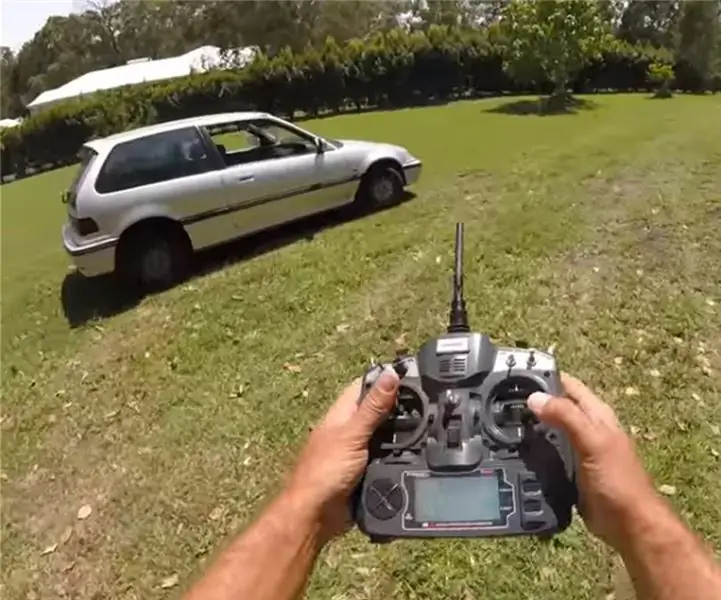
Table des matières:
- Étape 1: Contexte
- Étape 2: Compétences requises
- Étape 3: Coût de construction
- Étape 4: Liste des pièces
- Étape 5: Composants du système - Voiture
- Étape 6: Composants du système - Configuration de la batterie auxiliaire (en option)
- Étape 7: Composants du système - Allumage
- Étape 8: Composants du système - Sélecteur de vitesse
- Étape 9: Composants du système - Freins
- Étape 10: Composants du système - Accélérateur
- Étape 11: Composants du système - Pilotage
- Étape 12: Composants du système - Récepteur/Émetteur
- Étape 13: Programme final
2025 Auteur: John Day | [email protected]. Dernière modifié: 2025-01-23 14:45
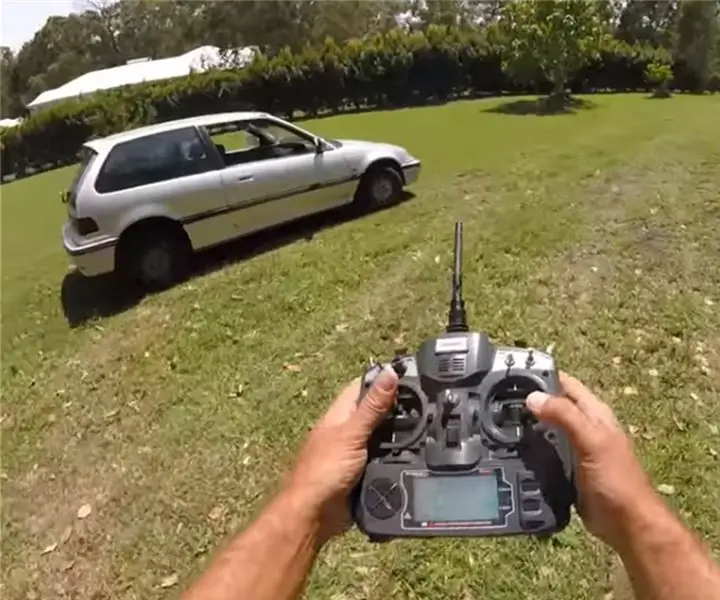
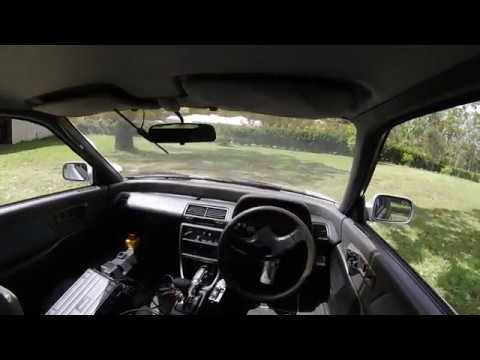
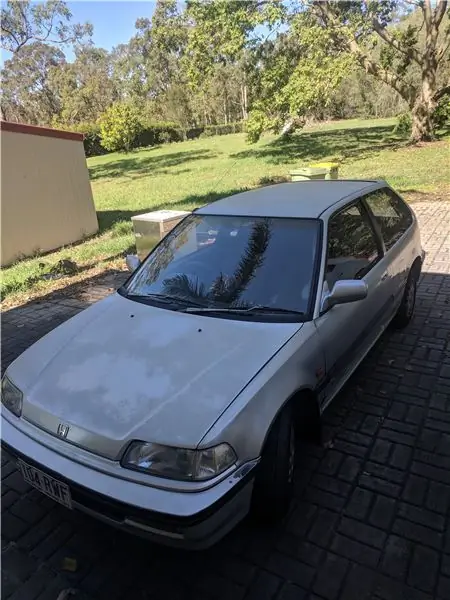
Qu'est-ce que c'est?
Vous pensez que les voitures RC sont réservées aux enfants ? Détrompez-vous ! Ce tutoriel vous montrera comment aménager et construire une voiture RC 1: 1 pleine grandeur. En équipant une voiture de ces commandes, c'est une bonne plate-forme de départ pour construire votre propre voiture entièrement autonome (phase suivante).
REMARQUE: Cette construction est basée sur une voiture de style non « drive-by-wire ». Si vous souhaitez lire mon autre tutoriel pour une voiture "drive-by-wire", consultez-le ici.
