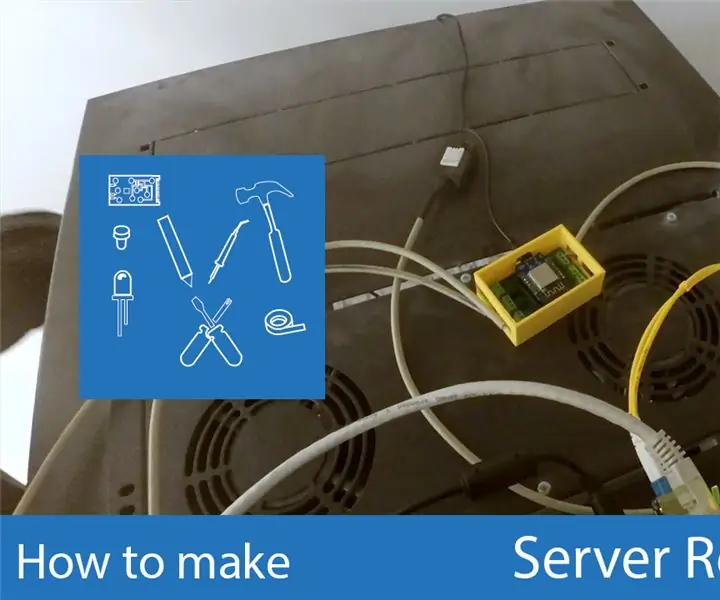
Table des matières:
2025 Auteur: John Day | [email protected]. Dernière modifié: 2025-01-23 14:45
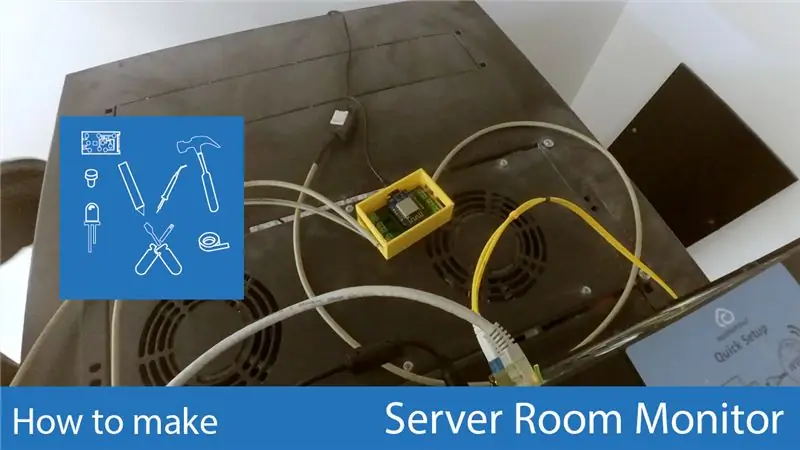
L'un des problèmes d'une salle de serveurs est la température. Avec différents équipements produisant de la chaleur, celle-ci augmente rapidement. Et si la climatisation tombe en panne, elle arrête tout rapidement. Pour prévoir ces situations, nous pouvons acquérir l'un des nombreux systèmes de surveillance environnementale du marché. Étant un système simple, j'ai décidé de créer une solution personnalisée et de construire un système de surveillance de salle de serveurs. Merci d'avance pour le soutien de PCBWay qui a fourni tous les circuits imprimés nécessaires.
Étape 1: Exigences
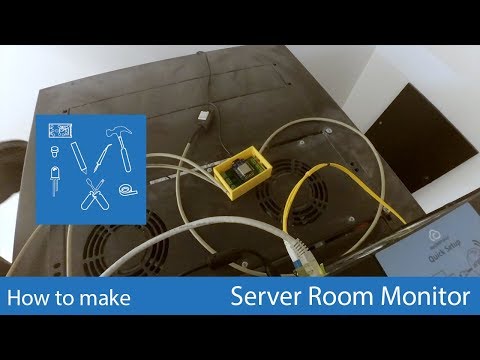
Au départ, j'ai créé un prototype sur une maquette, donc je connaissais les connexions nécessaires. Bien que le prototype ne comporte qu'un seul capteur et que le produit final en possède plusieurs, il n'a fallu que multiplier les connexions.
Ensuite, il a fallu créer le code. La configuration système requise est la suivante.
