoyé (le sac transparent permet l'inspection). Il n'y a pas besoin d'agitation constante puisque l'Edinburgh Etch ne se bouche pas. Une fois terminé (pas de cuivre visible), retirez le sac et ouvrez-le soigneusement, jetez le décapant dans un conteneur à déchets, ne le versez pas dans les égouts ! J'utilise un grand récipient en plastique avec une large ouverture que j'apporte à ma collecte communautaire de déchets dangereux pour le jeter.
Rincez le sac à l'eau, jetez-le également dans votre poubelle et retirez la planche avant de jeter le sac. Rincez la planche sous l'eau courante pour la nettoyer avant de retirer votre équipement de protection.
Retirez le toner comme d'habitude en l'essuyant avec une serviette en papier trempée dans de l'acétone ou du diluant pour laque.
Étape 11: appliquer le masque de soudure
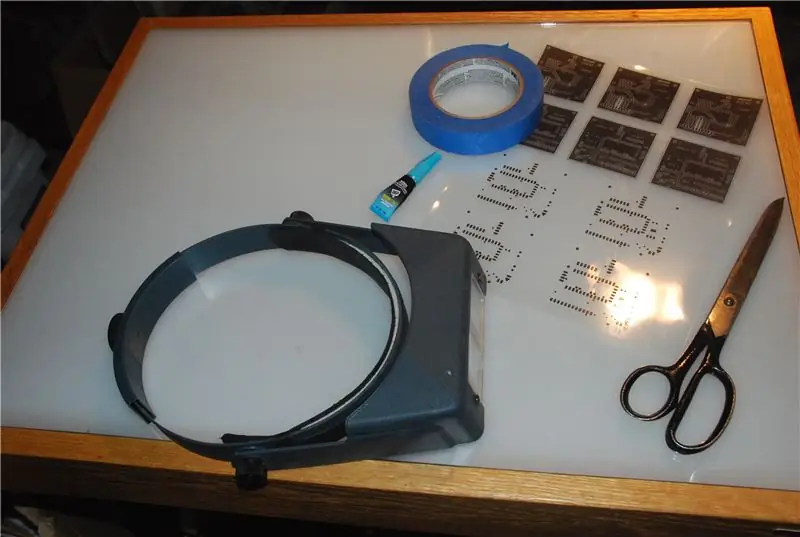
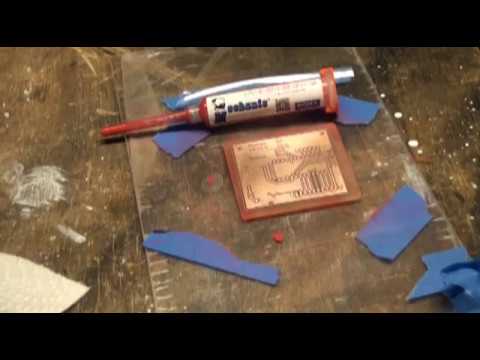
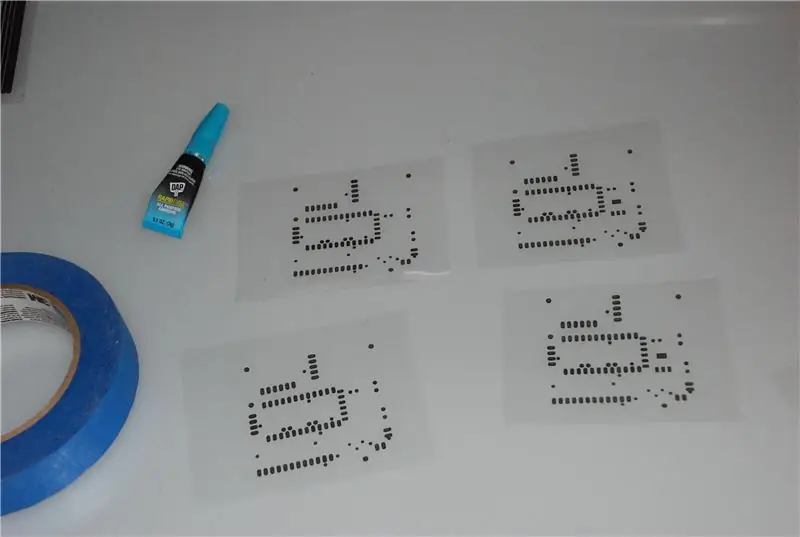
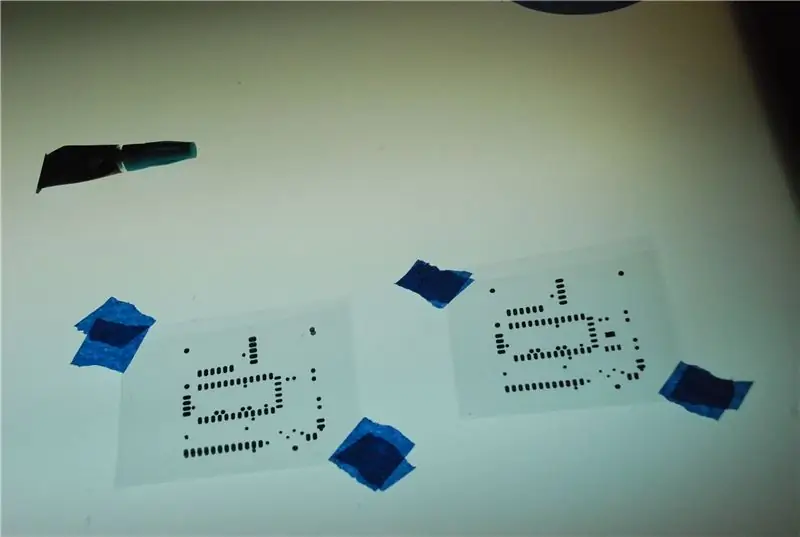
Une fois la planche sèche, il est temps d'appliquer un masque de soudure. Il s'agit d'une étape facultative, mais elle aidera à protéger le cuivre de l'oxydation, aura un aspect plus professionnel et améliorera le placement des composants SMD.
Encore une fois, étant donné que la description de ce processus ne transmet pas toutes les nuances nécessaires au succès, j'ai inclus une vidéo.
Le masque en film est difficile à trouver et très cher, j'utilise donc les tubes de masque de soudure durcissable aux UV obtenus auprès de diverses sources sur Internet. Peu importe si vous utilisez un film ou de la peinture, vous aurez besoin d'une source de lumière UV. J'ai construit une unité d'exposition aux UV à l'aide d'un rouleau de bandes LED violettes/UV.:
