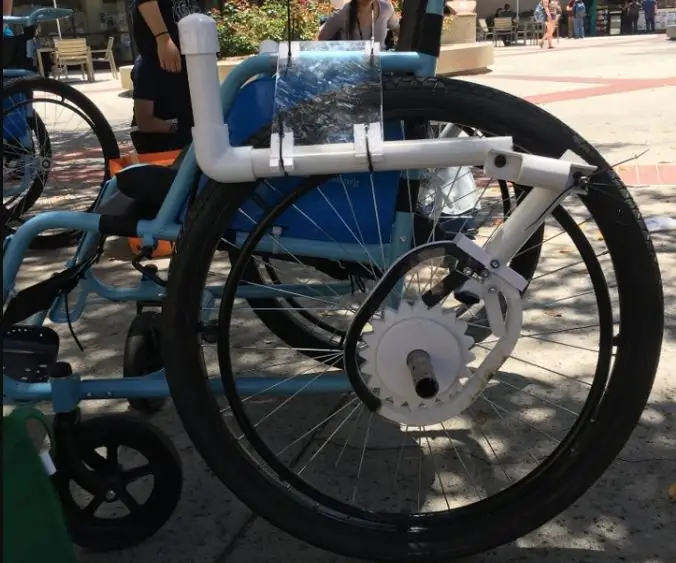
Table des matières:
- Étape 1: Créer le couvercle du boîtier extérieur pour le corps sur SolidWorks
- Étape 2: Créer le corps sur SolidWorks
- Étape 3: Créer le joint sur SolidWorks
- Étape 4: Créer le bras de levier/la poignée sur SolidWorks
- Étape 5: Créer l'accoudoir sur SolidWorks
- Étape 6: Créer l'engrenage sur SolidWorks
- Étape 7: Créer un cliquet sur SolidWorks
- Étape 8: Créer un bouton de direction sur SolidWorks
- Étape 9: Créer le support de tuyau
- Étape 10: Commencer l'assemblage sur SolidWorks
- Étape 11: Commandez des pièces chez McMaster-Carr
- Étape 12: Obtenir des pièces de la quincaillerie
- Étape 13: Fabrication des pièces
- Étape 14: Assemblez toutes les pièces
- Étape 15: Test itératif
- Étape 16: Page des cotisations
2025 Auteur: John Day | [email protected]. Dernière modifié: 2025-01-23 14:46
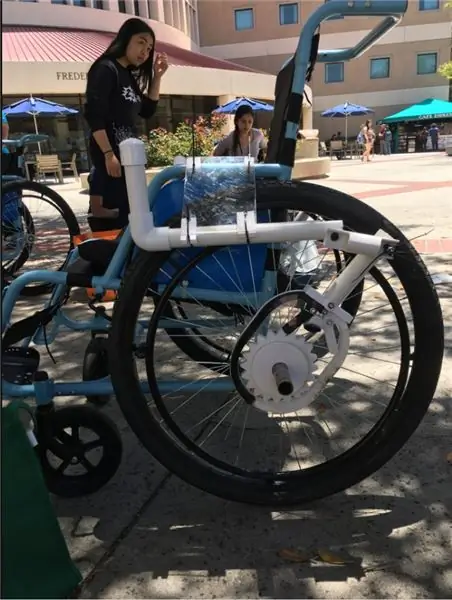
Le fauteuil roulant commun contient de nombreux défauts pour ceux qui ont une faiblesse des membres supérieurs ou des ressources limitées. Notre équipe a été chargée de concevoir un pilote de levier de fauteuil roulant pour les fauteuils roulants de la Free Wheelchair Mission qui permettrait aux utilisateurs d'aller plus loin dans leurs chaises et d'aider les personnes souffrant de faiblesse des membres supérieurs à utiliser les chaises. Le dispositif d'entraînement à levier pour fauteuil roulant Support System est un dispositif économique qui réduit considérablement le besoin de mouvement des épaules et réduit les niveaux de fatigue en utilisant des leviers horizontaux plutôt que verticaux, ce qui conviendrait aux patients affaiblis et aux patients des zones rurales. Le conducteur de bras de levier vertical typique se concentre trop sur les muscles des bras et des épaules, ce qui peut entraîner des complications pour les patients présentant des faiblesses des membres supérieurs. Par conséquent, notre équipe a conçu un pilote à levier horizontal qui vise à utiliser les muscles de la poitrine pour faciliter les personnes qui ne peuvent pas utiliser les muscles de leurs épaules.
Marché et proposition de valeur
Un moyen de traiter la douleur à l'épaule et la fatigue associées à l'utilisation d'un fauteuil roulant chez les personnes en particulier dans les villages ruraux avec des routes non pavées, notre levier de commande vise à atténuer le problème en utilisant un mouvement avant/arrière plutôt qu'un mouvement haut/bas avec un accoudoir amélioré pour le confort et le soutien. Étant donné que les villages ruraux et les routes non pavées sont généralement très rocailleux et non lisses, le patient devrait utiliser encore plus de force sur le bras de levier afin de déplacer son fauteuil roulant sur une certaine distance par rapport à un chemin lisse. Par conséquent, les personnes ayant des faiblesses des membres supérieurs dans les zones rurales sont encore plus gênées car elles ont besoin de plus de mouvement et de force pour se déplacer d'un endroit à l'autre, ce qui pose des problèmes car elles s'affaiblissent continuellement au fur et à mesure qu'elles continuent à utiliser les muscles de leurs épaules au quotidien.. Ainsi, en mettant en œuvre un levier de commande horizontal, les personnes des zones rurales présentant des faiblesses des membres supérieurs pourront non seulement se déplacer librement, mais également d'une manière qui réduit l'utilisation intense des muscles de l'épaule car ils utilisent plutôt la force de leur poitrine.
Analyse de coût
Nous avons décidé d'utiliser du PVC, de l'acrylique et de l'ABS. C'était un compromis de force et de coût. Les trois matériaux sont relativement moins chers, mais suffisamment solides pour fonctionner correctement. Le coût estimé est d'environ 170 $. Nous avions initialement prévu d'utiliser de l'aluminium pour la plupart des composants de notre levier d'entraînement, tels que le boîtier extérieur et les poignées de bras, car l'aluminium est moins cher que l'acier. Cependant, après avoir fait des recherches, nous avons vu que l'utilisation de feuilles et de tiges d'aluminium épaisses ne serait pas idéale en raison des coûts exceptionnels pour obtenir des quantités substantielles de métal. Au lieu de cela, nous avons trouvé des alternatives moins chères en utilisant différents matériaux pour différentes pièces. Nous avons utilisé une grande feuille d'acrylique pour l'enveloppe extérieure et découpé au laser la feuille en plus petites parties, ce qui a coûté environ 25 $. En comparaison, de grandes feuilles d'aluminium auraient coûté plus de 70 $. En outre, nous avons également décidé d'utiliser des tuyaux en PVC pour nos poignées de bras au lieu de tiges métalliques, car les tuyaux en PVC sont non seulement robustes, mais également extrêmement bon marché. Bien que les tiges en aluminium aient pu être plus robustes, nous aurions dépensé environ 30 $ de chaque côté du fauteuil roulant. En revanche, les tuyaux en PVC coûtaient environ 5 $. L'essentiel de nos coûts provient de l'impression 3D ABS. Parce que nous avons imprimé trois parties de notre système, le temps total pour imprimer toutes ces parties a pris au total environ 32 heures. En conséquence, avec le taux horaire d'utilisation de l'imprimante 3D, le total s'élevait à 130 $.
