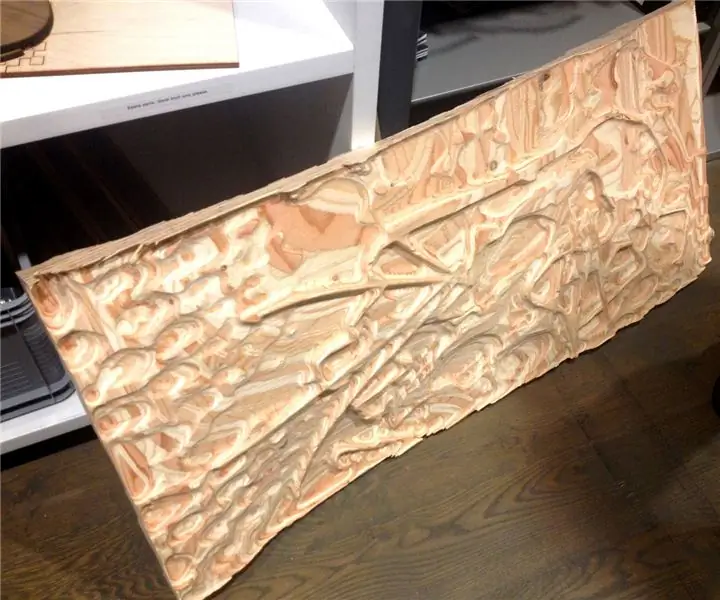
Table des matières:
2025 Auteur: John Day | [email protected]. Dernière modifié: 2025-01-23 14:46
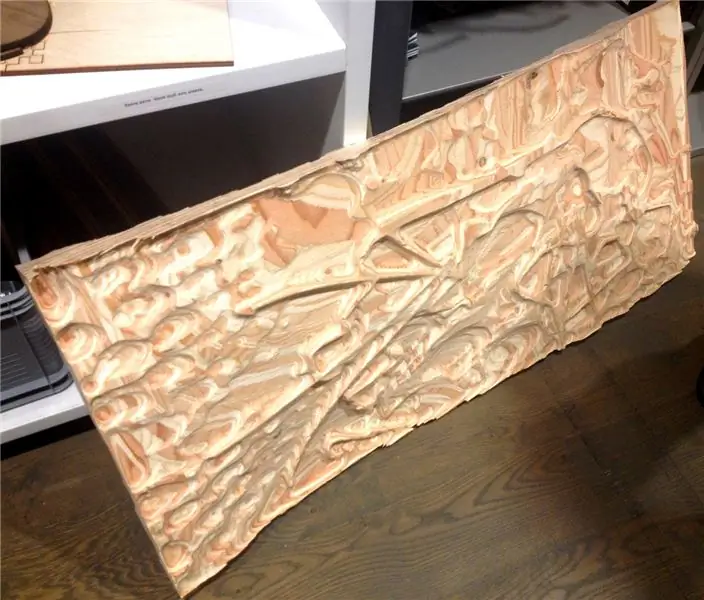
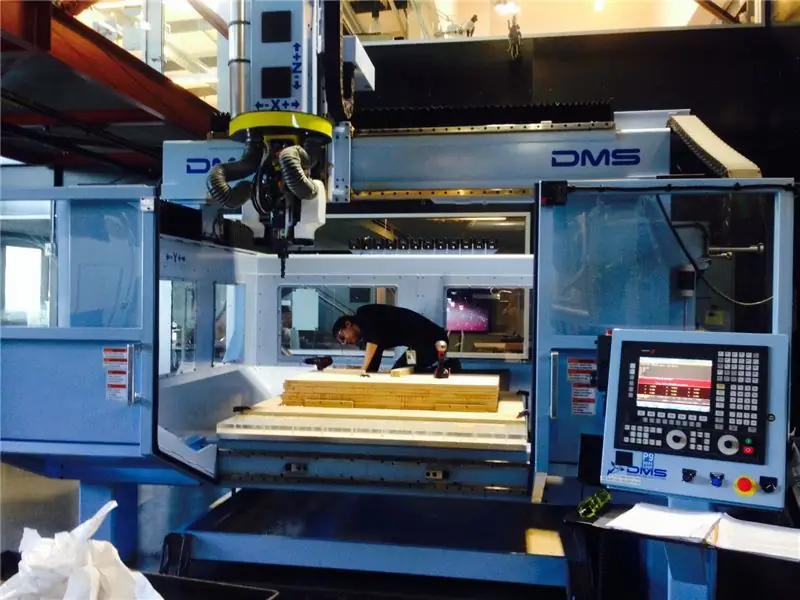
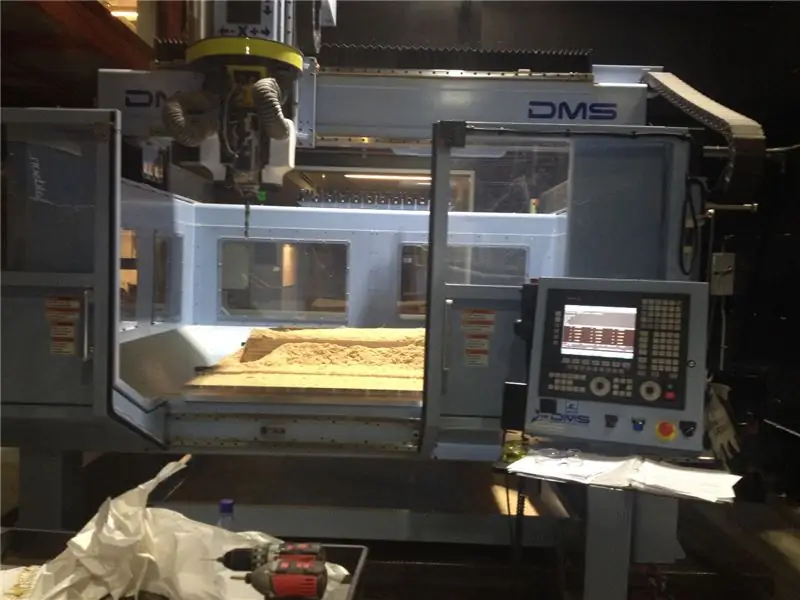
Après avoir réfléchi au potentiel de l'usinage par retournement à 3 axes, j'ai décidé de construire une peinture en relief tridimensionnelle à partir de contreplaqué stratifié. Cette pièce serait visible de chaque côté, et bien que les deux côtés soient liés l'un à l'autre, ils ne s'aligneraient pas nécessairement.
