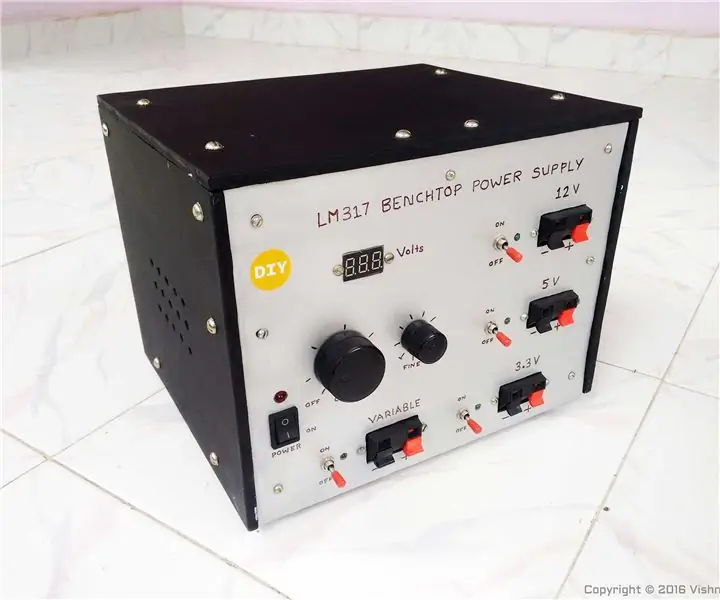
Table des matières:
- Étape 1: Se préparer
- Étape 2: Schéma
- Étape 3: modèle 3D SketchUp
- Étape 4: Rassemblez les outils et les pièces
- Étape 5: Construire le circuit imprimé
- Étape 6: Construire la boîte
- Étape 7: peindre la boîte
- Étape 8: Câblage
- Étape 9: Tester
- Étape 10: Finition
- Étape 11: Avantages et inconvénients
- Étape 12: Dépannage
- Étape 13: Améliorations
2025 Auteur: John Day | [email protected]. Dernière modifié: 2025-01-23 14:46
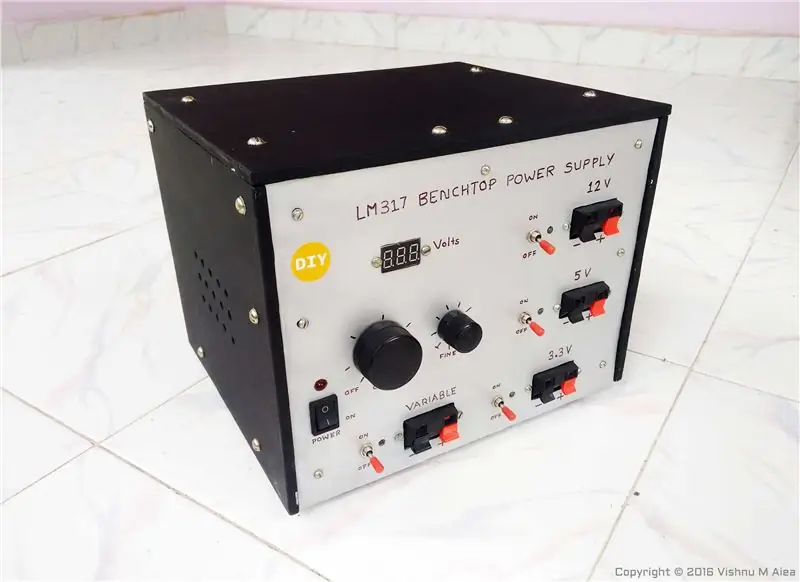
Une alimentation est incontestablement un équipement absolument nécessaire pour tout laboratoire d'électronique ou toute personne souhaitant réaliser des projets d'électronique, en particulier une alimentation variable. Dans ce tutoriel, je vais vous montrer comment j'ai construit une alimentation variable 1,2-30V basée sur un régulateur positif linéaire LM317 (1,2V à la tension d'entrée -2,7V en fait).
Ce sont les caractéristiques que je voulais que mon bloc d'alimentation ait.
- Une sortie variable avec courant minimum 2 A.
- Sortie fixe 12 V avec 2A.
- Sortie fixe 5 V avec 2 A.
- Sortie 3,3 V fixe avec 1A.
- Deux ports USB pour charger les téléphones à 1A.
L'alimentation n'utilise pas de transformateur au lieu de cela, elle réduit la tension d'entrée constante dans la plage de 15 à 35 V à de nombreuses tensions différentes à la sortie. Vous pouvez donc alimenter cette unité par n'importe quel SMPS avec une tension nominale de 15-35V et un courant de 2-5A OU une alimentation par transformateur avec les mêmes spécifications.
Étape 1: Se préparer
- Accédez à https://www.autodesk.com/products/eagle/free-download et téléchargez le logiciel de capture schématique Eagle pour votre système d'exploitation.
- Allez sur https://www.sketchup.com/download et téléchargez la dernière version de SketchUp et installez-la.
- Trouvez un bon SMPS avec une tension nominale comprise entre 15 et 36 V OU créez une alimentation à base de transformateur avec une tension de sortie CC de 15 à 36 V.
Étape 2: Schéma
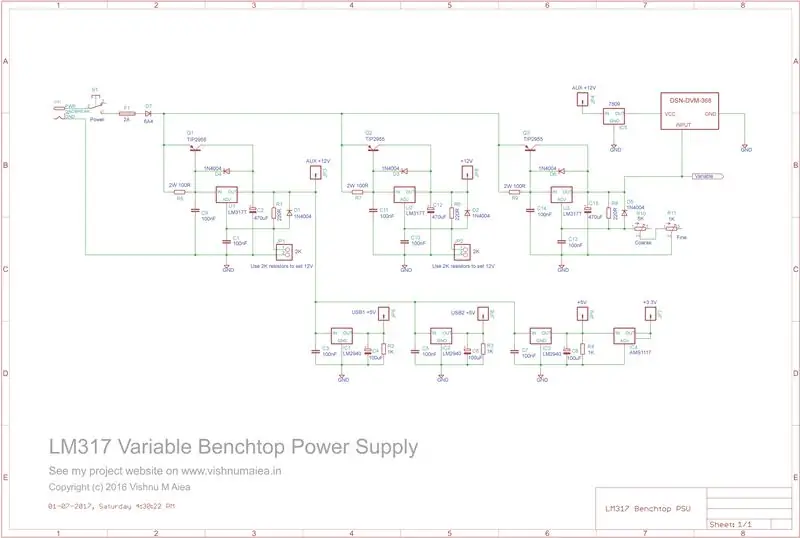
Le schéma vous donnera un aperçu de mon plan. Mais il n'a pas été conçu pour générer un fichier PCB car je perfboard habituellement pour mes conceptions uniques. Donc, je ne me souciais pas des packages de composants. Vous devez sélectionner les packages appropriés si vous souhaitez créer une mise en page PCB. Il y a trois LM317 et trois transistors TIP2955 PNP pour chacun. Chacun de ces LM317 réduira l'entrée 36V aux tensions programmées. U2 produira un 12V constant, U3 produira une tension variable et U1 produira un 12V auxiliaire pour les autres régulateurs 5V et 3.3 afin de réduire la chaleur dissipée par ceux-ci.
Le LM317 peut fournir un courant de sortie supérieur à 1,5 A. Mais dans ce cas, avec une grande différence de tensions d'entrée et de sortie, le LM317 devra dissiper l'excès de puissance sous forme de chaleur; tant de chaleur. Nous utilisons donc des éléments pass. Ici, j'ai utilisé le transistor de puissance TIP2955 comme élément de passage du côté positif. Vous pouvez utiliser TIP3055 ou 2N3055 comme élément de passage du côté négatif ou du côté sortie. Mais la raison pour laquelle j'ai choisi ceux PNP est qu'ils ne modifient pas la tension de sortie comme le feraient les transistors NPN (la sortie sera supérieure de +0,7 V lorsque NPN est utilisé). Les transistors PNP sont utilisés comme éléments de passage dans les régulateurs à faible chute et à très faible chute. Mais ils présentent des problèmes de stabilité de sortie qui peuvent être atténués en ajoutant des condensateurs à la sortie.
Les résistances de 2 W R5, R7 et R9 produiront une tension suffisante pour polariser les transistors de passage à des courants faibles. La sortie auxiliaire 12V est connectée aux entrées de trois régulateurs LM2940 ultra-faible chute 5V 1A dont deux sont utilisés pour les sorties USB et l'autre pour la sortie du panneau avant. L'une des sorties 5V est connectée à un régulateur AMS1117 pour une sortie 3.3V. C'est donc un réseau en série de différents régulateurs.
