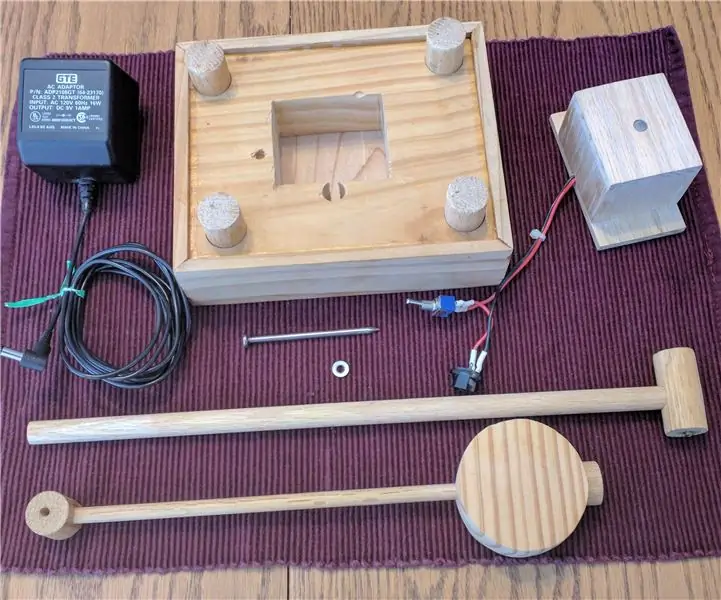
Table des matières:
2025 Auteur: John Day | [email protected]. Dernière modifié: 2025-01-23 14:45
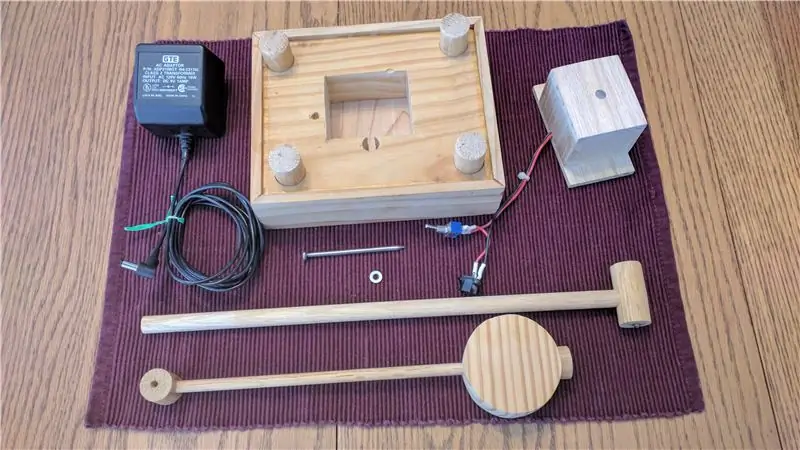
À la fin des années 1980, j'ai décidé de construire une horloge entièrement en bois. A l'époque il n'y avait pas internet donc c'était beaucoup plus difficile de faire des recherches qu'aujourd'hui… même si j'ai réussi à bricoler un échappement à roue et pendule très grossier. Le temps d'exécution était limité et c'était plutôt fastidieux, mais il cliquait pendant quelques minutes avant que le poids ne touche le sol. Mes ressources étaient également limitées… outils, argent, compétences en menuiserie… ce qui rendait le travail sur le projet plutôt frustrant. Ainsi, pour l'heure, le rêve de l'horloge en bois a été abandonné. Avance rapide de plus de 30 ans. Je suis à la retraite maintenant, j'ai beaucoup de très bons outils et mes compétences en menuiserie se sont considérablement améliorées. J'ai également accès à des ordinateurs, à d'incroyables logiciels de conception assistée par ordinateur (CAO) et à Internet. Le projet d'horloge est donc de retour. J'ai décidé d'écrire sur le processus au fur et à mesure que je progresse dans la conception. Cela semble juste être une chose amusante à faire.
Au départ, je voulais construire une horloge entraînée par gravité et régulée par un pendule. Récemment, alors que je fouillais au hasard sur Internet, je suis tombé sur un gars sur l'île de Kauai qui conçoit des horloges en bois et d'autres types d'« art cinétique ». Il s'appelle Clayton Boyer. C'est la découverte des conceptions d'horloges de M. Boyer qui m'a inspiré à poursuivre mon propre projet d'horloge. L'une de ses créations qui m'a fasciné s'appelait le « Toucan ». L'échappement à marche utilisé sur l'horloge ressemblait au bec de l'oiseau du même nom. C'était une horloge amusante à regarder et le design était très fantaisiste, mais ce qui a finalement attiré mon attention, c'est la façon dont elle était conduite. Il n'y avait ni poids ni ressorts. Le pendule semblait osciller comme par magie d'avant en arrière sans aucune perte d'énergie. Le secret était un système d'entraînement électromagnétique caché dans la base de l'horloge et un aimant à l'extrémité du pendule. En tant qu'ingénieur électricien, j'ai pensé que c'était vraiment cool et j'ai décidé de comprendre comment tout cela fonctionnait et de créer ma propre version du Toucan de M. Boyer. Pour être sûr… J'aurais pu acheter les plans pour l'horloge puisqu'ils étaient disponibles pour environ 35 $, mais où est le plaisir là-dedans ?
Après avoir creusé un peu plus sur Internet, j'ai découvert que le concept remontait au début des années 1960 avec les horloges anniversaire Kundo. Ils étaient alimentés par une pile sèche et fonctionnaient pendant environ un an avant de devoir changer la pile (d'où le nom, je suppose). La simplicité du circuit d'entraînement m'a intrigué. Il y avait deux bobines (l'une enroulée l'une sur l'autre), un transistor au germanium et une batterie. C'est tout! J'aime les choses simples qui fonctionnent et cela ne pourrait pas être beaucoup plus simple. L'une des bobines est connectée à l'entrée de base du transistor et l'autre bobine est du côté sortie du transistor en série avec la batterie. L'autre pièce du puzzle était un aimant monté au bout d'un pendule. Lorsque le pendule oscille par les bobines, l'aimant induit un courant dans la bobine entraînant la base du transistor. Cela provoque l'activation du transistor et le courant circule dans le circuit de sortie de la batterie à travers la bobine qui est en série avec elle. Il existe également un effet de transformateur qui provoque l'induction de plus de courant dans la bobine d'entrée jusqu'au point où le transistor sature. La quantité maximale de courant circule maintenant dans le côté sortie du transistor et la bobine de ce circuit est entièrement alimentée par la batterie, créant ainsi un électro-aimant de même polarité que l'aimant du pendule. Le timing est tel que le champ magnétique généré par l'électroaimant repousse l'aimant dans le pendule lorsqu'il passe et lui donne un petit coup de pied. Une fois que le pendule passe devant les bobines, le courant cesse de circuler dans la base du transistor et il s'éteint. Ce processus est répété à chaque fois que le pendule oscille par les bobines… fournissant l'énergie supplémentaire nécessaire pour surmonter les pertes au sein du système et maintenir tout en mouvement. Bien, hein ? Ce qui est vraiment génial, c'est qu'il consomme très peu d'énergie et que la batterie durera longtemps. Les horloges en bois entraînées par des ressorts ou des poids ne fonctionneront qu'un jour environ avant de devoir être remontées. Ils ont leur propre attrait, mais remonter l'horloge tous les jours m'a semblé pénible. Je pourrais encore en construire un un jour (j'adore les échappements Arnfield) mais pour l'instant, ce sera de l'électronique au lieu de la gravité.
