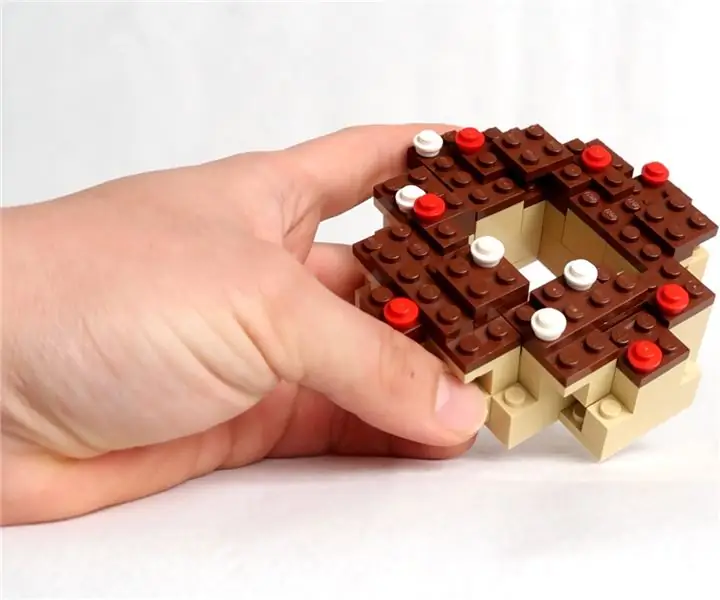
Table des matières:
2025 Auteur: John Day | [email protected]. Dernière modifié: 2025-01-23 14:45
J'ai conçu ce moteur en utilisant Fusion 360 pour une démonstration sur le thème des moteurs, je voulais donc faire un moteur rapide mais cohérent. Il montre clairement les parties du moteur, il peut donc être utilisé comme modèle des principes de fonctionnement de base présents dans un moteur sans balai.
J'ai trouvé que lors de l'alimentation du moteur avec un AA standard, cela fonctionne mieux avec un seul roulement en raison de la diminution du frottement. Lors de l'utilisation d'une tension plus élevée, le roulement supérieur aide à centrer le rotor et lui permet d'atteindre des vitesses plus élevées.
J'ai alimenté mon moteur en utilisant une alimentation CC réglée sur 1-12V et une limite de courant de 6A. Le 6,0 A illustré sur l'écran de l'alimentation n'est pas une mesure de la consommation de courant, mais plutôt une limite de courant. En raison de la résistance présente dans les enroulements du moteur de faible épaisseur, la consommation de courant réelle est bien inférieure à la limite définie. Si vous vouliez un moteur plus utile, avec plus de couple, vous pouvez essayer d'utiliser des enroulements plus épais.
Voici le lien vers les fichiers de ce projet:
www.dropbox.com/sh/8vebwqiwwc8tzwm/AAAcG_RHluX8c6uigPLOJPYza?dl=0
Comment ça marche: Lorsqu'elle est sous tension, la bobine crée un champ magnétique qui pousse ou tire un aimant. Lorsque la bobine est alimentée juste au bon moment, l'aimant est poussé ou tiré et le rotor tourne. La bobine est chronométrée à l'aide d'un interrupteur à lames: lorsqu'un aimant est près de l'interrupteur à lames, l'autre est juste à la bonne position pour être poussé ou tiré par la bobine, ce qui fait tourner le rotor.
Il peut sembler inapproprié d'appeler cela un moteur sans balais à cause du commutateur à lames, mais le commutateur à lames pourrait être remplacé par un capteur à effet Hall à verrouillage et même par une électronique de commande. Afin de piloter le moteur sans limitation de courant, ce capteur doit se connecter à la base d'une paire de transistors Darlington. J'ai opté pour un interrupteur à lames car j'en avais quelques-uns et je ne voulais pas trop compliquer le moteur, car je l'utilisais pour une démo sur les principes d'un moteur brushless.
Répartition des noms de fichiers:
'rotor': C'est le rotor qui aura besoin de supports pour imprimer.
'base': Eh bien, la base !
« sensorMount »: monte le commutateur à lames ou le capteur à effet Hall sur la base. Cette partie nécessite des supports pour imprimer.
'spool1' et 'spool2': imprimez un de chaque; Ceux-ci forment collectivement la bobine pour faire une bobine.
« switchMount »: cette partie facultative passe par-dessus le commutateur pour le maintenir en place.
**Le moteur peut être configuré de deux manières: Avec une source AA ou autre basse tension, le moteur fonctionne bien sans le support de roulement supérieur. En fait, même lorsqu'il tourne rapidement, le moteur n'a pas besoin du support de roulement supérieur et inférieur.