Étape 1: Contexte

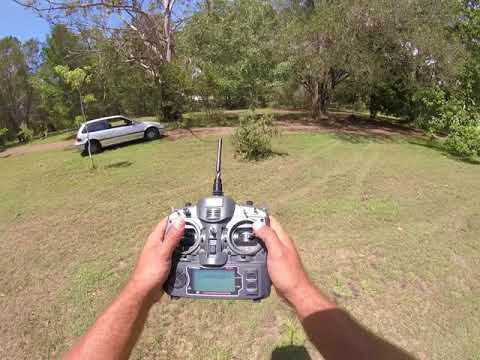
J'ai toujours voulu construire ma propre voiture autonome et il n'y a pas de meilleure façon de commencer que de modifier une vieille voiture pour que toutes les commandes soient gérées sans être humain dans la voiture. Ainsi, la première étape consiste à équiper une voiture de ces commandes puis à les actionner à distance via RC.
J'ai décidé de documenter ce processus pour montrer aux autres que la barrière à l'entrée pour construire une voiture autonome est super basse et pas très chère (<2k$). Je veux que des milliers de personnes construisent ces voitures afin que nous ayons beaucoup plus de personnes qui ont une expérience réelle de la mécatronique, de l'informatique et de l'ingénierie en général.
Mes compétences
- Construit et restauré plus de 8 voitures et 10 motos
- J'ai travaillé dans la fabrication toute ma vie
- Monteur et tourneur qualifié
- Outilleur qualifié
- Licence en Sciences informatiques
- Fondateur de QRMV - spécialisé en Robotique Industrielle Guidée par Vision
- Co-fondateur/CTO d'ollo wearables - téléphone portable à commande vocale pour seniors/personnes âgées (alerte vie moderne)
- Brevets multiples (attribués et provisoires) téléphonie, géo-positionnement et vision par ordinateur
Étape 2: Compétences requises
J'ai une formation très technique, mais je pense que toute personne un peu pratique devrait être capable d'en construire un assez facilement. Si vous n'avez pas toutes les compétences, la chose la plus simple à faire est de demander à d'autres que vous connaissez de se joindre à la construction. De cette façon, vous pouvez vous apprendre les uns les autres au fur et à mesure.
Mécanique - connaissez votre chemin autour d'une voiture et de ses composants et comment ils fonctionnent ensemble
Mécanique - être capable d'utiliser une grande variété d'outils manuels et électriques (perceuse, meuleuse, tour, etc.)
Électronique - comprendre, concevoir et construire des circuits de base (sélection des composants, soudure, etc.)
Dessin - Être capable de dessiner des composants en CAO à usiner par des tiers
Programmation - Être capable de créer des croquis Arduino simples, d'utiliser git, etc.
Étape 3: Coût de construction
En bref - <$2k. Le coût de construction d'une de ces voitures dépend vraiment du prix que vous pouvez obtenir pour la voiture en marche, car il s'agit probablement de l'élément de coût le plus élevé et le plus variable du projet. Pour la première voiture que j'ai construite, j'ai réussi à récupérer ma petite Honda Civic de 1991 pour 300 $ et elle était toujours immatriculée.
Pour tous les autres composants dont vous aurez besoin, ils sont pour la plupart "prêts à l'emploi", donc les prix ne varieront pas trop.
Étape 4: Liste des pièces
La liste complète des pièces et les fournisseurs/fabricants peuvent être trouvés ici.
- Voiture (style non drive-by-wire)
- Actionneur linéaire (électrique) - Sélecteur de vitesse
- Actionneur linéaire (électrique) - Freins
- Servo (couple élevé) - Accélérateur
- Module de direction assistée électronique - Direction
- Arduino Uno - Intégration du système de contrôle
- Alimentation régulée haute intensité (5A) 5-6V (pour servo)
- Contrôleur et récepteur RC 8/9 canaux
- Batterie à décharge profonde (en option)
- Batterie auxiliaire - Relais sensible à la tension (En option)
- Boîtier de batterie (en option)
- Isolateur de batterie
- Pilote de moteur 60A (multidirectionnel)
- Pilote de moteur 2 x 32A (multidirectionnel)
- 2 modules relais 30A 5V
- 2 x potentiomètres coulissants
- 2 x potentiomètres multitours
- ~50A Disjoncteur ou Fusible
- Boutons et contacts d'arrêt d'urgence
- Fil (courant élevé pour les moteurs/batterie et multiconducteur pour le branchement)
- Boîte à fusibles automobile
- Barre plate en acier (25x3mm et 50x3mm)
- Plaque en aluminium (3-4mm)
- Boîtiers ABS pour l'électronique
- Manuel d'atelier automobile
Étape 5: Composants du système - Voiture
Remarque: pour ce tutoriel, je construis sur une voiture de style non «drive-by-wire» étant une Honda Civic 1990. Si vous souhaitez construire sur une voiture "drive-by-wire", je publierai mes informations de construction à ce sujet dans les mois à venir.
Pour la voiture, vous voulez vous assurer qu'elle coche les éléments suivants;
- La voiture démarre, roule et peut conduire (sinon, faites-la fonctionner)
- Il a une transmission automatique
- Les freins fonctionnent
- L'alternateur est en bon état de fonctionnement
Étape 6: Composants du système - Configuration de la batterie auxiliaire (en option)
Dans ce tutoriel, j'utiliserai une batterie à décharge profonde secondaire/auxiliaire, mais cela est facultatif. J'ai choisi de le faire dans ma construction car la batterie d'origine de la voiture était très petite et il y avait un accord pour obtenir une batterie à décharge profonde avec une configuration de relais de batterie auxiliaire pour le même prix qu'une autre batterie. L'essentiel ici est que vous souhaitiez une batterie et un alternateur en bon état de fonctionnement dans la voiture, capables de fournir un courant élevé en cas de besoin.
Tout d'abord, débranchez la batterie de la voiture car nous allons travailler sur les deux terminaux. Configurer une batterie auxiliaire dans la voiture est assez simple. Tout d'abord, trouvez un endroit approprié/sûr pour monter la deuxième batterie à l'intérieur de la voiture, du coffre ou, si vous avez suffisamment d'espace, sous le capot.