La première étape de ce voyage consiste donc à comprendre comment construire le pendule à impulsion électromagnétique, car il régulera non seulement l'horloge, mais sera également le moteur qui l'entraîne. En fin de compte, en plus de ce didacticiel sur le pendule, je publierai un certain nombre de didacticiels couvrant la conception d'horlogerie en général, la conception d'engrenages, la construction de cadres, puis j'assemblerai le tout pour terminer une horloge fonctionnelle. Alors attachez-vous… c'est parti avec le processus de conception du pendule…
Fournitures
Le composant principal du pendule à impulsion électromagnétique est le circuit de la bobine. J'ai utilisé un clou commun 10d (disponible dans votre quincaillerie moyenne) comme noyau de ferrite. Le câblage des bobines est un fil magnétique de 35 AWG. Il s'agit d'un fil très fin recouvert d'un fin matériau non conducteur. Un transistor à jonction bipolaire 2N4401 NPN est utilisé pour contrôler le flux de courant dans le circuit. Le ruban Kapton recouvre l'ongle et le noyau terminé, mais vous pouvez utiliser à peu près n'importe quel type de ruban. Les embouts de la bobine sont en feuille acrylique de 1/16 de pouce ainsi qu'une pièce cylindrique en chêne pour loger le câblage du transistor et de la bobine. Divers morceaux de bois de rebut ont été utilisés pour le reste de l'assemblage du prototype ainsi que des tiges de goujon dans un certain nombre de diamètres. J'adore travailler avec des goujons… ça me rappelle l'un de mes jouets d'enfance préférés… Tinker Toys ! Je trouve qu'ils se prêtent assez bien au développement de prototypes. L'alimentation est un module mural enfichable qui convertit le 110 CA en 9 volts CC. En fin de compte, l'horloge finira par être alimentée par batterie, mais pour l'instant, le module enfichable est très pratique et cohérent. Un autre élément clé est un aimant en néodyme intégré à l'extrémité du pendule. L'aimant que j'ai utilisé mesure 1/2 pouce de diamètre et un quart de pouce d'épaisseur.
Étape 1: Assemblage du noyau de la bobine
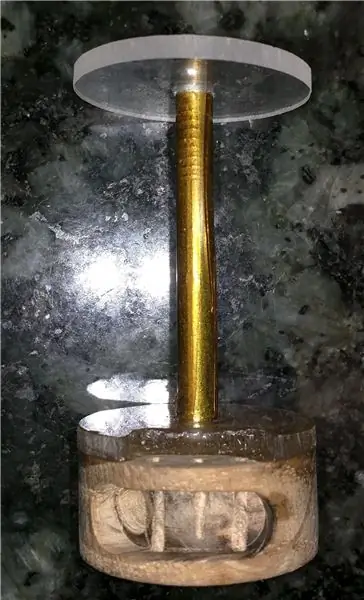
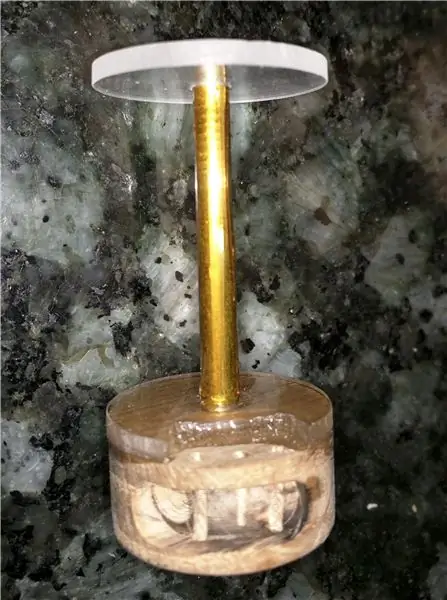
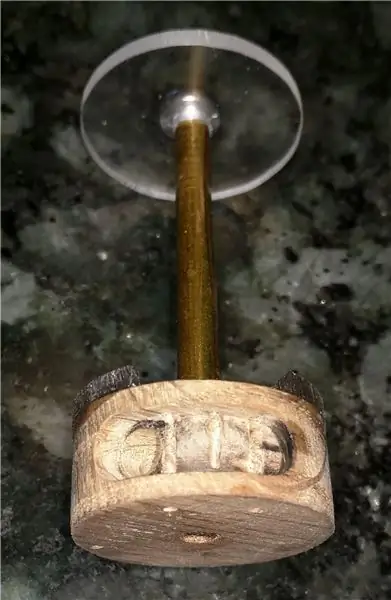
Alors que je faisais mes recherches pour la bobine, je suis tombé sur un forum de réparation d'horloges où l'un des fils de discussion discutait des détails de la conception de la bobine. Ils avaient de superbes photos qui m'ont donné l'idée de cacher le transistor et le câblage associé à l'intérieur de la base de la bobine. Un autre détail clé était qu'ils ont mentionné les bobines contenant 4000 tours. Wow, cela semblait beaucoup et a créé une petite inquiétude dans mon esprit quant à savoir à quel point il allait être raisonnable d'enrouler la bobine, mais j'ai quand même continué.
J'ai réfléchi à la taille que je voulais pour la bobine finie et j'ai choisi un pouce de diamètre et un pouce et quart de long. J'ai découpé des cercles de 1 pouce de diamètre dans une feuille acrylique de 1/16 pouce à utiliser pour les embouts et un autre disque de 1 pouce de diamètre dans un morceau de chêne de 1/2 pouce d'épaisseur pour la base. J'ai fraisé un canal d'un quart de pouce dans le disque de chêne et j'ai percé un trou de 3/16 pouce de diamètre pour loger le transistor. J'ai également percé de petits trous pour pouvoir acheminer le câblage dans le canal de la base. Voir les photos pour plus de détails. Au départ, j'ai découpé une section dans la pièce en acrylique inférieure pour faciliter le passage des fils dans la base. Avec le recul, j'aurais dû juste percer de petits trous pour correspondre à ceux de la base. Mais pas grave. Des trous ont également été percés dans les pièces en acrylique et la pièce en chêne pour un ajustement parfait sur l'ongle. L'assemblage était le suivant: Placer le disque acrylique non encoché sur l'ongle. Enroulez un morceau de ruban adhésif de 1-1/4 pouce autour de l'ongle comme indiqué, puis ajoutez le disque acylique cranté. J'ai appliqué de l'époxy sur le disque en chêne, puis je l'ai glissé sur l'ongle de manière à ce qu'il soit collé au disque acrylique.