'lowerBearingMountONLY': c'est le support que vous devez utiliser si vous ne souhaitez utiliser qu'un seul roulement pour réduire la friction.
« lowerBearingMount » et « upperBearingMount »: ce sont les supports que vous devez utiliser si vous choisissez d’utiliser deux roulements pour une stabilité et un équilibre accrus.
* Je ne suis pas responsable des blessures ou des dommages matériels pouvant résulter de la suite de ce Instructable. S'ils ne sont pas correctement fixés, les aimants en rotation peuvent présenter un risque pour vous et votre environnement.
Fournitures:
1. Imprimante 3D ou accès à une imprimante 3D (aucun filament magnétique spécial requis)
2. 2 aimants circulaires en néodyme de 12 x 5 mm
3. Fil de cuivre activé. J'ai utilisé ~ 26 jauge, mais je suggère d'expérimenter avec différentes jauges pour obtenir différentes quantités de couple et de vitesse; Un fil plus épais devrait permettre à plus de courant de circuler et se traduit souvent par un moteur avec plus de couple et une consommation de courant plus élevée, mais un kV inférieur. Un fil plus fin devrait avoir pour résultat le contraire des propriétés susmentionnées. N'oubliez pas: plus le calibre du fil est élevé, plus le fil est fin.
4. ~ fil de silicone de calibre 14
5. 1 ou 2 roulements à billes 608 non graissés/non scellés (même taille que ceux trouvés dans les spinners)
6. Interrupteur à lames ou capteur à effet hall de seuil
Étape 1: faire la bobine
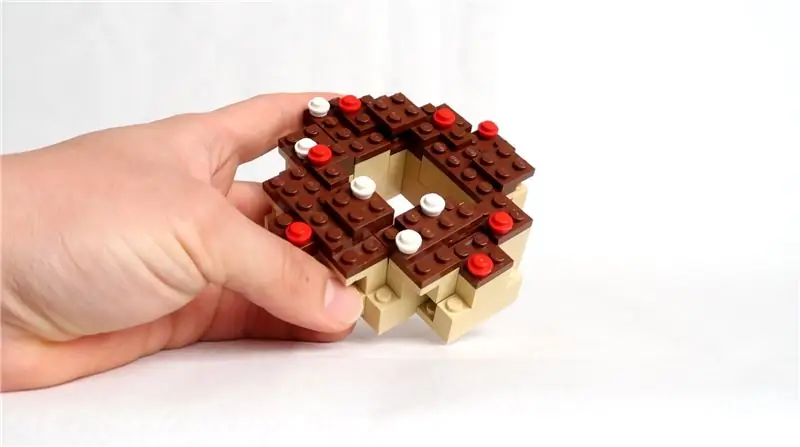
Collez le 'spool1' et le 'spool2' ensemble pour créer une bobine. À l'aide du fil de cuivre émaillé, faites une bobine sur la bobine jusqu'à ce qu'elle se trouve à environ 3 mm sous les bords. Gardez les deux extrémités du fil de quelques centimètres de long pour une utilisation ultérieure.
Étape 2: Assemblage du rotor
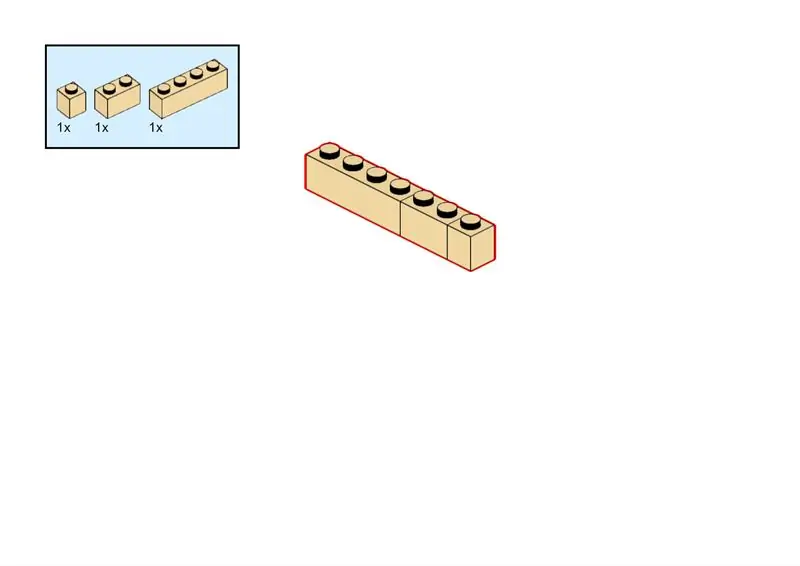
Enfoncez les aimants circulaires de 12 mm⌀ sur 5 mm dans le rotor et utilisez de grandes quantités de colle. Après une inspection plus approfondie de mon moteur après l'explosion (voir la vidéo d'introduction), j'ai découvert que les forces centrifuges élevées provoquaient le décollage d'un aimant et déséquilibraient le rotor. Enrouler du ruban isolant autour du rotor pour fixer les aimants ne serait pas une mauvaise idée. Une fois les aimants fixés, testez l'ajustement des arbres du rotor dans les roulements. Si l'ajustement est trop lâche, enroulez du ruban électrique autour des arbres jusqu'à ce que l'ajustement soit bien ajusté.
