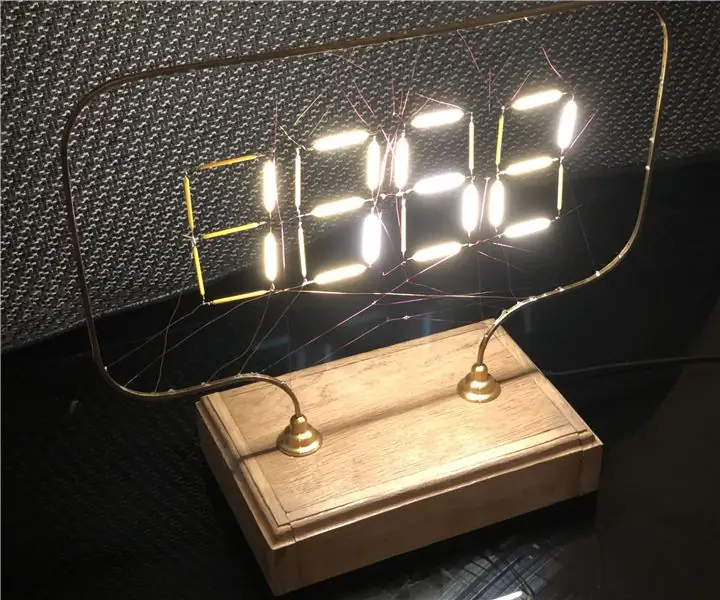
Table des matières:
- Étape 1: Pièces requises
- Étape 2: percez le matériau du cadre
- Étape 3: plier le cadre
- Étape 4: Branchez les LED
- Étape 5: Fabriquer la base et les pieds du cadre
- Étape 6: Fabriquer et tester le PCB de contrôle
- Étape 7: Montez les chiffres sur la base et triez tous les fils
- Étape 8: Flasher l'Arduino
- Étape 9: Attendez avec frustration la synchronisation radio
- Étape 10: Terminer
2025 Auteur: John Day | [email protected]. Dernière modifié: 2025-01-23 14:46
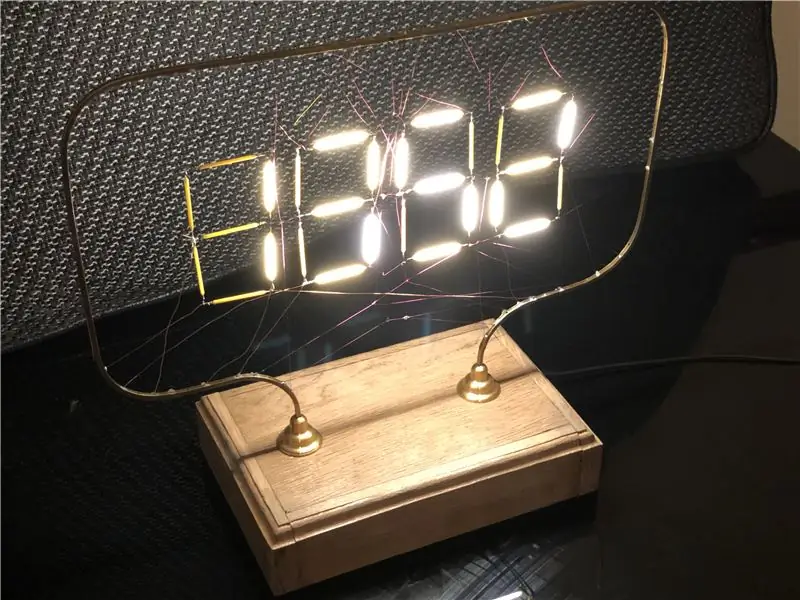
Depuis que j'ai vu les ampoules à filament LED pour la première fois, j'ai pensé que les filaments devaient être bons pour quelque chose, mais il a fallu attendre la fermeture de la vente d'un magasin de pièces électroniques local pour que j'achète des ampoules avec l'intention de briser eux et voir ce que je pourrais faire avec les filaments.
Il n'a pas fallu longtemps pour décider qu'ils feraient une horloge intéressante, et qu'il serait très amusant de faire flotter les segments dans l'air suspendus uniquement par leurs fils d'alimentation.
À mi-chemin de sa construction, j'ai réalisé qu'il rappelait étrangement les toiles d'araignées avec l'écriture du livre "Charlotte's Web"
Gardez à l'esprit que cet appareil a 80V sur le cadre en métal nu. Mais l'utilisation d'un convertisseur DC-DC et d'une alimentation isolante signifie qu'il est possible de toucher le cadre et de ne pas recevoir de choc. Ou du moins je ne l'ai pas fait.