Dans ce Instructable, je vais discuter de mon concept et détailler mon processus étape par étape.
J'ai joué avec différents concepts d'images avant de décider d'utiliser un fond basé sur la texture du brocoli Romanesco. Avec son motif fractal imbriqué et évolutif, cette texture créerait certainement un arrière-plan intéressant pour les deux côtés de la peinture. À partir de ce moment-là, j'ai commencé à regarder des croquis créés par des enfants comme imagerie source. Parce que ce projet CNC s'écarte loin de la norme - il n'est pas destiné à être fonctionnel et il ne sera pas produit en série - j'étais curieux de voir comment il évoluerait si mes premières étapes étaient aléatoires, spontanées et intuitives. Dans un contexte où le processus est généralement déterminé par des résultats prédéterminés, que se passerait-il sans un objectif final spécifique ? Pour cela, j'ai décidé de pousser les possibilités du geste en rapport avec la machine.
À l'école d'art, je m'étais habitué à générer des dessins gestuels de 30 à 60 secondes de la figure nue, et parfois des choses vraiment surprenantes se produisaient de ce processus. L'idée était de produire en vrac, puis de trier les piles de dessins pour trouver ceux qui correspondent vraiment à quelque chose - une ligne sans effort qui communique le mouvement, un coup de poignet qui charge d'émotion une silhouette voûtée. J'ai commencé à griffonner avec ma souris sur l'ordinateur, faisant légèrement référence au Romanesco mais travaillant principalement avec des gribouillis rapides et désordonnés pendant quelques secondes, puis je m'arrêtais. J'ai produit au moins vingt dessins, et j'en ai sélectionné deux pour le recto et le verso de mon projet CNC.
Étape 1: Génération de modèles ArtCAM
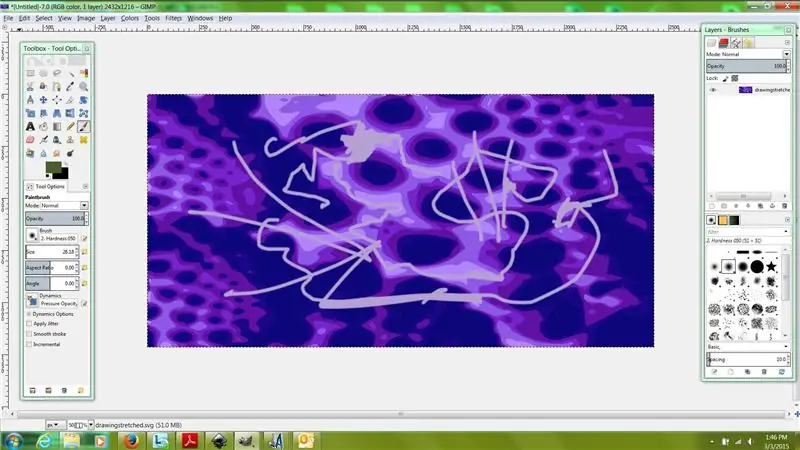
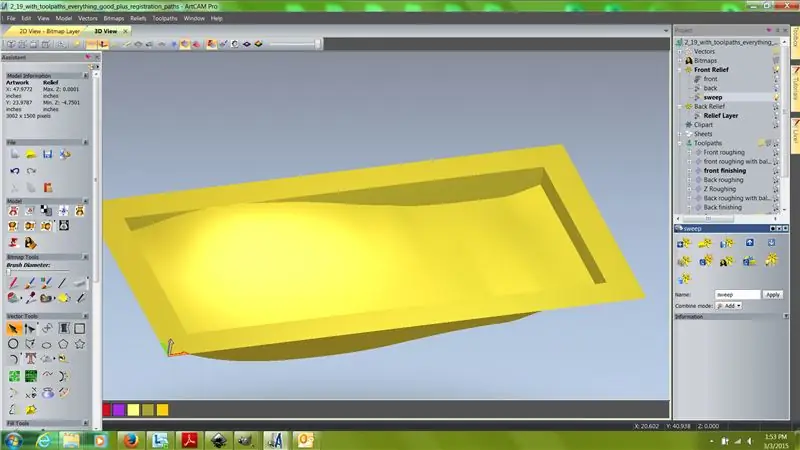
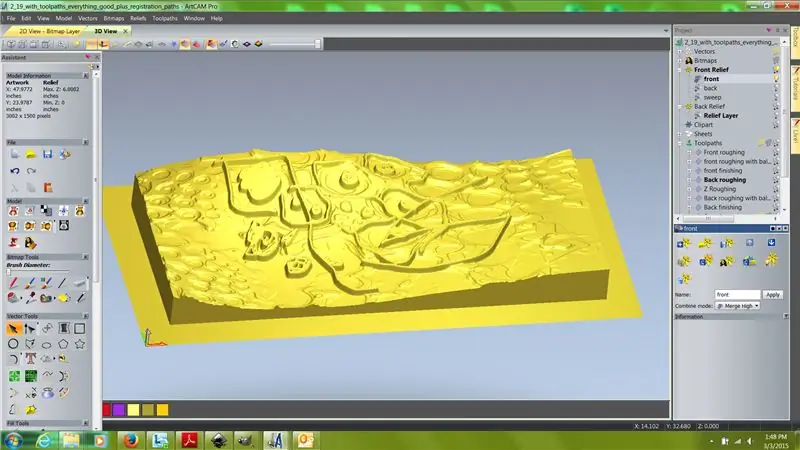
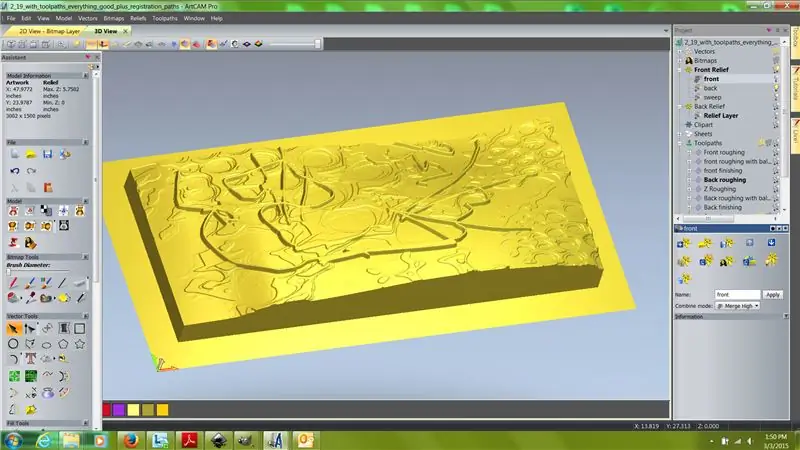