Avant de passer au processus d'enroulement de la bobine, j'ai fait quelques calculs rapides et grossiers pour avoir une idée approximative de la taille du câblage fini et de la résistance électrique des deux bobines. Il est apparu que je serais capable d'adapter tout le fil sur mon assemblage de noyau, donc j'étais heureux.
Étape 2: Gabarit d'enroulement de bobine
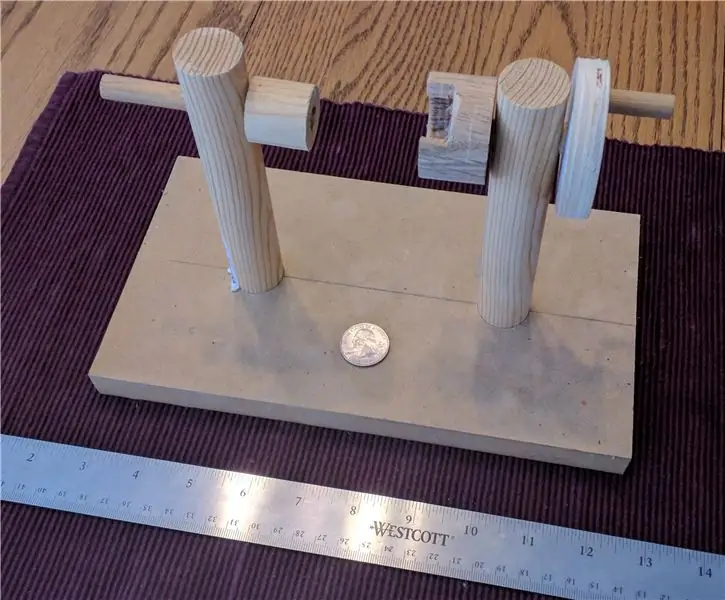
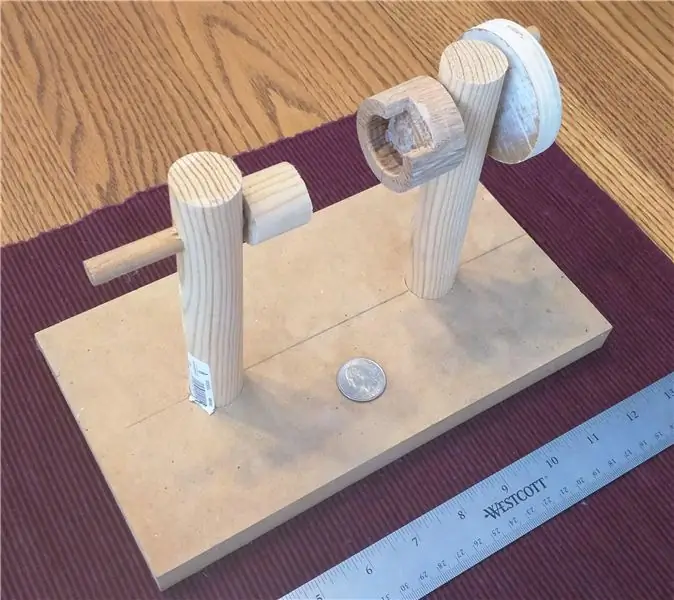
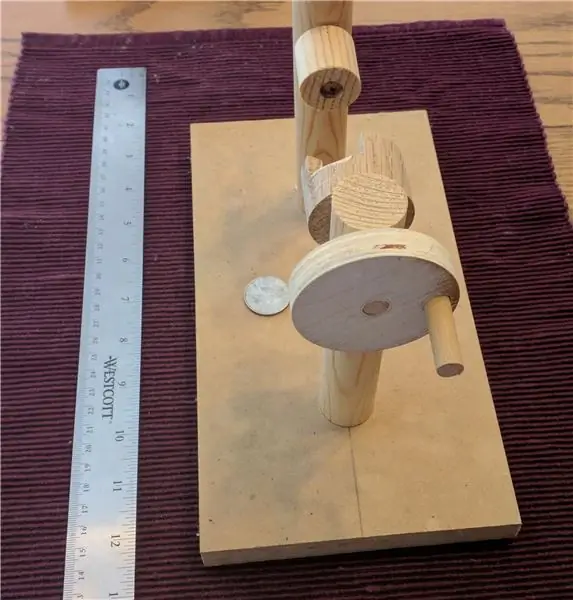
J'ai décidé qu'enrouler le fil autour du noyau totalement à la main serait une énorme douleur, alors inspiré par la technologie Tinker Toy, j'ai bricolé un gabarit à partir de goujons et de morceaux de contreplaqué et de MDF. J'ai constaté que je devais mettre un peu de colle chaude sur le disque en chêne du noyau de la bobine pour le maintenir bien en place. Sinon il y avait un peu trop de friction dans l'assemblage et le noyau ne bougeait pas quand je tournais la manivelle. Donc avec un peu plus de ponçage pour réduire encore les frottements et la touche de colle chaude le gabarit était opérationnel.