Étape 1: Pièces requises
Mes expériences ont montré que les LED ont besoin d'environ 55 volts pour s'allumer et briller à pleine puissance autour de 100V. En cours d'utilisation, ils sont disposés en paires série pour les marchés 230V / 240V et en parallèle pur pour les marchés 110V. Il y a une sorte de contrôleur dans le culot de la lampe, mais j'ai décidé de ne pas essayer de le réutiliser car je voulais que les filaments brillent beaucoup moins. Une horloge LED entièrement lumineuse serait pénible à lire. Une horloge d'affichage à 7 segments a besoin de 27 lignes de contrôle et au départ, j'avais l'intention d'utiliser un Arduino Mega. Cependant, lors de la discussion sur le contrôle du courant de 100 V (environ) à travers les LED avec un microcontrôleur sur un canal IRC indépendant, on m'a parlé de l'existence des puces de pilote DS8880 pour les écrans fluorescents sous vide. Ceux-ci sont parfaits pour le travail à accomplir car ils prennent 4 bits de données d'entrée BCD par chiffre et les convertissent en signaux d'entraînement à 7 segments avec contrôle de courant intégré et variable jusqu'à 1,5 mA. Les tests ont montré que 1,5 mA était idéal pour cette application. La chute de 7 bits à 4 bits par chiffre signifiait également que je pouvais utiliser un Arduino Nano ou Uno pour le contrôle car seulement 13 lignes de contrôle sont nécessaires. (2 x 4 bits 0-9 canaux, 1 x 3 bits 0-7 canaux et 1 x 2 bits 0-3 canaux)
J'ai décidé d'utiliser le signal radio MSF 60 kHz pour que l'Arduino connaisse l'heure de la journée. J'ai déjà utilisé cela avec un certain succès en utilisant des modules récepteurs standard, dont l'un était à portée de main. Cependant, ceux-ci semblent plus difficiles à trouver actuellement, il pourrait donc être plus facile d'utiliser un module WiFi si quelqu'un a envie de créer sa propre version de cette horloge.
Au cours des tests, j'ai découvert que les Arduino Nanos que j'avais tous semblaient avoir une base d'horloge médiocre, j'ai passé des heures à attendre qu'ils se synchronisent, puis, en désespoir de cause, j'ai essayé de brancher un ancien Duemilanove, qui s'est synchronisé dans la première minute et s'est habitué.
Pour créer le 80V nécessaire pour entraîner les filaments, j'ai utilisé un convertisseur DC-DC. Il en existe beaucoup qui fonctionnent à partir de 12V. L'Arduino peut être alimenté en 12V et crée une alimentation 5V pratique à partir de la logique à partir de celle-ci. Mais j'ai oublié ce fait et j'ai acheté une entrée 5V chère. Cela pourrait toujours être un bon choix, cela signifie que l'horloge fonctionnera également à partir de l'USB pendant la programmation et que le convertisseur coûteux a des sorties isolées de 5 kV. (ce qui signifie que le cadre 80V flotte, réduisant considérablement le risque de choc)
Les LED sont disponibles sur eBay, il n'est pas nécessaire de casser des ampoules pour les récolter.
Liste de courses:
Fil de cuivre auto-fluxant. 34 SWG (31 AWG / 0,22 mm) fonctionne.
Arduino
4 x pilotes DS8880 VFD
Au moins 28 filaments LED (mais ils se cassent facilement, alors obtenez au moins 25% de rechange)
Convertisseur DC-DC
Condensateur 47µF 5V
Condensateur 4.7nF 100V
Matériau du cadre (j'ai utilisé du laiton à section en U de 3 mm x 3 mm x 0,5)
Une base en quelque sorte
Adhésif cyanoacrylate
Prise d'entrée CC (ou USB monté sur panneau)
Module récepteur 60kHz (ou similaire) et antenne.
Boîtiers d'embase mâle à 7 broches (et bornes à sertir correspondantes)
Étape 2: percez le matériau du cadre
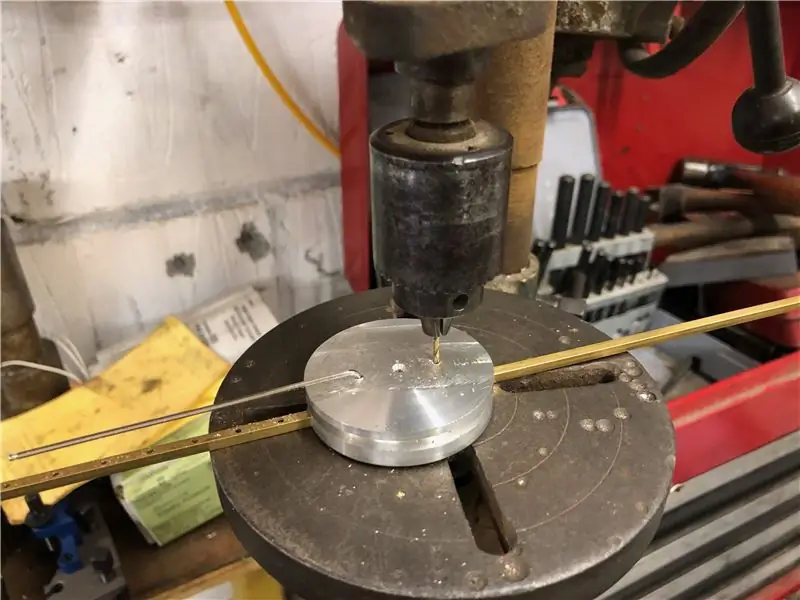
Le cadre est fabriqué à partir d'une longueur de 1 m de section en U en laiton de 3 mm (épaisseur de paroi de 0,5 mm) et ne suggère rien de plus léger que cela.
Les LED sont contrôlées par des interrupteurs côté bas. Cela signifie que chaque LED est connectée à un cadre conducteur à 80 V sur l'anode, puis un fil isolé traverse le cadre jusqu'aux circuits intégrés de contrôle.
