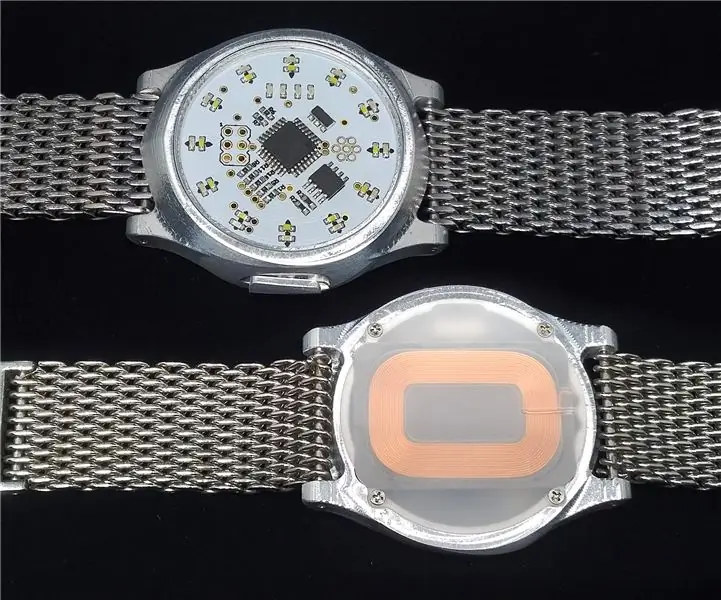
Table des matières:
- Étape 1: Conception électronique
- Étape 2: Assemblage électronique
- Étape 3: Programmation et test de l'électronique
- Étape 4: Configuration de l'usinage
- Étape 5: Usinage du boîtier
- Étape 6: Usinage du commutateur latéral
- Étape 7: Usinage du fond du boîtier
- Étape 8: Assemblage de la montre
- Étape 9: Notes finales
2025 Auteur: John Day | [email protected]. Dernière modifié: 2025-01-23 14:46
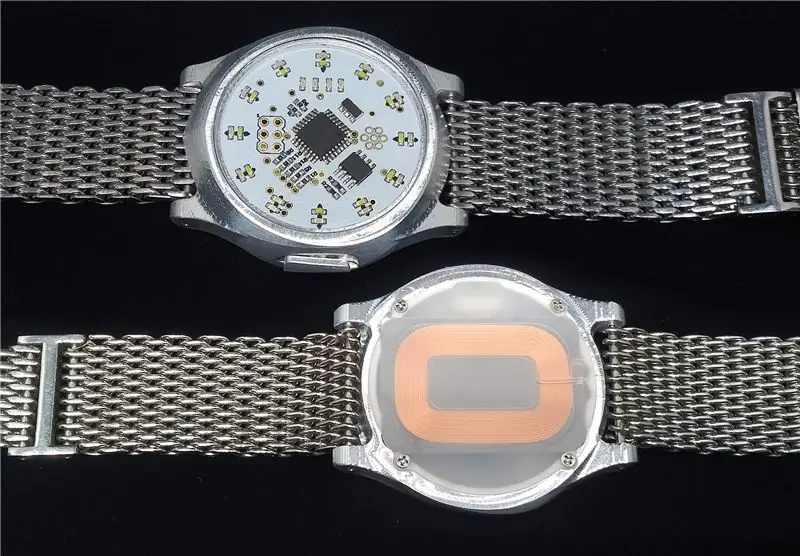
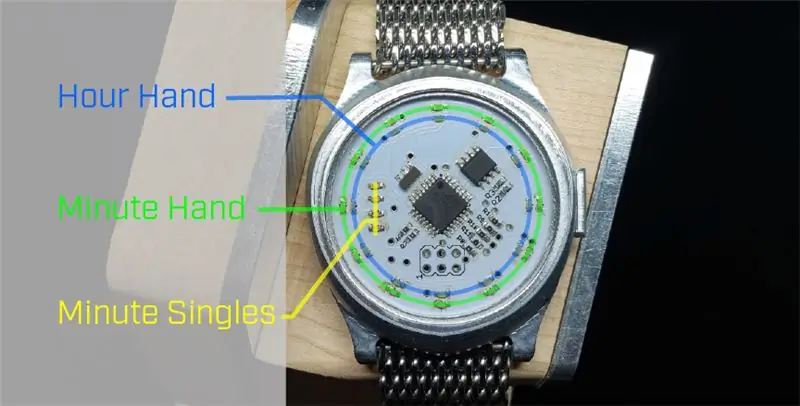
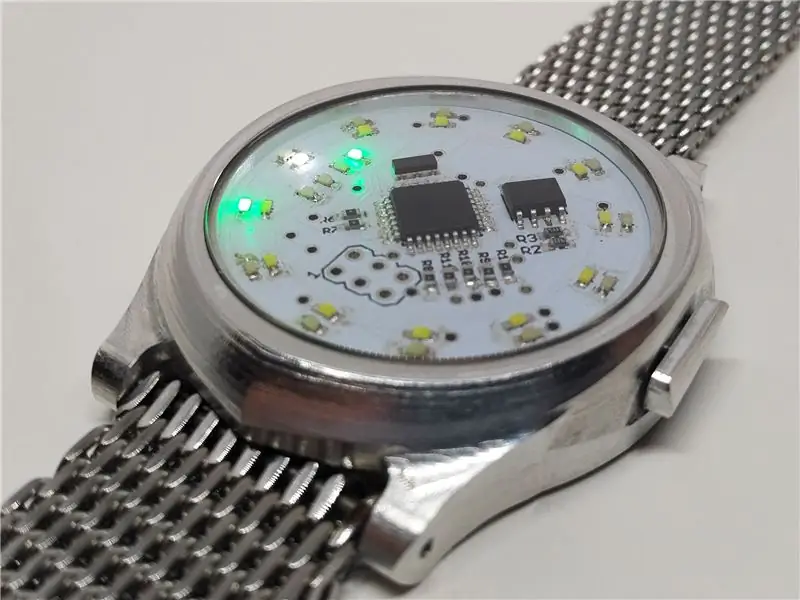
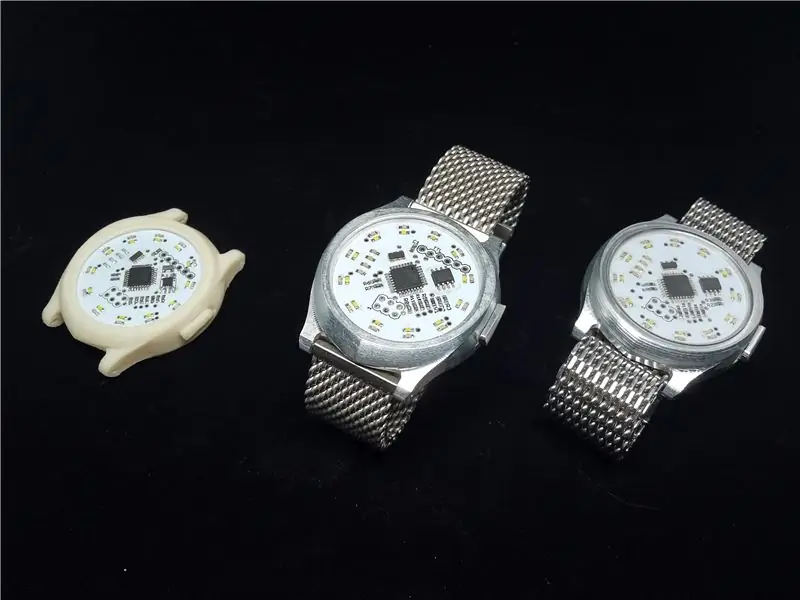
La MechWatch est une montre que j'ai conçue pour avoir les avantages d'Arduino en termes de flexibilité, mais je voulais qu'elle soit aussi professionnelle que possible. À cette fin, cette instructable utilise une électronique de montage en surface assez avancée (pas de connexions exposées à la soudure) et un équipement de fraisage CNC.
Je commencerai par la lecture de l'heure, avec une illustration sur la deuxième photo. Il y a deux anneaux LED, l'un est l'aiguille des heures et l'autre agit comme une aiguille des minutes, pointant de 1 à 12 comme sur une horloge analogique. Étant donné que l'aiguille des minutes ne peut se déplacer que par incréments de 5 minutes, il y a 4 LED distinctes pour indiquer chaque minute. À titre d'exemple, la troisième image montre la montre affichant 9h41.
L'interaction avec la montre se fait par un interrupteur à double sens sur le côté qui glisse vers les cornes (avant/arrière). Pour régler l'heure:
1. appuyez et maintenez le commutateur jusqu'à ce que les lumières s'éteignent. Lorsqu'il est relâché, l'heure clignote et l'interrupteur peut être poussé vers le haut/bas pour changer l'heure
2. Appuyez à nouveau sur l'interrupteur et maintenez-le enfoncé jusqu'à ce que les lumières s'éteignent pour passer au réglage des minutes de la même manière
3. Appuyez et maintenez l'interrupteur jusqu'à ce que les lumières s'éteignent à nouveau pour gagner du temps
4. Si vous attendez trop longtemps pendant que vous réglez l'heure sans appuyer sur un bouton, la montre se mettra simplement en veille sans enregistrer les modifications.