Il est important pour la protection de votre vue que la source UV soit enfermée dans une boîte étanche à la lumière. Il existe de nombreuses directions pour la construction d'autres appareils d'exposition aux UV sur instructables.com, construisez-en une qui vous convient. J'utilise une minuterie électronique capable de mesurer les secondes et d'activer un relais pour allumer et éteindre le courant continu vers la source UV.
Les imprimantes laser n'imprimant pas une image de densité suffisante, vous devrez combiner 2 images. Découpez deux copies de chaque masque de soudure dans le film et alignez-les soigneusement pour former le masque de chaque côté. Je les colle de façon permanente avec un petit point de "Super Glue" sur les coins opposés de l'image imprimée.
L'étape suivante est la plus heuristique et nécessitera de tester votre configuration d'exposition (voir les instructions ci-dessous) ainsi que quelques expérimentations avec votre application de peinture.
Test de votre appareil d'exposition aux UV - Je ne sais pas quel type de niveaux d'UV votre appareil produira ou l'épaisseur de votre peinture, il y a tout simplement trop de variables. Vous devez établir le temps d'exposition adapté à votre configuration particulière et à la densité de peinture. Pour ce faire, préparez un exemple de guide d'exposition et recouvrez une carte PCB vierge de peinture en suivant les instructions ci-dessous (j'ai joint une image d'exposition rayée que vous pouvez imprimer sur de l'acétate et utiliser comme masque de test, n'oubliez pas de la doubler et de la coller).