Le cadre doit être percé pour les fils. J'ai décidé de percer des trous à un pas régulier de 10 mm et j'ai fait un petit gabarit de guidage pour régler l'espacement. Une rainure dans le bas maintient le canal du cadre et une goupille (clé allen sur la photo) s'indexe sur un trou existant et permet d'en percer deux autres à l'écartement choisi.
Le gabarit de perçage sert également de gabarit de pliage. Il a une rainure pour empêcher le canal en U de s'étendre pendant le pliage.
J'ai utilisé des trous de 1 mm, mais des trous plus petits auraient probablement été mieux, facilitant le collage.
Étape 3: plier le cadre
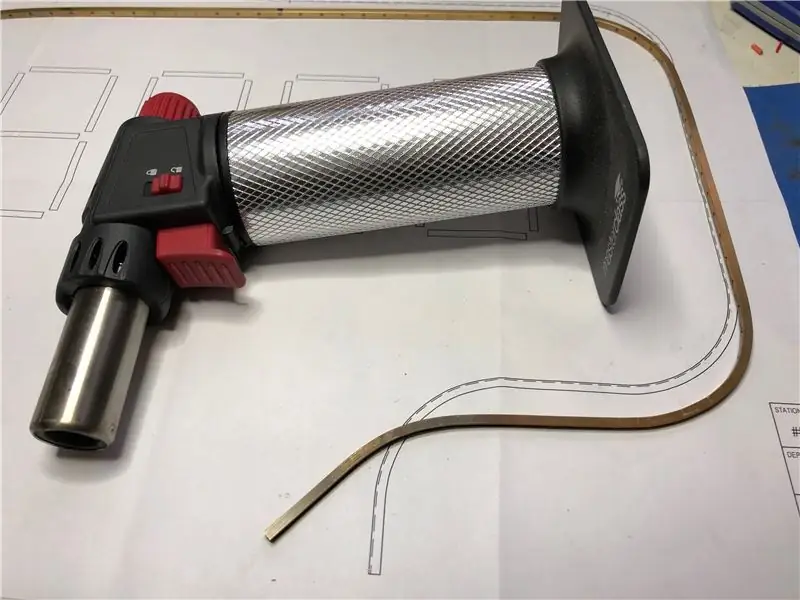
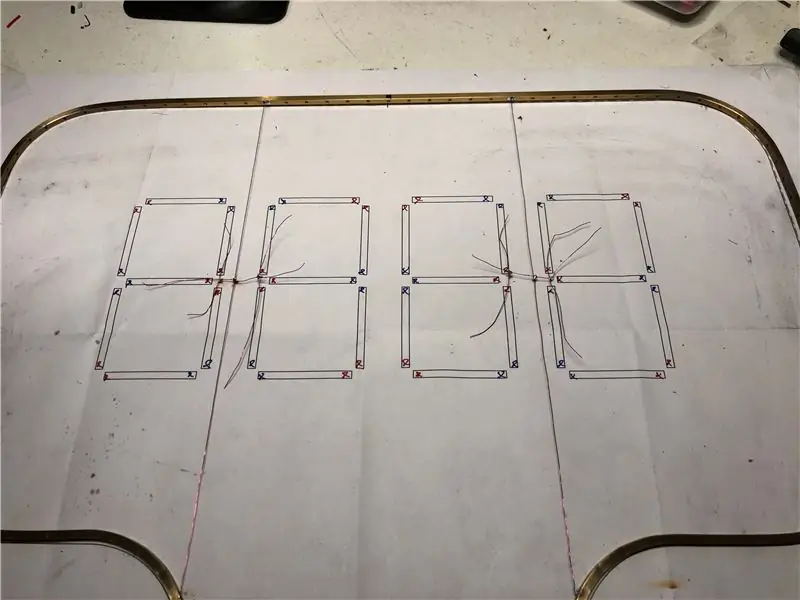
J'ai imprimé un modèle pour le cadre extérieur et le positionnement des LED. Cela a été collé à l'établi, puis j'ai soigneusement plié à la main le cadre en laiton pour qu'il corresponde.
Les coudes avec le côté ouvert du U vers l'extérieur étaient faciles, mais il était impossible de faire les coudes intérieurs sans casser le canal jusqu'à ce que je recuit le matériau avec un chalumeau. Il a eu besoin d'un peu de redressement après le recuit, il est donc préférable de ne recuire que les bits qui en ont réellement besoin. Réchauffez simplement avec le chalumeau jusqu'à ce qu'il brille terne et pas plus chaud. Aller trop loin et le faire fondre serait inutile.
Une fois pour façonner le cadre a été scotché au modèle.
Le modèle est disponible au format PDF ici. S'il est imprimé à l'échelle 1:1 (s'adapte sur du papier A3), le périmètre est d'exactement 1 m pour s'adapter à la longueur du matériau.