Étape 3: Enrouler les bobines
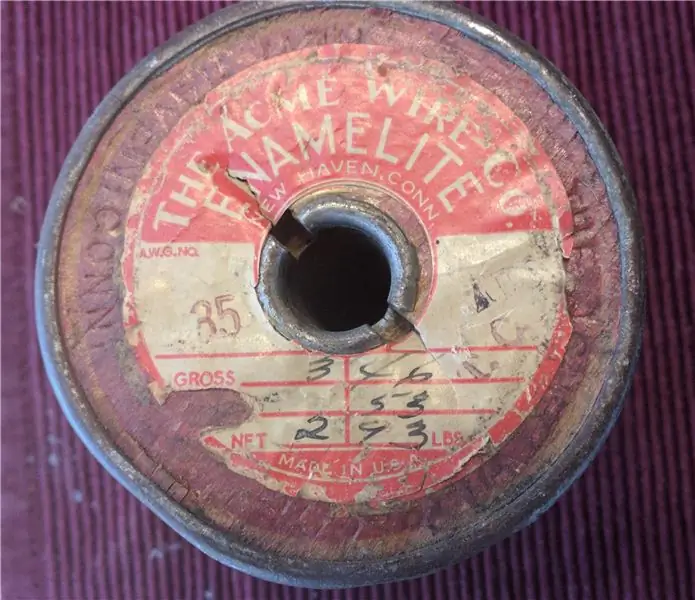
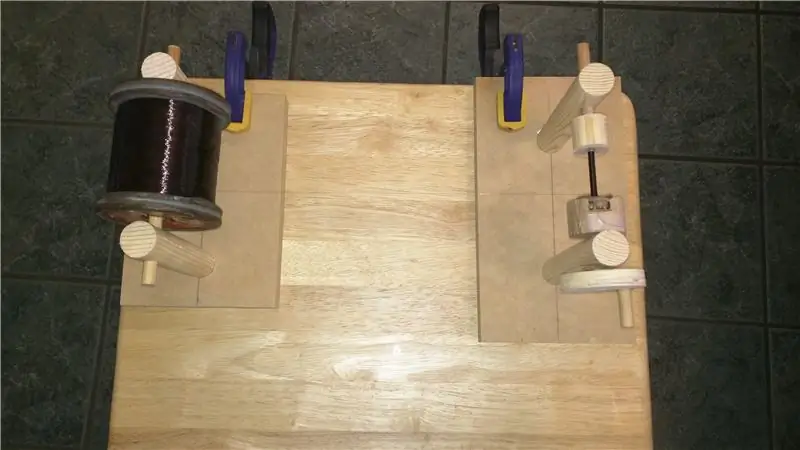
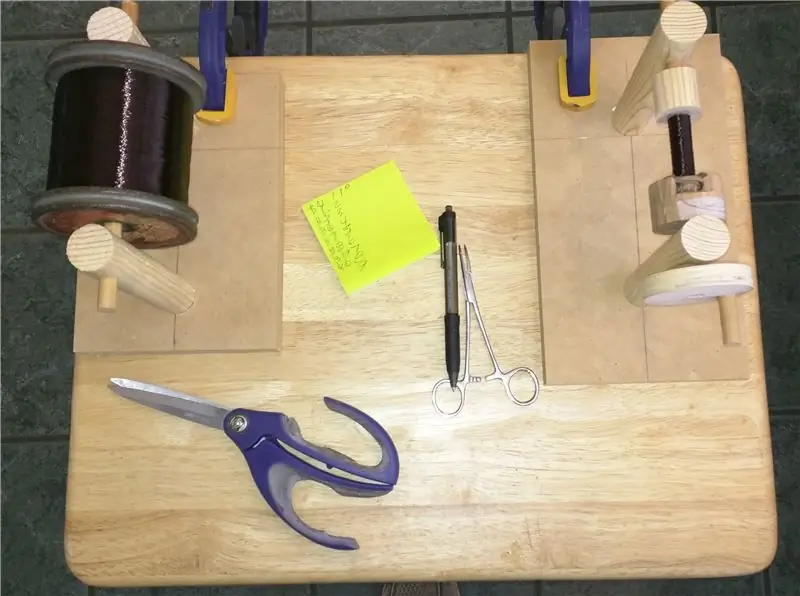
Le fil est un type spécial de fil appelé fil magnétique. Il s'agit d'un fil monobrin très fin recouvert d'un fin matériau isolant. J'ai utilisé du 35 AWG. C'est très courant et comme à peu près tout le reste, vous pouvez l'obtenir sur Amazon. J'ai récupéré la bobine que vous voyez sur la première photo de la poubelle au travail après un nettoyage de laboratoire. Je ne sais pas quel âge il a, mais il semble avoir été acheté il y a plusieurs décennies. MDR.
Nous allons enrouler deux bobines, l'une au-dessus de l'autre, sur le clou dans l'assemblage du noyau. Il est essentiel que les deux bobines soient enroulées dans le même sens autour de l'assemblage… sinon cela ne fonctionnera pas. Chaque bobine aura environ 4000 tours autour de l'ongle. Maintenant, ce n'est pas si grave si vous ne vous retrouvez pas avec exactement 4000 tours sur chaque bobine, vous n'avez donc pas besoin de vous soucier de ce détail, mais j'avais un bloc-notes que j'avais l'habitude de suivre. Cela a pris quelques heures pour terminer le processus d'emballage, mais je viens d'allumer un match de football à regarder pour ne pas m'ennuyer. Je pouvais faire environ 50 tours autour de l'ongle à chaque passage, donc je faisais quelques passages pour obtenir une centaine de tours et je le notais sur mon bloc-notes et j'ai continué jusqu'à ce que j'atteigne 4000 tours.
Voici le processus d'emballage: Commencez à enrouler la bobine intérieure en enfilant 2 ou 3 pouces de fil dans la pièce de base en chêne. Étiquetez l'extrémité de ce fil "1". Complétez vos 4000 enveloppements et assurez-vous de vous retrouver à l'extrémité de la base en chêne du noyau. Coupez le fil et laissez environ 2 ou 3 pouces de longueur supplémentaire afin que vous puissiez le remettre dans la base en chêne. Étiquetez cette extrémité « 2 ». Commencez la bobine extérieure de la même manière en enfilant 2 ou 3 pouces de fil dans la base en chêne. Étiquetez cette extrémité « 3 ». Faites encore 4000 tours, coupez le fil et enfilez l'extrémité dans la base de la même manière qu'avant. Étiquetez cette extrémité « 4 ». Les photos 4 et 5 montrent le résultat final du processus d'emballage. Encore une fois… Assurez-vous d'enrouler les bobines intérieures et extérieures dans le même sens !!!
Étape 4: Compléter le circuit

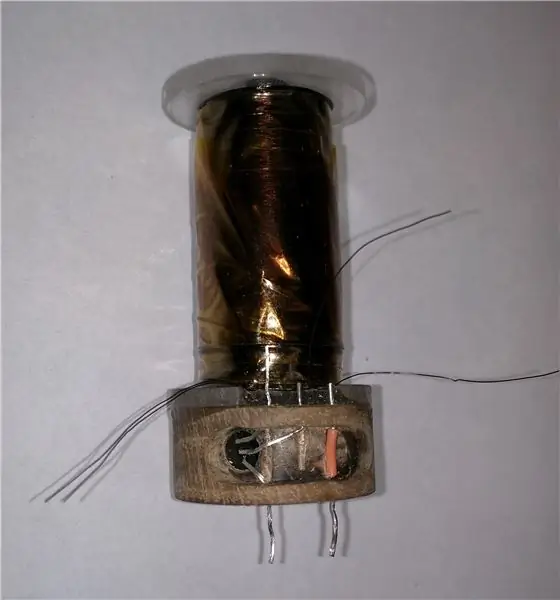
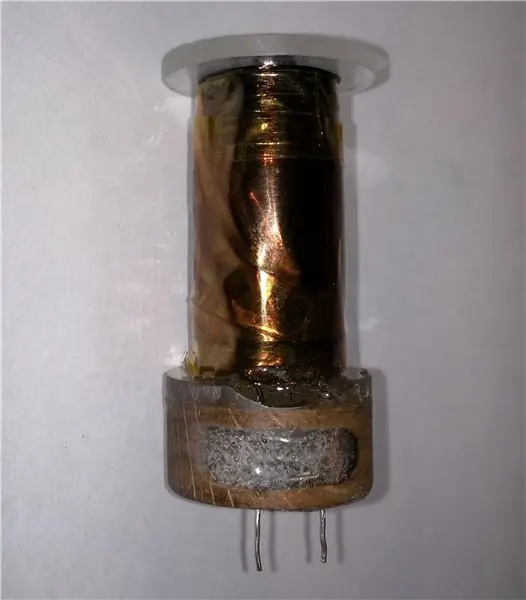
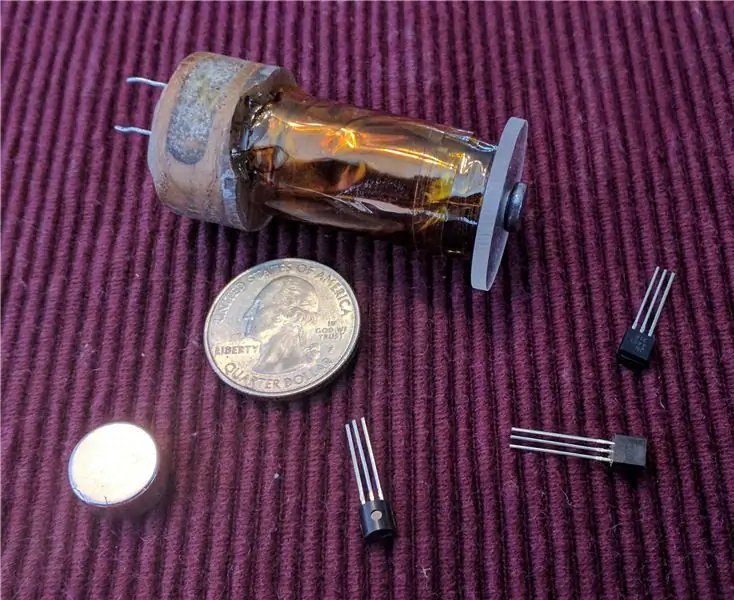
Comme vous pouvez le voir sur le schéma, le circuit est extrêmement simple, ce qui rend cet appareil incroyablement cool. J'ai vu des projets similaires qui utilisaient des processeurs à la place… ce qui pour moi est comme utiliser un marteau pour tuer une mouche. Je ne veux pas faire tomber ce type de projets, mais je suis juste un grand fan de conceptions qui font le travail avec le plus bas niveau de complexité.