Si vous avez besoin d'équilibrer le rotor, je vous suggère d'ajouter de petites quantités d'argile du côté le plus léger ou de poncer du plastique du côté le plus lourd.
Étape 3: Montage du commutateur
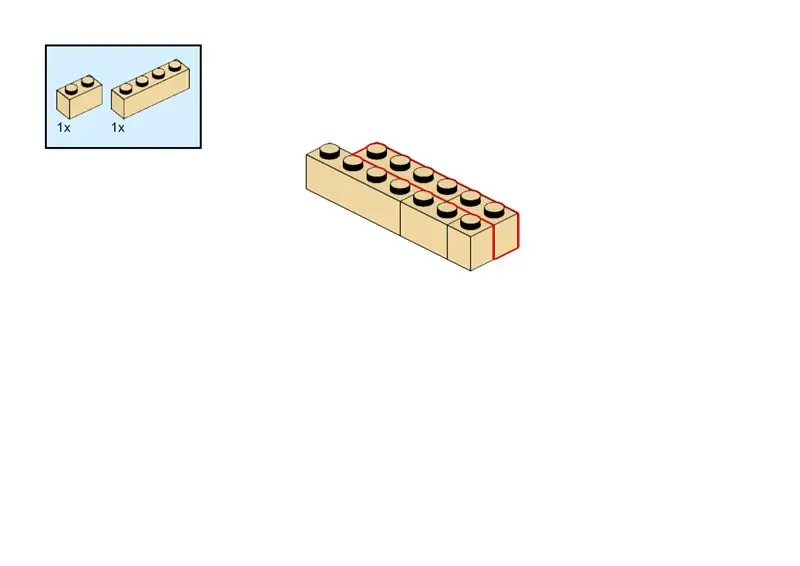
Le « switchMount » fait simplement le tour du haut du commutateur et est fixé avec de la colle. Le commutateur est facultatif mais utile.
Étape 4: Montage de la bobine
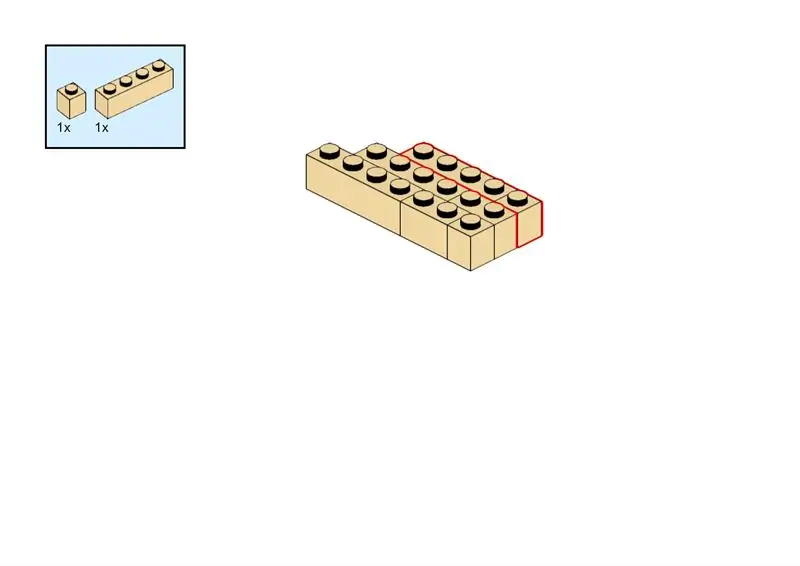
Faites glisser la bobine dans les deux fentes de la base et fixez-la avec de la colle. L'orientation n'a pas d'importance, car nous pouvons changer la polarité lors du câblage.