Étape 4: Branchez les LED
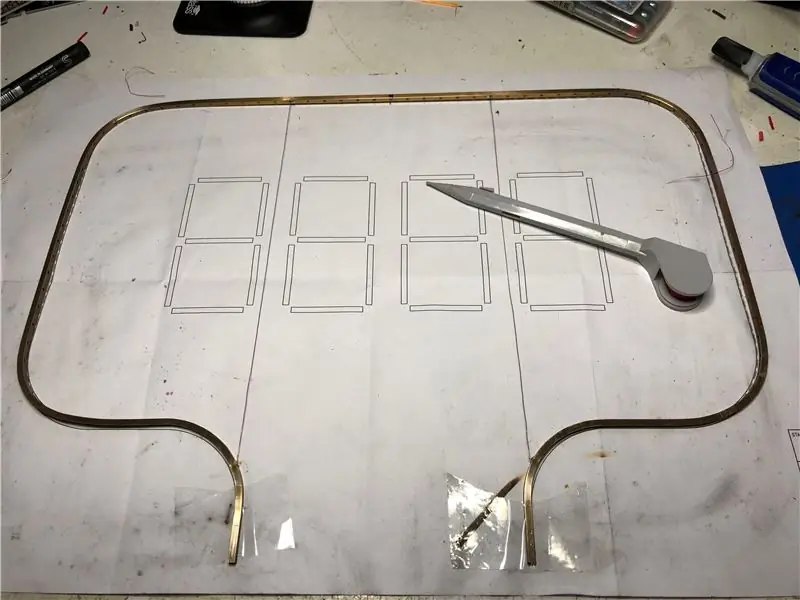
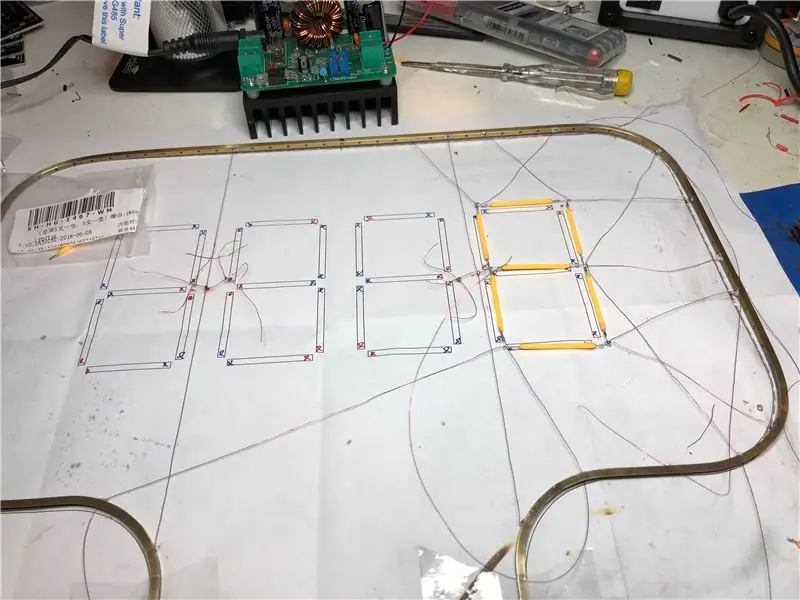
Déterminez d'abord quelle extrémité de la LED est l'anode (se connecte à une tension positive). Sur mes LED, cela était marqué par un petit trou juste à côté de la fin du revêtement en plastique.
Ces extrémités ont toutes besoin d'être soudées à des fils soudés au cadre. Je ne suis pas entièrement satisfait de mon schéma de câblage, je vais donc m'abstenir de faire des suggestions. Faites passer les fils dans le trou de votre choix, tirez légèrement et soudez en place. Coupez ensuite l'excédent. J'ai utilisé mon Veropen comme distributeur et support pour le fil, en partie parce que c'était le bon type d'isolation (le type qui peut être soudé sans dénuder, connu sous le nom d'"auto-fluxant")
Vous pouvez ensuite commencer à construire les chiffres, en fixant les fils de l'interrupteur (cathode) avec de l'adhésif cyanoacrylate au point où ils passent à travers les trous du cadre. Assurez-vous de laisser suffisamment de longueur pour boucler tout le tour du cadre et dans la base / le boîtier de commande.
Vous pouvez soutenir les fils les uns des autres pour obtenir des coins arrondis et éviter que les fils passent devant les chiffres. Soudez-les s'il s'agit de fils d'alimentation, collez-les s'il s'agit de fils d'interrupteur. Les coins des chiffres ressemblent aux fils doivent se toucher, mais si nécessaire, il est facile de les garder isolés les uns des autres.
Étape 5: Fabriquer la base et les pieds du cadre
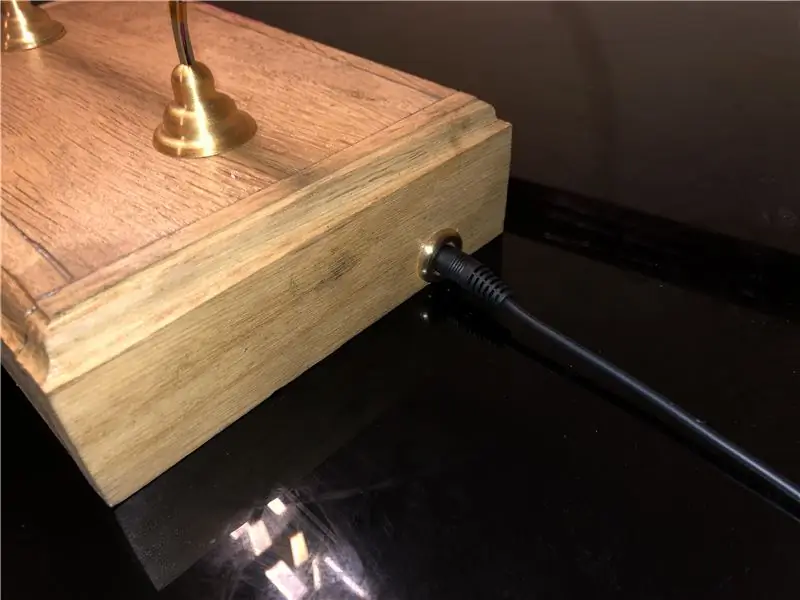
J'ai fabriqué une base en chêne et des pieds en laiton usinés pour le cadre sur mon tour CNC. Mais n'importe quelle sorte de boîte ferait l'affaire, et des pieds imprimés en 3D pour le cadre fonctionneraient bien, j'en suis sûr.