Commencez avec un temps de 10 minutes au total, divisez-le en quatre périodes de 2 1/2 minutes et exposez un échantillon de planche en déplaçant un morceau de carton toutes les 2 1/2 minutes de sorte qu'un segment soit exposé pendant 2 1/2 minutes ensuite pour 5 minutes, puis 7 1/2 et enfin les 10 minutes complètes. Retirez et nettoyez la planche à l'aide d'essuie-tout et de diluant à peinture pour voir quelles zones sont devenues dures et lesquelles ne l'ont pas été. Si c'est presque tout dur ou tout enlevé, doublez ou la moitié des fois et réessayez avec un morceau de carte de circuit imprimé propre. Utilisez ces horaires pour déterminer un temps d'exposition suggéré pour votre première planche.
Avertissement! Une fois que le masque a durci, il est presque impossible de l'enlever, déterminez soigneusement vos temps d'exposition avant d'engager votre circuit imprimé dans ce processus. Si vous êtes cohérent dans la préparation de vos planches, vous ne devriez pas avoir à modifier les temps d'exposition.
En utilisant les horaires que vous avez déduits du test, exposez votre masque. Après exposition de votre planche finie, retirez-la de la boîte UV, retirez le masque de soudure et retirez la feuille de couverture en acétate. Vous devriez voir la peinture coller à cette feuille là où les tampons apparaissent sur votre masque mais pas ailleurs sur le tableau. Maintenant, utilisez du papier essuie-tout et retirez la peinture non exposée avec un diluant à peinture. Toute la peinture doit être retirée des plots et vias en cuivre mais pas les traces, nettoyer le dos et le devant de la carte et sécher avec du papier essuie-tout. Pour finir de durcir votre masque, inspectez d'abord les zones non exposées et à l'aide d'un outil pointu, retirez toute peinture des zones indésirables. Placez ensuite la planche dans votre boîte d'exposition aux UV et exposez au moins deux à trois fois le temps d'exposition d'origine. Traitez le deuxième côté, si nécessaire, de la même manière.
Étape 12: percez votre planche
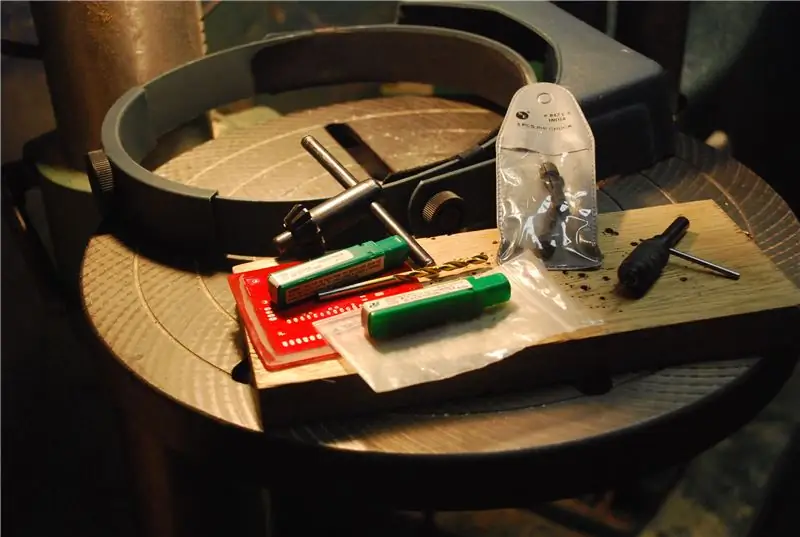
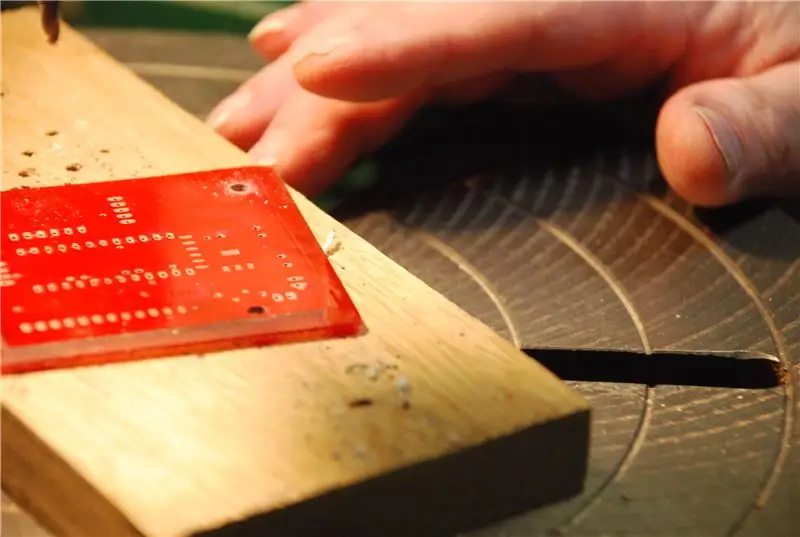
Percez les trous pour les vias, les composants traversants et les trous de montage. J'utilise une perceuse à colonne avec un étau pour les mèches de taille de fil. Je trouve que la planche est plus facile à manipuler si elle est percée avant de la couper à la taille finale.