La sortie variable est tirée de U3 comme indiqué dans le schéma. J'ai utilisé un potentiomètre 5K en série avec un potentiomètre 1K pour avoir un réglage grossier et fin de la tension de sortie. Un module voltmètre DSN DVM-368 (tutoriel sur mon site) est connecté à la sortie variable pour afficher la tension sur le panneau avant. Voir la rubrique "Câblage" pour voir les modifications à apporter au module voltmètre. Vous pouvez utiliser n'importe quel autre module V ou A sans trop de modifications.
Téléchargez l'image-p.webp
Étape 3: modèle 3D SketchUp
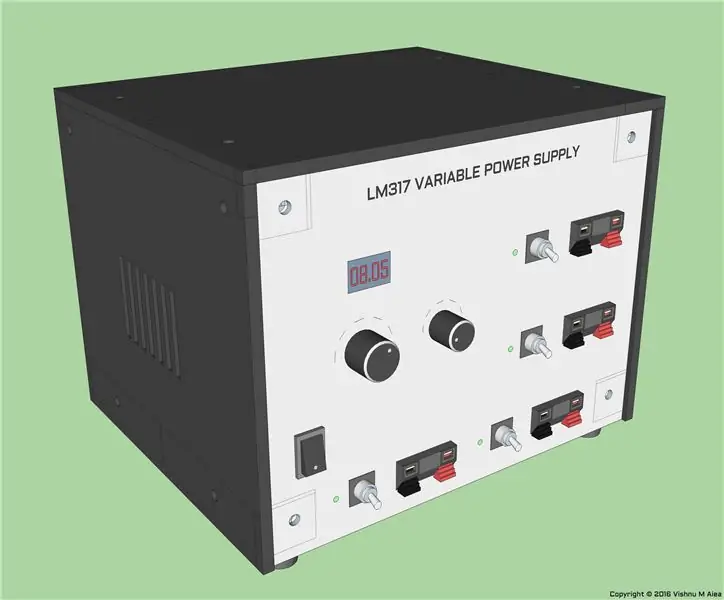
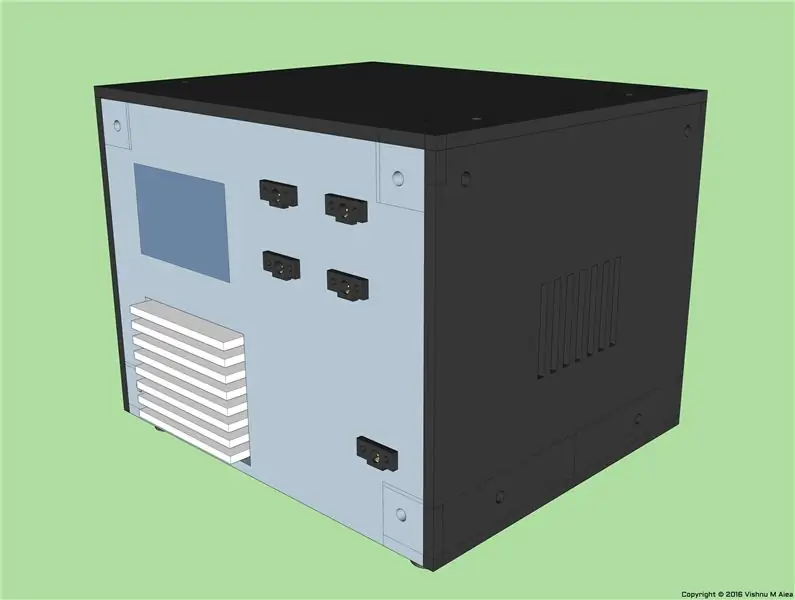
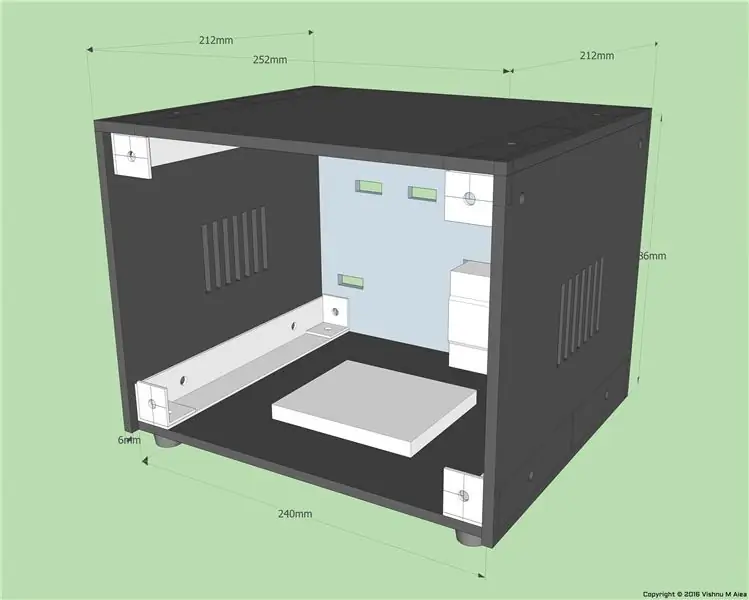
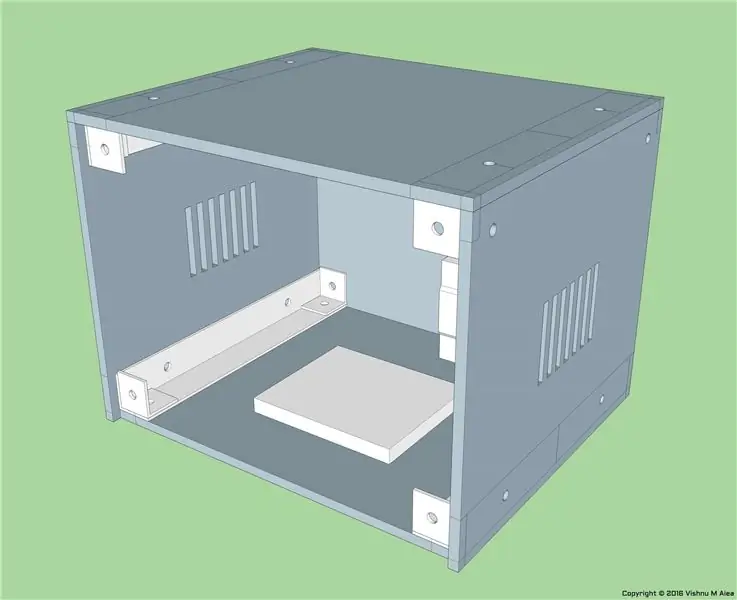
Pour planifier l'emplacement des connecteurs, des commutateurs, etc. et pour obtenir les dimensions correctes pour couper le panneau MDF, le canal en aluminium, etc., j'ai d'abord conçu un modèle 3D du boîtier d'alimentation dans SketchUp. J'avais déjà tous les composants avec moi. La conception du modèle était donc facile. J'ai utilisé des panneaux MDF d'épaisseur 6 mm et des extrusions d'aluminium (angle) de taille 25 mm et d'épaisseur 2 mm. Vous pouvez télécharger le fichier modèle SketchUp en utilisant le lien ci-dessous.
Fichier LM317 PSU SketchUp 2014: Téléchargez le fichier ci-dessous. Vous êtes libre de télécharger, modifier et redistribuer ce matériel.