Conditions
Stations de surveillance
- surveiller la température ambiante et l'humidité de l'air
- avoir plusieurs capteurs
- signaler ces données à un système central
Système central
- recevoir des données de plusieurs stations
- authentifier les stations et leurs données
- afficher un graphique par capteur des dernières 24 heures
- surveiller les données et envoyer un avertissement par e-mail si vous quittez la plage établie comme normale
Étape 2: Matériel
- 1 Wemos D1 Mini
- 3 DHT22
- 9 Connecteur Dupont
- Câble téléphonique
- 9 pull Dupont
- 9 broches d'en-tête
Pour le système central, j'ai développé une application utilisant PHP et MariaDB.
Pour chaque station j'ai développé un système basé sur Wemos D1 Mini, avec plusieurs capteurs DHT22.
Chaque station collecte les données des capteurs connectés toutes les 30 minutes, les encode et les envoie au système central via une connexion sans fil. Le système central décode les données, authentifie la station grâce à une clé prédéfinie et insère les données dans la base de données
Étape 3: Code et PCB
Code
Tout le code est disponible dans mon compte GitHub.
PCB
Après le prototype, j'ai créé le PCB. Pour créer le PCB, j'ai utilisé Autodesk Eagle. Ceci est disponible gratuitement pour les PCB jusqu'à 11 cm de côté.
Pour créer le PCB dans Autodesk Eagle, vous devez créer un projet et dans le projet, créer un schéma avec les composants et leurs connexions.
Après cela est créé, je crée le pcb. Pour cela, appuyez sur le bouton qui se trouve dans la barre d'outils. Autodesk Eagle crée un circuit imprimé avec tous les composants et indique les connexions respectives. Ensuite, il faut définir la taille du PCB, positionner les composants en place et faire les connexions entre eux (voir plus d'informations ici
Enfin, il est nécessaire d'exporter le dessin au format gerber pour le soumettre à la production. Comme il existe plusieurs possibilités, PCBWay fournit un didacticiel avec les étapes (https://www.pcbway.com/helpcenter/technical_support/Generate_Gerber_files_in_Eagle.html) et indique quels fichiers doivent être soumis.
La soumission est faite sur le site Web de PCBWay. Lors de la soumission, le coût est automatiquement mis à disposition. Une option qui devrait être vérifiée est le "sans plomb HASL", pour retirer le plomb des planches. Après la soumission, le processus de production est rapide, prenant entre 1 et 2 jours.
Étape 4: Assemblage
Après avoir reçu les PCB de PCBWay, j'ai soudé les différents composants en place. Les PCB sont préparés pour recevoir les composants, ce qui rend le processus assez simple.
Une fois les circuits imprimés prêts, j'ai créé les différents câbles de connexion des capteurs. Ceux-ci se composent d'un câble téléphonique à 2 paires, avec des connecteurs Dupont pour se connecter au capteur.
Ensuite, j'ai dû créer les cas. Ceux-ci ont été modélisés dans Autodesk Fusion 360 et imprimés en PLA sur un Prusa I3 Hephestos.
Ensuite, je l'ai pré-assemblé. Il a fallu placer le PCB sur le boitier ainsi que les différents capteurs. Il était également nécessaire de protéger les connecteurs avec un manchon thermorétractable.
Sur le site, l'assemblage final a été effectué. J'ai placé un capteur au milieu d'un rack et deux autres au-dessus de chacun. Cela me permet de surveiller la température et l'humidité en différents points de la pièce et à différentes hauteurs.
Enfin, j'ai vérifié s'il y avait une connectivité au système central et quelles données étaient transmises.
Dans une situation idéale, tous les capteurs, quels que soient leur emplacement et leur hauteur, devraient indiquer les mêmes valeurs. Si ceux du haut rapportent des valeurs plus élevées, la pièce se réchauffe.