Une fois que j'avais sélectionné mon arrière-plan Romanesco et deux dessins, j'ai ouvert ArtCAM et créé un nouveau modèle à 48" x 24" x 6". Pour le relief avant, j'ai utilisé le légume comme texture puis j'ai utilisé une cannelure à deux rails pour serrez le relief dans une forme torsadée de "tapis volant". Travailler avec la profondeur de cette manière est un bon moyen de capitaliser sur les capacités de la CNC. Je me suis assuré que ce relief ne mesurait que 42 "x 18" ce point) afin d'avoir une bordure de 3" sur tous les côtés de mon matériau lorsque je suis allé usiner ma pièce. Cela me donnerait une surface sur laquelle reposer la pièce après avoir terminé le retournement. J'ai ensuite converti mon premier dessin en un relief dans lequel les zones les plus sombres s'estompaient tandis que les zones les plus claires s'avançaient. J'ai fait des allers-retours entre ArtCAM et Gimp pour composer le dégradé, jusqu'à ce que le relief ait une belle variété de lignes en relief. J'ai ensuite suivi le même processus pour le relief arrière, en le décalant de 0,75" en dessous du relief avant et en m'assurant que les zones "surélevées" pointaient vers le bas - en d'autres termes, en m'assurant que mon modèle ne serait jamais plus fin que 0,75 ".
Une fois que j'étais satisfait de l'apparence des deux côtés, j'ai utilisé la fonction d'échelle pour m'assurer que la différence entre les valeurs z les plus élevées et les plus basses pour l'avant et l'arrière était de 5 . J'ai mis mon zéro dans le coin inférieur gauche du modèle, et Je me suis assuré que mon relief avant s'étendait sur z = 6 à z = 1. Ensuite (après avoir copié et enregistré le relief arrière en tant que calque au cas où je ferais une erreur), j'ai reflété le dos le long de l'axe que j'utiliserais pour retourner la pièce. cas, je retournerais la partie de la même manière que vous tourneriez la page d'un livre, de droite à gauche sur l'axe des Y. J'ai ensuite inversé mes valeurs z pour le dos et les ai définies de z = 5,75 à z = 0,75. Il m'a fallu un certain temps pour trier cela dans mon esprit - pour m'assurer que je n'usinerais pas accidentellement dans mon recto - mais cela m'a vraiment aidé à travailler avec des nombres simples. J'ai ensuite enregistré ce modèle.