Étape 5: Montage du rotor
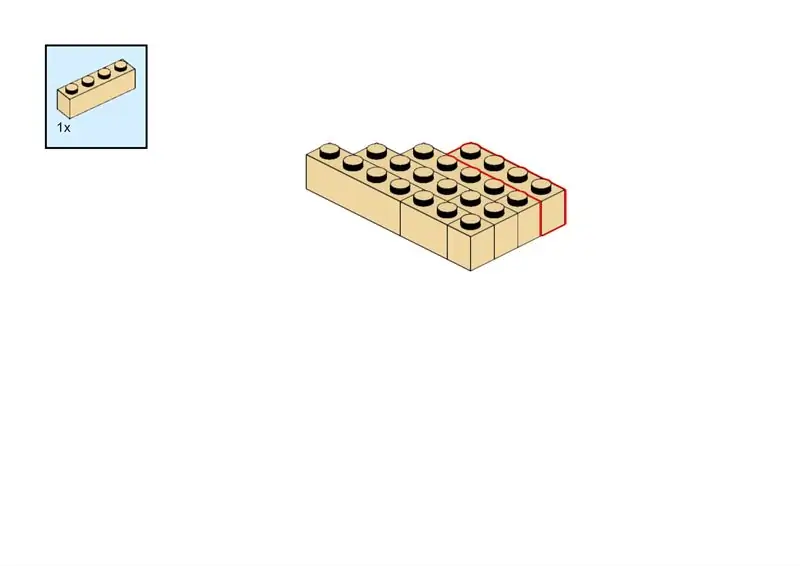
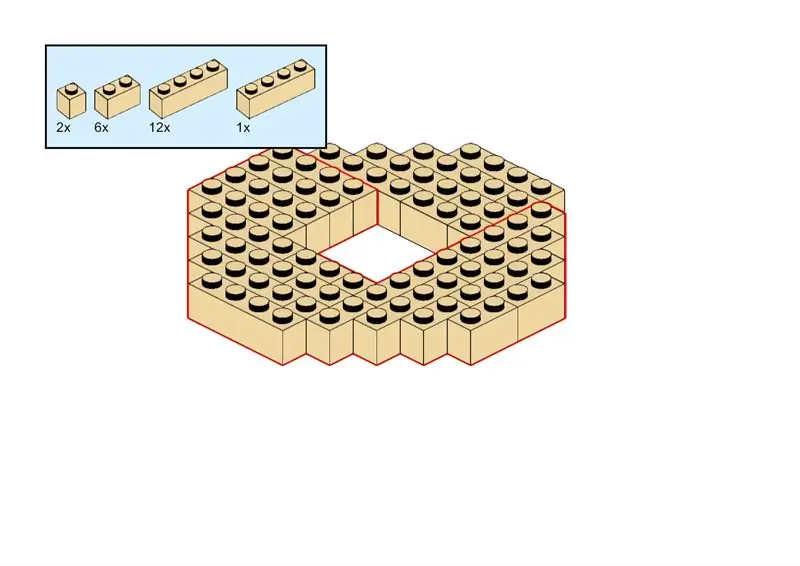
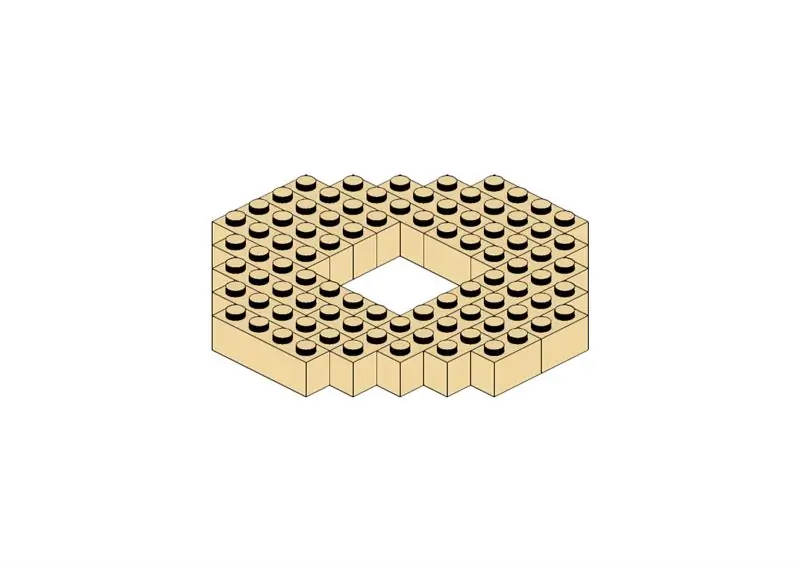
Testez l'ajustement des roulements 608 dans le « lowerBearingMount ». S'il est trop lâche, enroulez du ruban adhésif autour jusqu'à ce qu'il soit bien ajusté.