Conception de matériaux et de prototypage
-Tuyau PVC ~ 2,16 $
-Capuchon de douille en PVC ~ 1,66 $
- Coude à 90 degrés en PVC ~ 2,28 $
- Feuille acrylique ~ 24,98 $
- Engrenages ABS, cliquets ABS, boutons ABS ~ 130 $
- Vis en acier ~ 6,92 $
-Élastiques ~ $3.18
- Adhésif artisanal E6000 ~ 4,29 $
Étape 1: Créer le couvercle du boîtier extérieur pour le corps sur SolidWorks
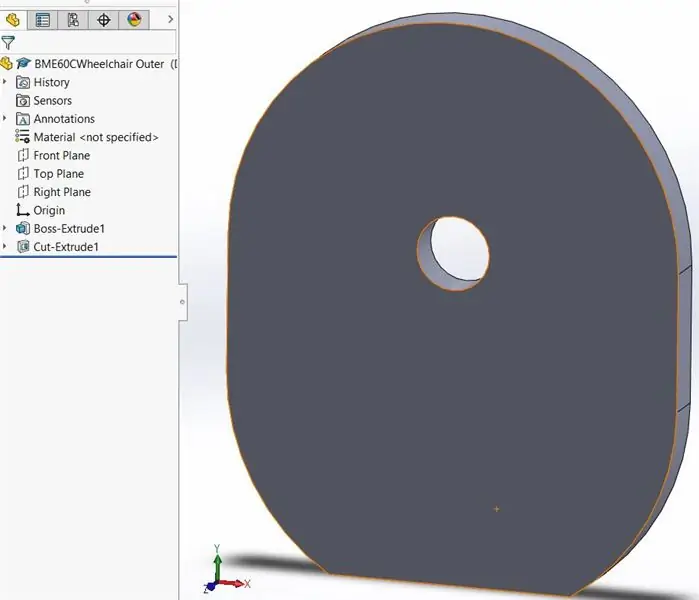
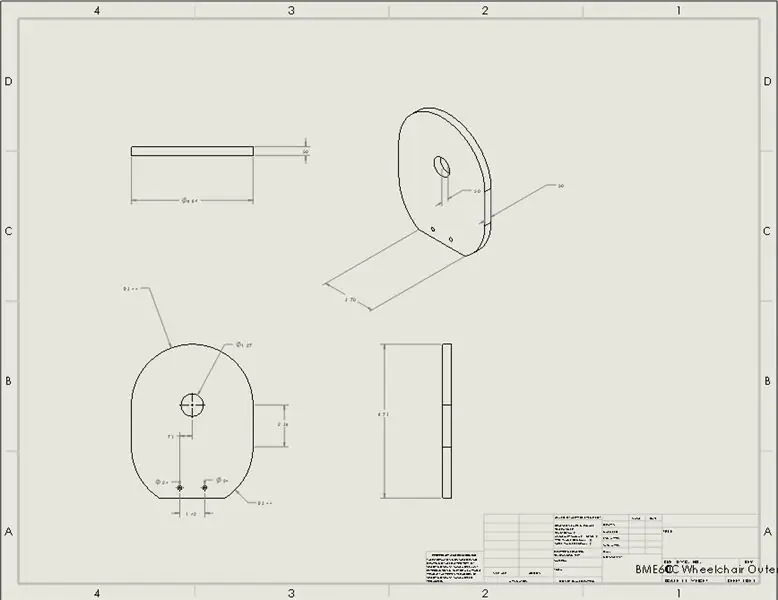
Avant de commencer l'ensemble du projet, définissez les dimensions à l'aide de MMGS.
À l'aide du plan de face, créez une nouvelle esquisse et tracez un cercle à l'origine d'un diamètre de 175 mm. Ensuite, dessinez deux lignes verticales aux tangentes du cercle qui sont toutes deux de 60 mm. Ensuite, dessinez des arcs tangents à la fin des deux lignes et connectez-les avec une ligne horizontale. Ensuite, à l'aide de la fonction "découper les entités", découpez la moitié inférieure du cercle à l'intérieur de la région.
Une fois l'esquisse terminée, le bossage extrude l'esquisse à l'aide d'une extrusion aveugle de 12,70 mm. Une fois l'extrusion terminée, ouvrez une nouvelle esquisse et tracez un cercle aligné avec le haut des lignes tangentes d'un diamètre de 32,20 mm et coupez l'extrusion en utilisant "à travers tout" faites un trou.
Pour créer les deux cercles du bas, ouvrez une nouvelle esquisse et dessinez deux cercles d'un diamètre de 6 mm et placez-les à 15 mm du bas et à 58,84 mm du centre de l'arc tangent. Une fois l'esquisse terminée, utilisez l'extrusion de coupe en utilisant "à travers tout" pour faire deux trous.
Étape 2: Créer le corps sur SolidWorks
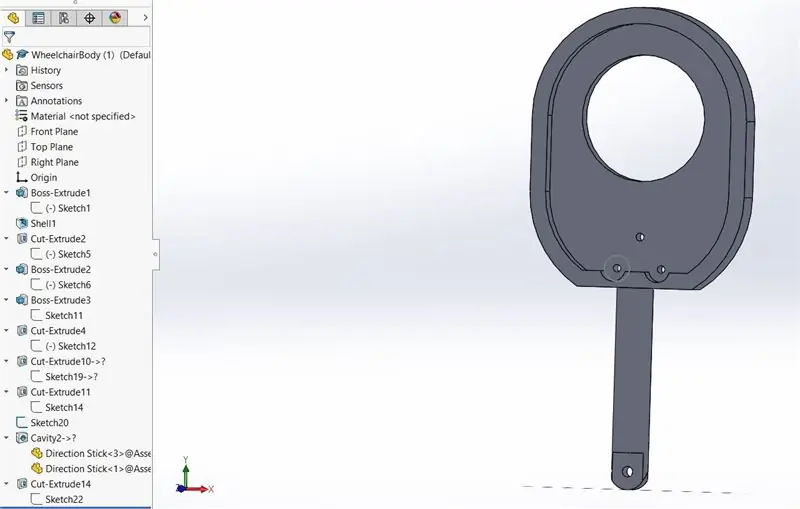
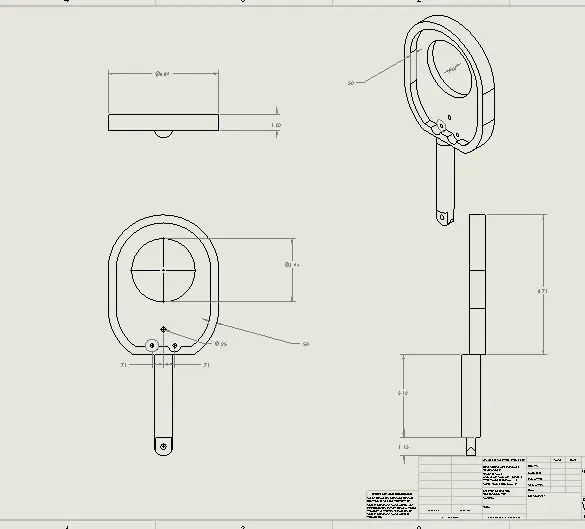
Pour commencer le corps, répétez le croquis comme dans la première partie pour créer la forme générale du corps et extrudez-le de 25,40 mm. Une fois la pièce extrudée, utilisez l'option coque sur l'une des faces de la pièce avec la dimension 12,70 mm.
Ensuite, ouvrez une nouvelle esquisse et dessinez un cercle au centre de la pièce d'un diamètre de 100 mm, à 133,84 mm du bas et à 87,50 mm des côtés de la pièce. Une fois l'esquisse terminée, coupez et extrudez en utilisant à nouveau "à travers tout" pour créer un trou.
Pour créer le levier, créez une nouvelle esquisse sur le plan supérieur et faites pivoter la pièce vers le bas. Commencez le croquis en réalisant un cercle d'un diamètre de 28,74 mm à la base de la pièce précédente et extrudez-le de 130 mm.
Une fois le levier créé, créez une nouvelle esquisse à la base du levier. Tracez deux lignes horizontales équidistantes de l'origine qui mesurent 25,10 mm de long. Ensuite, connectez les deux lignes avec des arcs tangents d'une hauteur de 14 mm. Une fois le croquis terminé, extrudez à l'aveugle le nouveau croquis de 30 mm.
À l'aide de la pièce extrudée la plus récente, créez une nouvelle esquisse sur le plan avant et esquissez un cercle à 14,95 mm du haut et à 12,55 mm du côté. Ensuite, coupez l'extrusion à travers tout pour créer un trou.
Avec l'ensemble du corps, esquissez deux trous au bas du corps avec un diamètre de 6 mm et une distance de 36 mm l'un de l'autre, de 15 mm du bas et de 58,84 mm du haut des arcs tangents. Après, coupez l'extrusion à travers tout pour créer deux trous.
Au bas de la pièce, créez une nouvelle esquisse. Tracez des lignes droites des deux côtés de 14,93 mm. Tracez une ligne horizontale de 28,74 mm pour relier les deux lignes. Dessinez un cercle qui a un rayon de 14,37 mm et alignez-le déjà sur le cercle au centre. Coupez-le pour faire un demi-cercle. Coupez l'extrusion à travers toute la figure en forme de rampe dans le bas de la pièce pour laisser un bord arrondi.
*Pour préparer la cavité, créez une nouvelle esquisse dans le plan arrière. Tracez un cercle avec un rayon de 20,57 mm à 15 mm du bas et à 58,84 de l'arc tangent latéral. Après avoir assemblé toutes les pièces, vous modifiez la pièce dans l'assemblage et utilisez la fonction d'empreinte pour créer les demi-cercles.
Sur le plan avant, faites une nouvelle esquisse. Dessinez un cercle au centre avec un diamètre de 6,35 mm entre le grand cercle et les deux petits cercles près du bas. Faites le cercle à 40,13 mm du bas et à 33,70 mm de l'arc tangent sur les côtés. Après, coupez et extrudez à travers tout pour créer un petit cercle au centre.