Dans la deuxième image, je jouais avec différentes stratégies de routage pour le câblage. J'en ai probablement fait une plus grosse affaire que je n'aurais dû. Il n'y a que quelques points clés… il suffit de le câbler comme sur le schéma, mais comme l'alimentation va être externe à l'assemblage de la bobine, vous devez avoir les fils qui se connecteront à la source d'alimentation qui dépassent du bas de l'assemblage. En d'autres termes: le fil V+ va au collecteur du transistor et le fil V- va au fil étiqueté "2" sur votre bobine. Donc, en fin de compte, votre assemblage de bobines aura une borne positive et une borne négative. C'est une bonne idée de les étiqueter comme tels lorsque vous avez terminé afin de ne pas oublier lequel est lequel. Ah… j'ai presque oublié. Vous devrez utiliser un morceau de papier de verre fin pour enlever le revêtement isolant sur le fil magnétique avant de le souder ! Pour plus de clarté sur le schéma… "Lo" est la bobine extérieure et "Li" est la bobine intérieure et notez également que j'ai étiqueté les extrémités des fils de la bobine 1, 2, 3 et 4 pour correspondre à la façon dont nous l'avons fait quand nous avons enroulé les bobines.
J'ai testé la bobine avant de la mettre en pot avec de l'époxy… bonne chose car j'avais fait une erreur ! Ha, je me suis fait mal en parlant de la simplicité de tout. Assurez-vous donc de tester votre assemblage avant de le mettre en pot.
Pour tester l'assemblage terminé, j'ai collé un aimant de terre rare sur une longueur de fil et je l'ai suspendu juste au-dessus de la tête du clou dans la bobine. Branchez ensuite l'alimentation sur la bobine et faites pivoter l'aimant au-delà de la tête du clou. Il devrait décoller tout seul. Il y a un point idéal pour la distance entre l'aimant et la tête du clou. Trop près et le mouvement est saccadé… trop loin et ça ne fonctionnera pas.
La dernière photo montre la bobine terminée ainsi que l'aimant en terre rare (néodyme) que j'ai utilisé.
Étape 5: Composants du pendule
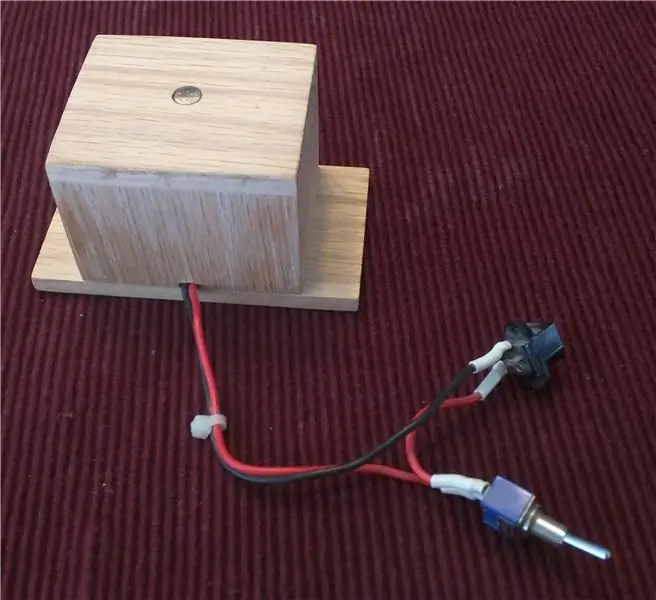
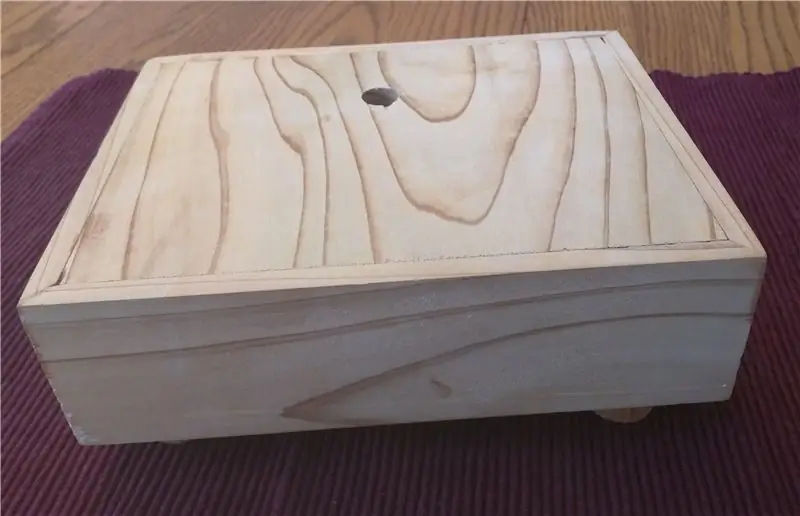
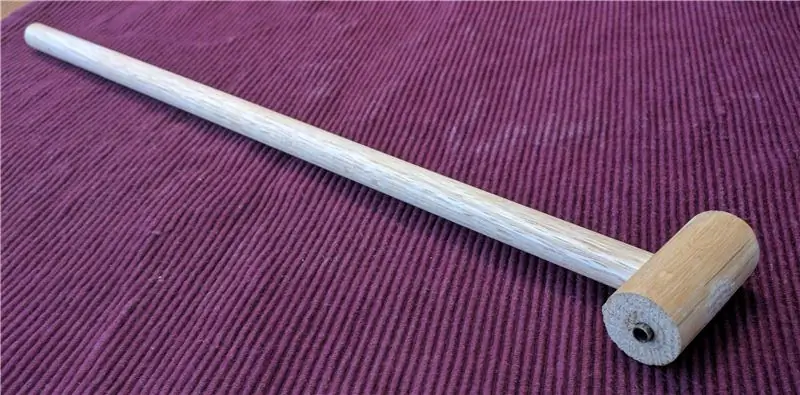
Une fois que j'ai eu une bonne conception de travail connue pour l'assemblage de la bobine, j'ai dû construire un prototype de pendule afin que je puisse évaluer ses caractéristiques de performance. J'étais très curieux de savoir combien de puissance l'appareil utilisait et j'avais également besoin de savoir à quel point le pendule oscillerait, car cela affecterait la façon dont je procédais avec la conception de mon horloge.