Le 'lowerBearingMount' ou 'lowerBearingMountONLY' doit être collé à 4 mm à droite de la bobine (du point de vue de l'interrupteur). Le côté de la partie qui a été imprimé face au lit d'impression doit être collé en touchant la base. Assurez-vous d'utiliser un adhésif à haute résistance car le mien s'est effondré lorsque je l'ai collé de manière lâche (voir la vidéo dans l'intro).
Si vous ne l'avez pas déjà fait, enfoncez le roulement dans son support puis enfoncez le rotor dans le roulement:
Si vous utilisez un roulement, appuyez sur le côté du rotor qui est tourné vers le haut lors de l'impression dans le roulement (retournez-le) comme indiqué ci-dessus
Si vous utilisez deux roulements, appuyez sur le deuxième roulement dans le 'upperBearingMount' et collez-le sur le 'lowerBearingMount'. Assurez-vous de le faire APRÈS avoir installé le rotor avec le côté tourné vers le bas pendant l'impression, vers le bas (ne le retournez pas).
Étape 6: Montage du capteur
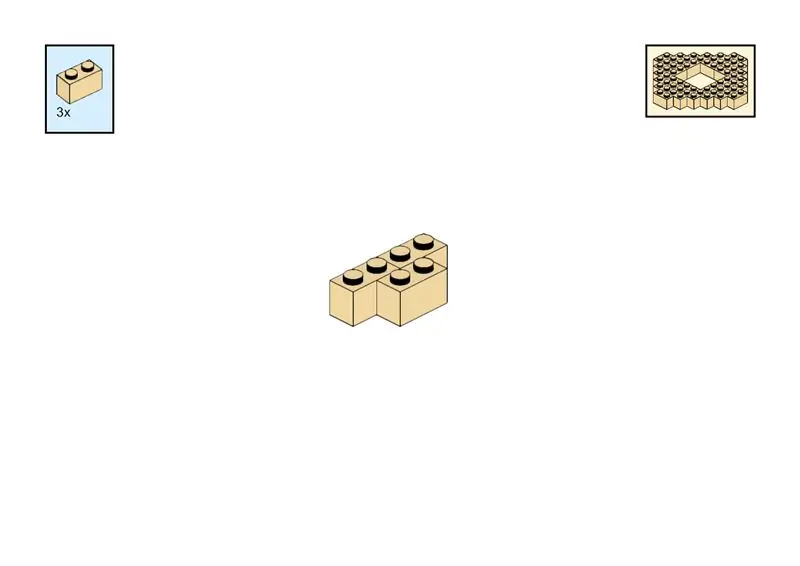
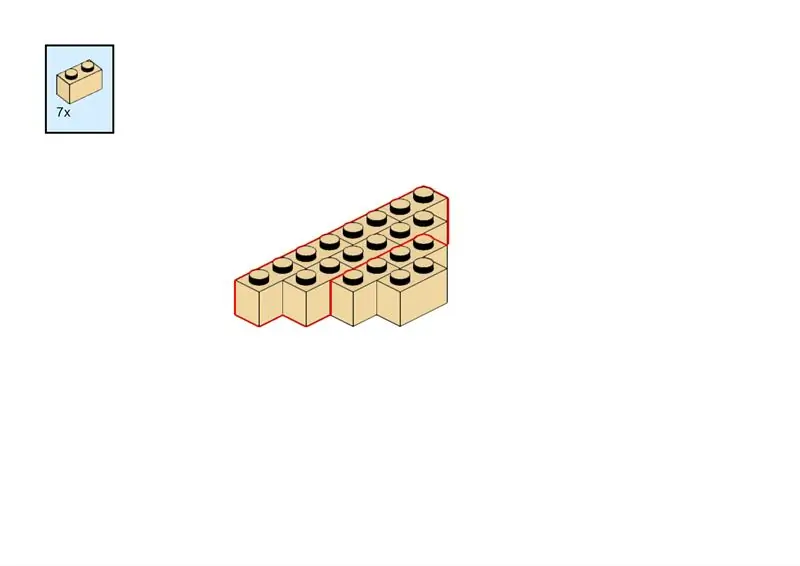
Vous pouvez utiliser un capteur à effet Hall à seuil qui s'allume lorsqu'un aimant est proche ou un interrupteur à lames. J'ai utilisé un commutateur à lames car j'en avais quelques-uns, mais un capteur à effet hall devrait également fonctionner (nécessitant éventuellement un transistor).