Montez le relais sensible à la tension aussi près que possible de la batterie de démarrage.
Utilisez un fil de gros calibre (6 AWG) pour relier la borne positive du connecteur de la batterie de démarrage au relais sensible à la tension. Ensuite, faites passer un autre morceau de fil de gros calibre du relais sensible à la tension à la batterie auxiliaire et connectez-y solidement une borne de batterie.
Le relais sensible à la tension doit avoir un fil négatif qui doit être connecté à la terre de la voiture. Assurez-vous que ce fil/connecteur a un très bon contact avec la terre.
Au niveau de la batterie auxiliaire, faites passer un fil de gros calibre (6 AWG) de la borne négative à une partie de la carrosserie métallique de la voiture et assurez-vous qu'il a une terre solide (métal nu). Mettez les connecteurs appropriés aux deux extrémités et vérifiez que la mise à la terre est correcte.
Remarque: assurez-vous que votre batterie auxiliaire est solidement fixée et qu'elle ne bougera pas pendant la conduite. Je recommande de le mettre dans un boîtier de batterie pour le garder en sécurité et bien rangé.
Je recommande fortement d'utiliser un isolateur de batterie dans votre système pour permettre une isolation simple et rapide de l'alimentation. Placez-le en ligne entre votre batterie et la boîte à fusibles du contrôleur
Étape 7: Composants du système - Allumage

La plupart des voitures démarrent par une clé tournée dans le contact. Cela applique ensuite l'alimentation à différents composants de la voiture, notamment l'ECU, le solénoïde de démarrage, la radio, les ventilateurs, etc. Nous allons remplacer le système de clé par des relais que nous pouvons déclencher à partir de notre Arudino.
Vous aurez besoin des schémas électriques des voitures pour effectuer ce travail, mais vous pouvez normalement les trouver en ligne en effectuant une recherche rapide sur Google ou en en achetant simplement un en ligne. Je vous recommanderais d'obtenir le manuel d'atelier complet de la voiture, car il comprendra également d'autres informations, notamment des conseils / astuces pour retirer certains composants. De plus, il est toujours bon d'avoir des informations à portée de main pour diagnostiquer et résoudre tout autre problème de voiture que vous pourriez rencontrer.
J'envisagerais également de retirer complètement la colonne de direction (y compris le barillet d'allumage, la tige d'indicateur, etc.) de la crémaillère pour vous donner plus d'espace. être laissé dans la voiture.
Regardez les schémas électriques des voitures pour l'allumage et déterminez le ou les fils qui alimentent l'allumage. Normalement, il y aura un fil d'alimentation constant positif fusionné de la batterie (IN), puis un tas d'autres fils qui alimentent les composants de la voiture aux différentes étapes du cycle d'allumage/d'alimentation de la voiture (Off, ACC, IGN1/Run, IGN2/Démarrer). Déterminez quels fils sont lesquels, car vous n'aurez besoin que dans la plupart des voitures plus anciennes du fil positif principal IN, des fils IGN1/Run et IGN2/Start pour faire fonctionner la voiture, mais cela varie d'une voiture à l'autre.
Pour la voiture que j'avais, je n'avais besoin que de 3 fils au total, mais ils fournissaient un courant élevé, j'avais donc besoin de relais robustes pour commuter la charge. Les relais que j'ai fini par utiliser sont des modules 30A 5V que j'ai trouvés en ligne. Je voulais quelque chose qui puisse gérer un courant élevé ~ 30A et pouvoir être commuté simplement par un signal 5V.
Branchez les fils d'allumage aux relais au besoin. Vérifiez toujours que les relais fonctionnent avant de les monter, car j'ai eu plusieurs relais «morts à l'arrivée» dans ma vie de construction, ce qui m'a littéralement coûté des jours de recherche de pannes.
Vous voudrez que ces relais fonctionnent de différentes manières. Le relais IGN1/Run de mon système a allumé l'ECU de toutes les voitures, le ventilateur du radiateur et le module d'allumage, ce qui, dans un sens, me permettrait d'allumer / d'éteindre les voitures. Simplement, sans alimentation électrique du module d'allumage, la voiture tournerait mais ne démarrerait jamais. Le relais IGN2/Start était directement connecté au solénoïde du démarreur qui ferait réellement démarrer le moteur. Avec ce relais, vous voudriez seulement l'activer momentanément pour faire fonctionner la voiture, mais une fois qu'elle fonctionne, vous voudriez la désengager afin de ne pas tuer le démarreur.
Essai
Circuit - Constituez un simple interrupteur (IGN1/Run Relay) et un circuit de bouton momentané (IGN2/Start) comme entrées pour votre Arduino
Programmation - Ecrivez un script de test simple pour tester le fonctionnement des deux relais sans que la batterie de démarrage soit connectée. Une fois en confiance avec votre circuit et votre script, connectez la batterie de démarrage et testez-la. À ce stade, vous devriez pouvoir démarrer et arrêter votre voiture.
Jalon
À ce stade, vous devriez avoir;
- Relais IGN1/Run câblé
- Relais IGN2/Start câblé
- contrôle des deux relais marche/arrêt via Arduino
- circuit de test pour contrôler les relais
- pouvoir démarrer la voiture
- pouvoir éteindre la voiture
Étape 8: Composants du système - Sélecteur de vitesse

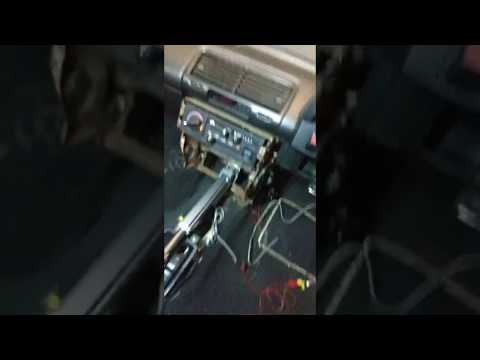
Comme nous utilisons une voiture avec transmission automatique dans cette construction, il est relativement facile de changer de vitesse car nous avons juste besoin de déplacer le levier dans un mouvement linéaire à certains points.