Cette instructable explique comment faire la montre complète et fournit tous les fichiers sources nécessaires.
Étape 1: Conception électronique
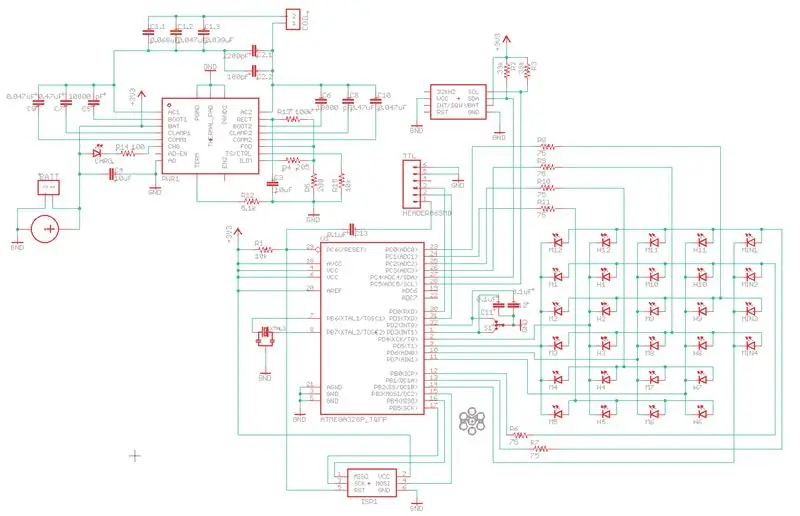
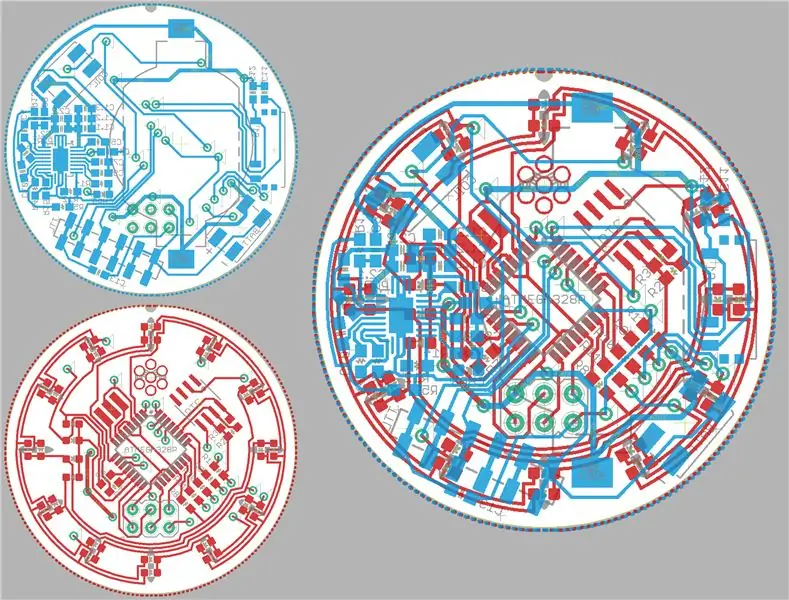
Cette étape décrit les spécificités de l'électronique. La première image est le schéma électrique, montrant comment toutes les pièces sont décrites. La deuxième image montre comment le tableau est disposé, le haut est rouge et le bas est bleu.
Pour toute personne intéressée par la nomenclature exacte de toutes les pièces électroniques ainsi que par l'endroit où je les achète, j'ai joint un fichier Excel avec des liens, plutôt que de faire défiler tout le monde par la longue liste.
Je voulais garder le haut du circuit imprimé relativement clair avec une esthétique de conception cohérente, alors j'ai placé le microcontrôleur au milieu et j'ai disposé le RTC, le cristal et les résistances autour. Les LED entourent l'extérieur et même les traces autour de l'extérieur reflètent l'esthétique du design circulaire.
Pour interfacer les LED avec le microcontrôleur, elles peuvent être disposées en grille, nécessitant 12 broches d'E/S numériques pour les piloter. De plus, je souhaite utiliser une horloge en temps réel (RTC) pour garder l'heure afin de pouvoir mettre le microcontrôleur en veille profonde pour économiser de l'énergie. Le RTC utilise beaucoup moins d'énergie qu'un microcontrôleur, permettant jusqu'à 5 jours entre les charges. Pour communiquer avec le microcontrôleur, le RTC nécessite une communication I2C. J'ai choisi l'ATMEGA328P car il répond à ces exigences et je suis déjà habitué à l'utiliser (il est également utilisé dans de nombreux Arduinos).
Pour interagir avec la montre, l'utilisateur a besoin d'une sorte d'interrupteur, j'ai donc trouvé un interrupteur coulissant bidirectionnel qui revient au centre à l'aide de ressorts. Un interrupteur coulissant externe se fixe à l'interrupteur électrique à l'aide d'une vis de réglage.
J'ai décidé d'utiliser une batterie au lithium pour tout alimenter et une charge inductive Qi pour le recharger. Je voulais éviter d'utiliser tout type de connecteurs pour recharger la montre car ils présentent des ouvertures pour laisser entrer la saleté et l'eau et se corroderont probablement avec le temps, étant si près de la peau. Après avoir lu plus de fiches techniques que quiconque n'en aurait jamais voulu, j'ai opté pour le BQ51050BRHLT. Il a de bons schémas de référence et un chargeur de batterie au lithium intégré (l'espace est précieux).
Comme il n'y avait pas de bonne façon d'arranger l'électronique de charge Qi sur le dessus, j'ai dû le mettre à l'arrière de la carte avec la batterie. L'interrupteur est également situé à l'arrière, mais c'est parce que c'est un meilleur emplacement pour attacher un interrupteur externe.
Étape 2: Assemblage électronique
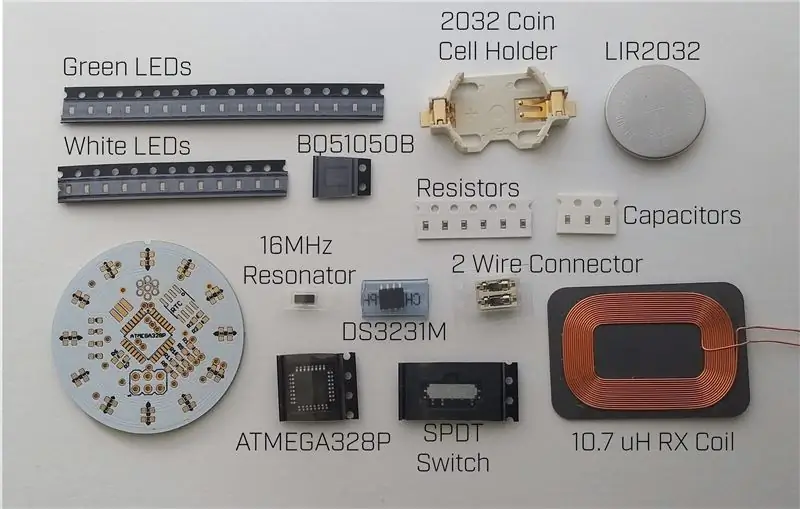
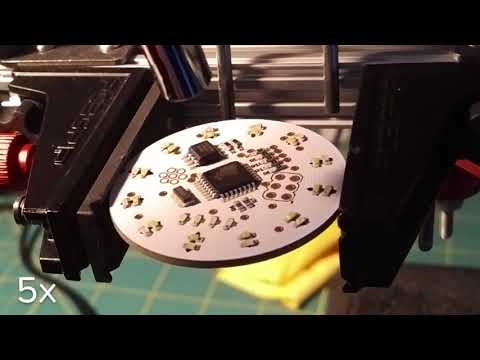
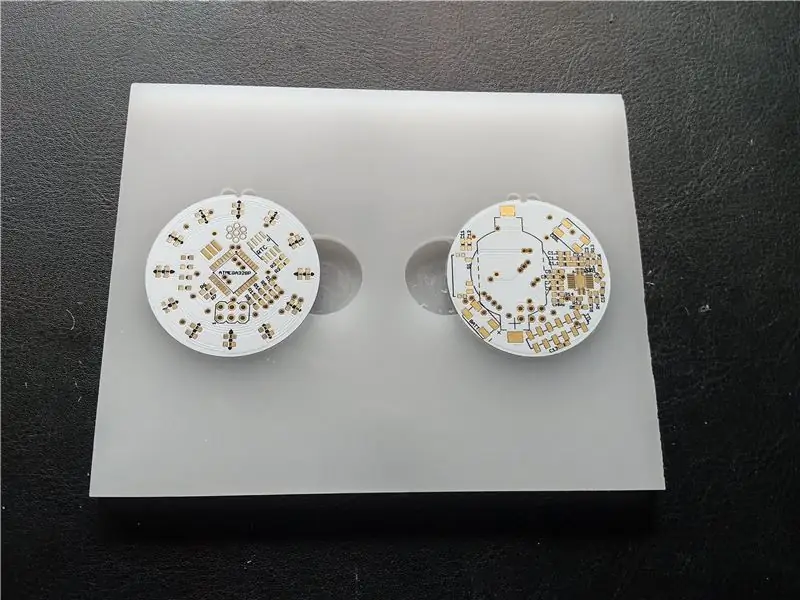
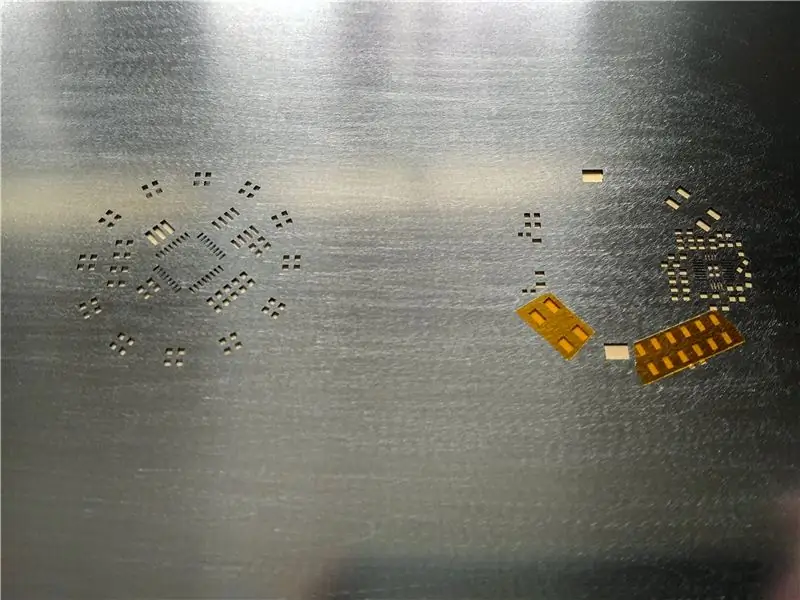
J'ai arrangé presque toutes les pièces électroniques de la première image. J'ai laissé de côté plusieurs condensateurs et résistances, car ils se ressemblent tous et sont faciles à mélanger ou à perdre.