Les pieds sont maintenus avec des vis M5 dans des trous taraudés décalés par rapport au trou central du cadre. Les vis s'insèrent dans les fentes usinées dans la base. Les fils passent par les mêmes fentes. Les fentes permettent d'ajuster l'espacement des pieds pour régler la tension dans les fils (dans une certaine mesure).
L'une des vis a en plus un œillet et un fil pour fournir l'alimentation +80V au cadre en laiton.
Les fichiers STL pour le support d'antenne et le montage PCB sont sur mon Github.
Étape 6: Fabriquer et tester le PCB de contrôle
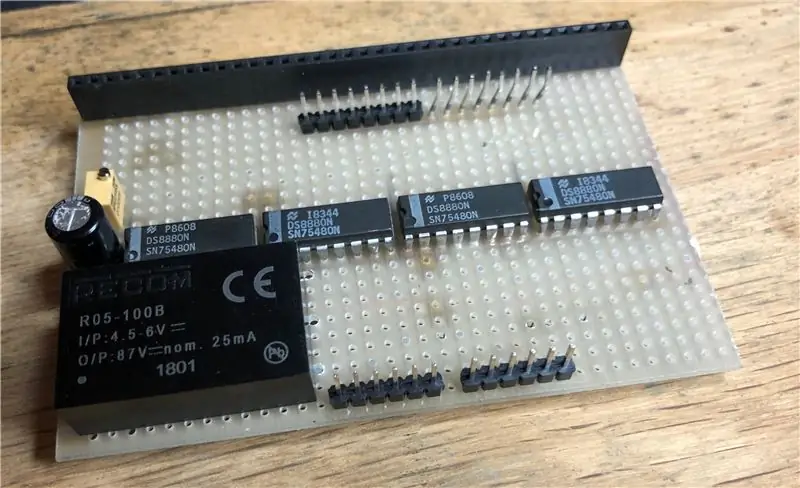
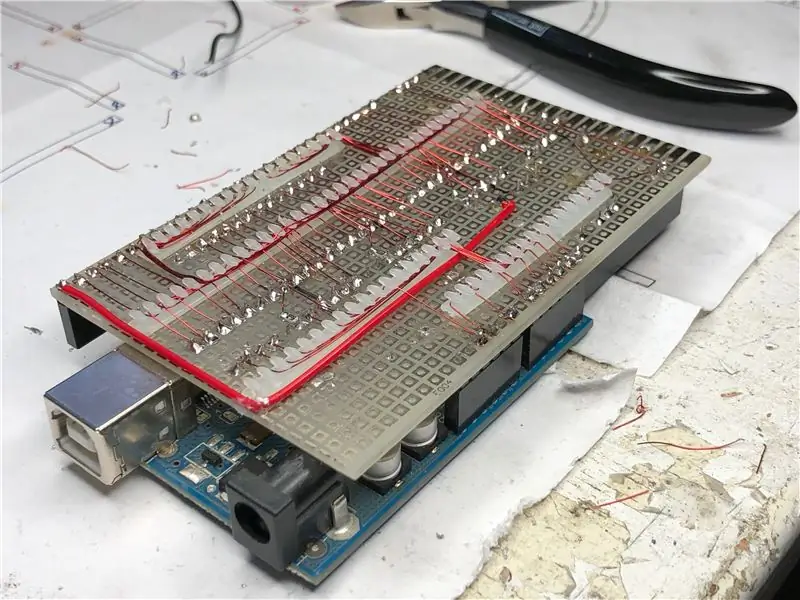
Les moyens de fabriquer le PCB de contrôle sont couverts dans un précédent Instructable.
Je n'ai pas travaillé à partir d'un schéma, je l'ai inventé au fur et à mesure. Cependant, j'ai fait un schéma après coup.
Format PDF ou KiCAD
Ce schéma peut manquer de certaines erreurs que l'esquisse Arduino a codées, et peut contenir des erreurs supplémentaires qui manquent à l'horloge réelle.
Les points importants à garder à l'esprit sont que le convertisseur DC-DC doit être connecté à la broche V-in de l'Arduino et que l'alimentation logique et le récepteur radio doivent être connectés au 5V régulé. Cela signifie que l'Arduino et le convertisseur peuvent fonctionner à partir de n'importe quel bloc d'alimentation jusqu'à 12 V et que la logique ne voit toujours que 5 V régulé.