Étape 13: Couper à la taille finale
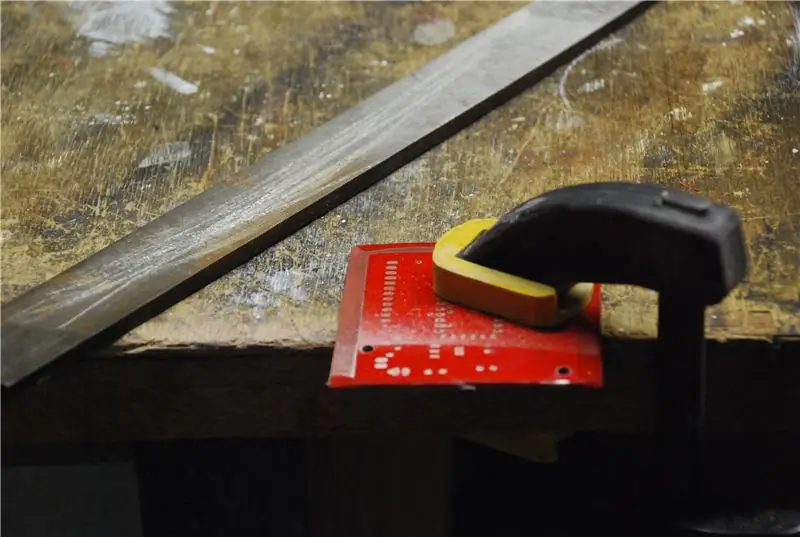
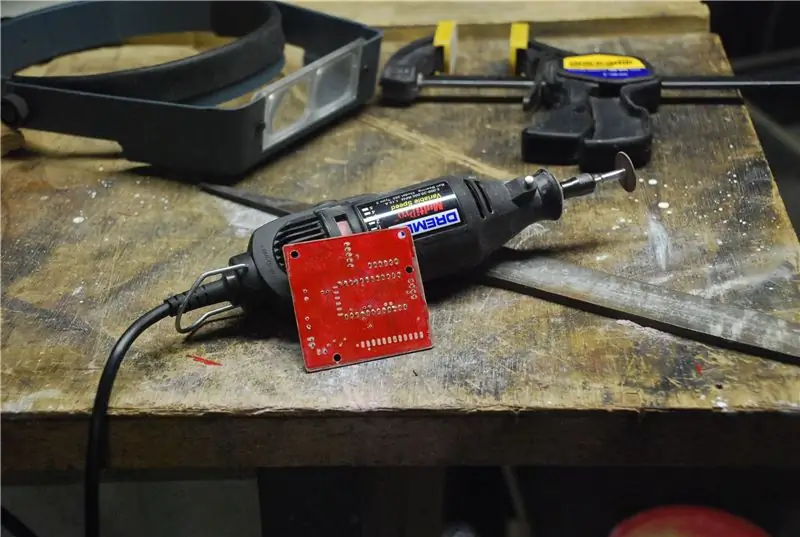
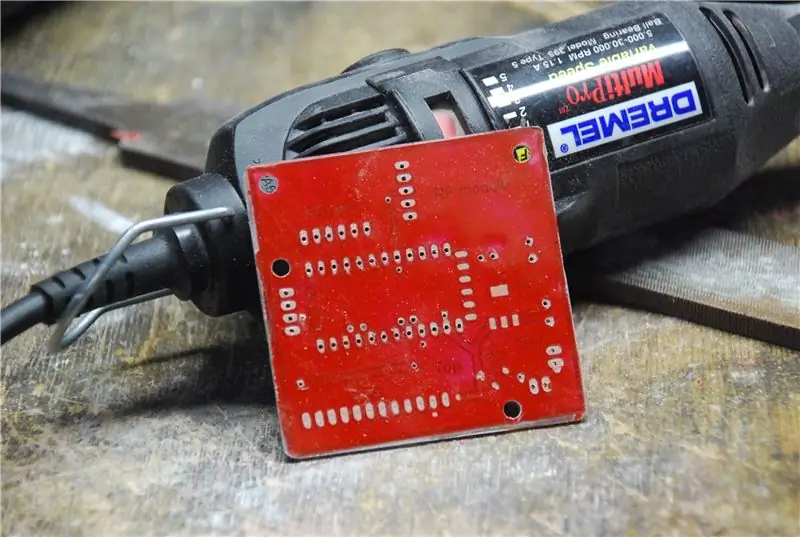
En utilisant les lignes de profil de la planche comme guide, coupez la planche à l'aide d'un outil rotatif et d'une meule à tronçonner, limez les bords et les coins arrondis
Étape 14: Remplissez votre tableau
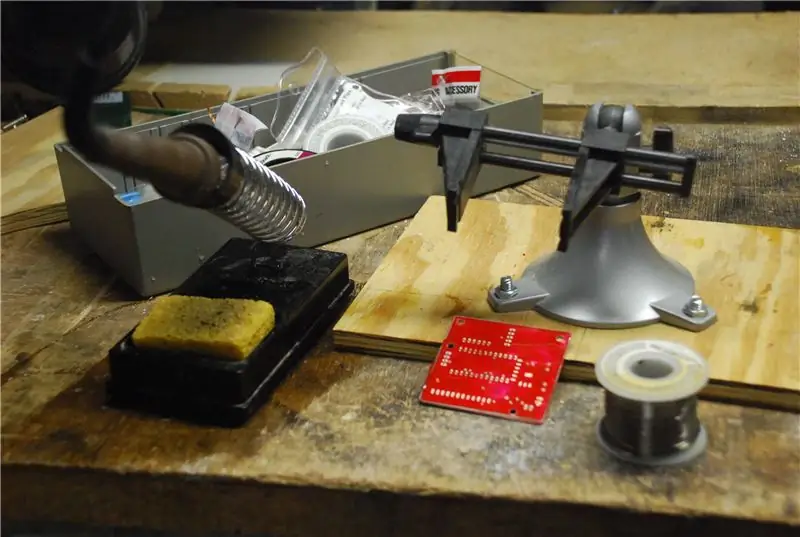