Pour obtenir la soudure sur les pastilles, j'utiliserai un pochoir à souder. J'ai rapidement fabriqué le support de la deuxième image pour garder les circuits imprimés alignés sous le pochoir, mais il existe plusieurs options plus faciles, la plus simple étant le ruban adhésif.
La troisième photo montre le pochoir aligné sur le tableau. La quatrième photo montre l'étalement de la pâte à souder dans les trous du pochoir. Il est important que le pochoir soit soulevé directement après l'application de la soudure. Cette photo révèle également la façon improvisée que je fais parce que je n'ai jamais utilisé de pochoir auparavant. La prochaine fois, je n'achèterais pas le cadre. Il aurait été plus facile de simplement coller une feuille plus petite le long d'un bord sans le cadre, de vivre et d'apprendre.
Maintenant, une tâche fastidieuse et difficile; placez chacune des pièces sur le plateau avec une pince à épiler. La photo 7 montre les pièces placées et la photo 8 les montre soudées.
La vidéo à la place de la 6ème photo montre le processus de soudure. J'utilise une station de soudure à air chaud réglée à 450C pour faire fondre la soudure sans perturber les pièces, alternativement il est possible d'utiliser un four à souder pour faire la même chose. Après avoir soudé le fond, utilisez un multimètre réglé sur le mode de continuité pour vérifier les courts-circuits entre les broches adjacentes du circuit intégré. Lorsqu'un court-circuit est détecté, utilisez un fer à souder pour l'éloigner de la puce et le casser.
Lors de la soudure comme celle-ci, il est important de chauffer lentement la carte pendant quelques minutes avant de la fondre. Sinon, le choc thermique peut détruire les pièces. Je suggérerais de regarder des instructions plus détaillées si vous n'êtes pas familier avec cette méthode.
Ensuite, il est nécessaire de connecter la bobine au connecteur 2 fils et de la maintenir au-dessus de la base de charge. Si tout s'est bien passé, le voyant de charge vert devrait s'allumer pendant environ une seconde, puis s'éteindre. Si une batterie est connectée, le voyant de charge vert doit rester allumé jusqu'à la fin de la charge.
Une fois que la charge fonctionne comme prévu, c'est le même processus pour souder la face supérieure de la carte. Une note pour les LED dans l'image 9, il y a un petit marquage sur le bas des LED pour montrer l'orientation. Le côté vers lequel la petite ligne sort est l'extrémité étroite du triangle dans le schéma des LED. Il est important de vérifier cela pour chaque LED à montage en surface que vous utilisez, car les marquages peuvent varier d'un fabricant à l'autre.
Étape 3: Programmation et test de l'électronique
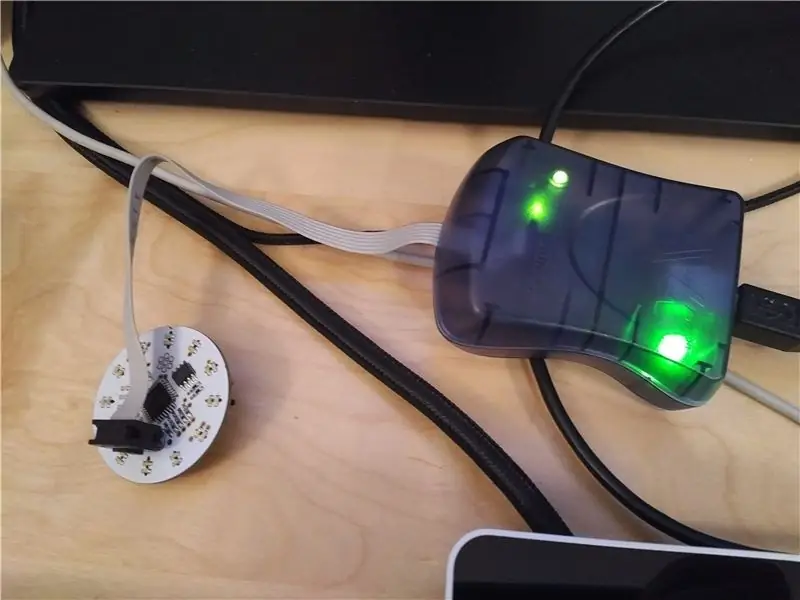
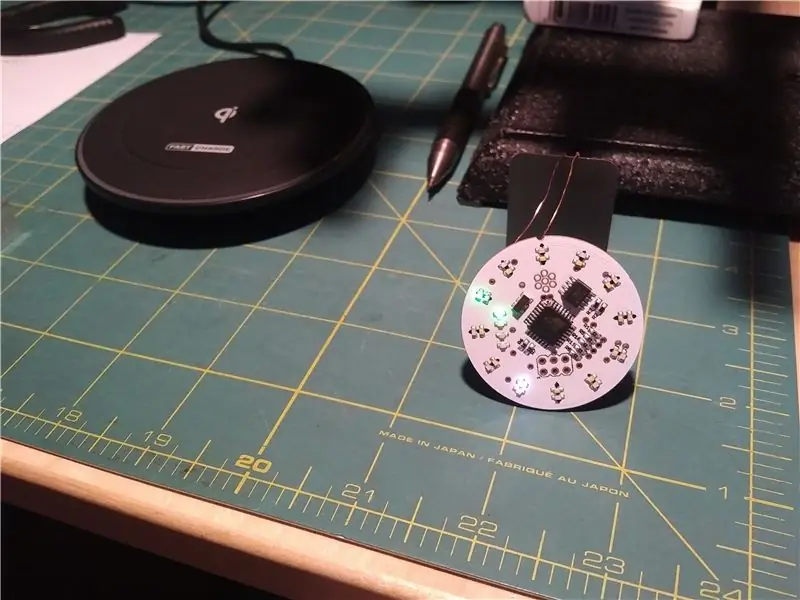
Utilisez un AVRISP mkII pour programmer le microcontrôleur (appuyez et maintenez la touche Maj enfoncée tout en cliquant sur télécharger dans l'IDE Arduino). Il est également possible de l'utiliser pour simplement graver le bootloader comme d'habitude et d'utiliser la connexion série à l'arrière de la montre avec un câble FTDI. Mais en contournant le bootloader et en programmant directement avec l'AVR ISP mkII, le code démarre plus rapidement à la mise sous tension.
J'ai également joint le code à cette étape. Si quelqu'un souhaite regarder plus en profondeur, j'ai commenté le code pour expliquer ce que fait chaque partie. La structure générale du code est une machine à états. Chaque état a un morceau de code qu'il exécute ainsi que des conditions pour passer à un état différent.
Une grande partie du code contrôlant les broches d'E/S contrôle directement les registres, c'est un peu plus difficile à lire mais il peut être jusqu'à 10 fois plus rapide en exécution que digital. Write ou Read.