Conseillé:
Lumière de salle de bain au milieu de la nuit : 5 étapes (avec photos)
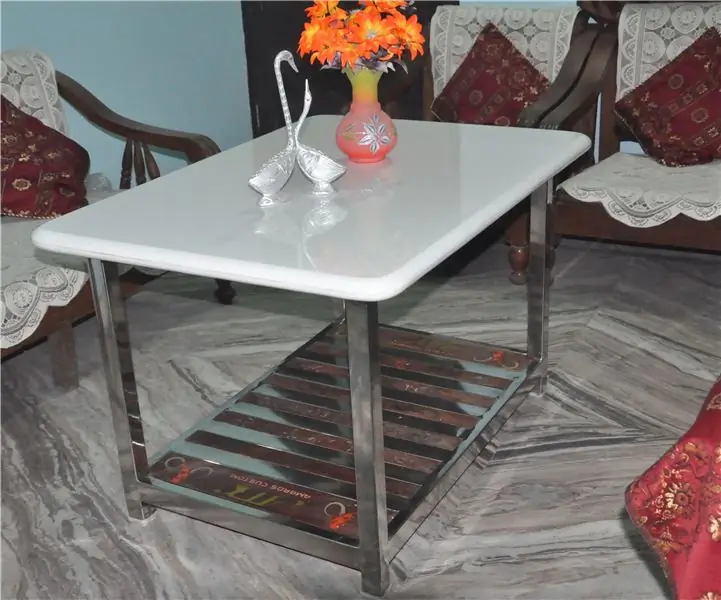
Lumière de salle de bain au milieu de la nuit : Certains d'entre nous ressentent le besoin d'utiliser la salle de bain au milieu de la nuit. Si vous allumez une lumière, vous risquez de perdre votre vision nocturne. La lumière blanche ou bleue fait perdre l'hormone du sommeil, la mélatonine, ce qui rend plus difficile le retour au sommeil. Donc
Balance de salle de bain Arduino avec cellules de charge de 50 kg et amplificateur HX711 : 5 étapes (avec photos)
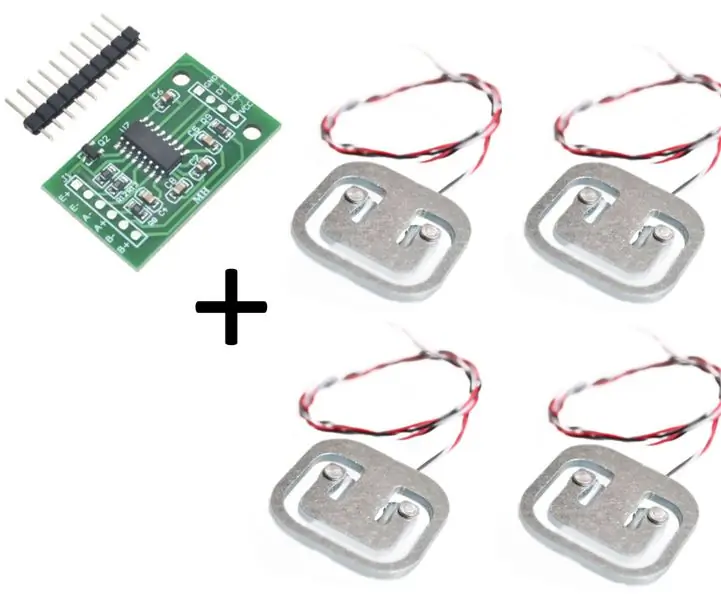
Balance de salle de bain Arduino avec cellules de charge de 50 kg et amplificateur HX711 : ce Instructable décrit comment fabriquer une balance à l'aide de pièces facilement disponibles sur étagère. Matériel nécessaire : Arduino - (cette conception utilise un Arduino Uno standard, d'autres versions ou clones d'Arduino devraient fonctionner aussi) HX711 sur le boa de rupture
Suivi des toilettes de la salle de classe Makey Makey : 5 étapes
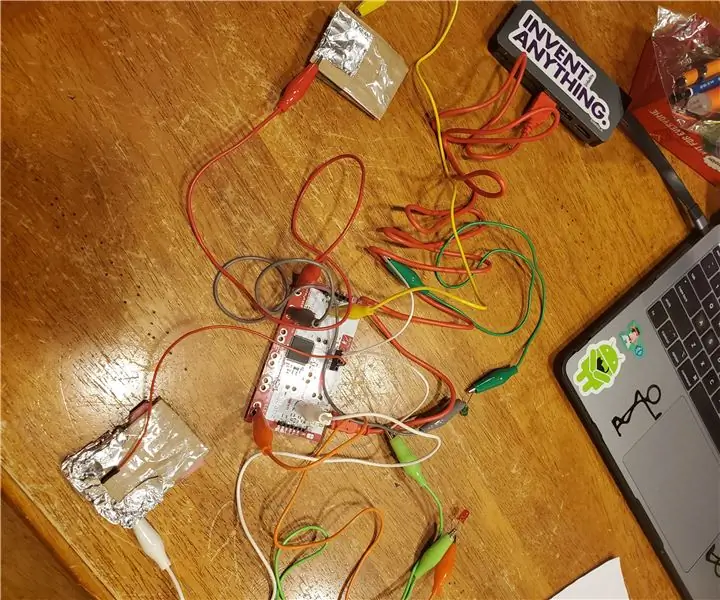