Étape 7: Montez les chiffres sur la base et triez tous les fils
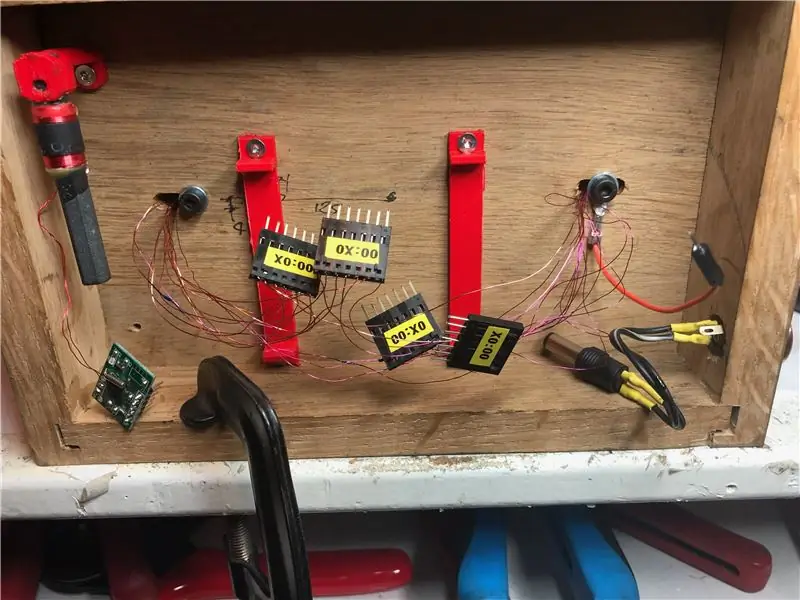
Avec les fils temporairement maintenus dans le canal avec de petits morceaux de ruban adhésif, les nombreux brins peuvent être acheminés jusqu'à la base. J'ai utilisé un convertisseur élévateur réglable pour déterminer quel fil était lequel. Je l'ai d'abord réglé sur une tension qui allumerait simplement un filament LED lâche, puis j'ai poussé la sortie positive à travers un trou du cadre. Ensuite, en touchant l'extrémité coupée de l'extrémité du fil de cuivre émaillé avec le fil d'alimentation négatif du convertisseur, j'ai pu voir à quel segment correspondait chaque led. J'ai ensuite serti le fil dans une broche et inséré en partie dans un connecteur.
Les cosses ne sont pas conductrices après sertissage, elles doivent également être soudées pour percer l'isolant en émail. Après soudure, les broches ont été poussées jusqu'à la maison.
Étape 8: Flasher l'Arduino
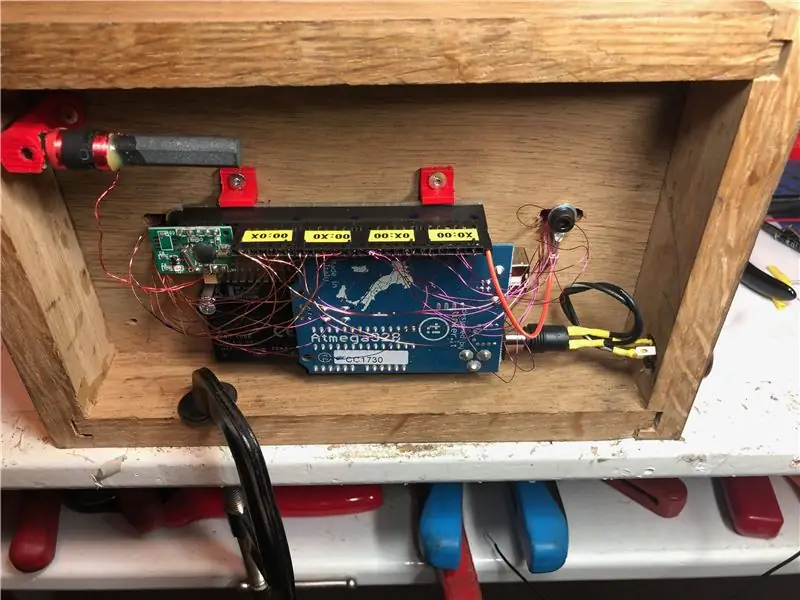
Le croquis Arduino peut être trouvé ici.
github.com/andypugh/LEDClock
Il y a deux croquis, un pour faire fonctionner l'horloge et un qui parcourt simplement les chiffres 0 à 9 sur chaque canal.
Cette esquisse de test vous permettra de déterminer quels en-têtes dans les broches de sortie doivent être échangés et si l'une des lignes de données BCD doit être échangée. (Si vous regardez le croquis, vous verrez que j'avais besoin d'échanger quelques canaux en raison de défauts de câblage, ceux-ci étaient plus faciles à corriger dans le logiciel).
Étape 9: Attendez avec frustration la synchronisation radio
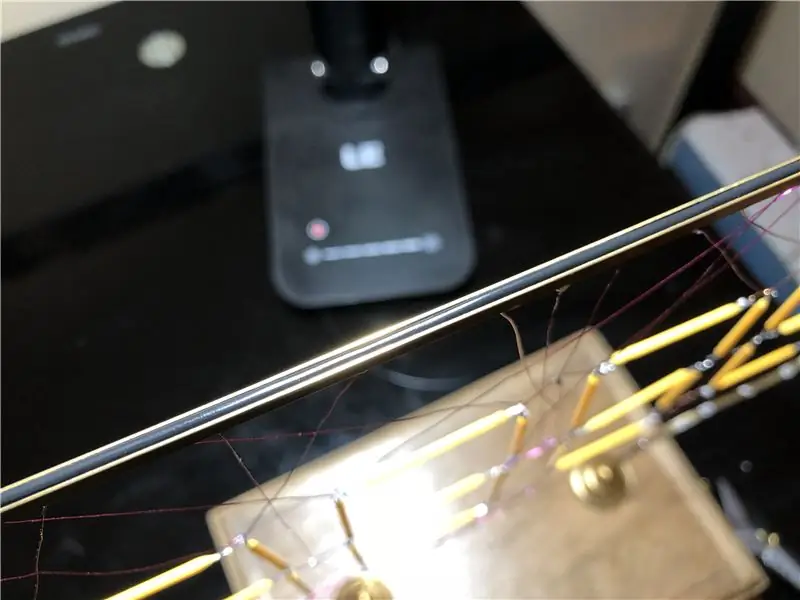

Le radio-réveil doit recevoir une minute complète de données. L'esquisse Arduino fait clignoter la barre centrale du chiffre des dizaines d'heures pour faire écho aux données radio entrantes, et les minutes montrent combien de bits de données sans défaut sont arrivés. S'il atteint 60, il y a de bonnes données et l'heure est affichée.