Remarque: j'ai décidé d'utiliser le levier existant et de ne pas le relier directement au câble de transmission car je voulais garder la voiture aussi stockée et l'intérieur aussi normal que possible.
La seule chose difficile à laquelle vous pourriez penser est que la plupart des transmissions automatiques vous obligent à appuyer sur un bouton avant de pouvoir déplacer le levier de transmission. Comme nous utilisons un actionneur linéaire doté d'une vis sans fin, nous pouvons utiliser sa capacité d'autoblocage pour maintenir le levier de transmission en place lorsqu'il ne le déplace pas. Quant au bouton, vous pouvez le verrouiller en permanence dans l'état « enfoncé ».
L'actionneur linéaire utilisé ici devait avoir une course suffisante pour passer de la position Park à Inverse, Neutral puis Drive. Dans le cas de ma voiture, il se trouvait à environ 100 mm de l'endroit où je montais l'actionneur. La force nécessaire pour déplacer le levier était très faible (<5kg) donc j'ai fini par utiliser un actionneur de force de course de 150mm/70kg car il était en stock.
Pour monter la base de l'actionneur, j'ai soudé un support et je l'ai fixé à une partie du cadre en acier qui a été utilisé dans la console centrale. Cela lui a permis de pivoter légèrement lorsqu'il s'est étendu/rétracté au cours de sa course.
Pour la fixation au levier de transmission, j'ai juste coupé quelques morceaux de barre plate en acier et utilisé quelques boulons pour le maintenir en place. Il n'est pas serré fermement autour du levier, il le contient simplement. Cela lui permet de bouger et de ne pas se lier lorsqu'il se déplace.
Pour déterminer la position de l'actionneur, j'ai utilisé un potentiomètre coulissant qui renverrait un signal analogique à mon Arduino. J'ai fait un support personnalisé pour le pot à l'actionneur à partir d'une barre plate. J'ai ensuite replié les languettes du curseur des pots autour du boulon du support de fixation du levier de transmission. Cela fonctionne mais je devrais changer cela pour qu'il s'agisse d'un meilleur accessoire pour le curseur des pots.
Pour alimenter l'actionneur, j'ai utilisé un pilote de moteur qui peut aller en avant et en arrière et être contrôlé via un microcontrôleur. J'ai utilisé un pilote de moteur Sabertooth 2x32A de Dimension Engineering, mais n'hésitez pas à utiliser tout ce qui fonctionne de manière similaire. Le premier canal sera utilisé pour contrôler l'actionneur de sélecteur de vitesses et le second contrôlera l'actionneur de frein. Le câblage et la configuration de ce pilote de moteur sont simples et bien documentés. Branchez le positif et le négatif de la batterie comme étiqueté et attachez les fils des actionneurs à la sortie du moteur 1. Connectez le 0V à la terre de votre Arduino et le fil S1 à une broche de sortie numérique.
Remarque: j'ai utilisé la configuration série simple sur cette version et cela a semblé fonctionner assez bien. Dimension Engineering a également créé quelques bibliothèques pour rendre la communication avec leurs pilotes très simple. Ils ont également quelques exemples simples pour vous permettre de démarrer rapidement.
Essai
Circuit - Pour déplacer l'actionneur vers l'avant et vers l'arrière, créez un circuit simple avec deux boutons momentanés comme entrées. L'un pour déployer l'actionneur et l'autre pour rétracter l'actionneur. Cela vous donnera alors un certain contrôle sur le positionnement de l'actionneur dans les positions d'engrenage.
Programmation - Ecrivez un script simple pour déplacer l'actionneur vers l'arrière et vers l'avant et sortir la valeur du potentiomètre coulissant. Lors de l'exécution du script, notez les valeurs du potentiomètre pour les positions de stationnement, de marche arrière, de point mort et de conduite. Vous en aurez besoin pour indiquer à l'actionneur de se déplacer vers ces positions dans le code complet.
Jalon
À ce stade, vous devriez avoir;
- actionneur solidement monté dans la voiture
- fixation autour du sélecteur/actionneur de vitesse
- pilote de moteur câblé avec actionneur et Arduino
- contrôle de l'extension/rétraction de l'actionneur via l'Arduino
- circuit de test pour contrôler l'extension/rétraction de l'actionneur
- connaître les valeurs/positions des potentiomètres pour chaque position de vitesse
Remarque: vous pouvez également utiliser un circuit de commutation multi-positions pour tester l'entrée du sélecteur de vitesse sur votre Arduino une fois que vous connaissez les positions. De cette façon, vous pourrez copier le code du sélecteur de vitesse directement dans la base de code de la voiture en cours d'exécution.
Étape 9: Composants du système - Freins
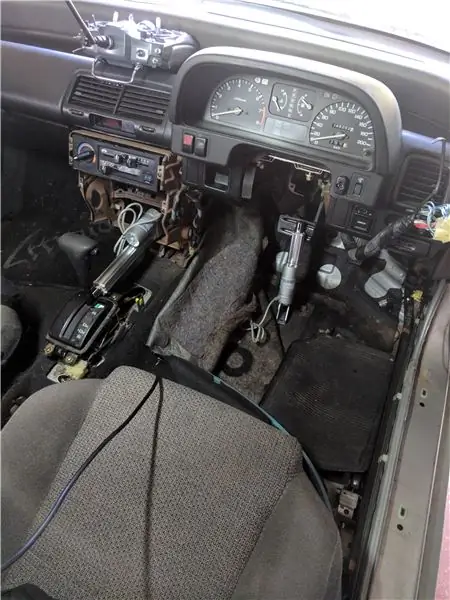
Arrêter la voiture est assez important, vous voulez donc vous assurer de bien faire les choses. Les freins d'une voiture sont normalement actionnés par votre pied qui peut appliquer une grande force si nécessaire. Dans cette version, nous utilisons un autre actionneur linéaire qui agira sur le pied. Cet actionneur devait avoir une force élevée (~30kg) mais ne nécessitait qu'une course courte ~60mm. J'ai pu obtenir un actionneur de course de 100 mm/force de 70 kg car il était en stock.