Makey Makey Classroom Restroom Tracker : Avez-vous déjà été occupé dans votre classe et perdu la trace de quel élève (ou si plusieurs) est allé aux toilettes ? J'enseigne l'informatique au lycée et je constate que les étudiants essaient souvent de quitter la salle de classe pour "utiliser les toilettes"
Moniteur de confidentialité piraté à partir d'un ancien moniteur LCD : 7 étapes (avec photos)
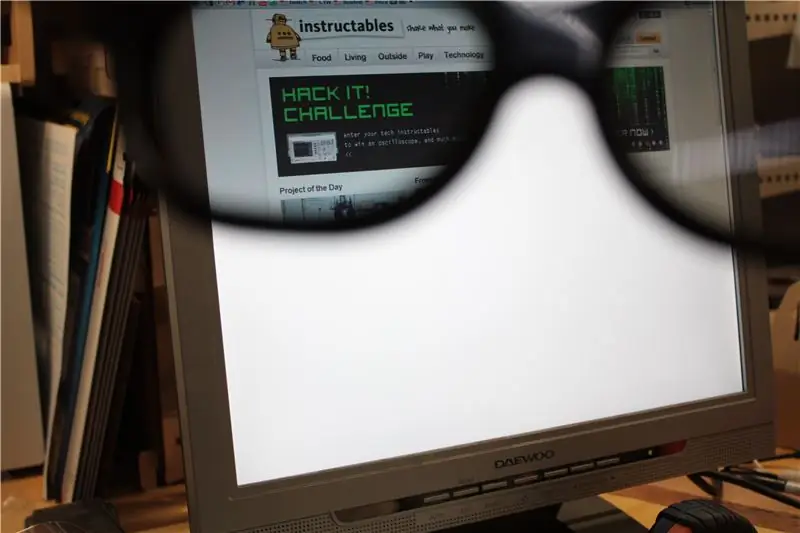
Moniteur de confidentialité piraté à partir d'un ancien moniteur LCD : Enfin, vous pouvez faire quelque chose avec ce vieux moniteur LCD que vous avez dans le garage. Vous pouvez le transformer en un moniteur de confidentialité ! Il a l'air tout blanc pour tout le monde sauf vous, parce que vous portez de la "magie" lunettes! Tout ce que vous devez vraiment avoir, c'est un pa
Conversion du répartiteur de moniteur VGA en commutateur de moniteur contrôlé par ordinateur : 4 étapes
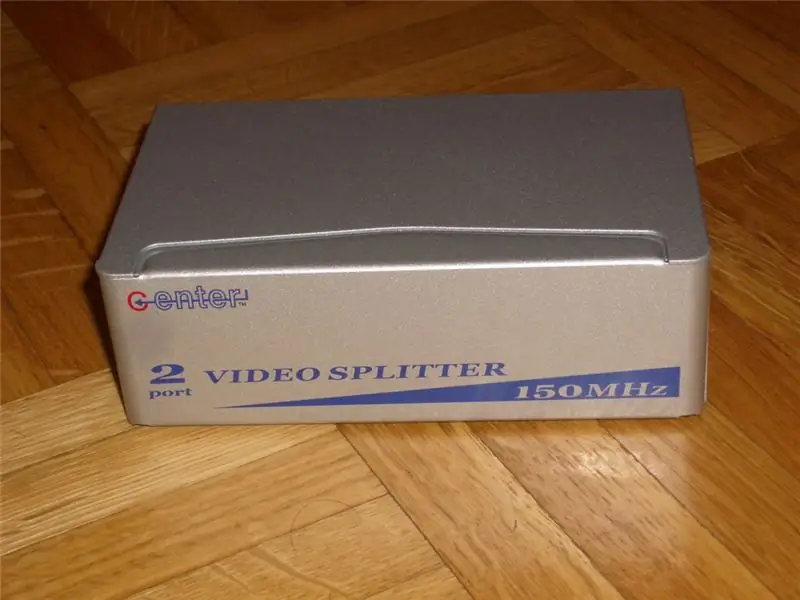
Conversion du séparateur de moniteur VGA en commutateur de moniteur contrôlé par ordinateur : cette instructable explique comment un séparateur de moniteur VGA bon marché (20 EURO) qui est utilisé pour connecter un PC à deux moniteurs peut être converti en un commutateur de moniteur contrôlé par ordinateur. L'appareil final est contrôlé via le port parallèle et permet de tur