Étape 4: Configuration de l'usinage
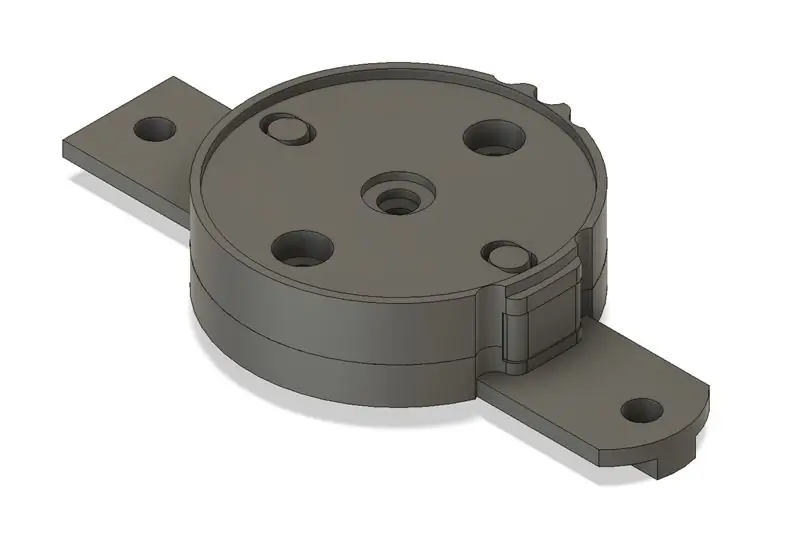
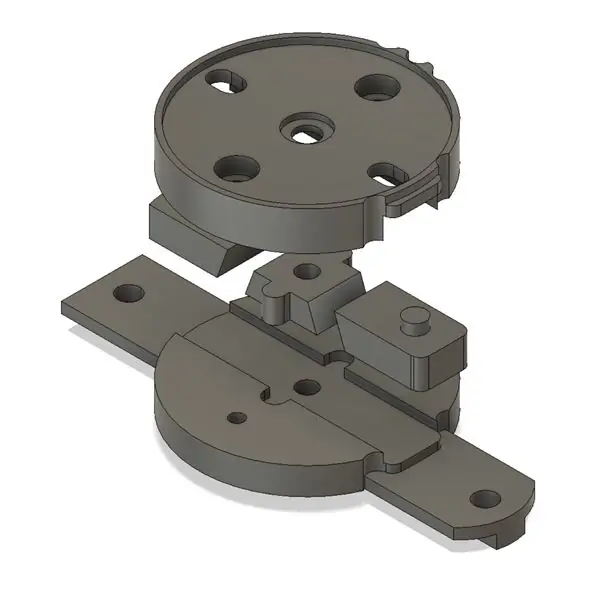
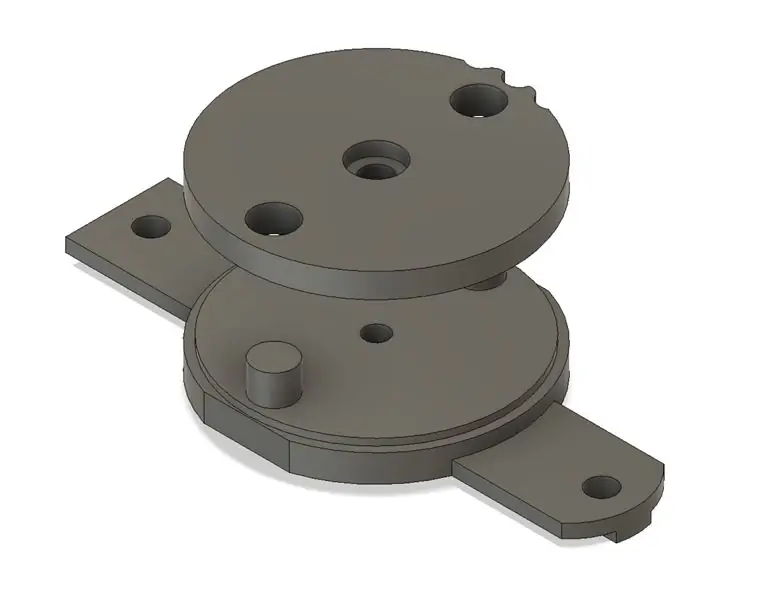
La configuration d'usinage du boîtier de la montre est assez complexe et nécessite une bonne préparation.
Le moulin que j'utilise est un Othermill v2 (maintenant appelé Bantam Tools) avec un kit de pince à orteils. Les pinces me permettent de tenir la pièce sur les côtés, que j'utilise pour la première configuration.
L'usinage de la montre se fait en trois configurations. La première configuration a juste le matériau de départ fixé au lit CNC et le moulin découpe la forme intérieure de la montre et enlève un peu de la surface. La configuration du logiciel d'usinage est visible sur la 6ème image.
La deuxième configuration nécessite un dispositif personnalisé pour maintenir le boîtier de la montre de l'intérieur, il est donc possible de couper toute la forme extérieure supérieure de la montre. Le luminaire personnalisé peut être vu dans la première image avec une vue éclatée dans la deuxième image. La petite pièce centrale a un trou taraudé. Ainsi, lorsqu'une vis est serrée, elle soulève la pièce et force les deux pièces latérales dans le boîtier de la montre, le maintenant en place. Le logiciel d'usinage pour la deuxième configuration est visible sur l'image 7.
La troisième configuration nécessite un autre appareil personnalisé pour tenir la montre; celui-ci est légèrement plus simple. Le luminaire se compose d'une base et d'une pièce qui va à l'intérieur de la montre. La pièce à l'intérieur de la montre s'inscrit avec deux poteaux sur la base et des vis en place pour maintenir le boîtier de la montre à l'envers.
J'ai usiné les pièces du luminaire à partir de gros morceaux d'aluminium et les ai laissés reliés par des languettes. Une fois les deux côtés usinés, j'ai coupé les onglets avec une scie à chantourner et les poncer en douceur.
J'ai inclus les fichiers CAO fusion360 que j'ai utilisés pour fabriquer toutes les pièces (y compris le boîtier de la montre et le commutateur latéral), mais utilisez votre propre jugement si vous essayez de fabriquer les pièces. Je ne suis pas responsable si quelque chose ne va pas et se brise.
Un conseil pour rendre les montages plus précis: usinez d'abord toute pièce qui s'interface avec la machine, puis placez-la à l'emplacement final, puis usinez-la aux dimensions finales. Cela garantit que de nombreuses petites erreurs ne s'aggravent pas et ne maintiennent le boîtier de la montre au mauvais endroit. Cette connaissance vous est apportée par un tas de ferraille d'aluminium.
Étape 5: Usinage du boîtier
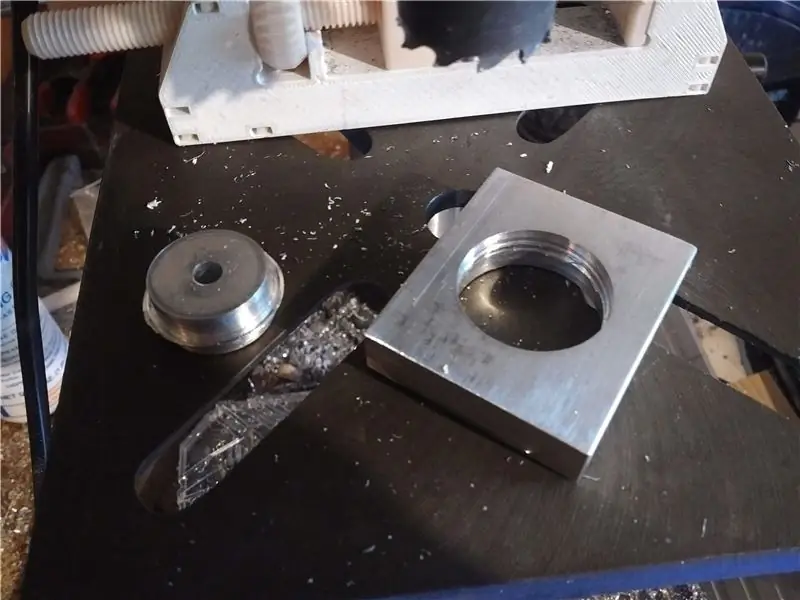

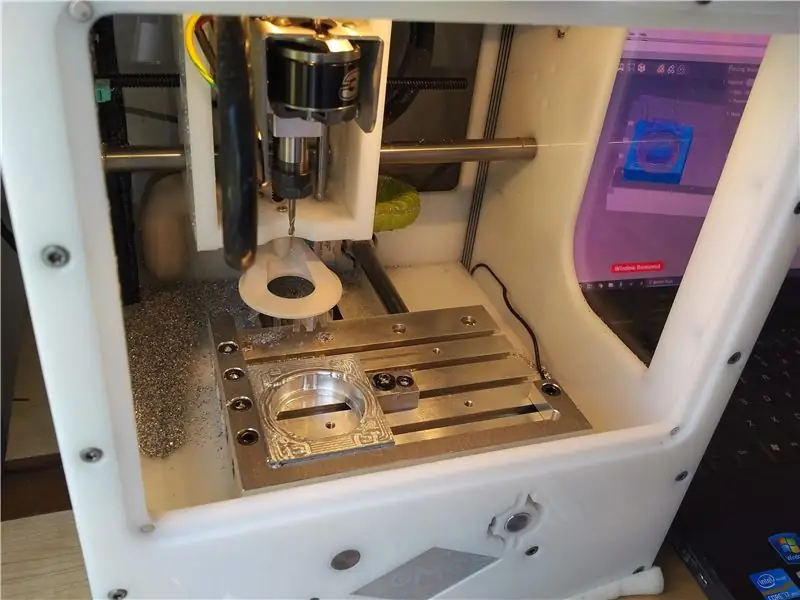
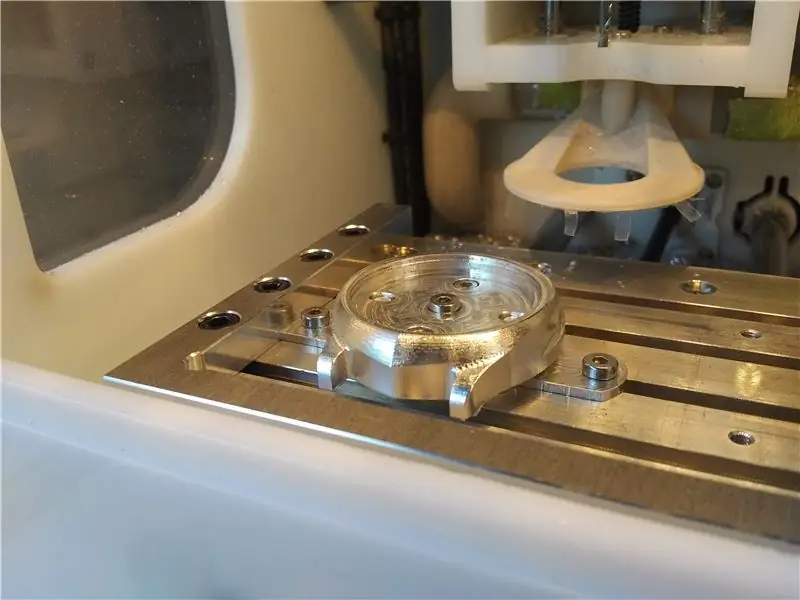
Le flan d'aluminium de départ est visible sur la première photo. J'utilise une scie cloche de 1-1/4 pour retirer le centre, cela permet d'économiser un peu de temps d'usinage.