Étape 2: parcours d'outil
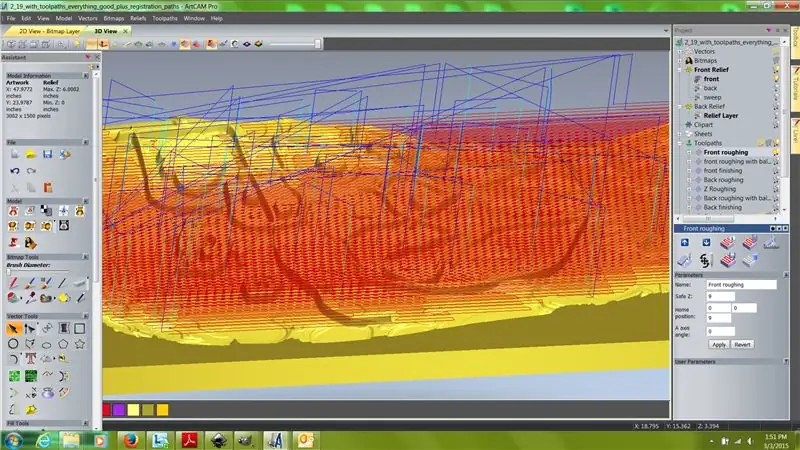
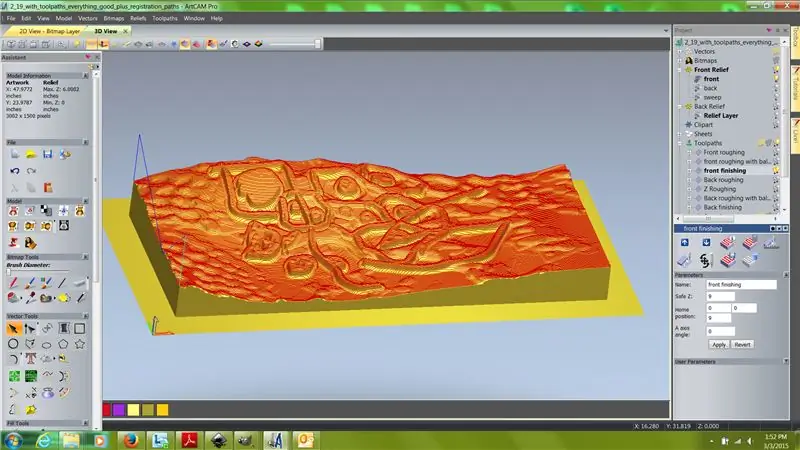
J'ai décidé d'utiliser une fraise en bout de 1" avec un pas de 0,5" et un pas de 0,325" pour les deux côtés comme parcours d'outil d'ébauche parallèle. Cela enlèverait beaucoup de matière rapidement et efficacement. Cependant, parce que la fraise en bout que j'avais prévu de l'utilisation n'était que de 4,5" de profondeur, je me suis assuré d'arrêter mon parcours d'outil au niveau az de 1,8" (rappelez-vous que mon zéro est au bas du modèle). Pour terminer la passe d'ébauche, j'ai utilisé une fraise à boule de 1" avec le même pas et un pas de 0,2" - cet outil mesurait plus de 7" de long. J'ai utilisé la même fraise sphérique pour les deux chemins de finition, en dépassant de 0,1" à chaque fois.
Pour ajuster ma pièce, j'ai créé un parcours d'outil qui irait à 0,125" dans une planche de spoiler. Ce chemin tracerait le contour du matériau sur la planche et me permettrait de définir mon zéro. Ensuite, après avoir déposé mon matériau, j'utiliserais un autre parcours d'outil pour équarrir le haut vers le bas. Je suis passé de z = 6 à z = 4 par paliers de 0,5". De cette façon, tout s'alignerait correctement lorsque je retournerais ma partie. Après avoir simulé mes parcours d'outils, je les ai post-traités et revu le code pour m'assurer qu'il n'y avait pas de problèmes.
Étape 3: configuration de la machine et usinage de la face avant
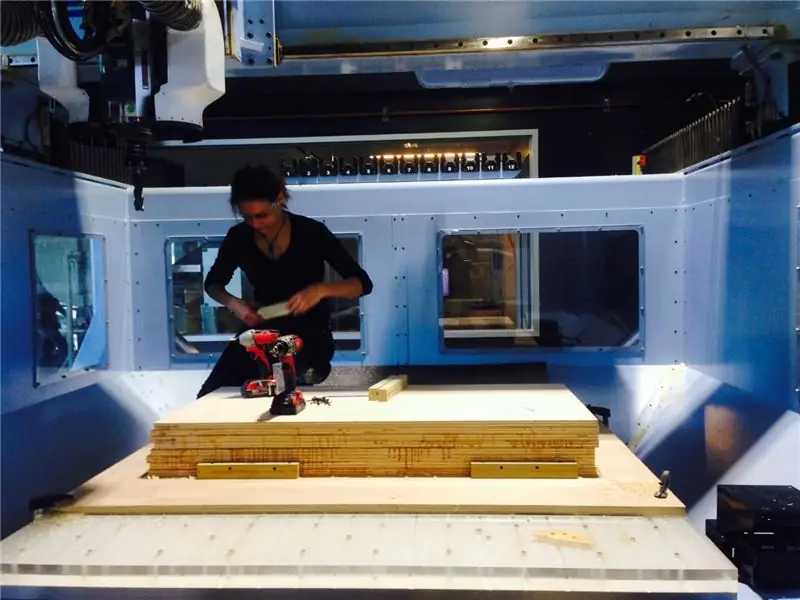
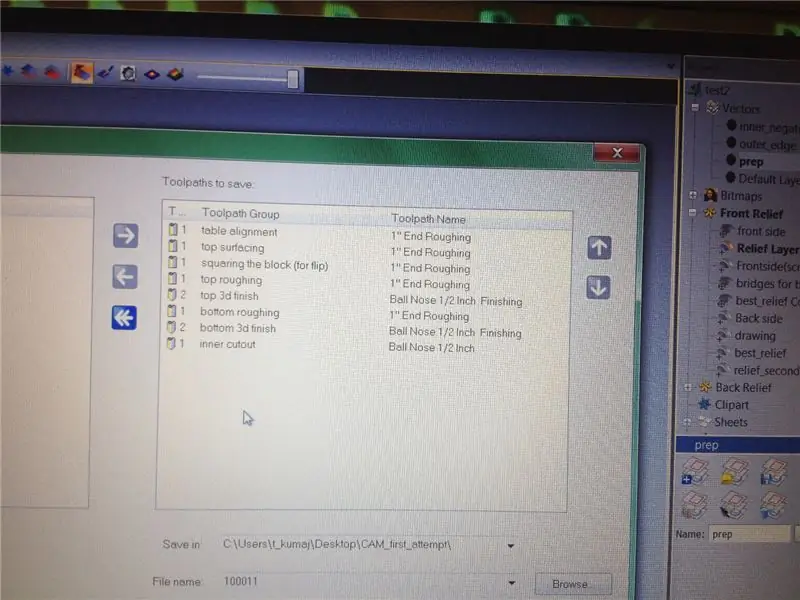
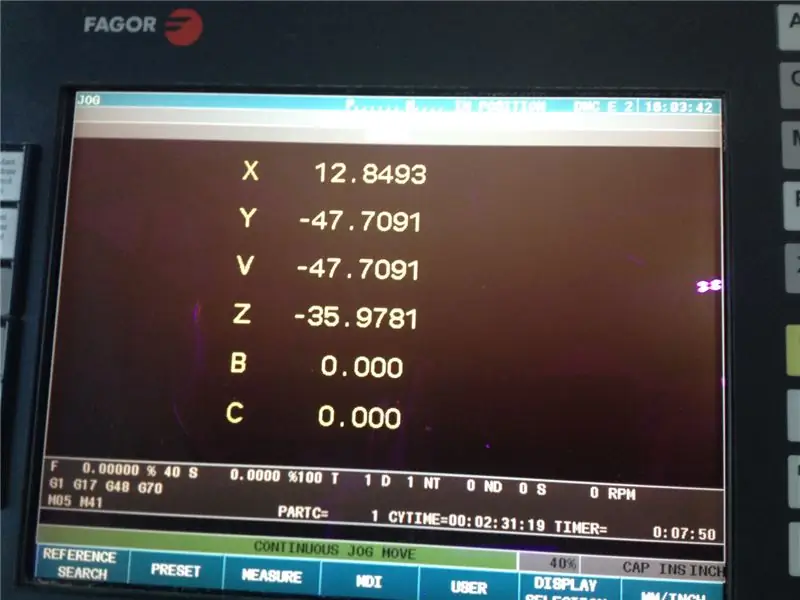