*Cette étape est à poursuivre ultérieurement après avoir assemblé toutes les pièces.
Étape 3: Créer le joint sur SolidWorks
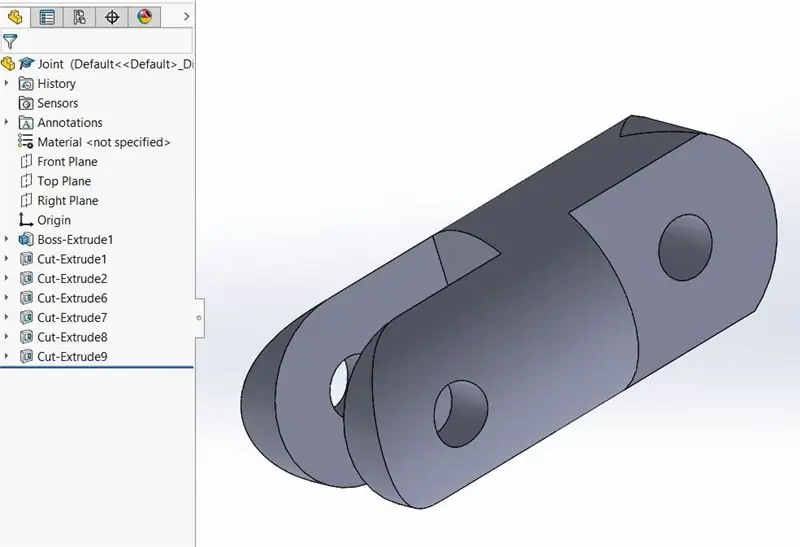
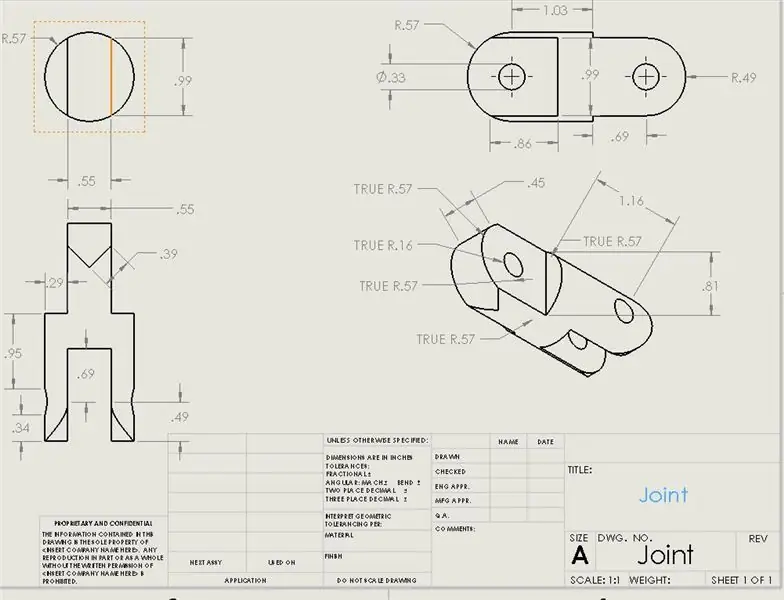
Pour commencer la jointure, commencez par créer un nouveau croquis sur la plaque avant et tracez un cercle d'un diamètre de 28,74 mm. Extrudez à l'aveugle le cercle qui vient d'être esquissé de 120 mm.
Ensuite, faites pivoter la pièce et esquissez au dos. Tracez deux lignes verticales d'une longueur de 25,10 mm et de 7,37 mm du bord du cercle. et coupez l'extrusion en utilisant "à l'aveugle" et une profondeur de 30 mm pour les deux régions.
Ensuite, en regardant depuis le plan de droite, dessinez un cercle sur la région que nous venons de couper. Le diamètre doit être de 8,38 mm avec une distance de 12,55 mm du bord supérieur et de 14,95 mm du bord latéral. Faites une coupe aveugle de 30 mm.
Sur le plan de droite, tracez des lignes droites des deux côtés de 15,05 mm. Tracez une ligne verticale de 28,74 mm pour relier les deux lignes. Dessinez un cercle qui a un rayon de 14,37 mm et alignez-le déjà sur le cercle au centre. Coupez-le pour faire un demi-cercle. Coupez l'extrusion à travers toute la figure en forme de rampe dans le bas de la pièce pour laisser un bord arrondi.
Après, en regardant depuis le plan arrière, esquissez deux lignes verticales d'une longueur de 25,10 mm et 7 mm du centre. Faites une coupe aveugle avec une profondeur de 35 mm.
Sur le plan de droite, esquissez un cercle sur la partie droite avec le centre à 17,24 mm du bord gauche de la pièce, coupez à l'aveuglette à travers tout pour créer un cercle
Sur le plan de droite, répétez la figure en forme de rampe sur le côté gauche de la pièce.
Étape 4: Créer le bras de levier/la poignée sur SolidWorks
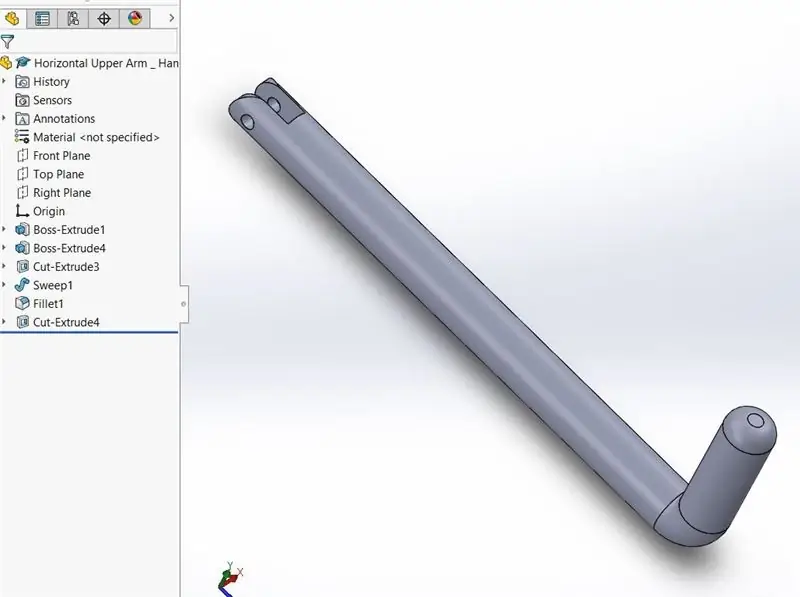
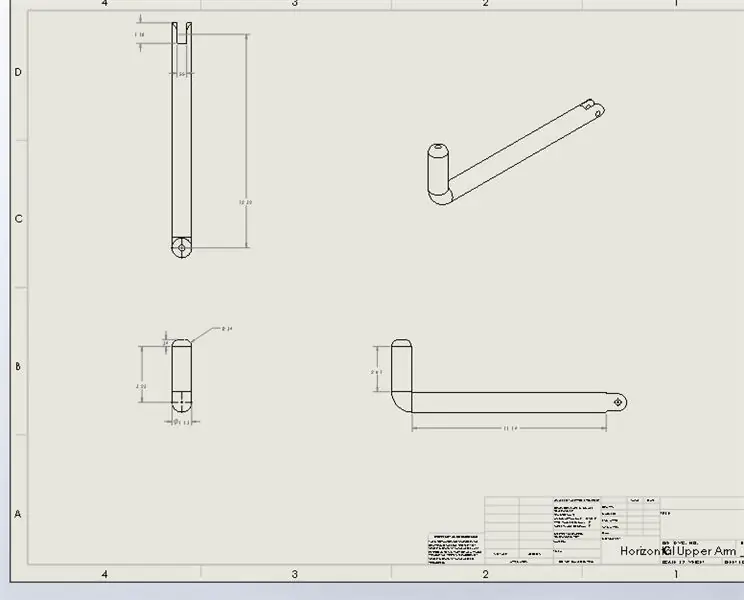
Sur le plan avant, esquissez un cercle d'un diamètre de 28,75 mm à l'origine. Boss l'extrude de 275 mm.
Ensuite, allez au plan arrière et esquissez deux lignes verticales d'une longueur de 25,10 mm à une distance de 7 mm du centre. Extrudez les deux lignes de sorte qu'il y ait un espace au milieu avec une dimension d'extrusion de 35 mm.
Sur la pièce que nous venons d'extruder, esquissez un cercle d'un diamètre de 8,40 mm avec une distance de 17,76 mm du centre du cercle au bord et de 12,56 mm du bas de la pièce. Coupez l'extrusion à travers tout pour créer un trou.