Comme mentionné à l'étape précédente, il existe 3 configurations pour usiner le boîtier. La première configuration après usinage est visible sur l'image 2. J'utilise d'abord une fraise en bout de 1 1/8" (à plat sur le fond) pour enlever la majeure partie de la matière. Je passe ensuite à une fraise en bout de 1/32" pour couper les 4 vis des trous. Pour couper les filetages dans les trous de vis, j'utilise ensuite une fraise à fileter M1.6 (de Harvey tools). Les paramètres spécifiques que j'utilise sont contenus dans le fichier CAO Fusion360.
L'image 3 montre la deuxième configuration avec l'usinage terminé et la 4ème image montre la troisième configuration avant l'usinage.
La deuxième configuration est usinée à l'aide d'une fraise en bout de 1/8" pour éliminer rapidement la majeure partie du matériau, puis j'utilise un broyeur à boulets de 1/8" (extrémité ronde) pour couper les surfaces courbes. Les opérations sont également les mêmes pour la troisième configuration.
La deuxième configuration nécessite l'utilisation d'un autre outil spécialisé, une scie à refendre 3/4 avec un arbre modifié afin qu'il puisse s'adapter étroitement au support de boîtier de la montre. La scie à refendre tourne à 16 500 tr/min et se déplace à 30 mm/min. Cette vitesse pousse ce dont l'Othermill est capable, il pourrait donc être nécessaire de le ralentir encore plus. Cette étape est montrée dans la vidéo ci-dessus.
Si vous cherchez à en savoir plus sur les spécificités de l'usinage CNC, je vous indiquerai NYC CNC sur YouTube, ils font un meilleur travail que je ne le pourrais jamais ici.
Juste pour référence pour ceux qui savent ce que cela signifie, les réglages utilisés sur l'autre fraise v2 pour la fraise en bout 1/8 sont de 16400 tr/min (163,5 m/min), 300 mm/min, 1 mm de profondeur de coupe et 1,3 mm de largeur de couper.
Parce que l'autre moulin n'a pas assez de hauteur z pour tenir la montre sur le côté, je dois percer manuellement les trous pour le bracelet de montre et le trou pour l'interrupteur latéral. Pour aider à les localiser sur les côtés de forme irrégulière de la montre, j'ai imprimé en 3D quelques guides, visibles sur les images 5-7. Pour améliorer la précision du perçage, il est important d'enfoncer le foret le plus loin possible dans le mandrin; cela rend plus difficile pour le bit d'errer.
Le trou de l'interrupteur latéral est une forme non circulaire, il doit donc être affiné après avoir commencé avec la perceuse, ce qui est fait à l'aide de limes suisses. À l'aide d'étriers, je mesure le trou actuel et le lime à la bonne dimension. Le trou doit être à 4,6 mm de la surface supérieure, à 3,8 mm de la surface inférieure et à 25,8 mm du point le plus éloigné de chaque patte. Je suggère de regarder Clickspring sur YouTube pour vous inspirer tout en remplissant le trou.
Étape 6: Usinage du commutateur latéral
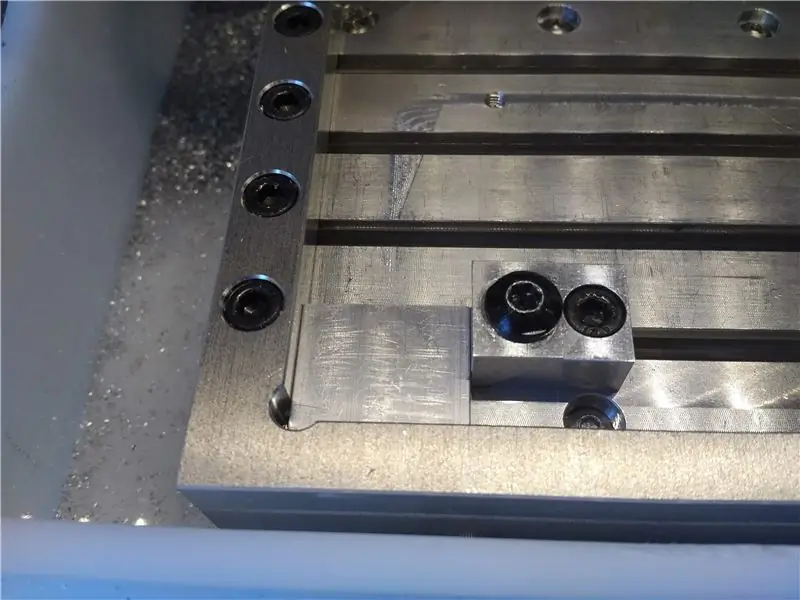
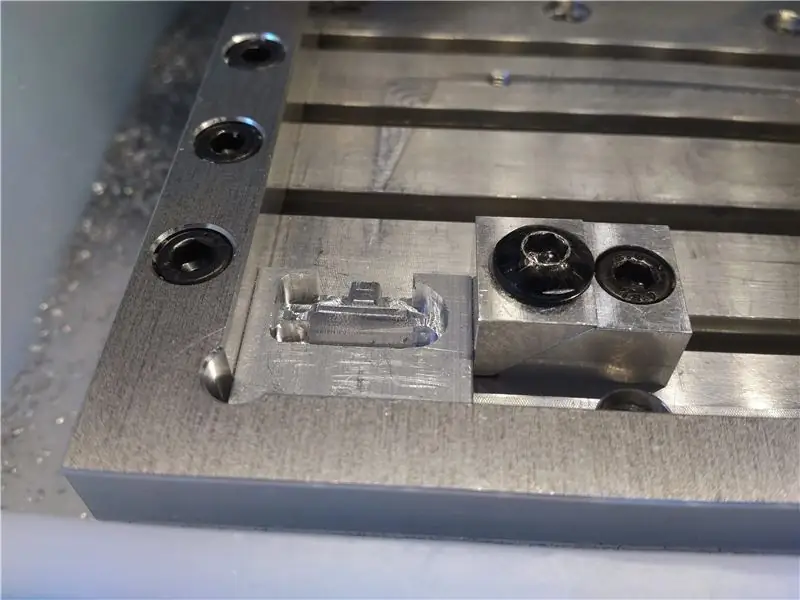
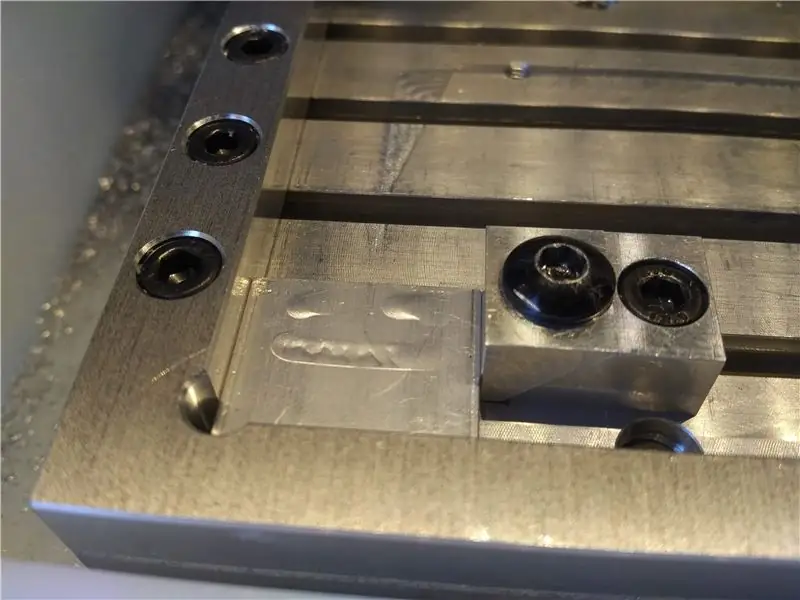
Les fichiers utilisés dans cette étape ont été inclus dans le fichier zip de retour dans la configuration d'usinage.