J'ai pris une photo de mes parcours d'outils dans ArtCAM et j'ai gardé un ensemble de notes détaillées pour m'assurer que je savais quel fichier. PIM à six chiffres correspondait à quel parcours d'outil. J'ai ensuite coupé une planche de spoiler de 5 'x 4' dans du contreplaqué et l'ai fixée à la table CNC DMS. Ensuite, après avoir effectué quelques essais, j'ai défini mes décalages TCP et pris une photo des coordonnées de la machine. C'était une partie essentielle du processus! J'ai ensuite exécuté mon premier parcours d'outil - le contour dans le panneau du spoiler. Ensuite, j'ai posé mon matériel et utilisé des blocs pour le visser dans le panneau du spoiler. C'était un bon système car je n'avais pas à m'inquiéter de la collision de ma broche avec un système de serrage. En remontant le temps pendant une seconde, mon matériau était composé de 8 feuilles de contreplaqué de bouleau stratifié, 2' x 4' x 0,75 . J'ai fait le collage en trois parties pour m'assurer d'avoir assez de temps pour chaque étape-- J'ai fait les deux moitiés, puis je les ai collées ensemble. C'était difficile à faire à ce genre d'échelle.
Retour à la machine CNC. J'ai quadrillé le matériau, puis la course a commencé. J'ai effectué la première passe d'ébauche à environ 80 % d'avance, ce qui était agressif mais cela a fonctionné. Cela a pris environ 2,5 heures. La passe finale a pris environ 1 heure, puis j'ai ouvert les portes avec empressement et aspiré toute la sciure de bois (il était difficile de voir les progrès à cause de toute la poussière - voir photo ci-dessus !).
Tout s'est bien passé ! Il y a eu quelques éruptions mais en général, le matériel et la résolution ont plutôt bien fonctionné.