Sur le plan de droite, créez une ligne courte d'une longueur de 9,24 mm qui se connecte à l'extrême gauche de la pièce. Tracez un arc avec un rayon de 30 mm. Ensuite, tracez une ligne verticale qui relie l'autre extrémité de l'arc avec une longueur de 76,39 mm. Une fois l'esquisse terminée, balayez l'esquisse.
Après, arrondissez le haut de la pièce que nous venons de balayer de 10 mm.
Enfin, sur le plan de droite, tracez des lignes horizontales droites des deux côtés de la pièce avec le trou que nous avons créé et d'une longueur de 17,78 mm. Tracez une ligne verticale de 25,10 mm pour relier les deux lignes. Dessinez un cercle qui a un rayon de 12,56 mm et alignez-le déjà sur le cercle au centre. Coupez-le pour faire un demi-cercle. Coupez l'extrusion à travers toute la figure en forme de rampe dans le bas de la pièce pour laisser un bord arrondi.
Étape 5: Créer l'accoudoir sur SolidWorks
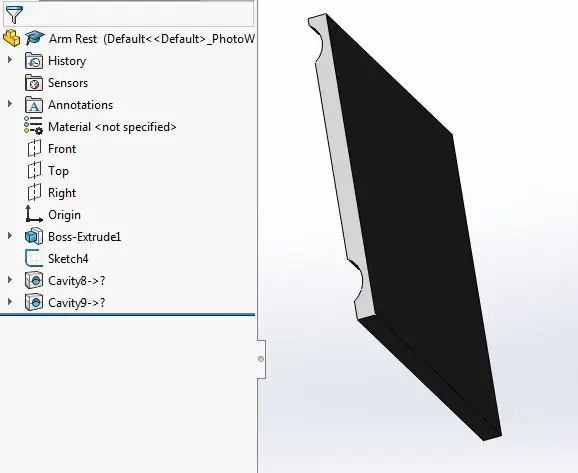
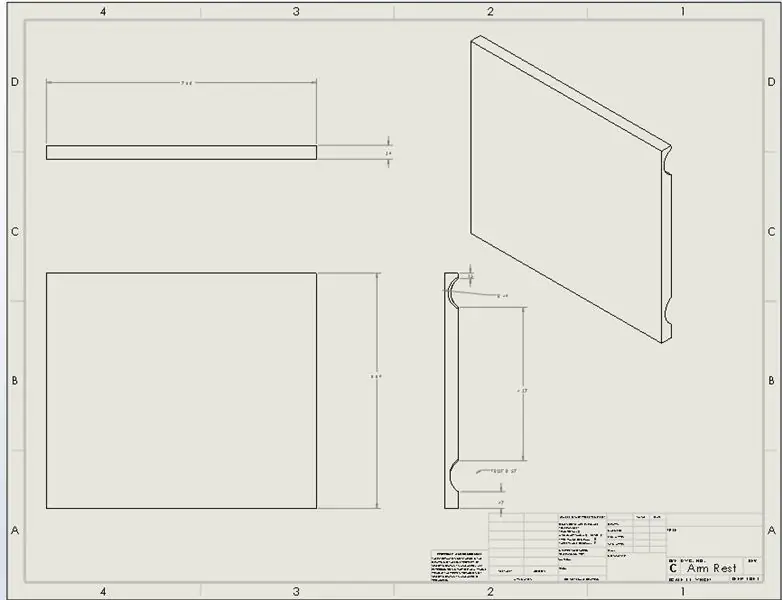
Sur le plan avant, esquissez un rectangle d'une hauteur de 170 mm et d'une longueur de 195 mm et faites une extrusion aveugle de 10 mm.
* Après l'assemblage, utilisez la fonction de cavité pour créer les retraits sur le prisme rectangulaire
Étape 6: Créer l'engrenage sur SolidWorks
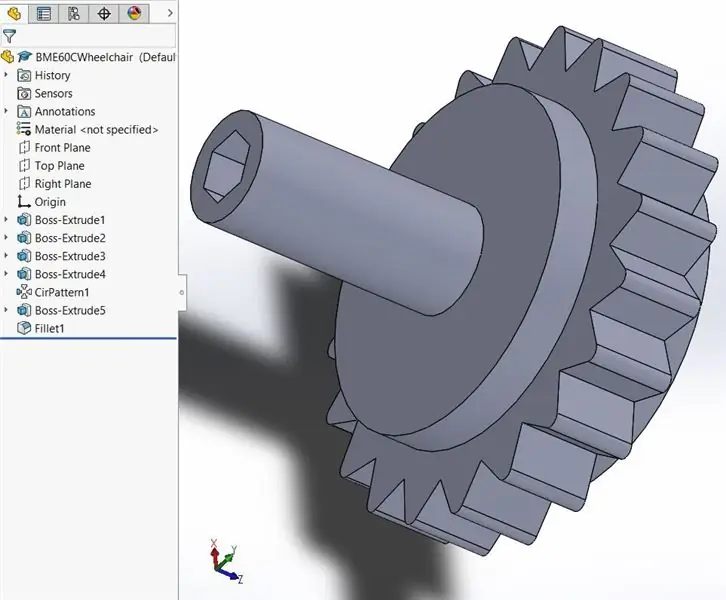
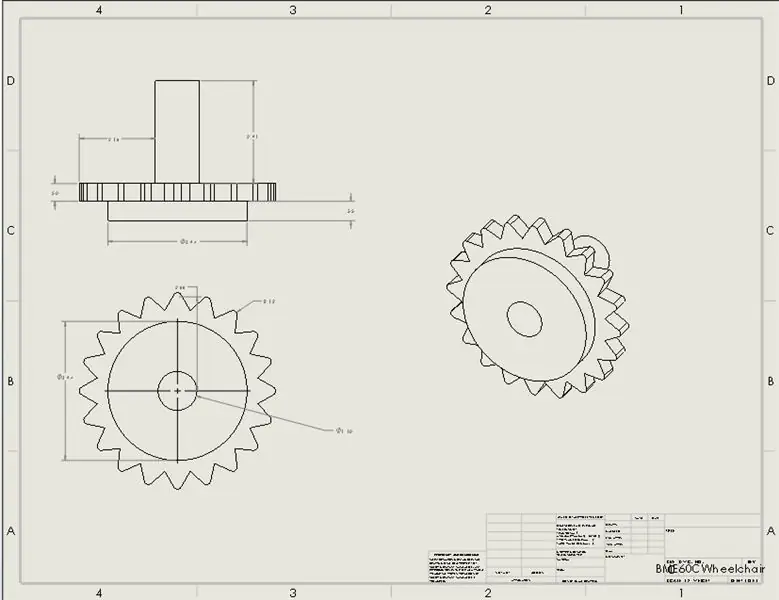
Pour commencer l'engrenage, créez une nouvelle esquisse sur le plan avant et dessinez deux cercles à partir du même point avec les diamètres de 25,40 mm et 31,75 mm. Ensuite, extrudez le bossage à l'aide d'une extrusion aveugle à 30 mm.
Une fois l'extrusion terminée, créez une autre esquisse sur le plan avant et dessinez un autre cercle de 31,75 mm de diamètre et extrudez 20 mm.
Ensuite, esquissez sur le plan avant un cercle de 100 mm de diamètre et extrudez-le à 12,70 mm.
Sur le dessus de la pièce que nous venons d'extruder, dessinez un triangle équilatéral de 30 mm de côté. Extrudez le triangle 12.70mm.
Une fois l'extrusion terminée, utilisez la fonction de motif circulaire pour avoir 20 triangles uniformes tout autour de la pièce. Ensuite, arrondissez tous les bords des triangles.
Sur le plan avant, esquissez un autre cercle de 100 mm de diamètre et extrudez-le de 13,97 mm.
Pour créer le trou au milieu de l'engrenage, esquissez un cercle sur le plan arrière avec un diamètre de 27,94 mm et coupez l'extrusion jusqu'à la surface.