Étape 4: Rassemblez les outils et les pièces
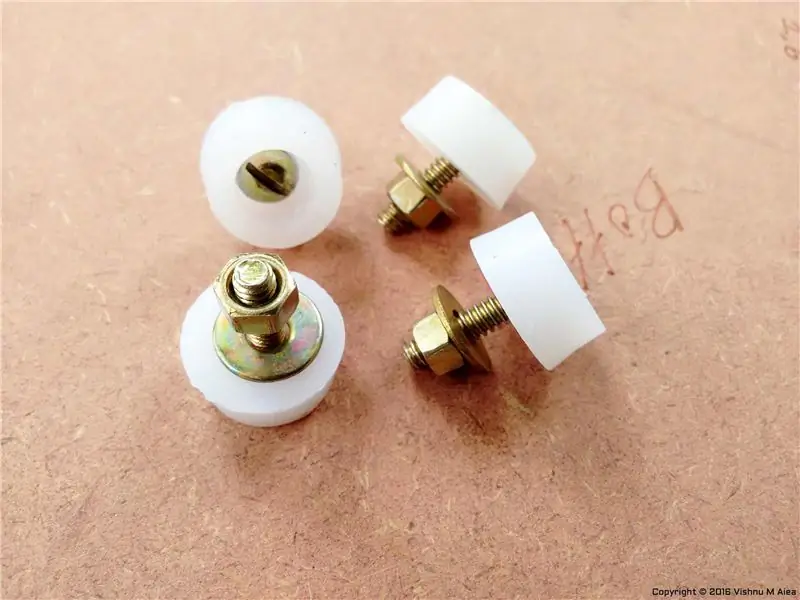
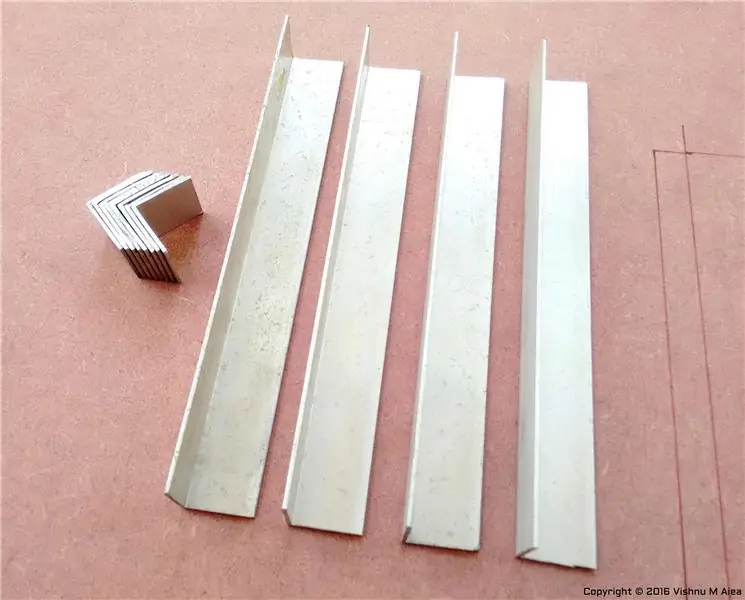
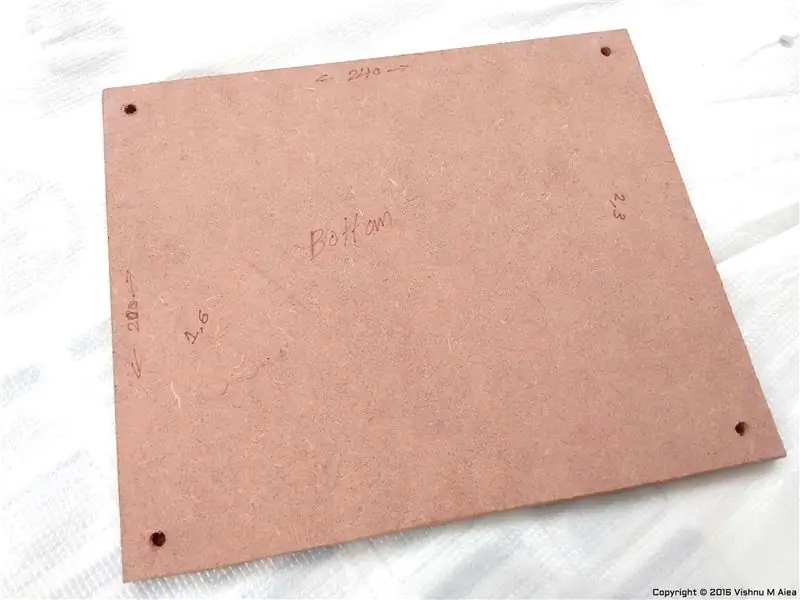
Il s'agit du matériel, des outils et des composants nécessaires.
Pour la boîte d'alimentation,
- Panneau MDF d'épaisseur 6 mm.
- Extrusions angulaires en aluminium - taille 25 mm, épaisseur 2 mm.
- Vis à métaux de 25 mm à tête ronde fendue et écrous et rondelles compatibles.
- Feuille acrylique ou ABS d'épaisseur 3-4 mm.
- Ancien dissipateur thermique et ventilateur en aluminium CPU.
- Pieds en PVC de taille 1,5 cm.
- Peinture en aérosol noir mat.
- Apprêt MDF.
Pour le circuit imprimé,
- 3x TIP2955 (ensemble TO-247)
- Isolateurs en mica pour transistors TO-247
- 3x LM317T
- 3x LM2940
- 1x AMS1117-3.3
- 3 résistances 2W, 100 Ohm
- 10 condensateurs céramiques 100 nF
- 6x 1N4007 diodes
- Bouchons électrolytiques 470 uF, 40 V
- 1x diode 6A4
- 3x résistances 1K
- 3 résistances de 200 Ohm
- 1x fusibles 3-4A et porte-fusibles
- Bouchons électrolytiques 100 uF, 10 V
- 1x potentiomètre linéaire 1K
- 1x potentiomètre linéaire 5K
- 2x boutons de potentiomètre
- Borniers à 2 broches
- Dissipateurs pour boîtiers TO220
- Pâte dissipateur de chaleur
- 4x interrupteurs à bascule/levier SPST
- Câbles et fils d'anciennes alimentations PC
- Tubes thermorétractables de 3 mm et 5 mm
- PCB à matrice perforée
- En-têtes de broche mâles
- 2x récepteurs USB type A femelles
- 4x connecteurs de haut-parleur OU 8x bornes de connexion
- 1x interrupteur à bascule SPST/DPDT
- 4x LED 3mm/5mm
- 1x voltmètre DSN-DVM-368
- 5x connecteurs cylindriques DC femelles (à visser)
- Entretoises en plastique
Outils
- Lames de scie à métaux
- Perceuse
- Joueur de nez
- Différents types de fichiers
- Différents types de clés
- Mètre ruban
- Marqueur CD permanent noir
- De nombreux types de tournevis Philips et à fente (acheter un kit)
- Couteau et lames rétractables
- Outil rotatif (pas nécessaire si vous avez des compétences)
- Papiers de verre grain 300 et 400
- Pince (pour fils de cuivre)
- Multimètre
- Fer à souder
- Fil de soudure et flux
- Pince à dénuder
- Pince à épiler
- Et tout outil que vous pouvez trouver.
- Masque anti-pollution/poussière pour protéger de la peinture.
Étape 5: Construire le circuit imprimé
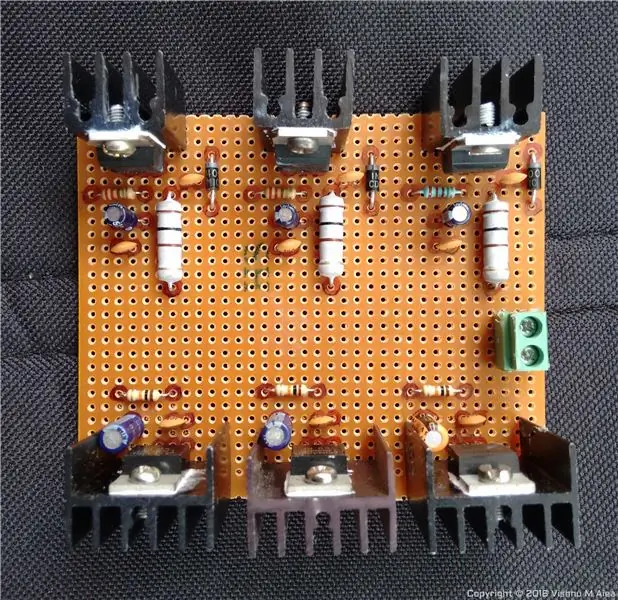
Coupez le perfboard selon vos besoins. Ensuite, placez et soudez les composants selon le schéma. Je n'ai pas créé de fichier PCB pour la gravure. Mais vous pouvez utiliser le fichier schématique Eagle ci-dessous pour créer vous-même un PCB. Sinon, utilisez votre ingéniosité pour planifier les emplacements et le routage et soudez le tout bien. Lavez le PCB avec une solution IPA (alcool isopropylique) pour nettoyer tout résidu de soudure.