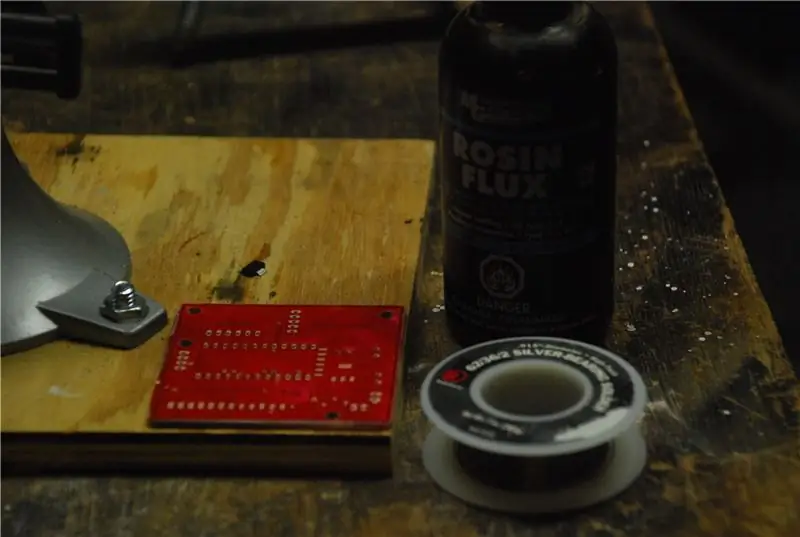
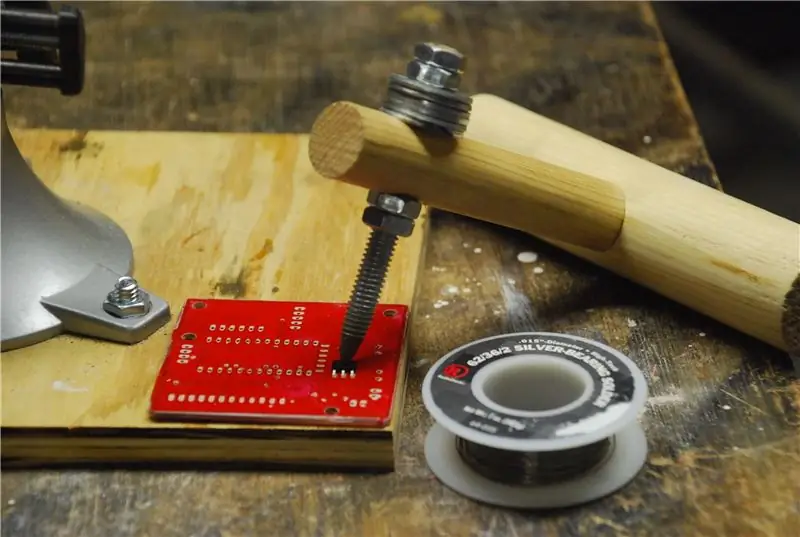
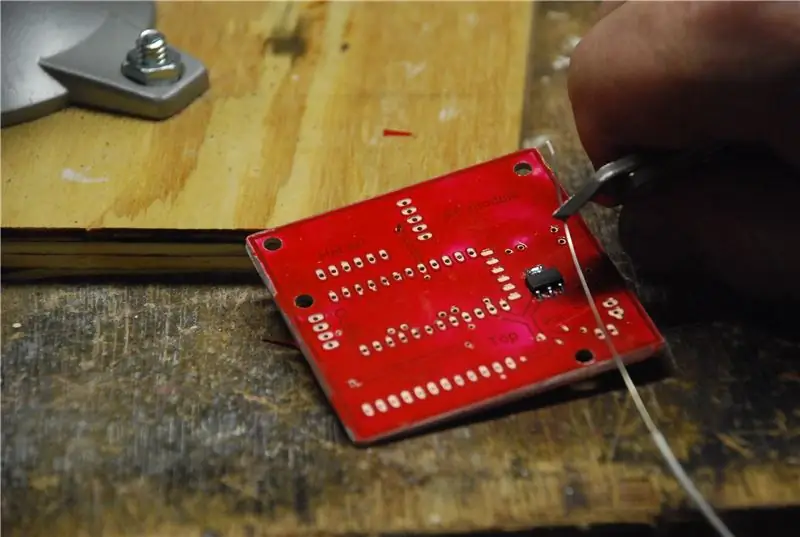
Je soude généralement à la main les pièces SMD d'abord, puis les vias et enfin les composants traversants.
J'ai fait cet appareil pour maintenir les composants SMD lors de la soudure à partir de quelques goujons, des rondelles et des écrous. J'applique un peu de flux liquide sur les pastilles CMS pour maintenir le composant en place puis souder en place.
Une astuce pour les vias est d'aplatir un peu l'extrémité du fil avec une paire de pinces afin qu'elles ne tombent pas à travers le trou de via. Soudez à l'avant, puis pliez le fil et soudez à l'arrière.
Votre planche est complète et prête à être testée.
J'espère que cette instructable si longtemps a été utile. N'hésitez pas à fournir des commentaires ou des idées constructifs.