Étape 7: Créer un cliquet sur SolidWorks
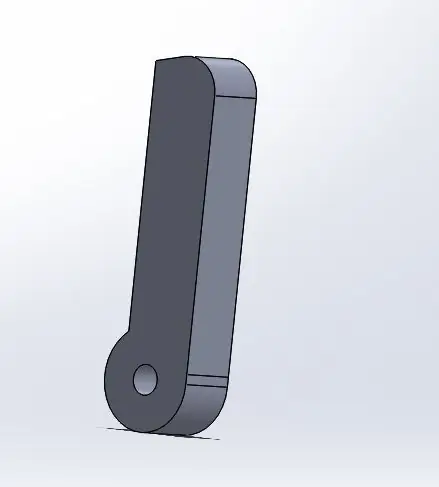
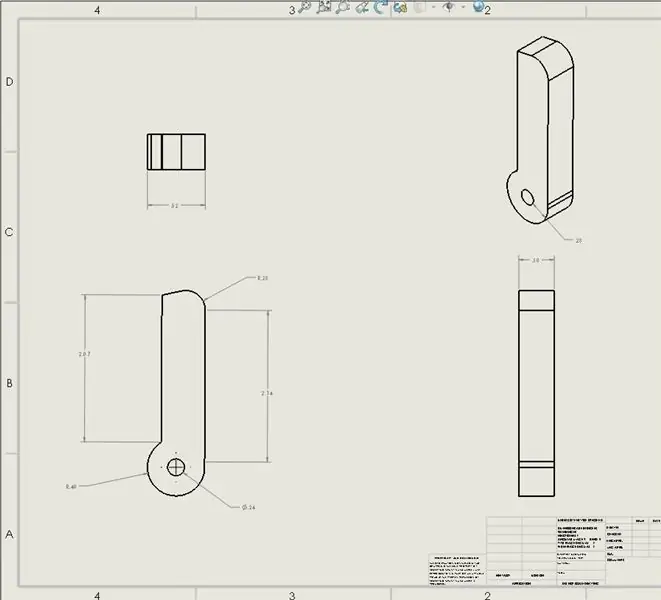
Sur le plan avant, tracez une ligne verticale d'une longueur de 2,07 pouces. Ensuite, tracez un arc d'un rayon de 0,40 pouce relié au bas de la ligne verticale. Tracez également une ligne horizontale reliée au bord supérieur de la ligne verticale. À l'aide des dimensions intelligentes, cliquez sur le bord supérieur, puis sur la ligne verticale et définissez l'angle sur 78,00 degrés.
Une fois l'angle défini, tracez une autre ligne verticale qui se connecte à la ligne inclinée d'une longueur de 2,14 pouces. Puis raccordez le bord de cette ligne avec la ligne horizontale avec un rayon de 0,28 pouces.
Une fois l'esquisse terminée, extrudez le bossage à l'aide d'une extrusion aveugle de 0,5 pouces. Pour créer le trou au milieu, esquissez un cercle qui a un rayon de 0,12 pouce au centre de la pièce et utilisez l'extrusion de coupe à travers tout.
Étape 8: Créer un bouton de direction sur SolidWorks
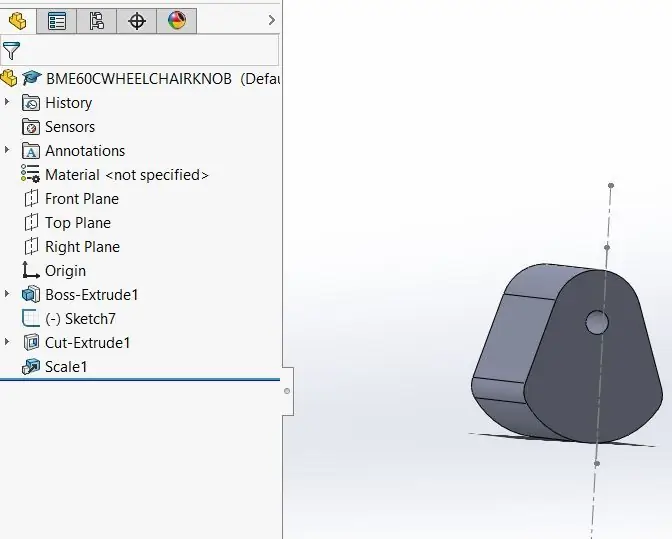
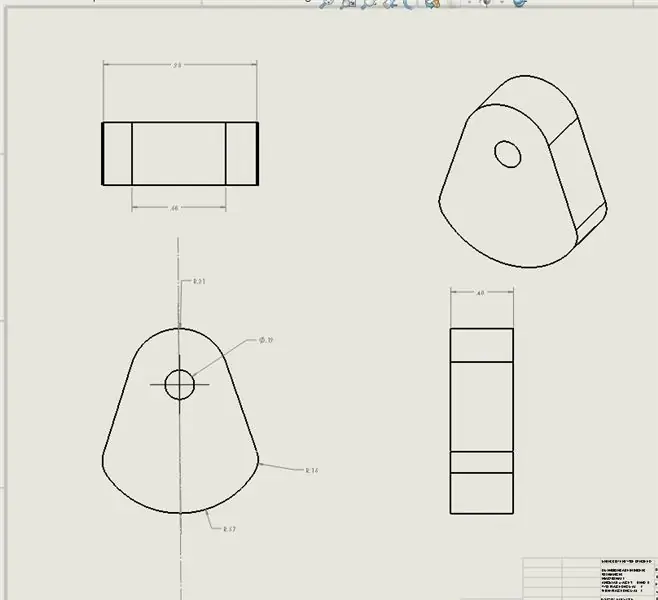
Sur le plan avant, esquissez une ligne médiane verticale. Ensuite, en haut de la ligne centrale, esquissez un arc avec un rayon de 10 mm. Ensuite, tracez des deux côtés des lignes obliques d'une longueur de 18,26 mm. Ensuite, tracez un arc des deux côtés avec un rayon de 5 mm. Pour connecter les deux côtés, tracez un autre arc avec un rayon de 18 mm. Extrudez l'esquisse en utilisant l'extrusion aveugle 12.70mm.
Pour créer un trou, esquissez un cercle d'un diamètre de 5,90 mm dont le centre est à 8 mm de l'origine. Utilisez la coupe extrudée jusqu'à la surface.
Mettez la pièce à l'échelle autour du centroïde avec un facteur d'échelle de 0,8 mm.
Étape 9: Créer le support de tuyau
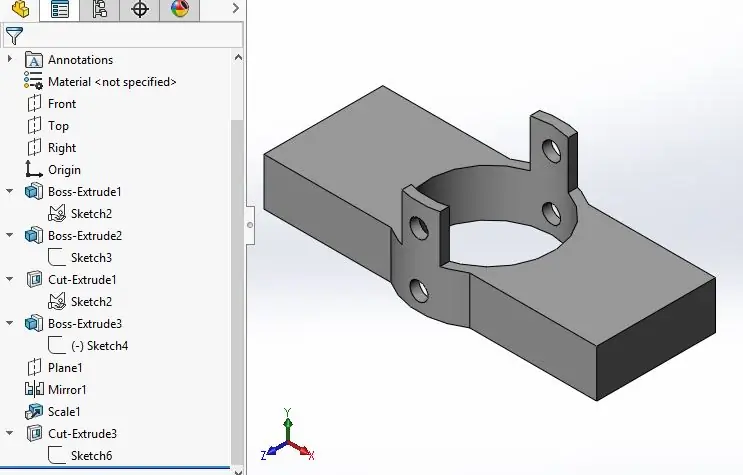
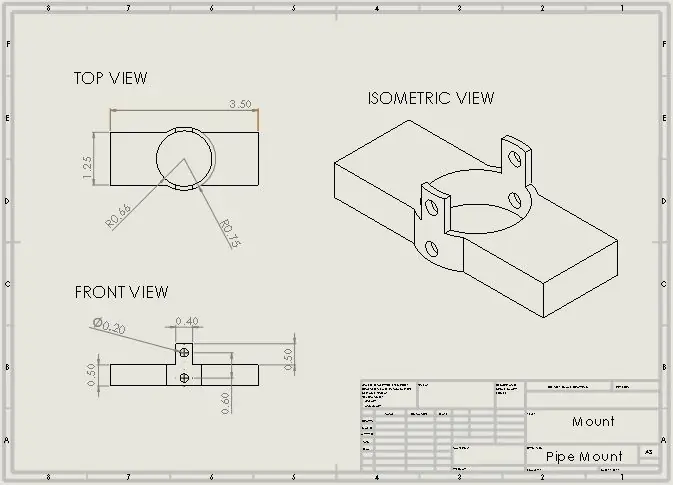
Afin de créer le support de tuyau qui fixera le bras de levier au corps de l'engrenage, commencez par un croquis de deux cercles. Le cercle intérieur doit avoir le diamètre du tuyau en PVC afin qu'il puisse glisser facilement autour, il doit donc mesurer 1,3125 pouces. Le cercle extérieur devrait être d'environ 1,5 pouces. Assurez-vous que les deux cercles sont concentriques et extrudez la partie entre les deux cercles de 0,5 pouces. Ensuite, esquissez un rectangle qui correspond à la face inférieure du boîtier extérieur de l'engrenage. Ce serait un rectangle de 3,5 pouces par 1,25 pouces. Centrez ce rectangle autour du cercle en définissant le bord long du rectangle à 1,75 pouces du centre du cercle et le bord court du rectangle à 0,63 pouces du centre du cercle. Extrudez le rectangle de 0,5 pouces. Étant donné que certaines parties du rectangle se trouvent à l'intérieur du cercle intérieur, coupez et extrudez le cercle intérieur pour l'effacer. Ensuite, à partir du plan supérieur de la pièce, esquissez une ligne médiane du cercle à la partie extérieure de l'arête extrudée. À partir de ce point central sur le bord extrudé, esquissez un rectangle de 0,2 pouces des deux côtés. Extrudez ce petit rectangle de 0,5 pouces. Créez un plan de référence orienté vers l'avant passant par le centre de la pièce et utilisez la fonction miroir pour créer un rectangle extrudé identique de l'autre côté du cercle.