Étape 6: Construire la boîte
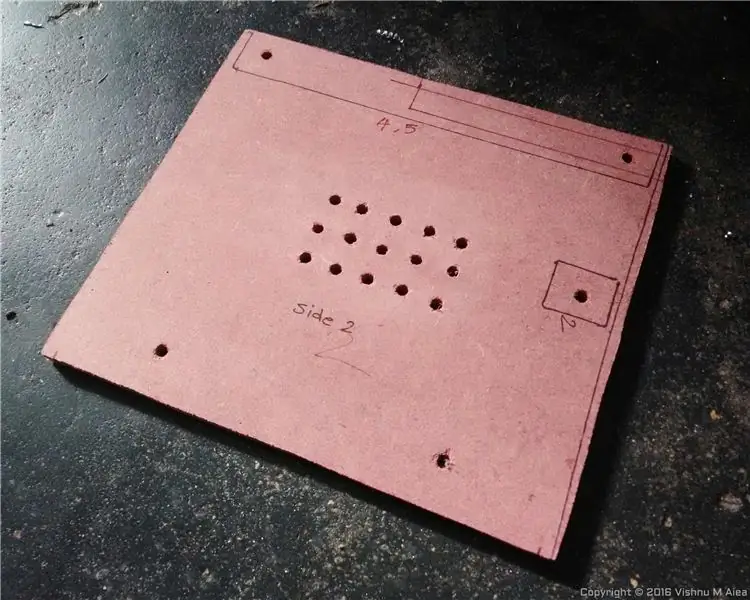
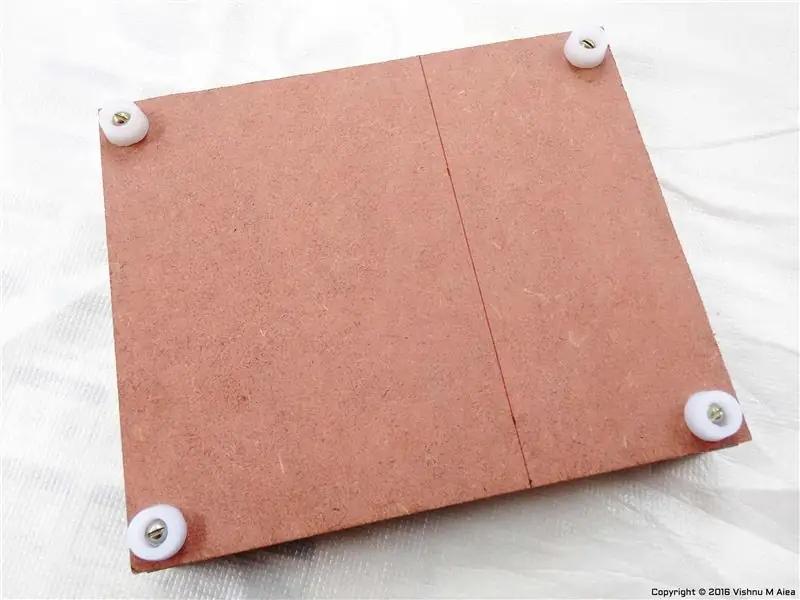
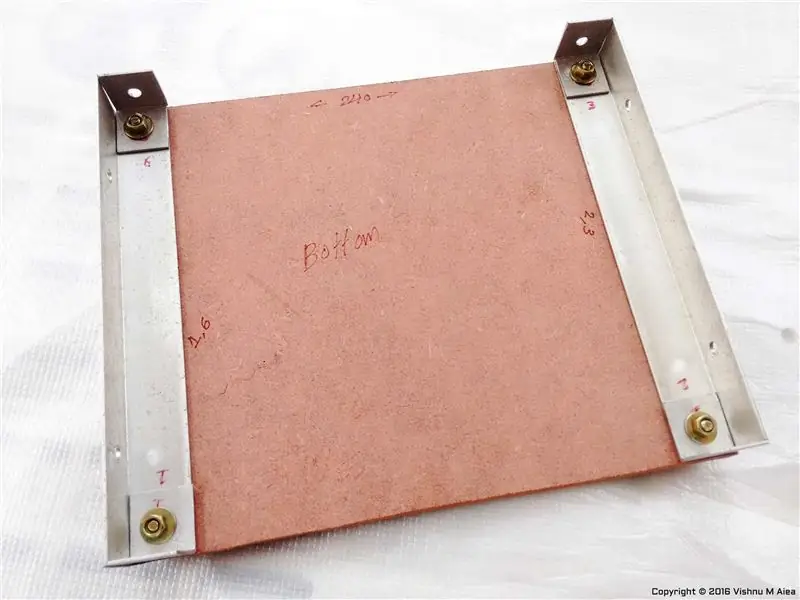
Toutes les dimensions avec lesquelles le panneau MDF, les canaux en aluminium doivent être coupés, les dimensions des trous, les emplacements des trous et tous sont dans le modèle SketchUp. Ouvrez simplement le fichier dans SketchUp. J'ai regroupé les pièces afin que vous puissiez facilement masquer des parties du modèle et utiliser l'outil Mesurer pour mesurer les dimensions. Toutes les dimensions sont en mm ou en cm. Utilisez des mèches de 5 mm pour percer des trous. Vérifiez toujours l'alignement des trous et des autres pièces pour vous assurer que tout s'emboîte facilement. Utilisez des papiers de verre pour lisser la surface des canaux en MDF et en aluminium.
Vous aurez une idée de la façon de construire la boîte une fois que vous aurez examiné le modèle 3D. Vous pouvez le modifier selon vos besoins. C'est un endroit où vous pouvez utiliser votre créativité et votre imagination au maximum.
Pour le panneau avant, utilisez une feuille d'acrylique ou d'ABS et découpez des trous à l'aide d'un cutter laser si vous pouvez en accéder. Mais malheureusement, je n'avais pas de machine laser et en trouver une serait une tâche fastidieuse. J'ai donc décidé de m'en tenir à l'approche traditionnelle. J'ai trouvé des cadres et des boîtes en plastique de vieux réfrigérateurs dans un magasin de ferraille. En fait, je les ai achetés à un prix déraisonnable. L'un de ces cadres était suffisamment épais et plat pour être utilisé comme panneau avant; il n'était ni trop épais ni trop fin. Je l'ai coupé avec des mesures correctes et j'y ai percé et découpé des trous pour accueillir tous les commutateurs et connecteurs de sortie. Une scie à métaux et une perceuse étaient mes principaux outils.
En raison de la conception spécifique du boîtier, vous pouvez rencontrer des problèmes pour fixer le panneau avant au reste du boîtier. J'ai collé des morceaux de plastique ABS derrière les angles de façade et les ai vissés directement sans avoir besoin d'écrous. Vous devrez faire quelque chose comme ça ou quelque chose de mieux.
Pour le dissipateur thermique, j'en ai utilisé un d'un ancien refroidisseur de processeur. J'y ai percé des trous et j'ai fixé les trois transistors de passage avec des isolants en mica (C'EST IMPORTANT!) Entre eux pour l'isolation électrique. Réalisant que le dissipateur thermique seul ne ferait pas le travail, j'ai ensuite ajouté un ventilateur de refroidissement de l'extérieur du dissipateur thermique et l'ai connecté au 12V auxiliaire.
Étape 7: peindre la boîte
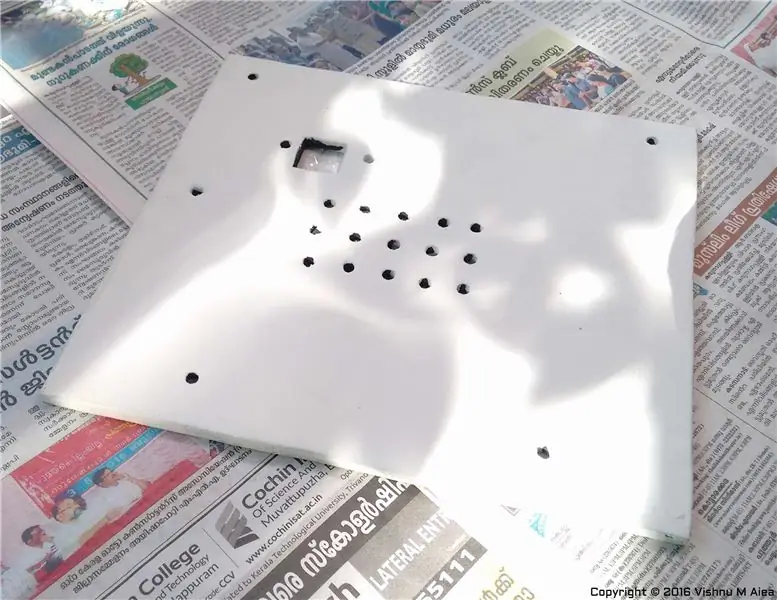
Vous devez d'abord poncer le MDF avec du papier de verre de grain 300 ou 400. Ensuite, appliquez une couche mince et uniforme d'apprêt pour bois ou d'apprêt MDF. Appliquez une autre couche après que la première couche est suffisamment sèche. Répétez cette opération selon vos besoins et laissez sécher pendant 1 ou 2 jours. Vous devez poncer la couche d'apprêt avant de pouvoir pulvériser la peinture. La peinture est facile à l'aide de pots de peinture compressés.