Trouver le bon endroit pour monter l'actionneur était un peu difficile, mais avec quelques essais et erreurs, j'ai trouvé une position sûre. J'ai soudé un morceau de barre plate en acier sur le côté du bras de la pédale de frein et j'y ai percé un trou où j'ai fait passer un boulon du haut de l'actionneur. J'ai ensuite soudé un support de montage pivotant à l'autre extrémité de l'actionneur au plan d'étage de la voiture.
Pour déterminer la position de l'actionneur, j'ai utilisé un potentiomètre coulissant (même configuration que l'actionneur de sélecteur de vitesse) qui enverrait un signal analogique à mon Arduino. J'ai fait un support personnalisé pour le pot à l'actionneur à partir d'une barre plate. J'ai ensuite replié les languettes du curseur de pots autour d'une petite languette de barre plate que j'ai montée à l'extrémité de l'actionneur.
Pour alimenter l'actionneur, j'ai utilisé l'autre canal du pilote de moteur Sabertooth 2x32A. Pour contrôler les deux moteurs, vous n'avez besoin d'utiliser qu'un seul fil (S1).
Remarque: j'ai utilisé la configuration série simple sur cette version et cela a semblé fonctionner assez bien. Ce pilote de moteur peut être configuré de plusieurs manières, alors choisissez une méthode que vous préférez.
Essai
Positionnement - Avant de connecter l'actionneur directement à la pédale de frein, vous voudrez avoir une idée de la distance que la pédale doit parcourir pour appliquer les freins. J'ai poussé mon pied sur les freins pour que la voiture s'arrête (en maintenant l'arrêt, pas les freins à fond). J'ai ensuite déplacé l'actionneur pour aligner son support de connexion avec la fixation de frein soudée. J'ai enregistré la valeur de sortie du potentiomètre afin de connaître ma position maximale de dépression des freins.
J'ai fait la même chose que ci-dessus pour la position de freinage.
Circuit - Pour déplacer l'actionneur vers l'avant et vers l'arrière, créez un circuit simple avec deux boutons momentanés comme entrées. L'un pour étendre l'actionneur et l'autre pour rétracter l'actionneur. Cela vous donnera alors un certain contrôle sur le positionnement de l'actionneur dans les positions d'engrenage.
Programmation - Ecrivez un script simple pour déplacer l'actionneur vers l'arrière et vers l'avant et sortir la valeur du potentiomètre coulissant. Lors de l'exécution du script, notez les valeurs du potentiomètre pour les positions d'activation et de désactivation du frein. Vous en aurez besoin pour indiquer à l'actionneur de se déplacer vers ces positions dans le code complet.
Jalon
À ce stade, vous devriez avoir;
- actionneur solidement monté dans la voiture
- fixation de la pédale de frein à l'actionneur
- pilote de moteur câblé avec actionneur et Arduino
- contrôle de l'extension/rétraction de l'actionneur via l'Arduino
- circuit de test pour contrôler l'extension/rétraction de l'actionneur
- connaître les valeurs/positions du potentiomètre pour les positions de desserrage et de marche du frein
Remarque: Dans le code final, j'utilise le signal des contrôleurs RC du canal pour contrôler la pression à appliquer sur le frein proportionnellement à la position de son manche. Cela m'a donné la plage allant de complètement éteint à complètement allumé.
Étape 10: Composants du système - Accélérateur
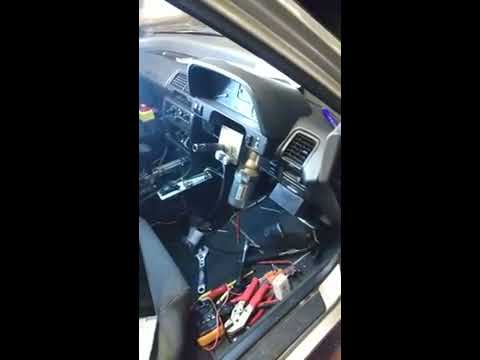
Maintenant, faisons tourner ces moteurs et pour ce faire, nous devons brancher l'accélérateur. Comme nous utilisons une voiture non «drive-by-wire», nous tirerons en fait sur un câble connecté au corps de papillon. Les corps de papillon ont normalement un ressort puissant qui ferme le papillon très rapidement lorsque l'accélérateur est relâché. Pour surmonter cette force, j'ai utilisé un servo à couple élevé (~ 40 kg/cm) pour tirer sur le câble.
J'ai boulonné ce servo sur un morceau de barre plate en acier et monté sur le côté de la console centrale avec des supports à angle droit. J'avais également besoin d'acheter un câble d'accélérateur plus long (2 m) car le câble d'origine utilisé dans la voiture était trop court. Cela m'a également donné beaucoup plus d'options de montage, ce qui m'a fait gagner beaucoup de temps.
Sachez que ces servos à couple élevé tirent normalement plus haut que le courant normal, alors assurez-vous de pouvoir l'alimenter de manière appropriée. J'ai utilisé une alimentation régulée 5V 5A pour cela, ce qui lui donne facilement suffisamment de courant pour fonctionner à plein couple. Le fil de signal du servo a ensuite été renvoyé à une sortie numérique de l'Arduino.
Essai
Programmation - Écrivez un script simple pour faire pivoter le servo de la position d'accélérateur désactivé à complètement activé (si vous êtes en train de jouer). J'ai ajouté un paramètre de configuration de l'accélérateur qui limiterait la quantité de mouvement que le servo aurait pour me permettre d'ajuster rapidement la sensation de l'accélérateur.