L'interrupteur latéral est usiné de manière très similaire au boîtier MechWatch. Il est fraisé avec une fraise en bout de 1/8" en utilisant les mêmes paramètres que le boîtier. Ensuite, utilisez un broyeur à boulets de 1/8" sur les surfaces courbes, les mêmes paramètres que précédemment.
La deuxième configuration est visible sur les images 3-4 avant et après l'usinage. Fraise en bout 1/8", broyeur à boulets 1/8", fraise en bout 1/32" puis fraise à fileter M1.6. (il y a un trou fileté pour le maintenir à l'interrupteur sur la carte).
J'usine le commutateur à partir d'un plus gros morceau d'aluminium pour deux raisons. La première raison est que je peux serrer les côtés et ne pas fraiser accidentellement la pièce qui la tient. La seconde est ainsi quand je la place dans la fente pour la troisième opération elle peut encore être serrée (voir photo 5).
Étape 7: Usinage du fond du boîtier
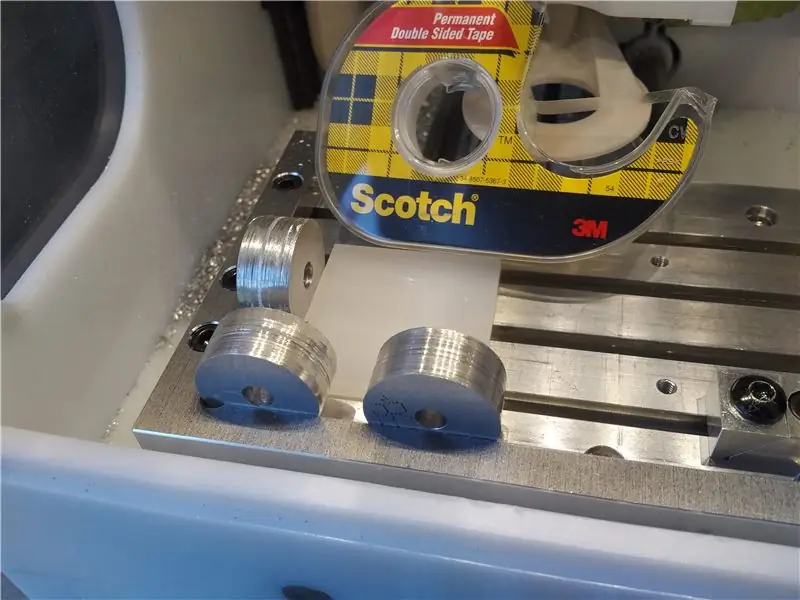
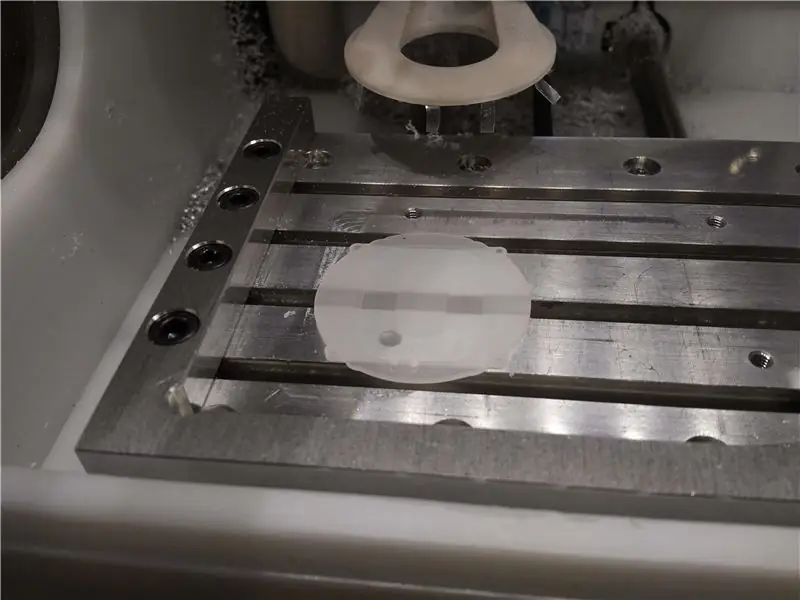
Le fond de la montre est en acrylique, il doit être non métallique en raison de la charge inductive. J'utilise des chutes d'aluminium pour l'espacer du bord (chacune de 12,7 mm d'épaisseur) et du ruban adhésif double face pour le maintenir en place.
Parce que le plastique est beaucoup plus facile à usiner que l'aluminium, il est possible d'être plus agressif avec les réglages CNC. En commençant par une fraise en bout de 1/8", les réglages sont de 16 500 tr/min, une vitesse de coupe de 600 mm/min, une profondeur de coupe de 1,5 mm et une largeur de coupe de 1 mm. Pour couper les détails fins, utilisez une fraise en bout de 1/32" avec le mêmes réglages mais 0,25 mm de profondeur de coupe et 0,3 mm de largeur de coupe.
Après avoir tourné un cure-dent d'une bûche (je devrais utiliser un stock plus fin, mais c'est ce que j'ai), j'ai terminé le dos de la montre. Il a la forme d'un électro-aimant découpé pour garder la montre mince.
Pour le retirer du lit, j'ai mis une clé Allen dans la fente en T et j'ai doucement fait levier, en passant au point suivant lorsqu'il commence à se desserrer.
La dernière étape consiste à prendre un foret et à fraiser doucement les trous sur la face inférieure. Je fais cela en tournant le foret à la main. Je trouve qu'il est plus facile de rester centré et sous contrôle.
Encore une fois, les fichiers utilisés dans cette étape ont été inclus dans le fichier zip de retour dans la configuration d'usinage.
Étape 8: Assemblage de la montre
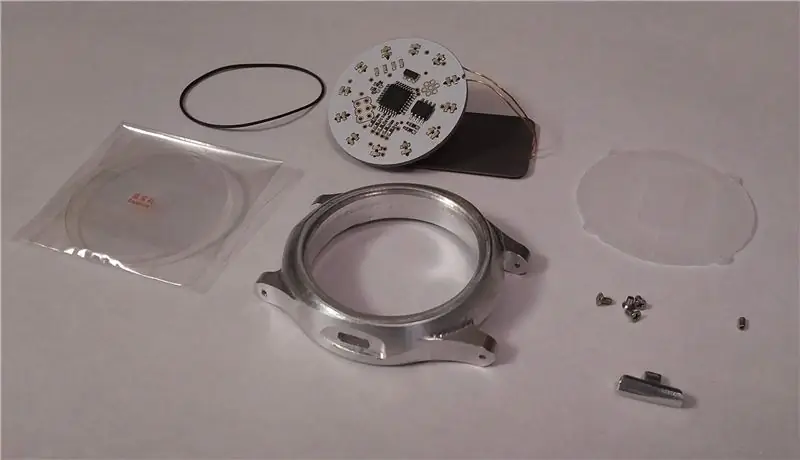
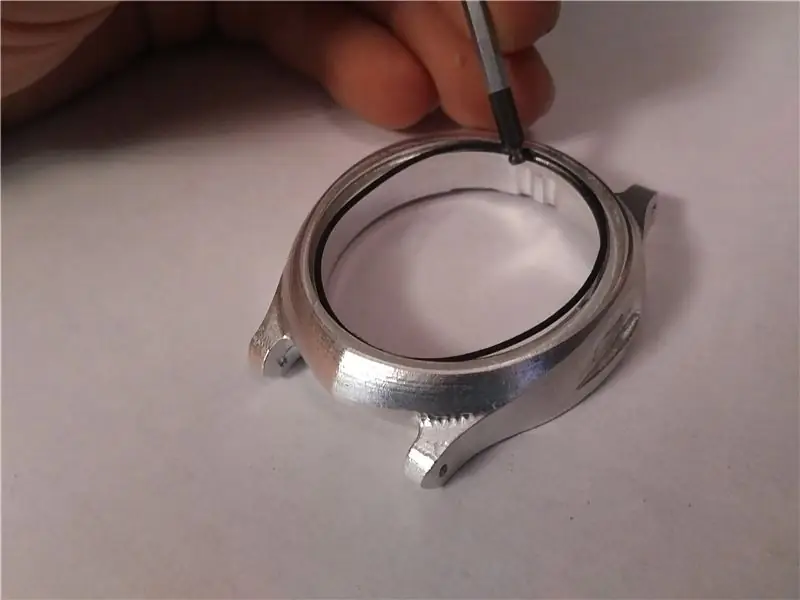
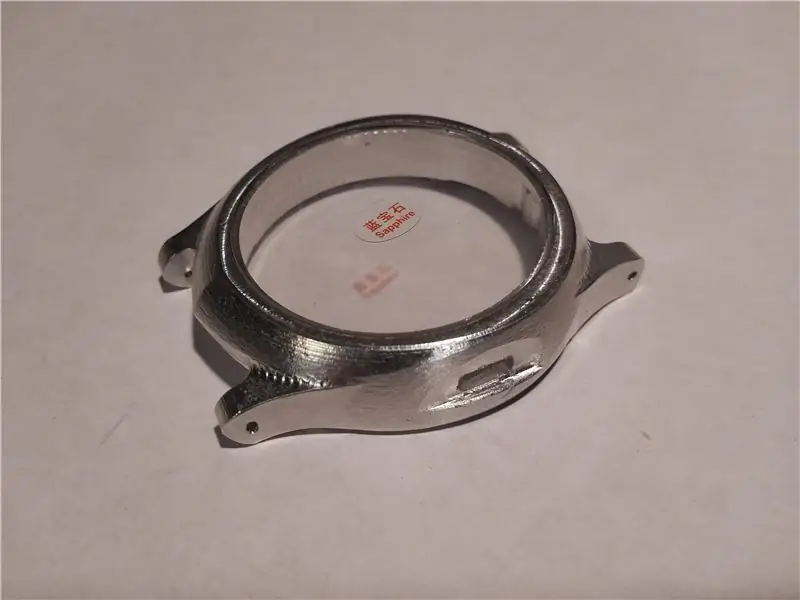
C'est l'étape la plus gratifiante, prendre toutes les pièces et les assembler dans la montre finale. Toutes les pièces disposées (moins le bracelet de montre de 24 mm de large et les barres à ressort à dégagement rapide de 24 mm de long et de 1,5 mm de diamètre) sont visibles sur l'image 1.