Merci d'avoir pris le temps de regarder mon processus et de vous amuser à construire vos projets électroniques.
Conseillé:
Cartes de circuits imprimés à l'acide de l'imprimante 3D SLA : 7 étapes (avec photos)
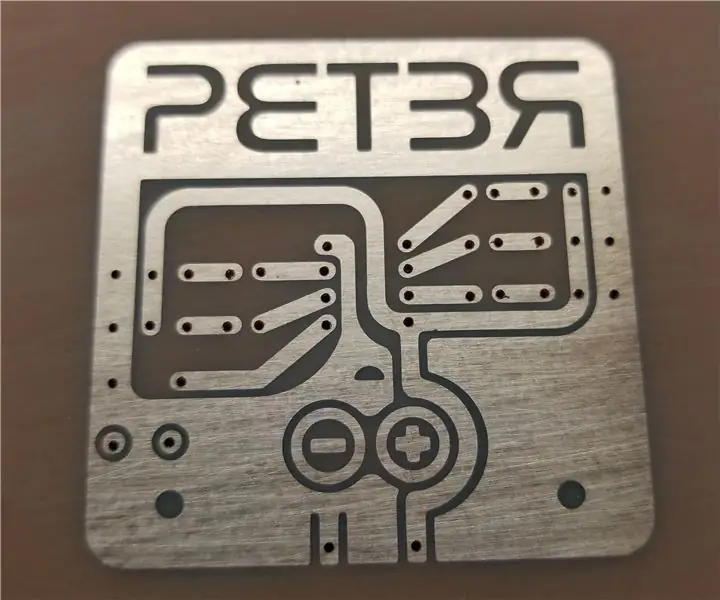
Cartes de circuits imprimés à l'acide de l'imprimante 3D SLA : Remix..remix.. Eh bien, j'ai besoin d'une carte de développement pour mes puces ATtiny. Je n'ai pas de CNC pour découper un PCB Je ne connais pas Kicad, et je ne veux pas commander de cartes. Mais j'ai une imprimante résine… et acide et je connais SketchUp. Et aime faire des choses. Quel bonheur
Impression de circuits imprimés personnalisés avec une imprimante 3D : 7 étapes (avec photos)
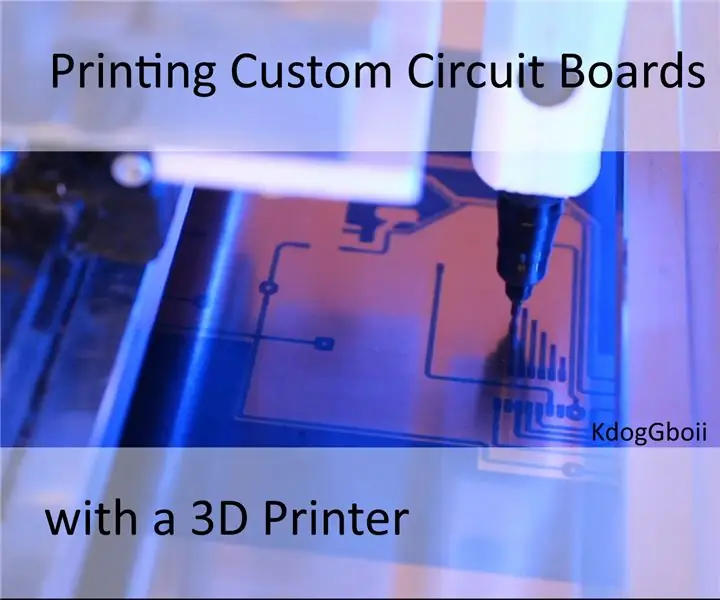
Impression de circuits imprimés personnalisés avec une imprimante 3D : Si ce n'est pas la première fois que vous voyez une imprimante 3D, vous avez probablement entendu quelqu'un dire quelque chose du genre : 1) Acheter une imprimante 3D2) Imprimez une autre imprimante 3D3) Renvoyez l'original 3D imprimante4) ????????5) ProfitMaintenant, n'importe qui w
Faire des circuits imprimés avec des lasers : 4 étapes (avec photos)
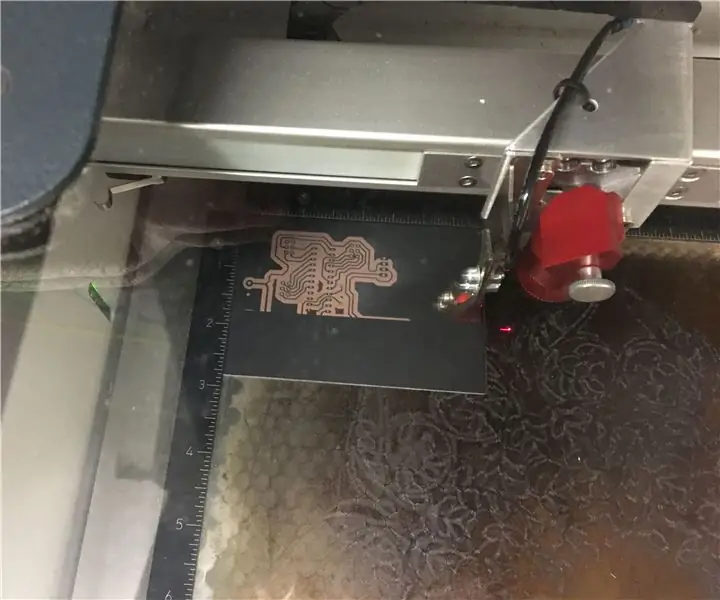