Étape 4: retournement de la pièce et usinage de la face arrière
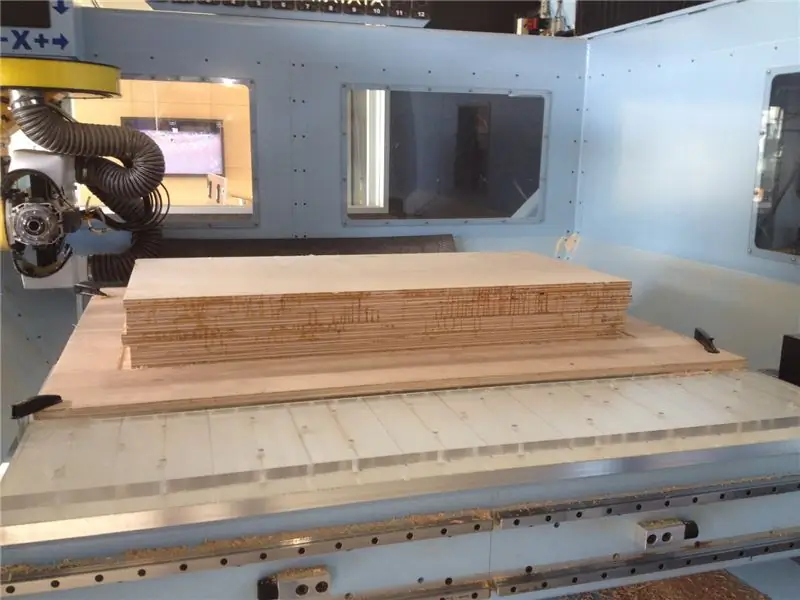
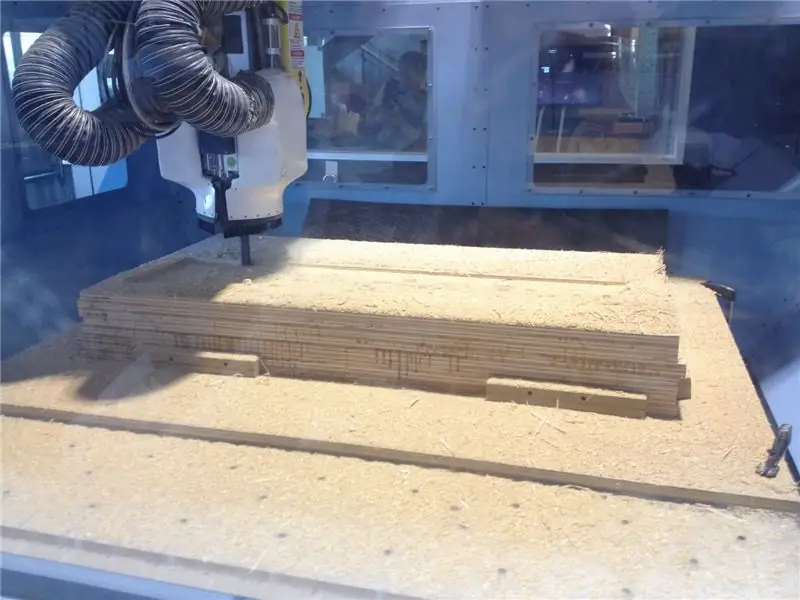
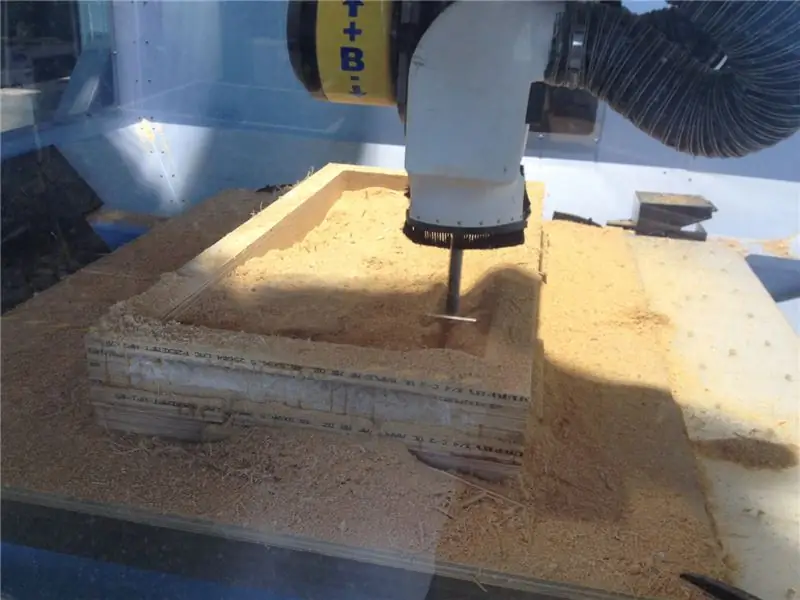
C'était la partie effrayante - est-ce que tout s'alignerait correctement ou est-ce que j'usinerais ma face avant ?
J'avais arrêté la machine pendant le week-end, alors quand je suis rentré, j'ai retiré ma pièce, nettoyé le panneau du spoiler et retourné le matériel. Je l'ai aligné avec le parcours d'outil dans le panneau du spoiler et j'ai utilisé les mêmes blocs pour le visser en place. Ensuite, j'ai utilisé la saisie manuelle des données pour amener la tête de broche aux coordonnées x et y de la machine qui correspondaient à mon point zéro. J'ai défini mes décalages TCP x et y à partir de là. Ensuite, j'ai déplacé x et y et j'ai touché l'outil jusqu'à la carte du spoiler et j'ai défini mes décalages TCP z.
J'ai effectué les passes d'ébauche et de finition à des vitesses similaires à celles de la face avant. J'ai eu du mal à voir ce qui se passait, encore une fois à cause de la sciure de bois, mais avec le temps, je suis devenu plus confiant que tout fonctionnait comme prévu. Quand tout a été fait, j'ai aspiré la poussière et révélé l'arrière!