Lorsque vous imprimez des pièces en 3D, il est toujours judicieux de tout mettre à l'échelle légèrement afin d'éviter les interférences lors du placement de la pièce sur l'assemblage. Dans ce cas, la partie entière a été agrandie de 1,05. Enfin, esquissez deux cercles de 1/4 de pouce de diamètre définis pour être sur la face avant du centre de la pièce avec un sur le petit rectangle et un sur le côté du cercle. En vous assurant que les deux cercles sont liés verticalement, ils peuvent ensuite être coupés à travers toute la pièce, en découpant quatre cercles au total. Il s'agirait de trous pour lesquels les boulons peuvent être placés pour relier le PVC au corps principal du carter d'engrenage.
Étape 10: Commencer l'assemblage sur SolidWorks
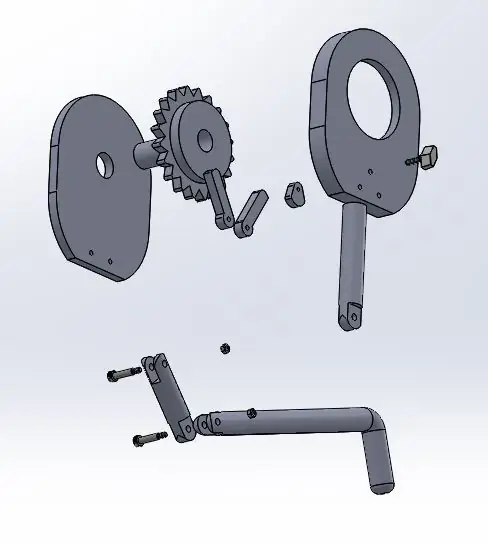
Tout d'abord, insérez toutes les pièces qui ont été créées au cours des étapes précédentes avec le bouton extérieur, les vis et les écrous du commerce, faisant du corps du fauteuil roulant le composant de base.
Commencez par accoupler le corps et l'engrenage en cliquant sur le bord de l'engrenage et le bord du corps et utilisez un accouplement concentrique. Ensuite, cliquez sur la face de l'engrenage et le corps pour créer une contrainte coïncidente.
Ensuite, assemblez le corps et le bouton de direction en cliquant sur la face du bouton de direction et le corps pour créer une contrainte coïncidente.
Maintenant, assemblez le bouton extérieur et le corps du fauteuil roulant en cliquant à la fois sur la face du bouton extérieur et sur le corps pour créer un accouplement coïncident.
Créez une contrainte concentrique en cliquant sur la face du corps et la face du bouton extérieur.
Ensuite, créez une contrainte concentrique en cliquant sur la face du bouton de direction et le bord du corps.
Cliquez maintenant sur les faces du corps et du cliquet pour créer une contrainte coïncidente et répétez l'opération pour l'autre cliquet.
Créez une contrainte tangente en cliquant sur la face du bouton de direction et du cliquet et répétez l'opération pour l'autre cliquet.
Ensuite, créez une contrainte coïncidente en cliquant sur la face du corps et le boîtier extérieur et créez une contrainte concentrique en cliquant sur la face du corps et le bord du boîtier extérieur. Ensuite, rendez la face du corps et la face du boîtier extérieur parallèles.
Créez un angle limite qui a une valeur maximale de 78 degrés et une valeur minimale de 35 degrés pour la face du corps et la face du cliquet et répétez pour l'autre cliquet
Ensuite, assemblez l'articulation et le corps en cliquant sur la face des deux pour créer une contrainte concentrique. Créez ensuite une contrainte de largeur centrée pour les deux faces de la liaison et du corps.
Ensuite, créez une contrainte concentrique pour le bord du bras de levier et le bord du joint. Créez une autre contrainte de largeur centrée pour les deux faces du joint et le bras de levier.
Réalisez une autre contrainte concentrique pour la face du joint et la vis. Ensuite, créez une contrainte tangente en cliquant sur la face du joint et la face de la vis.
Sur le plan de droite, esquissez deux lignes d'axe pour une future référence d'accouplement, la première ligne étant l'endroit où le corps rencontre l'articulation et la seconde l'endroit où l'articulation rencontre le bras de levier.
Ensuite, créez une contrainte concentrique en cliquant sur la face du bras de levier et la deuxième vis. Une fois la contrainte effectuée, créez une autre contrainte tangente avec la face des deux composants.
Avec le premier axe dessiné précédemment, assemblez le bord du premier écrou et l'axe pour créer une contrainte concentrique.
Utilisez un compagnon coïncident pour la face de la première vis et du premier écrou et répétez l'opération pour la deuxième vis et l'écrou.
Faites un compagnon concentrique avec le bord du deuxième écrou et le deuxième axe.
Créez une autre contrainte concentrique avec la face du corps et la face externe de la première vis. De plus, créez une contrainte coïncidente pour ces pièces.
Réalisez une contrainte concentrique pour la face du cliquet et la face externe de la troisième vis.
Créez une contrainte coïncidente avec la face du corps et la face externe de la troisième vis.
Ensuite, créez une autre contrainte concentrique en cliquant sur la face du boîtier externe et la face externe de la troisième vis et faites-les coïncider.
Créez une contrainte concentrique en cliquant sur la face du corps et la face du cliquet et faites-les coïncider. Répétez l'opération pour l'autre cliquet.
Créez une contrainte concentrique en cliquant sur la face du bouton de direction et le bouton extérieur.
Enfin, assemblez la face du corps et le bord du bouton de direction pour créer une contrainte concentrique.
Étape 11: Commandez des pièces chez McMaster-Carr
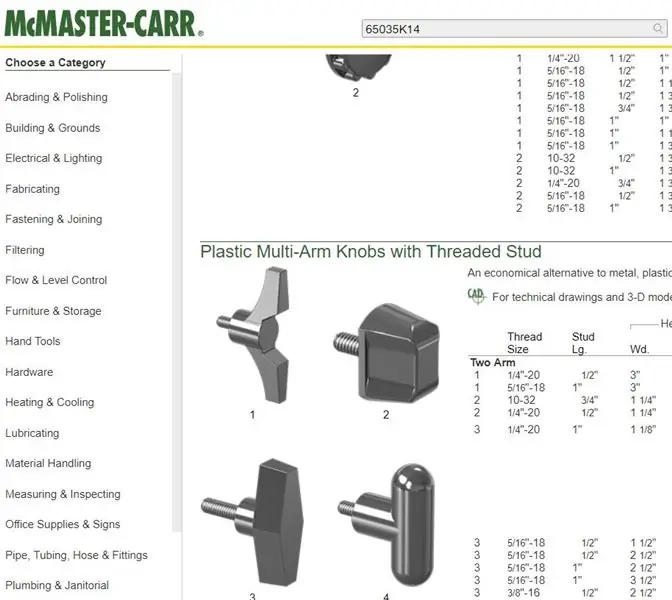
Commandez le bouton en plastique à deux bras (bouton extérieur), la vis à épaulement en alliage d'acier, les écrous hexagonaux en acier et les attaches de câble chez McMaster-Carr. Les numéros d'article sont respectivement 65035K14, 92981A205, 90592A016 et 70215K61.
Étape 12: Obtenir des pièces de la quincaillerie
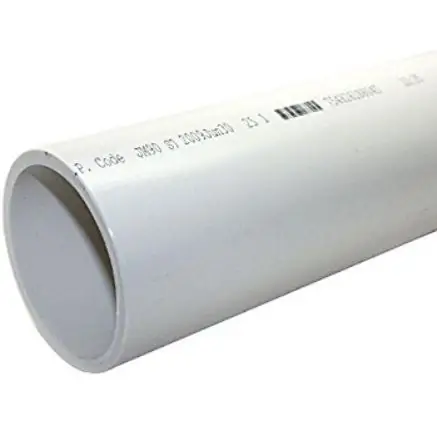
Dans une quincaillerie locale, procurez-vous les éléments suivants:
- Feuille d'acrylique 18" x 24" x.220"
- Adhésif transparent (Adhésif E6000)
- Capuchon de douille en PVC 1 (2)
- Tuyau à bout lisse en PVC de 1 x 10'
- Coude 1 PVC 90 degrés (2)
Étape 13: Fabrication des pièces
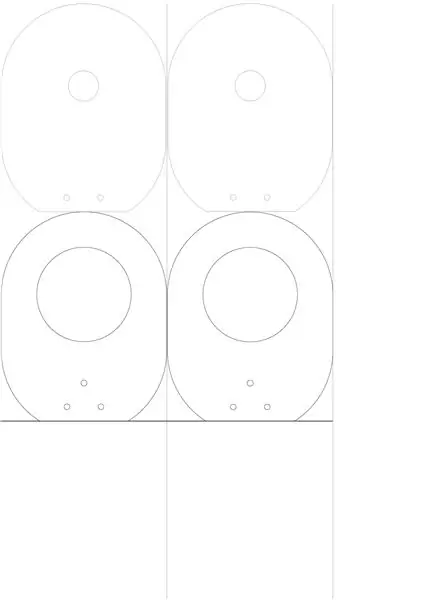
Pièces imprimées en 3D: préparez les pièces SolidWorks et convertissez-les en fichiers STL. De là, placez les pièces dans le logiciel Makerware et disposez les pièces à imprimer (coque du corps, engrenages, pièce de montage, cliquets, bouton de direction, empreintes des accoudoirs*). Si les pièces ne tiennent pas sur le lit de l'imprimante, attendez pour réimprimer à nouveau. Lors de l'impression, veillez à ajouter des supports et des radeaux afin d'éviter que les impressions échouent.