La première partie est délicate car les joints toriques de 40 mm de diamètre que j'ai commandés sont en fait plus proches de 37 mm, ils doivent donc être étirés et installés rapidement. Utilisez l'extrémité d'une clé Allen sphérique pour la mettre en place en la faisant rouler le long de la rainure comme le montre l'image 2.
Lorsque le joint torique est bien en place, appuyez fermement sur le cristal (40 mm de diamètre et 1,5 mm d'épaisseur) dans le boîtier de la montre. Le joint torique doit le maintenir en place tout en étant presque invisible.
Il est maintenant temps d'installer l'électronique. Tout d'abord, essuyez l'intérieur du cristal avec un chiffon non pelucheux et placez l'électronique dans le boîtier, en faisant attention à la clé pour garder l'orientation droite. Le PCB doit être bien en place dans le boîtier, mais s'il est lâche, il peut être fixé avec une petite goutte de super colle sur la clé pour le maintenir en place.
Une fois que l'électronique est insérée, l'interrupteur latéral passe à travers le trou et sur l'interrupteur monté sur le PCB. Une vis de réglage M1.6 maintient les deux pièces ensemble comme le montre la photo 4.
Ensuite, les câbles les plus longs de la bobine doivent être repliés et rangés de manière à ne pas frotter les contacts électriques exposés.
L'avant-dernière étape consiste à fermer le tout et à fixer le boîtier en plastique à l'aide des 4 vis M1.6. Il est important de faire attention à ce que la forme à l'arrière s'aligne avec la forme de la bobine. Il peut être nécessaire de modifier le placement du fil pour qu'il s'adapte mieux.
La dernière étape consiste à attacher le bracelet de la montre à l'aide des barres à ressort à dégagement rapide (images 8-9). Selon la bande choisie, il peut être nécessaire de modifier la bande pour fonctionner avec les barrettes à ressort. Pour la bande de maille de requin illustrée, j'utilise des pinces coupantes pour créer un petit trou pour accueillir le mécanisme de dégagement rapide.
Étape 9: Notes finales
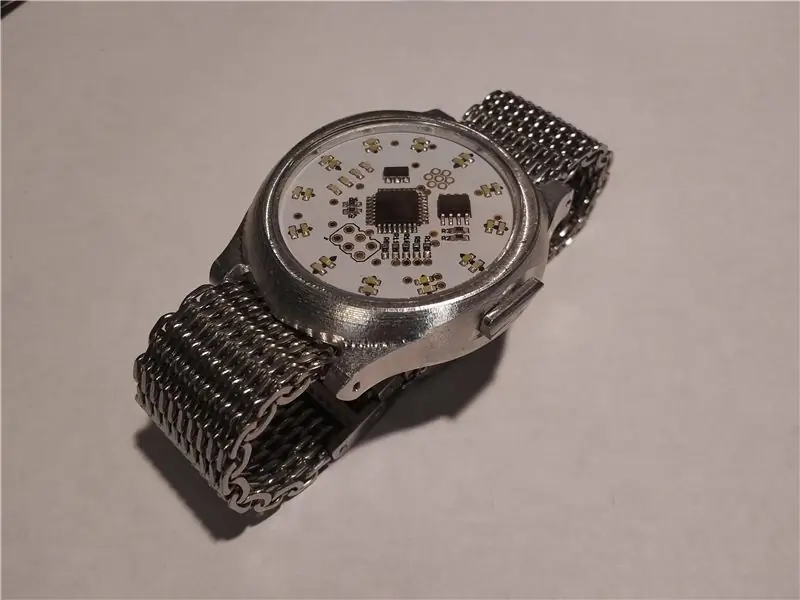
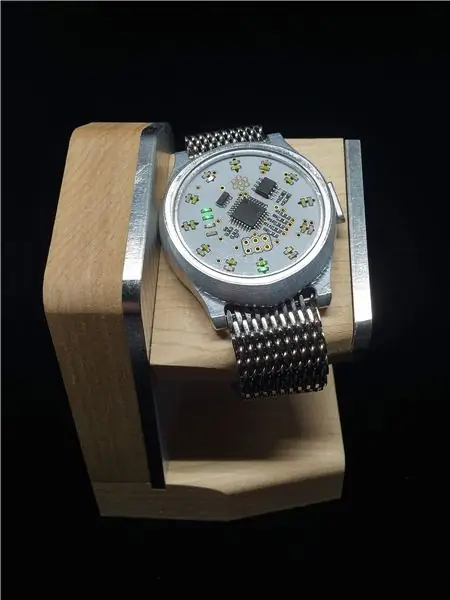
La montre est maintenant terminée !
Juste quelques remarques: l'interrupteur latéral peut parfois devenir un peu collant, pour résoudre ce problème, il peut être nécessaire d'agrandir le trou ou d'ajuster l'emplacement de l'interrupteur en desserrant la vis de réglage, en maintenant l'interrupteur près du corps et en resserrant le vis.
Pour charger la montre, j'ai fabriqué un support de charge personnalisé basé sur le chargeur Adafruit Qi (https://www.adafruit.com/product/2162) vu sur la deuxième photo, mais c'est un sujet pour une autre fois.
Quel que soit le chargeur choisi, il est important de noter qu'aucun métal ne peut se trouver entre la bobine et le chargeur. Parce que le groupe que j'ai choisi est en métal, il faut qu'il fasse le tour du chargeur
Merci d'avoir lu jusqu'au bout, j'espère que vous avez appris quelque chose. Je suis heureux de partager le MechWatch après des mois de fabrication.