Fabriquer des circuits imprimés avec des lasers : Un circuit imprimé fait maison n'est aussi bon que le masque que vous y mettez. Quelle que soit la méthode que vous utilisez pour effectuer la gravure proprement dite, vous devez toujours coller une image de votre circuit sur la carte et vous assurer qu'elle laisse des traces nettes, propres et solides derrière
Conception de circuits imprimés avec des étapes simples et faciles : 30 étapes (avec images)
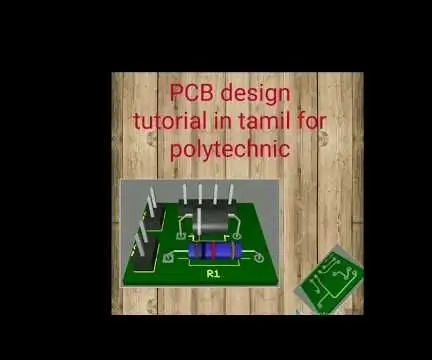
Conception de circuits imprimés avec des étapes simples et faciles : BONJOUR AMIS Son tutoriel très utile et facile pour ceux qui veulent apprendre la conception de circuits imprimés, commençons
Création de circuits imprimés avec une imprimante JET D'ENCRE : 8 étapes (avec photos)
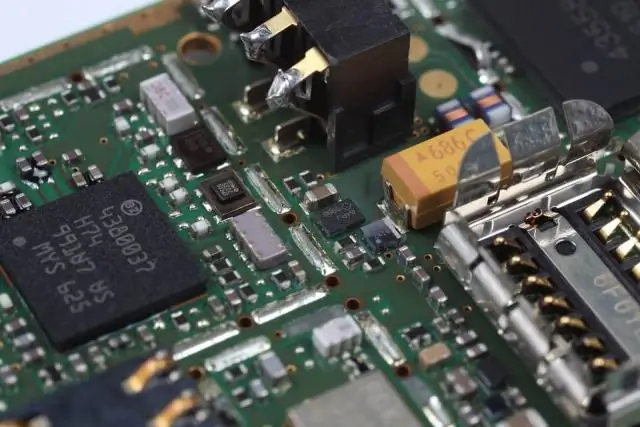
Création de cartes de circuits imprimés avec une imprimante JET D'ENCRE : Lorsque j'ai commencé à chercher comment graver mes propres cartes de circuits imprimés, chaque Instructable et tutoriel que j'ai trouvé utilisaient une imprimante laser et repassaient le motif d'une manière ou d'une autre. Je ne possède pas d'imprimante laser mais j'ai une encre bon marché