Dans un esprit de divulgation complète, il s'agit d'une simulation. Je n'arrivais à le synchroniser que lorsqu'il était alimenté par l'USB de mon Mac et lorsqu'il se trouvait dans un endroit non photogénique. Dans le cas de données réelles, les impulsions d'une seconde sont de longueurs différentes, pour coder le binaire.
Il y a aussi un élément paresseux (il brille, mais plus faible que les autres) La LED elle-même est bonne. Je crains un problème avec la puce du driver mais je vais essayer de recâbler d'abord le cuivre émaillé. (en fait, je vais probablement faire passer un fil supplémentaire)
Étape 10: Terminer
Les fils peuvent être maintenus dans le canal avec une longueur d'isolant dénudé d'environ 1,5 mm2. Mais attention à ne pas endommager les fils fins.
Avis de non-responsabilité: je ne prétends pas être le premier à avoir eu l'idée d'utiliser ces filaments pour une horloge, mais j'ai eu l'idée de manière indépendante. Lors de la recherche de pilotes appropriés, j'ai trouvé cet article de 2015 qui montre une horloge fabriquée à partir des mêmes filaments (bien que la sienne semble flexible, ce qui aurait été beaucoup plus facile).
Je suis peut-être le premier à les faire pendre dans l'espace sur leurs fils électriques, mais je ne voudrais pas parier là-dessus non plus.
Conseillé:
Horloge de retraite / Compte à rebours / Horloge Dn : 4 étapes (avec photos)
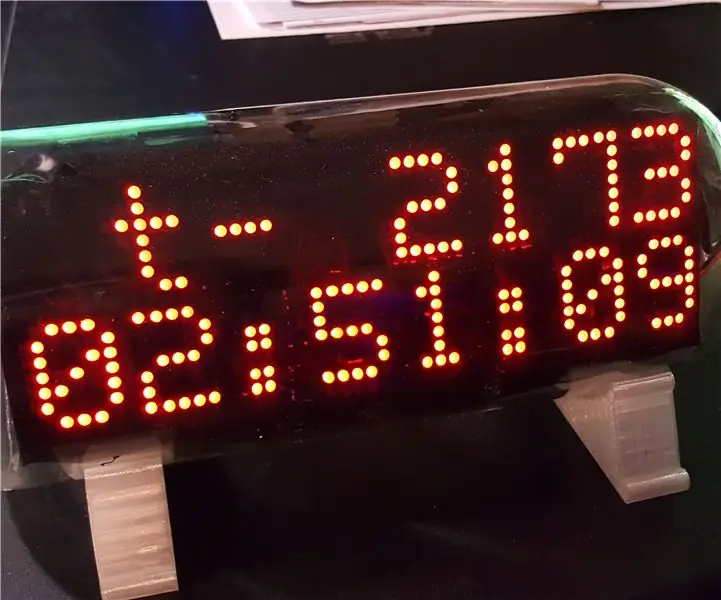
Retirement Clock / Count Up / Dn Clock: J'avais quelques-uns de ces écrans à matrice de points LED 8x8 dans le tiroir et je réfléchissais à ce que je devais en faire. Inspiré par d'autres instructables, j'ai eu l'idée de construire un affichage de compte à rebours/up pour compter jusqu'à une date/heure future et si l'heure cible p