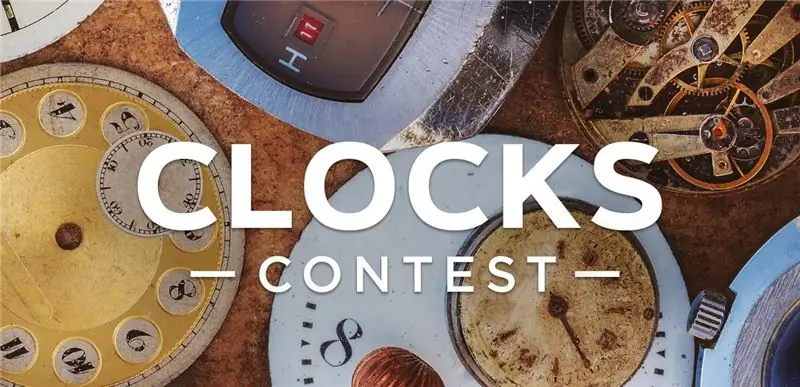
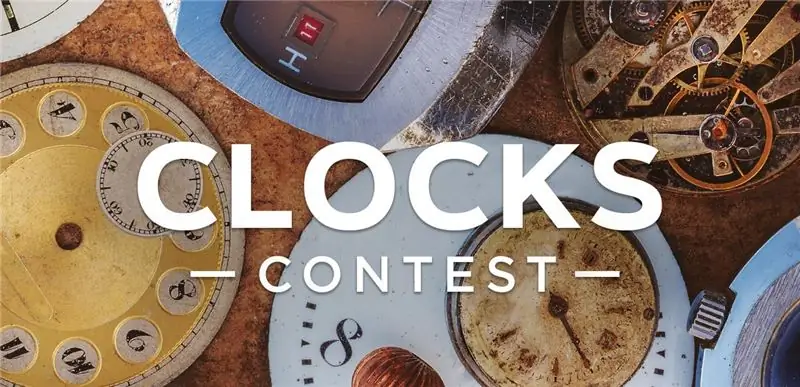
Premier prix du concours d'horloges
Conseillé:
ATtiny85 Montre et programmation de suivi d'activité vibrant portable ATtiny85 avec Arduino Uno: 4 étapes (avec photos)
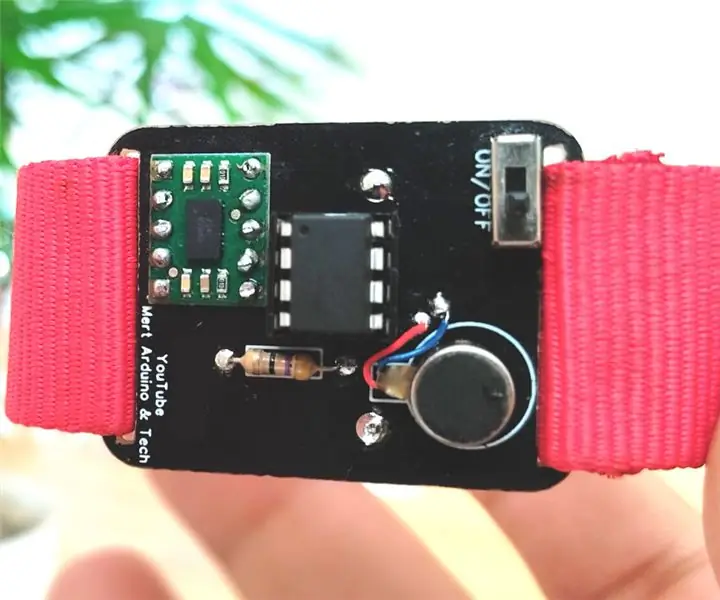
ATtiny85 Montre de suivi d'activité vibrante portable et programmation ATtiny85 avec Arduino Uno: Comment fabriquer la montre de suivi d'activité portable? Il s'agit d'un gadget portable conçu pour vibrer lorsqu'il détecte une stagnation. Vous passez la plupart de votre temps sur l'ordinateur comme moi ? Vous êtes assis pendant des heures sans vous en rendre compte ? Alors cet appareil est f
Armoire d'arcade Bartop personnalisée : 32 étapes (avec photos)
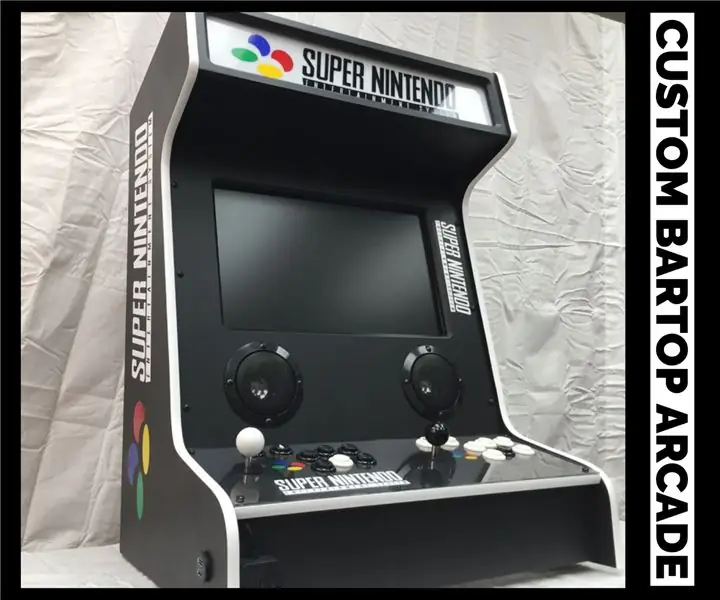
Armoire d'arcade Bartop personnalisée : Bonjour et merci d'avoir consulté mon premier Instructable sur la façon de construire une armoire d'arcade bartop personnalisée ! Les arcades ont vraiment commencé à faire leur retour à mesure que nous vieillissons et que nous voulons profiter de jeux rétro nostalgiques. C'est une belle opportunité
Apprenez à concevoir un PCB de forme personnalisée avec les outils en ligne EasyEDA : 12 étapes (avec photos)
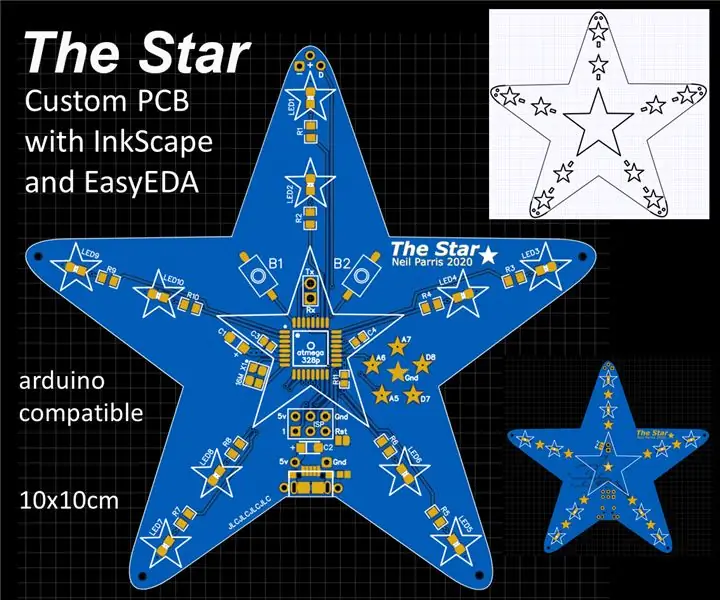
Apprenez à concevoir un PCB de forme personnalisée avec les outils en ligne EasyEDA : J'ai toujours voulu concevoir un PCB personnalisé, et avec des outils en ligne et un prototypage de PCB bon marché, cela n'a jamais été aussi facile qu'aujourd'hui ! Il est même possible d'assembler les composants de montage en surface à moindre coût et facilement dans un petit volume pour économiser le sol difficile
Montre programmable avec affichage à quatre caractères : 5 étapes (avec photos)
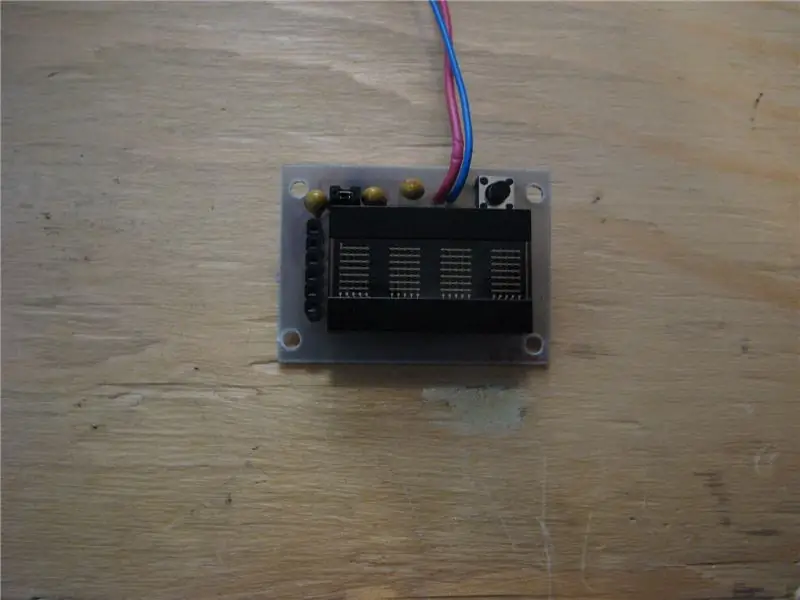
Montre programmable avec affichage à quatre caractères : vous serez la vedette de la ville lorsque vous porterez cette montre-bracelet odieuse, surdimensionnée et totalement peu pratique. Affichez votre langage grossier préféré, les paroles de chansons, les nombres premiers, etc. Inspiré par le kit Microreader, j'ai décidé de faire une montre géante en utilisant
Horloge personnalisée avec aiguilles photo : 5 étapes (avec photos)
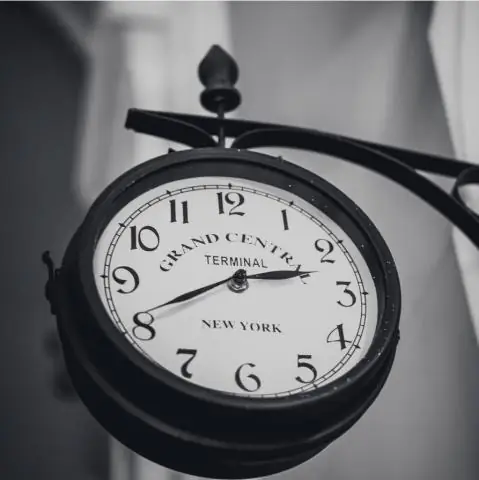
Horloge personnalisée avec aiguilles photo : Certaines personnes sont des observateurs d'horloge. Désormais, tout le monde peut être l'horloge. D'autres projets personnalisent le cadran de l'horloge. Celui-ci personnalise les aiguilles de l'horloge. Il a l'air cher, mais coûte moins de 5 dollars et environ 30 minutes par horloge. Parfait pour Chr