J'ai collé le commutateur à lames sur le « sensorMount » et j'ai collé le support à 45 ° sur la bobine. Si vous souhaitez avancer le timing pour optimiser les performances du moteur dans une direction particulière, vous pouvez le faire en rendant la position du capteur légèrement supérieure ou inférieure à 45°. Il doit être espacé du rotor juste assez pour permettre un dégagement pour les aimants. Voir les images ci-dessus.
Étape 7: Câblage
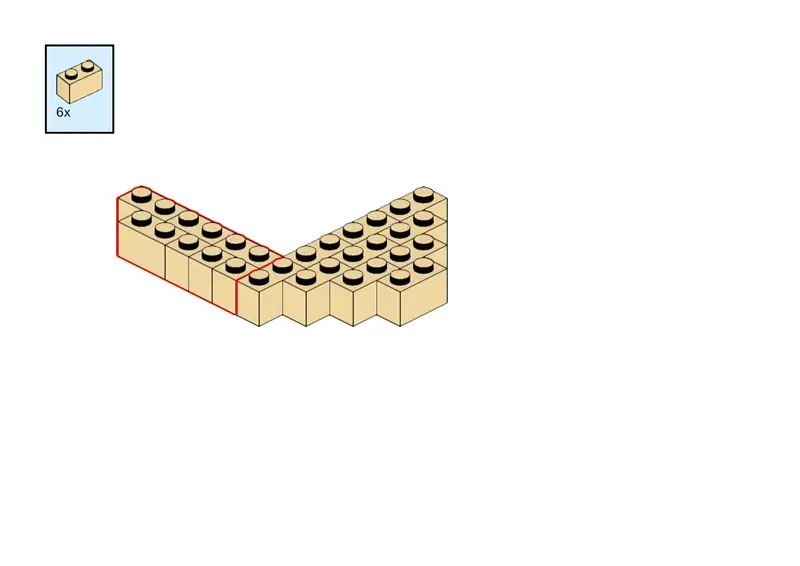
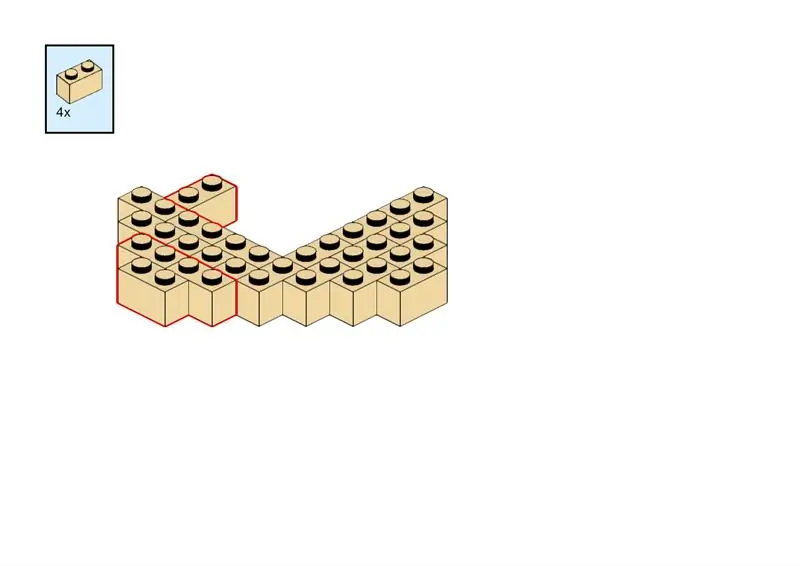
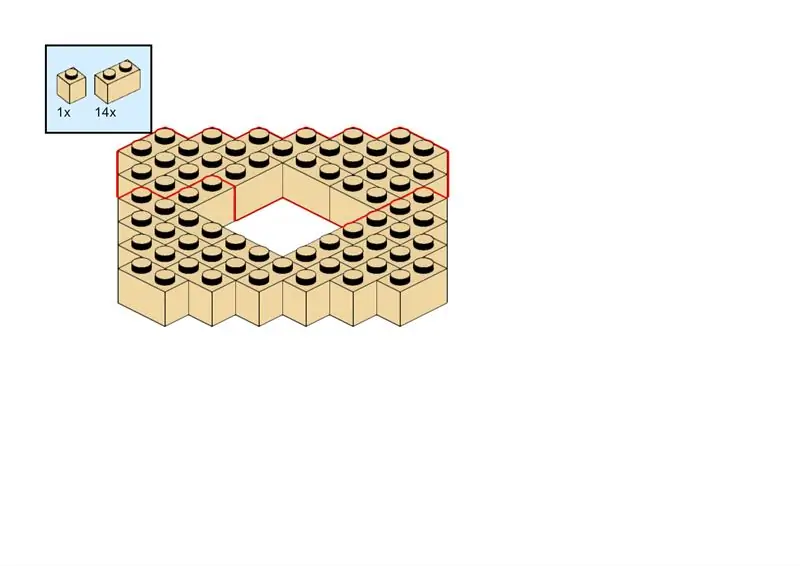
Interrupteur à lames: connectez un fil de la bobine au fil noir de l'interrupteur, puis attachez l'autre fil de la bobine au haut de l'interrupteur à lames. Ensuite, connectez le bas du commutateur à lames à un fil 12 AWG qui ira à votre source d'alimentation. Le fil rouge de l'interrupteur ira également à votre source d'alimentation.