Jalon
À ce stade, vous devriez avoir;
- servo solidement monté
- câble d'accélérateur connecté du corps de papillon au bras de servocommande
- alimentation câblée pour fournir suffisamment de courant au servomoteur
- contrôle de la position du servo via Arduino
- positions connues pour le servo de l'accélérateur éteint et complètement allumé
Remarque: dans le code final, j'utilise le signal des contrôleurs RC du canal pour contrôler la quantité de mouvement à appliquer à l'accélérateur proportionnellement à la position de son manche. Cela m'a donné la plage allant de complètement désactivé à complètement activé avec le paramètre de configuration de l'accélérateur comme limiteur.
Étape 11: Composants du système - Pilotage
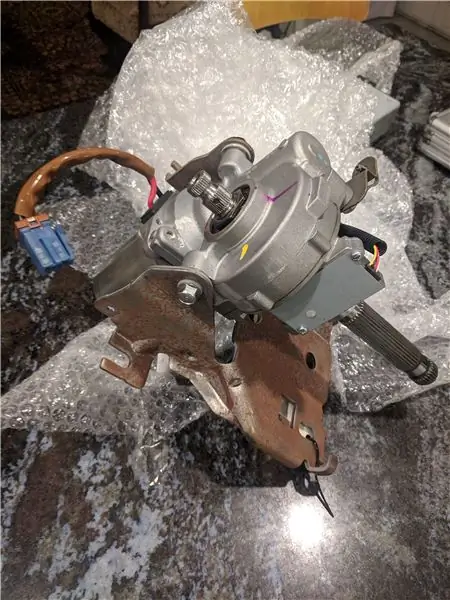

Pouvoir diriger la voiture où nous voulons qu'elle aille est assez important. La plupart des voitures fabriquées dans le passé (avant ~ 2005) utilisaient une direction assistée hydraulique pour rendre le volant très léger pour l'utilisateur. Depuis lors, en raison de la technologie et des demandes des constructeurs automobiles de réduire les émissions, ils ont développé des systèmes de direction assistée électronique (EPS). Ces systèmes utilisent un moteur électrique et un capteur de couple pour aider le conducteur à faire tourner les roues. En supprimant la pompe de direction assistée hydraulique, le moteur est désormais moins sollicité, ce qui permet à la voiture de fonctionner à des régimes plus bas (réduction des émissions). Vous pouvez en savoir plus sur les systèmes EPS ici.
Dans la configuration pour diriger ma petite voiture, j'ai utilisé un système de direction assistée électronique (EPS) d'une Nissan Micra 2009. Je l'ai acheté chez un démolisseur de voitures pour 165 $. J'ai monté ce module EPS sur les boulons de fixation de la colonne de direction existants via un support que j'ai plié à partir d'une barre plate en acier.
J'avais également besoin d'acheter l'arbre de colonne de direction inférieur (~ 65 $) pour connecter l'EPS à la cannelure de la crémaillère de direction. Pour l'adapter à ma voiture, j'ai modifié l'arbre de la colonne de direction en coupant et en soudant la cannelure de la colonne de direction d'origine que j'ai découpée de la Honda à cet arbre.
Pour alimenter/contrôler le moteur EPS à gauche ou à droite, j'ai utilisé un contrôleur de pilote de moteur Sabertooth 2x60A de Dimension Engineering. Je n'ai utilisé qu'un des canaux, mais vous devez vous assurer que vous utilisez un pilote de moteur qui peut fournir ~ 60A+ en continu, fonctionne dans les sens avant/arrière et peut également être contrôlé via un microcontrôleur.
Pour connaître la position de l'angle de braquage, j'ai conçu un capteur de position d'angle de braquage personnalisé. La plupart des voitures utilisent une version numérique qui fonctionne sur le bus CAN, ce qui ne me dérange pas de faire de la rétro-ingénierie. Pour mon capteur de position analogique, j'ai utilisé 2 potentiomètres multitours (5 tours), 3 poulies de courroie de distribution, une courroie de distribution et une plaque en aluminium pour monter les composants. Sur chaque pignon de distribution, j'ai percé et taraudé des trous pour les vis sans tête, puis sur les pots et le PSE, j'ai usiné des méplats pour empêcher les pignons de tourner librement. Ceux-ci ont ensuite été connectés via une courroie de distribution. Lorsque le volant était centré, les pots seraient à 2,5 tours. Quand il était au verrouillage de direction complètement gauche, il serait à 0,5 tour et au verrouillage complet à droite, il serait à 4,5 tours. Ces pots ont ensuite été câblés dans des entrées analogiques sur l'Arduino.
Remarque: La raison de l'utilisation de deux pots était que si la ceinture glissait ou se cassait, je pouvais lire les différences entre les pots et générer une erreur.
Essai
Positionnement - Avant de connecter l'EPS à la colonne de direction inférieure et à la crémaillère de direction de la voiture, il est préférable de tester votre code pour l'EPS et le capteur d'angle de braquage déconnectés.
Circuit - Pour faire pivoter l'EPS à gauche ou à droite, créez un circuit simple avec deux boutons momentanés comme entrées. Un pour faire pivoter l'EPS à gauche et l'autre pour faire pivoter à droite. Cela vous donnera alors un certain contrôle sur le positionnement de l'EPS dans les positions de pilotage.
Programmation - Écrivez un script simple pour positionner le volant au centre, à gauche et à droite. Vous voudrez contrôler la quantité de puissance fournie au moteur car j'ai trouvé que 70% était plus que suffisant pour faire tourner les roues pendant que la voiture était immobile. La livraison de puissance à l'EPS nécessitera également une courbe d'accélération/décélération pour positionner la direction en douceur.