Pièces découpées au laser: En utilisant l'acrylique 18" par 24", les plaques avant et arrière de l'enveloppe extérieure du corps peuvent être fabriquées. Cela peut être fait en prenant la face avant des deux plaques sur SolidWorks et en les enregistrant toutes les deux en tant que fichier DWG. Ceux-ci peuvent ensuite être téléchargés vers le logiciel de découpe laser (dans ce cas Epilog) dans lequel leur orientation peut être configurée comme le montre l'image. Deux de chaque seront découpés dans l'acrylique et dans le matériau restant, deux rectangles seront découpés. Les rectangles serviront d'accoudoirs.
Pièces coupées à la main: Prenez les tuyaux et coupez-les en différentes longueurs (deux de 4,5 pouces pour la poignée, deux de 4,5 pouces pour le joint, deux de 6,5 pouces pour le levier et deux de 13,25 pouces pour le bras). À partir de là, coupez les morceaux de bras de 13,25 pouces à une extrémité (30 ou 35 mm) au milieu de l'autre côté du tuyau et percez un trou de 1/4 à 15 mm des bords du tuyau. Coupez et percez deux des Des pièces de joint de 4,5 pouces de la même manière mais des deux côtés du tuyau en PVC commun. Faites de même (coupez et percez) d'un côté du bras de levier, tuyau de 6,5 pouces.
*Les retraits d'accoudoir ou l'ensemble de l'accoudoir de l'étape précédente peuvent être utilisés.
Étape 14: Assemblez toutes les pièces
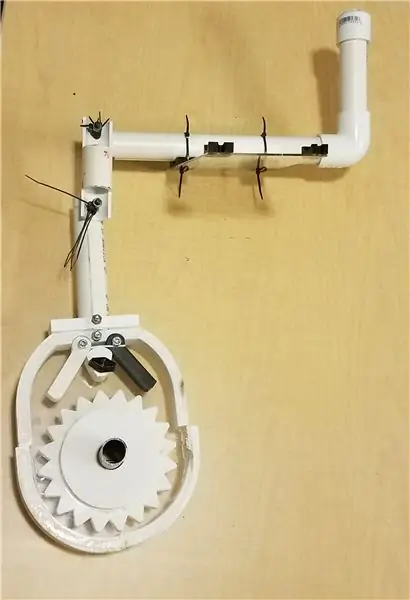
Assemblage du corps:
Prenez les pièces extérieures du corps découpées au laser et les pièces de coque imprimées en 3D. Prenez un côté du boîtier extérieur et collez les morceaux de coque en conséquence sur les bords du boîtier. Ensuite, prenez un élastique et enroulez-le autour des deux cliquets. Placez les cliquets dans leurs emplacements respectifs et utilisez le boulon partiellement fileté et placez-le dans le trou du corps et des cliquets. Ensuite, prenez le bouton de direction et le bouton en plastique. Placez le bouton en plastique à travers le boîtier extérieur et tournez les deux ensemble avec le boîtier extérieur entre les deux. Enfin, placez l'engrenage dans son trou respectif et placez le couvercle supérieur du boîtier extérieur sur l'engrenage et collez la coque sur le boîtier extérieur supérieur. Laissez reposer et sécher. N'oubliez pas de fixer également les deux boulons partiellement filetés avec les écrous hexagonaux après avoir placé et collé le couvercle supérieur sur la coque.
Prenez le tuyau en PVC à levier de 6,5 pouces et collez-le sur la face inférieure du corps. À partir de là, laissez reposer et sécher. Prenez la pièce montée et faites-la glisser à travers le tuyau jusqu'à ce qu'elle repose à plat sur la face inférieure du corps. Prenez un foret de 1/4 pouce et percez les trous sur le tuyau et à travers le corps à ses endroits respectifs. Fixez les boulons avec un écrou hexagonal.
Assemblage de l'accoudoir:
Avec l'accoudoir, il suffit de placer et de coller les empreintes sur les 4 coins de l'accoudoir. Percez ensuite deux trous (trous de 5/32'') de chaque côté des entailles et placez-y des attaches zippées. Les plus grands renfoncements peuvent ensuite être alignés et attachés au tuyau en PVC de 13 pouces du bras de levier. Le plus petit renfoncement doit s'aligner et plus tard être attaché au bras du fauteuil roulant avant utilisation.
Assemblage du bras de levier:
Placez le capuchon sur le tuyau de la poignée de 4,5 pouces et placez le coude solidement de l'autre côté. Avec l'autre ouverture du coude, placez le tuyau de bras de 13 pouces et connectez-le à un côté du joint (tuyau de 4,5 pouces) avec un boulon à épaulement. De l'autre côté du joint, prenez un autre boulon à épaulement et joignez-le au bras de levier (tuyau de 6,5 pouces). Prenez un écrou hexagonal et fixez le boulon à épaulement. Étant donné que les boulons à épaulement sont partiellement filetés, les joints dans lesquels il est fixé peuvent être fragiles. Afin de rendre les joints plus serrés et plus sûrs, placez environ cinq fermetures éclair autour de chaque boulon à épaulement pour serrer chaque joint.
Étape 15: Test itératif
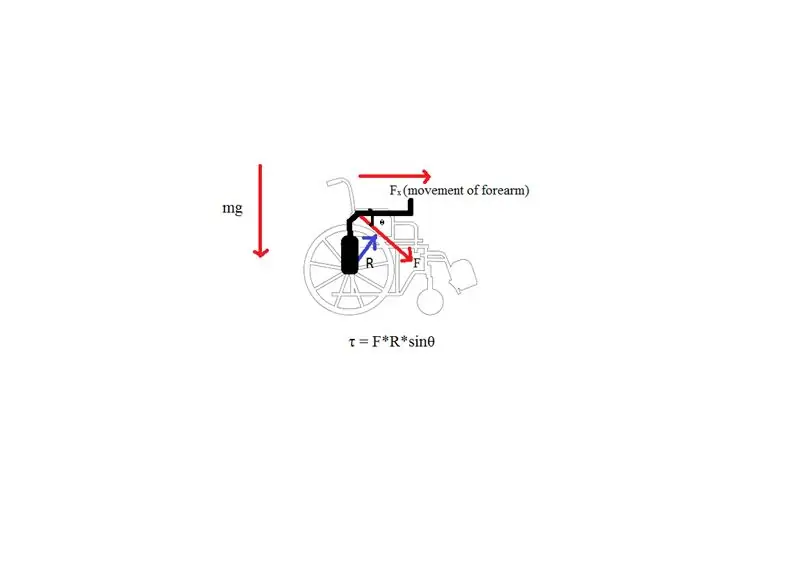
Pour tester, assurez-vous d'avoir accès à l'un des fauteuils roulants.
Fixez le bras de levier à la roue. Assurez-vous que les pièces s'adaptent là où elles sont censées aller et assurez-vous que certaines pièces sont parallèles aux parties respectives du fauteuil roulant, comme l'accoudoir. Assurez-vous que les trous percés dans le tuyau en aluminium et le corps du bras de levier sont alignés. Si les pièces sont disproportionnées, revenez en arrière et modifiez les dimensions.
Une fois que les dimensions et les relations sont toutes correctes, demandez à un testeur de s'asseoir sur le fauteuil roulant et d'utiliser le bras de levier. Comme indiqué sur le diagramme du corps libre, le testeur poussera horizontalement vers l'avant pour créer une force diagonale qui serait utilisée pour créer un couple et propulser le fauteuil roulant vers l'avant. Analysez les éventuels problèmes: fragilité du joint, excès ou manque d'espace horizontal, rupture de pièces etc.