ESP8266 Horloge réseau sans RTC - Nodemcu NTP Horloge Pas de RTC - PROJET HORLOGE INTERNET : 4 étapes
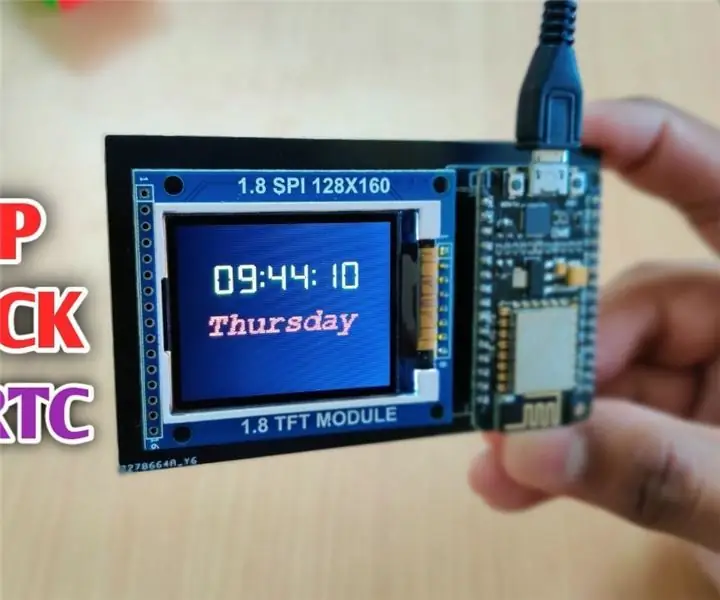
ESP8266 Horloge réseau sans RTC | Nodemcu NTP Horloge Pas de RTC | PROJET D'HORLOGE INTERNET: Dans le projet, un projet d'horloge sans RTC prendra du temps sur Internet en utilisant le wifi et l'affichera sur l'écran st7735
Horloge électronique C51 4 bits - Horloge en bois : 15 étapes (avec photos)
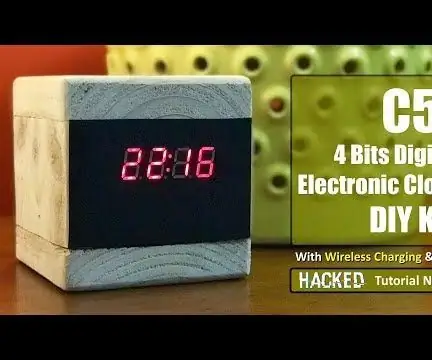
Horloge électronique C51 4 bits - Horloge en bois : J'ai eu du temps libre ce week-end, alors je suis allé de l'avant et j'ai assemblé cette horloge numérique électronique bricolage 4 bits de 2,40 AU $ que j'ai achetée sur AliExpress il y a quelque temps
Horloge d'animation SMART LED connectée au Web avec panneau de commande Web, synchronisation du serveur de temps : 11 étapes (avec images)
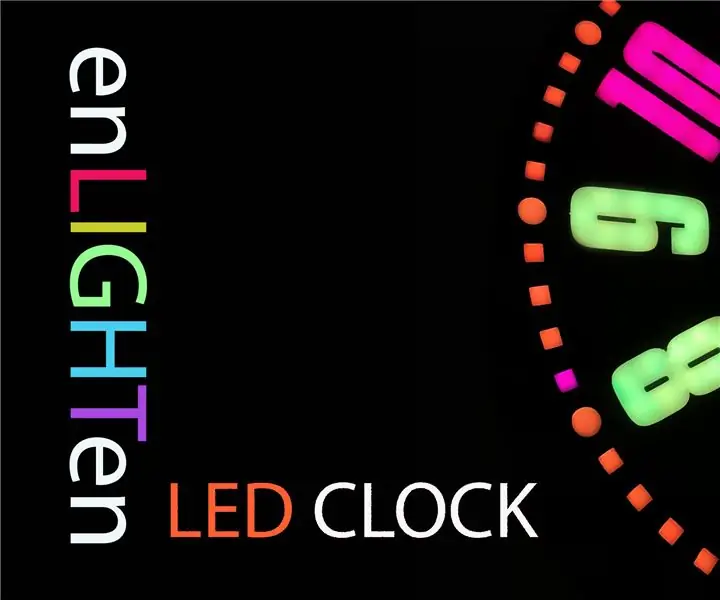
Horloge d'animation SMART LED connectée au Web avec panneau de commande Web, synchronisation du serveur de temps : l'histoire de cette horloge remonte à plus de 30 ans. Mon père a lancé cette idée quand j'avais à peine 10 ans, bien avant la révolution des LED - à l'époque où les LED atteignaient 1/1000 de la luminosité de leur éclat aveuglant actuel. Une véritable
Horloge LED en bois - Style analogique : 11 étapes (avec photos)
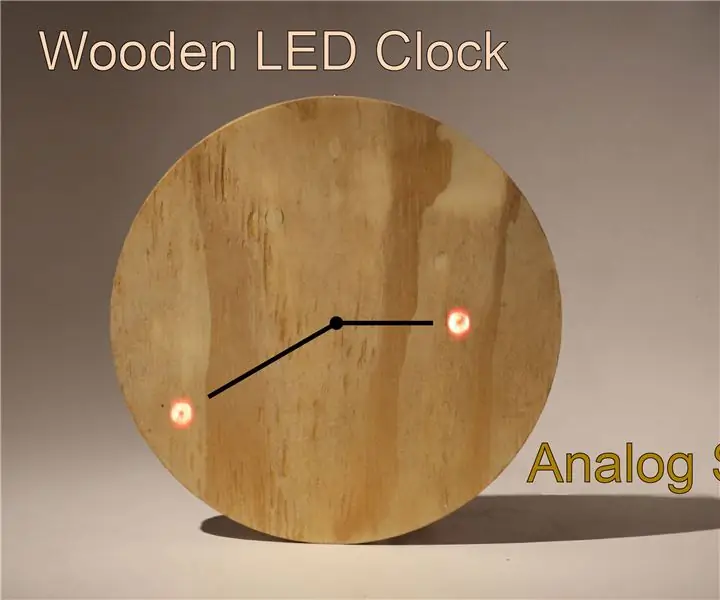
Horloge LED en bois - Style analogique : C'est une horloge LED en bois de style analogique. Je ne sais pas pourquoi je n'en ai jamais vu un auparavant..même si les types numériques sont très courants. Quoi qu'il en soit, c'est parti