J'ai emballé mon assemblage de bobines dans une petite boîte en bois et j'ai ajouté un interrupteur et une connexion électrique. La boîte s'insère à l'intérieur d'une découpe au bas de l'assemblage de base illustré à la deuxième image. Tout était un ajustement par friction afin que je puisse faire des ajustements en cours de route pour obtenir des performances optimales. J'ai ajouté un tube en laiton au montant de l'image 3 pour aider à réduire le frottement. J'ai utilisé un clou 10d pour la goupille pour connecter le pendule à la pièce verticale. Sur la photo 5, vous pouvez voir l'aimant de terres rares au bout du pendule. Je n'ai jamais rien trouvé qui disait que la polarité de l'aimant était importante. Cela n'a pas l'air d'avoir d'importance…. ce qui me dérange parce que, intuitivement, je pense que cela devrait. Mais je n'y ai jamais prêté attention et cela semble toujours fonctionner, donc je suppose que non. La dernière photo montre la source d'alimentation 9 volts DC. La capacité de courant de 1 A est excessive… elle n'a pas besoin d'être proche de cela, comme je l'ai découvert plus tard.
Étape 6: Assemblage du pendule
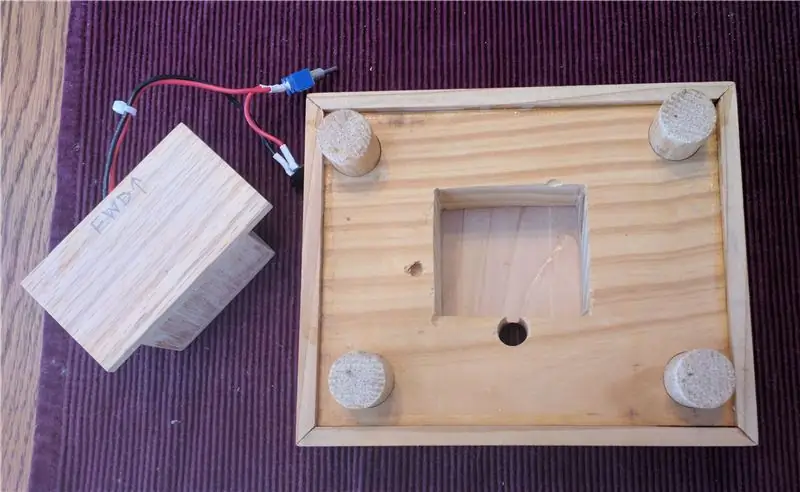
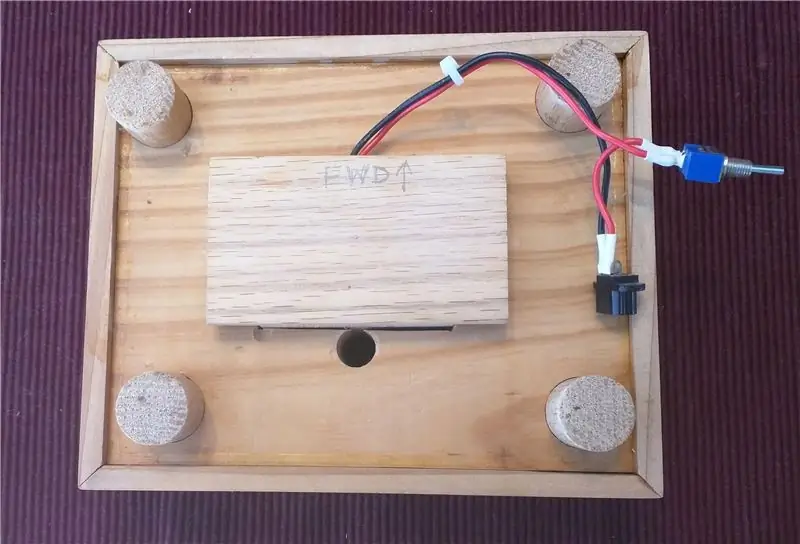
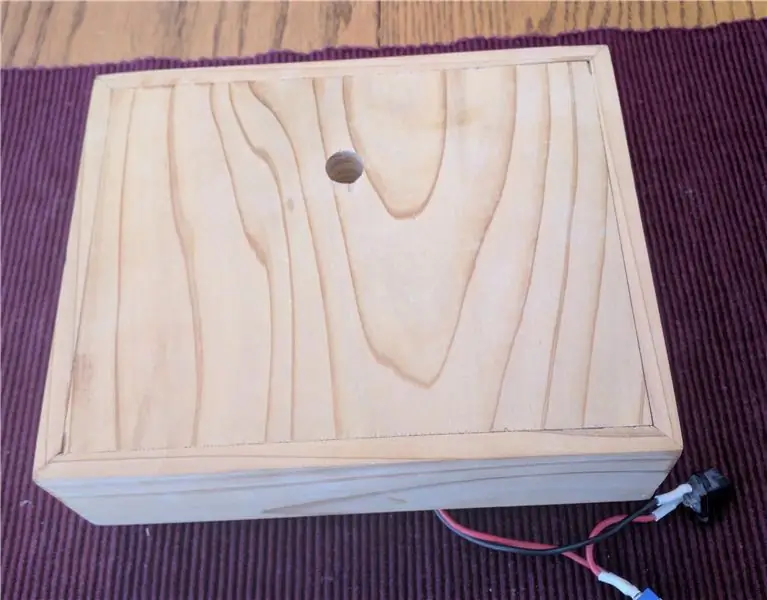
La base est un morceau de pin de deux pouces d'épaisseur. Je voulais qu'il soit lourd pour empêcher l'ensemble de basculer lorsque le pendule se balançait. Même s'il s'agissait d'un prototype, j'ai quand même décidé de l'habiller un peu et de le tailler avec de minces morceaux de cèdre rouge. Je n'ai pas pu m'en empêcher !:)
Le module de bobine se branche sur la partie inférieure de la base (photo 2) et le tout est retourné du bon côté (photo 3). Le montant est inséré dans le haut de la base (photo 4). C'est un ajustement par friction. Insérez le clou dans le tube en laiton du montant (photo 5). Et enfin, appuyez le pendule sur l'ongle (photo finale).