La polarité n'a pas d'importance car le moteur tournera simplement dans la direction opposée si la polarité est inversée.
Vous pouvez utiliser à la place un capteur à effet Hall et Arduino pour piloter le moteur plutôt que d'utiliser un commutateur à lames, mais j'avais quelques commutateurs à lames qui traînaient et je ne voulais pas trop compliquer le moteur car je l'utilisais pour une démonstration.
Conseillé:
Inrunner de moteur à courant continu sans balais : 6 étapes
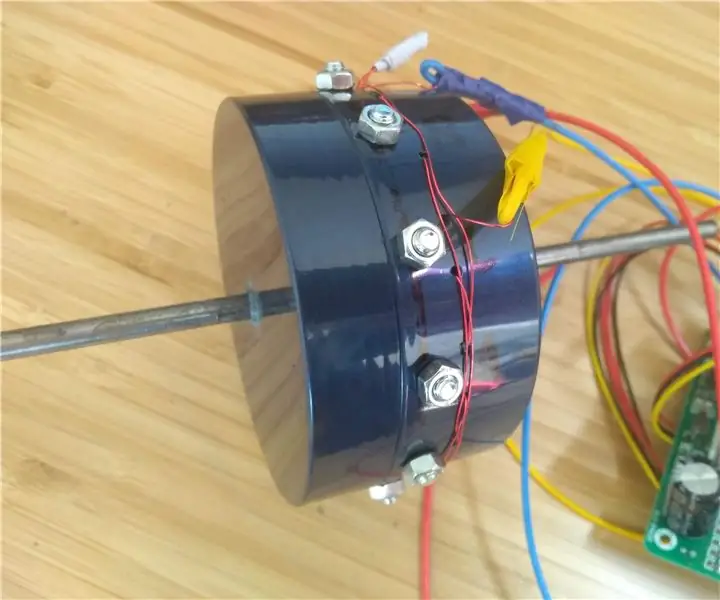
Brushless DC Motor Inrunner : Ayant lu l'Instructable https://www.instructables.com/id/Make-A-Brushless-… et étant en possession d'une bobine de fil magnétique (j'avais acheté pour enseigner à mon fils à propos des électro-aimants) J'ai pensé, pourquoi ne pas essayer aussi.Voici mon effort
Interfaçage d'un moteur à courant continu sans balais (BLDC) avec Arduino : 4 étapes (avec photos)
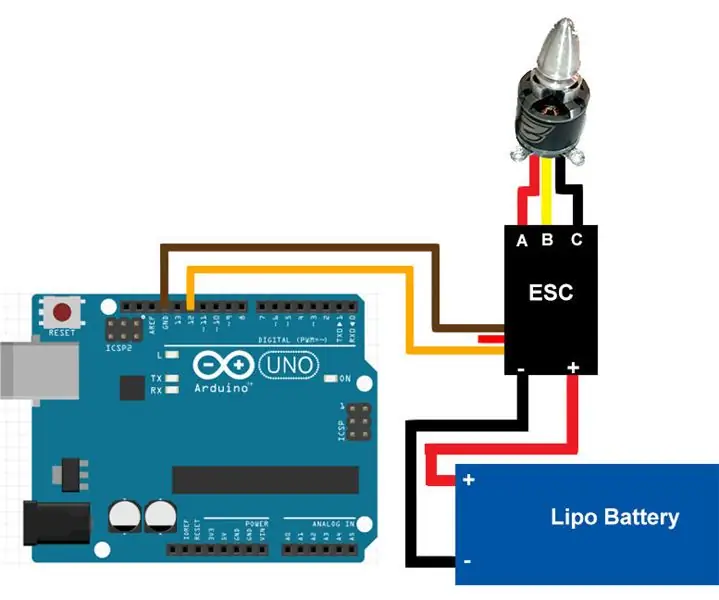
Interfaçage d'un moteur à courant continu sans balais (BLDC) avec Arduino : il s'agit d'un didacticiel sur la façon d'interfacer et d'exécuter un moteur à courant continu sans balais à l'aide d'Arduino. Si vous avez des questions ou des commentaires, veuillez répondre dans les commentaires ou par courrier à rautmithil[at]gmail[dot]com. Vous pouvez également me contacter @mithilraut sur twitter.Pour