Étape 8: Câblage
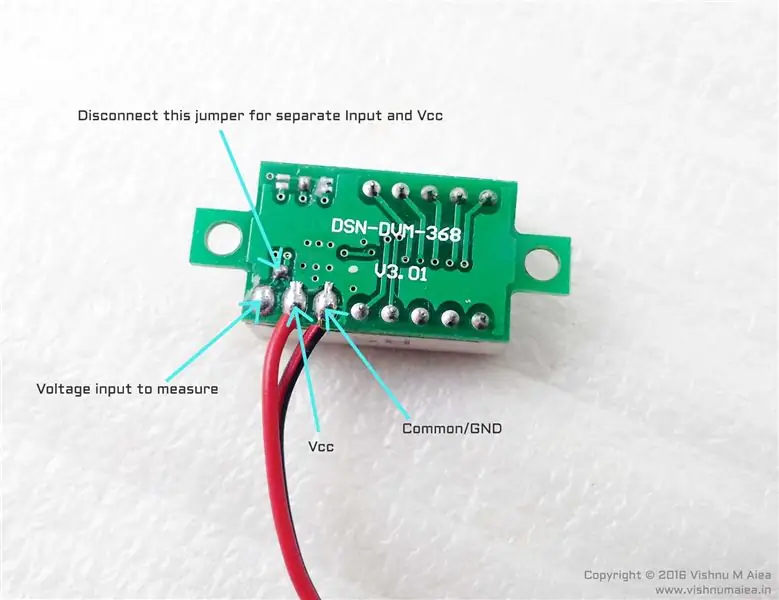
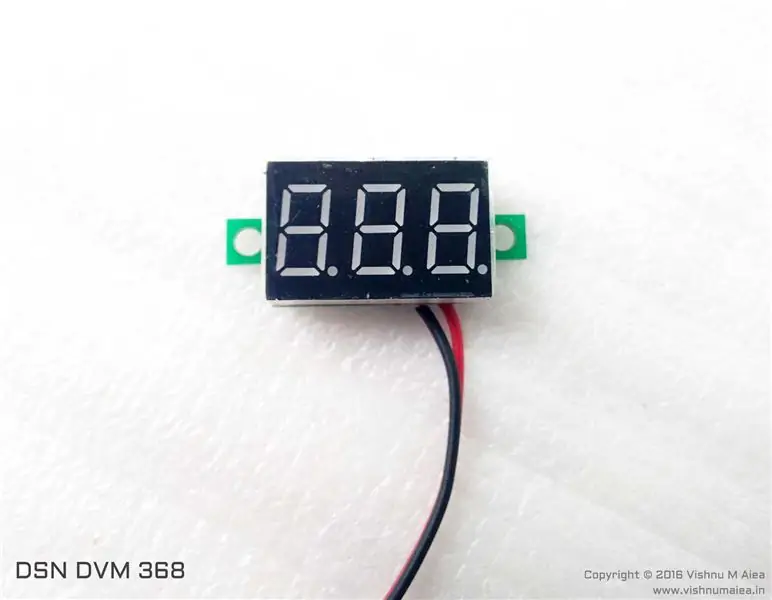
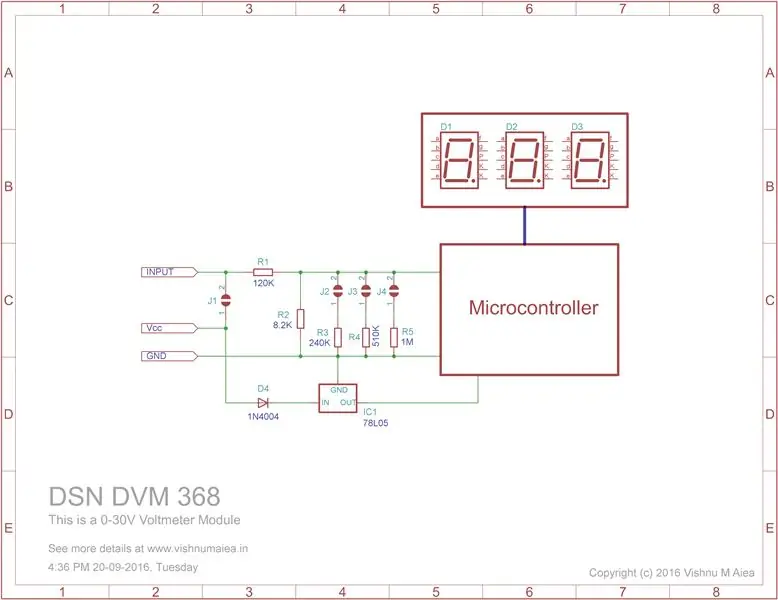
Fixez la carte que vous avez soudée au centre de la feuille inférieure et vissez-la à l'aide de petites vis mécaniques et d'entretoises entre elles. J'ai utilisé des fils de vieilles alimentations d'ordinateur car ils sont de bonne qualité. Vous pouvez soit souder les fils directement sur la carte, soit utiliser des connecteurs ou des embases à broches. J'ai fait le bloc d'alimentation à la hâte donc je n'ai utilisé aucun connecteur. Mais il est recommandé d'utiliser des connecteurs chaque fois que possible, pour que tout soit modulaire et facile à assembler et à démonter.
J'avais rencontré des problèmes assez étranges lors du câblage et des tests initiaux. Le premier était l'instabilité de la production. Comme nous utilisons des éléments de passage PNP, la sortie oscillerait, donnant une tension continue efficace réduite sur le compteur. J'ai dû connecter des condensateurs électrolytiques de grande valeur pour rectifier ce problème. Le problème suivant était la différence de tension de sortie dans la carte et au niveau des connecteurs de sortie ! Je ne sais toujours pas exactement quel est le problème, mais j'ai résolu ce problème en soudant directement des résistances de grande valeur, 1K, 4,7K, etc., aux bornes de sortie. J'ai utilisé une valeur de résistance 2K (1K+1K) pour programmer les sorties Aux 12V et principales 12V.
Nous n'avons besoin que du voltmètre DSN-DVM-368 pour la sortie variable car toutes les autres sorties sont fixes. Vous devez d'abord déconnecter (IMPORTANT !) le cavalier (Jumper 1) comme indiqué sur la figure puis utiliser les trois fils comme sur le schéma. Le voltmètre a déjà un régulateur 5V à l'intérieur. L'alimenter directement en 12 V provoquera un échauffement indésirable. On utilise donc un régulateur 7809, 9V entre l'AUX 12V et l'entrée Vcc du voltmètre. J'ai dû faire du 7809 un composant "flottant" car il a été ajouté après avoir soudé la carte.
Étape 9: Tester
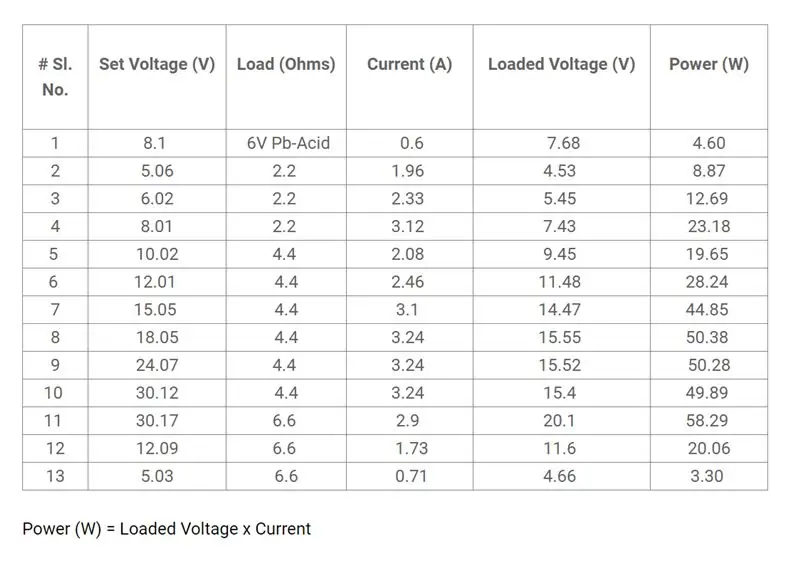
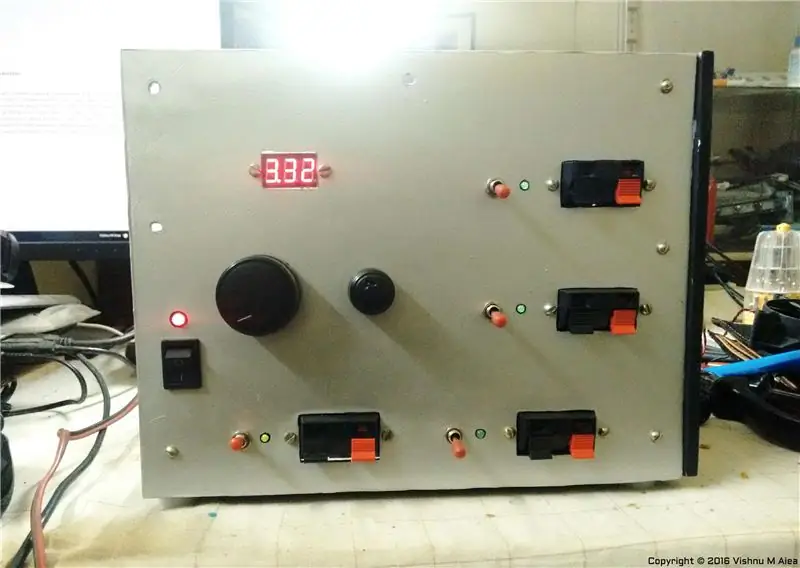
Connectez un SMPS avec une tension nominale comprise entre 15 et 35 V et un courant d'au moins 2 A à l'entrée de la carte via une prise cylindrique CC. J'ai utilisé 36V 2A SMPS avec protection contre les surintensités (arrêt) intégrée. Voir ci-dessus le tableau des mesures du test de charge.