Jalon
À ce stade, vous devriez avoir;
- Système de direction assistée électronique (EPS) solidement installé
- colonne de direction inférieure modifiée pour passer de l'EPS à la crémaillère de direction
- capteur de position d'angle de braquage fournissant l'angle de la crémaillère de direction à Arduino
- pilote de moteur câblé avec EPS et Arduino
- contrôle de la rotation de l'EPS via l'Arduino
- circuit de test pour contrôler le sens de rotation de l'EPS
- Tournez la direction de la voiture complètement à gauche, au centre et à droite via Arduino
Étape 12: Composants du système - Récepteur/Émetteur
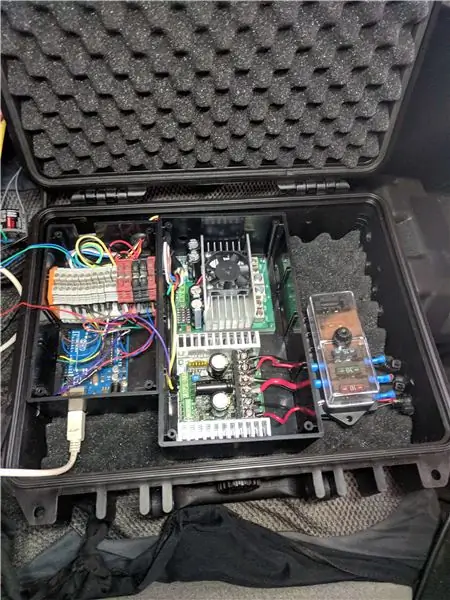
Passons maintenant à la partie amusante qui relie tout le travail que vous avez fait jusqu'à présent. La télécommande est la première phase de suppression de la composante humaine de la conduite, car les commandes seront désormais envoyées au récepteur, puis transmises à l'Arduino pour être exécutées. Dans la deuxième phase de cette série, nous remplacerons l'émetteur/récepteur humain et RC par un ordinateur et des capteurs pour contrôler où il va. Mais pour l'instant, voyons comment configurer l'émetteur et le récepteur RC.
Pour contrôler les composants que nous avons construits à l'intérieur de la voiture jusqu'à présent, nous devons câbler les canaux de sortie du récepteur RC à l'Arduino. Pour cette construction, j'ai fini par n'utiliser que 5 canaux (accélérateur et frein sur le même canal), la direction, le sélecteur de vitesses (commutateur à 3 positions), l'étage d'allumage 1 (alimentation/fonctionnement de la voiture) et l'étage d'allumage 2 (démarreur). Ceux-ci ont tous été lus par l'Arduino en utilisant la fonction PulseIn si nécessaire.
Essai
Programmation - Écrivez un script simple pour lire tous les canaux récepteurs que vous utilisez pour contrôler vos systèmes à l'intérieur de la voiture. Une fois que vous pouvez voir tous les canaux du récepteur fonctionner correctement, vous pouvez commencer à intégrer le code que vous avez créé précédemment avec le code du récepteur. Un bon point de départ est le système d'allumage. Remplacez la lecture des entrées de l'interrupteur et du bouton du circuit de test que vous avez créé par les canaux du récepteur RC que vous avez configurés pour contrôler le système d'allumage (IGN1/Run et IGN2/Start).
Remarque: si vous utilisez l'émetteur Turnigy 9x comme je l'ai fait, vous voudrez le démonter et déplacer quelques commutateurs. J'ai échangé le commutateur momentané "Trainer" avec le commutateur à bascule "Throttle Hold" pour contrôler l'entrée IGN2/Start. Je l'ai fait car vous ne pouviez pas programmer le commutateur « Trainer » en tant que commutateur auxiliaire, mais vous le pouviez avec le commutateur « Throttle Hold ». Avoir un interrupteur momentané pour l'entrée IGN2/Start m'a permis de ne pas détruire le démarreur car il ne ferait que verrouiller le relais haut pendant
Jalon
À ce stade, vous devriez avoir;
- Toutes les sorties du récepteur câblées à l'Arduino
- Arduino capable de lire les entrées pour chaque canal
- Chaque canal est capable de contrôler chaque composant de la voiture (freins, sélecteur de vitesses, etc.)
Étape 13: Programme final

C'est à vous de décider, mais vous trouverez ci-dessous un lien vers mon code qui vous aidera comme point de départ de base pour que votre voiture soit opérationnelle.