Moteur à courant continu sans balais : 6 étapes (avec photos)
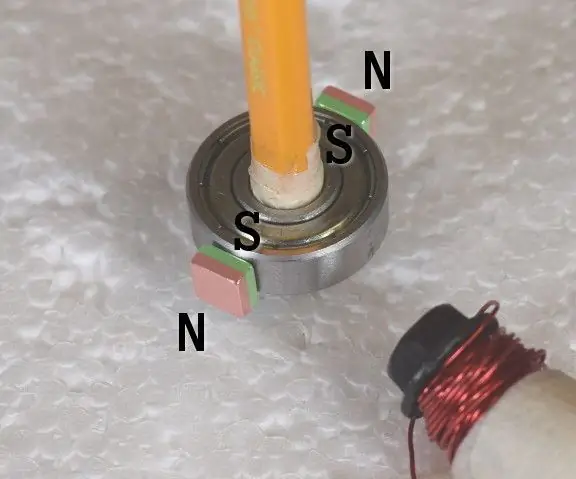
Moteur à courant continu sans balais : fabriquons un moteur électrique qui tourne à l'aide d'aimants et de fils en néodyme. Cela montre comment un courant électrique est converti en mouvement. Nous construisons un moteur à courant continu sans balais primitif. Il ne remportera aucun prix d'efficacité ou de design, mais nous aimons
Contrôlez la vitesse du moteur à courant continu sans balais à l'aide d'un module Arduino et Bluetooth (HC-05): 4 étapes
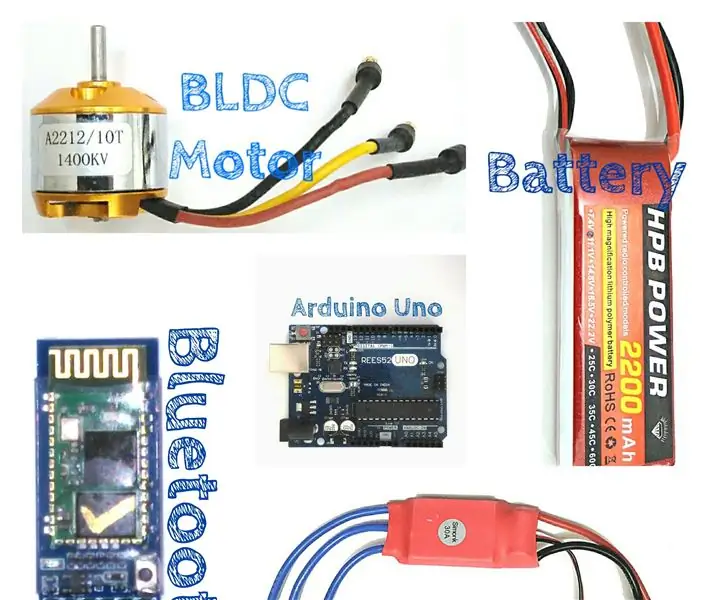
Contrôler la vitesse du moteur à courant continu sans balais à l'aide d'Arduino et du module Bluetooth (HC-05) : IntroductionDans ce didacticiel, nous allons contrôler la vitesse du moteur à courant continu sans balais à l'aide d'Arduino UNO, du module Bluetooth (HC-05) et de l'application Android pour Bluetooth ( Contrôleur Bluetooth Arduino)
Exécuter un moteur sans balais par Arduino + L298 : 6 étapes
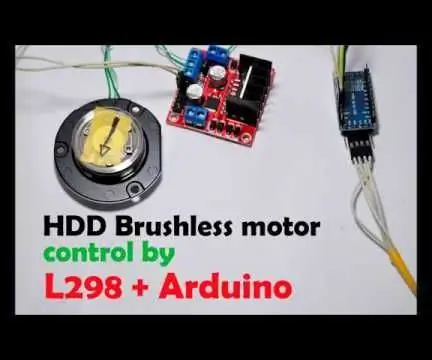
Exécuter le moteur sans balai par Arduino + L298 : cette instructable montrera comment faire fonctionner le moteur sans balai CC (tiré du disque dur) avec H-Bridge L298