Analyser les problèmes et reconcevoir à nouveau.
Dans notre prototype, le fauteuil roulant se déplaçait, mais à un rythme lent. La partie du corps n'a pas fini de coller à temps, donc le bras de levier s'est cassé pendant notre essai. De plus, l'articulation peut avoir été trop grande et lâche, et il n'y a peut-être pas eu suffisamment d'espace horizontal et de mouvement sur le bras de levier, ces deux éléments limitant la quantité de force exercée par poussée.
Étape 16: Page des cotisations
Cotisations individuelles pour le système de soutien
Chef de projet: Sophia Ynami 12732132
- La chef de projet, Sophia Ynami, était chargée de s'assurer que chaque membre du groupe était tenu responsable de ses fonctions respectives et que toutes les tâches étaient accomplies dans les délais. J'ai aidé dans le processus d'assemblage final ainsi que testé et ajusté l'appareil avant le dernier essai.
Fabricant: Yvonne Szeto 94326050
- Le fabricant, Yvonne Szeto, s'est chargé de préparer les différents composants pour l'assemblage. J'étais responsable de la découpe laser des matières premières, du perçage et de l'impression 3D de différentes pièces. J'ai également assemblé les différents composants ensemble.
Ingénieur des matériaux: Willis Lao 15649487
- L'ingénieur des matériaux, Willis Lao, était chargé de décider quels matériaux utiliser pour chaque composante du projet et de les commander/choisir auprès de McMaster Carr/Home Depot. J'ai également contribué aux Instructables en écrivant l'introduction, l'analyse des coûts, le processus étape par étape de création de pièces et l'assemblage.
Testeur: Matthieu Maravilla 25352925
- Le testeur, Matthew Maravilla, était chargé de superviser et d'analyser la méthode de test itérative, notamment de tester le bras de levier et de signaler les changements de dimension ou de pièce à ajuster. J'étais également responsable du contour et de la majorité des Instructables.
Concepteur principal: Anthony Cheuk 30511803
- Le concepteur principal, Anthony Cheuk, était chargé de proposer une conception réalisable en tenant compte des différents matériaux pouvant être utilisés et de préparer les fichiers et la conception prêts pour la fabrication (impression 3D et découpe laser).
Conseillé:
Fauteuil roulant contrôlé par joystick avec suivi d'obstacles : 3 étapes (avec photos)
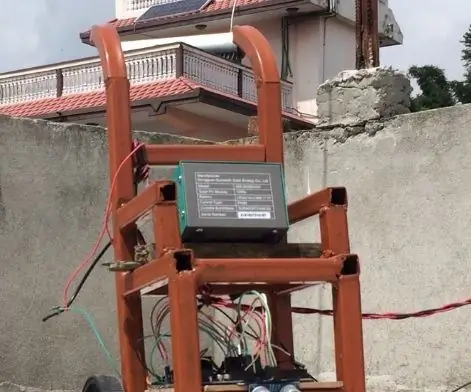
Fauteuil roulant contrôlé par joystick assisté par un traqueur d'obstacles : afin de permettre aux personnes handicapées de conduire en toute sécurité, un capteur à ultrasons est utilisé pour suivre les obstacles présents sur le chemin. Sur la base du mouvement du joystick, les moteurs entraîneront le fauteuil roulant dans quatre directions et vitesses sur chaque di
Fauteuil roulant basé sur un accéléromètre pour personne physiquement handicapée : 13 étapes
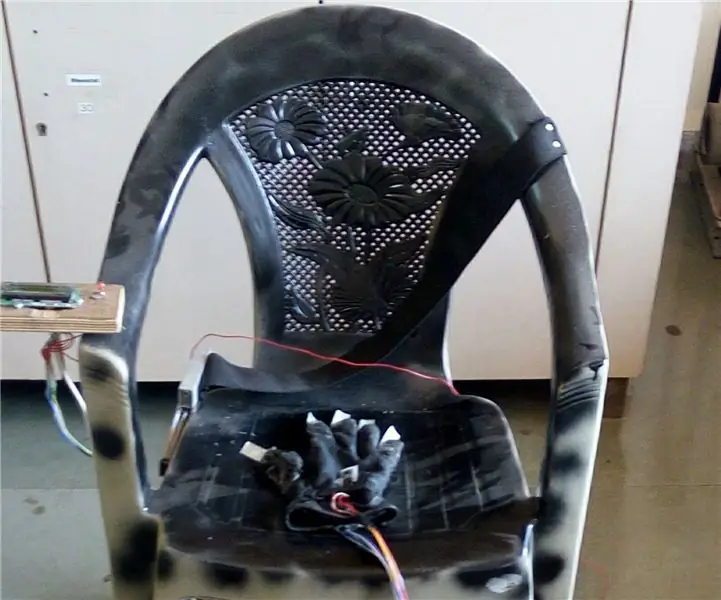
Fauteuil roulant à accéléromètre pour personnes physiquement handicapées : dans notre pays de 1,3 milliard d'habitants, nous avons encore plus de 1% de personnes âgées ou handicapées, qui ont besoin d'un soutien pour la mobilité personnelle. Notre projet a pour objectif de répondre à leur exigence de mobilité avec une technologie intelligente. Le problème
Fauteuil roulant pour chien : 4 étapes
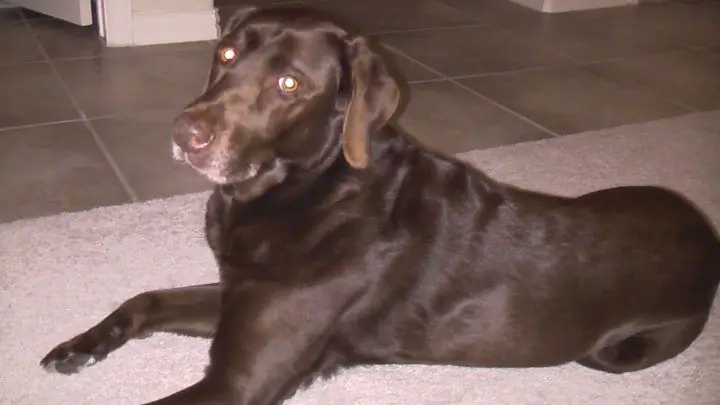
Fauteuil roulant pour chien : Bonjour aujourd'hui, je vais vous montrer comment fabriquer un fauteuil roulant pour chien pour votre chien. J'ai eu cette idée en cherchant sur Internet pour voir comment les gens peuvent profiter davantage des chiens plus âgés. Je n'en avais pas vraiment besoin car mon chien a 2 ans mais le chien de ma tante qui a 8 ans
Fauteuil roulant teckel : 6 étapes (avec photos)

Fauteuil roulant teckel : notre teckel s'est blessé au dos, alors pour la rééducation, nous l'avons fait nager beaucoup et j'ai construit cette chaise jusqu'à ce qu'il puisse à nouveau utiliser ses pattes arrière
D4E1 - Bricolage - Technologie d'assistance : Plateau de fauteuil roulant réglable : 7 étapes (avec photos)
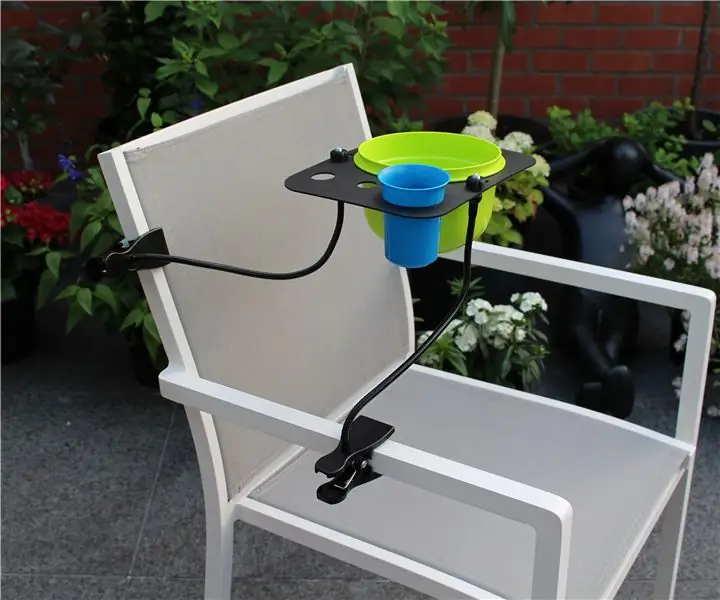
D4E1 - Bricolage - Technologie d'assistance : Plateau de fauteuil roulant réglable : Kjell a un handicap congénital : quadriparésie dyskinétique et est incapable de manger tout seul. Il a besoin de l'aide d'un moniteur, d'un ergothérapeute, qui le nourrit. Cela s'accompagne de deux problèmes : 1) L'ergothérapeute se tient derrière le volant