Conseillé:
Comment faire un BB8 grandeur nature avec Arduino : 12 étapes
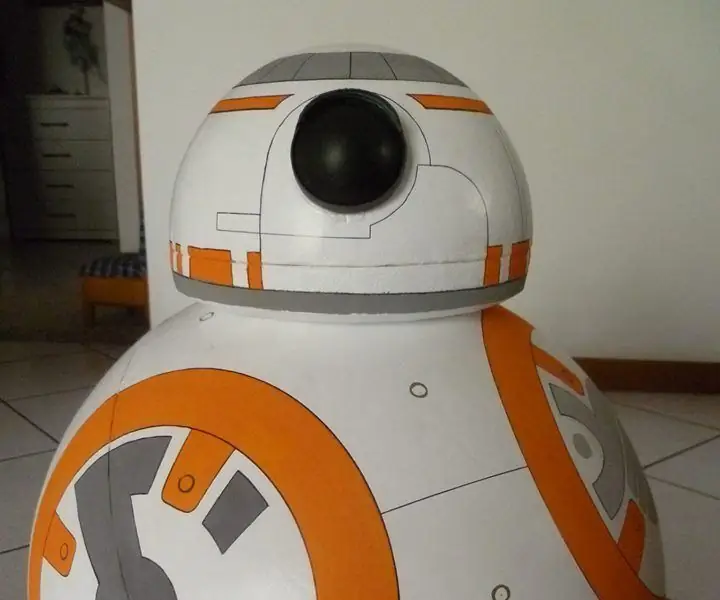
Comment faire un BB8 grandeur nature avec Arduino : Bonjour à tous, nous sommes deux étudiants italiens qui ont construit un clone BB8 avec des matériaux bon marché et avec ce tutoriel, nous voulons partager notre expérience avec vous ! Nous avons utilisé des matériaux bon marché en raison de notre budget, mais le résultat final est très bon
ASPIR : Robot humanoïde imprimé en 3D pleine taille : 80 étapes (avec photos)
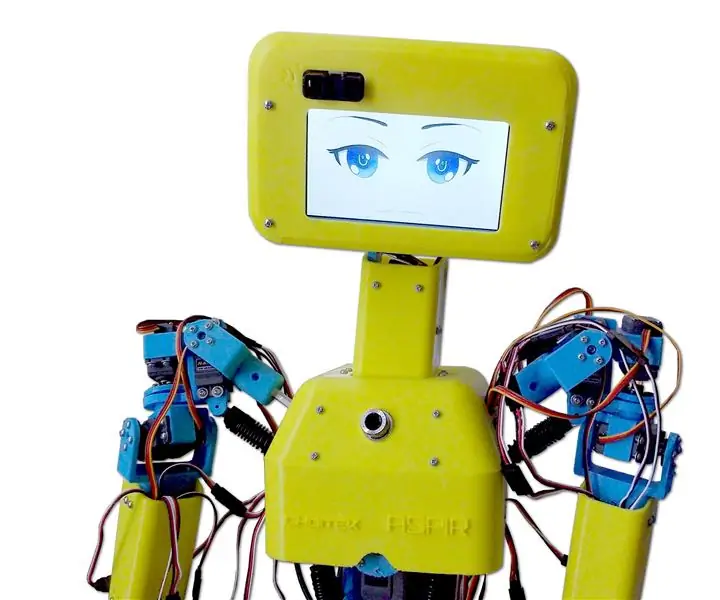
ASPIR : Robot humanoïde imprimé en 3D pleine taille : Robot de soutien autonome et d'inspiration positive (ASPIR) est un robot humanoïde imprimé en 3D open source de 4,3 pieds que n'importe qui peut construire avec suffisamment de motivation et de détermination.Table des matièresNous J'ai divisé cet énorme Instructable en 80 étapes en 10 e
FinduCar : une clé de voiture intelligente guidant les gens vers l'endroit où la voiture est garée : 11 étapes (avec photos)
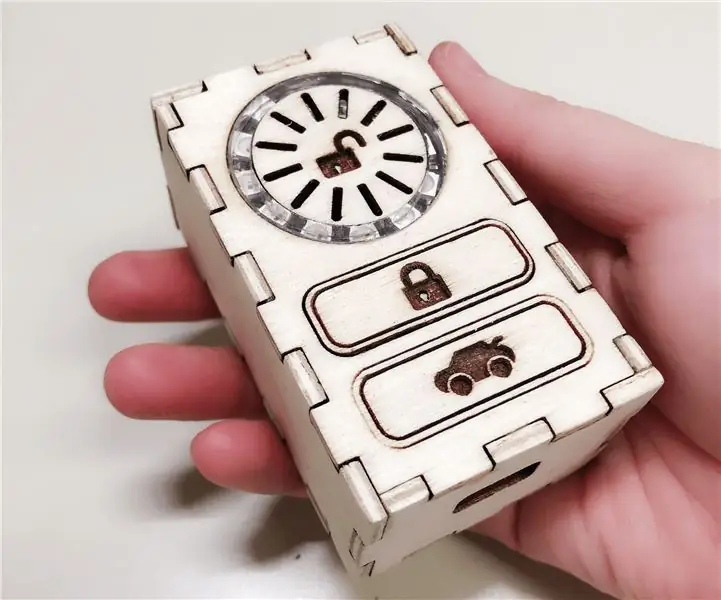
FinduCar : une clé de voiture intelligente guidant les gens vers l'endroit où la voiture est garée : Afin de résoudre les problèmes ci-dessus, ce projet propose de développer une clé de voiture intelligente qui pourrait diriger les gens vers l'endroit où ils ont garé la voiture. Et mon plan est d'intégrer un GPS dans la clé de la voiture. Il n'est pas nécessaire d'utiliser l'application pour smartphone pour suivre le
Circuit redresseur pleine onde via la rectification de pont : 5 étapes (avec photos)
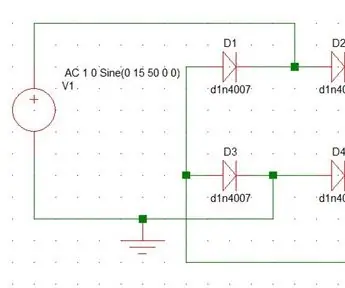
Circuit redresseur pleine onde via la rectification de pont : la rectification est le processus de conversion d'un courant alternatif en courant continu
Jeu d'opération grandeur nature : 14 étapes (avec photos)
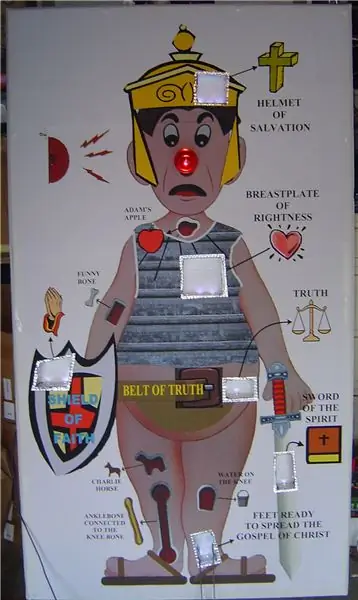
Jeu d'opération grandeur nature : Enfant, j'adorais le jeu d'opération Milton Bradley, le buzzer me faisait toujours peur quand il sonnait, mais c'était amusant. Le but du jeu Opération est de retirer une partie du corps sans toucher la pince à épiler sur les côtés métalliques qui entourent l'objet