J'ai ajusté le pendule pour qu'il y ait un léger écart entre celui-ci et la base.
Étape 7: Résultats des performances du prototype
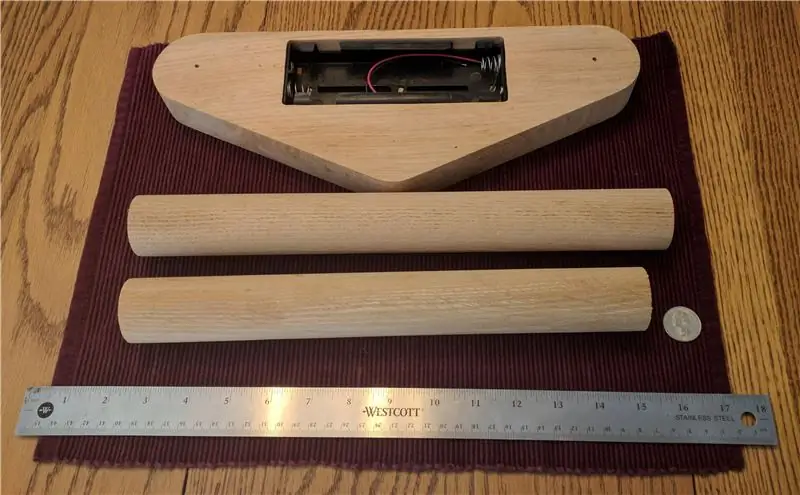

En regardant le graphique que j'ai placé derrière le pendule de travail dans la vidéo, vous pouvez voir que le pendule dépasse la ligne médiane mais ne dépasse pas tout à fait la dernière ligne. Cela place tout l'arc que le pendule oscille entre 72 et 80 degrés… J'estime environ 75 degrés. Il s'agit d'informations précieuses lorsqu'il est temps de concevoir l'échappement de marche pour l'horloge.
J'ai également connecté une sonde de courant à la ligne électrique et surveillé la consommation de courant pendant le fonctionnement. J'ai été extrêmement heureux de découvrir que la consommation de courant moyenne était d'un peu plus de 2 milliampères !!! Ce qui est vraiment cool à ce sujet, c'est que je vais pouvoir alimenter l'horloge sur batterie. Si j'utilise des piles C, j'aurai plus de 5 mois d'autonomie avant de devoir changer les piles. Pas mal!
La raison pour laquelle je suis enthousiasmé par l'utilisation de piles est que je ne veux pas qu'un câble d'alimentation soit relié à l'horloge pour révéler le secret de son fonctionnement. Je vais cacher les piles dans la base de l'horloge. De plus, je pourrai le mettre n'importe où.
Étape 8: À venir…
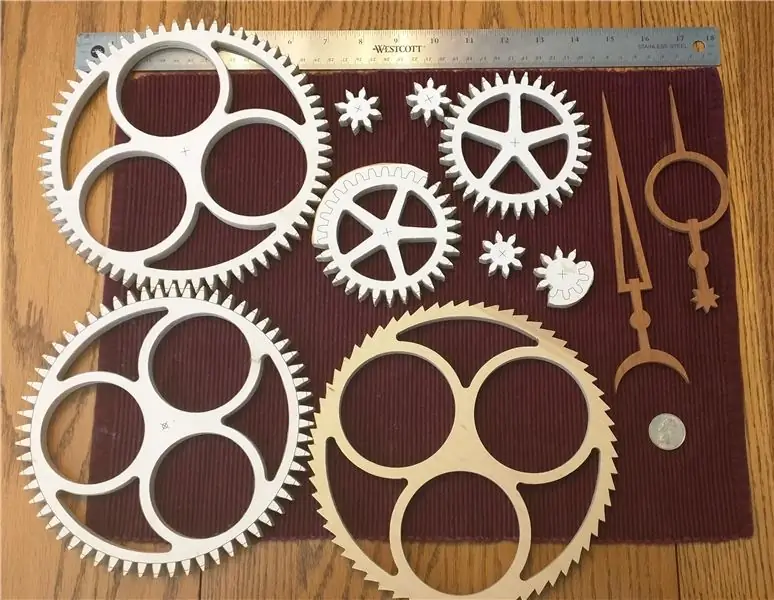
Comme vous pouvez le voir, j'ai été occupé avec les prochaines étapes de la conception de mon horloge. Je me suis brûlé en coupant les dents de l'engrenage. Oh mon Dieu, c'est un processus fastidieux. Si jamais je décide de construire un tas de ces horloges, je pense que j'investirai dans un joli routeur CNC !!!
Ainsi, tout en faisant une pause dans le sciage des dents d'engrenage, j'ai découpé les aiguilles et j'ai commencé à travailler sur le cadre de l'horloge. Jusqu'ici tout va bien!
Alors que je pense au prochain instructable de cette série, je crois que je vais parler du processus que j'ai suivi pour concevoir et construire les engrenages, alors restez sur celui-là.
À plus tard!