La régulation de la charge ici n'est pas très bonne en raison de la limitation de la puissance de sortie du SMPS que j'utilise. Cela limitera le courant et s'arrêtera à des courants élevés. Je n'ai donc pas pu effectuer de tests de courant de surtension. Jusqu'à 14V, la régulation de charge semblait bonne. Mais au-dessus de la tension définie de 15V (#8, #9, #10), lorsque je connecte la charge, la tension de sortie diminuera à environ 15V avec un courant constant de 3,24A. Au #10, la tension chargée est la moitié de la tension réglée à 3.24A courant ! Il semblait donc que mon SMPS ne fournissait pas assez de courant pour maintenir la tension à ce qui est réglé. La puissance maximale que j'ai pu obtenir était à #11, de 58W. Ainsi, tant que vous maintenez le courant de sortie bas, la tension de sortie restera là où elle est censée. Gardez toujours un œil sur la tension, le courant et la température du dissipateur thermique car une quantité importante d'énergie y sera dissipée.
Étape 10: Finition
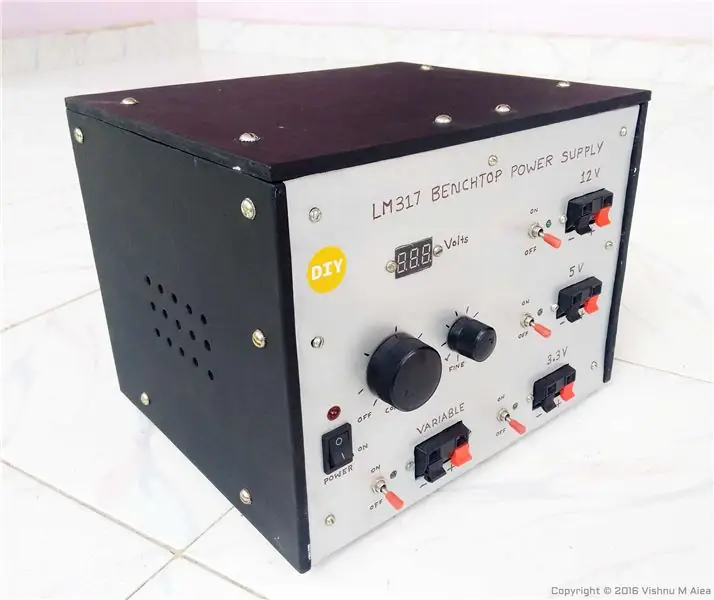
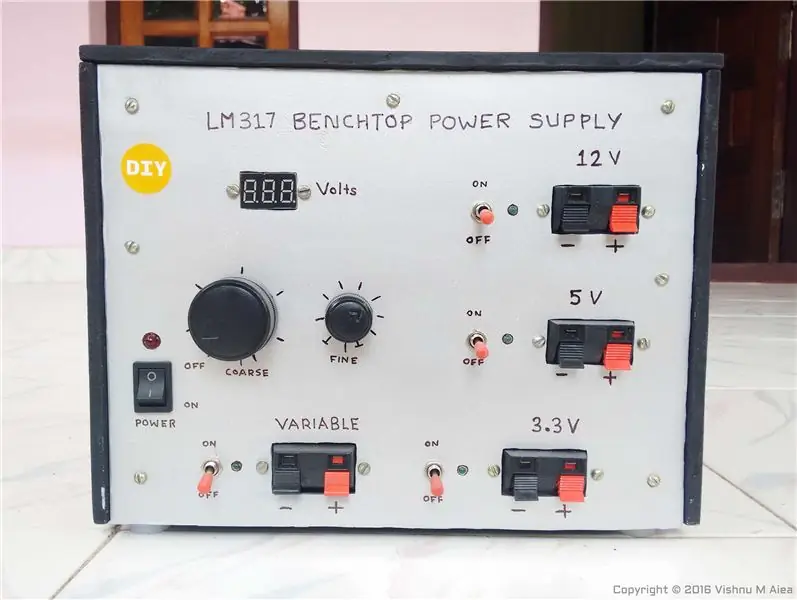
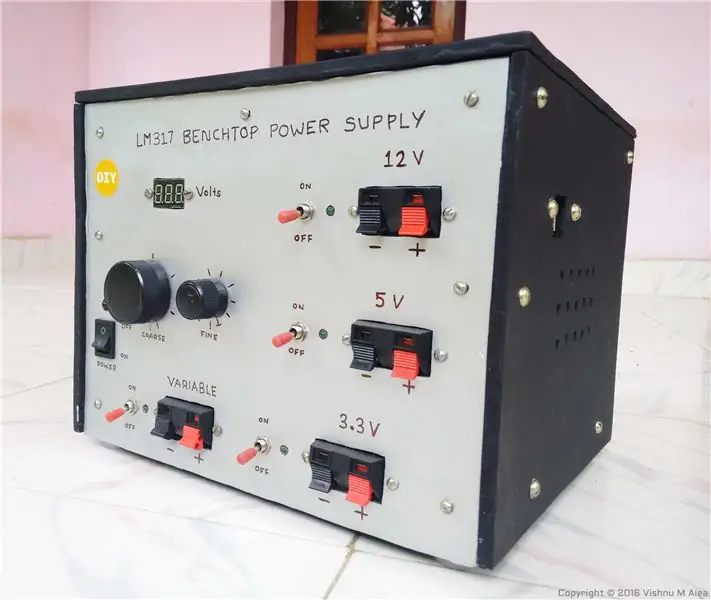
Une fois les tests terminés, assemblez le tout et étiquetez le panneau avant comme vous le souhaitez. J'ai peint le panneau avant avec de la peinture argentée et j'ai utilisé un marqueur permanent pour étiqueter les choses (pas une bonne façon de faire). J'ai mis un autocollant DIY que j'ai obtenu avec mon premier Arduino, sur le devant.
Étape 11: Avantages et inconvénients
Cette conception d'alimentation présente de nombreux avantages et inconvénients. Cela vaut toujours la peine de les étudier.
Avantages
- Facile à concevoir, construire et modifier car il s'agit d'une alimentation linéaire régulée.
- Moins d'ondulations indésirables à la sortie par rapport aux unités SMPS ordinaires.
- Moins d'interférences EM/RF produites.
Désavantages
- Mauvaise efficacité - la majeure partie de l'énergie est gaspillée sous forme de chaleur au niveau des dissipateurs thermiques.
- Mauvaise régulation de la charge par rapport à la conception de l'alimentation SMPS.
- Grande taille par rapport aux SMPS de puissance similaires.
- Aucune mesure ou limitation de courant.
Étape 12: Dépannage
Un multimètre numérique est le meilleur outil pour résoudre les problèmes d'alimentation. Vérifiez tous les régulateurs avant de souder à l'aide d'une maquette. Si vous avez deux multimètres numériques, il est alors possible de mesurer le courant et la tension simultanément.
- S'il n'y a pas d'alimentation à la sortie, vérifiez les tensions de la broche d'entrée, aux broches d'entrée du régulateur et vérifiez si les connexions PCB sont correctes.
- Si vous trouvez que la sortie oscille, ajoutez un condensateur électrolytique d'une valeur d'au moins 47 uF près des bornes de sortie. Vous pouvez les souder directement aux bornes de sortie.
- Ne court-circuitez pas les sorties et ne connectez pas de charge à faible impédance aux sorties. Cela pourrait entraîner la défaillance des régulateurs car il n'y a pas de limitation de courant dans notre conception. Utilisez un fusible de valeur appropriée à l'entrée principale.