Étape 5: Couper les épaules et nettoyer la pièce
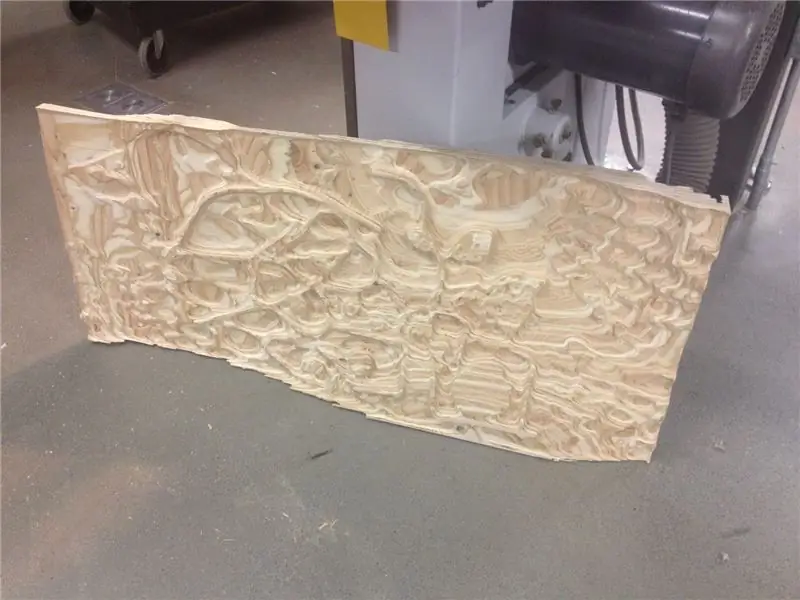
J'ai coupé une épaule sur la scie à table dans l'atelier de menuiserie. Après avoir réalisé que je n'avais plus vraiment de surface à placer contre la clôture, j'ai utilisé la scie à ruban pour les trois autres côtés. J'ai ensuite poncé mes bords et nettoyé les parties soufflées du contour avec un outil dremel.
La pièce s'est avérée être un paysage inattendu et criblé de contours qui semblait assez éloigné de l'impulsion initiale pour créer l'œuvre. Cette pièce est un bon candidat pour la peinture, même si j'aime la façon dont la topographie est mise en valeur par le placage de contreplaqué. Il ferait aussi un moule intéressant pour des reliefs à plus grande échelle. Alors que ma résidence au Quai 9 se poursuit, j'ai hâte de voir comment ce processus fournira un tremplin pour de futurs travaux.
Conseillé:
Steam Punk Your UPS pour obtenir des heures de disponibilité pour votre routeur Wi-Fi : 4 étapes (avec photos)
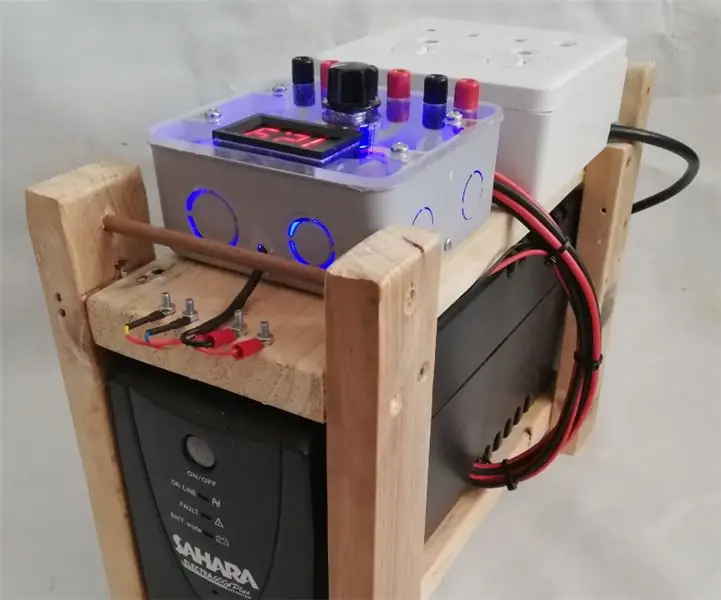
Steam Punk Your UPS pour obtenir des heures de disponibilité pour votre routeur Wi-Fi : 12V CC ! Vous êtes également confronté au [typiquement
UPS pour routeur WiFi V4 : 6 étapes (avec photos)
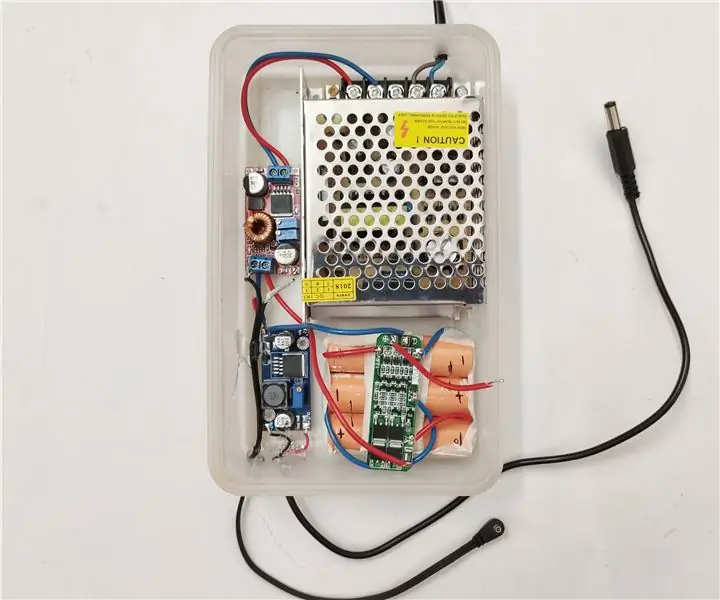
UPS pour routeur WiFi V4 : Salut à tous, Avec l'augmentation du travail à domicile, nous voulons tous travailler sans interruption, les pannes de courant sont très courantes en Inde. De nombreux appartements ont installé des générateurs de secours, qui démarrent en quelques secondes après une panne de courant. Même si la panne de courant est pour f