Willy
Conseillé:
Péndulo Inteligente De Newton Con Electricidad (Pendule de Newton avec électricité): 17 étapes (avec photos)
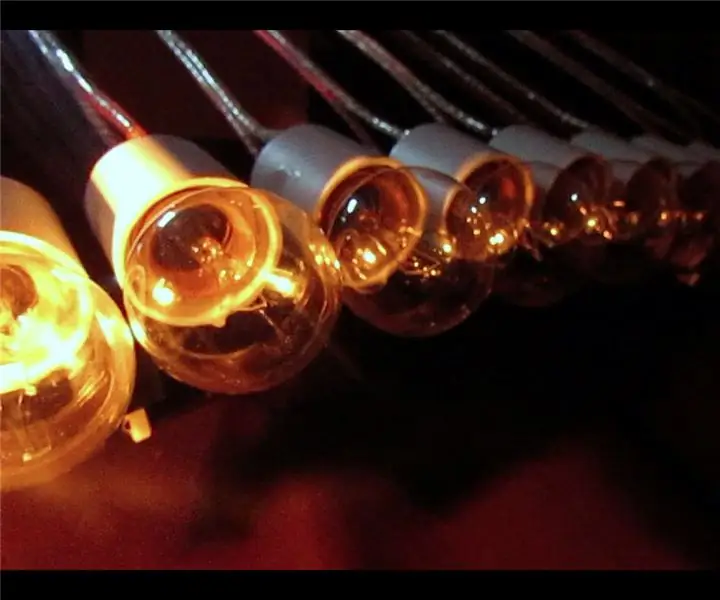
Péndulo Inteligente De Newton Con Electricidad (Pendule de Newton avec électricité): Este proyecto lo hice con un fin educativo, ya que resulta curioso e hipnotizante la manera en que fluye la electricidad por medio de los bombillos. Pienso que es una buena Herramienta para enseñar a las personas el principio del Péndu
Pendule inversé : théorie du contrôle et dynamique : 17 étapes (avec images)
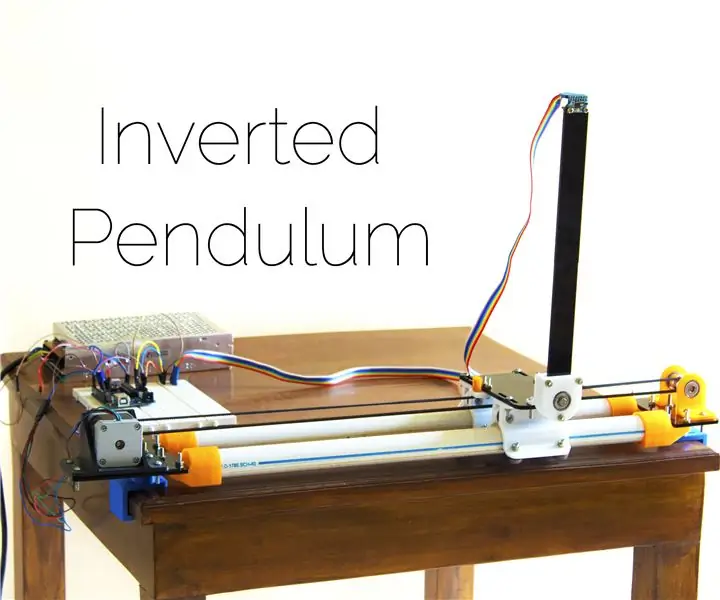
Pendule inversé : théorie du contrôle et dynamique : Le pendule inversé est un problème classique de la dynamique et de la théorie du contrôle qui est généralement élaboré dans les cours de physique ou de mathématiques du secondaire et du premier cycle. Étant moi-même passionné de mathématiques et de sciences, j'ai décidé d'essayer de mettre en œuvre les concepts
Bâton électromagnétique : 4 étapes (avec photos)
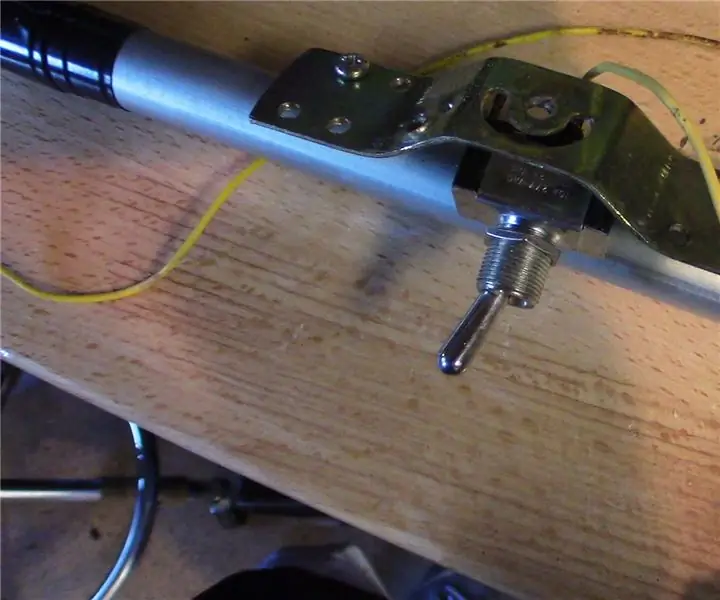
Personnel électromagnétique : Ce projet permet d'atteindre des objets ferromagnétiques autrement inaccessibles. Il pourrait être utilisé pour aider les personnes handicapées mais personnellement, je l'ai construit parce que c'est vraiment cool
Horloge Nixie Laser pendule électromagnétique, avec thermomètre : 5 étapes (avec photos)
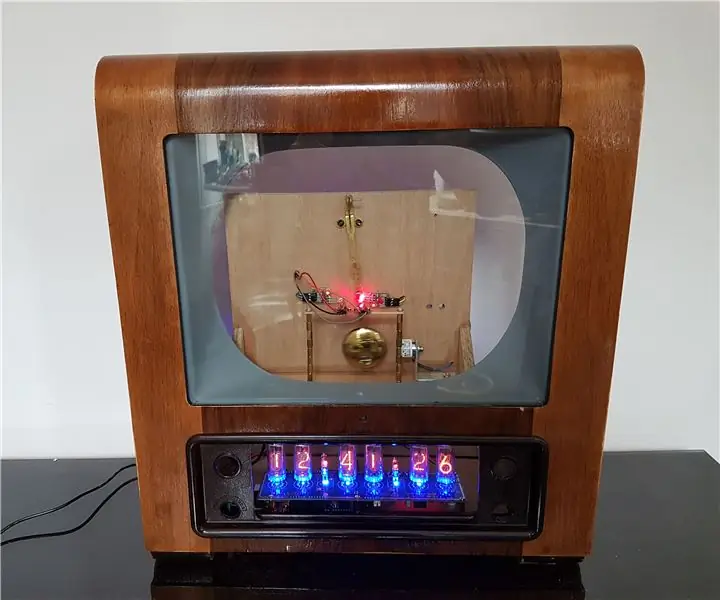
Horloge Nixie laser à pendule électromagnétique, avec thermomètre : j'ai déjà construit quelques horloges Nixie Tube à l'aide d'un Arduino Nixie Shield que j'ai acheté sur ebay ici : https://www.ebay.co.uk/itm/Nixie-Tubes-Clock -IN-14… Ces cartes sont livrées avec un RTC (Real Time Clock) intégré et le rendent très simple
Actionneur électromagnétique : 4 étapes (avec photos)
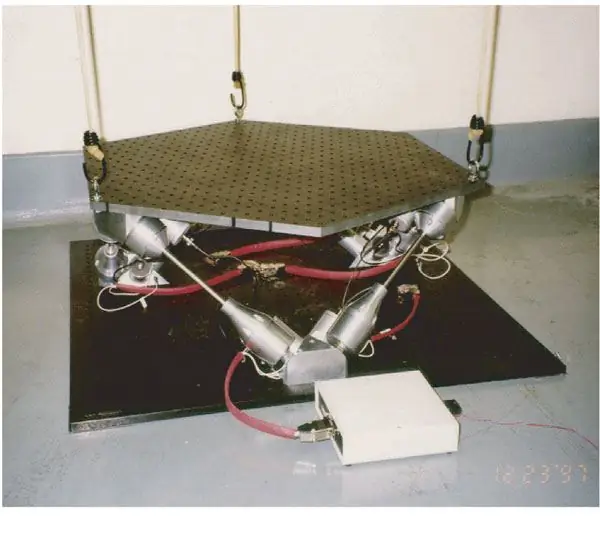
Actionneur électromagnétique : souvent appelé moteur linéaire ou bobine voix/haut-parleur, l'actionneur électromagnétique est polyvalent et relativement facile à concevoir/construire