Étape 13: Améliorations
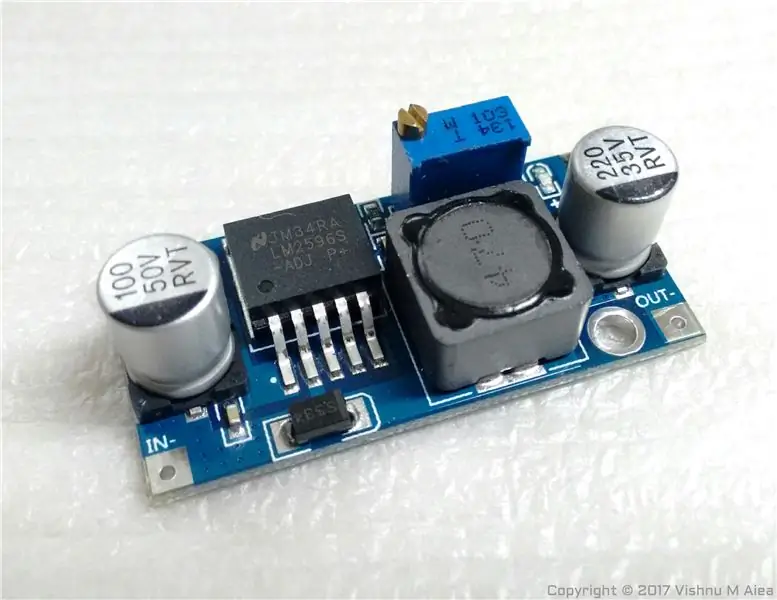
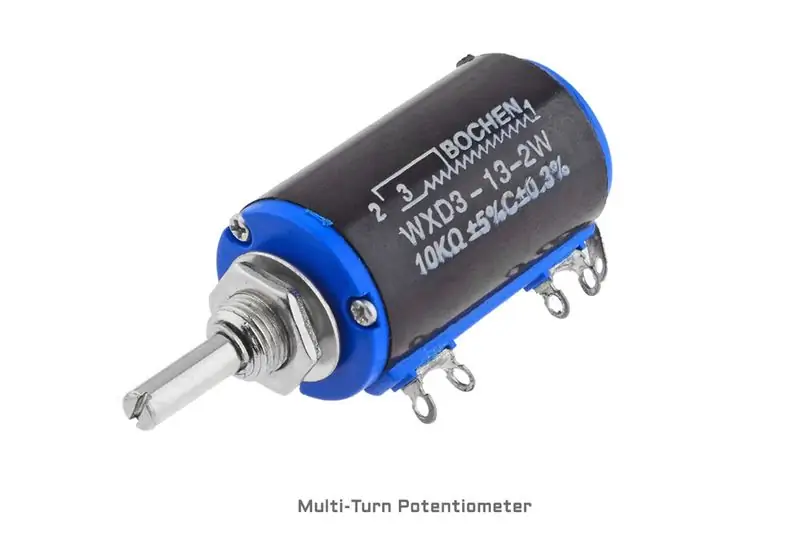
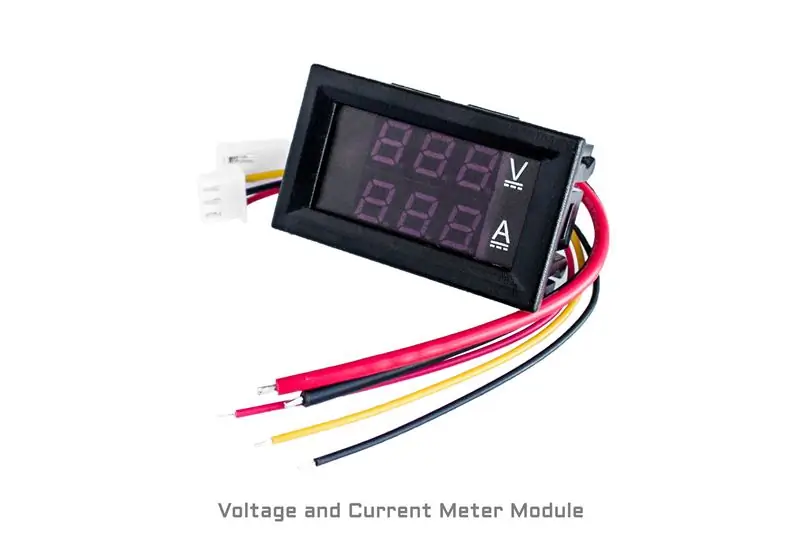
Il s'agit d'une alimentation linéaire de base. Il y a donc beaucoup de choses que vous pouvez améliorer. Je l'ai construit à la hâte parce que j'avais tellement besoin d'une sorte d'alimentation variable. Avec l'aide de cela, je peux construire une meilleure "alimentation numérique de précision" à l'avenir. Maintenant, voici quelques façons d'améliorer la conception actuelle,
- Nous avons utilisé des régulateurs linéaires tels que LM317, LM2940, etc. Comme je l'ai dit précédemment, ils sont si inefficaces et ne peuvent pas être utilisés pour une configuration alimentée par batterie. Donc, ce que vous pouvez faire, c'est trouver l'un de ces modules buck DC-DC bon marché dans n'importe quelle boutique en ligne et remplacer les régulateurs linéaires par eux. Ils sont plus efficaces (> 90 %), ont une meilleure régulation de charge, plus de capacité de courant, une limitation de courant, une protection contre les courts-circuits et tout. LM2596 est l'un de ce genre. Les modules buck (step down) auront un potentiomètre de précision sur le dessus. Vous pouvez le remplacer par un "potentiomètre multi-tours" et l'utiliser en face avant à la place des pots linéaires normaux. Cela vous donnera plus de contrôle sur la tension de sortie.
- Nous n'avons utilisé qu'un voltmètre ici, nous sommes donc aveugles sur le courant fourni par notre bloc d'alimentation. Il existe des modules de mesure "Tension et Courant" bon marché. Achetez-en un et ajoutez-en un pour chaque sortie.
- Il n'y a pas de fonction de limitation de courant dans notre conception. Essayez donc de l'améliorer en ajoutant une fonction de limitation de courant.
- Si le ventilateur de votre dissipateur thermique est bruyant, essayez d'ajouter un contrôleur de ventilateur sensible à la température peut-être avec contrôle de vitesse.
- Une fonction de charge de batterie peut être facilement ajoutée.
- Sorties séparées pour le test des LED.
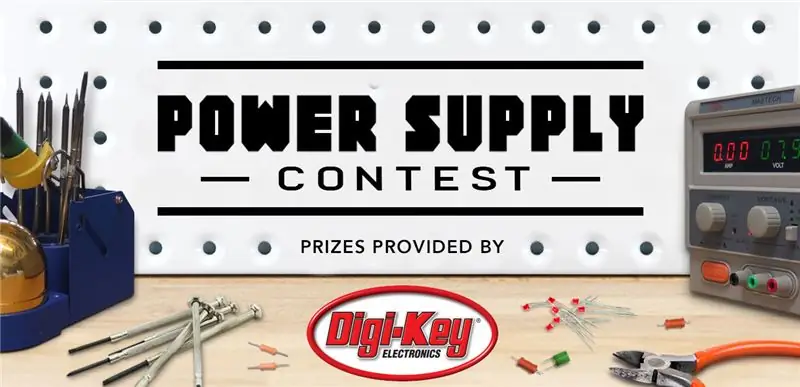
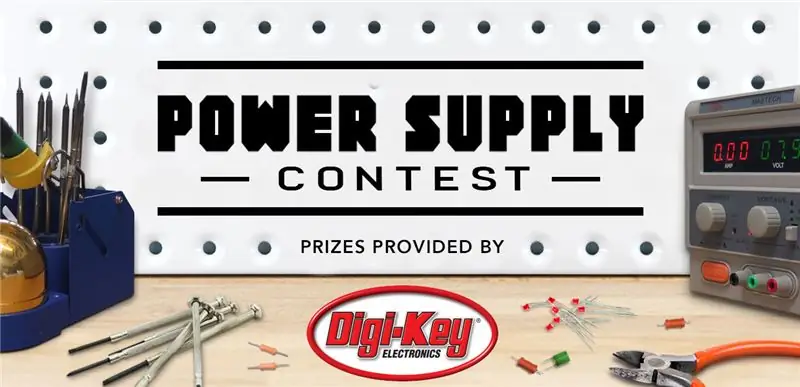
Premier prix du concours d'alimentation
Conseillé:
Comment créer une domotique basée sur l'IoT avec le relais de contrôle des capteurs NodeMCU : 14 étapes (avec photos)
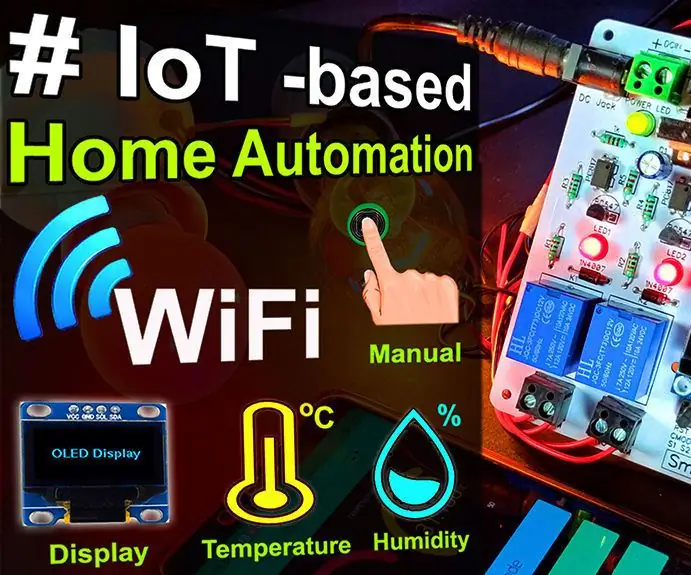