Ajouter un tachymètre optique basé sur Arduino à un routeur CNC : 34 étapes (avec photos)
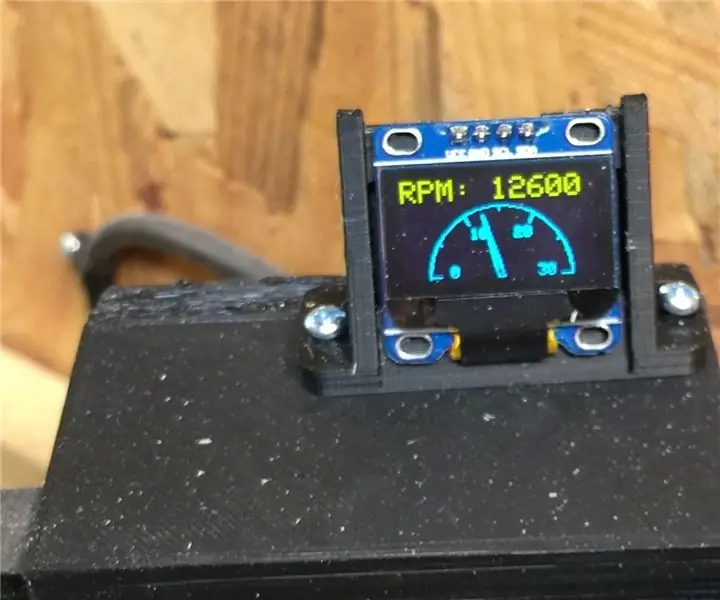
Ajoutez un tachymètre optique basé sur Arduino à un routeur CNC : créez un indicateur de régime optique pour votre routeur CNC avec un Arduino Nano, un capteur photodiode IR LED/IR et un écran OLED pour moins de 30 $. J'ai été inspiré par la mesure RPM d'eletro18 - Optical Tachometer Instructable et je voulais ajouter un tachymètre
Routeur domestique sans fil avec compteur d'utilisation analogique : 5 étapes (avec photos)
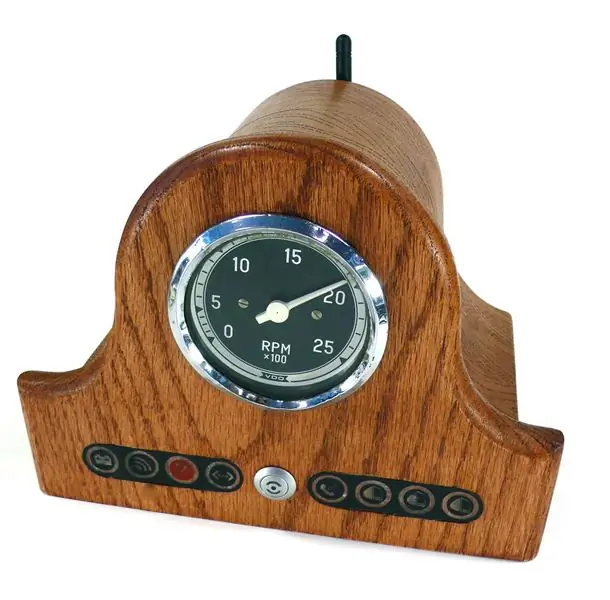
Routeur domestique sans fil avec compteur d'utilisation analogique : j'ai grandi dans et autour de bateaux en fabriquant des métiers à tisser et des panneaux de commande, et j'ai une collection de jauges et d'amp; cadrans qui seraient normalement trouvés connectés à de petits moteurs diesel marins. Aujourd'hui, je travaille en tant que concepteur dans la construction d'interfaces pour la mise en réseau
Routeur CNC 3 axes - 60"x60"x5" - JunkBot : 5 étapes (avec photos)
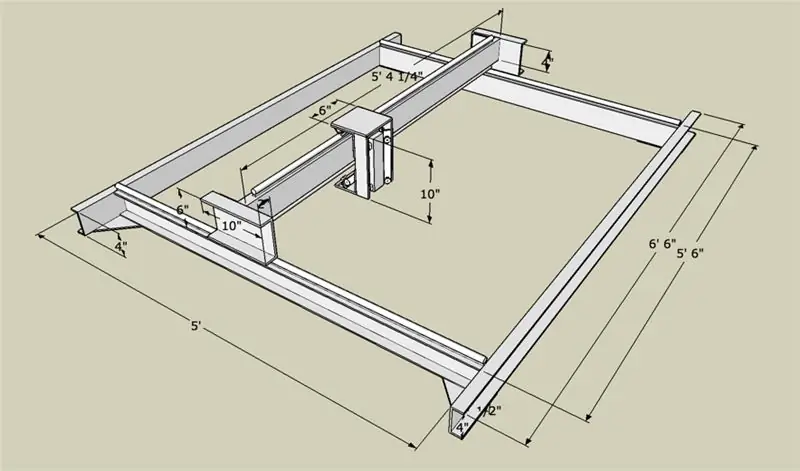
Routeur CNC 3 axes - 60 "x 60" x 5" - JunkBot : ce Instructable est le premier d'une série documentant la construction d'un routeur CNC DIY 3 axes. C'est aussi mon entrée pour le concours Universal Laser Cutter. Le but de ce Instructable n'est pas de montrer une progression complète étape par étape mais plutôt