Comment faire de la domotique basée sur l'IoT avec le relais de contrôle des capteurs NodeMCU : Dans ce projet basé sur l'IoT, j'ai réalisé la domotique avec le module de relais de contrôle Blynk et NodeMCU avec retour en temps réel. En mode manuel, ce module de relais peut être contrôlé à partir d'un mobile ou d'un smartphone et, commutateur manuel. En mode automatique, cette smar
Flipper de table utilisant Evive - Plateforme intégrée basée sur Arduino: 18 étapes (avec photos)
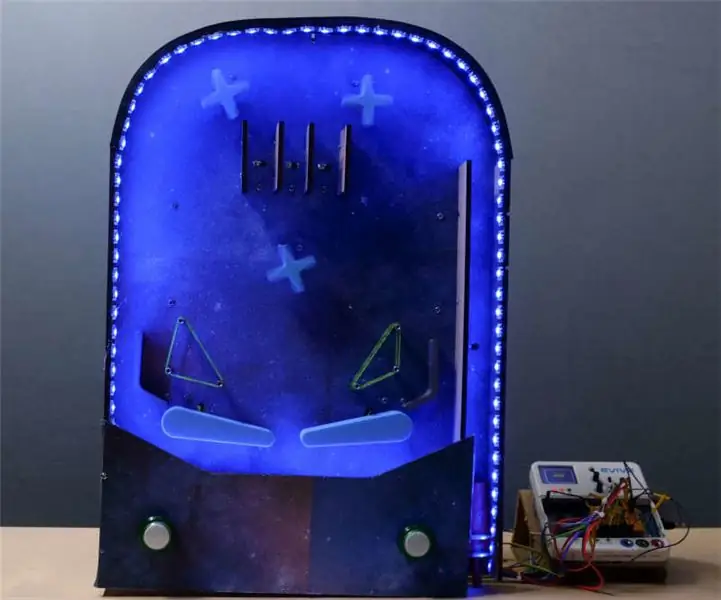
Flipper de table utilisant Evive - Plateforme embarquée basée sur Arduino : Un autre week-end, un autre jeu passionnant ! Et cette fois, ce n'est autre que le jeu d'arcade préféré de tous : Pinball ! Ce projet vous montrera comment fabriquer facilement votre propre flipper à la maison. Tout ce dont vous avez besoin, ce sont des composants de l'Evive
Gestion d'installation solaire basée sur le poids avec ESP32 : 7 étapes (avec photos)
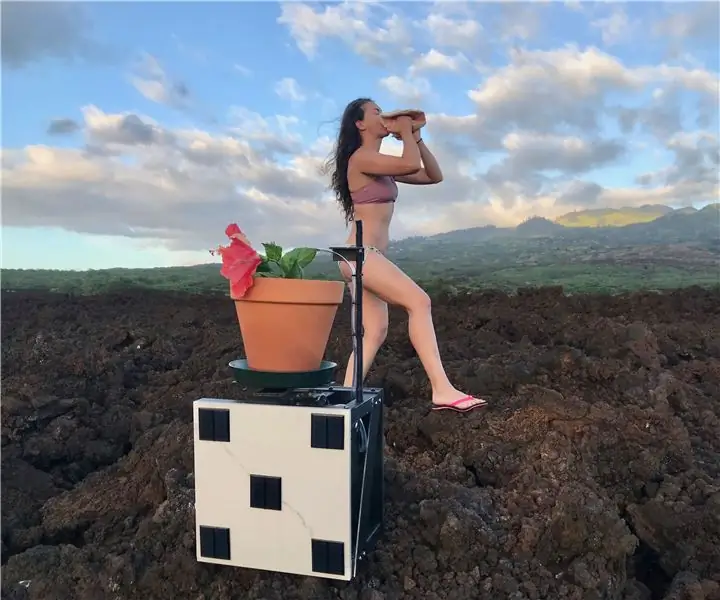
Gestion solaire des plantes basée sur le poids avec ESP32: Cultiver des plantes est amusant et arroser et en prendre soin n'est pas vraiment un problème. Les applications de microcontrôleur pour surveiller leur santé sont partout sur Internet et l'inspiration pour leur conception vient de la nature statique de la plante et de la facilité de surveillance
Barrette d'alimentation intelligente basée sur Beaglebone Black et OpenHAB : 7 étapes (avec photos)
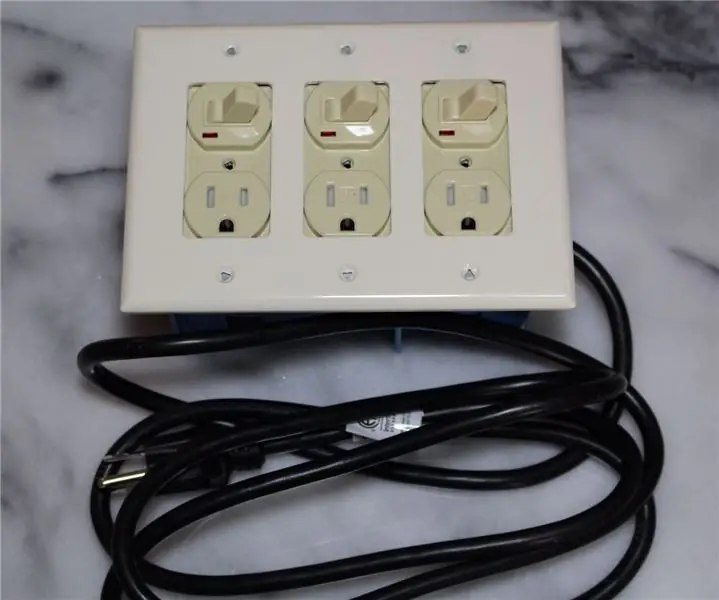
Barrette d'alimentation intelligente basée sur Beaglebone Black et OpenHAB : !!!!! Jouer avec le secteur (110/220V) est dangereux, soyez TRÈS TRÈS prudent !!!!! Il existe des conceptions de multiprises intelligentes basées sur le "Raspberry Pi" et deux Arduinos, qui est montré dans l'image "Ancien design".Ce nouveau de
Une solution de vision abordable avec bras robotique basée sur Arduino : 19 étapes (avec photos)
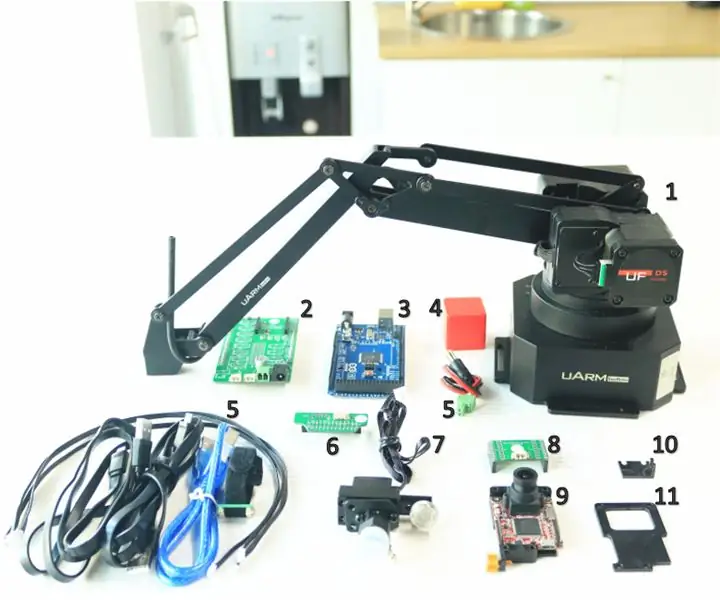
Une solution de vision abordable avec bras robotique basée sur Arduino : lorsque nous parlons de vision industrielle, cela nous semble toujours tellement inaccessible. Alors que nous avons fait une démo de vision open source qui serait super facile à faire pour tout le monde. Dans cette vidéo, avec la caméra OpenMV, peu importe où se trouve le cube rouge, le robot est